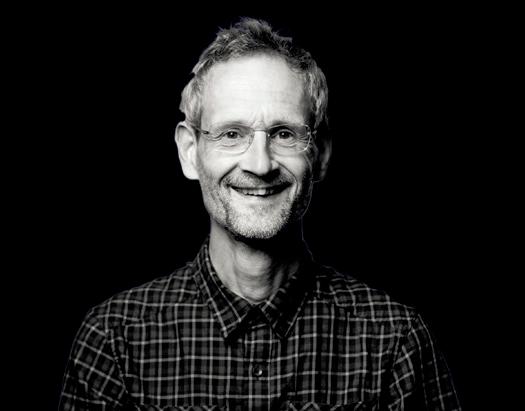
9 minute read
DCA delivers EMR ergonomic mock up and HF reviews safely under Covid restrictions
Article by Paul Rutter Transport Sector Manager
Throughout 2020, despite the difficult working environment caused by the pandemic, DCA has been very busy safely designing and mocking up new trains destined to run on UK railways in the near future. Although public transport has been hit particularly hard by travel and working restrictions, plans are well on the way to provide new high speed trains built by Hitachi for East Midlands Railways and Avanti West Coast services.
The restrictions in place have not stopped us working in our large build facility close to the centre of Warwick, enabling a range of design and human factors studies to take place. Hitachi are in the final stages of the process to validate the design of the driver’s cab for the new Class 810 BMU trains. These high speed bi-mode trains can operate self-powered by on-board diesel generators or from overhead electric power lines. This flexibility extends their useful operating range and provides an efficient and sustainable solution as part of an overall strategy to move towards a low CO2 electric future.
DCA has supported the engineering team at Hitachi in Pistoia, Italy throughout the design process, actively engaging in the design of the driver’s cab, ensuring that from an operational and human factors view point it meets all the latest requirements. A key part of the process was designing and building a full size ergonomic mock up of the cab. With our usual steel framework suppliers in lockdown, we had to design a lightweight composite wood supporting structure that we then built ourselves in-house. The exterior of the cab was not a visual requirement for the HF process and was left as a nominal surface design that the proposed EMR livery was applied to. The key exterior components that impact upon the HF performance of the cab, like the windscreen and wiper, the access steps and cab side door were accurately replicated and proven during driver trials. Inside, the driver’s desk is a visual facsimile of the proposed final design and was used by drivers to review the layout through a series of task analyses, and sign off the position of buttons, switches, and the control HMI (Human Machine Interface) including the use of CCTV and digital displays. And all this was achieved under a series of new procedures and working practices, aligned with the Government’s Covid guidelines and designed to protect the safety of our staff and our visitors from Hitachi and EMR, including the drivers taking part in the HF reviews.
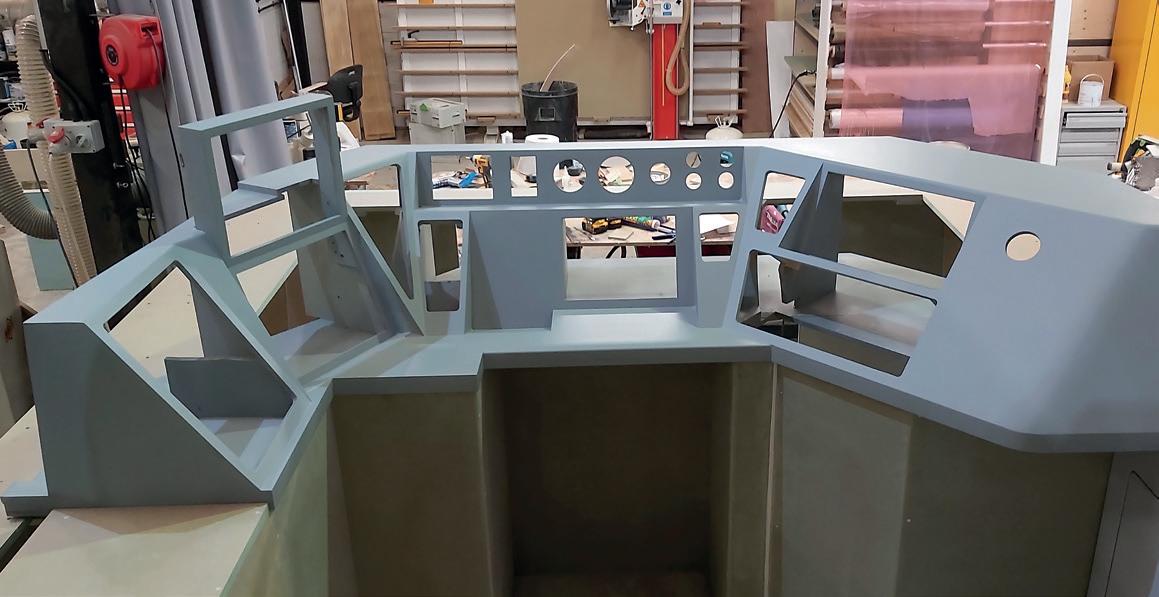
The design process has involved collaboration at each step on the way from inception through design development, human factors assessment and detail engineering. Wherever possible, particularly during the early stages, the project was coordinated through virtual meetings on-line. Once the mock up took shape and needed to be physically assessed and reviewed, a Covid secure meeting space was set up in our large build facility to allow face to face meetings and HF trials to take place. These required safe physical distancing and the implementation of appropriate control measures such as screens, hand sanitising and face coverings. This has allowed the HF validation process to continue, engaging representatives from all interested parties, including Hitachi, EMR, the Driver’s Counsel, union representatives and the drivers themselves, with mock up to agree and sign off the design outcomes.
Mechanical Engineering
DCA’s engineers work side-by-side with our design team to ensure that while our designs remain true to the original creative intent, they are functional, durable and costeffective. We continually research manufacturing processes, materials and technologies to support these aspirations and ensure we can deliver the experience as designed.
Quantum Seating
M100 Range Regional Seat
Lightweight Standard Class rail seat
Design research
Mechanical engineering
Industrial design
Visual brand language
Usability and HF
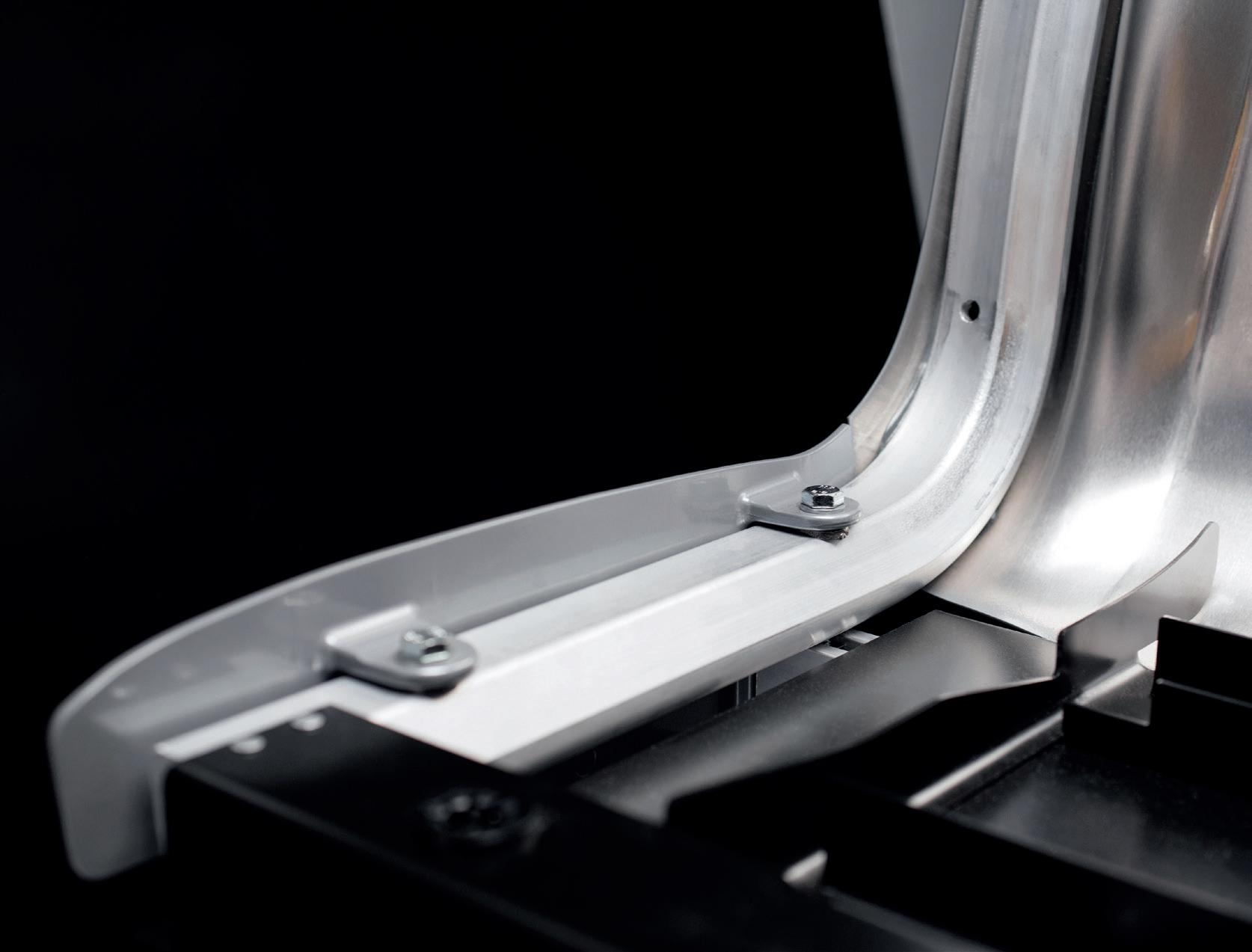
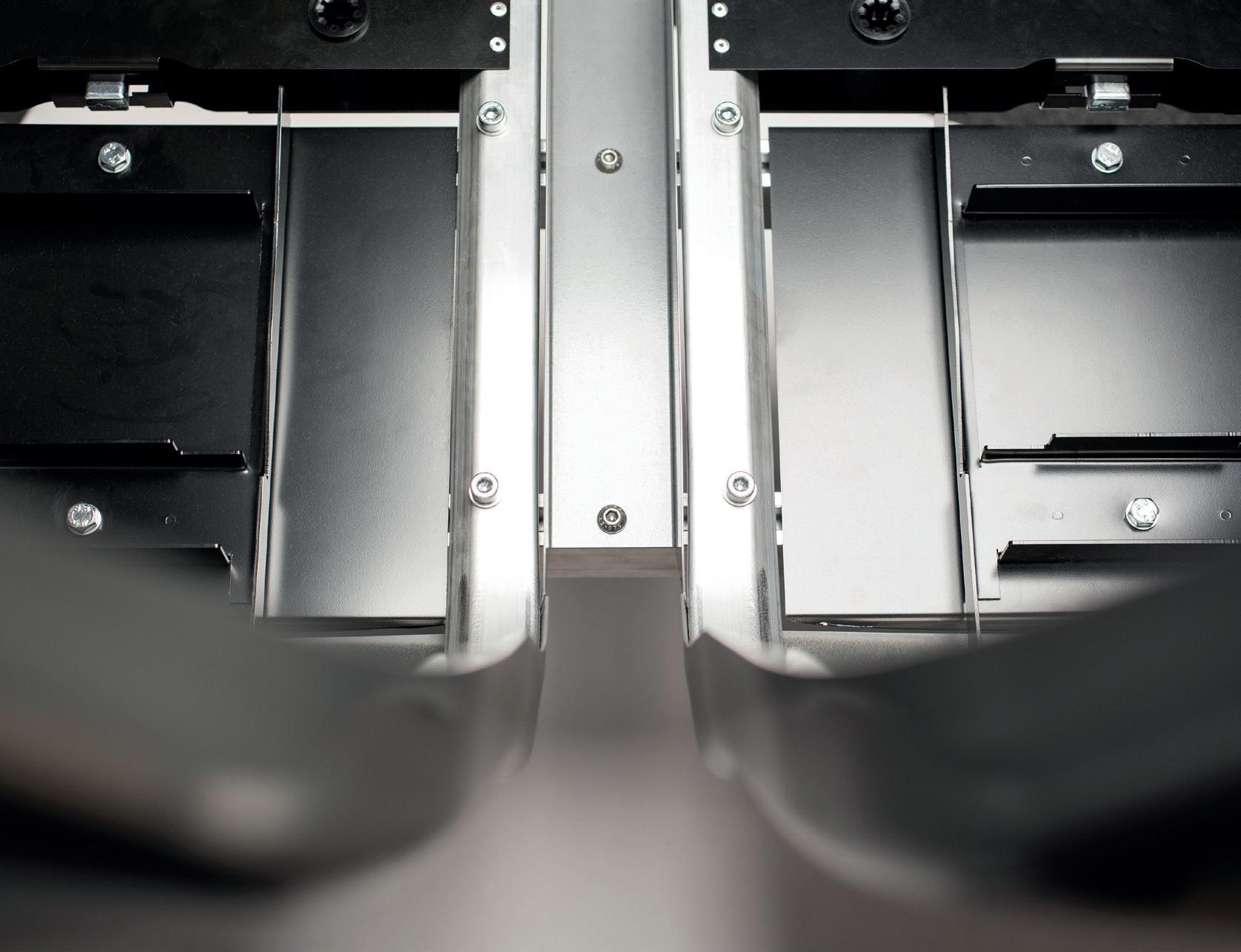
Percy Lane Products
SSL Detrainment System
Emergency detrainment steps
Usability and HF
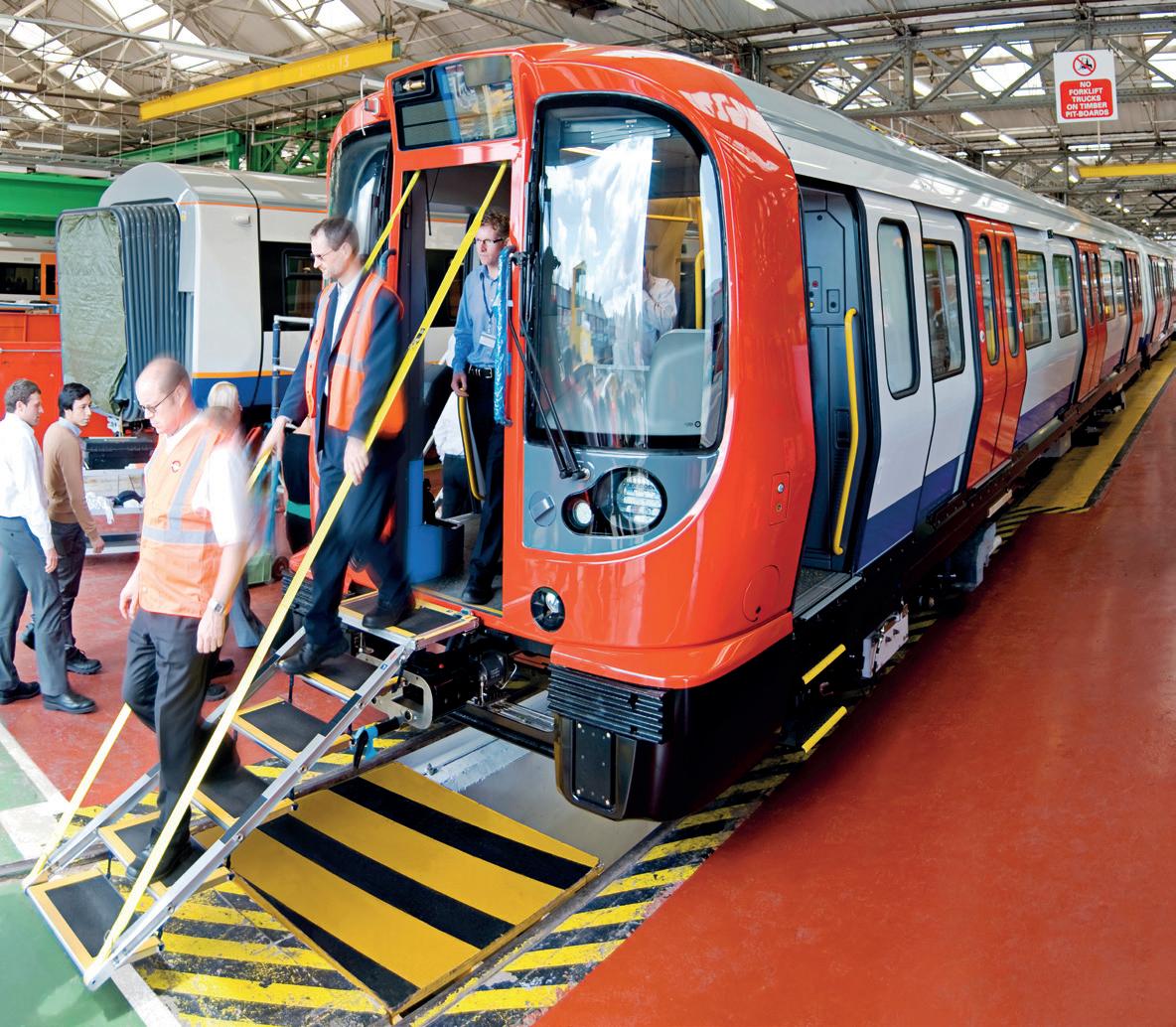
Mechanical engineering
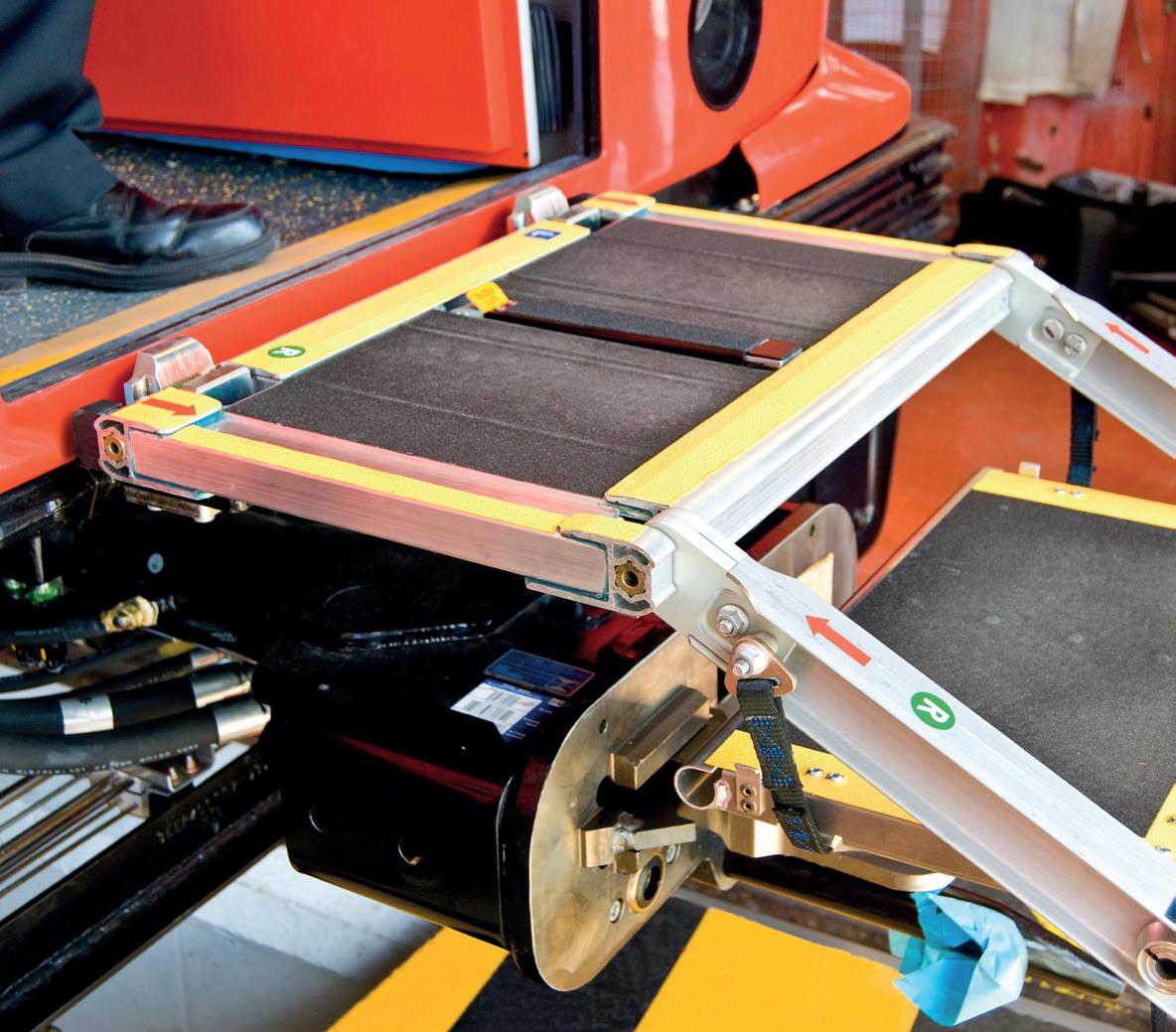
Prototyping
Testing and evaluation
Production support
Westinghouse
Platform screen doors for Jubilee line
Industrial design
Colour, material and finish
Interior design
Visualisation and animation
Engineering
Production support
Prototyping and Evaluation
In-house models and mock ups.
We are rare amongst design consultancies in being able to build scale models, large ergonomic rigs and full size visual mock ups in-house using our own model making team.
This gives us unrivalled levels of flexibility, responsiveness and control during the production of your models, rigs, prototypes and mock ups. And this is backed up by the experience, skill and attention to detail of our dedicated workshop team.
VolkerFitzpatrick
Cross Rail
Training mock-up for Crossrail
Mechanical engineering
Production support
Prototyping
Testing and evaluation
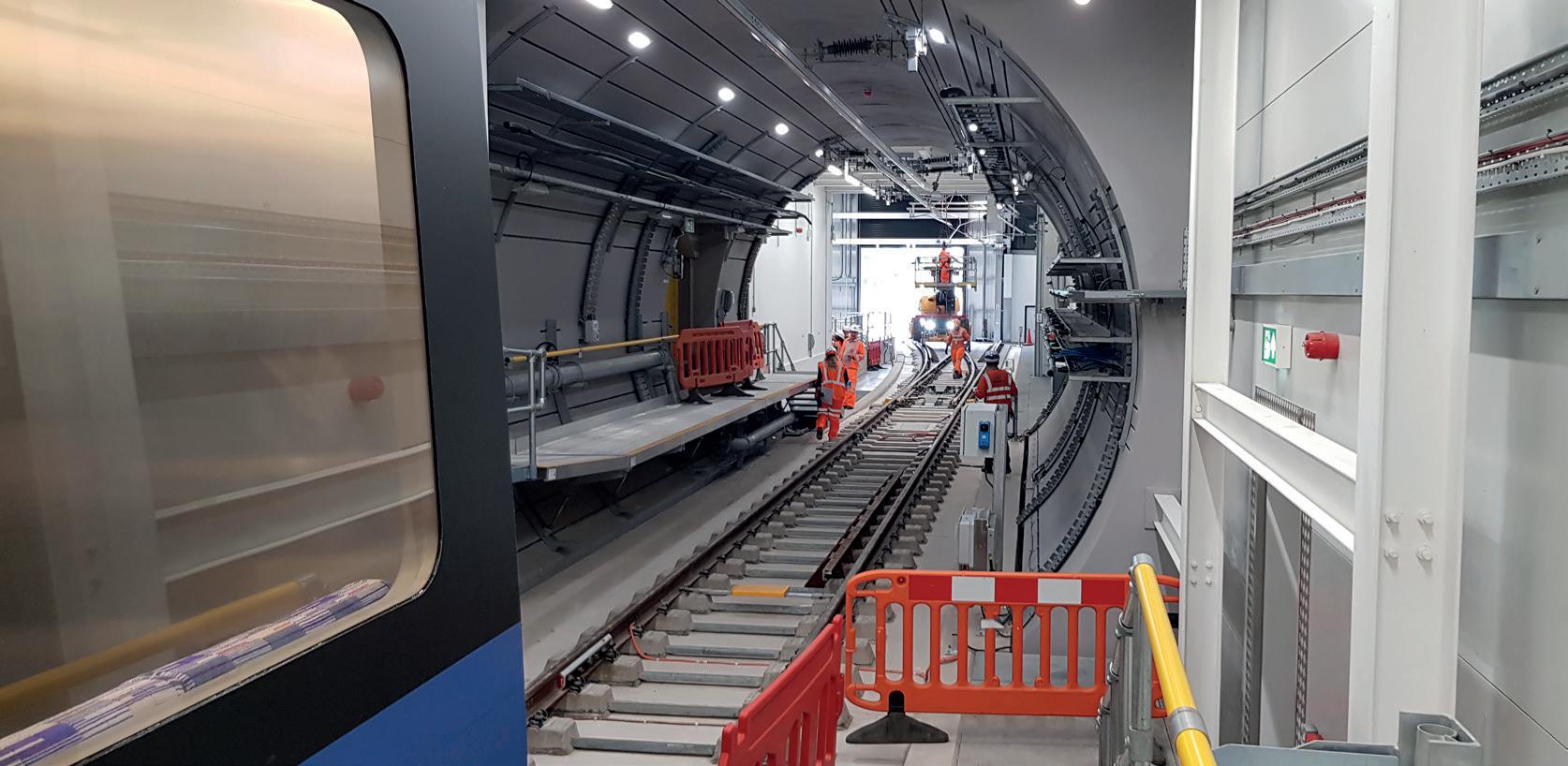
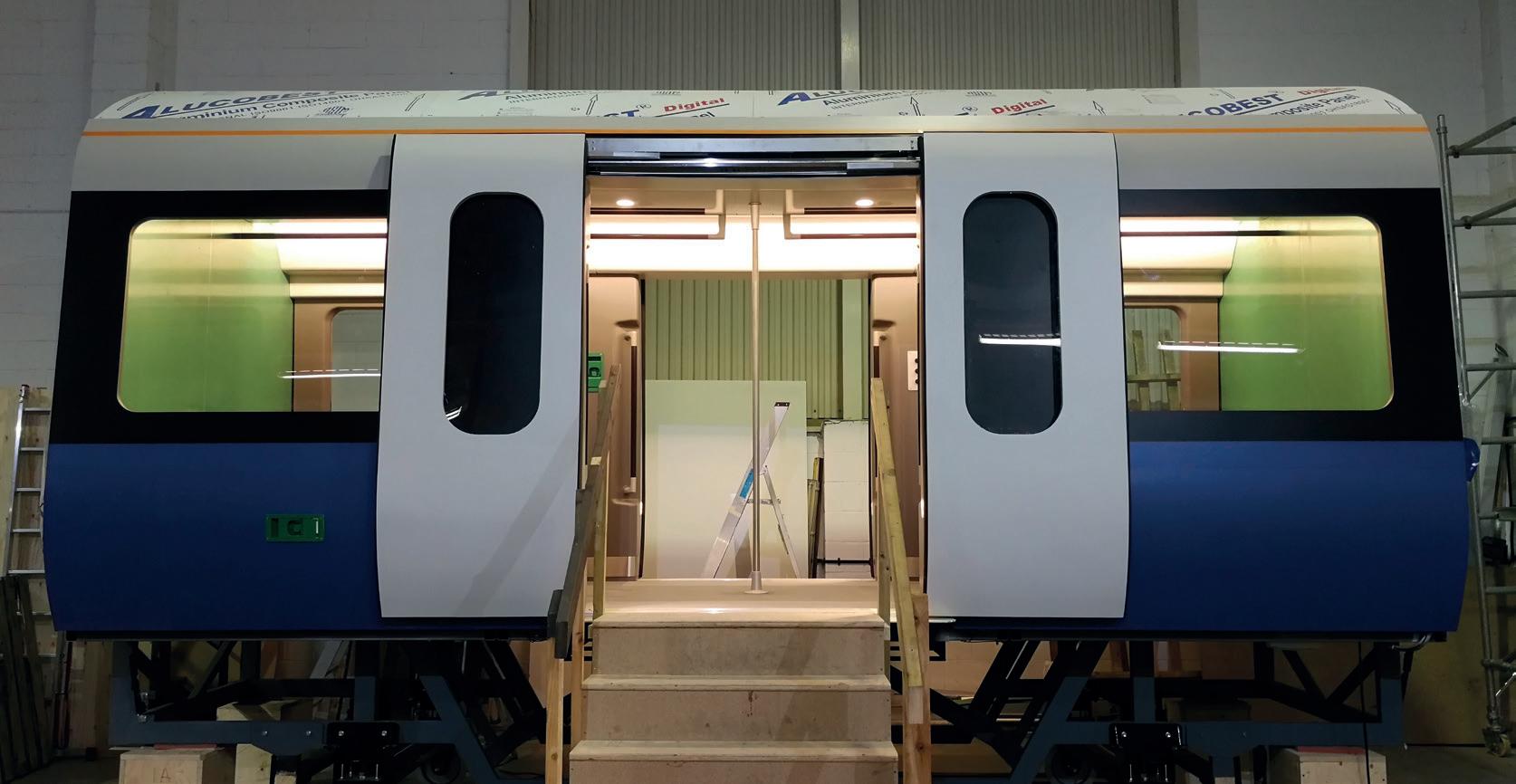

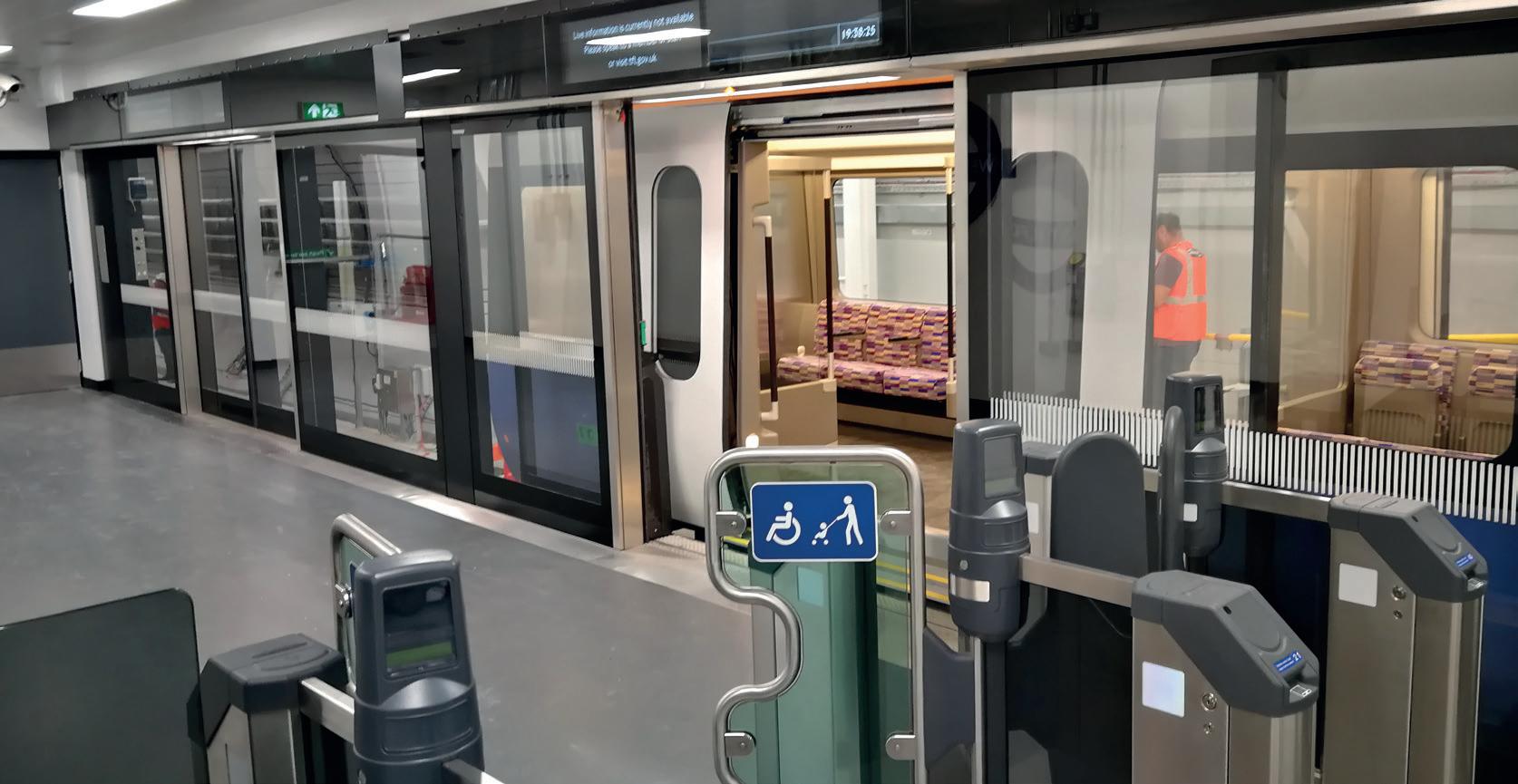
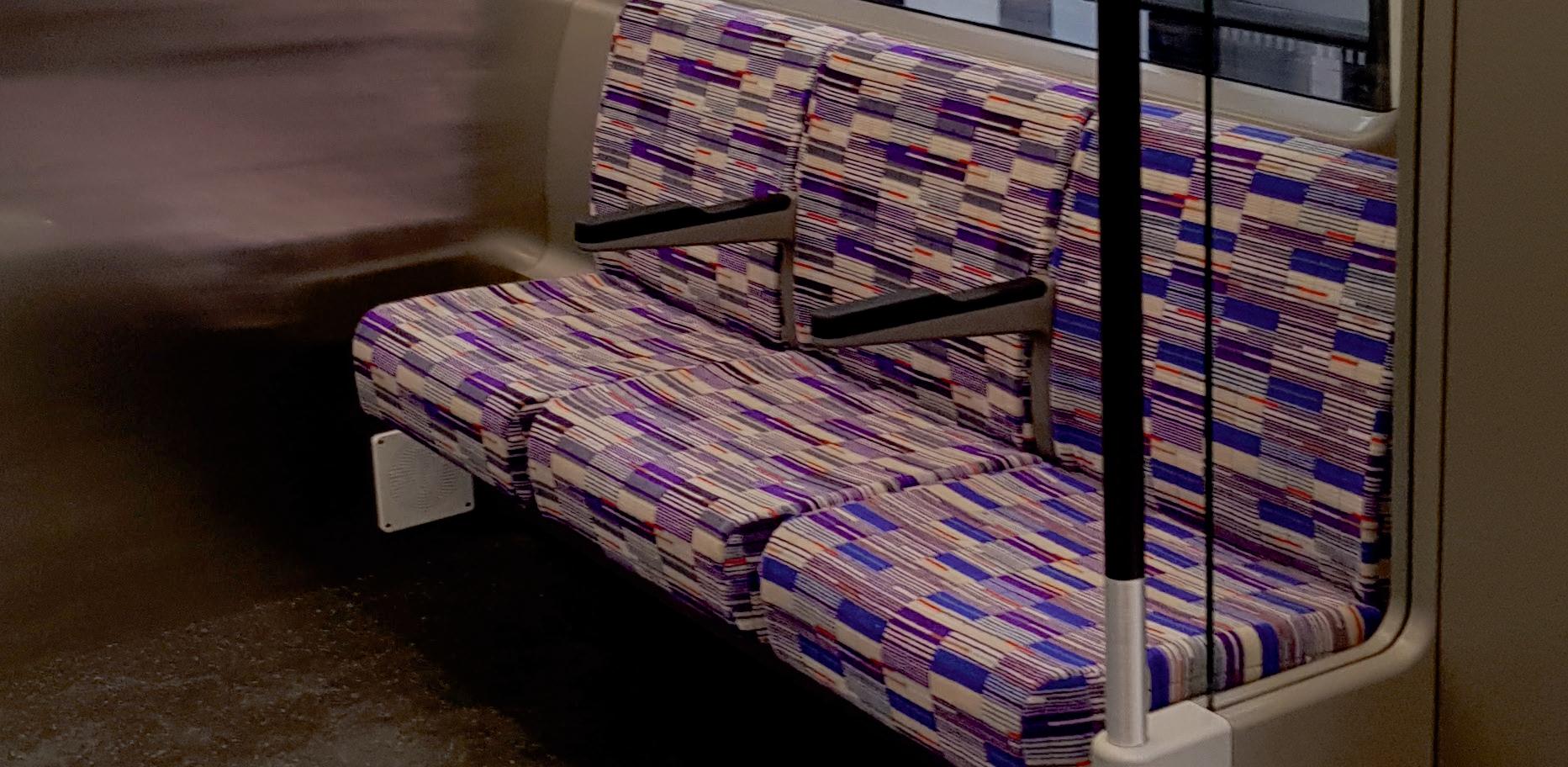
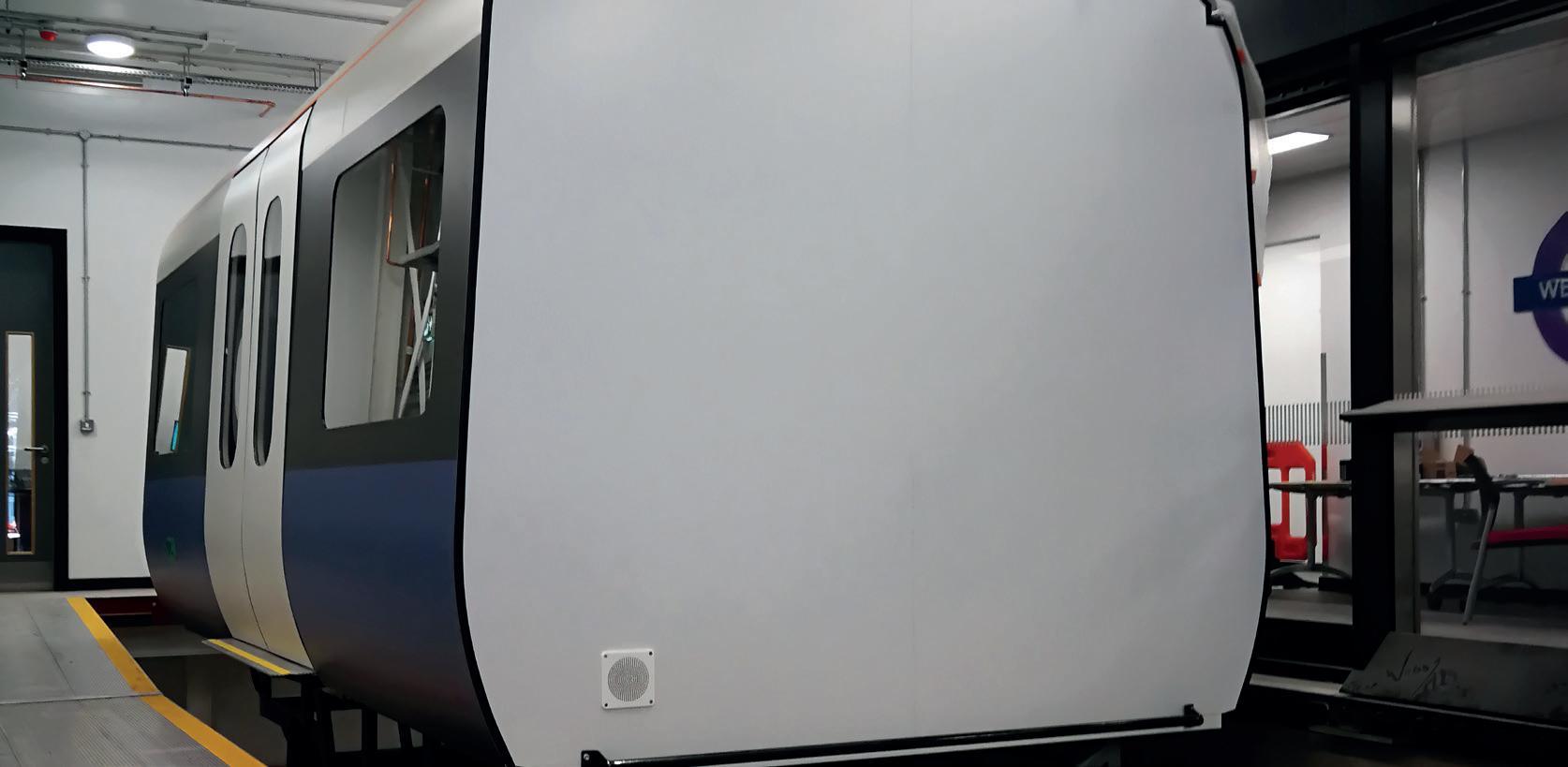
Virtual Reality and Visualisation
We are working with the latest Oculus and HTC Vive platforms to visualise rendered 3D CAD environments as personal virtual reality experiences. Users can explore the proposed design in VR and gain a real sense of how they will interact with it, even during the relatively early stages of development.
Incorporating VR technology intelligently into a development programme can improve the detailed understanding and assessment of the design before mock ups are built. This in turn can mean fewer physical mock ups and fewer mock up modifications are required.
Zoeftig
Vista modular seating system
Engineering and visual design
Design research
Industrial design
Visual brand language
Mechanical engineering
Model making
Usability and HF
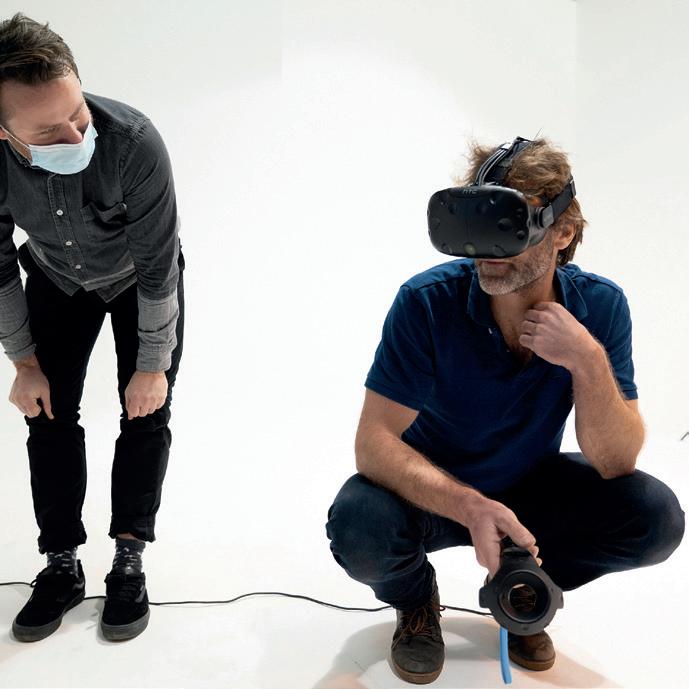
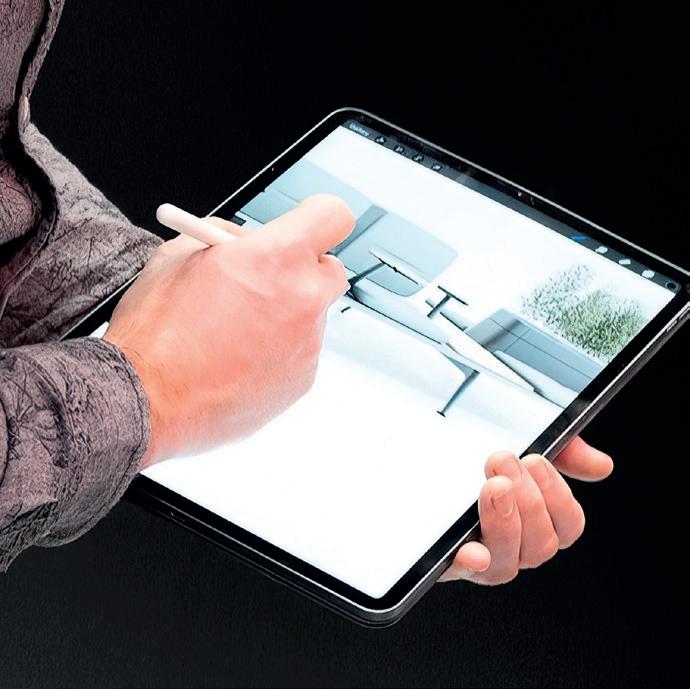
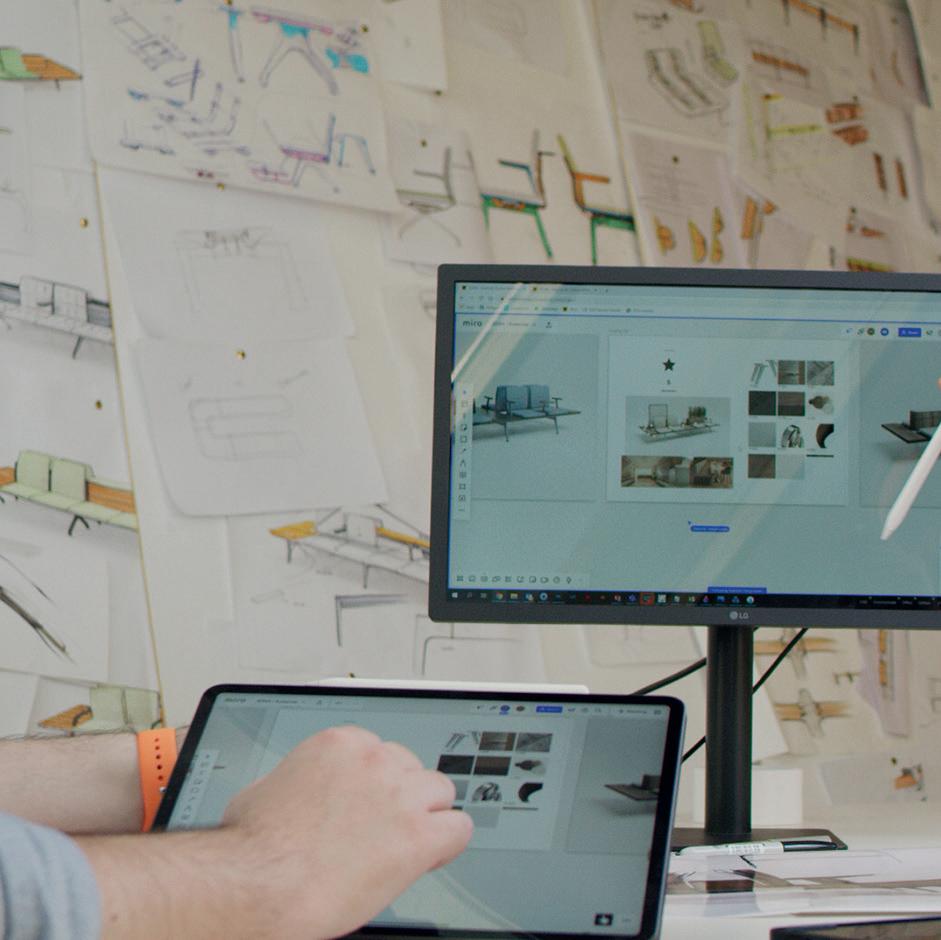
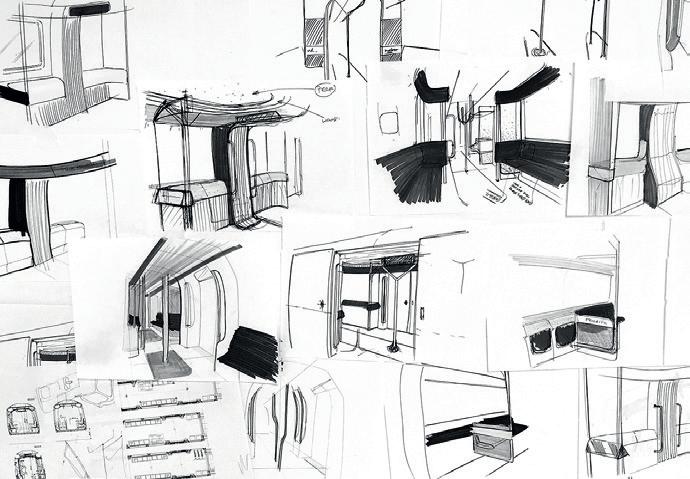
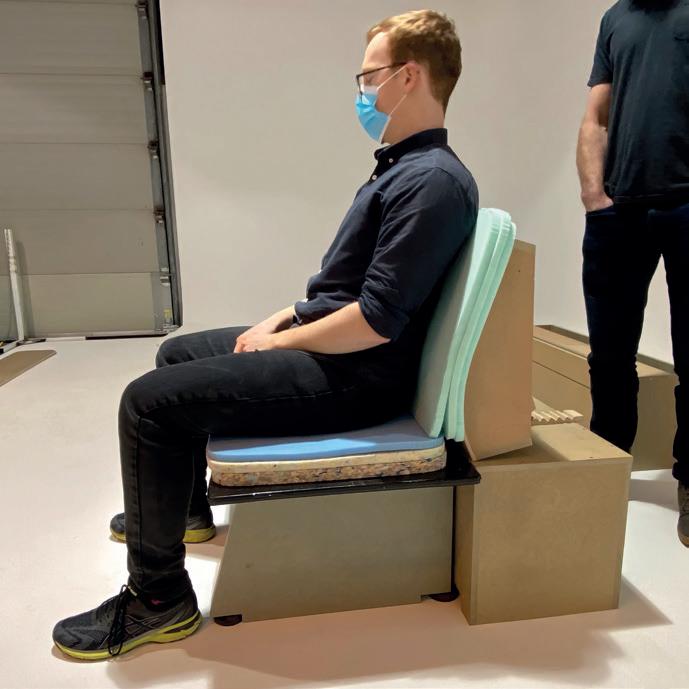
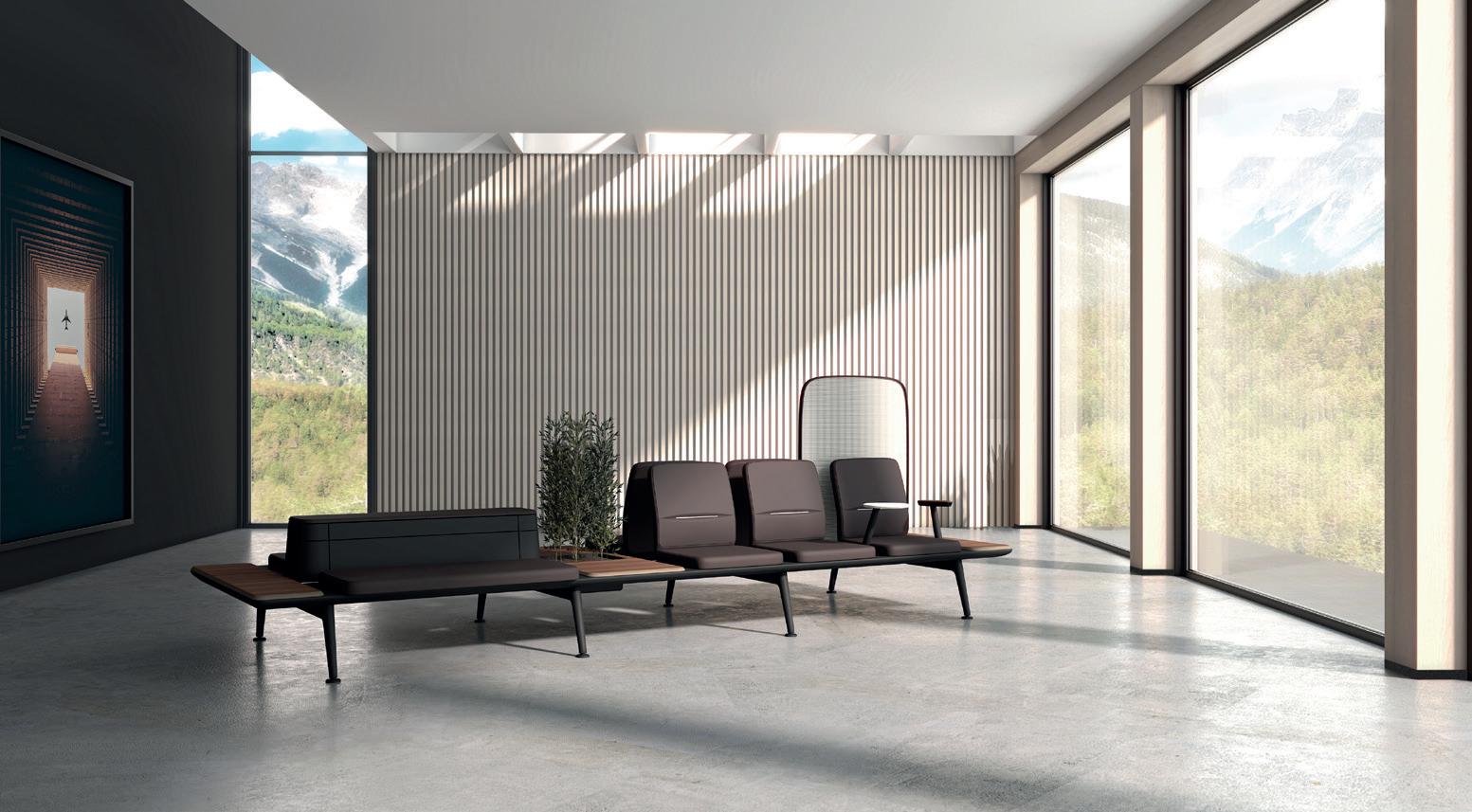

Electronic Engineering
Our software and electronics specialists work alongside our mechanical engineers and designers in multidisciplinary teams to deliver complex electro mechanical systems.
The challenge with such systems is making them robust, reliable and future proof without overengineering and introducing unnecessary complexity or cost.
Our approach is to balance theory, simulation and analysis with producing physical test rigs and prototypes at appropriate points in the development cycle to reduce project risk while keeping the development timescales and budget lean.
Electro-mechanical design and construction
Mechanical engineering
Industrial design
Colour, material and finish
Production support
FiveAI
Autonomous vehicle sensor mounting and enclosure
Design and construction of 5 prototype road vehicles
Exterior styling
Industrial design
Mechanical engineering
Production support
Prototyping
Testing and evaluation
Virtual Reality

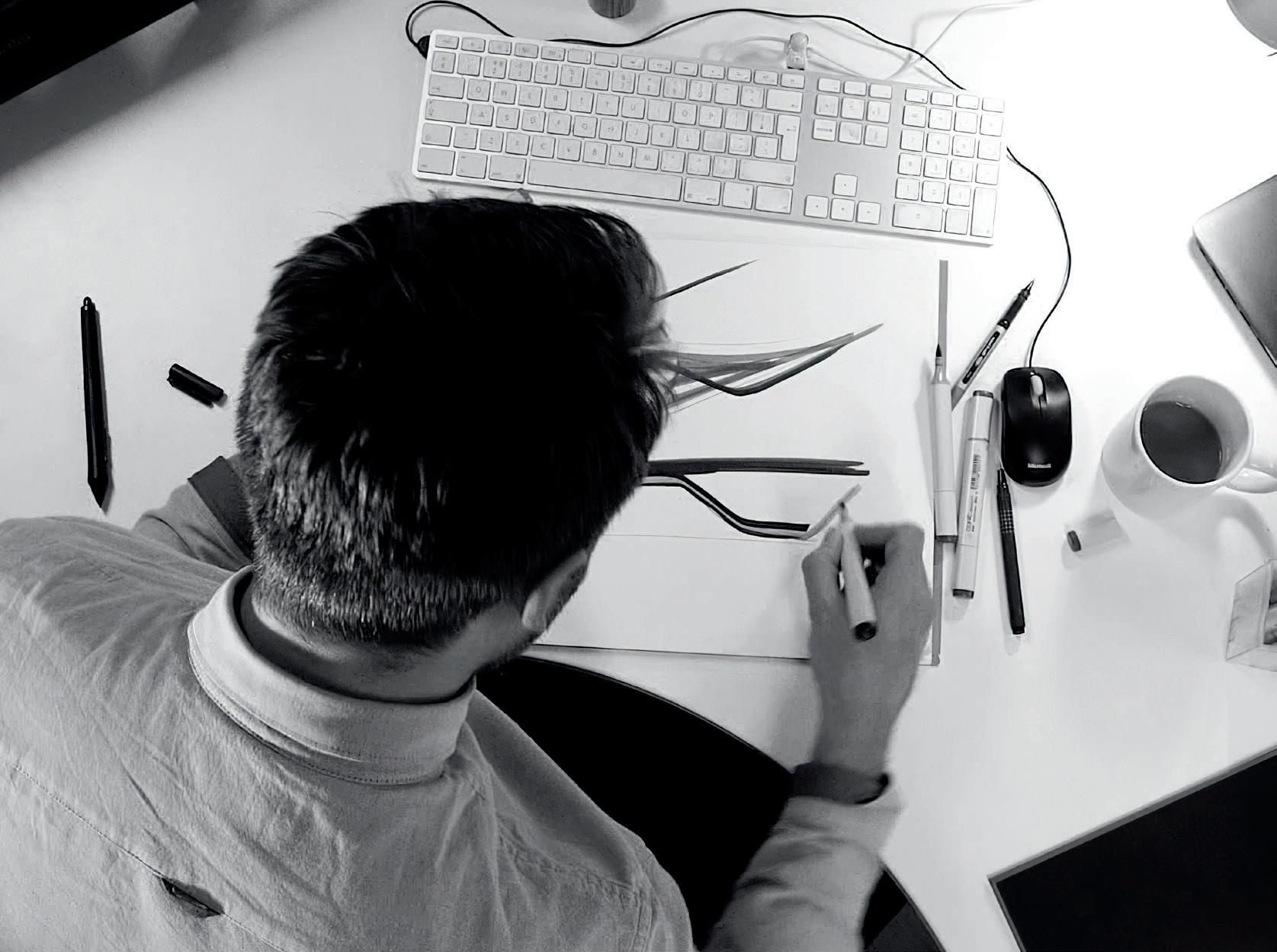
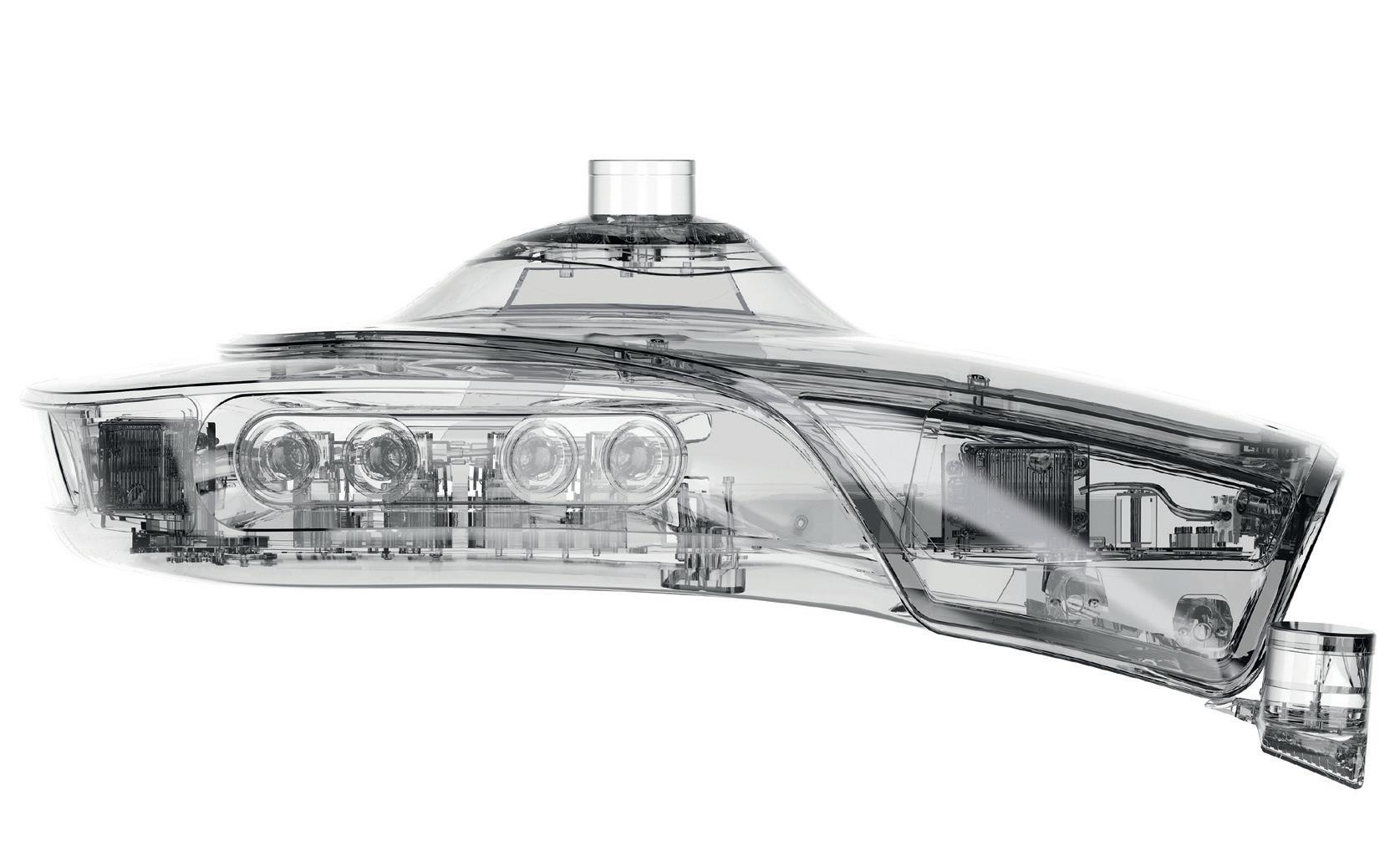
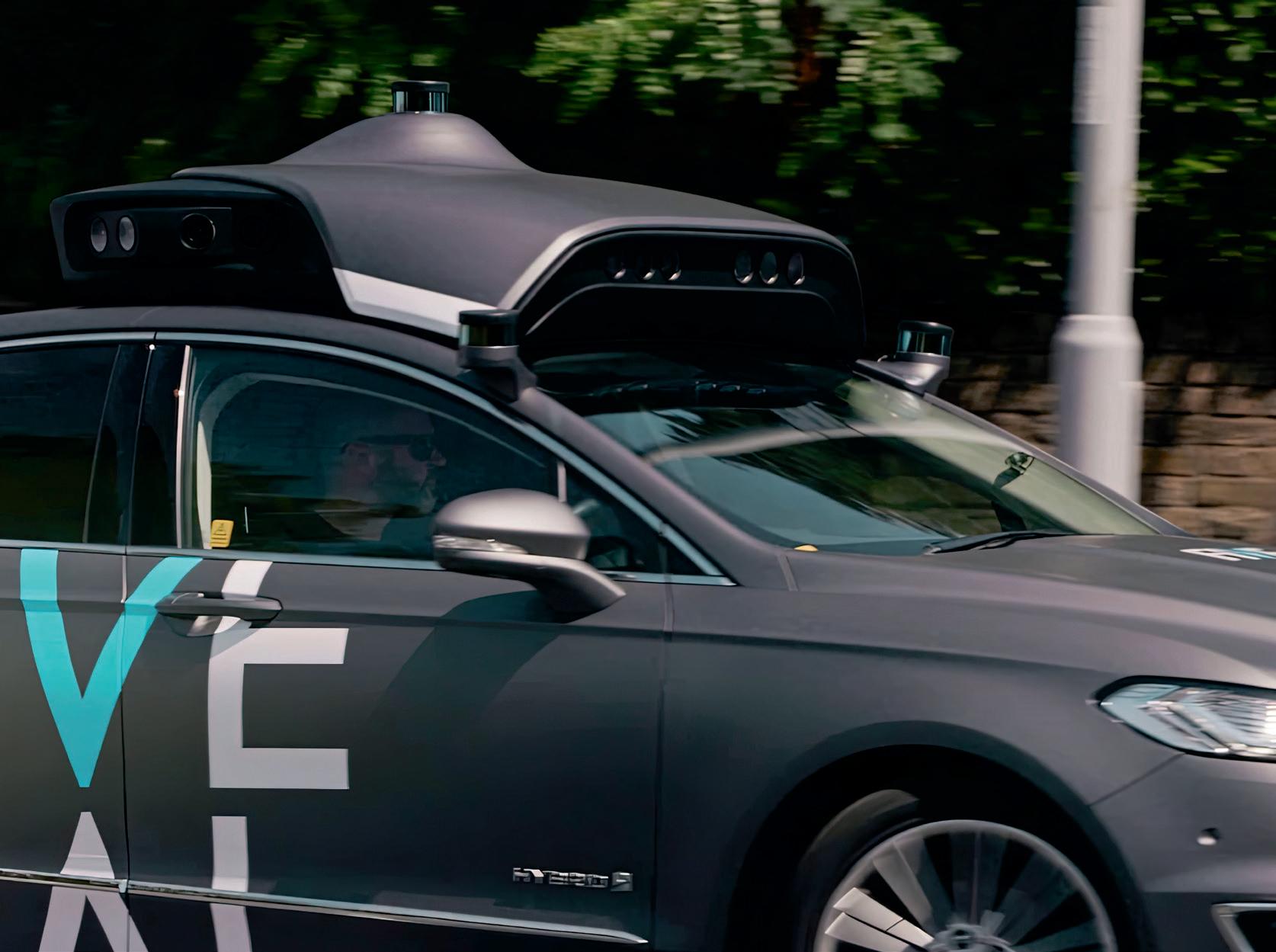
The ever-increasing ability to connect systems and devices together is presenting new challenges, as well as creating entirely new service opportunities. Understanding how smart devices can interact securely with each other is the key to successfully adding connectivity to transport products, systems and services. Working closely with our user experience team, we can create proof-of-concept Apps and websites in parallel with the electronics hardware and embedded software.
D-Fly Ltd
Hyperscooter
Multidisciplinary development of Personal Electric Vehicle
Colour, material and finish
Electronic engineering
Electronic hardware
Exterior styling
Industrial design
Mechanical engineering
Prototyping
Software development
Testing and evaluation
Usability and HF
Virtual Reality
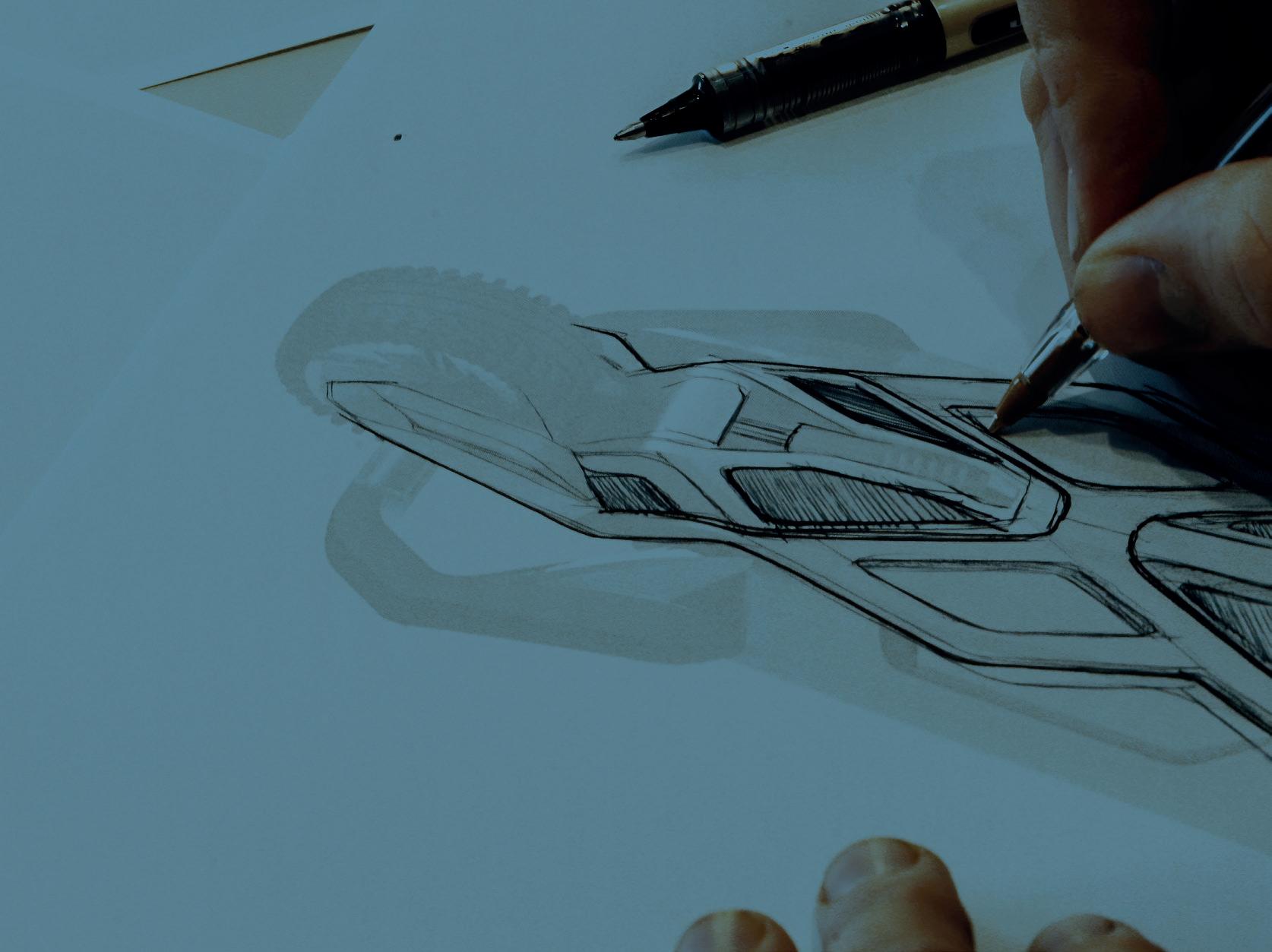
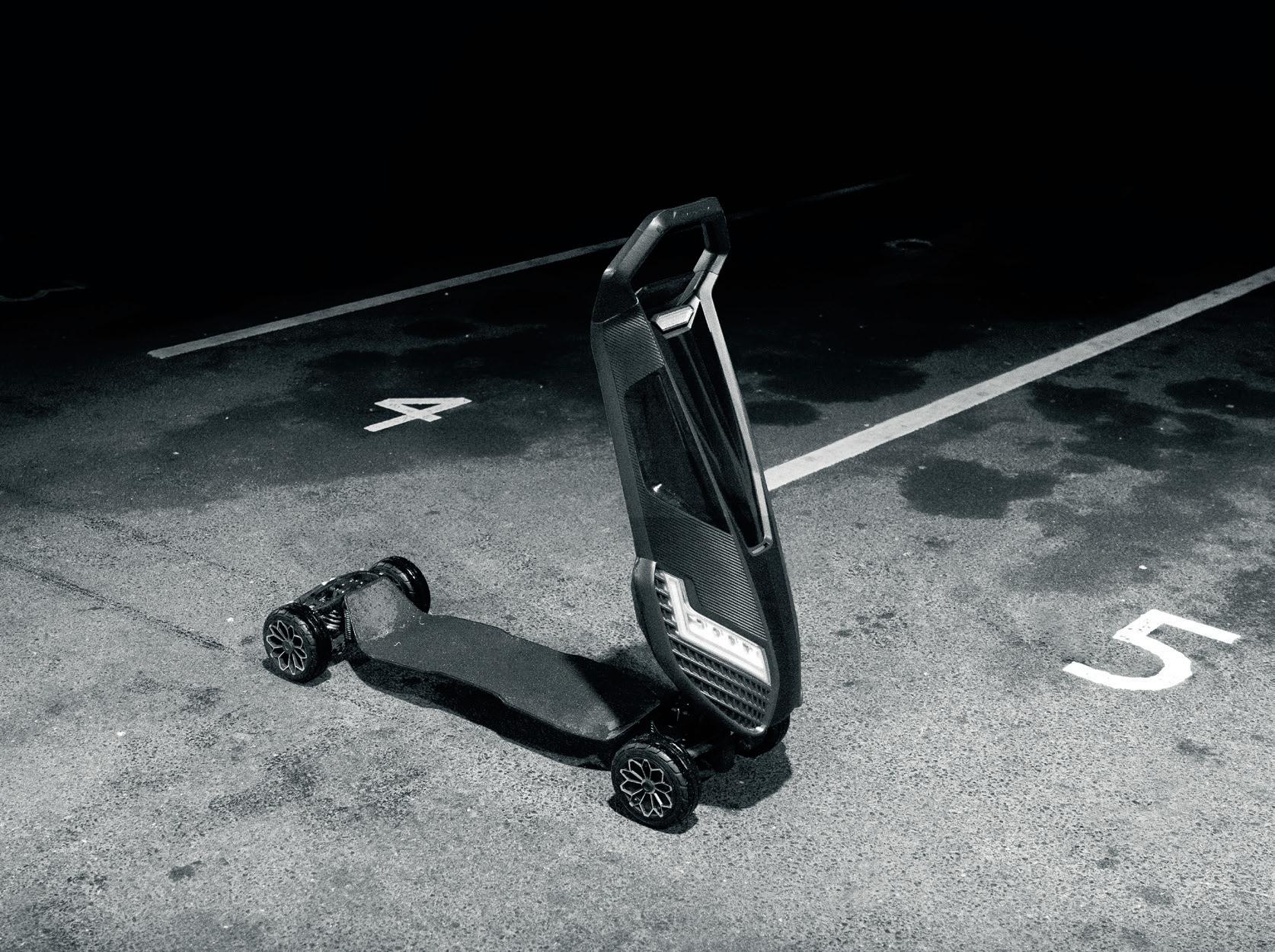
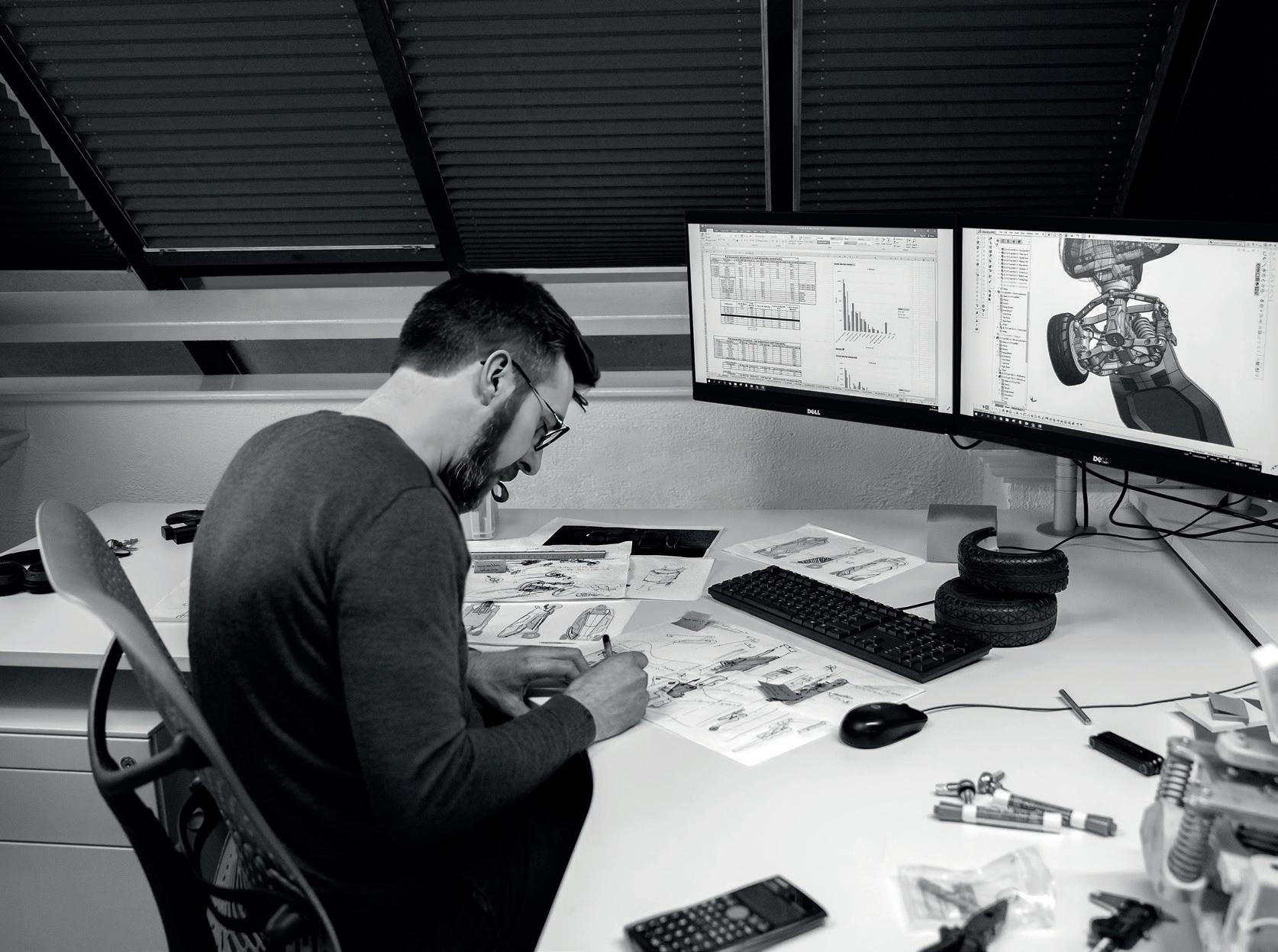
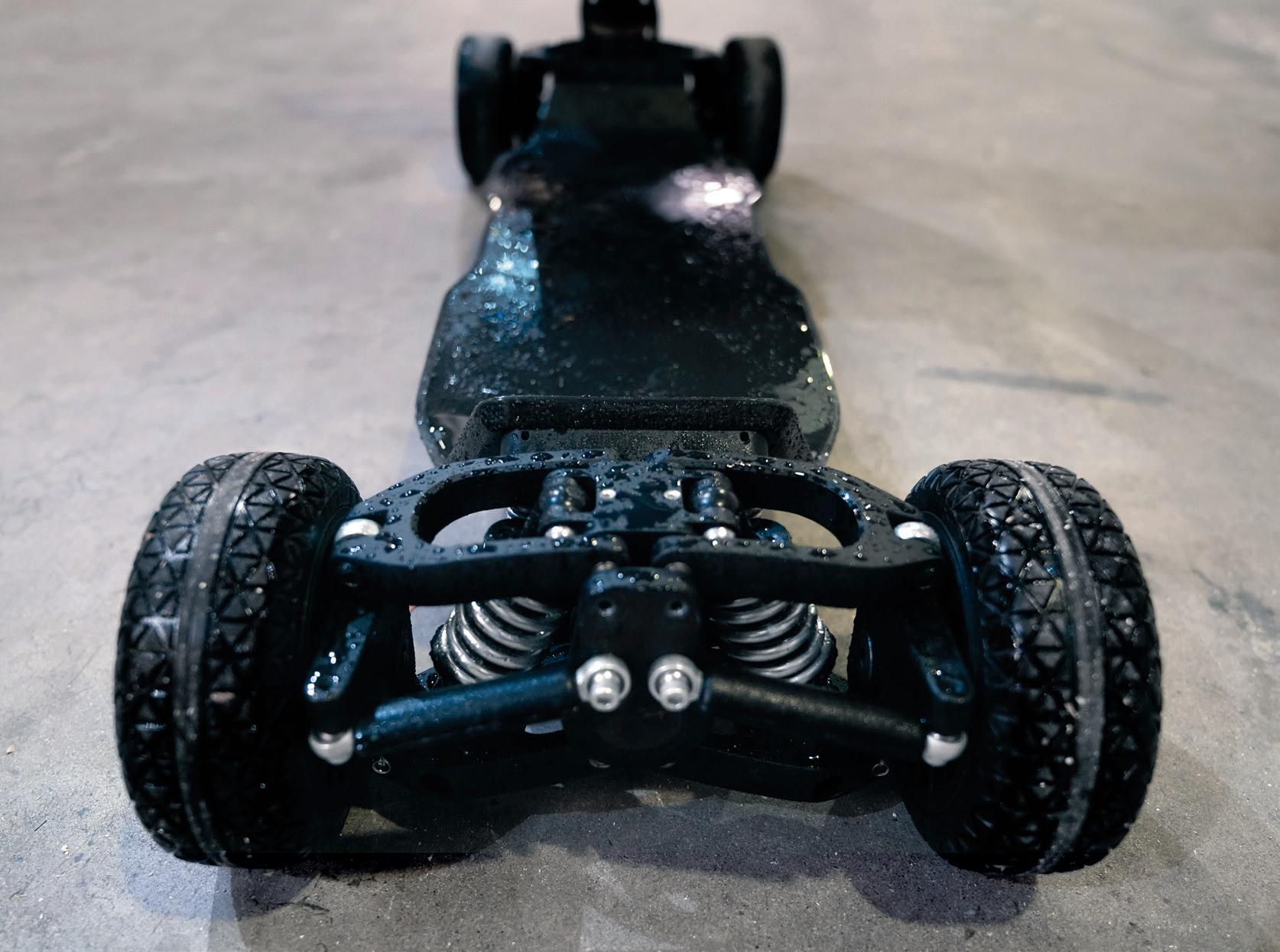
Article by R-P Kruizinga Transport Sector Manager & Senior Associate
Since its launch in 2019, the A-Star electric and autonomous shuttle bus has proved to be a very successful product for Xiamen Golden Dragon. Just before the Chinese New Year in 2021, it reached the impressive milestone of 1,500 units sold.
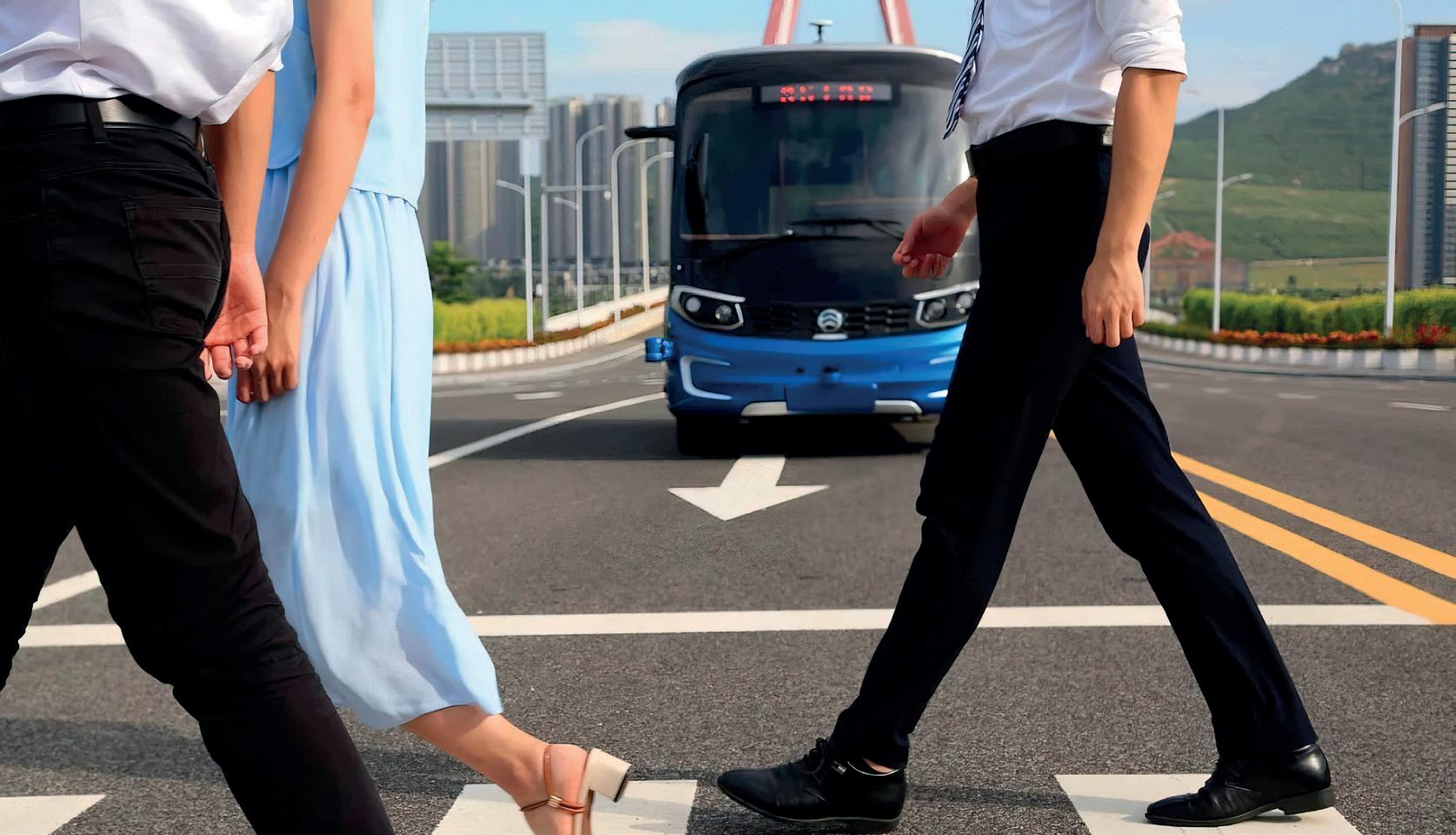
The idea for a zero-emissions and autonomous passenger shuttle was born from a collaborative design project between DCA and Golden Dragon. Having explored several ideas for future vehicles, the project focused on an electric, autonomous shuttle bus that would answer the demands raised by incoming environmental legislation and trends in urban planning and traffic management in China. At the time of its launch, the A-Star was the first of its kind, offering a zero-emissions solution to reduce urban congestion and pollution by transporting people between transport hubs and car parks outside of high-density urban areas such as city centres, business parks and tourist sites.
Today, the A-Star is in operation in many cities in China and beyond, and has won several awards. Competitors have tried to replicate the success of this transportation format, but the A-Star has remained the leading product in the market segment it helped to create.
The flexible architecture means that Golden Dragon has been able to use the A-Star as a development platform, constantly upgrading the drivetrain and autonomous driving systems, moving towards the goal of full autonomy.
Such modularity also means that the vehicle can be ordered in many different configurations, catering for the needs of specific regions or operators. There are even versions being used as food trucks in tourist sites where vehicles with internal combustion engine are not allowed to enter.
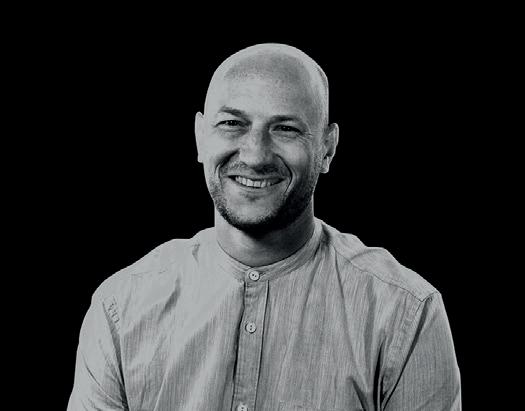
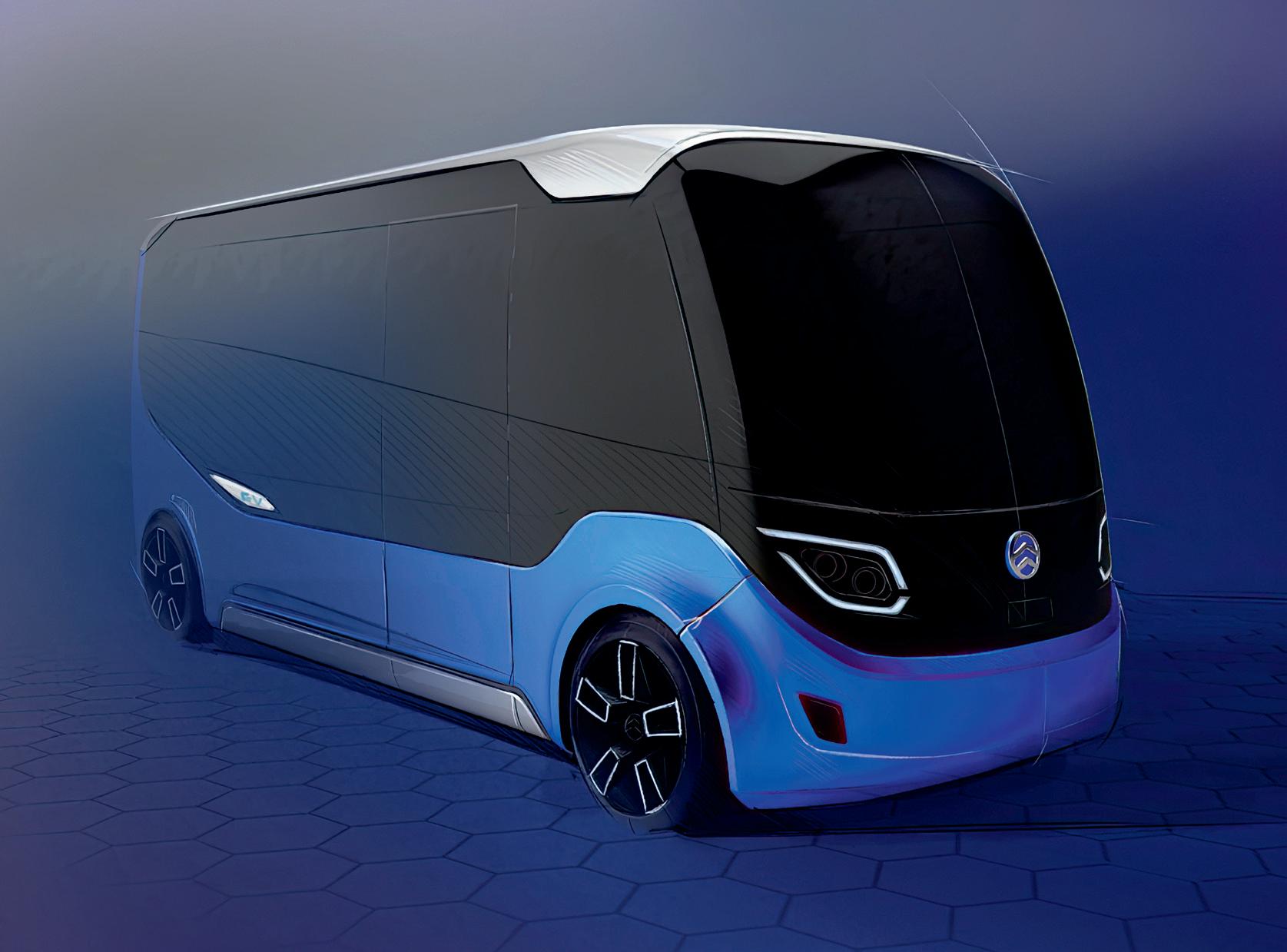

Xiamen Golden Dragon
A-Star
A-Star autonomous electric vehicle
Interior and exterior design
Usability and HF
Industrial design
Interior design
Testing and evaluation
Brush and Bombardier
Le Shuttle trains for Eurotunnel
Driver’s cab, single and double deck vehicle carriages
Industrial design
Colour, material and finish
Interior design
Prototyping
Exterior styling
Usability and HF
Bombardier Transportation
M6 double deck train for SNCB
Interior layout and design of double deck passenger saloons
Design research
Usability and HF
Industrial design
Colour, material and finish
Interior design
Prototyping
Testing and evaluation
Production support
CAF
C4K train for Northern Ireland Railways
Passenger interiors and cab exterior livery
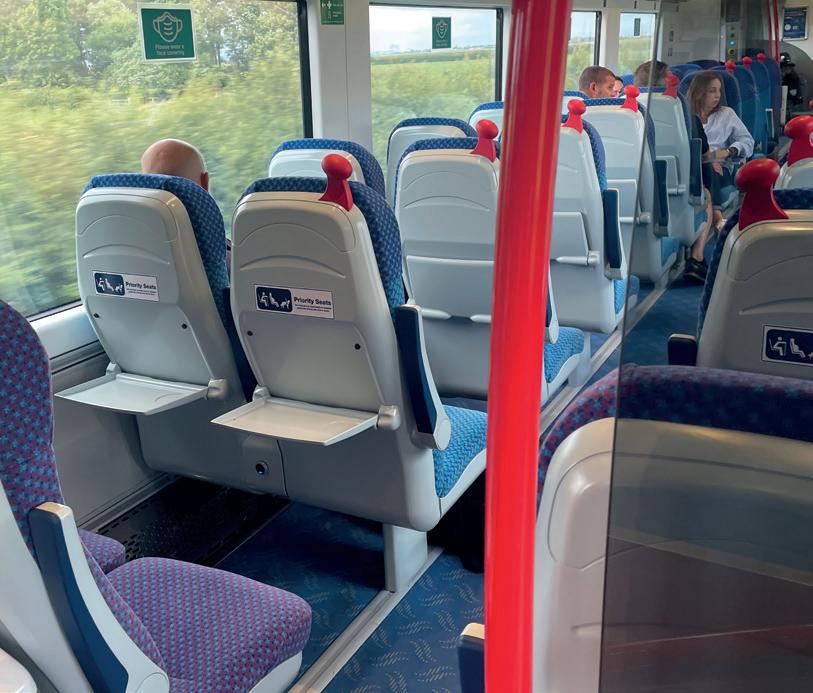
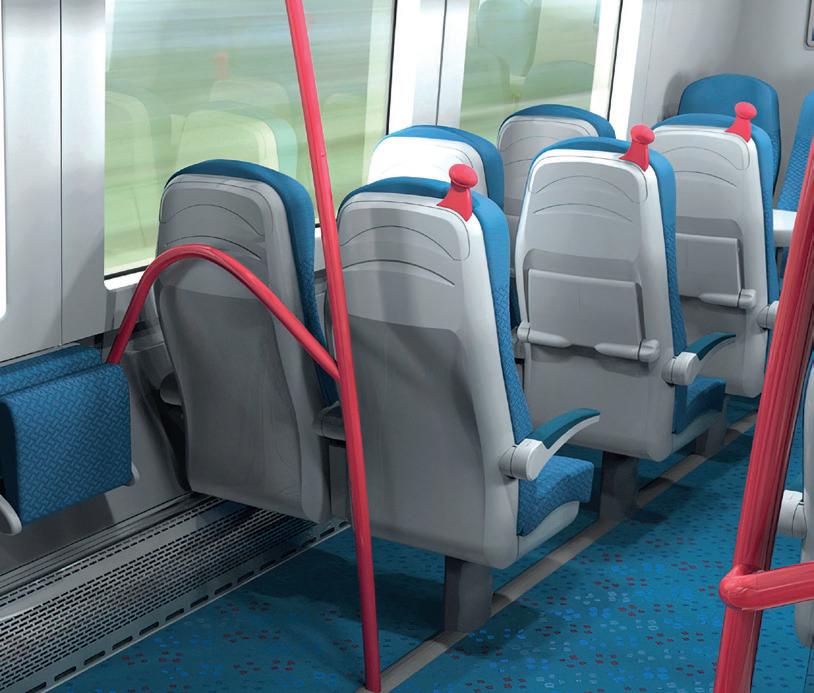
Industrial design
Colour, material and finish
Interior design
Livery design

Zoeftig
Contact module seating system
Engineering and visual design
Design research
Industrial design
Visual brand language
Mechanical engineering
Model making
Usability and HF
Productionisation
Are you sitting comfortably?
Does your chair ask you whether you are sitting comfortably? It may seem futuristic but the technology is available to monitor an occupant’s comfort in a seat and automatically adjust the lumbar support, back rest angle or head rest height, for instance, to provide real time posture control.
Article by Dominic Hargreaves Senior Sector Manager
We know that sitting isn't always the optimum experience for your health and that we need to stretch and exercise our muscles but this often isn't realistic, especially when you are travelling. Most of us usually wait until our back lets us know that we are doing damage though aches and pains before we do anything proactively to improve our seated comfort. We are even less likely to readjust our seat geometry to properly suit the demands of individual activities. In any case, it is often challenging to determine what combination of the multitude of available adjustments is actually going to achieve your personal optimal set-up. The “one size fits all” mentality adopted for the majority of seat designs now feels like an out-of-date concept. Now, whether you are travelling in a car, a plane or a train, Artificial Intelligence (AI) has the potential to improve your comfort, posture and health.
When setting out to design a chair, one of the first considerations is how the seat should feel. The received wisdom is that a seat should be soft for initial engagement, then firmer for the long haul. The basis of this approach is that when you first sit down you want to feel that initial embrace of the cushion (softness) and then as you relax into the journey, your seat needs to feel supportive in your optimum position (firmer) with a degree of flexibility providing the ability to shift your position slightly to relieve local pressure points or discomforts. This combination of softness, support and flexibility is what provides the comfort factor. There are great examples of welldesigned wooden chairs that can be surprisingly comfortable due to the natural give of this material when you initially sit down, the firm support after this initial contact, and the natural spring or flexibility when you move around.
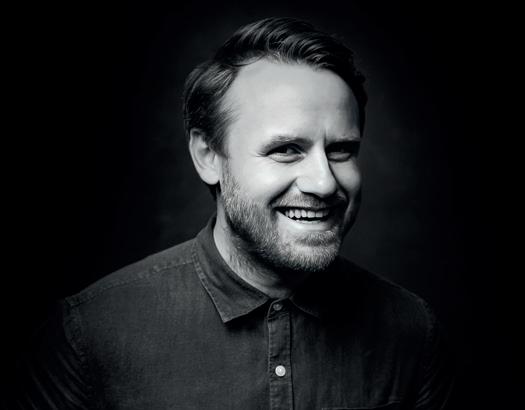
The concept of dynamic comfort is one where a seat adapts in real time to provide support where it is needed and adjusts over the length of journey to maintain a constant level of comfort over time. Harnessing the power of machine learning to process the inputs from a range of sources including pressure sensors and posture recognition software, we are benchmarking and developing new seats that provide this all important dynamic comfort factor.
The key step is to correlate real-time AI learning with seat movement to build a chair that makes micro-adjustments on the fly to keep your body comfortable in the optimum seated position.
It is no longer just luxury top of the range cars that offer a seat memory function to automatically return the seat to your pre-selected preferred settings. But how can a user be sure that these settings are actually optimal for them, and are the same settings always the most suitable in all situations? With AI there is now an opportunity to monitor the user’s behaviour in their seat and dynamically adjust the seat’s settings using the electrically powered adjustment mechanisms already provided on these seats.
The combinations of human body structure, weight, size and other physical variables, not to mention our own individual views on what we perceive as comfortable, are seemingly endless. So currently, compromises have to be made when designing seating to meet set constraints like a given seat height and width or a range of target user percentiles from 5% female to 95% male physiques. The aim of dynamic comfort is to avoid these compromises and get the chair to automatically and unobtrusively adjust to suit the user’s physique, posture and task, optimising your comfort level to suit your own personal preferences, while not irritating you through a constant series of microadjustments.
The automotive industry has now introduced seats that stiffen the bolsters when you are taking a corner at speed. This is a specific, controlled scenario but it shows the potential of automated control. We believe that AI can be harnessed, in conjunction with pressure sensors and posture recognition algorithms, to control seat adjustments in a practical and effective way to create seats with dynamic comfort features that deliver real comfort benefits for users.
Designing seats to actively look after your back and posture better than you could yourself must be an adjustment in the right direction.
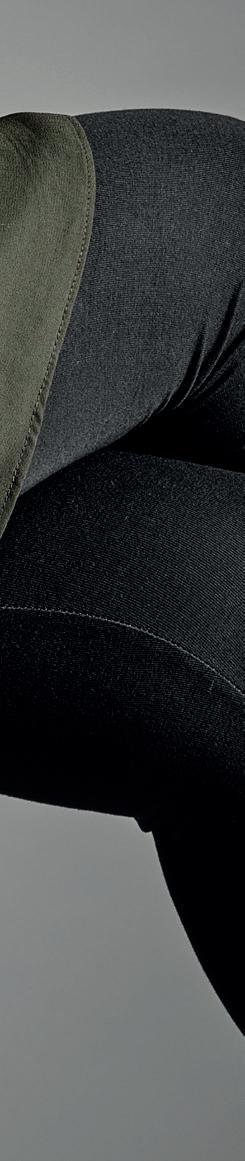
Our Location
We work globally from our campus of offices, studios and workshops in the historic town of Warwick, UK. We are located in the heart of the UK with easy road, rail and air transport links.
From Birmingham International Airport
Travel time 25 minutes
From London Heathrow Airport Travel time 1 hour 30 minutes
Birmingham
Warwick
London