
59 minute read
By the editorial staff Re-starting The national (and international) packaging industry has never actually closed the doors of its factories, but has indeed responded with determination to the requests of the community, asserting its strategic value on the field in times of the Covid-19 emergency. Data and facts from the real world, amidst difficulties and signs of encouragement
INDUSTRY - Re-starting with packaging RE-STARTING
Let’s start again from ... 2*. The start of the fateful and longed for “Phase 2” in Italy has foreseen a generalized recovery of production and commercial activities. The national (and international) packaging industry has never actually closed the doors of its factories, but has indeed responded with determination to the requests of the community, asserting its strategic value on the field in times of the Covid-19 emergency. Data and facts from the real world, amidst difficulties and signs of encouragement.
Advertisement
For a few months, the world has ceased its headlong rush ... We listen to the silence of the cities, mourn the misfortunes of many and the failures of all too many, to trace out the boundaries of a future not free of tension and uncertainties... Hence the worldwide Corona virus health emergency would therefore seem to have torn apart the social and economic framework, painstakingly built over years of relative well-being in different parts of the globe, requiring the redesign of the rules of peaceful cohabitation. Will we be able to get back on track? The question is a must and the answer must necessarily be “yes”, regardless of the time it takes.
By the editorial staff
Each to their own
By narrowing the field of observation to the industrial forces of the packaging supply chain, as reporters we have closely followed the reactions of many companies that, fielding specific skills and resources , have been at the forefront in providing the right support to FMCG producers, food and pharmaceuticals first of all (fully documented on our websites packmedia.net and italiaimballaggio.net). Of these companies, we want to underline the speed of reaction in managing the complexity of the moment, with the aim of also safeguarding, together with production continuity, our own human capital and more generally public health: reconversion of existing plants to create and package protective devices, donations of various sizes and in various forms, support
* A quotation freely inspired by an Italian film of some years back ... “Let’s start again from 3” said the dreamer Massimo Troisi to a pragmatic Lello Arena.
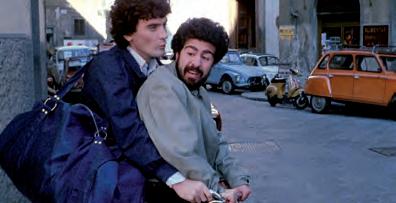
“Troisi: What has been has been ... enough, I start from three ... Arena: From scratch you mean!... “Troisi: Eh? ... Arena: From scratch: I start from scratch. “Troisi: No sir, I start from ... ie ... I managed to succeed in three things in life, why should I also jettison them? Why should I start from scratch? I want to start from three! “
Maurizio Nannucci (2003), Garden of the Guggenheim’s Museo in Venice
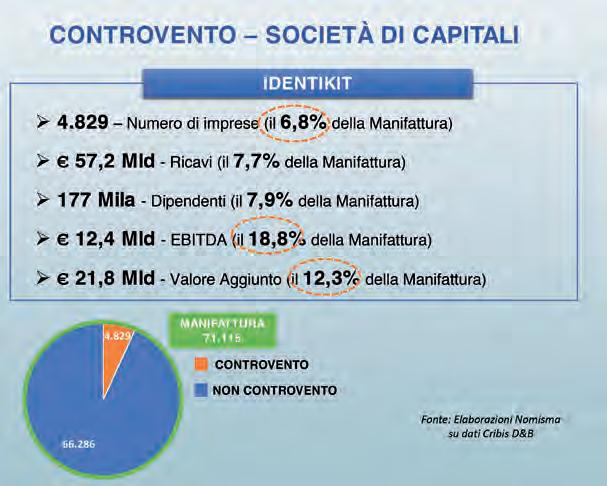
for workers and territories, creating new and effective ways of communicating with the market or remote assistance to customers via previous investments in digitization… And this is an attitude that has united machine and packaging materials manufactur-

ers, a mode of doing business that continues to look ahead.
Those who falter are lost
That packaging companies can - and must - continue to drive our country system, was also clearly stated by Nomisma in the recent “Controvento” [countertrend] research, illustrated via webinar to over 600 operators on 7 May.
• Under observation 71,115 companies, which represent 14% of the Italian manufacturing sector and which in 2018 expressed revenues of 741.3 Bln (70% of the sector) giving work to 2.3 million employees (66% of the sector), with an added value of € 178 billion (around 10% of Italian GDP).
• After identifying some structural factors that guarantee a greater propensity for competitiveness (i.e. geographical location and company size) and defining the performance criteria with respect to the main economic and financial variables (revenues, EBITDA, added value ...), There are 4,829 so-called Contravento
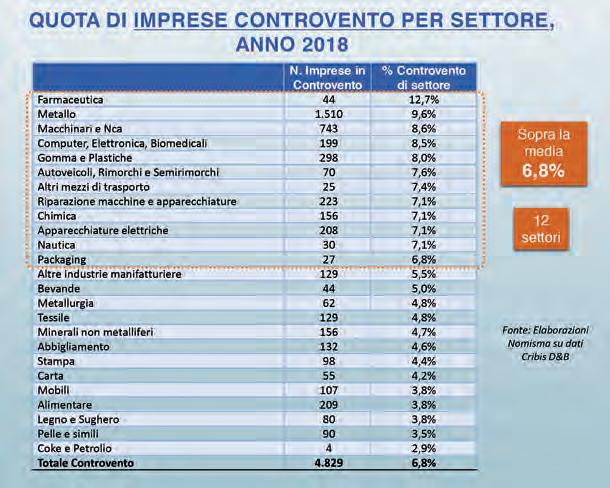
[countertrend] companies, those that perform better in practice. Packaging and pharmaceutical companies also feature among the “winning sectors” of this ranking.
• We read in the research that «... In particular in packaging, the concerns that feature as Controvento companies, are among the more-structured, larger ones, those with over 500 employees, while things do not look so good for the medium and small concerns. In the pharmaceutical sector, however, the size class does not appear to discriminate in ensuring greater relative competitiveness within the sector itself».
• The generation and accumulation of a liquidity buffer and the maintenance of a solid financial and capital structure also become essential in facing any downturn situation , such as for example the current COVID-19 emergency. In this sense, the cash equivalents generated and also maintained for sudden financial needs have become the key to the survival of companies (these aspects were analyzed by Crif-



Rating in a study presented during the Nomisma webinar).
• Therefore, the question Lucio Poma, Nomisma’s Scientific Director of Industry and Innovation, is not rhetorical about the importance of the “Controvento” analysis at a time when the country has to face the Corona Virus emergency «as it becomes more than ever essential that the group of companies driving the country don’t lose too much momentum. If this leading group were to lose ground significantly, the damage would be incalculable».
Automatic machines: let’s face reality
The survey carried out between March and April 2020 by MECS, UCIMA market analysis company (and presented at the same time as Controvento) shows the substantial stability of the “packaging” sector, without, however, obviously underestimating the unknowns posed by the emergency. The significant participation of companies in the survey here enables one to draw a reliable picture of the situation, providing important indications both in relation to the first quarter and with respect to the forecasts for the whole of 2020.

• In the light of the data collected from 165 packaging machines and systems manufacturers, Luca Baraldi (MECS-Confindustria Ucima study center) enters into the merits of

the analysis (of which we give a summary), and recalls that, globally in 2019, the the sector has developed a turnover of around 45.5 billion Euros (CAGR of 5.2% between 2015 and 2019). In this context, with the 8 billion turnover recorded in 2019, Italy has maintained the leading position of the ranking, overtaking its German competitors.
• During the emergency, Italian packaging companies never stopped production: only 4 out of 100 did so, while 1 out of 5 declared a slowdown in commercial and after-sales activities, without ever interrupting production.
• All of them have introduced safeguard measures for their employees: smart working, holidays, diversified shifts and access to social safety nets have “impacted” on business productivity for 9 out of 10 companies.
• The problems related to subcontracting have caused slowdowns for 8 out of 10 companies although, in most cases, the packaging companies have supported their historical suppliers, as a heritage to be safeguarded. 1 out of 10 companies have been forced to change supplier.
• From the beginning of the emergency to the beginning of May, only 1 out of eight companies (12.9%) reported some signs of increased demand (especially from the food, pharmaceu-
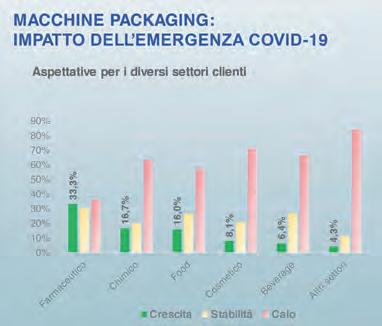
tical and chemical sectors); overall, 80% of the sample estimates a sharp drop in production, turnover and orders, with a contraction of more than 25% for half of the companies and more than 50% for a significant share of companies (14.2% of the turnover , 24.1% on orders);
• The negative forecasts for the whole of 2020 are corroborated: 86.7% of companies estimate that the impact of the emergency will result in a drop in turnover and for 50% of the sample it will be a heavy drop. The only sector for which signs of improvement are visible is the pharmaceutical sector, where expectations of stable or growing results (63.6%) exceed those of worsening (36.4%).
Summing up
Summing up, it seems to us correct to underline that the overall picture presented is in all probability affected by the emotions of people called to express themselves in an exceptional moment in terms of unpredictability and scope. Already, after a month, we are in fact collecting different signals that partially mitigate what emerged from the Ucima survey. Thus, in the following pages, we present some case histories that open up new perspectives. For our part, we thank those who have accepted our invitation to tell about their industrial and human experience, sharing emotions and future strategies.
Protection of people and continuity of services
Aliplast’s double challenge in emergency management.
Carlo Andriolo, Aliplast SpA CEO (Hera Group) transforms plastic waste to make it become a resource by managing the integrated cycle in a sustainable way.
The health emergency that has hit the country represents a double challenge for Aliplast, a Hera Group company and primary reality in European plastic recycling. In fact, it was necessary to combine the primary need to guarantee the health of employees with that of continuing to carry out strictly necessary services on a daily basis, which cannot be interrupted. These are services aimed both at the community, such as the recovery of plastic from segregated collection to give it new life, as well as the production sector, such as the manufacture of articles in plastic materials which are also fundamental for the food sector, also at the forefront of this emergency. The range of initiatives undertaken, and still active, for the protection and safety of personnel has been wide and articulated.
Guaranteed and safe production, with satisfaction Marco Torta, Arcoplastica (Andezeno, TO), a leading company in the sector of thermoformed and extruded plastic materials.
«We have never stopped business, to ensure the operational continuity of our customers, almost all engaged in the food sector, and aware of the responsibility to keep the supply chain active» comments Marco Torta, who summarizes what has been done in the company. «Fortunately we were able to find facemasks and sanitizing gel already in early March, which allowed us to immediately implement the distance between the workers and comply with the indications, which were then incorporated into the various DCPMs. In addition to producing in compliance with the rules, we therefore immediately guaranteed the health of our employees, for whom we have also activated insurance. We are also studying a bonus to be paid in welfare to the workers who supported us in the period of March-April, allowing us not to stop the plants. For the moment, we have not had the need to activate social safety nets, but instead we have, where possible, resorted to smart working, involving in particular the commercial, accounting and administration sectors (approximately 70% of the staff). Whenever possible, however, we expect a gradual return to normal business hours: in fact we believe that, for our reality, the “traditional” form of work is more efficient and effective. Also in relation to finding the raw material, we reacted promptly from the first signs of the emergency: also in March we decided to acquire massive materials, mostly from abroad, which guaranteed us full operation».

Since the beginning of the emergency, Aliplast has put into practice the directives, recommendations and prescriptions provided by the Hera Group for all companies and territories; in particular, the use of safety devices, the sanitization of all company areas and systems, the displacement of work shifts to minimize contacts between the members of the operating teams, repeated information and awareness activities for staff on behavior correct to be adopted during the performance of one’s job to operate safely avoiding any risk of contagion. In addition to the adoption of measures and actions to protect multiutility workers, not least the COVID-19 insurance coverage policy for all employees who are infected with the virus, Aliplast has developed an extraordinary remote working plan, organizing a large staff turnover to lighten the presence in the offices as much as possible. The situation is still evolving and, for this reason, in the Hera Group there are working groups that meet constantly to follow the evolution of the emergency and consequently adapt in parallel, day by day, the organization of work and services to continue to guarantee, in maximum safety for all, an indispensable service for
citizens and businesses.
The choices and technological investments undertaken in the past prove useful to face the situation. Torta is convinced of this, specifying: «The company choice to be as “autonomous” and verticalized in all phases of the supply chain has allowed us not to suffer delays and not be penalized too much in this difficult period. We have three extruders with which we internally produce PET-PP-PS-PLA and 19 thermoforming lines, with which we convert the finished product starting from the material made with our extruders. All equipment is new and avant-garde, in line with the “philosophy” I4.0: and this made it possible to solve some problems very quickly (by means of remote diagnostics), avoiding the movement of technicians, even so impossible in this moment in time.
Although it is still difficult to make an objective assessment of the trend of these months, Torta expresses a cautious optimism:
«Certainly, we recorded a significant drop in sales in the technical sector, but it is realistic to think that it was due to the serious difficulties of the entire sector rather than to a loss of
Arcoplastica’s market share.
Fortunately, the technical sector affects only about 10% of the company’s turnover, while the remaining 90% is linked to the food chain, where the losses have been more contained. This being the case, we will probably not be able to match the 2019 turnover, yet we consider ourselves lucky, because we operate in a sector that has not stopped. And then, we can look to the future with greater faith, triggered by the awareness that the perception of plastic packaging has been completely re-evaluated, going from a “demonized” article to a hygienic, light and safe means, which has allowed us not to stop the chain of food supplies in the most tragic period of the pandemic».
Farsighted and therefore prepared
Capsulit vs. COVID-19
Gianluca Rossi, Capsulit Spa (Roncello, MB), manufacturer of safety capsules for the pharmaceutical
resort to any social safety nets. ployees who, in such a difficult moment, understood the impor-
industry.
«If any problems have arisen in relation to the procurement of raw
Capsulit carried out a pandemic risk assessment as early as spring 2009, during the spread of the influenza virus AH1N1v (swine flu). «On that occasion - explains Gianluca Rossi - we elaborated a plan with the aim of limiting the contagion of the employees and being able to guarantee the deliveries of period. This plan, updated and revised periodically in the following years, was put in place even before the Italian government declared the recent lockdown, with the adoption of all the necessary countermeasures».

In addition to the effort to quickly obtain PPE and disinfectant liquids - despite the known contingent difficulties - and to have followed all the prevention protocols established by the Government, Capsulit has organized training and training meetings for all staff, where possible activating smartworking for some business functions. Committed to the pharmaceutical market, hence Capsulit and its subsidiaries Giglioli and Capsulit Iberica, never stopped production, allowing pharmaceutical laboratories and multinationals to pack essential, life-saving medicines during the health emergency. Recognized by numerous customers as a “strategic supplier”, in compliance with the protocols, it has always been fully operational “which - specifies Rossi - has also allowed us to not have to In this regard, we want to express maximum gratitude to our emtance of their work, demonstrating seriousness, commitment and availability, guaranteeing the continuity of production».
the products to the pharmaceutical companies, even in a critical materials, we have nevertheless managed it thanks to the stocks supplied in a timely manner according to the provisions of the pandemic plan. And in any case, the majority of suppliers with whom we have consolidated partnerships for years have responded very well to our requests.
From the turnover point of view, in addition to the positive effect of some projects started even before the emergency, we record a demand of the Pharma companies in significant increase: on the one hand, the requests are oriented by the contingent need to package life-saving drugs, on the other we see the will of the big pharma to not be understocked and run the risk of not being able to distribute the necessary products. In fact, the Covid-19 emergency leads us to predict an incremental growth trend in our business». The Capsulit group invests a large part of its turnover in technological innovation, which has certainly played a decisive role in these months, where «for example, some supplies delivered in record time have found justification in the elasticity of the service that we are able to offer the market». What about the future? Difficult to make predictions, «also because - concludes Rossi - much will depend on how good we will be at keeping at a distance and the protocols laid down to avoid the further spread of the virus».
Navigate and stem the perfect storm Essential, proactive, communicative and digitized
Marco Parretti, CEO of Etipack (Cinisello Balsamo, MI), production of coding and labeling systems
«More than “starting up again”, Etipack has been of the idea carrying on sailing to stem the perfect storm »Marco Parretti begins, reiterating that “starting up again” is a label that we do not feel we can apply to our situation, since we have never different points of view, we are pleased to be able to highlight some positive and unexpected aspects in our reaction to the emergency. Our being immediately listed among the categories of producers of essential goods, in addition to giving us continuity, has allowed us to better follow the numerous customers who operate in critical sectors such as food and pharmaceuticals. Smart working, which allowed us to continue working by reorganizing the workstations in the best possible spaces, in full compliance with health and safety requirements, was a positive experience, which we will certainly integrate in the future as a stable alternative for improve working well-being. As far as the performance of the business is concerned, we believe we are among the least affected industrial concerns since we have been able to count on the one hand, on a clientele consolidated in the essential supply chains that has not suspended operations, on the other on our international network of distributors and builders, which allowed us to contin-
actually stopped and indeed, in this negative experience from ue operating in the areas least affected by the pandemic. Furthermore, our sales and after-sales networks, widespread and independent, and the technical assistance service entrusted to distributors in the various countries, have allowed us to keep our support to our customers active».
«The surprise - continues Parretti - was instead the enormous possibility offered by digital. The strong acceleration towards the adoption of digital tools and processes has simplified some procedures, leading us to find new solutions. It also gave us the opportunity, thanks also to the cancellation of the fairs, to enhance our communication and presence on digital channels to maintain contact and faith with all our stakeholders. To continue the fight against the spread of the virus, we have drawn up a very detailed containment plan, also signed by the union representatives, which we have shared and made available for consultation on our website».
Action and reaction
Always close to employees and customers
Gabriele Gnudi, GB Gnudi Bruno SpA (Bologna), sale and assistance of machines for the chemical-pharmaceutical, food, confectionery, cosmetic, paper and various sectors.
The history of GB Gnudi Bruno SpA has distant roots: founded by Bruno Gnudi in 1965, it has witnessed decades of Italian social and economic history, overcoming “dark” periods and increasingly consolidating its position in the sale and assistance of CAM brand packaging machines. With sincerity, Gabriele Gnudi today admits: «We were not prepared, like everyone else, to face a world pandemic that, until a few weeks before, could only be credible in science fiction films: in a new context our history and our experience had little to teach us. But after a very first and understandable moment of loss, we gave ourselves two priorities: maintain productivity and supervise the relationship with employees». «As for our activities, fortunately we have never had significant blocks: our customers, mostly pharmaceutical companies, have never stopped production, with the consequent need for completion, updating or assistance of their lines. We initially reduced the trips of the technicians, but the deliveries in progress did not suffer significant delays and the after-sales assistance activity continued as usual. Only a small minority of subcontractors - Gnudi points out - had to stop the activity, right at the beginning of the pandemic, delaying deliveries». At the time of writing, the company does not believe it has lost market shares in the first quarter of the year, despite recording a decrease of around 10% in turnover. «Authorized to work as part of the pharmaceutical supply chain, we have always remained active without resorting to social safety nets and rather encouraging the use of residual holidays. However, wanting to guarantee the greatest possible peace of mind for our collaborators, we have, like many others, “improvised” remote work which has proved, even to our surprise, an effective and highly appreciated method by employees, having also taken care to strengthen the moments of meeting, albeit virtual, to maintain a high communication exchange and a sense of belonging. To date we are continuing in a “mixed” way and, in the future, we will try to preserve some of the advantages experienced. Finally - concludes Gnudi - we joined the control program encouraged by the Emilia Romagna Region, subjecting all employees to a first serological test, which will be repeated three-weekly always on a voluntary basis».

ItaliaImballaggio.pdf 1 24/06/2020 11:28:29
www.npac.it - info@npac.it
YOUR SLEEVE SPECIALIST
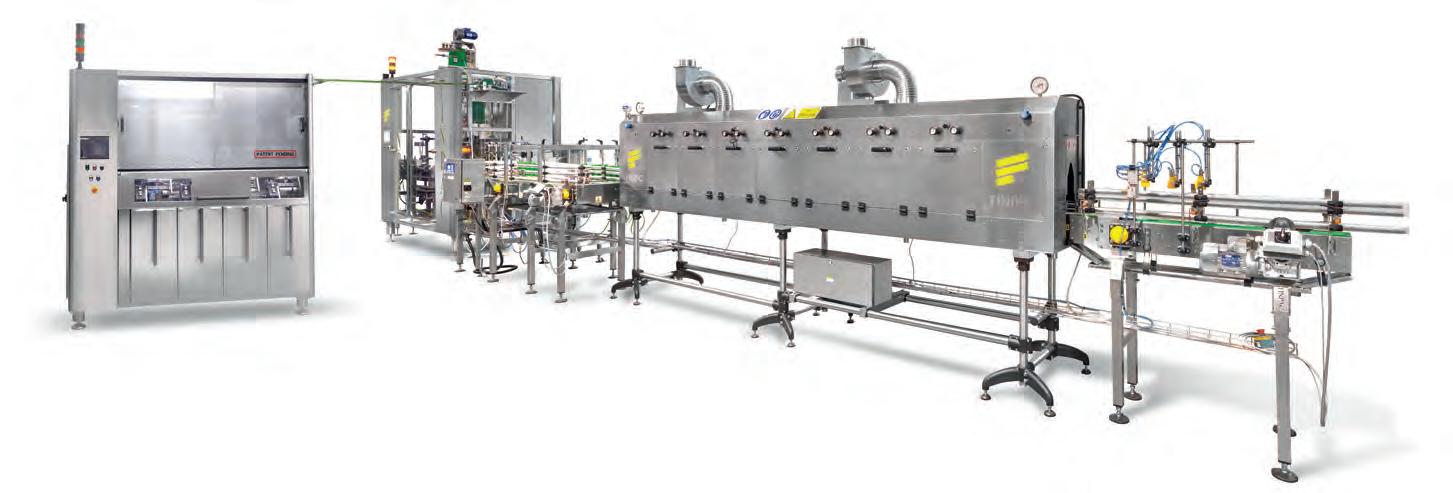


Well-managed stocks, upgraded plants, fast responses
Financial statements and perspectives from IGC
Patrizia and Maura Tuzza, IGC Srl (Busto Garolfo, MI), pioneers in the production of heat-sealed single-dose sachets.
Patrizia and Maura Tuzza agree in recounting their experience at IGC in times of Corona Virus. «During these months of the Covid-19 emergency our company has never closed its doors. We rigorously applied national prevention protocols, used smart working where possible and introduced incentives for our employees, who continued to work with great commitment and responsibility. We managed not to be found unprepared, both thanks to the strengthening of some production lines carried out in the previous months, and due to a careful management of supplies».
The only drawback, note the Tuzza sisters, the forced postponement of the installation of a new plant at the end of the year. Overall, also thanks to the ability to respond quickly to new customer requests, IGC has not undergone a significant contraction in orders and turnover. «Indeed, we have seen an increase in sanitizers and oil and vinegar sachets for intended for catering, sectors that have had to adapt quickly to the logic of the single-dose, which is more than ever suited to the strict sanitary rules imposed by the pandemic. Our forecast is that of a 10% drop in turnover at the end of the year, mainly due to the contraction of orders from customers who do not work for large-scale distribution. But it is only an estimate, because the situation is constantly evolving and we need to verify the end users’ purchasing propensity. Hence our IGC strategy does not change, on the contrary it has been strengthened by what has happened in recent months. «We believe more and more in the thousand possibilities of using the heat-sealed sachet, also as an alternative to the plastic bottle. And we will continue to suggest environmentally friendly solutions to customers who are more attentive to sustainability issues. Because even if the world of heat-sealed sachets will also no longer be as it was before, we need to make sure that it is greener».
Plastics gets its own back
Guaranteed and sustainable productivity, even in smartworking
Paola Centonze, Marketing & Communication Manager ITP - Industria Termoplastica Pavese (Bosnasco, PV), manufacturer of flexible packaging
Converter of flexible packaging intended mainly for the food sector, ITP has never stopped the plants because, according to Ateco codes, it was immediately included among the essential activities. «We have therefore not activated social safety nets, but - explains Paola Centonze - we have subscribed to an additional health policy and rewarded out employees in recognition of their commitment. From the management point of view, then, the streamlining of the bureaucratic rules regarding smartworking has shown that, without major impedences and obstacles at regulatory level, companies are able to adapt quickly and successfully to changing needs. Even those who resorted to smartworking immediately demonstrated their ability to adapt to new ways of working and communicating. And they did it with a sense of responsibility. The benefits, in this sense, exist both for the company and for the workers, but I would also add for the environment, thanks to the reduction of travel: so I don’t see why we should deprive ourselves of an instrument that is now in step with the times ... provided that the State is not anxious to over-regulate it, curtailing the benefit, but rather incentivating it».
In addition to having complied with the national anti-Covid prevention protocols, ITP has provided for the daily sanitization of the work environments, has redeveloped meeting rooms transforming them into additional refreshment areas/workstations and has established a direct line with medical specialists listening and support.

Centonze also states: «Given that the supply chain has guaranteed operational continuity, even our initial fears about possible difficulties in procuring materials and transport immediately vanished. This is demonstrated by the fact that, especially at the beginning of the emergency, we have faced many requests, which fortunately we managed to fulfil in a very short time. Then when the prolongation of the state of confinement forced us to eat meals at home, and the home delivery service became increasingly popular, the purchase of food (packaged, of course) became a priority. And as never before, consumers have understood the importance of hygiene and the value of food safety guaranteed by packaging. «If therefore, we can imagine a “positive” impact of the health emergency on the business - adds Centonze - we must however take into account the costs of the extraordinary measures put in place by the companies ... We will see how and if they will weigh on the budget. At the same time, the impossibility of completing development projects with customers has oriented our efforts on production and immediate delivery, aiming for maximum efficiency. In this we have been facilitated by the investments made previously: the diversification of the offer that we have put in place since the 1980s, investments in R&D and technologies have proved successful choices. The same can be said about the growth of some figures, such as the Protection and Prevention Service Head and the KPO, who proved to be of extraordinary support during the emergency».
Proceeding well, with the necessary precautions and warehouses always stocked
And 2020 will still be strategic, thanks to technological innovations
procedures, which allow us to have a constantly stocked warehouse available to respond promptly to all customer requests.
Angelo Maggi, Administrator of ULMEX Italia (Padua, PD), supplier of technical components, consumables, equipment, spare parts and services for the world of flexo and gravure quality packaging printing.
During the weeks of health emergency, ULMEX has never stopped its activity, guaranteeing the continuity of its service and in particular the supply of consumables and technical assistance to all those customers who, operating in the food, pharmaceutical and All in full compliance with government regulations regarding social security and distancing, ensuring maximum commitment to reducing risks. A part of ULMEX employees has operated and continues to operate in smart working: a procedure which had already been introduced for some time for the commercial forces, which in this way can manage their activities in the areas of competence with maximum flexibility, working by objectives. For those who remained in the company, we have reorganized the work shifts so as not to create gatherings and ensure compliance with safety distances. At an operational level, we found some inevitable delays in deliveries by suppliers, which suffered a forced stop of activities. However the inconvenience was minimal. This is thanks to our regular raw material and component procurement and storage Of course, we too have experienced a drop in orders in recent months which will also partly reflect the turnover for the year, mainly linked to the fact that some customers, not coming under what were considered essential services, had to stop production. However, this is a relatively contained decrease, as ULMEX operates in diversified markets, some of which have always continued
newspaper printing sectors have never stopped their work. to operate. Furthermore, the investments made in recent years to strengthen the presence on the Italian and international market, thanks to partnerships with the best brands, have proven extremely important in recent months.
Customer faith and interest in the products and solutions proposed by ULMEX has never faded, guaranteeing constant growth over time in terms of orders and supply contracts stipulated. If 2019 was a particularly positive year for ULMEX, 2020 too, despite all the difficulties and uncertainties related to the health emergency, will be particularly strategic for us, with important innovations also in the technological field. Our goal is to internationalize services and commercial activities. For this reason we are working on the launch of new proprietary technologies and latest generation solutions that allow our customers to further improve their print quality. With this in mind, we already look positively towards drupa 2021, which will be an important international showcase for us for the presentation of these technological innovations.
No stop to maintenance
Working on the territory, in the sign of continuity
Stefano Paolucci, Nimax Marketing Manager (Bologna), coding and marking systems, inspection and control, labeling
Nimax has normally continued its business, thanks to the hundreds of customers belonging to the agri-food and pharmaceutical supply chain, today more than ever essential for our country and who have never been able to interrupt their activities. «For this - Stefano Paolucci explains - we have decided to remain open to guarantee them all the necessary assistance, paying the utmost attention to the health indications provided by the competent authorities to face this health emergency, guaranteeing the health of our employees, our customers and therefore of the community». Nimax has therefore adhered to the protocol prescribed in the instructions of the Ministry of Health. «We have facilitated smart working for as many people as possible to avoid crowding in our offices; our technical team has been equipped with masks and gloves, as well as anyone of us who comes into contact with people outside the company; we periodically sanitize our workplaces and to all the people who still carry out their duties in the office we have distributed sanitizing gels ... It goes without saying, lastly, that there is a 15day preventive stay at home for those with mild flu symptoms or who have entered contact with people passing through the red areas». All these procedures have allowed Nimax to support its customers: although, where possible, remote telephone assistance has been privileged, all repairs and maintenance at the production plants have not been interrupted. «As for the sending of spare parts and consumables or new equipment - Paolucci continues - in consideration of the fact that many operators in the logistics sector have reduced the terms of service and / or the territories served, Nimax has made efforts to ensure that all customers receive the materials they needed as quickly as possible, in order to continue their activities without interruption».
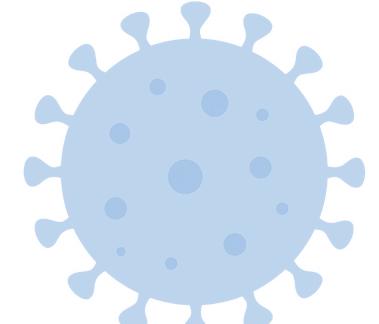

The future that awaits us You can also learn from an emergency
Mattia Dall’Armellina, Sales Department Laborplast (Busto Arsizio, VA), regeneration of rigid PVC, used in the production of compounds, by extrusion and injection molding, and of cores for coils.
The lockdown imposed for the containment of the COVID-19 epidemic has had a huge impact on the economic and social fabric of our country. Like many companies in this period, Laborplast has faced major changes in order to be able to continue its business, while ensuring the necessary safety for all its employees. Before the obligations deriving from national regulations, distancin, risk training, supply of PPE, sanitization and safety measures were activated in all departments. The use of smart working has been implemented for all areas not related to the production sector, and a health insurance policy has been activated to support the possible risks deriving from COVID-19. «The management of this change - Mattia Dall’Armellina points out - has not only involved a passive response to events, but has also been a test bench for evaluating projects and investments undertaken over the years and a strong incentive to devise new strategies to apply in a scenario highly destabilized by the epidemic». Laborplast had the opportunity to continue working also thanks to the choices made over the past few years: alongside the PVC cores for packaging, which have been fundamental to support the production of the food and pharmaceutical sectors, the production of rigid PVC granules and the new range of technical semi-finished products, have allowed us to face this crisis on different fronts. «We are aware - concludes the manager - that the economic repercussions will certainly be felt during 2020, but the possibility of facing this phase has allowed us to accelerate many of the ongoing projects and to create new ones, such as the search for new materials for our souls for winding or strengthening the green footprint of our regenerated PVC, through the study of the product life cycle and obtaining environmental certifications. All these new projects will also be carried out thanks to the new plant, which will become operational at the end of 2020, demonstrating how it is necessary to focus on the development of new roads especially in the most difficult periods».
Plan, manage, optimize, digitize
Smart working and distance learning are doing well, hoping for a “V-shaped crisis”
Antonella Rioso, Marketing Communications Pilz Italia Srl (Lentate Sul Seveso, MB), global supplier of vertical automation solutions for security and control systems.

Functional to the chain of essential activities, Pilz also did not stop its activities during the lockdown. Thanks to the solid and little “leverised” capital structure, it has not activated social harmonizers for the moment. «We are aware of the fact that - intervenes Antonella Rioso - the explosion of the Coronavirus has entailed and will have serious consequences for everyone, including Pilz. However, in a context of high economic and financial unpredictability, we have organized ourselves to ensure effective monitoring of the planning, budgeting and reporting processes, leveraging above all on the optimization of cash flow and investments, favoring those in digital technologies» . Moreover, the IT structure of Pilz immediately proved to be extremely advanced and well thought out even in dealing with personnel management during the pandemic: «The first problem faced was in fact to manage the concerns and difficulties experienced by the employees, some of whom come from the” red areas “. However, taking advantage of our IT structure, we can say that we have hit the accelerator in adopting smart working programs, even if we do not know if it will be a permanent measure. I would also like to emphasize the rapid adoption and dissemination of digitized training services. When the virus leaves us and we can go back to work with more peace of mind, the experience acquired in the field of smart working and distance learning will allow us greater efficiency in work and in the services to our customers».
Reassuring news also on the “supplies” front, although the closure of the Chinese factories at the beginning of the pandemic triggered understandable alarm bells. «Pilz has suppliers operating in different areas of the world; and then, on the strength of past experience with the 2008-2009 crisis, we have long since identified alternative sources for at least the most critical components, which has allowed us to face the new emergency without too many jolts in the delivery times of our products».
But what is the estimated impact of the Coronavirus emergency on production, turnover and orders? «Pilz expects a 12% drop in turnover and orders in Italy in the first half of the year, while in 2020 by 6%, but only if the health crisis stops by June. And we sincerely hope that this is a “V” crisis, as already happened in 2008-2009, when companies, especially the automation sector, were able to recover quickly within a year and a half. However, we do not believe we have lost market shares; indeed, thanks to our innovative spirit, we have continued to satisfy our client companies’ thirst for innovation, typical of times of crisis, necessary to survive and maintain high competitiveness. The choices and technological investments undertaken in the past, as well as the convinced adherence to the themes of Industry 4.0, has meant that Pilz has transferred the concepts of innovation not only to its products but also to the production sites; and it is precisely thanks to the extreme digitalization of the processes that we believe we have the right flexibility to face the difficult times that lie ahead».





Readily available materials and services Attention to workers, the market and the environment: having valorised a common skill base, we are moving towards stability.
Davide Morten, Sales and Marketing Director Robatech Italia (Cesena, FC), green technologies for bonding.
As usual, Davide Morten goes straight to the point. «Robatech’s activity has never stopped: in fact, we have continued to provide our customers with both materials and services, thanks to a “smart” organization and the availability of our team. We made partial use of the tools arranged by the authorities, trying to balance the load between the collaborators and minimize the inconvenience. Of course, the company has always anticipated the payment of remuneration to its collaborators. For some time I have considered Robatech a smart company - continues the manager - and our habit of dematerialising documents and automating procedures has allowed us to ferry activities to smart working mode quickly and easily. The professional scenario for all of us has therefore changed, in many cases definitively: for this reason we are further implementing our infrastructures and processes towards an even smarter and greener way of working. On the other hand, our natural predisposition to work in an agile and ecological way has been fundamental to allow us to maintain the levels of service that Robatech’s customers have come to expect».
After having equipped all our co-workers with every tool imaginable useful to combat the spread of the virus, in Robatech an additional special insurance was immediately activated, aimed at covering the possible medical and social costs due to a possible, undesired contagion. «Fortunately nobody has needed it, but we are still convinced that it was a sensible investment by a company very attentive to the well-being and health of its staff. We have also started a survey, to determine the level of well-being perceived as a function of working in an agile way, the results of which are being studied to implement further investments and operational reorganizations».
Robatech is a multinational company whose supply chain is spread over several continents. «It was therefore inevitable to face some logistical difficulties, due more to transport problems than to the supply of the goods. Fortunately, thanks to optimized warehouse management and interconnection between branches, we can say with certainty that we have minimized the negative consequences for customers. In all probability, also due to this - Morten continues, crossing his fingers - the perception that the Coronavirus emergency impact on production, turnover and orders is lower than the worst expectations: we are in fact only 10% below our budget, with a fairly stable forecast towards the end of the year. It goes without saying that any forecast, in this period and with the present scenario, is difficult and presents a high risk of inaccuracy. However, in the first quarter of 2020 we did not lose market shares; our drop in turnover, which was contained compared to a much more severe context of general contraction, leads us to think that we have even improved our position on the market compared to many competitors. The 2020 forecast, revalued on the basis of the data currently available, positions our turnover volumes at around -10% compared to the previous year».
The new normal: rethink and improve yourself Team pride, guaranteed supplies
Neni Rossini, President of SIT Group SpA (Faetano, Republic of San Marino), flexible packaging solutions that are technologically advanced, safe and designed to limit environmental impact to the maximum.
«Those who know us know that in general we are optimistic - says Neni Rossini - and even in this serious situation we have managed to see opportunities, in particular the possibility of rethinking the way we work, to improve it. During the pandemic, the most important result was being able to guarantee supplies to customers in the food supply chain: therefore, not only did we not lose turnover but, despite the difficulties, we safeguarded the continuity of production and the reliability of deliveries, proving to be a more than reliable partner... counting on the fact that this will also be recognized in the future».
The emergency period that involved the whole world had undoubted repercussions and a heavy impact on all businesses, both for the unpredictability and extent of the events and for the speed with which they followed one another. «But - explains Rossini - since SIT Group is part of one of the essential supply chains, the food supply chain, we have been able to operate in all our factories and we have done so by introducing, since February, the rigorous measures to contain the risk of contagion, which have allowed us to go on safeguarding everyone’s health, by far the most precious asset and the fundamental value that has always guided our choices». Smart working has been activated for almost all office activities, however in production this was obviously not possible and the people involved «have seriously done their duty», scrupulously respecting the new procedures, with a sense of responsibility and proud to know that the availability of food in supermarkets (one of the few certainties left, if not the only one) was also partly thanks to them. It seems to us that this difficult situation has made the awareness of the social role of the company and, with it, the pride of being part of a team emerge stronger than ever».
But what can we expect today with the start of the so-called “phase two”? «I believe - Rossini reiterates - that we will have to adapt to living no longer an “extemporaneous” emergency, with a beginning and an end, but a new reality or better, a new normalcy, which imposes severe changes ... in habits and behavior, in work procedures and operating procedures, even in human relations. On the other hand, it is precisely in the most critical moments that creativity and the ability to question the routine and habits acquired in a personal comfort zone can be best expressed. In this sense, countering the fear and uncertainty of the beginnings, initiative, the desire to adapt and tenacity must prevail».

We feel that even the people who continued to “run” the machines are proud, thinking about how precious their contribution has been in not making Italians miss an essential goods item like food: it has been a beautiful and highly engaging experience.
Opportunities arising from skills and knowhow
Good prospects for closing the year
Volpak (Coesia company), headquartered in Barcelona (E) designs and markets automatic machines for packaging in flexible pouch bags.
During the lockdown period, Volpak operated in compliance with the provisions of the Spanish government: as the company works in the sectors of primary necessity, it has kept production active, but immediately adopted strict safety measures. The protocols for accessing Volpak currently involve measuring body temperature, washing hands, using gloves and masks and maintaining a distance of at least 2 meters between one person and another. The work areas are also constantly disinfected by certified companies. Smart working has been privileged wherever possible. Even before the Covid-19 emergency, the company favored remote forms of trend. At present it is difficult to predict how the situation will evolve in the long run, but it is plausible to think that remote work will be privileged wherever possible. Indeed, the crisis has not impacted production but, on the contrary, has brought new opportunities. Volpak is in fact traditionally linked to the various categories of the Food and Personal Care sector, with specific expertise in the field of disinfectant wipes. In recent months, all these sectors have seen considerable growth, both through the organized distribution channel and in the e-commerce sector. This has
work and the crisis triggered by the pandemic consolidated this led to a great demand for machines and systems for processing and packaging. The period of crisis has also seen a great deal of commercial work, to consolidate the relationship with historical customers and at the same time develop links with new realities. All this combined with the traditional technological vocation of the company. Volpak has always focused on research and development and on the flexibility of its solutions. Its portfolio of machines is wide and diversified, offering the possibility of effectively serving various needs, both in terms of types of packaging and production performance. All this has enabled the providing effective answers to market requests which, especially in times like these, are constantly evolving.
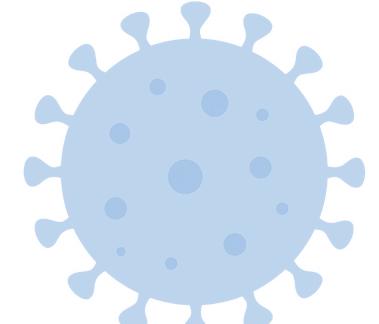
Today, the company has 47% more orders than the corresponding period in 2019, with good prospects for the closure of the current year and for 2021.
Tubes big and small in total safety
Work creates sociality, companies invest but… what about the incentives?
Fabio Gussoni, CEO Scandolara Spa (Garbagnate Milanese, Mi), production of aluminium and plastic tubes for the packaging of cosmetic, oral care, pharma and food products.
«The generous legislative production Anti-Covid 19 which began on Sunday 8 March, has provided for the so-called necessary activities, including plastic packaging and metal containers for food and pharmaceutical use: for which Scandolara has fortunately never stopped working and has not even yet had to activate social safety nets »underlines Fabio Gussoni, entering into the merits of the organization of the work. «Our company has a strong industrial connotation, organized over three work shifts from Monday to Saturday from 06:00 to 06:00, and for most functions, presence is required either in production or in support activities. Only a few “central” figures could have been de-materialized and operated in smart working; we have therefore decided to favor elderly colleagues or those who, in the family, had or still have relatives who are a lowered immune system or who are affected by particular pathologies... Overall, a dozen out of a total of 238 employees. At this moment, only colleagues from the sales department located in the north of Milan take turns to observe some periods of smart working, but as soon as we have the opportunity to return to the company, we will all do so with great enthusiasm. We are actually tired and tried and tested by staying at home and not directly interacting with colleagues because, after all, work is the truest expression of sociability... My thoughts go to a seller who cannot shake hands and greet his customer or to the quality manager who must, remotely, judge the quality of a process or product...».
Gussoni also notes with satisfaction the diligence with which all the preventive measures have been activated in the company: «In advance of 15 days from the “Save Italy” Decree, we had prepared the use of the necessary medical devices, the frequent sanitization of work environments, the “social” distancing both during the canteen break and entering and leaving the premises, anticipating or postponing entering/exiting the company by 30 minutes, so as to avoid gatherings. But - he adds - let me emphasize that Scandolara has been ISO 15378 certified for some time (as specified in the requirements of the Quality Management System for companies manufacturing materials used in the primary packaging of medical and cosmetic devices) as well as ISO 9001: it is therefore in our DNA to respect stringent procedures guarding against any danger of contamination».
In the face of some slight delays by non-strategic suppliers following the closure of certain areas in Italy or abroad, Scandolara did not experience any particular problems with the subcontracting or the procurement of materials, so much so that «contrary to any forecast, for the first quarter we recorded a surge in the order backlog, thanks above all to the food and parapharmaceutical sector. The situation between April and May was different, however, when we were hit by the effects of the closure of the entire professional beauty sector (beauty treatments, beauty salons, Spas, hairdressers ...). Unfortunately - the manager reasons - we must consider that the 11 weeks of lockdown will never be recovered by the affected product sectors. Do not think of recoveries along the way; what is lost, remains lost! We can only hope that consumers will return to the “pre-Covid” consumption of goods and services as early as this promising start to summer. But it is true, however, that the recovery should be supported by economic incentives and shock absorbers, both for exhibitors and consumers; however, apart from a few “lucky” ones, there are still millions, and I mean millions, of citizens waiting to receive the subsidy for the month of March».
Gussoni concludes his discussion with a second, albeit calm, polemical note: «The emergency forced us to unexpected expenses, generated by the Anti-Covid package, some “one shot “, many other recurring and mandatory; the government has indeed undertaken to recognize the total deductibility of these expenses up to a maximum limit of € 20,000; however, we know that only a few lucky people have won the “click-day” lottery, ensuring the “bonus” for a 50% tax credit with a maximum limit of €50million. In a country like Italy, where there are millions of businesses ... we can only imagine the vying for favor and the confusion».
Extraordinary times require extraordinary actions
Reliable and efficient, also via the web or which is opening on the short term, can connect via
Marchesini Group (Pianoro, BO), design
and construction of customized machines Live assistance. Customers with technical assistance and lines for the packaging of pharma- needs can contact Customer Care, which will provide IT ceutical and cosmetic products. support tools, including an app to download to their To continue offering maximum support in an interna- to see what is happening on the machine and provide tional context conditioned by recent events, Marchesini resolutive indications in real time; Group - which as an essential activity never stopped during the Covid-19 pandemic - has undertaken a series Teleservice assistance. Customers who have installed of initiatives aimed at guaranteeing its standard relia- the software for the Teleservice service on their systems bility and efficiency, preventing health risks. can remotely set up the operator panel through a secure The company has done a lot to ensure supplies to cus- connection, allowing Marchesini specialists to work on tomers, especially pharma, because many of them are the machine directly from their office. at the forefront of studying the vaccines and products needed to fight Covid-19. The initiatives closely related to the product have been To ensure full operational continuity for the “galaxy of accompanied by numerous internal provisions - compharma”, it has also enhanced online services: thanks to pany canteen closure, daily temperature measurement, these new tools, added to consolidated procedures, serological tests for all collaborators - and institutional Marchesini Group can today and in the future respond initiatives. These include the free home-based babysitto all requests for assistance from Italy and abroad, ting service for children up to 6 years of age and the placing the customer first despite the adversities of the donation of 200,000 euros to the Sant’Orsola moment. Foundation. Finally, a reminder that Marchesini Group FAT streaming. Customers who are unable to physical- to 3D technology, protective devices starting from snorly reach the Group’s offices and have a test in progress keling masks.
Servotecnica and positive thinking
Reduced contraction in turnover thanks to the continuity of deliveries
Emilio Bistoletti and Sabrina Bistoletti, respectively CEO and Communication Manager of Servotecnica, specialist in motion control.
«Servotecnica has never stopped working, also thanks to the fact that - explains Sabrina Bistoletti - in 2019 we completely digitized the internal organizational procedures: we were therefore able to activate smart working in real time and, having recognized our activity as essential, as required by the government decree, we were able to guarantee the processing of orders and deliveries to customers of the primary production chain. In fact, every smartworking worker had a laptop with remote connection software installed, which in fact allowed the virtual transfer of the workstation to the home for full operation. At the state of the art - continues the manager - Servotecnica has managed to cope with the situation, avoiding social safety nets and trying to protect its employstreaming, communicating with in-house technicians. smartphone. In this way, an expert operator will be able has collaborated with other companies to create, thanks ees as much as possible. Attentive as we are to technological evolution, we immediately took action to allow them to work safely both in the company and at home, providing all of the appropriate tools: in addition to complying with national prevention protocols, we have, for example, invested in the purchase of devices for sanitizing the air and surfaces, so as to guarantee a safe environment for workers, but also for customers and our partners».
Emilio Bistoletti intervenes on the impact of the
Coronavirus emergency on production, turnover and orders, who reports of a situation that is in many ways comforting: «We have not lost market share, but we report a 25% drop in orders on the first quarter compared to the budget. However, the turnover had a much lower than expected contraction, as we managed to maintain the continuity of deliveries to the industrial sector which remained active during the lockdown. However, a review of the spending plan was necessary, planned in consideration of a 20% reduction on an annual basis. The trend in order collection for the month of May - the CEO points out - seems to suggest a good recovery. We are therefore confident in the second half of the year that it will recover the two months of lockdown, allowing a better closing than the post Covid-19 revised forecast».
Hygiene and safety: single-dose keywords
Pandemic-proof and “Phase 2” packaging
Graziana Tassinari, sales manager of Valmatic, a key concern in the international single-dose packaging market.
Valmatic is part of the list of strategic and essential production companies that have never stopped. «In these months - Tassinari explains - we have had to organize ourselves to continue the activities by respecting all safety standards, establishing shifts, alternate attendance in the office and smart working, a measure with which the company has met the needs of a staff composed in prevalence of women, many of whom are struggling with the management of children at home after school closes. Regarding the work in the production plants, in a certain sense, we have been advantaged in respecting the anti-covid protocols, given that our standard procedures have always provided that operators work individually on the machines with caps, masks and with the adequate distancing». As a demonstration of the appreciation for the work done in such a difficult moment, Valmatic rewarded the employees with a bonus in their paychecks but also supported some solidarity initiatives in the area, including the donation of surgical masks to the Municipality of San Prospero, all the hospitals of Mirandola and the San Prospero Red Cross («sourced, when still difficult to find, thanks to a contact in China»), as well as the delivery of hand sanitizers to some old people’s homes. «As far as the economic consequences are concerned - the manager continues - I have to start by saying that the health emergency has fallen during a period of great expansion of our business, in terms of turnover, orders, staff ... By 2020 we had planned to maintain this trend, also in view of the important international fairs we should have participated in as an interpack, but also China Beauty in Shanghai. Obviously, like all of us globally we suffer from the heavy consequences of the pandemic, however, as good Italians, we are reinventing ourselves to seize the opportunities to work better, even in this difficult situation. We expect a drop in orders in sectors penalized by the lockdown in the second half of the year, first of all the cosmetic one, one of our main markets which in recent months has seen a significant contraction in demand in almost all sales channels. But I also think of the single-dose supplies for the airlines, which have suffered a drastic drop. On the other hand, today more than ever, the hygienic safety of products is of crucial importance, and the advantages offered by the single-dose in this sense are pushing many manufacturers to turn their attention to this type of format. For a concern like ours, new and significant opportunities have therefore opened up, already translated into concrete projects. In the health sector, we have started the production of a line of hand sanitizers and as regards food - in line with anti-covid regulations that provide for the obligation in bars and restaurants to supply single dose condiments at the tables - we are moving to offer new single-use packs of balsamic vinegar and olive oil. We aim to offer an impactful design, more appealing than the classic sachet, perceived by many manufacturers and exhibitors as too cheap, inadequate to present high-end products. To satisfy customers’ needs, we have lowered our MOQs, in order to make the service for third parties more usable and flexible. Even from the foreign market, despite everything, there is no lack of positive signs: although the postponement of international fairs will make it more difficult to make new contacts, many foreign customers have asked us to supply single-dose machines to be included in their production lines, to offer their products in a cleaner and more hygienic cladding, for which today there is a high demand.
New needs open up new potential in automation
Proven efficiency of smart working
Engineer Simone Bassani, COO WITTENSTEIN SpA, specialist in transmissions, complete range of gearboxes and servoactuators.
CoVid has modified and will modify many aspects of professional daily life in all areas, including ours. The change in structure will lead to new ways of using, selling, automating and enjoying the services. Attention and reactivity in this phase must be particularly high to catch and anticipate new trends. Smart working extended to all employees thanks to previous investments in portable technology has allowed WITTENSTEIN SPA to carry on, even during the lockdown. The sudden transition to the new mode has not been “traumatic” and has made it possible to maintain high efficiency while limiting costs, without so far resorting to social safety nets. All protocols have been adopted to guarantee employees maximum protection, from personal equipment to organizational measures in the warehouse, workshop and offices.
The lockdown occurred between the first and second quarters so that, looking at the market, we expect a drop in turnover in the following half year. Projected on an annual basis, losses should account for around one third of our turnover. Several sectors are still stuck but others, especially those related to the direct or indirect production of PPE, have benefited from new opportunities. The production of PPE will perhaps impact only in the medium-short term for OEMs, but the other measures that must be taken could open up more long-term prospects, if not real new fields of application. An example? Access controls and social distancing, advanced logistics for e-commerce and all the tasks that can be entrusted to more or less collaborative robots that would have had much slower growth rates without the pandemic. With our state-of-the-art mechanical and mechatronic solutions, we are moving to enter these sectors promptly, also proposing our services to manufacturers who are having to solve advanced automation problems for the first time.
We have gone from customer meetings to smart working videocalls, but once we became familiar with the new means, we found we could advise and support customers even more quickly, even if human contact is missing! The availability of the products remained good and only during the acute phase of the lockdown did the shipments in transit take a few more days. We therefore look to 2020 with the awareness that it will be a year of transition, with inevitably reduced turnover, but with the hope that it will bring new ways of working, producing and automating that will give future growth opportunities.



From difficulties, precious ideas for the future
When digital technologies guarantee continuity - it will be like having a highly experienced Cama engineer
Annalisa and Daniele Bellante, owners of
always on site».
Cama Group (LC), automated high-tech Also with regard to the organizational aspects, the managesecondary packaging systems for the food ment of internal activities and resources, the company reand non-food sectors. sponded promptly, knowing how to draw new and precious suggestions for improvement for the future from the emer«Necessity is the mother of invention - says Daniele gency situation. Bellante with conviction - and it is even more true and nec- Annalisa Bellante spoke on the subject: «After the anessary in these times». A principle that, today more than nouncement of the national lockdown, we immediately ever, is at the heart of Cama’s strategies for restarting. moved to implement all the preventive measures necessary «In terms of the technological proposal - continues the to work in total safety, even before the government protoCEO - we responded to the difficulties generated by the cols were issued, preparing masks and DPI devices, physical pandemic by strengthening digital production services distancing, smart-working, staggered shifts for the canteen with the launch of the Live FAT (Factory Acceptance and common areas. In addition, we took out anti-covid inTesting) program. Last addition to the Cama digital solu- surance for all employees and anyone who was sick, or lived tions portfolio, the new platform offers further remote with hospital workers, those at the greatest risk of infection, functions, such as pre-sale visualization, virtual design were kept at home for a month. and commissioning, in augmented reality, of all our sys- The need to deal with an anomalous situation compared to tems. It is therefore a valuable solution to manage routine has in fact led us to acquire a new awareness and a emerging problems, but also suitable, regardless of the broader vision of real performance within the company. This emergency, to meet the needs of a globalized market. allowed us, also at a managerial level, to make assessments Without a doubt, the launch of the Live FAT service, which and considerations with a view to continuous improvement we had been working on for several months, fell into a of our internal processes. If I have to make a first assess“perfect” moment. In fact, virtualization to be applied to ment of the consequences of the pandemic on our business various aspects of a machine’s life cycle allows overcom- - Bellante continues - I would say that the prospects for ing geographical, economic, technical and, in this case 2020 remain fairly good: From the information in our posalso socio-health obstacles, which weigh on the produc- session it appears that customers active in the key sectors tion landscape. For our customers - Bellante concludes in which we operate (food, personal and home detergency, pharmaceutical), have not suffered serious consequences ... and perhaps some difficulties have arisen from having to unexpectedly accelerate demand. So, for 2020 we expect a slight drop in turnover compared to 2019, which was however exceptionally positive having achieved a growth of 25. We received a good number of orders for April and May, however it is more difficult for us to formulate forecasts on incoming orders in the coming months, and certainly the uncertainty of foreign markets is a critical factor. Let’s think, for example, of Russia and South America, where we are very present and still suffering from a serious situation. Today more than ever, therefore, we think we must proceed with the caution and diligence of “good parents”, trying to combine a forward-looking and courageous vision with a greater foresight in managing resources, focusing on what is necessary to ensure a peaceful company future».
Always connected with the market
Operate in complete safety, and onward with confidence
Alberto Vacchi, President and CEO of IMA, design and production of automatic machines for the process and pack-
aging.
IMA has remained in business since the production of automatic machines and related services are essential for the food and pharmaceutical supply chains. «During the lockdown period - explains Alberto Vacchi - the Group has made every effort to respond to the requests of its customers all over the world, in full compliance with the regulations and prescriptions issued to prevent contagion. IMA launched “Stay Connect!” the platform which, within a single touchpoint, enhances and makes the entire range of digital products created by the Group easily accessible. In addition to the support represented by connected machines to remotely monitor the state of health of the systems, the platform offers products for technical assistance, augmented and virtual reality, applications for digital documentation, training in their various forms. In short, a single platform guarantees an interaction never achieved before with machines and systems. We also achieved good results and experimented with new relationships remotely with customers with the 500 people in smart working... An experience that will also be useful in the future». Since the early stages of the Covid-19 emergency, the company has promptly taken a series of actions to ensure safety conditions at work. «Our priority - underlines Vacchi - was in fact protecting the health of our employees, while ensuring continuity of production in total safety».
Full operation was also ensured by a consolidated and efficient subcontracting network. «IMA’s approach to the supply chain has always been innovative and, over time, we have perfected an unconventional model. The scheme has evolved with the participation of IMA in the share capital of the most strategic suppliers, allowing us to better face the recent challenges. Moreover, a model that is perfectly consistent with the logic of Industry 4.0». And precisely in the wake of the logical ones, the choices and technological investments undertaken have proved useful to face the situation. «Investments in Research and Development (53.9 million euros in 2019) proved to be very useful, as was the acquisition policy. In this period IMA has carried out with extreme speed, thanks to the subsidiary Teknoweb acquired in 2015, the design and manufacture of an automatic machine for the production of surgical masks. The IMA Face 400 is an innovative machine, to which the whole company has worked with pride to make a contribution of collective interest. This is an important technical development which confirms, once again, the great industrial and engineering flexibility that characterizes the Group. The Civil Defense has chosen this machine which is attracting a lot of interest on the international market».
In addition to the operational measures put in place, the economic and financial actions taken since the first moments of the Covid-19 emergency have also been designed to mitigate their effects. «The Group’s results in the first quarter reflect the economic and financial impact of the emergency - admits Vacchi - yet the solidity of IMA, combined with the great innovative capacity that distinguishes the Group, will allow us to face the next phases of the emergency with optimism, better planning this period of high uncertainty. The consistency of the order backlog (908.3 million euros at March 31, 2020) and the number of projects currently being negotiated, including significant amounts, represent a positive sign even if they do not provide total visibility over the entire year. We are led to look with confidence at the rest of the year, although the emergency situation continues to involve not only Italy, but the whole world. If the signals indicated above will be confirmed during the year - concludes Vacchi - we believe that the Group can achieve a result that is not significantly lower than in the previous year».
Ogni cosa ha il suo packaging Tutti hanno…
The Voice of Italian Packaging
Webmagazine by ItaliaImballaggio