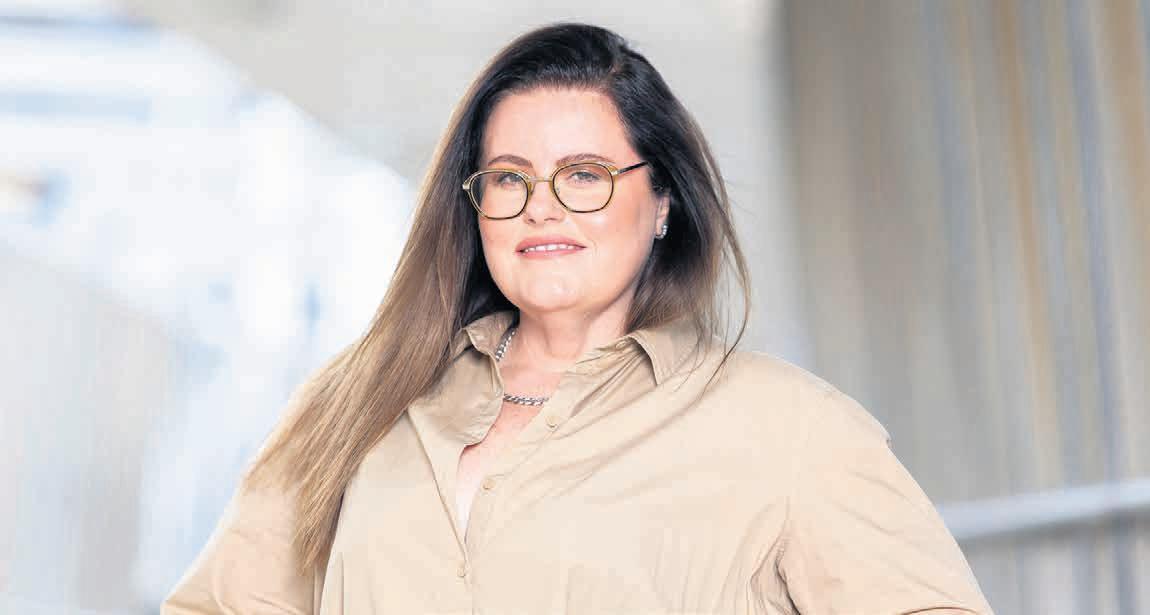
12 minute read
PRODUCTS
Safety plan targets tankers
WORK HAS begun on a new training program to improve road safety in the dairy industry.
Transport and logistics specialist insurer National Transport Insurance has received Federal Government funding through the National Heavy Vehicle Regulator’s Heavy Vehicle Safety Initiative to develop and deliver ‘Spilt Milk: A national crash reduction program for the dairy industry’ during the next two years.
National Transport Insurance’s Staci Clark said NTI would work with experts and those involved in transport for the dairy industry to develop and test training programs, resources and workshops.
“The goal is to reduce dairy tanker rollovers and improve road safety by working with drivers, fleet managers and maintenance consignors,” Ms Clark said.
The Australian dairy industry produces $4.4 billion of milk each year.
NTI data shows on average dairy tankers are 2.4 times more likely to be involved in a major crash than other freight transport. That’s the equivalent of one in 17 dairy tankers compared to one in 41 other heavy vehicles.
Ms Clark said a similar education program in Victoria’s forestry industry resulted in a 65 per cent reduction in rollovers from 29 in a year to FY20 being rollover free.
“For the dairy industry it is about improving road safety and protecting the environment because dairy tanker crashes not only put drivers
National Tranpsort Insurance’s Staci Clark says NTI will work with experts and those involved in transport for the dairy industry to develop and test safety training programs, resources and workshops.
and road users at risk, but can cause milk and diesel spills,” she said.
“Keeping Australian industry moving toward a safer and more sustainable future is our priority and this program is another example of NTI working with industry to achieve that.”
To express interest in NTI’s Spilt Milk program, email: sustainability@nti.com.au
Find out more about the program at: www. nti.com.au/better-business-hub/our-expertise/ spilt-milk


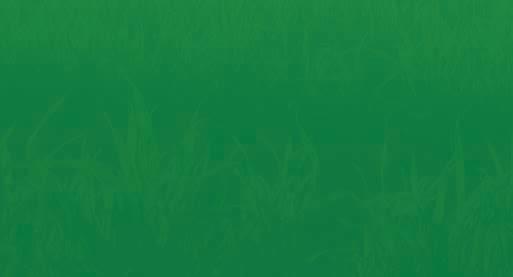
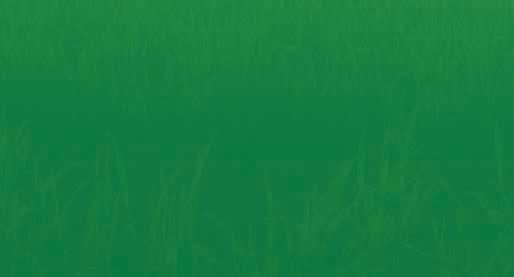
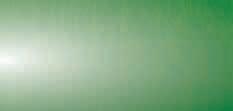

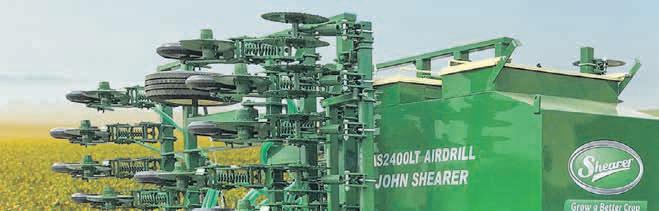
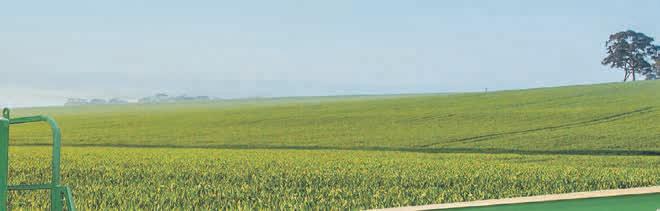


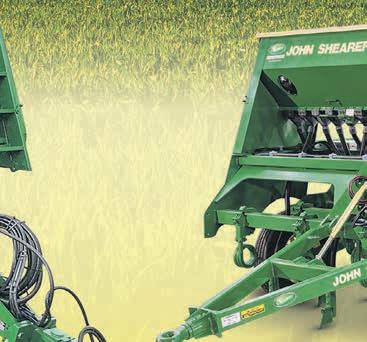

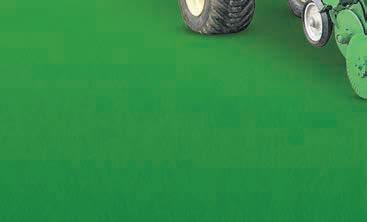
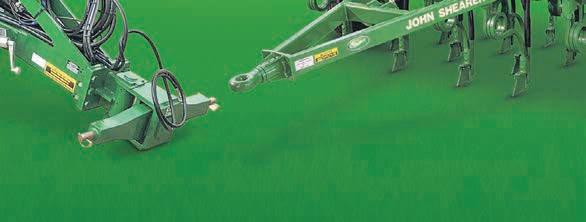
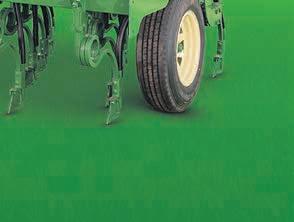
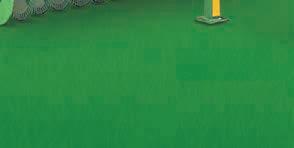
No job is too hot too handle
LOCATED NEAR the picturesque North Yorkshire village of Holmefirth, Longley Farm is best known to the Australian food industry as the parent company of Richmond Dairies in Casino, NSW.
Richmond Dairies, which is known for its fast freeze technology, produces a range of dairy ingredients for the food manufacturing industry in Australia and abroad, exporting products around the globe.
Longley Farm has been owned by the Dickinson family since 1948 when brothers Joseph and Edgar inherited their great uncle’s farm together with 10 cows.
Today the farm boasts one of the best Jersey cow herds in the United Kingdom with 300 of its own cattle, and tops up demand with milk from up to 40 trusted farmers around the country, which is used in its award-winning range of dairy products.
The farm also makes its own ice-cream, together with the traditional specialty Yorkshire curd. Longley Farm is the world’s leading commercial manufacturer of this uncooked fresh curd product, which is the key ingredient in a traditional Yorkshire curd tart.
All of Longley Farm’s products are made without the use of artificial additives, colourings, preservatives or stabilisers and are sold in local shops and some national supermarkets. The need for heat exchangers
Like most dairies, the factory operates a number of heat exchangers to remove the heat from processing and manufacturing its dairy products, which must be chilled for sale.
Most of these are of a traditional plate design, which is fine for simple heating or cooling purposes, but recent upgrades to the machinery which produces fresh cream and Yorkshire curd have seen new corrugated tube type heat exchangers installed.
These new HRS heat exchangers incorporate corrugated tubes that provide a number of advantages over flat plate or smooth tube types.
The biggest advantage is that heat transfer is increased, particularly at higher flow rates, meaning that less heat transfer area is required and resulting in a shorter, more compact design, together with associated cost savings.
This also results in gentler handling of the product during the cooling phase, which is crucial for fresh cream production.
“For a cream process we want the cooling profile to be very gentle and we want to agitate the cream as little as possible,” Longley Farm’s Konrad Schwoch said.
Corrugated tube heat exchangers have a lower pumping requirement than other tube-type heat exchangers as their compact nature results in a lower pressure drop during the heat exchange process. This helps contribute to the long operational life and reduced maintenance of the unit, which has advantages for Longley Farm.
“For me, the value in the tube-type heat exchanger is that it is a more robust piece of equipment,” Konrad said.
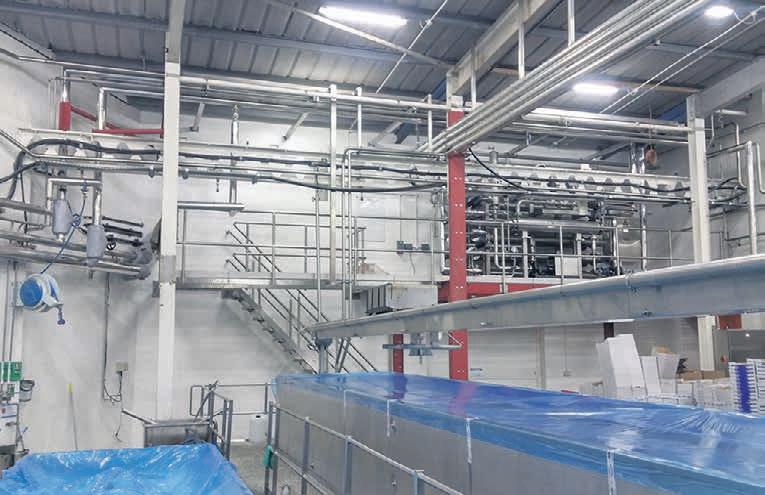
The compact HRS system sits on a platform above the dairy processing area.
“It’s harder to break and easier and cheaper to service, saving money over the lifespan of the unit.”
Like all HRS heat exchangers, the corrugated tube units are made from high quality stainless steel.
“Because of the innovation you get from HRS, such as multi-tubes and annular spaces, you have a lot more surface area than a traditional tubular heat exchanger,” Konrad said.
“Because of this … the actual size of the new system is smaller than the old equipment it is replacing, making it easier to incorporate into the factory layout.”
Continued page 33

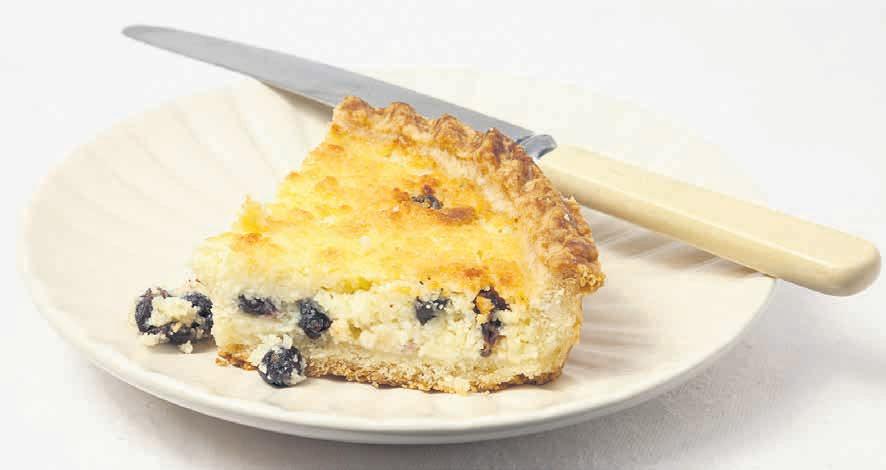
Longley Farm uses HRS heat exchangers to process fresh curds used in a traditional Yorkshire curd tart.
Different design needed for curds
The new heat exchanger chosen to improve Yorkshire curd production is a different design to that used for cream.
This time a corrugated tube design, which specifically increased turbulence, was chosen to help to reduce fouling inside the tubes.
While most dairies make curds and whey by adding bacteria to the milk to turn the lactose into lactic acid and stimulate the proteins to stick together, for Yorkshire curd production Longley Farm adds acid directly to the milk, which is the traditional way of making the product.
“Using this traditional method creates a problem when you want to heat or cool the solution,” Konrad said.
“The curd can be very, very small, so when you are pumping it you get curd mixed into the whey portion.
“When you want to pump it you know you are going to get particulates in it, so we need to use a corrugated tube heat exchanger because traditional plate heat exchangers can easily become blocked with the small bits of curd.”
This unit has been specifically designed by HRS to handle these particulates, even if they reach levels well in excess of those found in normal operation.
“With all our different requirements, including heating and cooling, it can be difficult to automate quite a complex group of processes and not end up with the biggest, most complicated plant in the world,” Konrad said.
“The clever thing has been keeping the heat exchanger solution simple while providing everything we need.”
DESIGNED WITH OPERATORS IN MIND
Operator comfort and convenience are at the centre of the latest updates to the Case IH Maxxum and Puma ranges.
New Puma SWB models (150hp to 180hp) now feature CVT transmission options to complement the existing Powershift offering. Upgrades to the 2022 Maxxum and Puma SWB tractors include a lowmounted front screen wiper with an increased sweep area for better visibility; new highperformance LED safety lighting features; an improved entrance area with aluminium steps; and an integrated cool box.
“Obviously when the operator is more comfortable in the cab, this can only help to reduce fatigue and increase productivity in the field,” Case IH’s Seamus McCarthy said.
“The Maxxum and Puma are among Case IH’s most versatile tractors, and with these upgrades this versatility is enhanced and customer experience improved.”
He said a number of standard vehicle modifications were also aimed at providing enhanced performance and connectivity for customers. New electronic joystick and improved telematics with additional display functionality allow greater efficiency and precision.
“Fast and reliable in-field connectivity is critical in realising the full potential of precision agriculture, with a direct result of that being an improvement in the profitability of farming operations, and Case IH is working hard to deliver that potential across our lower horsepower ranges,” he said.
“Customer expectations are increasingly high when it comes to the sophistication of their machinery, and the latest updates on our Maxxums and Pumas are an example of listening to our customers and interpreting their needs through the new features.”
Updated MY22 models are now available for order with the Puma due to arrive in Australia mid-year and the Maxxum expected in the second half of 2022.
For more information contact your local Case IH dealer.
BUILT TOUGH
Multi 4 & Multi 5 Bale Feeders
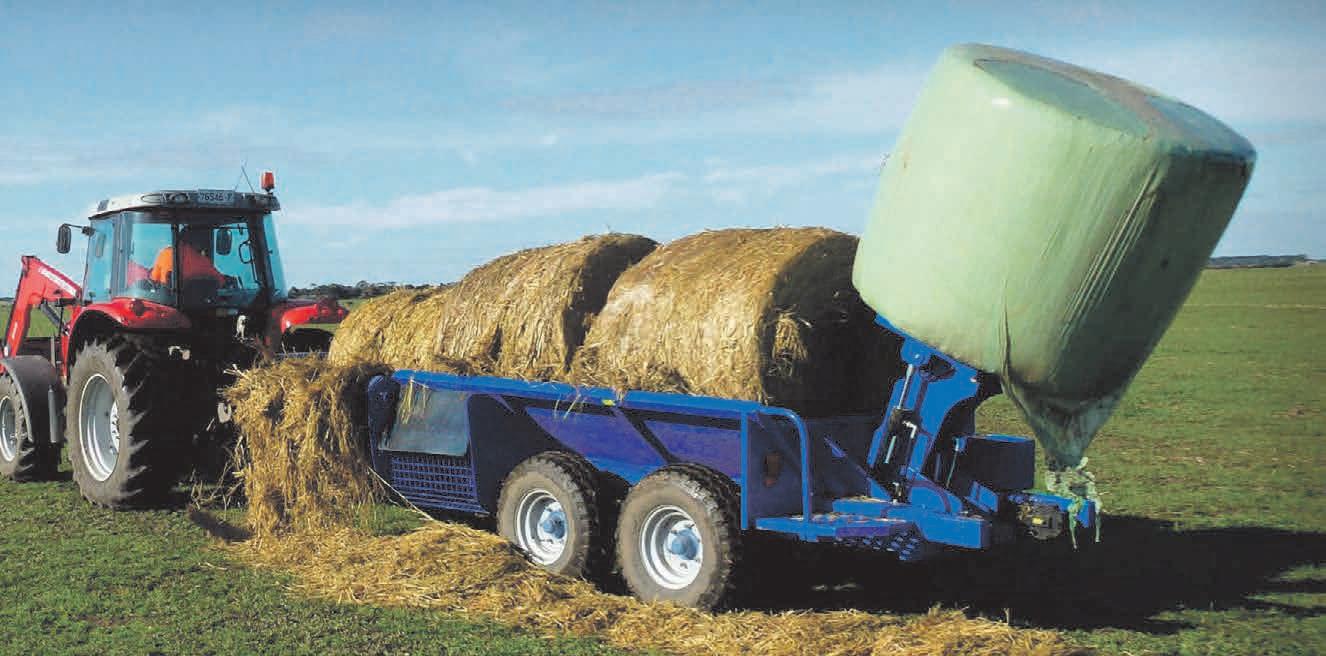
You expect strength, quality and performance from your farm machinery and McIntosh Bale Feeders deliver all three.
The range of McIntosh Bale Feeders are designed to a strength and performance standard with an all steel construction. Every detail has been carefully thought out to reduce breakdowns and provide trouble free operation for years to come.
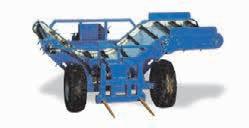
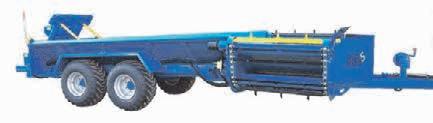
Plan aims to improve data use
As part of the collaboration, John Deere and Food Agility CRC will work together to apply a newly developed Food Agility Data Sharing Agreement Template to data flow scenarios and to improve the template before it is released more widely to industry later in the year.
The template, developed with National Farmers’ Federation and Minter Ellison, establishes key considerations between farmers and service providers including data transfer, storage, disposal and access, and provides clarity on the roles, responsibilities, deidentification and control of data.
John Deere’s Benji Blevin said it was pleased to contribute industry expertise to a project that would inform future frameworks for best practice data management.
“AgTech has the transformational ability to drive productivity, performance and sustainability across the ag sector, and while it continues to develop at an increasingly rapid rate, it is vital to ensure Australian producers feel confident they have control and transparency when managing their farm data,” Mr Blevin said.
“As a technology innovator, we are continuously reviewing and improving our own robust data policies and practices and we are delighted to work with Food Agility CRC on this project to empower Australian producers to collect and share their data with confidence and control.”
Food Agility CRC’s Dr Mick Schaefer said the Data Sharing Agreement Template was also being piloted in other research projects, including its $6.5million collaboration with AACo, and would ultimately benefit the broader agricultural industry.
“We are stress testing the Data Sharing Agreement Template to ensure it meets the needs of farmers and service providers in a range of circumstances. We aim to release it for wider industry use later in the year to help drive best practice across the sector,” Dr Schaefer said.
Ensuring farmers have control of their data and the value attributed to it, is a goal within the NFF’s plan for agriculture to be a $100 billion industry by 2030.
NFF CEO Tony Mahar said the Template Data Sharing Agreement was a practical application of the NFF’s Farm Data Code, which aimed to give farmers clarity and transparency in how their data is managed.
“Every year digital tools and services are playing a bigger role on-farm. Farmers need to have confidence that the data they share is being protected,” Mr Mahar said.
“It’s great to see Food Agility CRC applying the principles of our Farm Data Code to develop a template that will be available for broader industry.”
The project is due to be completed mid-2022.
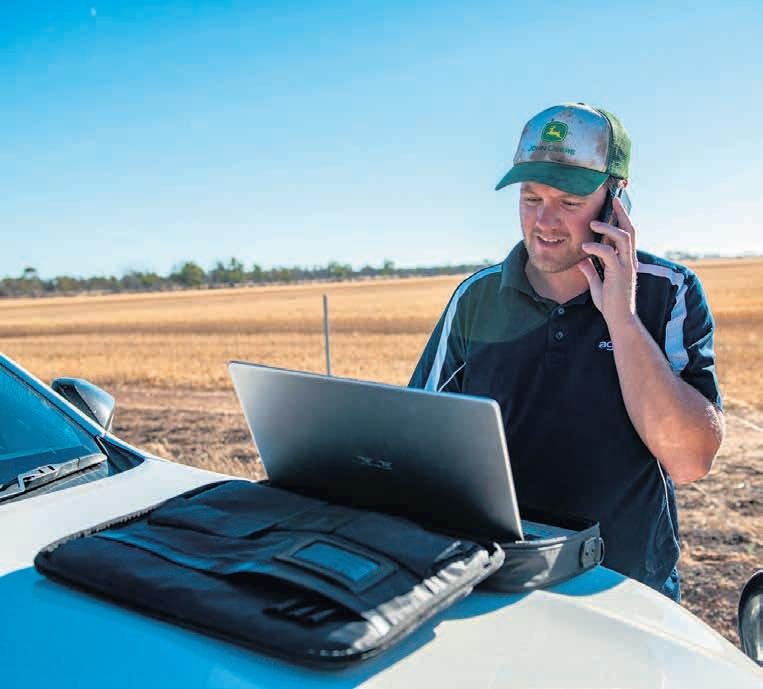
Industry and science are coming together for a new project focused on driving improvements in the use and management of agricultural data.
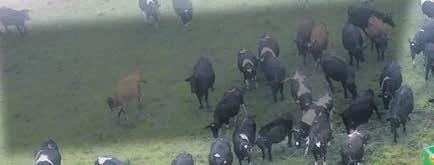
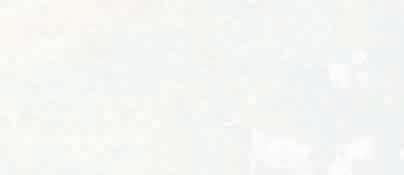
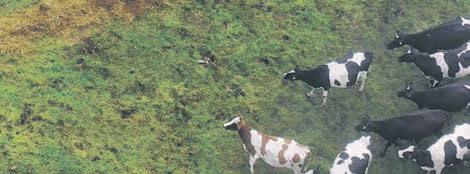
CUT DOWN YOUR CUT DOWN YOUR CUT DOWN YOUR CUT DOWN YOUR FEED COSTS FEED COSTS FEED COSTS FEED COSTS
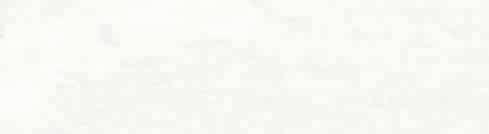
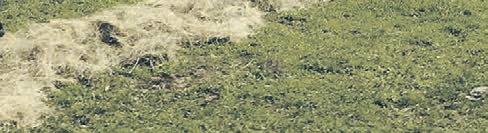
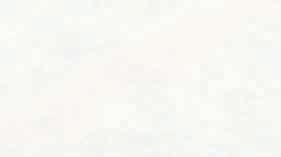
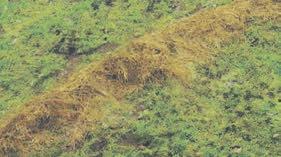
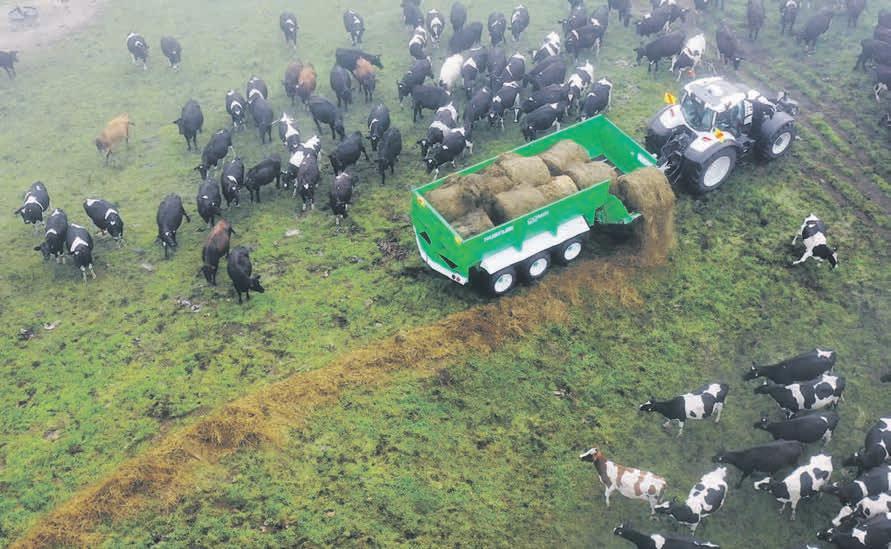
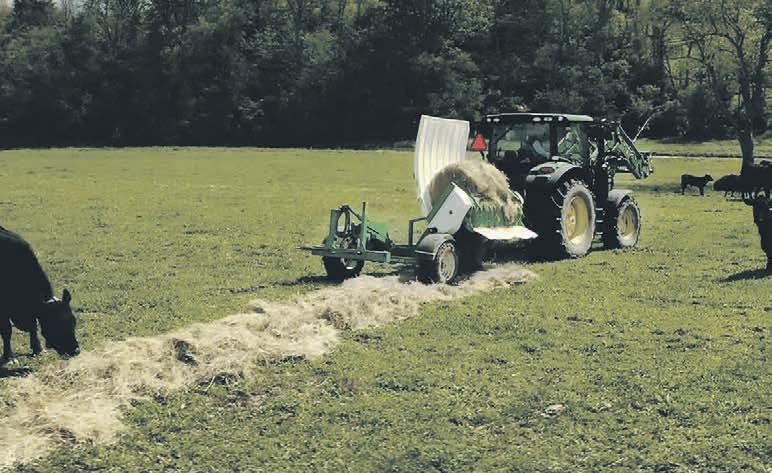


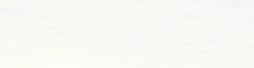
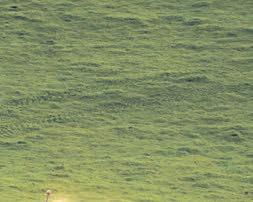
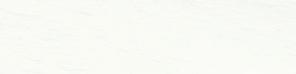

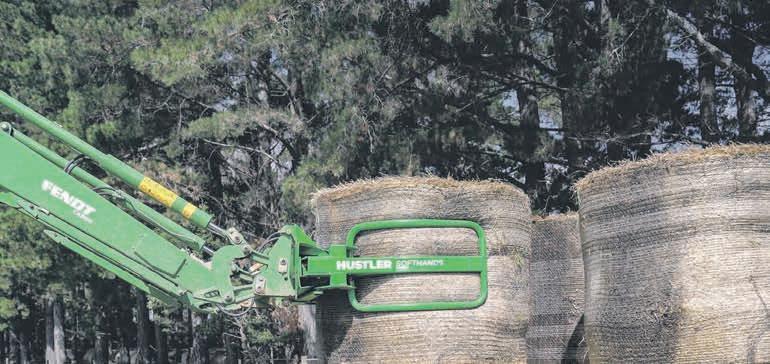
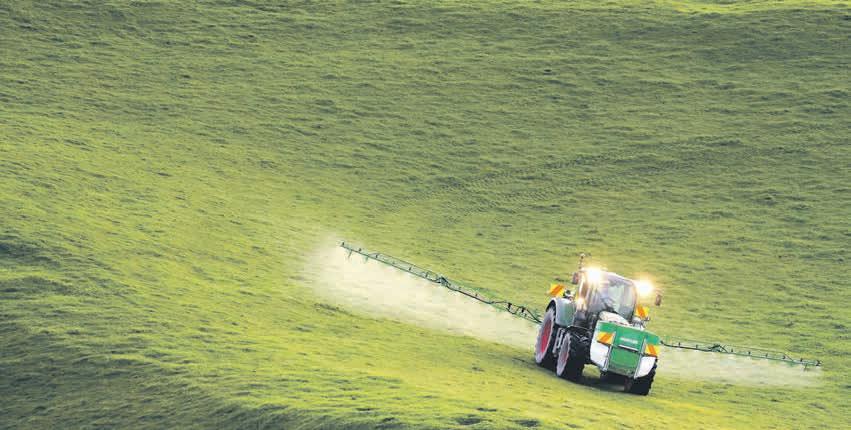

and get a chance to win a Stihl Chainsaw! a Stihl Chainsaw!

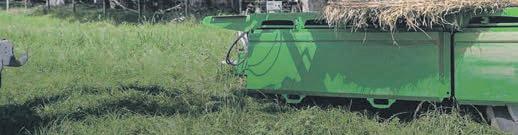
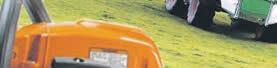
