About DB3
Founded in 1883, DB3 Group is an award-winning, dynamic practice consisting of DB3 Architecture & Design, DB3 Building Services Engineering, DB3 Net Zero, DB3 Professional Services, and Formation 3D.
DB3 Group has seven studios across the UK including in Leeds, London, Birmingham, Manchester, Glasgow, Cardiff and Aberystwyth, so we are never too far away from your project.
Renowned for our quality design and technical delivery, we have long standing relationships with some of the biggest global brands across private and public market sectors.
From architectural vision to the completed build, we provide multi-disciplinary expertise aimed at meeting the diverse needs of our client base. We embrace the latest technology, including Building Information Modelling (BIM), to assist in our process and operations for design, visualisation, design team co-ordination and more.
We maintain a focus on not only delivering the project on time, with exceptional quality and within cost, but also in ensuring long term value is designed into facilities to ensure that they are easy and safe to operate, sustainable, minimise energy use and are cost effective to maintain.
Our dedicated team of experienced Architects, Project Managers, Building Services Engineers, Interior Designers and Surveyors provide a quality service regardless of project value, size or complexity, to deliver the best for our clients. Working collaboratively, we aspire to make this an enjoyable process and build relationships which result in us returning to work for the same clients on future projects.
SECTORS
Commercial
Conservation & Heritage
Education
Energy & Waste
Healthcare
Hospitality
Industrial & Manufacturing
Retail
Residential
Science & Labs
Sports & Leisure
EXPERTISE
Architecture
Passivhaus Design
Urban Design
Visualisation
Principal Designer
NEC Supervisor
Building Services Engineering
Building Tomorrow’s Food Facilities
At DB3, we design smart, sustainable spaces that drive productivity, quality, and compliance across the Food & Drink Processing & Manufacturing sector. Our expertise spans production methods like continuous and batch processing, modular builds, and scalable layouts. We work across diverse sectors, from dairy and poultry processing to brewing, baking, and beverage production, integrating efficient workflows, robust compliance, and advanced hygiene systems tailored to each process.
With clients like Coca-Cola, Nestlé, Innocent Foods, Marshall’s Chunky Chicken, and Country Food Group, our projects optimise every stage - from raw material intake and processing through to packaging and distribution - delivering production environments that meet stringent industry standards.

Long-standing Relationship
Location: UK-Wide
Expertise Area: Architecture
PROJECT DOVE
DB3 acted as Architect and Design Team Leader for a new build freeze-dried coffee production facility on behalf of Nestlé.
We worked alongside a multinational team of process engineers from the inception of the project to develop innovative new technology and research facilities, integrating complex manufacturing process systems with building services and large scale building envelope design. As lead designers we co-ordinated the design and project team, together with Nestle’s own inhouse engineering staff, to develop a total of 11 different buildings. Careful phasing was developed to allow the installation of cutting edge process equipment specifically developed for the project. We co-ordinated the input of the design team through an online common data environment, 4 Projects. Here all design team members, client and contractor could store and exchange information.
FAWDON
We collaborated closely with Nestlé to create a pilot sustainable, low-carbon manufacturing site. Our brief was to guide Nestlé on their sustainability journey and design a ‘look and feel’ that visually expresses a commitment to green practices. To achieve this, we developed a comprehensive masterplan and architectural designs.
Biodiversity was at the heart of the project, with a nature walk through the facility to enrich the environment and experience for visitors and employees alike. Along the perimeter, a west-east visitor impact corridor showcases key sustainable features, such as a new green wall, biomass boiler, and wildlife corridor, highlighting Nestlé’s commitment to ecological responsibility. These sustainable upgrades contribute significantly to energy and water efficiency and support waste reduction efforts, including an on-site anaerobic digestion plant that minimises landfill waste, establishing a new standard for green manufacturing.

HALIFAX
DB3 was appointed as the Architect and Interior Designer to reimagine the gatehouse, security, client reception, and back-of-house office areas at Nestlé’s Halifax site. The project focused on creating a refreshed, high-quality entrance that reflects Nestlé’s standards for both staff and visitors. Given the need to keep the factory fully operational, special consideration was given to maintaining continuous access throughout construction.
DB3 collaborated closely with the on-site team to develop practical and effective solutions tailored to this complex, high-traffic project. This approach ensured a seamless transformation of the site’s main entrance, balancing functionality with an upgraded visual identity for the brand.
QUALITY ASSURANCE CENTRE
DB3 was appointed to lead the refurbishment and extension of the NQAC labs in York, ensuring the labs remained fully operational throughout the project. The scope included a comprehensive upgrade of services and additional plant to meet the latest standards for testing labs. This involved reconfiguring and adapting the testing labs and technical offices, as well as updating the reception and entrance areas.
To support new climate control and filtration systems, the roof was restructured and new plant areas were installed, modernising the facility to meet stringent environmental requirements. DB3 managed all design and project coordination through each phase, from planning and health and safety compliance to tender and delivery under a traditional contract.
The quality labs remained in continuous use, so all alterations were completed in a food-safe, hygienic environment, blending seamlessly with existing facilities while laying the groundwork for future upgrades.
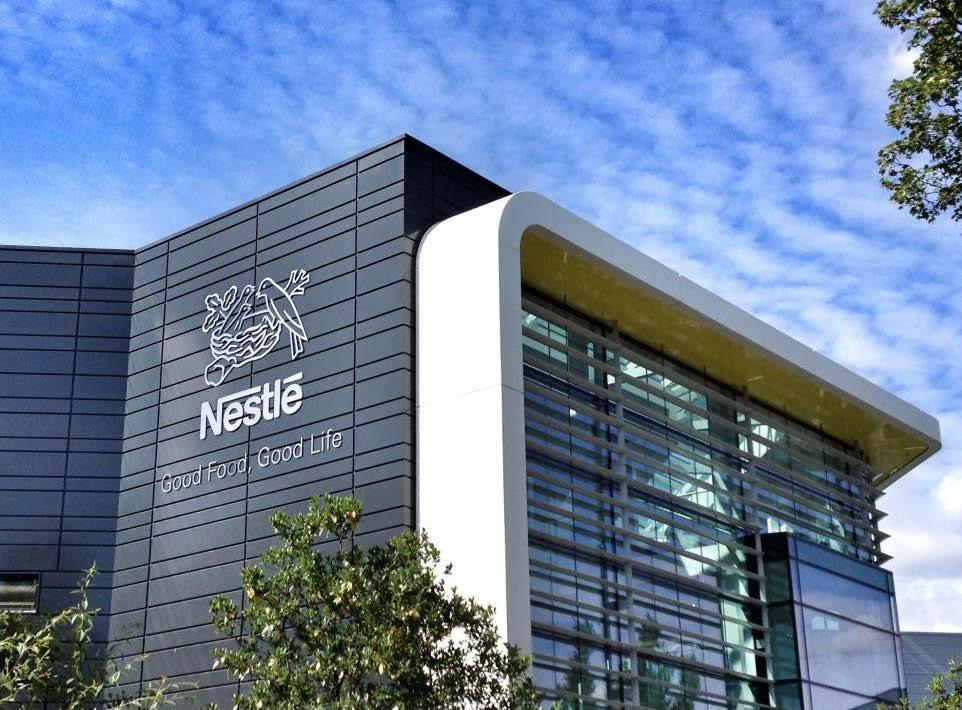
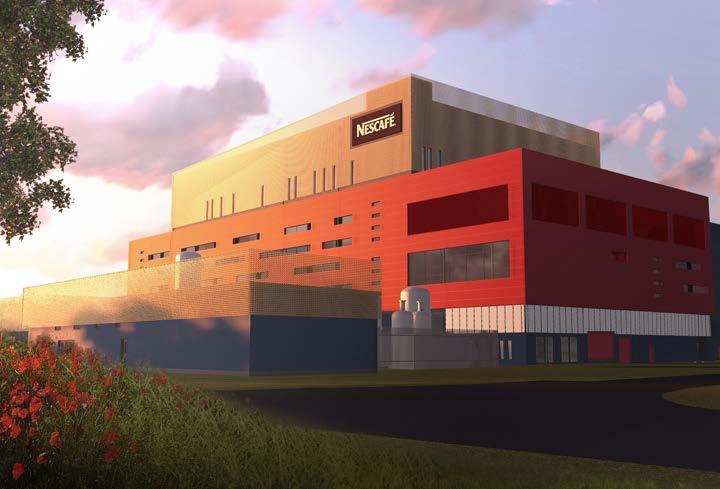
COCA COLA
Long-standing Relationship
Location: UK-Wide
Expertise Area: Architecture
ASRS SIDCUP
DB3 was appointed to deliver a new automated warehouse facility within the existing Coca-Cola site at Sidcup. The new automated facility houses around 26,000 pallets and has a fully integrated clad rack system and MHE linking into the dispatch area and existing production lines.
The scheme includes a 40m high ASRS building, new distribution building and a link warehouse to the main production halls. A new gatehouse and completely re-designed goods yard and access, alongside flood elevation works, also form part of the work. The project has been carefully designed to incorporate the requirements for logistics and functionality.
DB3 dealt with the full planning applications to Bexley Council and London City Council, requiring complex negotiations and coordination of all supporting information during a public consultation. Visuals and clear concise information were required from the outset.
A high degree of process integration was required to ensure the MHE works across all levels and is fully accessible. The link warehouse contains MHE multi-level change towers to allow feeds from differing lines directly into the ASRS which contains seven fully automated cranes. This links to the distribution warehouse and feeds directly to the loading docks for rear loading and side loading as required. Due to its complexity and advanced engineering, viewing galleries have also been incorporated. DB3 played a key role in evaluating tenders and MHE queries to ensure deliverability of the project.
ASRS WAKEFIELD
DB3 was appointed to provide architectural and lead design services for a ten-story Automated Storage Retrieval System (ASRS) at the CocaCola Wakefield site. The scheme includes a sitewide refurbishment as well as a raw materials warehouse extension, sugar dissolving plant and citric tanks enclosure, ingredients store canopy, new canning line and walk on ceilings.
Driven by Coca-Cola’s expanding storage needs,
the project aims to enhance on-site automated warehousing capacity, reducing dependence on off-site storage.
Coordinating with an active facility, DB3 meticulously modelled the existing structures despite limited initial data, addressing physical constraints and bridging over existing site structures. Key challenges included a complex fire strategy to ensure compliance for the ASRS expansion, which we navigated with proactive solutions and workshops with fire engineers.
Our experience in live-site industrial projects and strong knowledge of British Standards and building regulations enabled efficient solutions that secure specialised equipment and technology.
ASRS EAST KILBRIDE
DB3 was appointed as the Architect to reconfigure an existing Automated Storage and Retrieval System (ASRS) in East Kilbride. The scope of work includes designing a new waste facility canopy, reimagining loading bays, adding a cold storage facility, and refurbishing office spaces to create a more staff-friendly environment.
With extensive experience in live-site industrial projects, DB3 leverages in-depth knowledge of British Standards and building regulations to deliver efficient, tailored solutions that protect specialised equipment and technology.
DISTRIBUTION CENTRES
DB3 have worked as Architects for Coca Cola’s UK distribution facilities for over 20 years. We provide a range of services that aim to optimise the functionality, efficiency, and aesthetic appeal of these facilities.
Collaborating closely with Coca Cola’s logistics team, helps us prioritise their specific requirements and operations. This includes insights into the volume and nature of the products being distributed, storage needs, material handling systems, and traffic flow patterns. By understanding the unique demands
of Coca Cola’s distribution network, we can design facilities that are tailor-made to meet their specific needs and operational processes. We focus on creating efficient spaces that optimise storage capacity, streamline movement of goods, and promote smooth workflow. This includes allocating areas for storage, loading and unloading zones, processing areas, office spaces, and staff facilities. Our goals is to design a layout that minimises congestion, enables efficient movement of products during distribution, to enhance operational productivity & reduce costs.

Throughout the process, we adhere to industry standards, local regulations, and sustainability principles. We ensure compliance with building codes, health and safety regulations, and environmental requirements. Designing sustainable features, including energy-efficient lighting systems, water management strategies, and waste reduction measures.
DB3 collaborates with contractors and suppliers to ensure seamless execution.
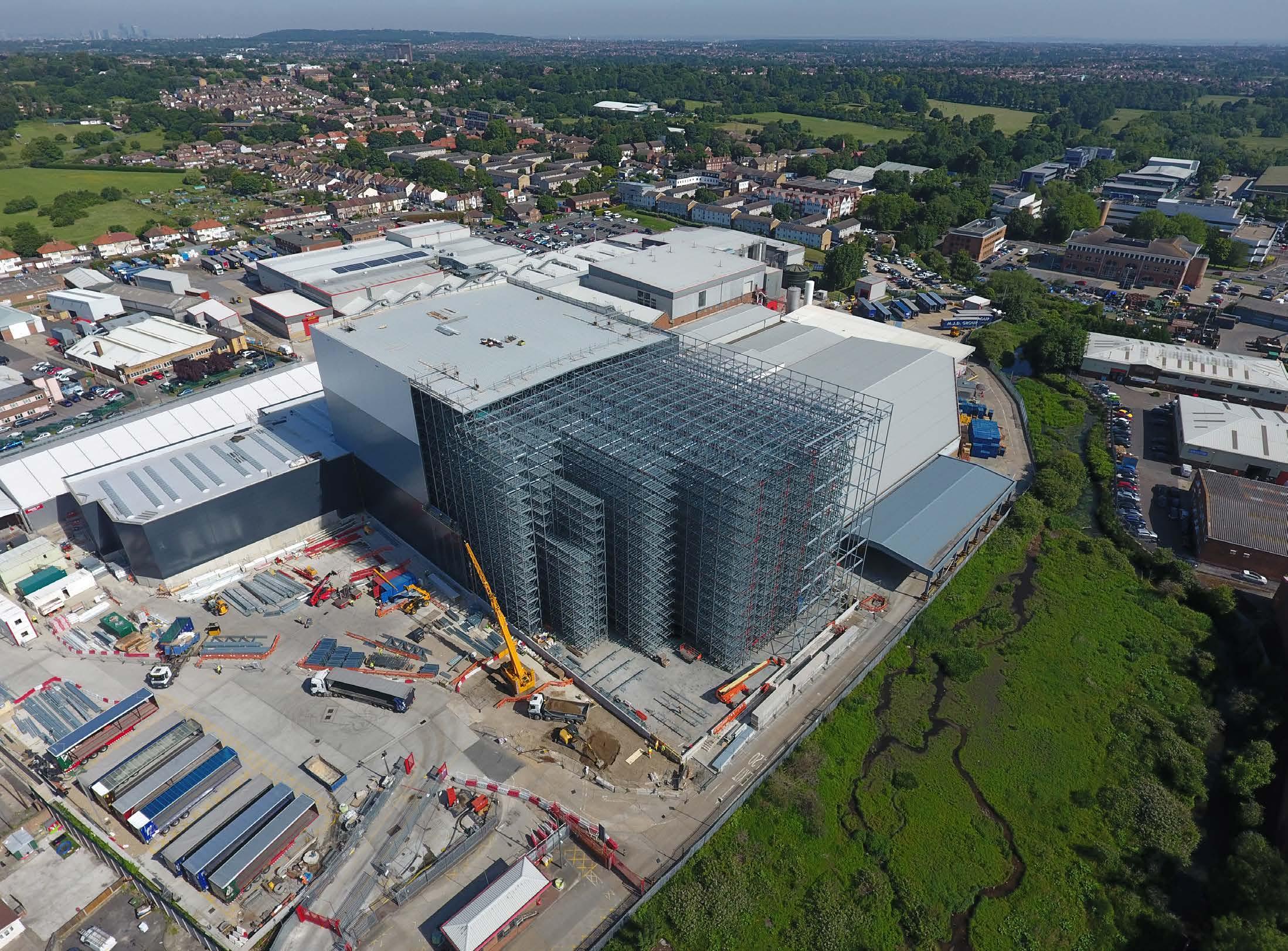

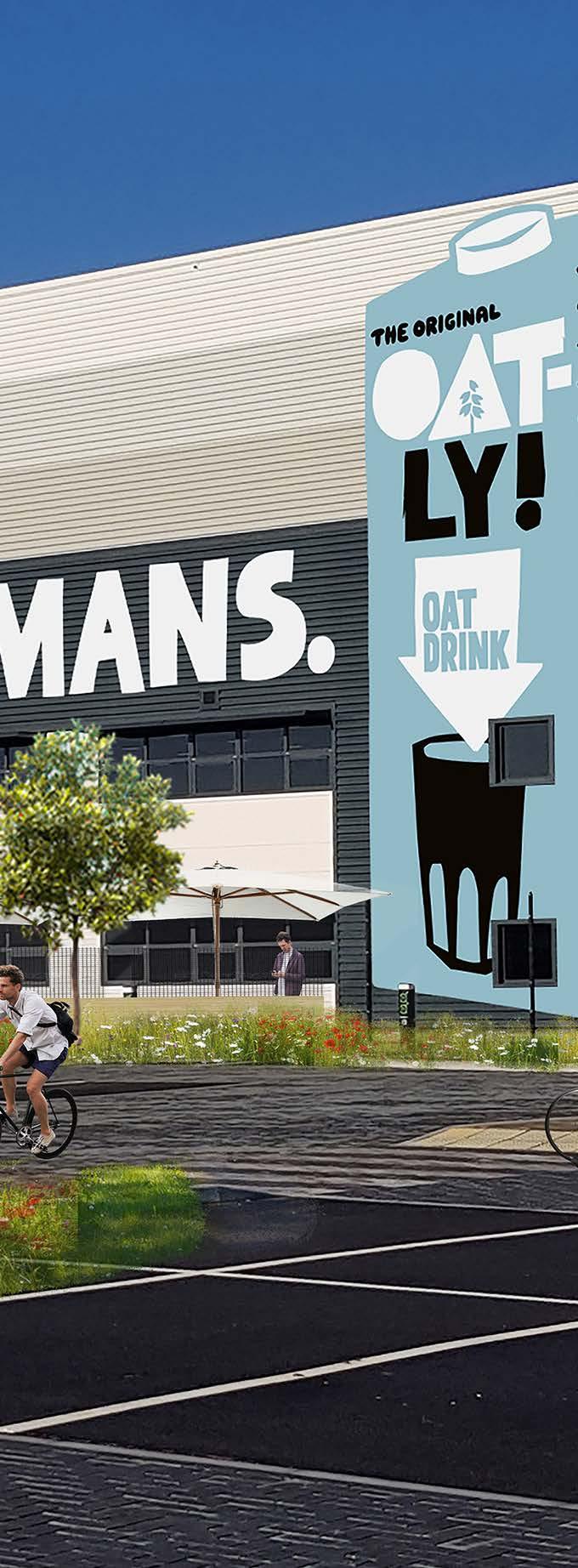
INTEGRATED FOOD PROJECTS
Oatly’s First UK Factory
Location: UK-Wide
Expertise Area: Architecture, Building Services Engineering, Principal Designer
DB3 supported Oatly, the alternative dairy producer, with site selection and design for a new UK manufacturing facility. After evaluating various locations and considering new builds versus site enhancements, Oatly chose an existing site in Peterborough. DB3 acted as Architect, Building Services Design Engineer, and Principal Designer to redevelop a 35,000 sqm warehouse into a sustainable, high-capacity facility. The design scope included production lines, a test kitchen, labs, an ingredients store, HVAC systems, and employee amenities such as an onsite gym and faith room. The facility aimed to launch with a production capacity of 300 million litres per year, with future expansion to 450 million litres.
Oatly’s primary objective was to establish a sustainable, future-proof UK factory. A senior sustainability advisor reviewed each design stage, ensuring the facility aligned with Oatly’s commitment to environmental stewardship. Employee wellbeing was also emphasised, with designs following WELL standards to create a health-oriented workplace.
Incorporating production lines and fire compartmentation within the existing structure proved challenging. Extensive consultations with fire engineers and local authorities led to a compliant strategy that addressed site constraints and fire safety requirements. Another challenge involved designing sprinkler systems to accommodate equipment configurations, requiring substantial modifications and new valves and piping. DB3 also managed the integration of HVAC, ammonia plant, and process equipment within the site’s constraints.
DB3 leveraged its expertise to deliver responsive, compliant design solutions, emphasising fire compartmentation, safety, and phased work processes to support seamless equipment installation. The new facility design included upgraded fire suppression, electrical systems, and drainage, with structural reinforcements for hygiene areas. Additionally, the project enhanced employee welfare areas, setting a high standard for work environments in manufacturing.
WARP SNACKS
New Production Line
Location: Nuneaton, West Midlands
Expertise Area: Architecture, Building Services Engineering
DB3 served as the Project Architect for Warp Snacks’ latest expansion, introducing a new popcorn production line within their live facility. The design emphasised consistent access to the main warehouse, with DB3 working closely with the on-site team to develop practical, site-specific solutions.
The project involved constructing a 12-metre-high hygienic facility to accommodate the production line, an ingredients store, a cooking area, and HVAC systems. This facility was compartmentalised from other warehouse areas in compliance with BS9999 standards. To streamline the process, construction was phased, allowing for the coordinated installation of process equipment and facility build-out. New rapid-rise doors and fire
shutters were installed between the warehouse and production areas, while existing openings were filled, and new ones were added to the façade to facilitate material deliveries and future use.
Additionally, the existing stair core was removed, and a single-storey enclosure was created. A new mechanical HVAC system, equipped with kitchen extraction, was implemented to meet BS9999 requirements. Fire suppression systems and an upgraded electrical installation were added to meet the specific needs of the production line. New drainage systems and structural reinforcements were installed to support the hygiene box and other new openings in the existing building.
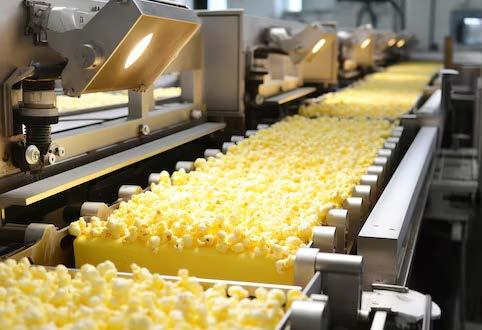
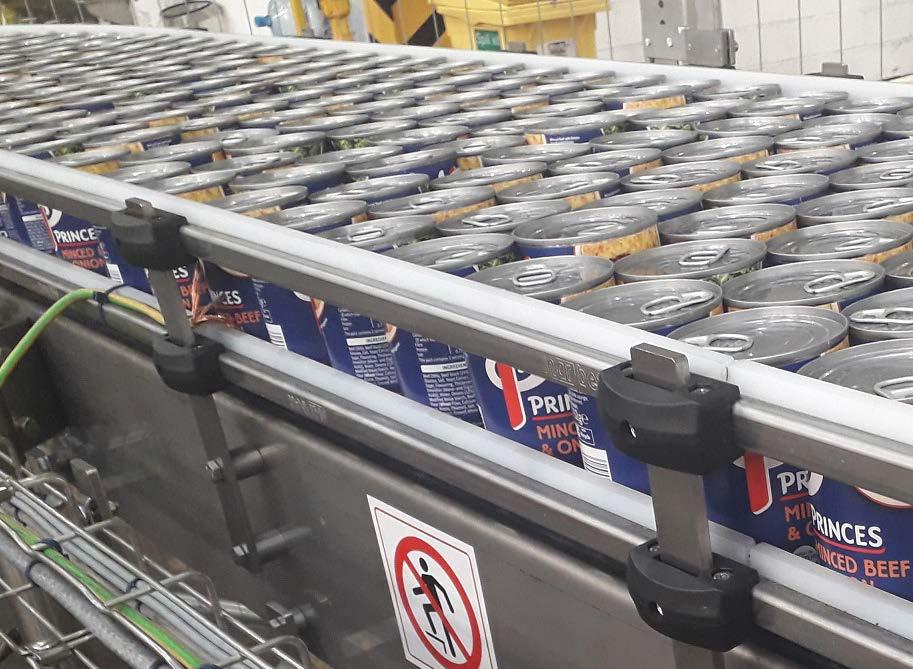
PRINCESS FOODS
Warehousing & Pea Processing Plant
Location: UK-wide
Expertise Area: Building Services Engineering
DB3 were engaged as the Building Services Engineers for the Princes Foods raw materials warehouse and pea processing plant at Long Sutton. This facility includes cold and chilled storage areas, offices, and loading bays, which are essential to its operations. Flexible shuttle racking systems facilitate versatile raw material storage, while dedicated areas for cooking, preparation, and logistical management - such as HGV and forklift loading bays - ensure smooth operation. A high-load mezzanine further optimises space for future expansion.

DB3 provided the MEP design for the building, encompassing utilities, drainage, heating, ventilation, lighting, power and data, CCTV, fire alarms, and additional control systems. As part of Princes’ £80 million investment in the site, the warehouse and processing plant were developed to integrate seamlessly with nearby buildings, minimising disruption to ongoing production. It adheres to strict environmental and food hygiene standards, supporting a highly regulated food processing environment.
HAYWOOD & PADGETT
Bakery Facilities
Location: Barnsley, South Yorkshire
Expertise Area: Architecture
The project involved the alteration and extension of the existing scone bakery facility, which included production areas, warehouses, and office spaces, as well as staff welfare and engineers’ workshops. DB3 was appointed as the Architect for all stages of the project, from initial design through planning to completion.
Additionally, DB3 was engaged to design a new bakery facility and head office on the site for an alternative product range called “Nib Nibs,” developed as part of the overall masterplan project.
The scope of the project included creating updated layouts for production lines, incorporating new equipment, and ensuring efficient workflows while adhering to high industry standards and food safety requirements. The refurbishment also aimed to optimise space utilisation and energy efficiency.
DB3 re-engineered the site layout, introducing a one-way circulation route around the bakery for HGVs to enhance safety.
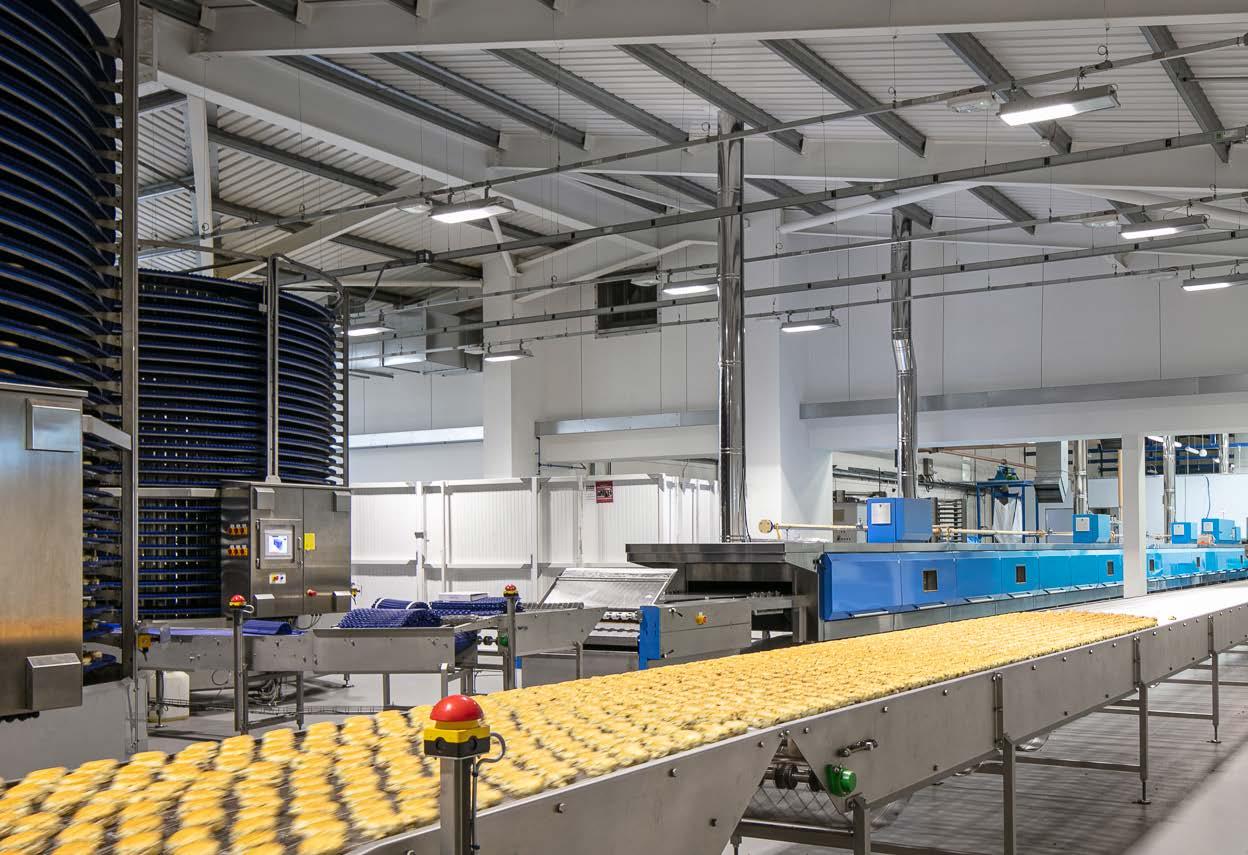
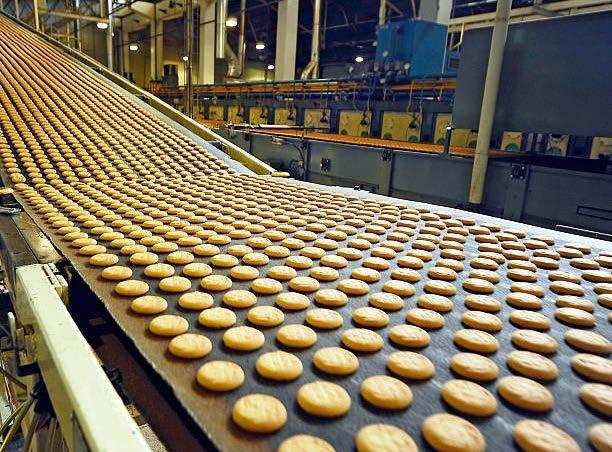
Expansion Project
Location: Bradford, West Yorkshire
Expertise Area: Architecture
DB3 has been appointed as the Architect for a significant extension and refurbishment of CSM Bakery’s Bradford factory, which produces ‘mini-bite’ baked goods for the UK food market. This new facility enables CSM to efficiently distribute an extensive range of bakery products and ingredients, serving artisan and industrial bakeries, as well as in-store and out-of-home markets.
The project scope for this food production unit includes a comprehensive upgrade, incorporating a new drainage system, complete mechanical and

electrical installations, a steel mezzanine floor, and an extensive refurbishment throughout the facility. Key updates include an internal upgrade to the existing facility, a redesigned entrance, refurbishment of the main building elevations, a new internal layout for ingredient handling, and modernised fallow areas. Additionally, a walkon ceiling has been added above fallow areas, with new walls, expanded washrooms, and the demolition of the previous nut storage area to increase operational space.
WALKERS
Distribution Centre
Location: Peterlee, County Durham
Expertise: Architecture
High-bay Warehouse at Walkers Snack Foods (Distribution) Ltd. This project allowed the business to optimise its supply chain and increase the local storage capacity within its logistics network. The phased investment proposal was for a new automated storage warehouse built to the rear of the existing distribution centre followed by a new first floor office extension over the existing warehouse offices providing training rooms, meeting rooms and IT rooms.
The building is required to hold an increasing production volume and growing variety of product ranges. This is a highly automated warehouse with a capability to hold a further 9,500 pallets of product ready for sorting, order picking and delivery to our customers.
This initiative reduces inefficient vehicle movements between our existing Distribution Centres and the periodic requirement for off site third party storage and the associated intermediate vehicle movements.
Several options were considered to make this significant investment either at Peterlee, at one of their other sites or even at a new location, but after careful analysis they proposed to expand the Peterlee Regional Distribution Centre site.
Detailed consultation and planning carefully developed our proposal that created a state of the art logistics facility, taking full advantage of modern technology and operating methods to minimise the environmental impact both locally and nationally.
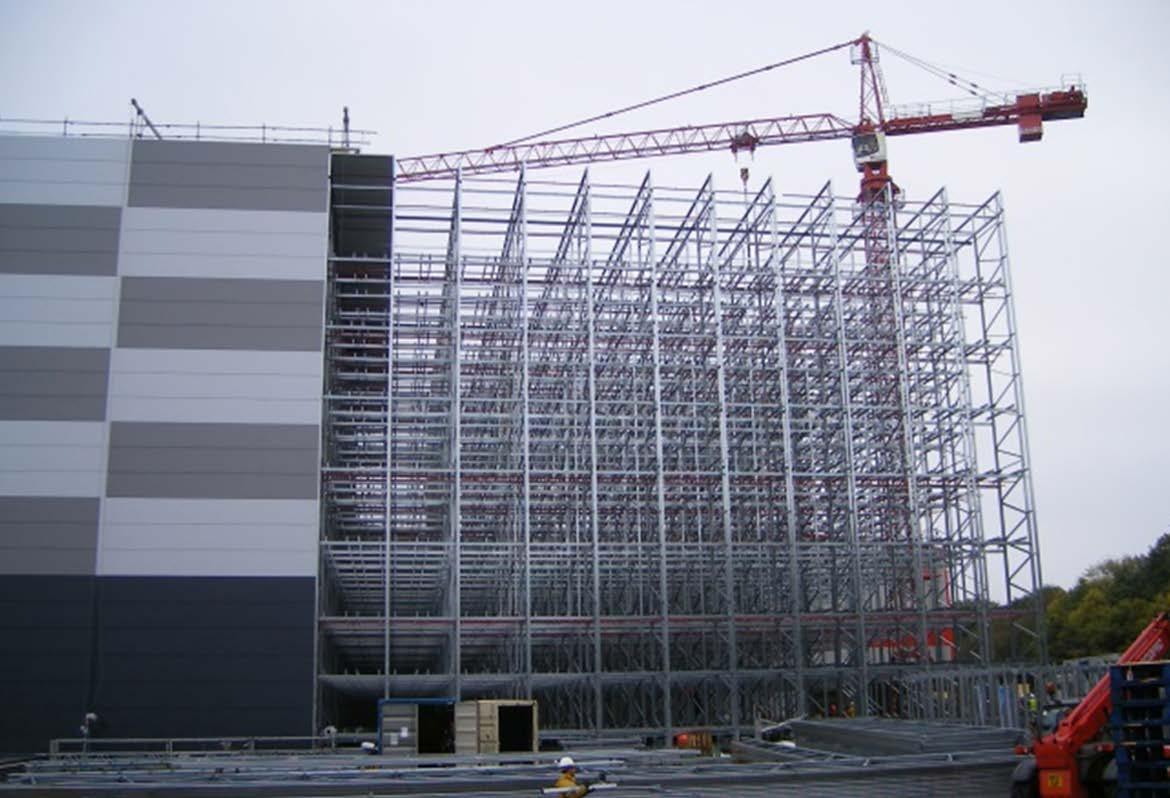
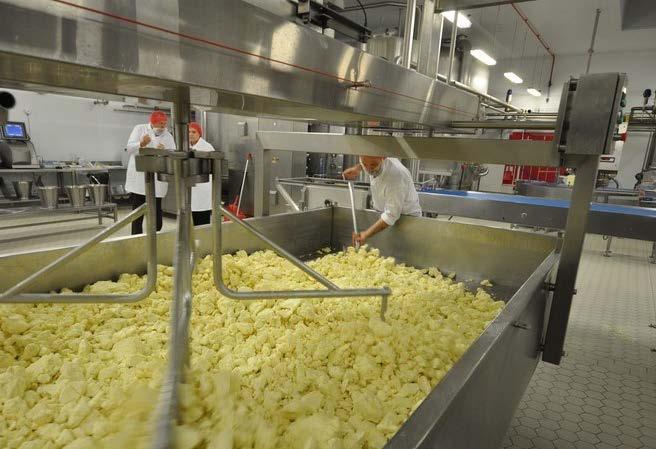
Location: Caernarfon, Gwynedd
Expertise Area: Architecture, Principal Designer
DB3 has been appointed as the architect and principal designer for the £26 million South Caernarfon Creameries expansion project. This development will enhance the existing cheese production facility with two new buildings, as well as the extension and refurbishment of an existing structure.
Given the challenges of working on a live site, meticulous planning has been essential, along with a flexible approach to accommodating the needs of both the client and contractors.
The scale and duration of the project have led to necessary adjustments throughout construction, allowing us to respond to evolving requirements. Our team has adapted design modifications and coordinated with all stakeholders to ensure smooth progress without delays, delivering a facility that meets the highest standards in both functionality and safety.

INTEGRATED FOOD PROJECTS LIMITED THIS
Location: Chiswick, London
Expertise Area: Architecture, Principal Designer
DB3 is proud to have been appointed as architect and principal designer for the innovative plantbased food brand, THIS. Engaging closely with all stakeholders throughout the project, we guided the design and construction process across RIBA stages 2-4 to ensure the vision was fully realised. Located within a conservation area, this project
involves a series of thoughtful upgrade works, including a new product development suite and an inviting front-of-house space. These enhancements not only support the brand’s ambitious growth but also respect and contribute to the character of the surrounding area.
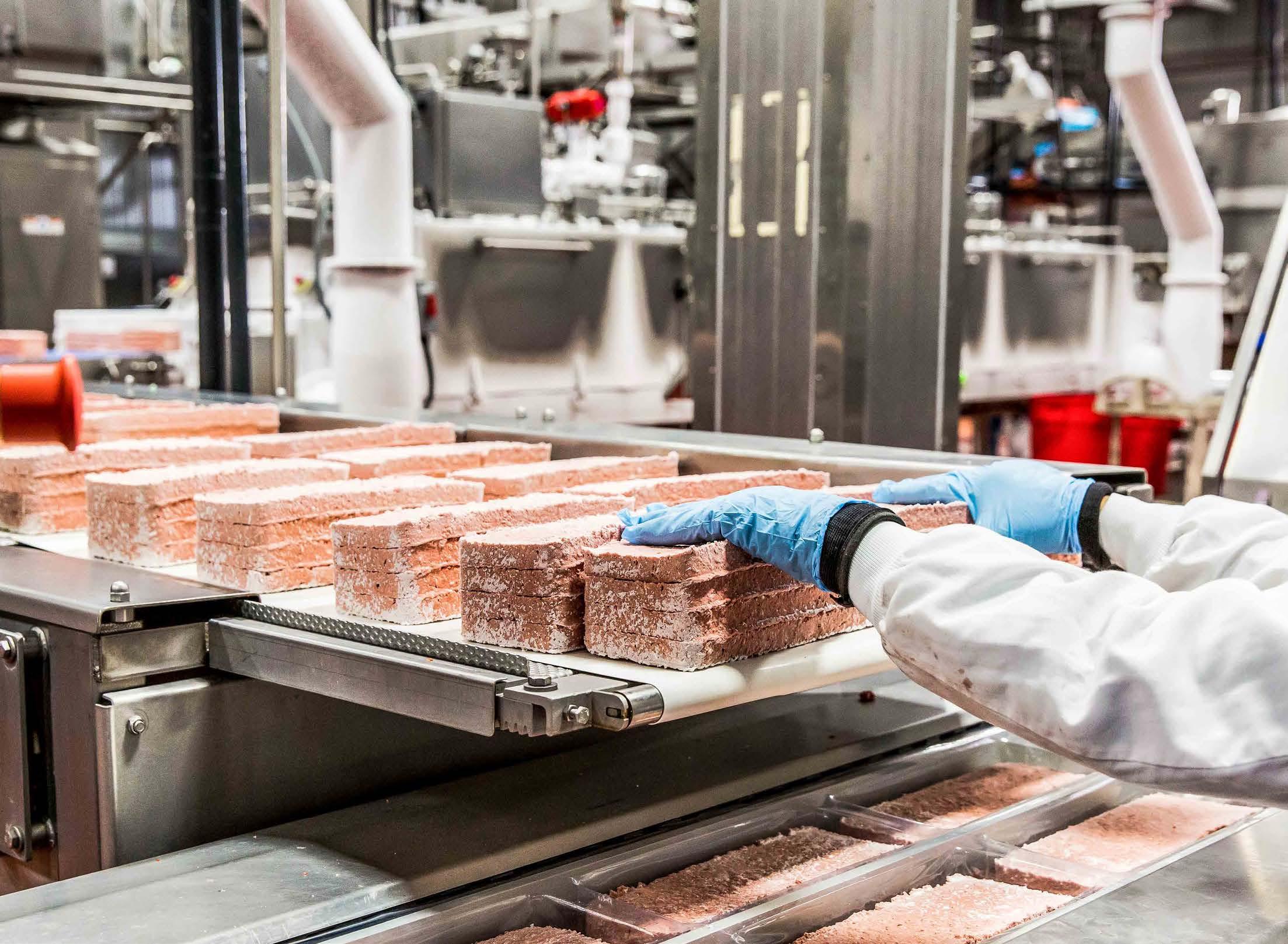
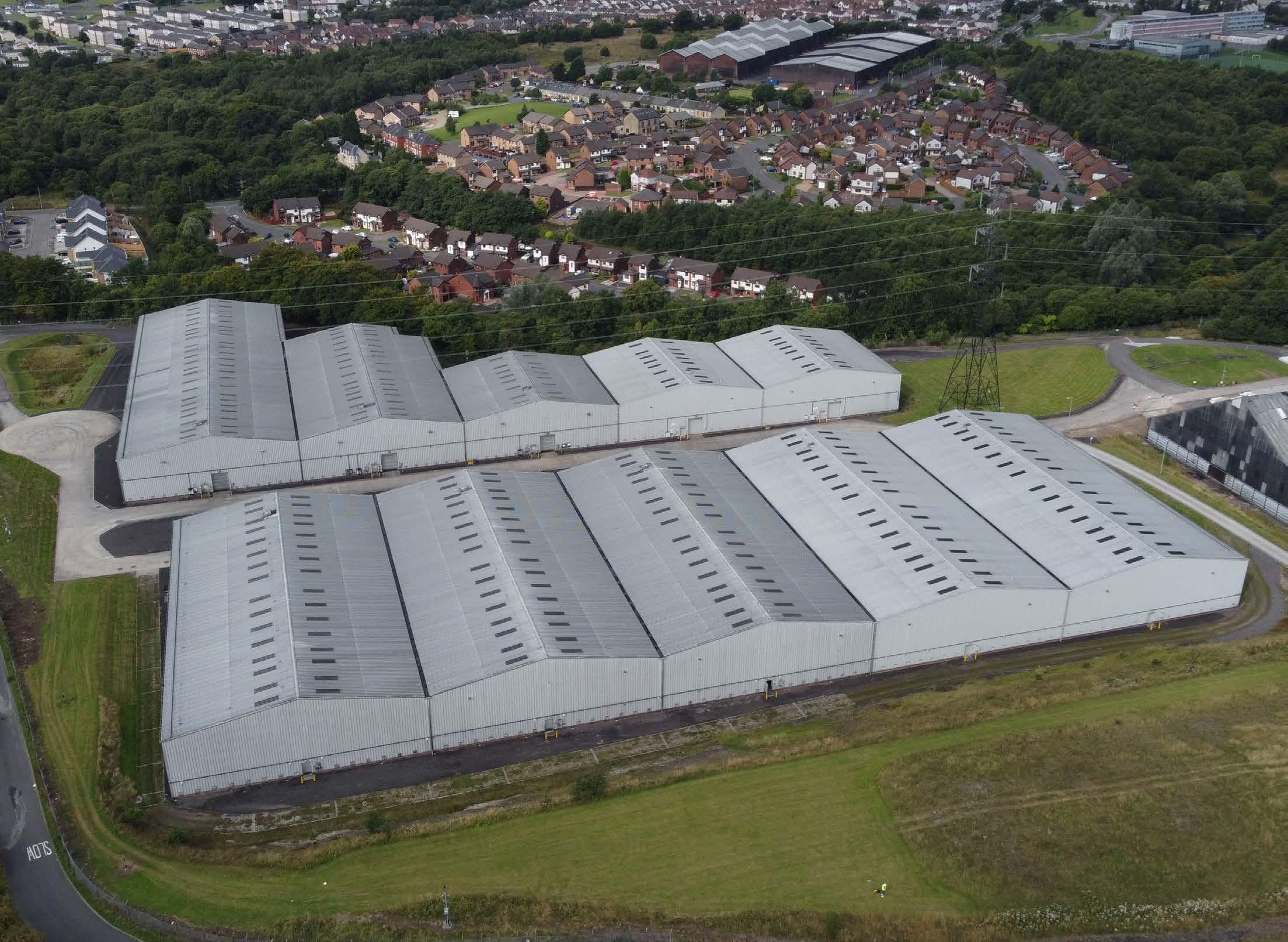
INVER HOUSE DISTILLERIES
Bonded Warehouse Facility
Location: Airdrie, North Lanarkshire
Expertise Area: Architecture
We have a long-standing relationship with Inver House Distillers (IHD). Initially being appointed in 2017 to deliver 18 bonded warehouses for the storage of cask whisky at their site in Airdrie, our successful relationship has continued over a 7-year period with work including the production of IHD’s masterplan for the site, and alterations to the existing warehousing to bring up to current regulations.
Our team are currently delivering 16 new bonded warehouses, each bond being 1000sqm. We engaged with IHD stakeholders to establish a clear brief and maximised the potential of the site ensuring maximum profitability from each facility, with optimised storage capacity.
Following the issue of recent new HSE advisory
notices relating to ventilation requirements within bonded warehouses, DB3 Group have incorporated the relevant solutions within our current design, including adjustable louvres. The louvres enable our client to make necessary adjustments to ensure the internal environment is compliant with potentially varying regulations whilst safeguarding evaporation rates.
Our value engineering exercise resulted in advising IHD on best practice with regard to managing condensation, which also provided a significant saving to our client.
Ecological planning challenges for large storage buildings were met with compensatory planting across the site.
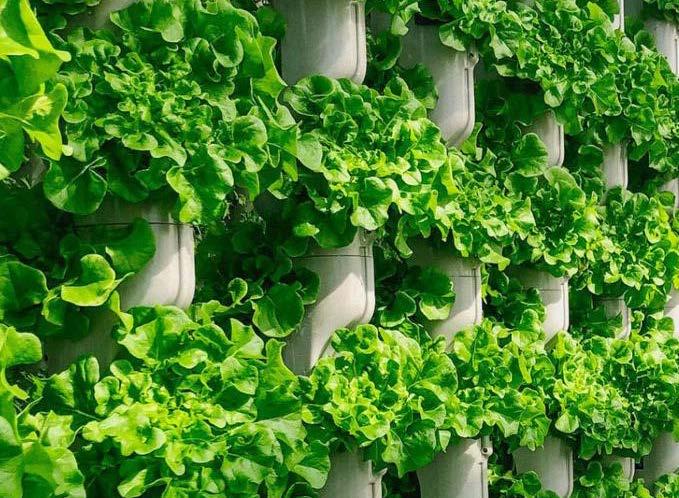
GROWUP FARMS
Vertical Farm
Location: Sandwich, Kent
Expertise Area: Architecture
GrowUp Farms comissioned a cutting-edge vertical farm for lettuce production, with DB3 being appointed to design the internal layout and ancillary administration spaces.
By the time we joined the project, the shell structure and stair cores were already under construction, with layouts defined by the contractor. Working within these parameters and a challenging timeline, we led the design process to develop an efficient, functional, and welcoming internal layout tailored to the client’s needs.
The two-story administration space was designed to support both factory and office staff while accommodating specific client requirements. The ground floor features changing facilities, a driver’s breakroom, and a client-facing atrium and reception area.
On the first floor, we created a variety of hotdesking office spaces, a client-facing product test kitchen, a recreational area with kitchen facilities, meeting rooms, private offices, and a control room overseeing factory operations.
This project presented unique challenges, including working within a pre-existing shell and core design, managing a tight budget, and addressing the client’s limited construction process knowledge. Additionally, a key milestone required that the ground floor be completed within a set time, necessitating a streamlined and accelerated design process to meet this deadline. DB3’s adaptability and efficiency were essential in ensuring the project progressed smoothly while meeting the high standards set by GrowUp Farms.
INNOCENT DRINKS
Carbon Neutral Bottling Plant
Location: Netherlands
Expertise Area: Architecture
DB3 was appointed by Innocent Drinks to provide architectural services for a new carbon-neutral bottling plant in the Netherlands. Working in collaboration with Integrated Food Projects, we developed a concept design and an evaluation study, which included a detailed delivery programme. Our scope also covered cost-benefit analysis and the feasibility of establishing a new manufacturing facility.
This €223 million development is projected to produce approximately 400 million bottles of chilled juices and smoothies annually, with products set for distribution across 17 European countries.

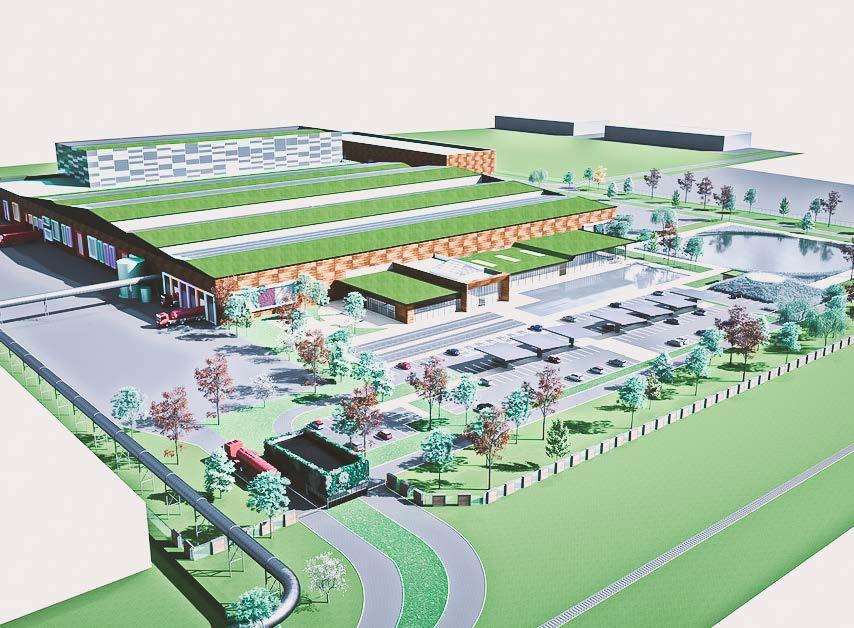
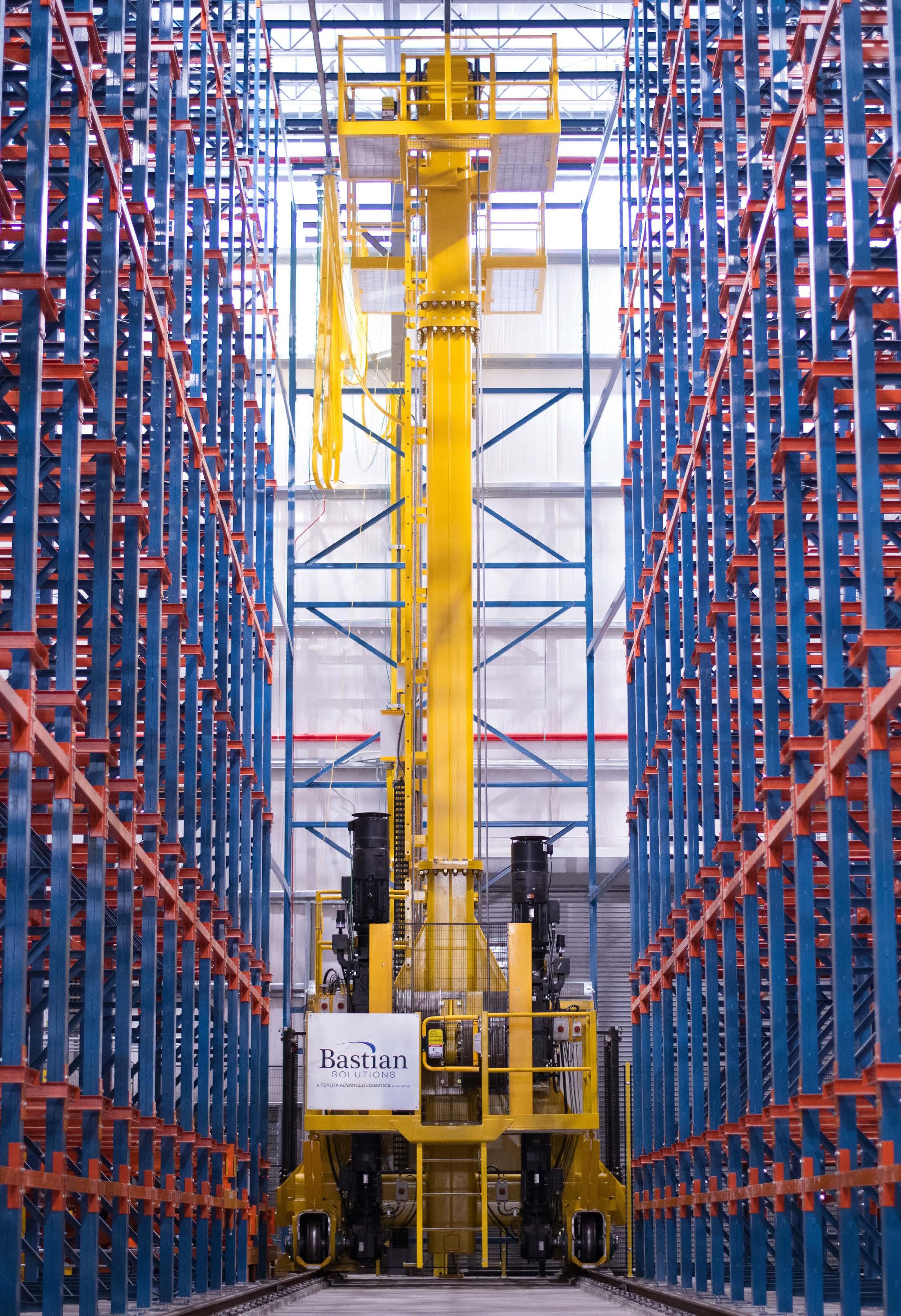
CONFIDENTIAL CLIENT
ASRS
Location: Scotland
Expertise Area: Architecture
We are collaborating with a Scottish whisky distillery to design and build an Automated Storage and Retrieval System (ASRS) as an extension to their existing distillery and processing plant. The project covers all RIBA Stages, with our initial work focusing on fire safety in isolation.
The need for the ASRS arose from inefficiencies in the distillery’s current storage system, which relies on manual operations. The new ASRS will introduce automated racking to streamline stock management, improve handling and rotation efficiency, and minimise operational delays. Once complete, the ASRS facility will accommodate up to 36,000 pallets—equivalent to around 46 million bottles of whisky.
One of the key challenges in this project has been the client’s requirement for a 10,000-square-metre storage facility. Scottish Technical Standards limit storage to 1,000 square metres for unsprinklered areas and 2,000 square metres for sprinklered areas, making our project scope non-compliant under typical standards. To navigate this regulatory complexity, we engaged early with the Building Control Authority and Scottish Fire and Rescue Service. Together, we adopted a “red, amber, green” approach to categorising compliance:
Red: Standards we could not fully comply with and would require specific mitigations.
Amber: Standards that we could work towards meeting through modifications with the ASRS manufacturer.
Green: Elements already compliant with regulations.

Our fire safety strategy highlighted a gap in existing regulations. As a bonded warehouse storing goods under controlled conditions with limited foot traffic, it is not distinguished from more general-purpose warehouses in the regulations. Bonded facilities like this ASRS have distinct characteristics as highly controlled environments with restricted access.
To address this, we designed an enhanced sprinkler system tailored to the facility’s 30-metre height. Additionally, we analysed how smoke detection systems interact with these unique storage conditions, implementing customised fire safety measures to mitigate risks.
The facility layout itself introduces several innovations. We incorporated a north-to-south fire access corridor to enhance emergency response, as well as both wet and dry mains for fire services. Escape routes are designed with a two-hour fire rating, and the external façade includes special treatments to further support fire safety and compliance.
This approach allows us to balance the client’s operational requirements with the highest safety standards, setting a precedent for advanced storage solutions in the spirits industry.
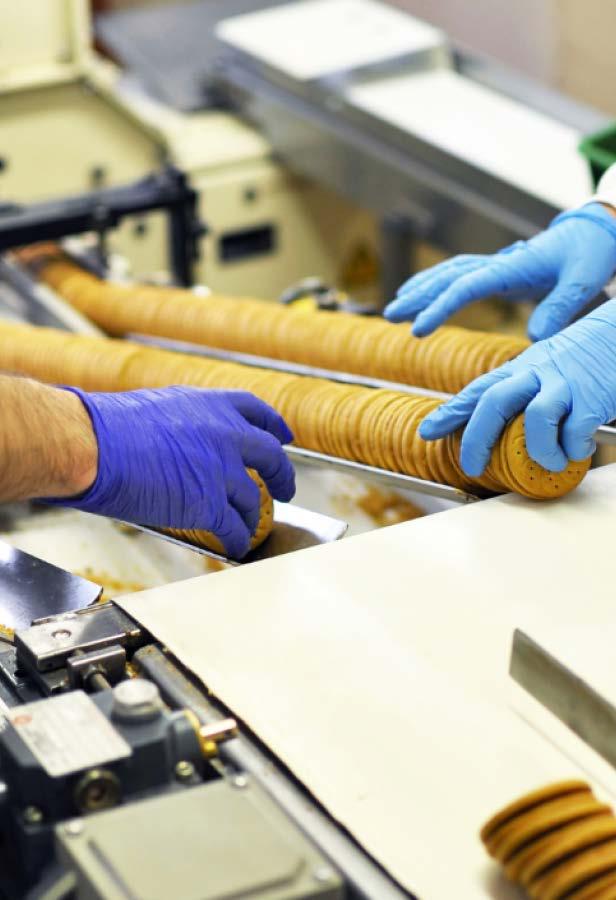
Architecture and much more
As a multi-disciplinary consultancy, our expertise extends beyond architecture, meaning our clients can pick and choose key areas or combine a number of our service skill sets and project management skills when selecting our single point service offer. DB3 Group offers the following four individual business units.
DB3 Architecture & Design
Providing RIBA Chartered sustainable architecture, urban design, landscape design and masterplanning, with supporting services including BIM, visualisation and interior design. DB3’s architectural team comprises 35+ architects, supported by a strong team of 40+ technologists and architectural assistants with the capacity to resource projects across all sectors.
DB3 Building Services Engineering
Offering CIBSE Chartered Mechanical and Electrical Engineering to all sectors. The team have particular experience in the leisure sector, having delivered numerous wet and dry leisure facilities across the UK. The team incorporates Building Physics Engineering, are CIBSE Low Carbon Energy Assessors and offer Thermal Modelling (DSM).
DB3 Net Zero
Drawing on the experience of our in-house mechanical & electrical engineers, architects, energy assessors, Passivhaus designers and sustainability experts. Our suite of Net Zero consultancy services is broken down into six categories which cover topics around whole life cycle. These categories include; Carbon, Efficiency, Passivhaus, Wellbeing, Performance & Compliance.
DB3 Professional Services
The team deliver building surveying, retail project management, principal designer, contract administration and NEC supervisor roles, across the UK. Working alongside DB3’s architectural and M&E teams, these roles can be incorporated into a multi-disciplinary offering or procured as an independent service.
Accreditations
AJ100 Company
RIBA Chartered Practice
Passivhaus Trust Member
Certified Passivhaus Designers
CIAT Registered Practice
CIBSE Directory of Practices & Firms
CIBSE Low Carbon Energy Assessors
ISO9001:2015 Quality Management System
ISO14001:2015 Environmental Management System
Altius Approved Elite Vendor
H&S SSIP Accredited, through Eurosafe and Alcumus
Constructionline Gold Member
Achilles RISQS Accredited
Cyber Essentials Plus
Awards
DB3 Group: Shortlisted - COBBA 2024 ‘Architect of the Year; Shortlisted - Yorkshire Insider Awards 2024 ‘Architecture Practice of the Year’; WinnerUK Enterprise Client Service Excellence Award 2024 ‘Best Sustainable Architecture Practice’; Shortlisted - The Grafters Awards 2024 ‘Best RIBA Architectural Practice’; ’Shortlisted - MMC Awards 2024 ‘Women in Modern Methods of Construction’; Winner - Build Architecture Awards ‘Best Sustainable Architecture & Design Firm 2023’; ShortlistedWest Midlands Insider Awards 2023 ‘Architecture Practice of the Year’; Winner - Yorkshire Insider Awards 2023 ‘Architecture Practice of the Year’; Shortlisted - COBBA 2023 ‘Business Development Professional’; Shortlisted - UKREiiF Awards 2023 ‘Consultant of the Year’ & ‘People & Skills Torchbearer’; Shortlisted - COMBA 2023 ‘Architecture Practice’ & ‘Business Development Professional’; Shortlisted - Grafters Awards 2023 ‘Architecture Practice’; Winner – COMBA & COBBA 2022 ‘Architect of the Year’; 2021 Digital Enterprise Top 100; Winner – Insider Property Awards 2018 ‘Architectural Practice of the Year’ & ‘Design Excellence’; Shortlisted – BD Awards 2017 ‘Sports & Leisure Architect of the Year’; RICS Design Through Innovation Award 2017; Insider Property Industry Awards 2015 ‘Highly Commended Architectural Firm of the Year’
Castle Farm Leisure Centre: ‘Best Public or Community Building’ - LABC Regional Awards Printworks Campus: ‘Project of the Year Education (Secondary & Higher)’ - MMC Awards 2024
Helensburgh Waterfront Development: Highly Commended - Argyll & Bute Awards 2023 ‘Aesthetic Design’; Finalist - Planning Awards 2023 ‘Outstanding Contribution to Placemaking: Best Use of Arts, Culture or Sport’; Highly CommendedIStructE Awards 2022 ‘Leisure Project’
Llys Cadwyn Regeneration: Winner – Cardiff Property Awards 2021 and Ystadau Cymru 2021 Award for ‘Creating Economic Growth’; Highly Commended – British Construction Industry Awards 2021; CLAW Project of the Year Awards 2021; Winner –Constructing Excellence Awards Wales 2021 ’Integration and Collaborative Working’ & ‘Building of the Year’
Adidas Oxford Street: Gold Winner – London Design Awards 2020
Leeds College of Music: Winner – RIBA Regional Award 2015 ‘Small Project Award’; Shortlisted –Insider Property Industry Awards Yorkshire 2018 ‘Regeneration Project of the Year’, Education Estates Awards 2018 ‘Refurbishment Project’, AJ Retrofit Awards 2018 ‘Further & Higher Education’;
Constructing Excellence Yorkshire & Humber Awards 2018 ‘Building Project of the Year’
Chancery Lane Residential: Shortlisted –London Construction Awards 2018 ‘London Build Excellence’ & ‘Regeneration Project’
Airedale Air Conditioning: Winner – RICS 2017 Regional Award ‘Design through innovation’
Ysgol Craig Y Deryn School: RTPI Wales Planning Award 2014
Kirkcaldy Leisure Centre: Commended – SCALA Awards 2014 ‘Civic Building of the Year’
MOMA Machynlleth Tannery Gallery: CPRW Awards 2014 ‘Special Award’
Michael Woods Leisure Centre: Highly Commended – SCALA Awards 2014 ‘Civic Building of the Year’; Scottish Property Awards 2014 ‘Architectural Excellence’
Marks & Spencer, Liverpool: Highly Commended –CIAT Award 2010 ‘Technical Excellence’
PAN Emirates, Dubai: Shortlisted – Retail Interiors Awards 2010 ‘Best International Interior’
Threeways School, Bath: BCSE Awards 2009 ‘Inspiring Design for Special Schools’
ASDA Stores Supplier Awards: 2009 ‘Best Consultant’ & ‘Best EDLC (Every Day Low Cost) Initiative’
University of Huddersfield, Creative Art Building: Bronze Awards – RIBA White Rose Award 2009; Commendation – CIAT Award 2009; Shortlisted –RICS Pro Yorkshire Awards 2009
University of Huddersfield, Milton Centre: Winner – Insider Yorkshire Renaissance Awards 2006 ‘Best Restoration Project’
Aberdovey Yacht Club: Winner – Snowdonia
National Park Awards 1992 ‘Good Design in the Countryside Award’
St Giles Business Park for the DBRW: Winner –Prince of Wales Design Awards 1990 ‘Good Design’
Llwydcoed Crematorium: Winner - RIBA Wales Architecture Awards 1971
Royal Institution of Chartered Surveyors (RICS): 2017, 2011, 2010
Green Apple Awards: 2015, 2013, 2010, 2009, 2008
LABC Building Excellence Awards: 2013, 2012, 2011, 2010, 2009, 2008
LABC Design Excellence Awards: 2013, 2012, 2009, 2008, 2003, 2002