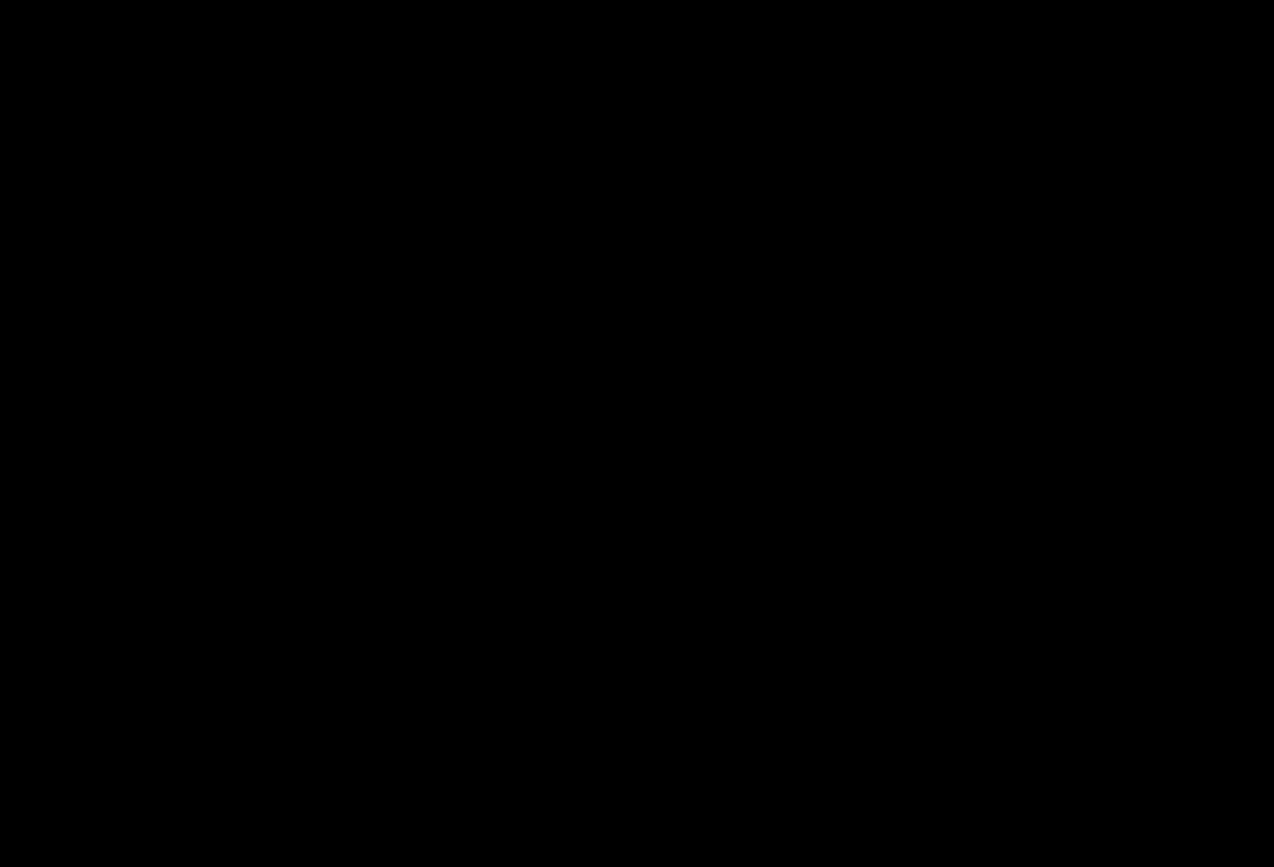
7 minute read
ENVIRONMENT
Combs and Beaters: Made of wood or metal or both, weaving combs and beaters push the weft down toward the beginning of the weaving. This process tightens the weaving. The teeth of these tools are just wide enough to fit in between the strands of the warp. Shuttle: It is easier and faster to use shuttles made for working with different kinds of yarns. Ski and rag shuttles are made to handle thicker yarns, which are wrapped lengthwise around the shuttles. Boat shuttles work more quickly owing to the presence of a bobbin in the bobbin's center. The bobbin holds yarns of medium and fine thickness. Spool Rack: Spool racks allow you to keep your fibers organized while you are weaving. They also prevent unwanted knots as they keep each thread of fiber separated from any other threads while being fed into the loom. YARN DEPOT
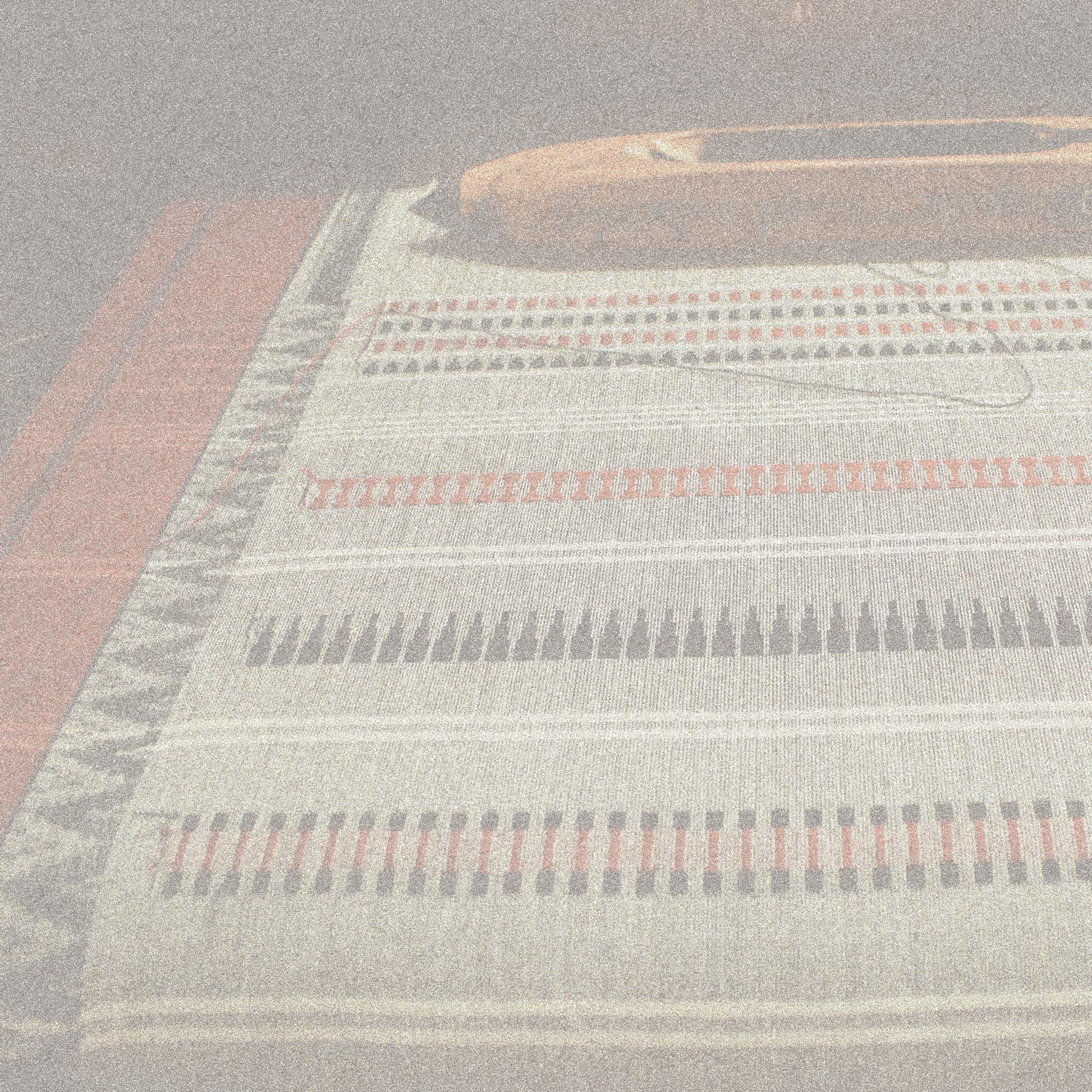
Advertisement
At Begampur earlier weavers‘ groups had to pay the National Handloom Development Agency (NHDA) in advance for the purchase of yarn. After the implementation of the IHDS, the Government paid three lakh rupees to the NHDA in order to ensure seamless supply of yarn to the weavers at the yarn depot in the cluster, which was also built by them.
DYEING PROCESS
Dyeing is a process of imparting colour to fibers, yarns, fabric or garments. This is done by exposure to dyes, which are coloured substances with affinity towards the substrate that is to be dyed. In Begampur, usually yarn dyeing is carried out. Yarns are received in hank form. To
achieve proper white colour, they are bleached. Yarns are also bleached if they are to be dyed in a light colour. For darker shades, bleaching is not required.
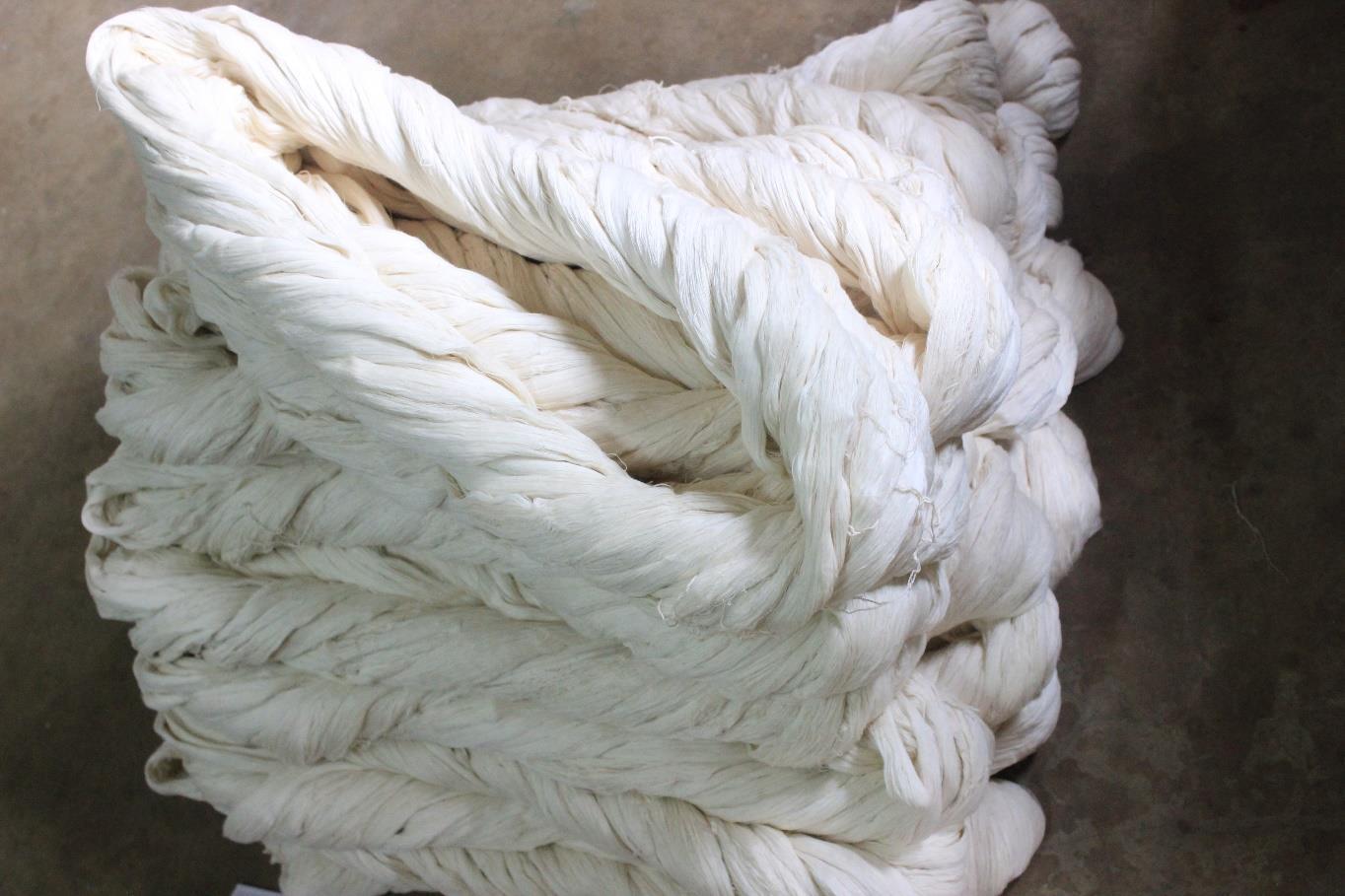
FIGURE: 6.5- RAW YARNS
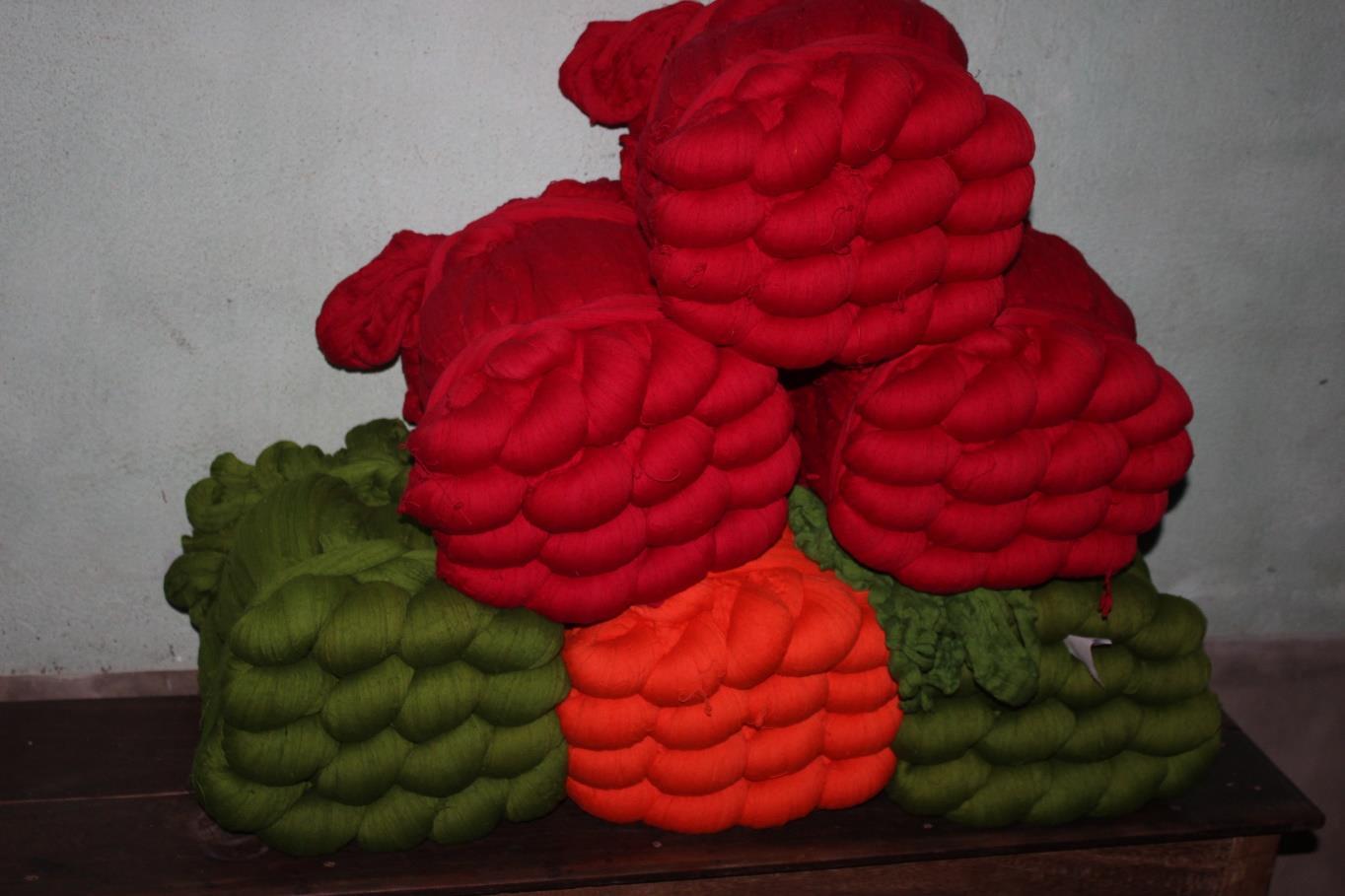
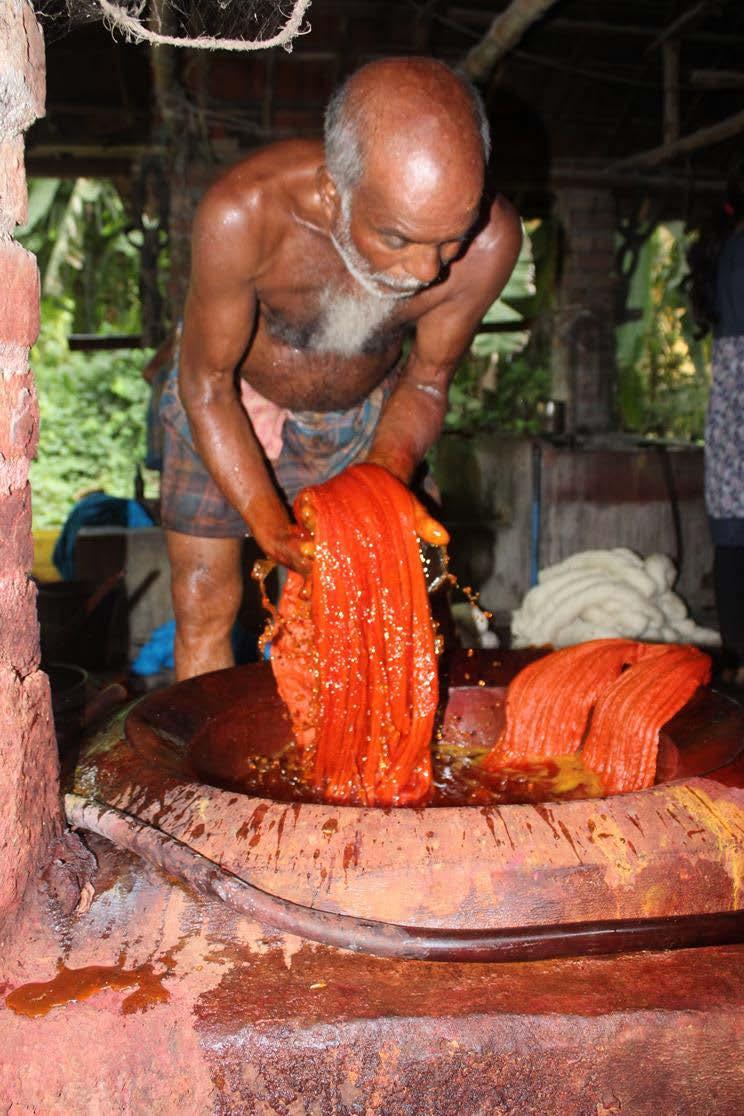
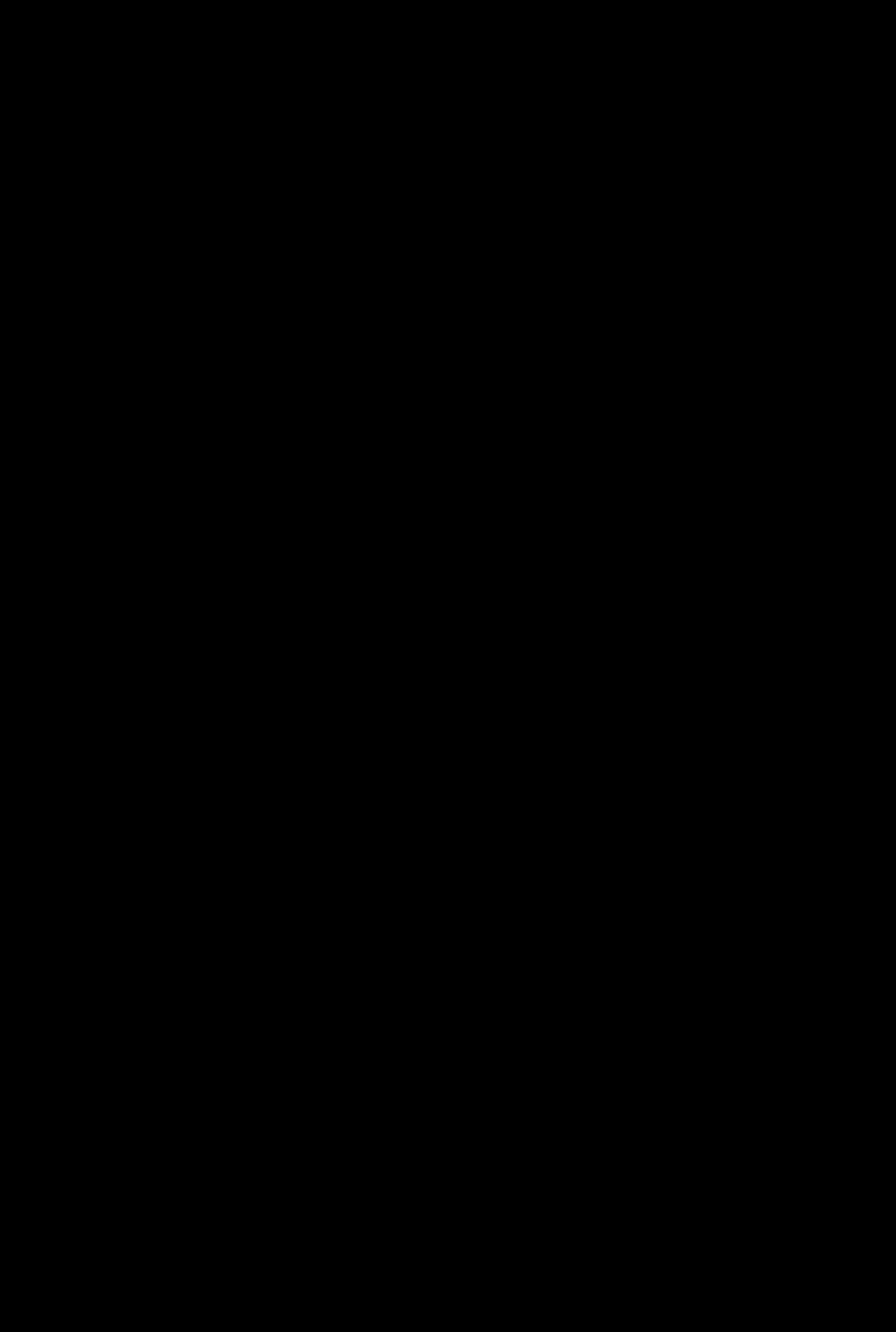
For dyeing, usually direct dyes are used. They are cheap and do not affect health adversely. The water used to be soft water, because hard water has impurities that hinder the dyeing process. Sometimes, rain water is reused for dyeing as they form an ideal environment for the dyes to work. The dyer uses two wooden sticks to handle
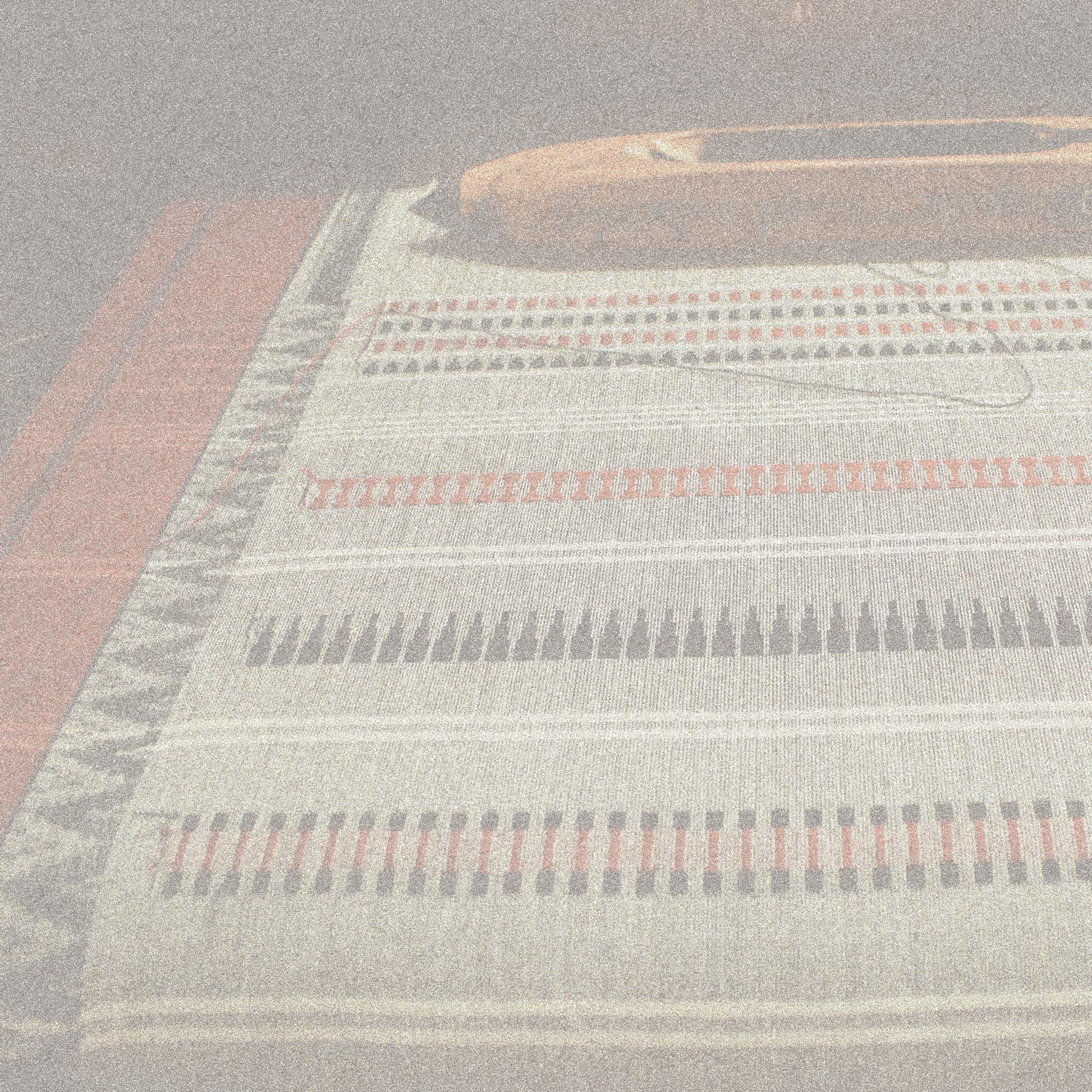
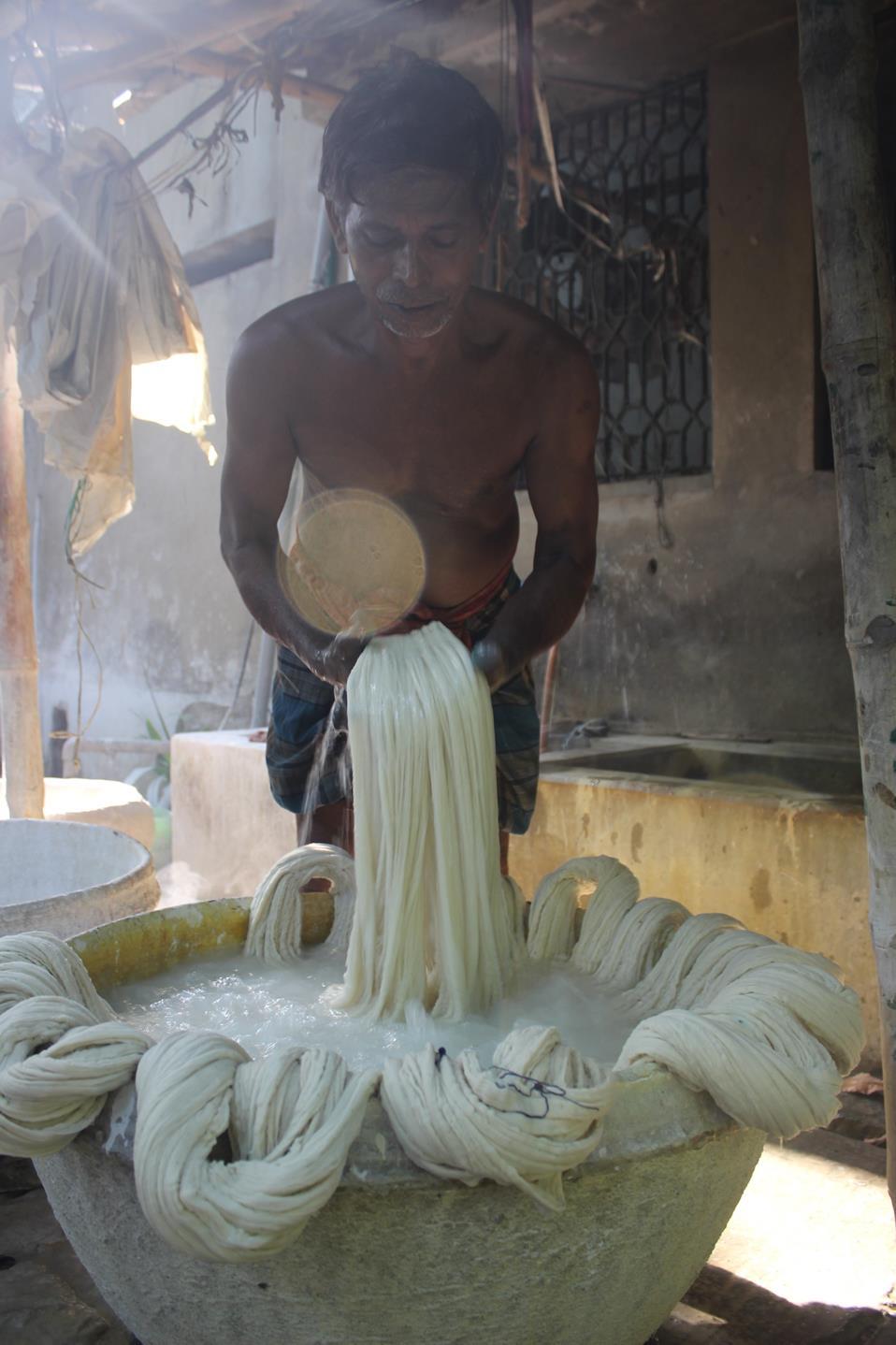
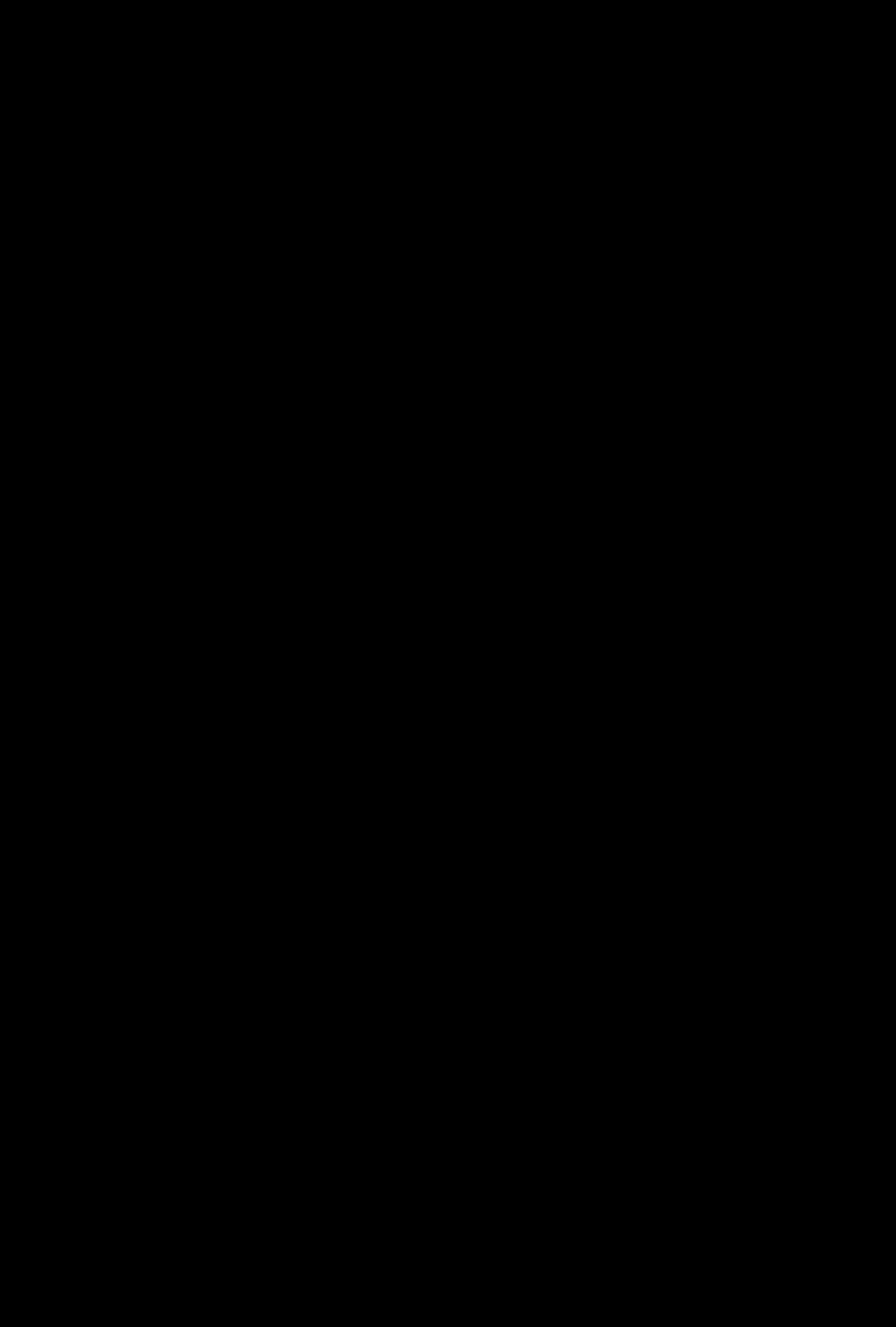
the hanks during dyeing process. They use it to put the yarns into boiling water bath, to take it out, squeeze the coloured water from it and then to dip it again into the same bath. When the dyed batch of yarns matches the shade of the approved sample, it is taken out of the dye bath. For dyeing yarns black, sulphide is used. And if same hank is to be coloured with two colours to give ombre or striped effect, hank is either half covered with plastic or tied tightly with some different yarn respectively. A hundred grams of dye is required for dyeing one kilogram of yarns. After dyeing, the hanks are dipped in cold water. Then it is washed with a glycerine soap called ‗Monopoly‘, to remove all kinds of oil or stain.t since they cannot achieve too many colours from only this type of dye, sometimes vat and napthol dyes are used too. However, vat dye is quite expensive, so yarns dyed with them are more expensive too.
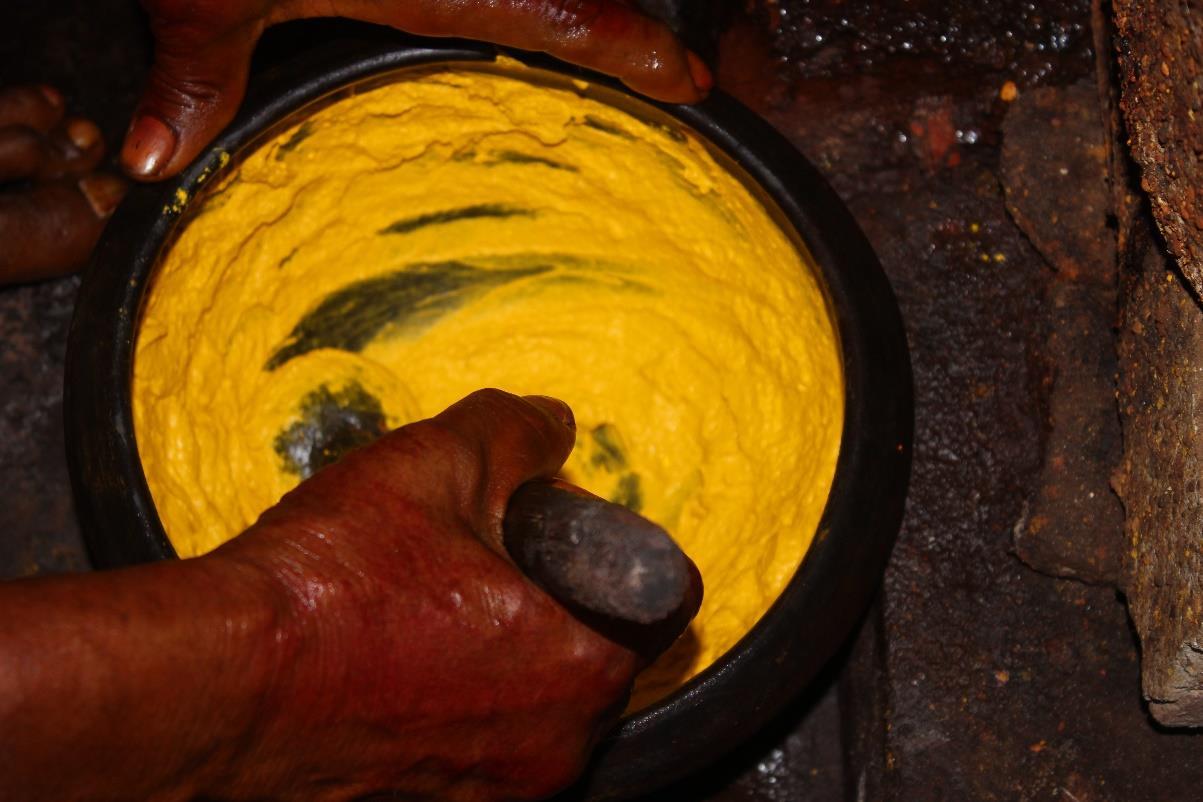
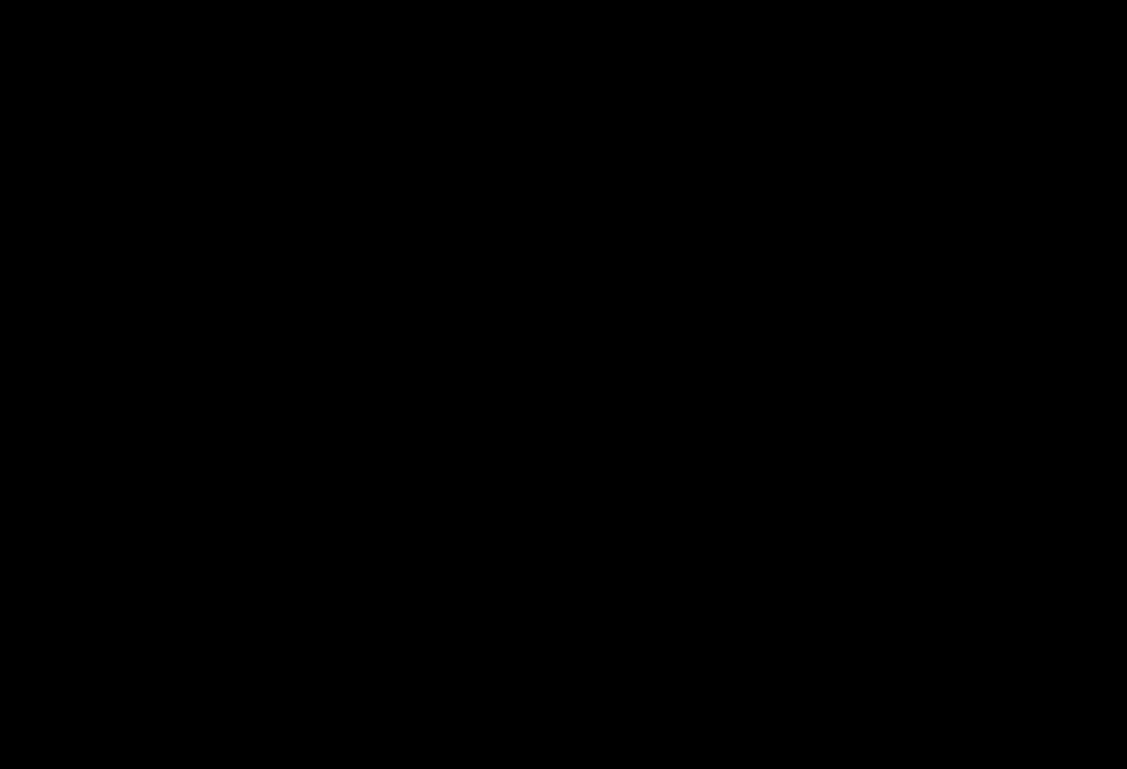
FIGURE: 6.7- WASHING OF RAW YARNS The water bath for each type of dye is different. For direct dye, the bath contains hot or cold water, with salt and caustic soda. For reactive dye, it‘s salt and soda in water at room temperature. For vat dye, there is caustic soda in hot water, and for napthol dye, it‘s salt in cold water.
The yarns are immersed in the proper bath and undergo the actual process of dyeing. It is done according to the approved samples dyeing recipe. Yarn is immersed in water bath for two hours for proper dyeing to occur. It is important after dyeing, excess water from the hanks are removed and then they are kept to dry under the sun. During sun-drying, oxidation occurs on the surface of the fabric, which may lead to slight change of colour. Once dried, the coloured yarn undergoes the pre-processes of weaving.
FIGURE: 6.9- DYEING OF YARNS
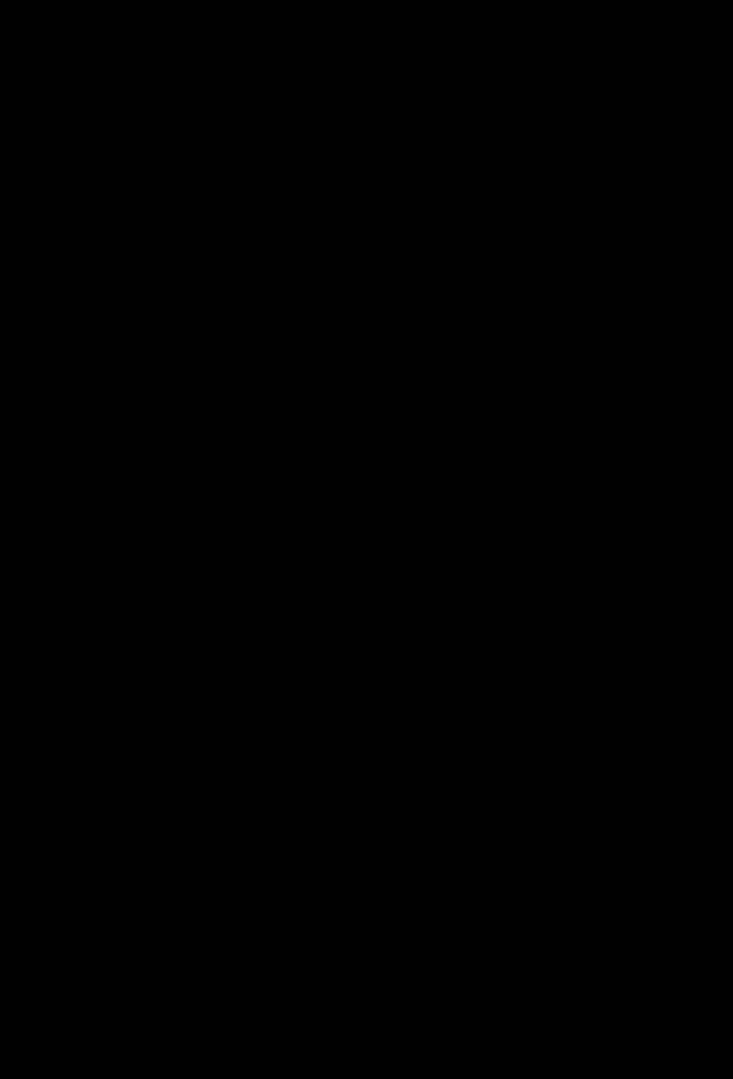

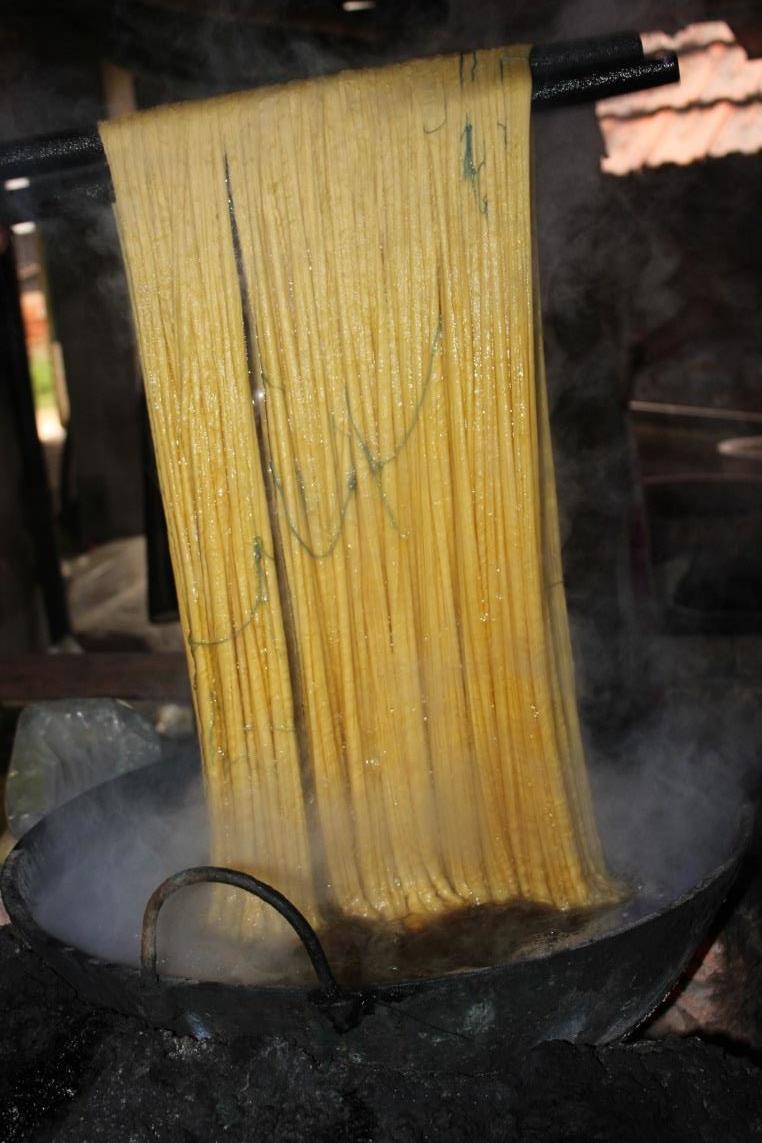
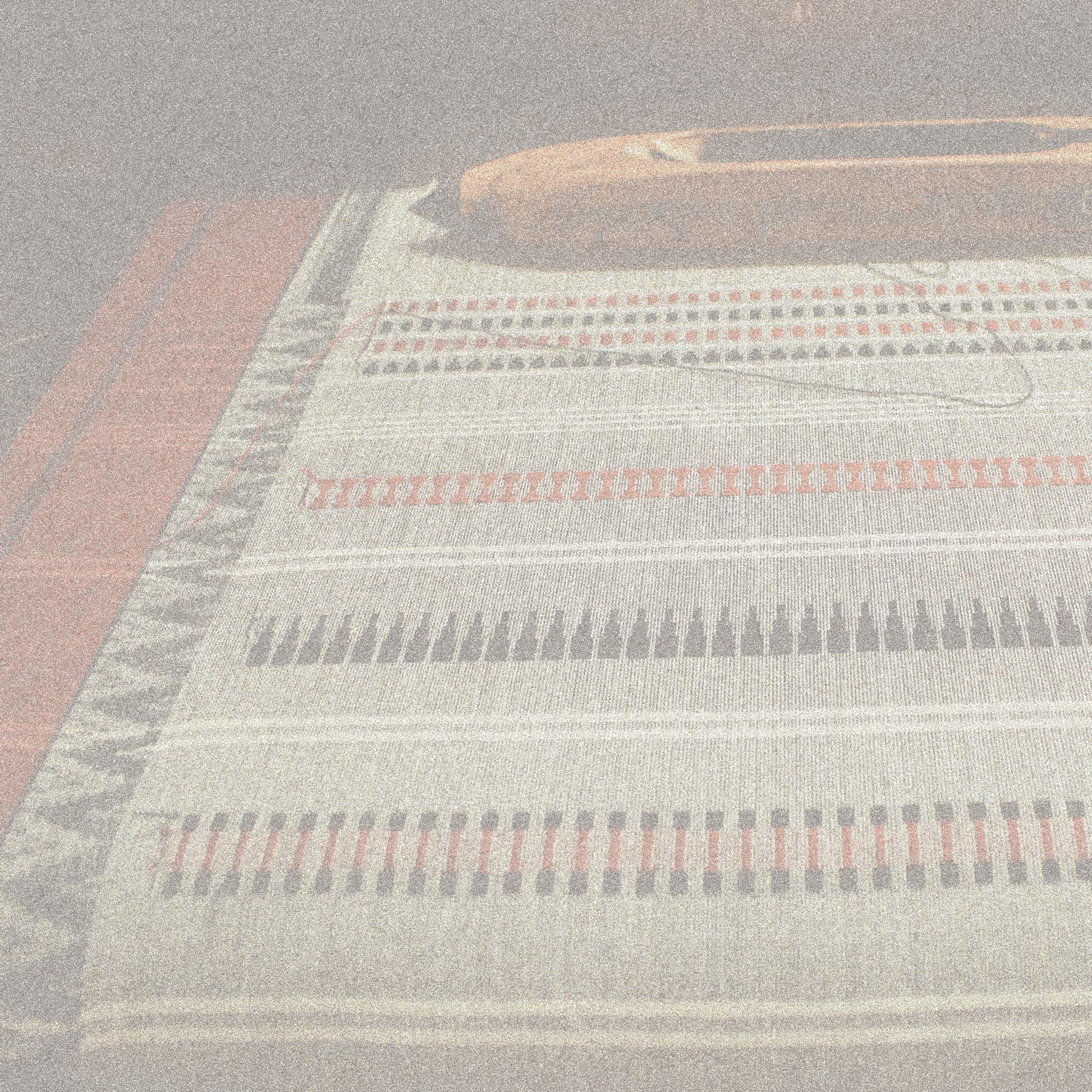

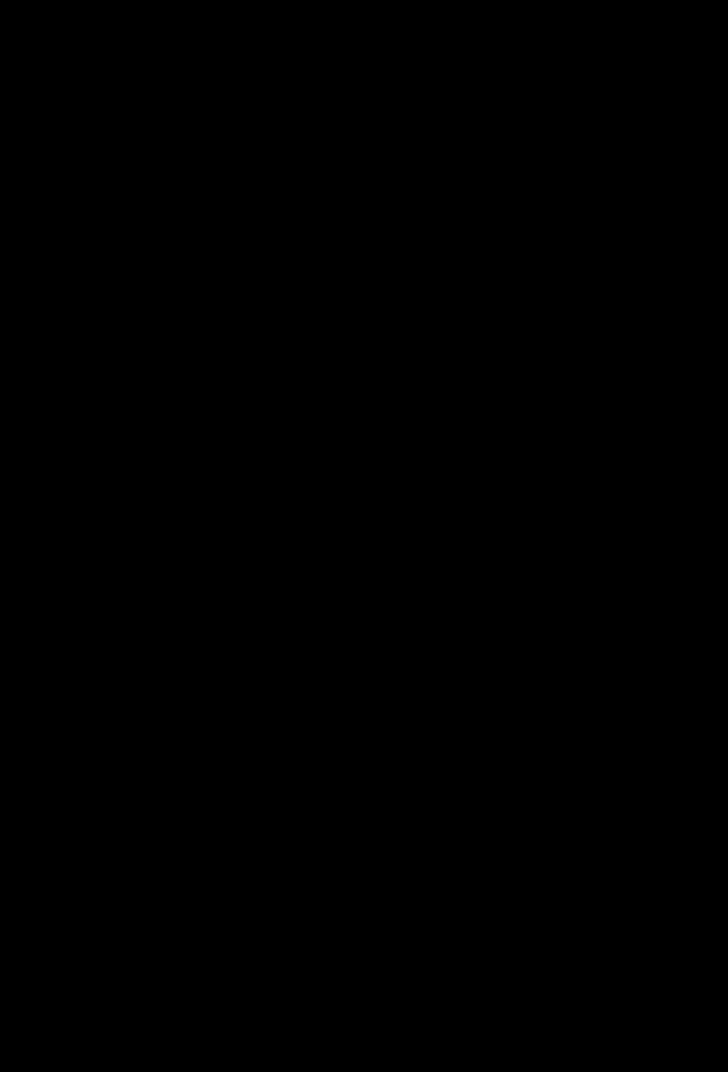
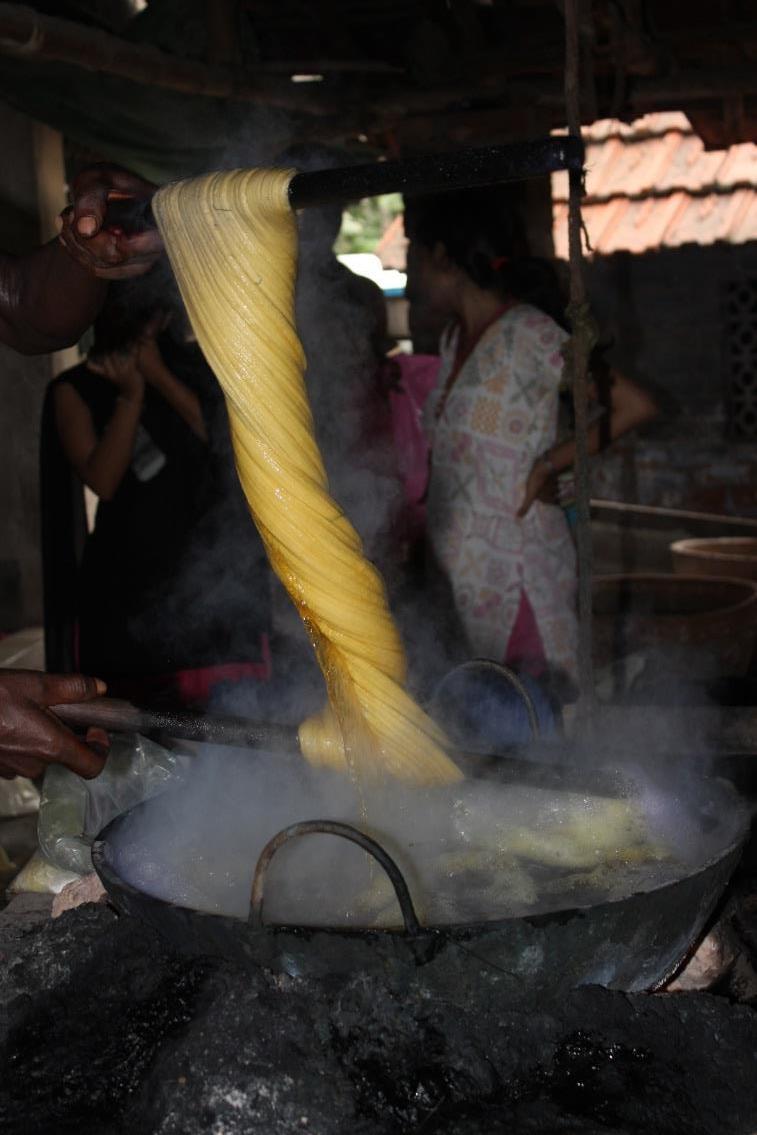
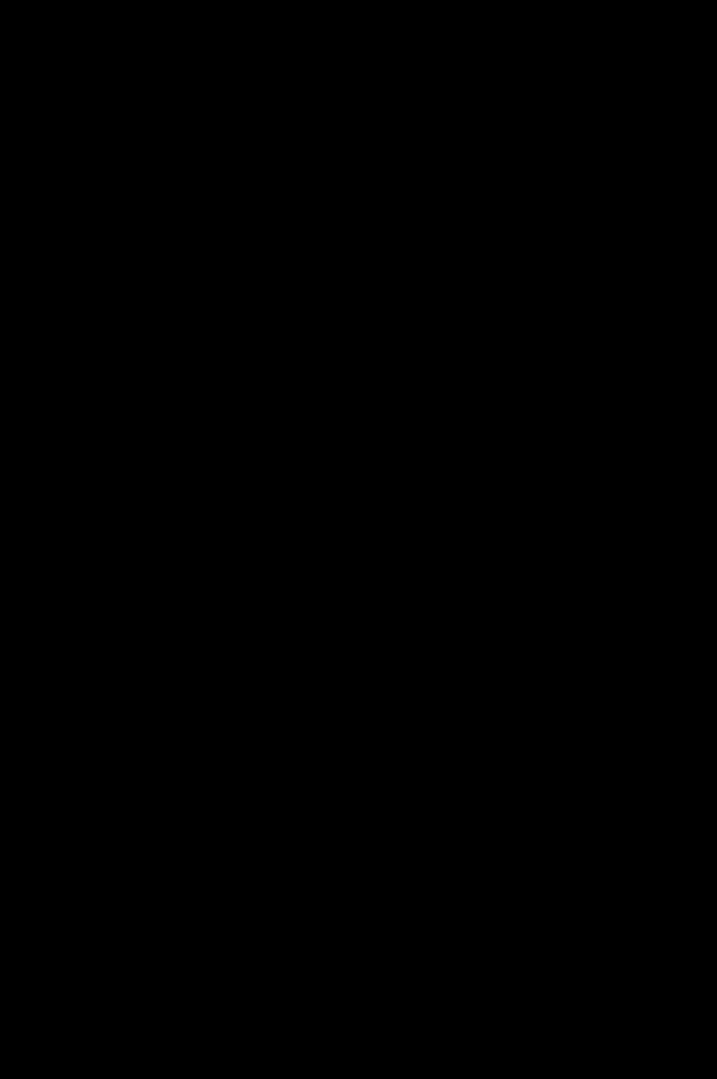
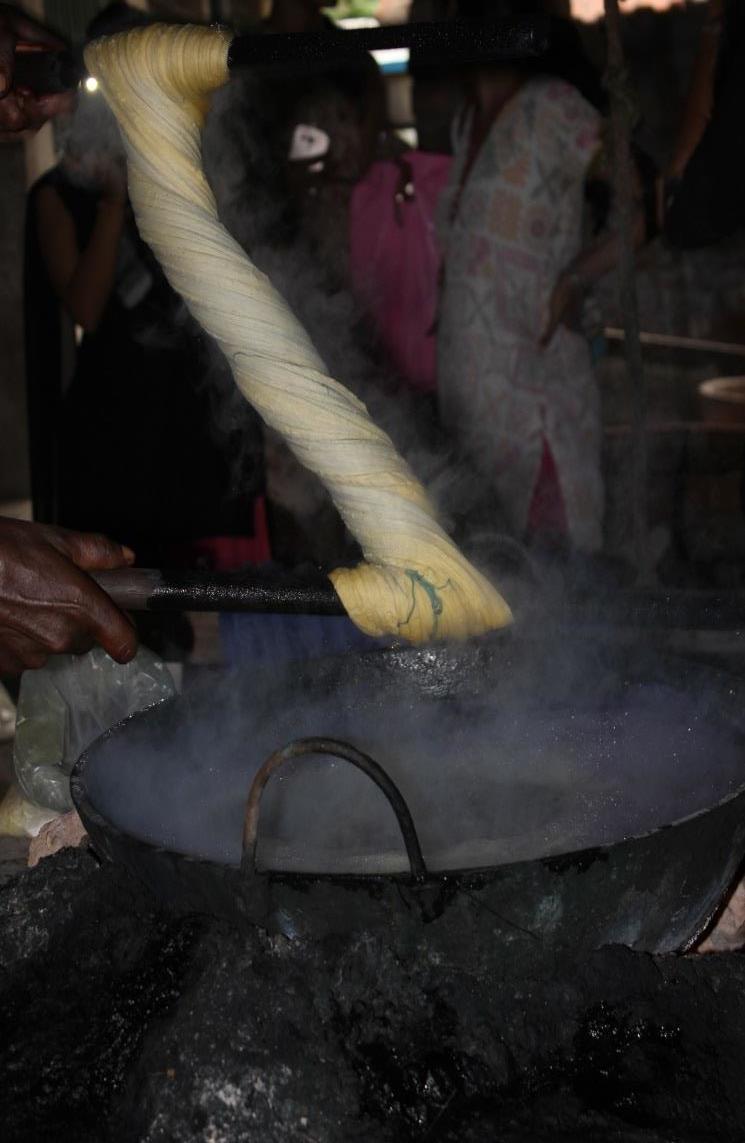
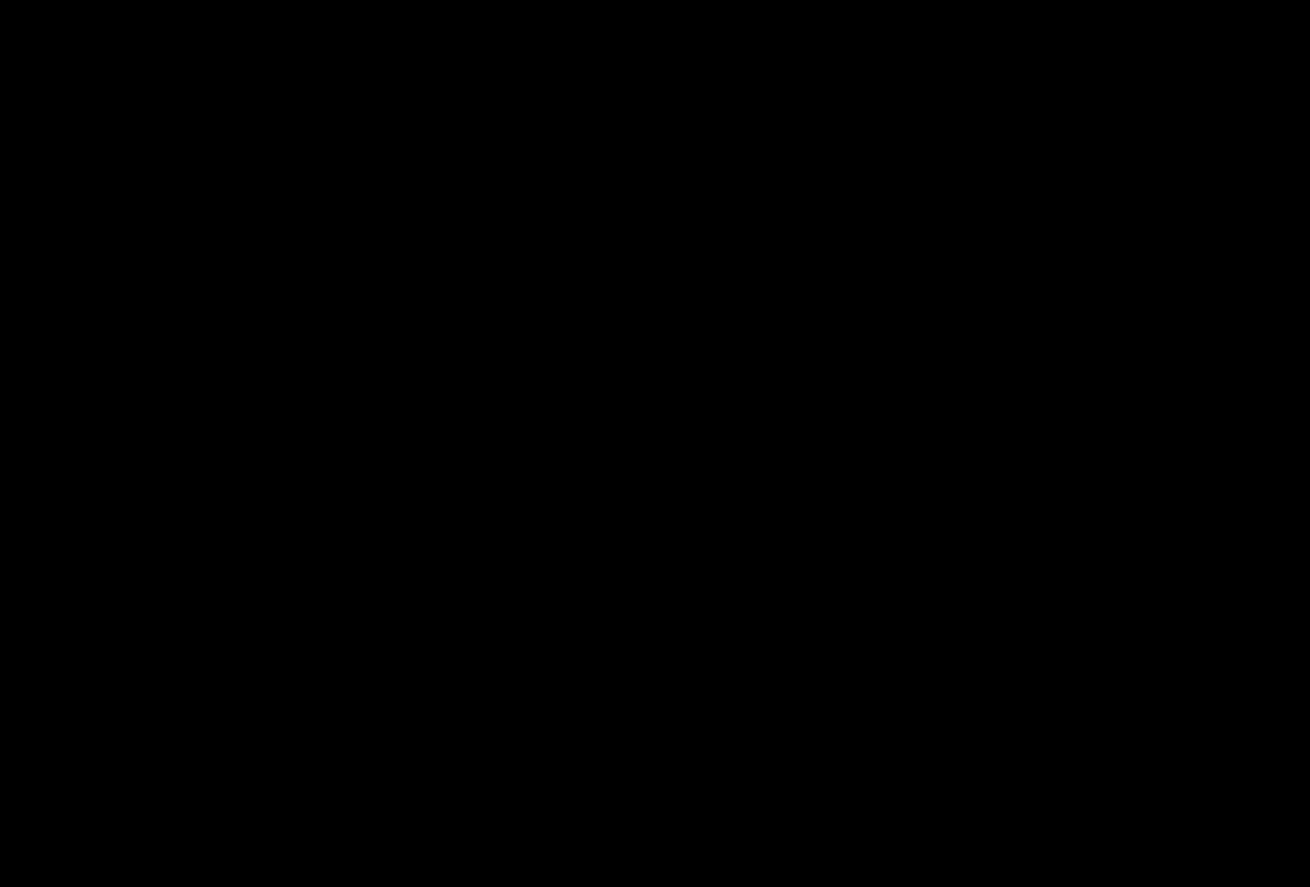
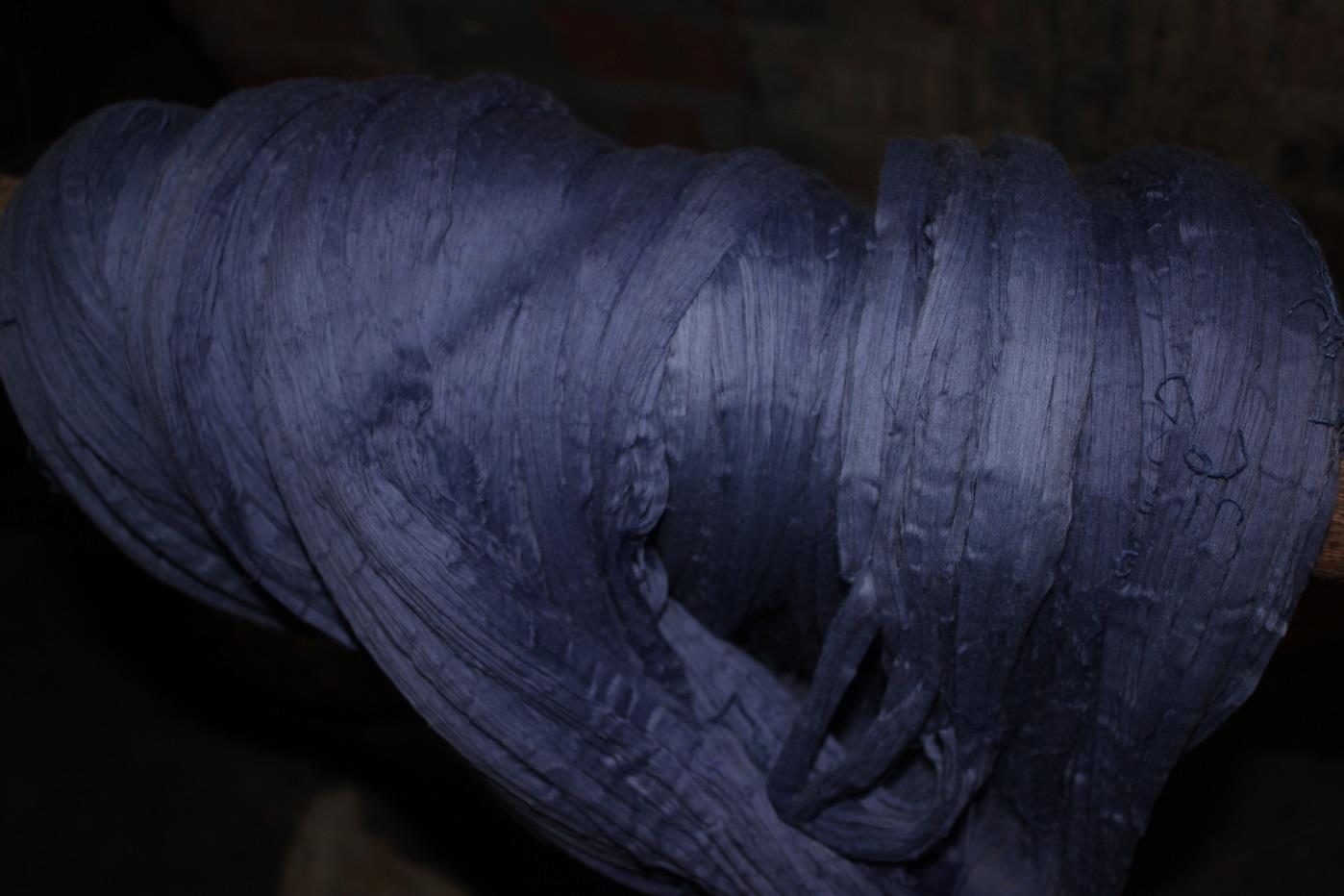
FIGURE: 6.10- DYEING PROCESS OF YARNS FROM VAT DYE FIGURE: 6.11- YARNS AFTER DYEING
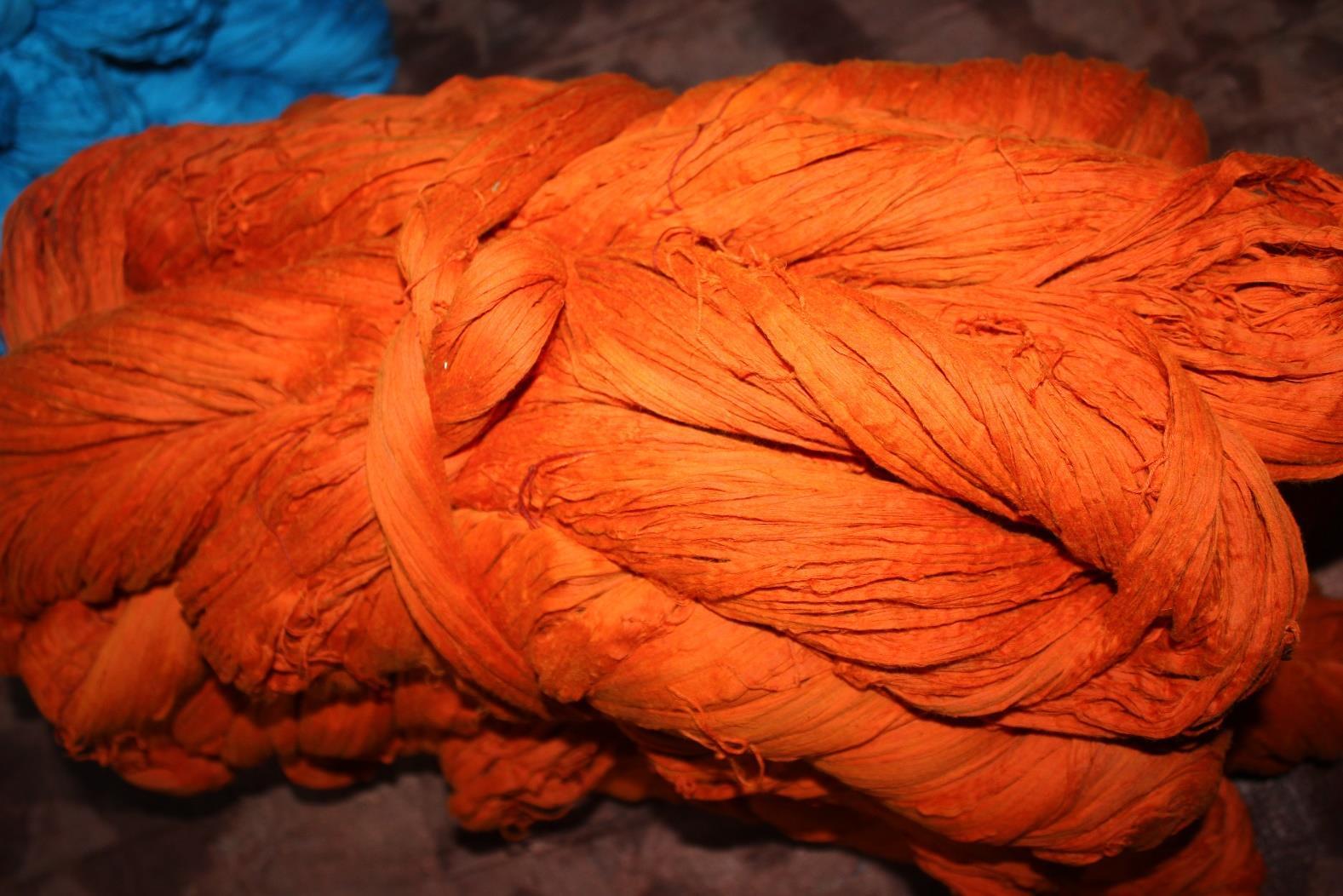
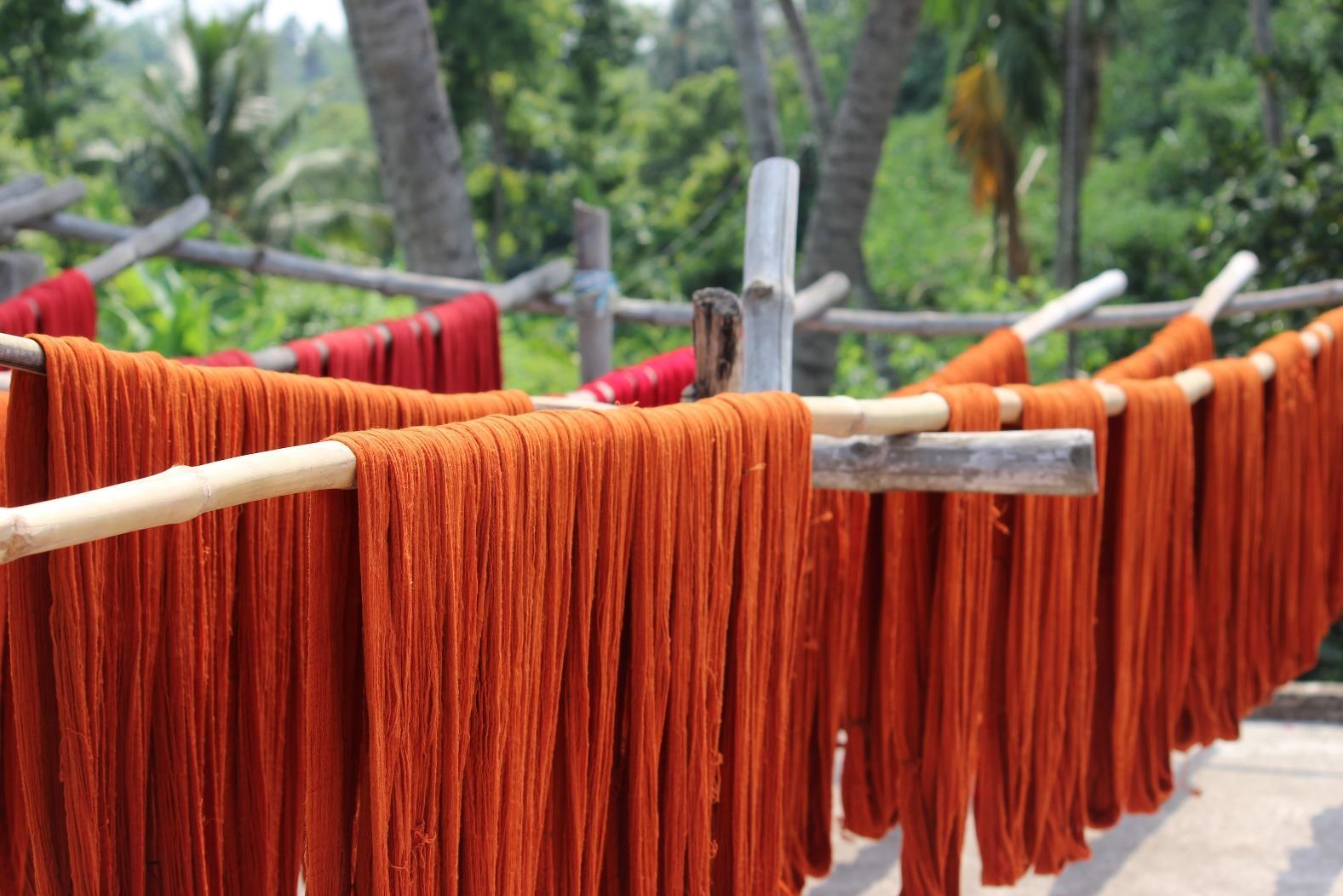
FIGURE: 6.12- DRYING PROCESS OF DYED YARNS
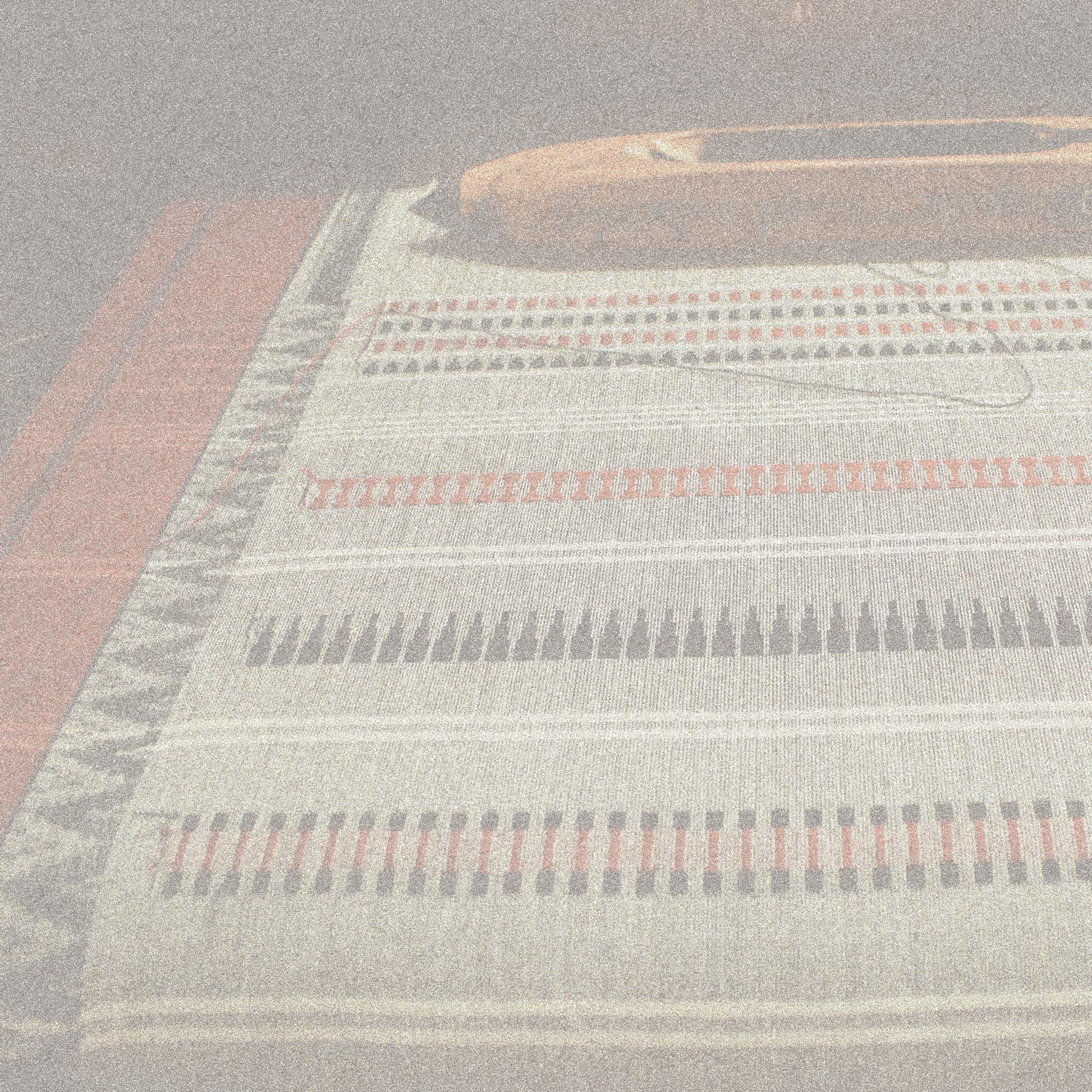
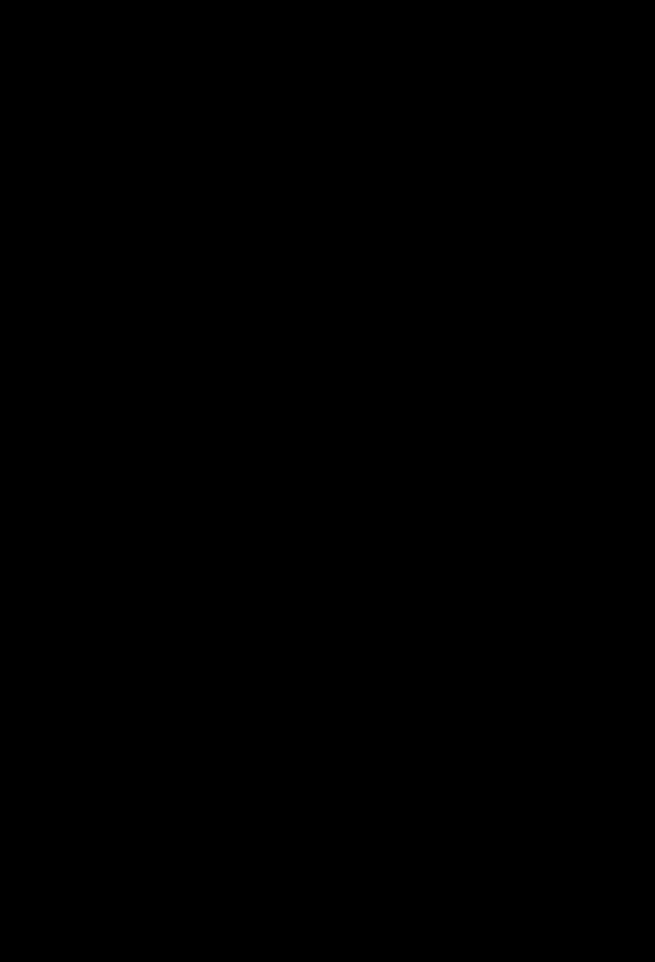
The first process is called sizing. Sizing is a process of applying an adhesive size paste to yarns to facilitate weaving. This is often called the ‗heart of weaving‘. Its main functions are to improve the weave ability of the warp yarn, increase the elasticity of yarn, increase it tensile strength, to smoothen yarn surface and thus reduce electrostatic charge formation. At first, the size is prepared. who wake up early, complete their household chores and then get to work with sizing. The most popular way of making size is with starch or ‗maar‘, but in Begampur, most people make size with ‗saabu‘ and blue vitriol. The two ingredients are boiled together in a container and are stirred continuously. Once the size is prepared, it is rubbed continuously to the ball of yarn for a long time, so that all areas are covered properly. Then the yarn is passed first through a charkha and then a charkha for winding onto bobbin. The charkha may be manual or automatic. Then comes warping.
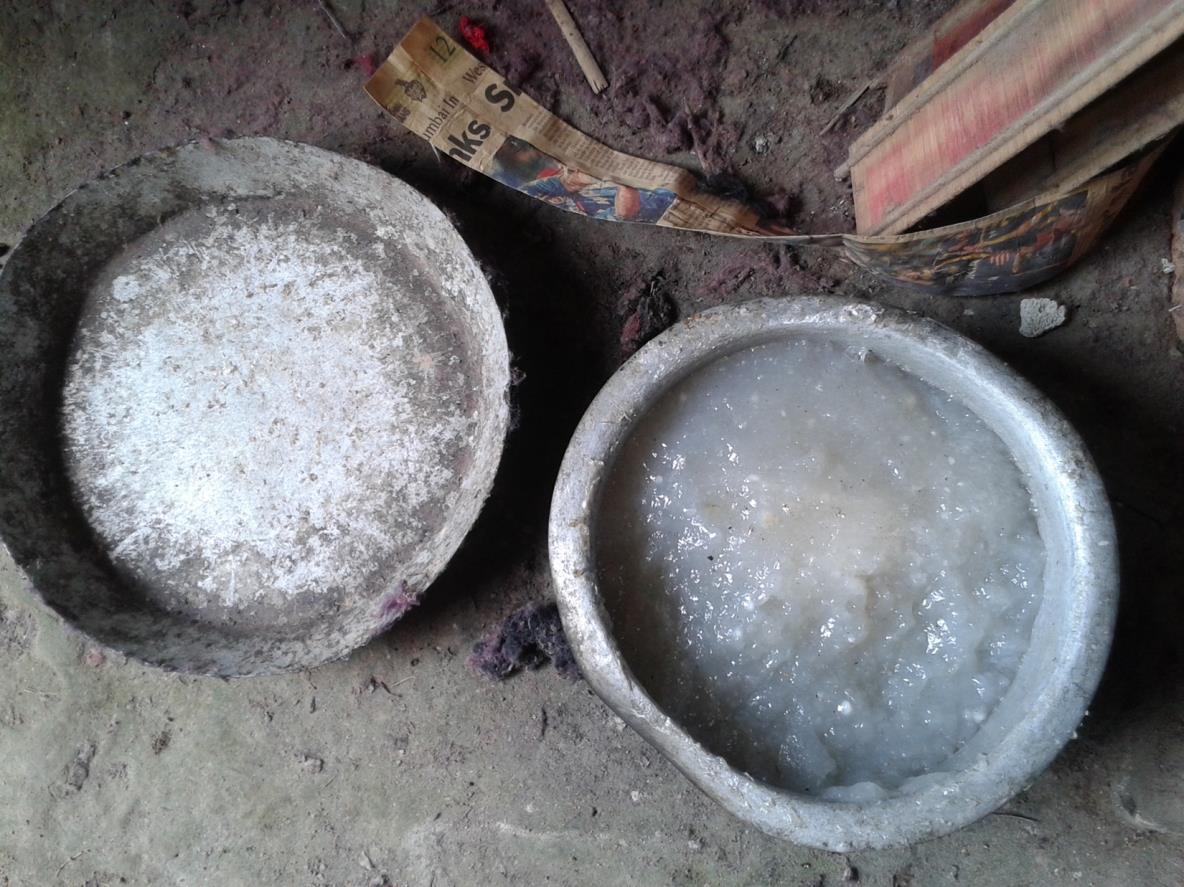
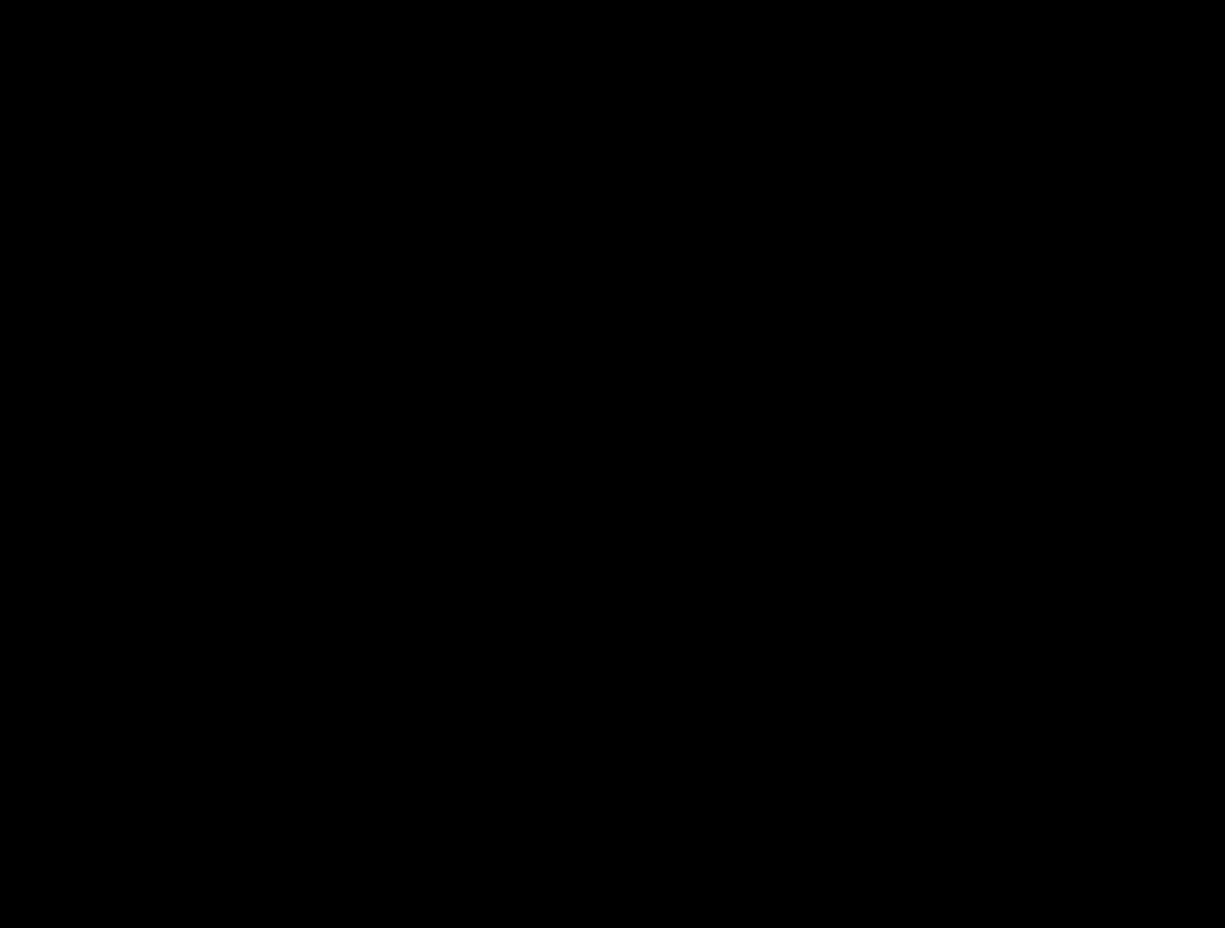
FIGURE: 6.13- SIZE MIXTURE
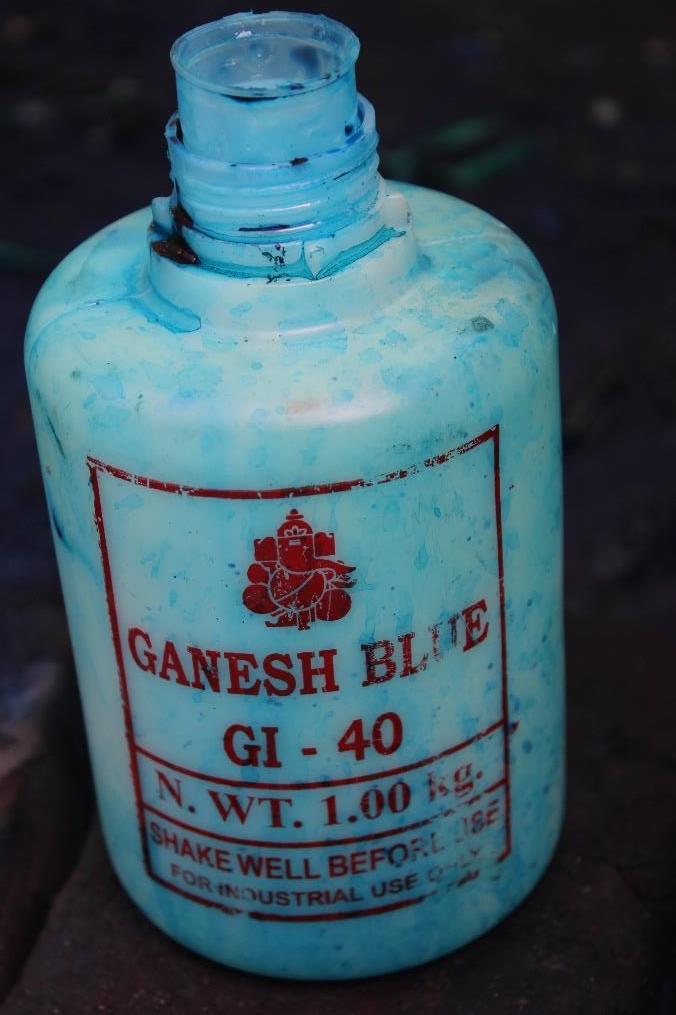
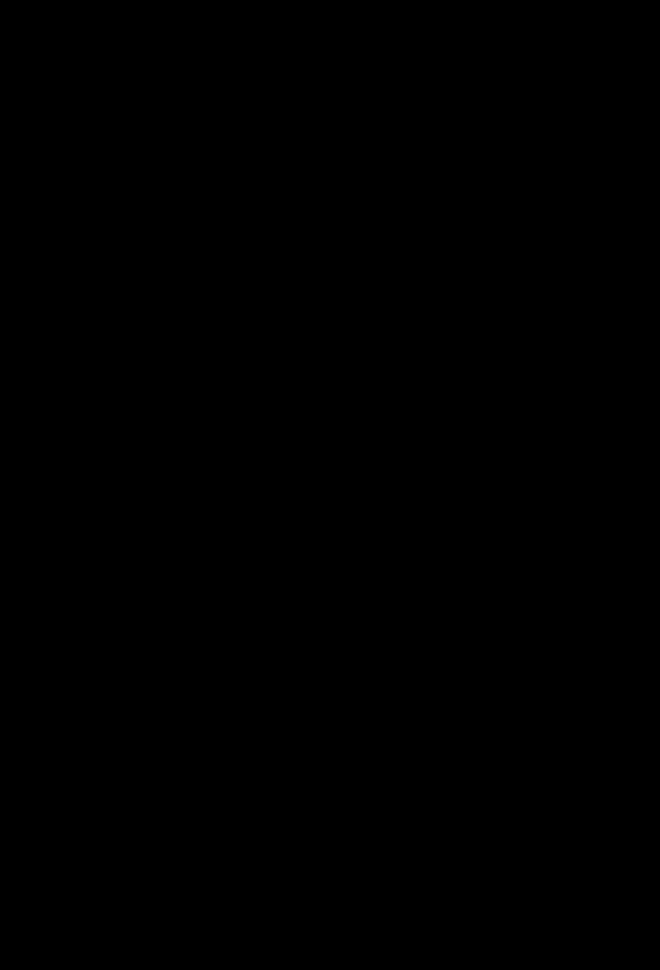
FIGURE: 6.14BLUE VITRIOL
FIGURE: 6.15- BOBBINS WARPED WITH YARNS WARPING This comprises winding parts of the warp yarns, normally from bobbins, on a warping beam, whereby sequential parts are wound next to each other until the full weaving width is covered. The warping beam is then normally in a next step of warp preparation used for beaming. BEAMING
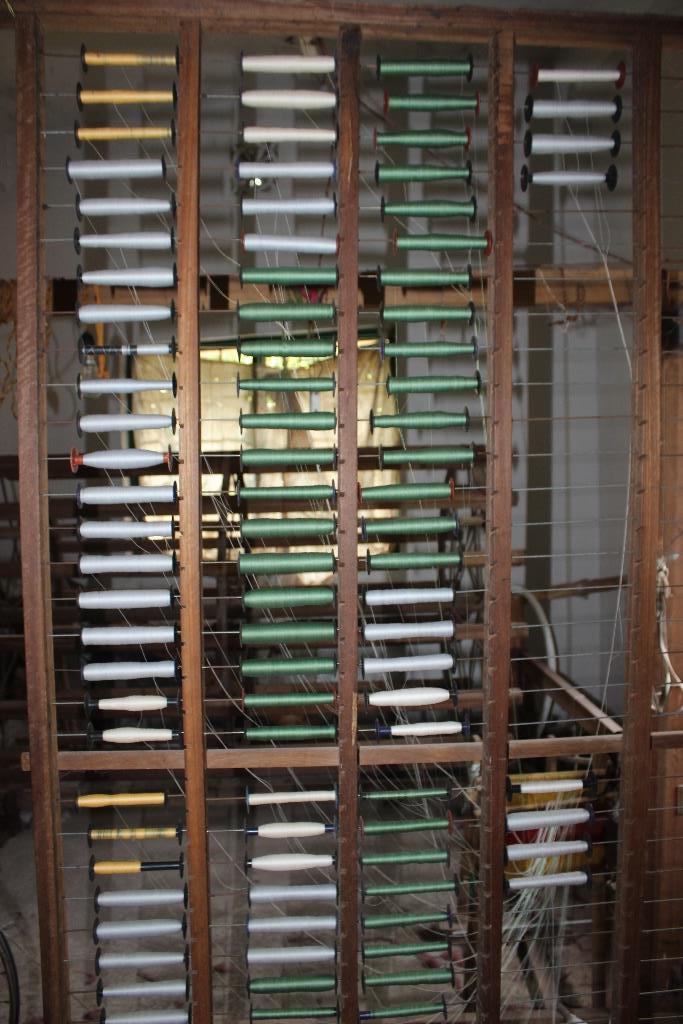
Beaming comprises winding the full width of the warp yarns in a single winding operation on the weaving beam (i.e. the beam which is to be placed on the loom). The warp yarns can be wound from a creel or a warping beam.
The next step is leasing.
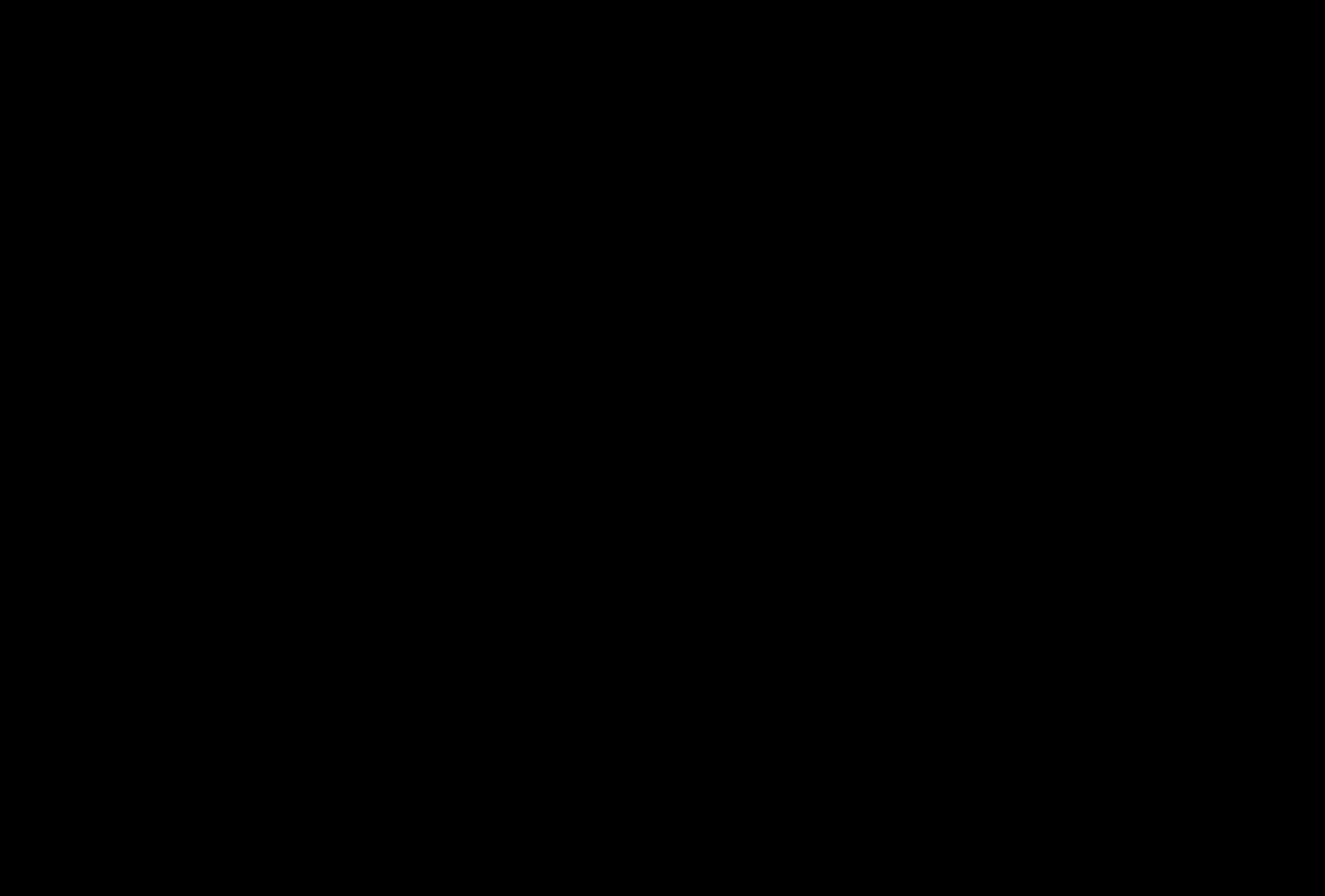
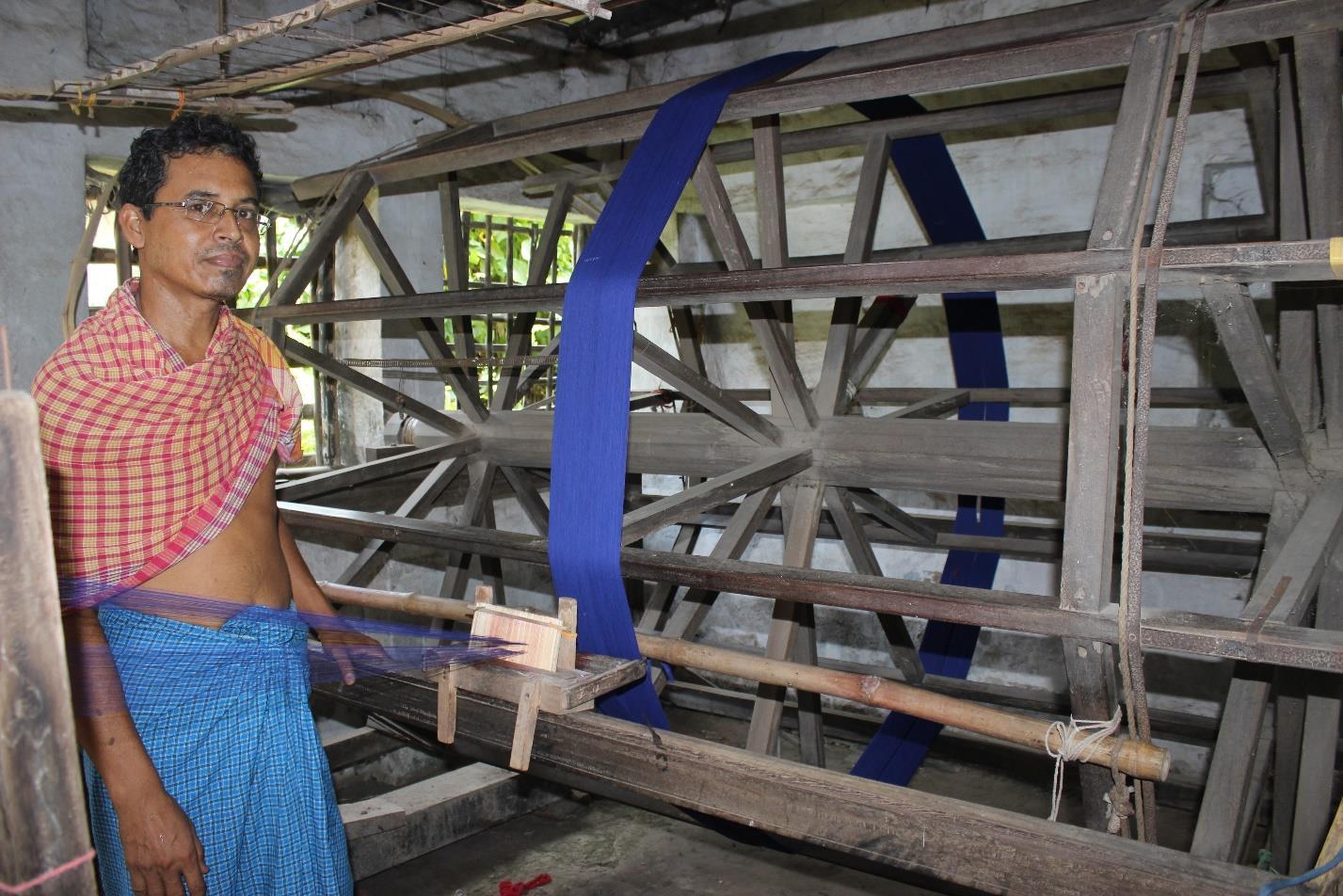
FIGURE: 6.16WARPING

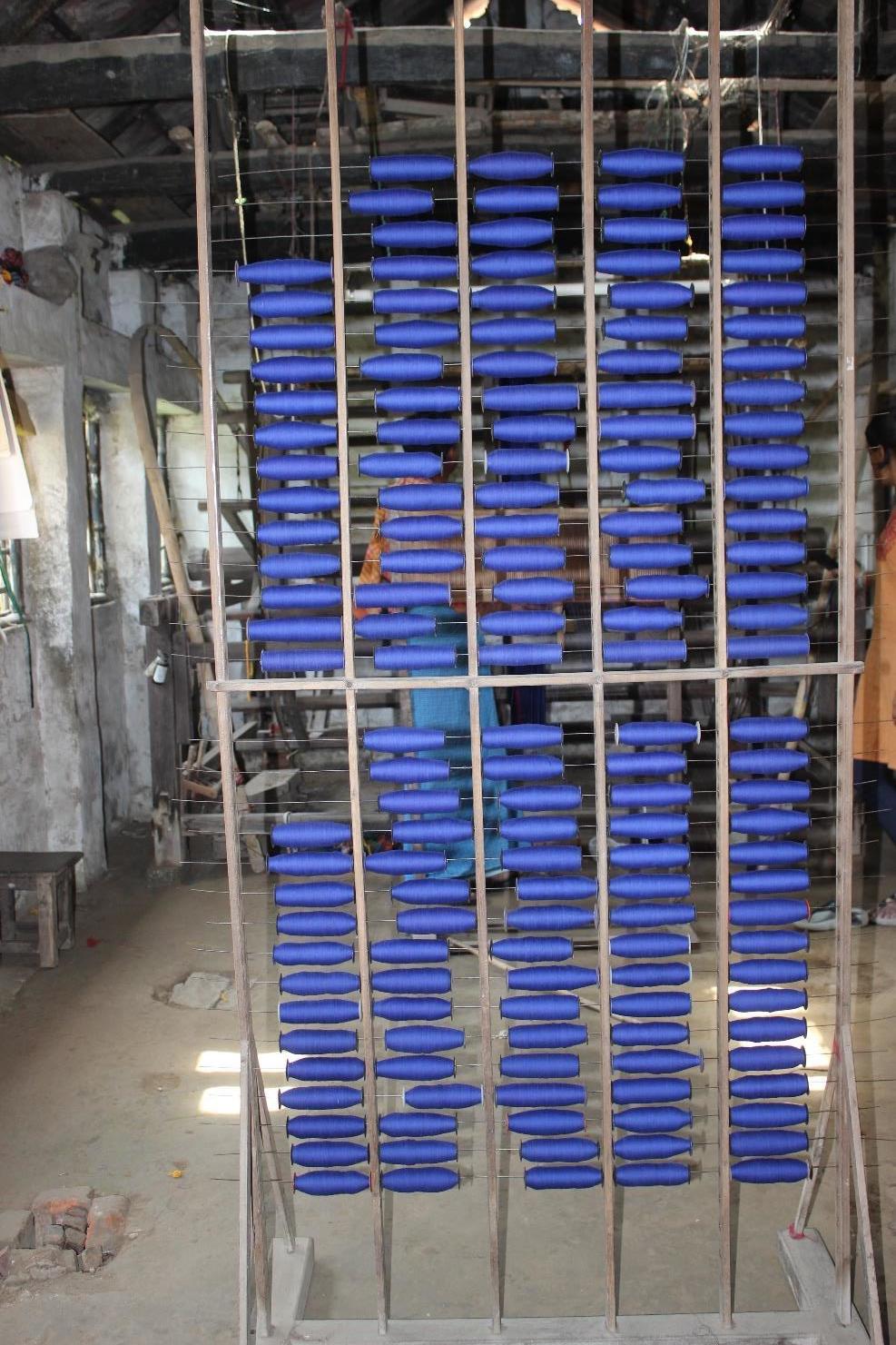
This comprises inserting lease cords between the warp yarns to separate groups of warp yarns. A lease is needed to be able to separate the individual threads in a warp sheet from one another, or to precisely define the thread sequence. This process establishes the warp ends in the required sequence.
The warp threads pass through the dents after going through the heddles and before becoming woven cloth. This is called denting. The number of dents per inch determines the fineness of the cloth. One or more warp threads go through each dent. The number of warp threads that go through each dent depends on the warp, and it is possible that the number of threads in each dent is not constant for a whole warp.
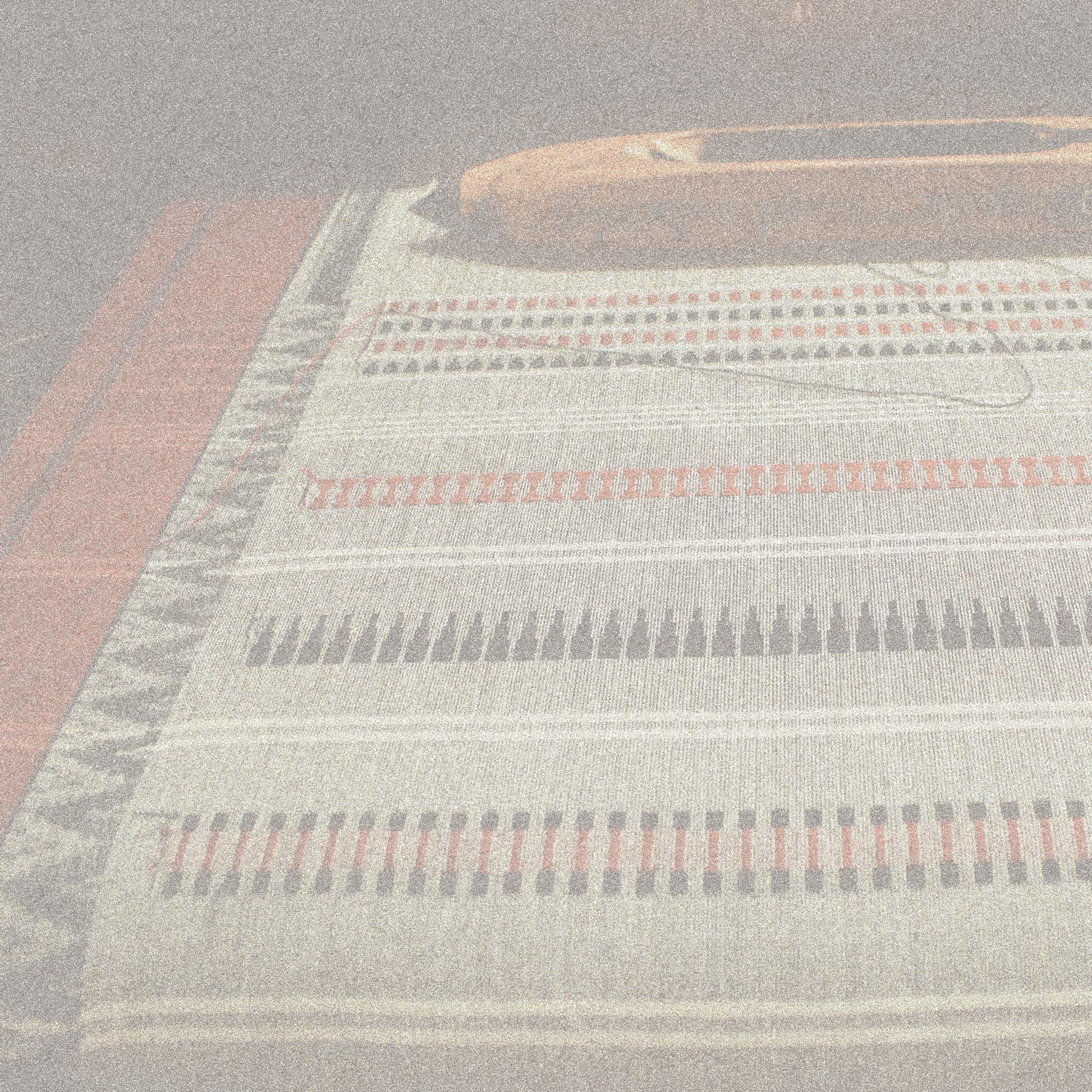
Then the weaver‘s beam is mounted and weaving is started.
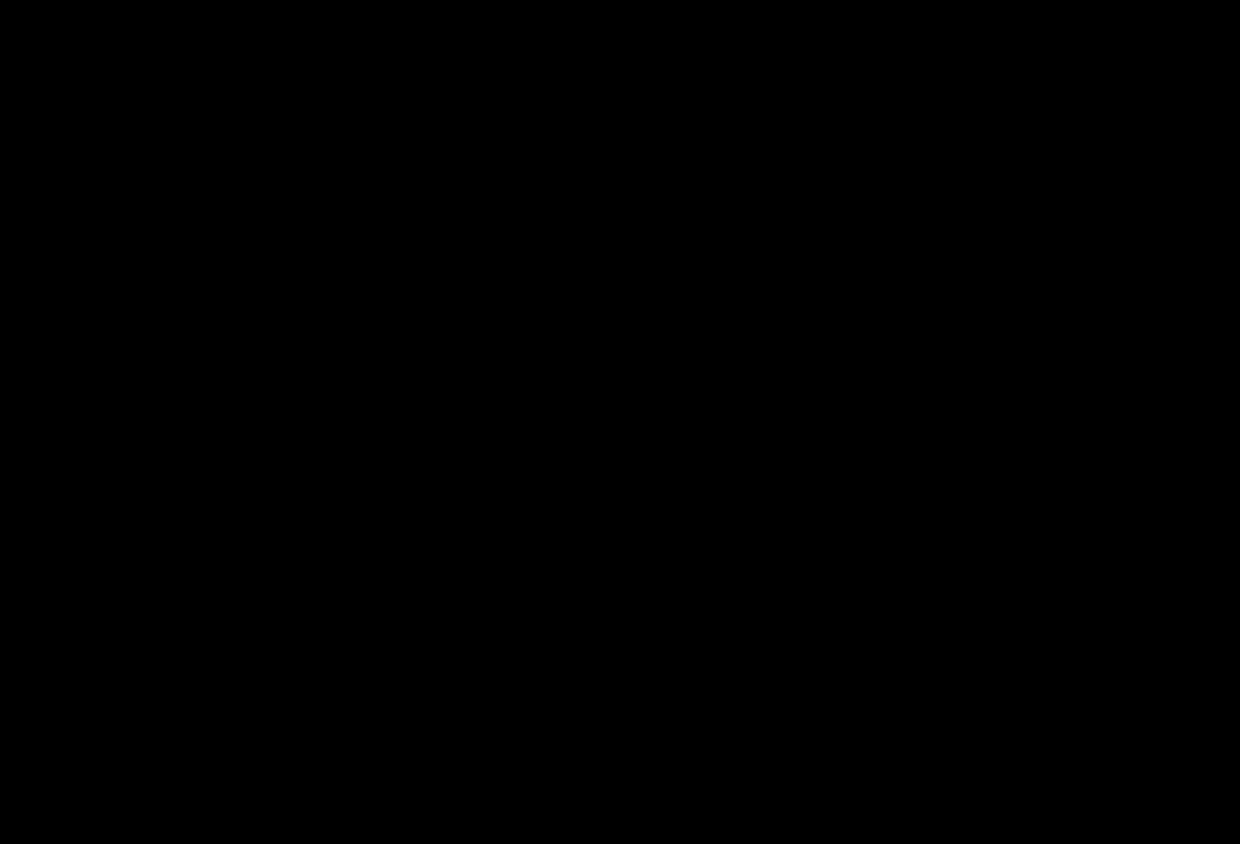
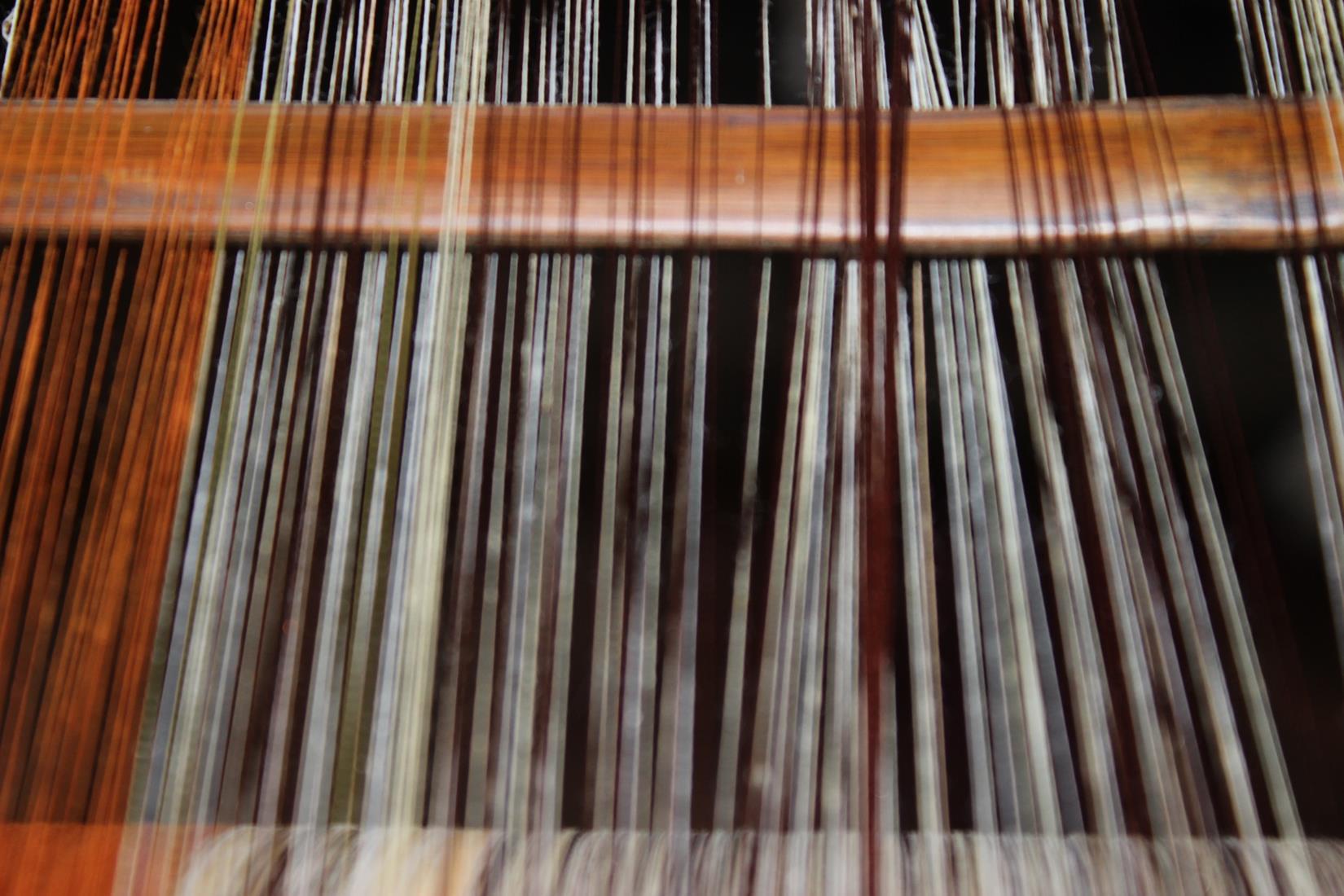
FIGURE: 6.18- LEASING
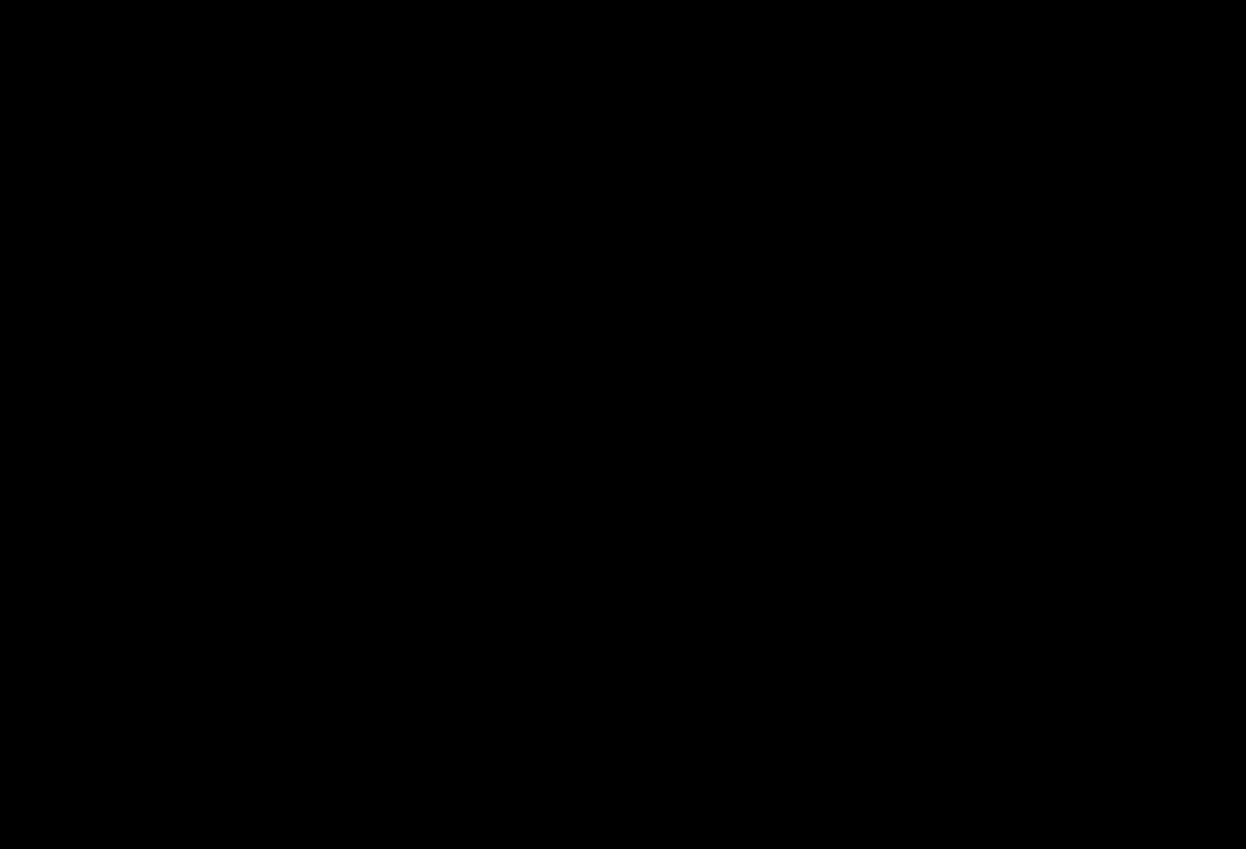
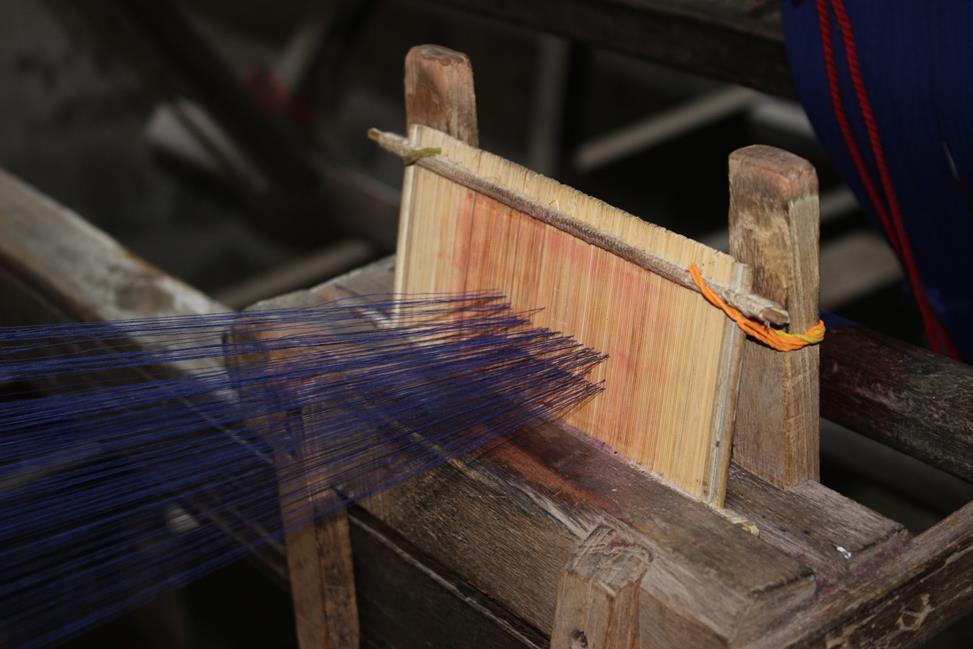
FIGURE: 6.19- DENTING