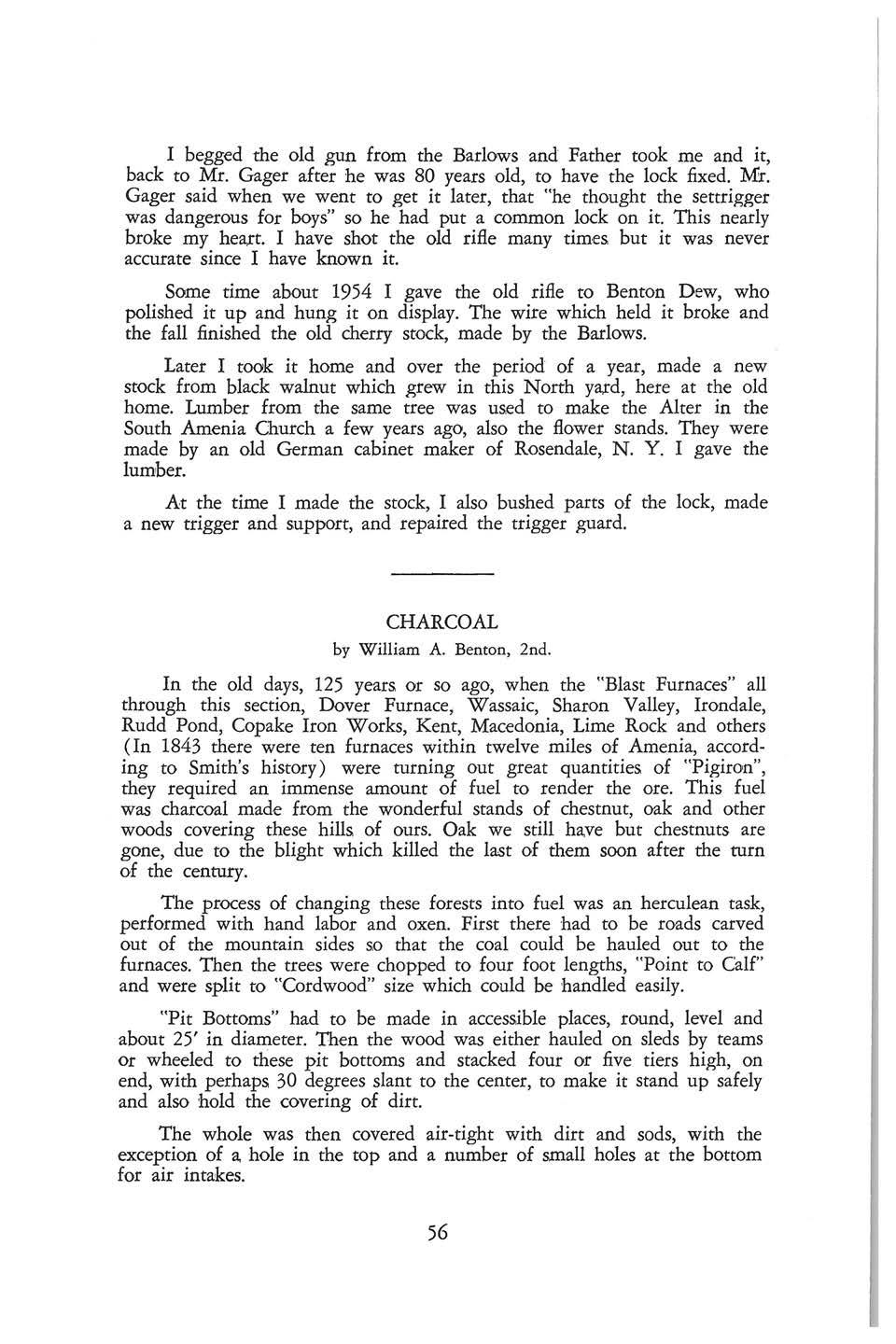
5 minute read
Charcoal
I begged the old gun from the Barlows and Father took me and it, back to Mr. Gager after he was 80 years old, to have the lock fixed. Mr. Gager said when we went to get it later, that "he thought the settrigger was dangerous for boys" so he had put a common lock on it. This nearly broke my heart. I have shot the old rifle many times but it was never accurate since I have known it.
Some time about 1954 I gave the old rifle to Benton Dew, who polished it up and hung it on display. The wire which held it broke and the fall finished the old cherry stock, made by the Barlows.
Later I took it home and over the period of a year, made a new stock from black walnut which grew in this North yard, here at the old home. Lumber from the same tree was used to make the Alter in the South Amenia Church a few years ago, also the flower stands. They were made by an old German cabinet maker of Rosendale, N. Y. I gave the lumber.
At the time I made the stock, I also bushed parts of the lock, made a new trigger and support, and repaired the trigger guard.
CHARCOAL
by William A. Benton, 2nd.
In the old days, 125 years or so ago, when the "Blast Furnaces" all through this section, Dover Furnace, Wassaic, Sharon Valley, Irondale, Rudd Pond, Copake Iron Works, Kent, Macedonia, Lime Rock and others (In 1843 there were ten furnaces within twelve miles of Amenia, according to Smith's history) were turning out great quantities of "Pigiron", they required an immense amount of fuel to render the ore. This fuel was charcoal made from the wonderful stands of chestnut, oak and other woods covering these hills of ours. Oak we still have but chestnuts are gone, due to the blight which killed the last of them soon after the turn of the century.
The process of changing these forests into fuel was an herculean task, performed with hand labor and oxen. First there had to be roads carved out of the mountain sides so that the coal could be hauled out to the furnaces. Then the trees were chopped to four foot lengths, "Point to Calf" and were split to "Cordwood" size which could be handled easily. "Pit Bottoms" had to be made in accessible places, round, level and about 25' in diameter. Then the wood was either hauled on sleds by teams or wheeled to these pit bottoms and stacked four or five tiers high, on end, with perhaps 30 degrees slant to the center, to make it stand up safely and also hold the covering of dirt.
The whole was then covered air-tight with dirt and sods, with the exception of a, hole in the top and a number of small holes at the bottom for air intakes.
56
When it was not feasible to use a team for bringing the wood to the pit, the callers used long, flat wheelbarrows with the wheel near the middle and the front slanted up. The wood was loaded crosswise and little paths were made to wheel on.
Before the wood was stacked there was a carefully laid pile of kindling placed in the center and an opening left to the outside as the wood was stacked, so that the kindling could be lighted with a torch.
Great skill was required to control the air and prevent the wood from burning up, or perhaps going out if not enough air was given, and to judge when the coal was completely charred and ready to be smothered.
Now! After quite a wait we have the coal properly burned and every spark of fire completely dead, WE HOPE.
Perhaps we sould say something about the colliers who burned the coal. Around here they were mostly French. Wonderful axe-men and very skillful in their trade. I think they usually contracted for the job of burning the "Bush" (Coal bush) at so much a bushel, "Delivered on the teamsters head". You can think that over till we get the answer later.
The next job was to get the coal down off these mountaians to the Blast Furnaces. Heavy lumber wagons were used for this, with deep, hopper shaped bodies, not very long because they could not get around on the narrow mountain roads, I think about twelve feet, but six or seven feet wide at the top, and about eight feet high from the ground. The bottoms of these bodies were made of 2 x 6 planks, each with an eye on the back end, which were pulled out by these eyes, one at a time with the team when unloading.
The collier had to uncover the charcoal, fork it into baskets, which were large and rather flat I have been told, and help the teamster to put it on his head, who would then walk to the wagon, up a wooden horse of suitable height and dump the coal into the hopper. Helping the teamster set the basket on his head was part of the contract.
I said "We hoped" the fire was all out for sparks were a real hazard. Every teamster carried a pail and was always ready to run his team to the nearest brook to douse a fire. Sometimes they did not make it and lost their wagon. Also this fire hazard dictated that each load of coal be dumped in a separate pile on the "Charging field" of the furnace, so that if fire did occur it would be confined to one load.
On the furnace bank at Wassaic there are two large charcoal pits built of stone with doorways at both top and bottom, in addition to air openings. These are considerably larger than the dirt covered pits in the woods. The wood was hauled to these stone pits where available, which saved a great deal of work in covering the mountain pits and also had the advantage of being at the furnace where it was loaded directly into the "charging" carts.
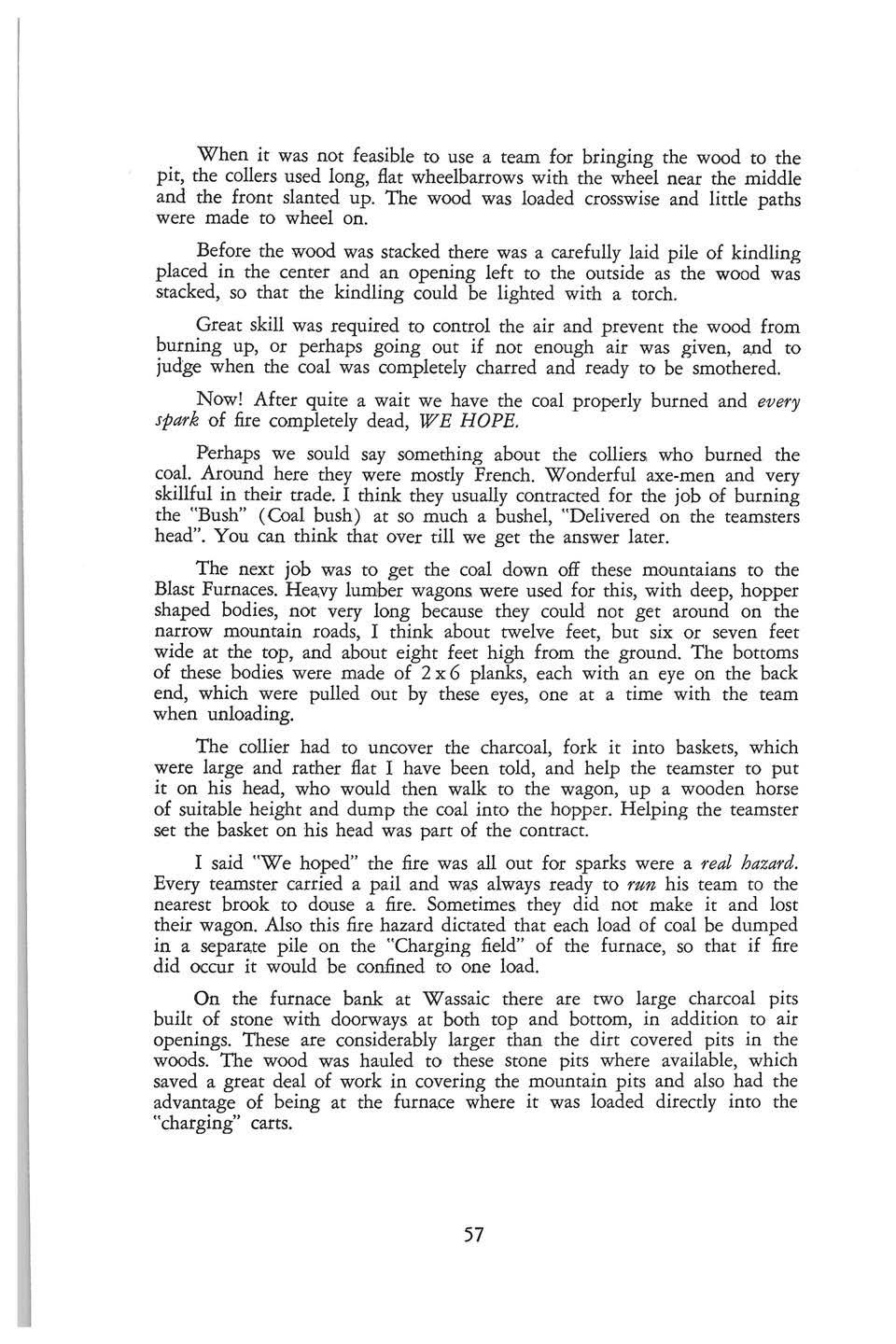
57