
2 minute read
Cost, carbon and payback
When approaching natural ventilation, another potential hurdle is the sheer array of systems, options and strategies available. Ultimately, there tends to be a common goal of providing outdoor air for energy savings and health. Here we present our “simple approach” to thinking about cost, carbon and payback of natural ventilation.
The hardware required to deliver natural ventilation is comparatively low-cost and low-embodied carbon:
• The hardware for an automated NV system typically includes window actuators, control panels, bracketry, framing for openings, weather stations and cabling
• An automated natural ventilation system typically costs around 20 to 50 USD / m² for the areas served1 This includes the hardware and the installation and commissioning of the system
• The whole life carbon of these hardware elements is fractional, typically around 0.1% of the project’s whole life carbon 1
The openings through which air enters and leaves carry much greater cost and embodied carbon. On this basis:
• It is optimal to consider how openings can be integrated with glazing that is functional for daylight and environmental quality. Where possible, integrate openings with glazing as it allows one feature to perform multiple functions (daylight, ventilation, environmental quality)
• Likewise, features such as atria and solar chimneys can be highly beneficial in expanding natural ventilation across large parts of the building but are best utilised and adapted where they would exist independently of the needs of the natural ventilation system
1 Based on Introba project experience
• Designers should think carefully about the potential payback of major architectural interventions such as double-skin walls and ideally carry out preliminary whole life carbon (WLC) calculations early on to guide these decisions. In some cases, the double skin may be required to control wind, but quite often these interventions provide limited payback in heating and cooling energy saving
Heat loss through leakage is another consideration, particularly in colder climates. While actuated systems can achieve an effective seal, many types of automated opening can increase infiltration and may cause drafts.
Natural ventilation systems should consider how to be as economical as possible. For example, use the stack effect and/or harness the wind energy to achieve the target airflows from fewer openings and architectural interventions.
The detailed design of NV openings in facades needs to take due consideration of other design criteria such as fire, acoustics, security and safety. The position, size and detailing of opening vents can have a significant impact on facade costs and must be considered with an appropriate specialist.
Finally, natural ventilation achieves more than just energy and potential carbon savings. It is hard to put a number to the health benefits and resilience of natural ventilation.
In buildings such as Vienna House2 , in Vancouver, Canada where mechanical systems can be reduced through the application of natural ventilation, there is a much more tangible payback regarding overhead costs, bills, and whole life carbon.
2 https://viennahouse.ca/
University of Waterloo Academic Building—Natural Ventilation Schematic
1. Outdoor air enters directly via automated windows
2. Acoustic ducts allow airflow without noise transfer
3. Used air rises in the solar chimney
4. Direct sun provides additional bouyancy
5. Additional pressure is generated by wind at chimney exhaust
6. Perimeter offices enjoy single-sided natural ventilation
Figure 1: Whole Life Carbon (WLC) analysis of three alternate natural ventilation options for The University of Waterloo Academic Building.
1. WLC includes initial embodied carbon emissions of NV hardware and additional glazing components.
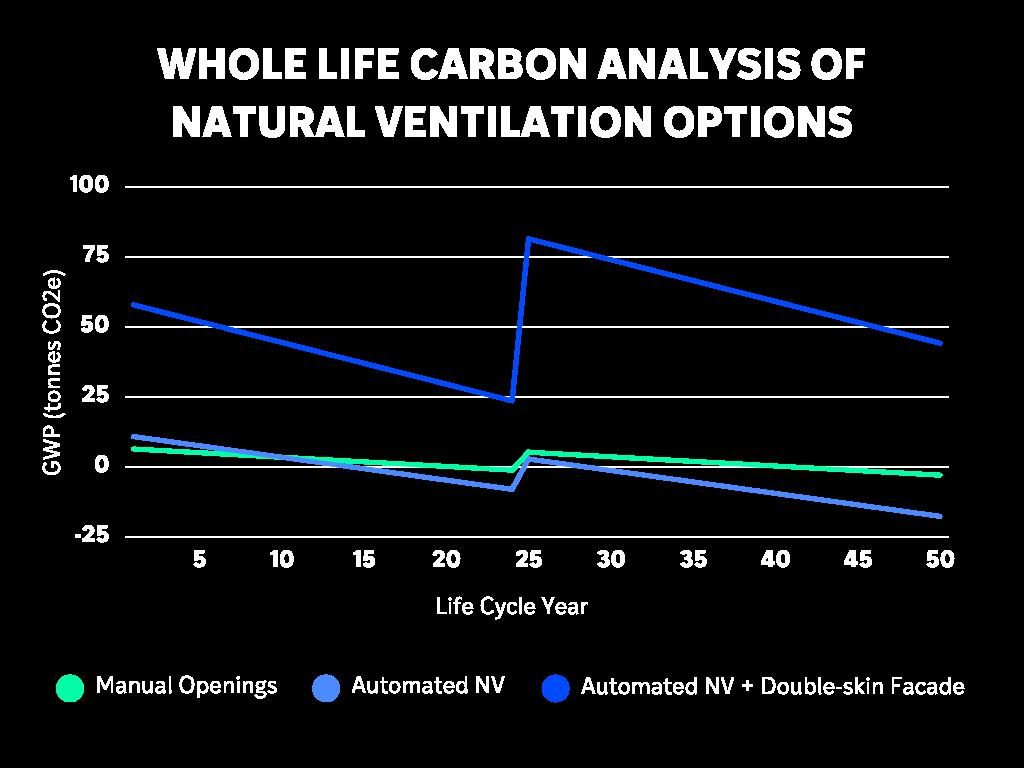
2. Reduction in WLC over time resulting from cooling energy savings (and heating energy savings for double-skin facades)
3. Spike in whole-life carbon at 25 years because glazing components are replaced. Note, the NV hardware component replacements at 12.5 year intervals have minimal impact. Note this calculation is representative of one building in one location - although insights may be transferable, we recommend conducting a WLC study on each project to verify outcomes.