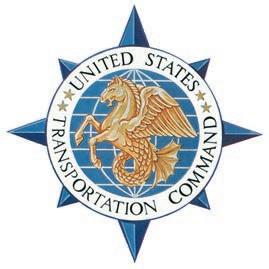
44 minute read
Developing a Unique DOD Unit Movement Transportation Tracking Number
to Force Movement Visibility
By David A. Vail, CIV, USTRANSCOM (TCJ3-IR)
“Logistics sets the campaign’s operational limits. The lead time needed to arrange logistics support and resolve logistics concerns requires continuous integration of logistic considerations into the operational planning process. This is especially critical when available planning time is short. Constant coordination and cooperation between the combatant command and component staffs— and with other combatant commands—is a prerequisite for ensuring timely command awareness and oversight of deployment, readiness, and sustainment issues in the theater of war.
”— Joint Pub 1: Joint Warfare of the Armed Forces of the United States
LEARNING FROM INDUSTRY The commercial distribution sector has had widespread success by adopting webbased, web-assigned tracking numbers. Their underlying motive is certainly the “bottom-line’” and to affect that “bottomline,” companies have sought to better serve their customer needs through the application of information technology. The assignment of unique life-cycle tracking numbers for customer visibility is a cornerstone strategy for corporate America. Today, nearly every successful enterprise uses some form of tracking number to manage their products and services.
Whether it is a mega-volume small package carrier such as FedEx, DHL, or UPS; a large retail chain such as WalMart; an international ocean carrier such as APL, SeaLand, or Maersk; or even a fish and game wildlife environmentalist—everyone relies upon unique lifecycle tracking numbers to hold business information together as it passes through enterprise databases. They realize that by tightly integrating corporate data, they can provide quick, simple and understandable responses to any customer inquiry. In the end, satisfied customers breed more business opportunity, and more business opportunity breeds larger “bottom-lines.”
In addition to the tangible customer benefits from this data integration strategy, there are internal corporate benefits as well. The strategy also allows these organizations to track critical corporate information across domain boundaries; eg, operations, finance, inventory/tracking, scheduling (planning), marketing, and resource management. Without a business focused integration strategy to share information, the business becomes fragmented, and critical business information becomes compartmentalized and eventually loses inherent value to the business as a whole. 1 So, if this approach is being used so successfully by so many, why has the Department of Defense (DOD) not yet realized the value to be gained by the in
1 The Electronic College of Process Innovation, Daniel S. Appleton, “Business Rules: The Missing Link” troduction of a unique tracking number for unit deployments? Over the past 20 years, the DOD’s joint planning and execution community has continued to seek ways to compare actual execution detail with its associated planned movement. This has continually been identified as a major command and control goal—to accurately depict a “plan versus actual” view and make needed adjustments as real world events affect the plan. However, the fundamental pitfall of this goal has always been that the classified planning domain of Joint Operation Planning and Execution System (JOPES) and the unclassified execution domain of the Defense Transportation System (DTS) use significantly different data models with differing levels of detail. For that very reason, an accurate, detailed portrayal of “plan versus actual” has met with failure.
The United States Transportation Command (USTRANSCOM) and United States Joint Forces Command-sponsored Transportation Tracking Number (TTN) initiative finally addresses this issue.
EARLY EFFORTS TO TRACK UNIT MOVEMENTS Subsequent to September 11, 2001, the high volume deployments supporting
US operations in Afghanistan mandated better deployment data visibility. Early analysis revealed extensive variance in the accuracy and completeness of unit deployment data, and, over time, the reported operational picture of the unit deployment status was significantly distorted.
When viewing Unit Line Number (ULN) requirements in the JOPES, the corresponding scheduling and movement regularly occur in the execution-planning cycle and provided fertile areas for attacking unit move visibility problems in order to develop a long-term solution.
Overall the study revealed that systems work as designed when provided all critical data at the beginning of the process. However, it also revealed that the lack of process discipline and continuous human intervention with the data created signifi
This early look into deployment data uncovered significant data breakdowns that regularly occur in the execution-planning cycle and provided fertile areas for attacking unit move visibility problems in order to develop a long-term solution.
visibility was no better than 27 percent. When the same unit deployment data was researched in the Global Transportation Network (GTN) with the Unit Identification Code (UIC), 85 percent of the unit shipment data was visible.
Of significant interest was the magnitude of “key” data element errors across multiple systems and processes; eg, incorrectly constructed Transportation Control Numbers (TCNs), missing and/or incorrect Unit Line Numbers (ULNs). This early look into deployment data uncovered significant data breakdowns that cant voids in the ability to maintain these critical data associations. New tools, new procedures, and a greater emphasis on data quality will be needed in the future to affect a long-term solution.
In the deployment planning and execution domains there are crucial pieces of information represented by data elements that must be understood. During contingencies, initial movement requirements are defined in an aggregated fashion in JOPES while the actual shipment detail during movement of these requirements is recorded in DTS systems.
ONE COMPANY, I NDIVISIBLE, WITH SERVICES AND SCHEDULES FOR ALL.
Now, all the divisions of The Kane Company – Office Movers, Inc., Office Installers, Inc., Office Shredding, and Kane 3PL Third Party Logistics – are available on GSA schedule through Kane Government Services. From office moving, furniture storage, delivery and installation and library relocations, to secure document destruction, safe computer equipment handling and worldwide logistics solutions, The Kane Company offers one-stop shopping for all federal agency and DoD needs.With Kane, one call really does do it all.
www.kanegovernmentservices.com Call 866-GSA-RELO (866-472-7356)
To get a “planned versus actual” perspective, critical pieces of information from the plan and execution space must be held together from the very beginning of movement planning through closure at the end of movement. It is only by maintaining cross-domain linkages of these relationships that a user can ultimately understand the status of deployment and determine how real-world events are affecting that movement. The initial steps of our data analysis effort were to understand the realities of these critical data relationships during deployments to Afghanistan and Iraq.
To achieve quality in-transit visibility (ITV) for unit moves from the planned requirement through its execution and delivery, the relationship of these four critical data elements must be fully understood:
• OPLAN Identification (PID) • Unit Line Number (ULN) • Unit Identification Code (UIC) • Transportation Control Number (TCN)
It is absolutely essential to hold these elements together in order to fully trace JOPES planned records with its DTS execution detail. Since the JOPES domain is limited to an aggregation of data in contrast to the DTS execution systems that contains item level detail, all critical data relationships must be maintained throughout the entire deployment planning and movement life cycle as the data passes from system to system.
Remembering that the planning data in JOPES differs significantly from the movement data in the DTS systems, these DTS systems must eventually roll the details up into aggregated data sets for JOPES. Once this aggregated data is in JOPES, the details of the deployment can no longer be understood.
The process can be likened to melting ten pennies into a copper mass. Once accomplished, one can no longer read details that were stamped on the coins; all independent detail is lost in the aggregation process. Additionally, if any critical data linkages for the cargo are lost, an accurate rollup is again impossible. With two disparate domains operating two independent databases any rollup picture is, at best, a very precarious one.
In spite of deployment doctrine and policy, data standardization, business rules
and personnel training in deployment processes, this decentralized approach to manually generating critical data elements has opened the door for users to regularly introduce non-compliant and inconsistent data into deployment execution systems. Although the Defense Transportation Regulations (DTR) states that unit move TCNs must be unique, they are not, especially over relatively short timeframes and across OPLANs. Currently, there is no unique key created at the beginning of requirement identification process in JOPES that remains tightly associated with shipment data throughout the deployment process. Our current decentralized process is very cumbersome and labor intensive, such that enforcement of doctrine, policy, data standardization, and business rules is non-existent.
OPERATIONS ENDURING FREEDOM AND IRAQI FREEDOM Deployment data quality was consistently monitored throughout the last five years of OEF/OIF. The first report, completed in October 2002, reflected that of the 123,730 unit move TCN shipment records, only 29 percent contained a ULN needed for possible return to JOPES. During the intervening period from October 2002 to January 2003, a software change was made to a DTS air manifesting system, improving the data quality to 46 percent. In February 2003, USTRANSCOM and the Army’s Forces Command (FORSCOM) personnel reconfigured a data exchange between the COMPASS and GTN Systems to obtain a post-FORSCOM–edited data feed, vice the existing pre-edit feed, resulting in a significant improvement (61 percent) in Army data quality.
As far as real data quality is concerned, USTRANSCOM has begun to move from the art of guessing to the initial stages of applied scientific research to help identify and point to the resolution of data quality issues across the DTS. Even with these first steps, there is no real data quality visibility inside these segments of data. By January 2004, the level of data quality reached 77 percent, yet within a year that number had fallen to 65 percent and has remained representative.
OVERCOMING THE PROBLEM To overcome the data integrity issues outlined above, USTRANSCOM, in part
UAN Analysis: 18 July 07 Total Mobility TCN Shipments 117,715
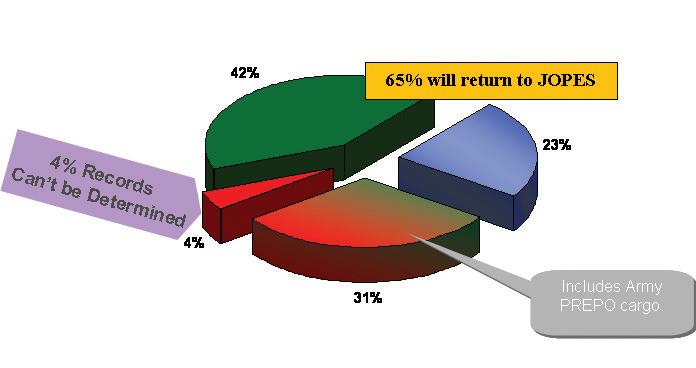
Figure 1: Deployment Data Quality – July 2007 Figure 1 shows the results of deployment data quality as of July 2007. The green and blue segments reflect the presence of a ULN in the record set. The red-green slice depicts valid service records that did not have the ULN. When translated to the warfighter, his view of unit deployments continues to be affected by the loss of 35 percent of his data.
nership with JFCOM, has sponsored a FedEx-like tracking number concept for all DOD unit deployment cargo. This initiative is called the Transportation Tracking Number (TTN). The basic concept for the unit movement TTN has several critical characteristics that must be kept in focus. These characteristics are:
• each number is truly unique over a significant timeframe (upwards of ten years); • each number is a data key that can cross classification boundary without comprising OPSEC; • the number is assigned as early in the deployment planning process as possible; and • this number remains associated with the shipment data in every system that processes and stores transportation data.
The TTN will ensure that all unit move requirements are reported back to JOPES for a fully-realized “plan versus actual” capability-based closure assessment.
TRANSPORTATION TRACKING NUMBER INITIATIVE Fundamentally, the TTN concept has two parts. Account numbers are established in JOPES at the highest level and are subsequently used as a “seed” for creating individual tracking numbers for each shipment. At the outset of any new deployment requirement in JOPES, a system generated account number would be ascribed to each requirement. It would be based on an algorithm that represents a combination of JOPES PID and ULN data. It would not be a concatenation of these values, but would be a newly generated randomized customer TTN Account Number (TTAN).
Two key aspects of the number are: (1) it does not have innate intelligence in and of itself; and (2) it remains unique throughout its life-cycle to prevent reuse or duplication within the transportation domain.
The TTAN will be established sometime prior to, or during, the planning/ sourcing process. This account number is established electronically in JOPES at the moment a requirement record (ULN) is created. As unit movement documentation is created, a sequential counter for each shipment is added to the TTAN to create a complete TTN. This TTN is collected in a service-owned deployment repository, as well as processed through all the other DTS systems and eventually collected in the TRANSCOM global
ITV database. As the shipment is moved through the execution environment, the TTN serves as the “data key” for ensuring data reliability throughout the complete movement.
To gain visibility of actual movements, the TTNs are available on the unclassified systems for TTN Account Number
Figure 2: TTN Process and Services
queries. Additionally, at various points in the execution, the TTNs movement event updates would be reported to the C2 environment for the comprehensive planned versus actual assessments.
Within the Joint Staff’s Operations Directorate (J3), its Command Systems Operations Division has taken the lead in having the Defense Information Systems Agency (DISA) engineer the TTN initiative and support services, thus setting the stage for the FY08 prototyping in preparation for future implementation. In this effort, DISA will be providing a range of Service Oriented Architecture (SOA) services and documentation for developers to use in their prototype and eventual implementation efforts. Figure 2 identifies a basic view of the systems and where various SOA services are envisioned.
REMOVING OLD BARRIERS Since the TTN is designed for machineto-machine data exchange, there is no human user involved in its creation, exchange, or processing; it remains guaranteed unique and traceable and unalterable. The TTAN provides JOPES the single unique data key that can be used to hold the entire life cycle of planning and execution data together.
Because there is no embedded intelligence in the creation of the basic TTAN in JOPES, it is not restricted from the classified-to-unclassified data flow . . .
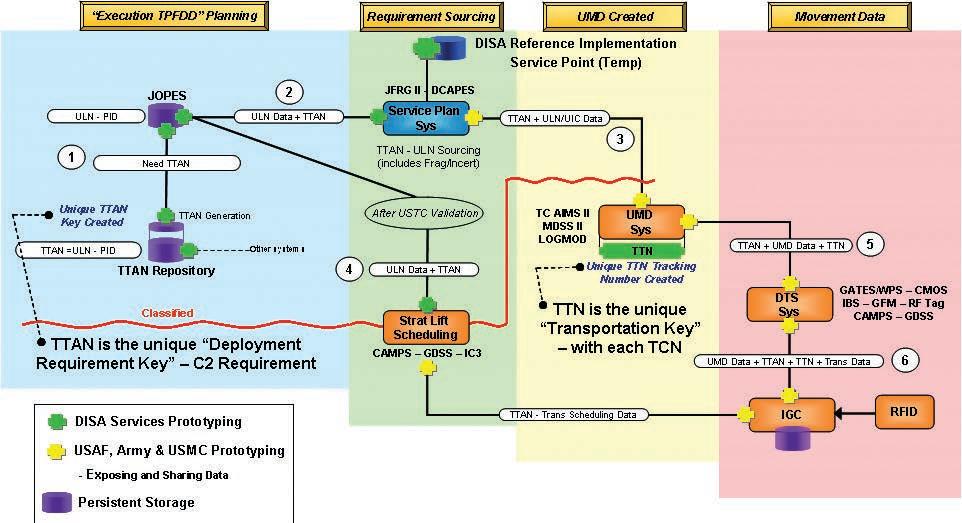
thus removing the requirement for: (1) establishing an alias for the PID to be used on unclassified systems; and (2) maintaining the classified PID to unclassified “PID-alias” cross-reference table. Through the TTAN, the PID–ULN relationship can be freely exchanged across the classified boundary without violating operational security. The unalterable and unintelligent TTN removes any motivation for customer changes that traditionally destroy embedded intelligence in current TCN, such as changing sustainment TCNs into unit move TCNs to avoid HAZMAT restrictions or to avoid billing by moving on contingency missions.
Finally, the TTN removes the dependency on process enforcement for any success in achieving improved unit move data quality.
NEW CAPABILITIES ENABLED BY TTN In the simplest terms, the TTN resolves many long-standing issues with deployment data quality, while at the same time fulfilling critical command and control objectives. Because the TTN initiative provides the linkages across JOPES and the unclassified transportation systems, it offers the opportunity to assemble an accurate “plan versus actual” picture at the item-level of detail. The essence of the “plan versus actual” picture is that it provides a true relationship of the plan requirements and all the detail about unit movements. The TTN enhances command and control of deployment from origin to destination, affording commanders better insight for posturing support, coordinating delivery, and conducting capability assessments.
The orchestration of this detail data enables the combatant commander and staff to better understand force capability and the synchronization and integration of that capability before, during, and after deployment of their forces. Strategic and theater replanning is empowered by the availability of accurate deployment planning and execution data that provides any aggregation needed by strategic, operational, and tactical stakeholders; eg, ULNs, UICs, Force Tracking Numbers (FTN), or even type equipment and the related capability. Significantly, the TTN allows unit equipment to be moved on any plane or ship without the loss of ITV, and more importantly, its OPLAN relationship. It is this final point that opens the potential to transform the financial process for billing and paying for lift. The TTN offers the opportunity to transform the world of deployment data. DTJ
David Vail is a senior civilian in the Operations Integration Division, Operations & Plans Directorate, United States Transportation Command, Scott AFB, IL, overseeing the design and development of the Transportation Tracking Number (TTN) initiative. Significant contributions to the TTN effort and this article have been provided by Randall Heim, Jim Donovan, and Tom Black of MITRE.
ACKNOWLEDGEMENTS In addition to the MITRE team mentioned above, the following agencies have made significant positive contributions to the advancement of the TTN initiative: Joint Staff J3-CSOD, DISA PEO-C2C, CENTCOM AJ3, TRANSCOM J5/4, and JFCOM J9 JDPO.
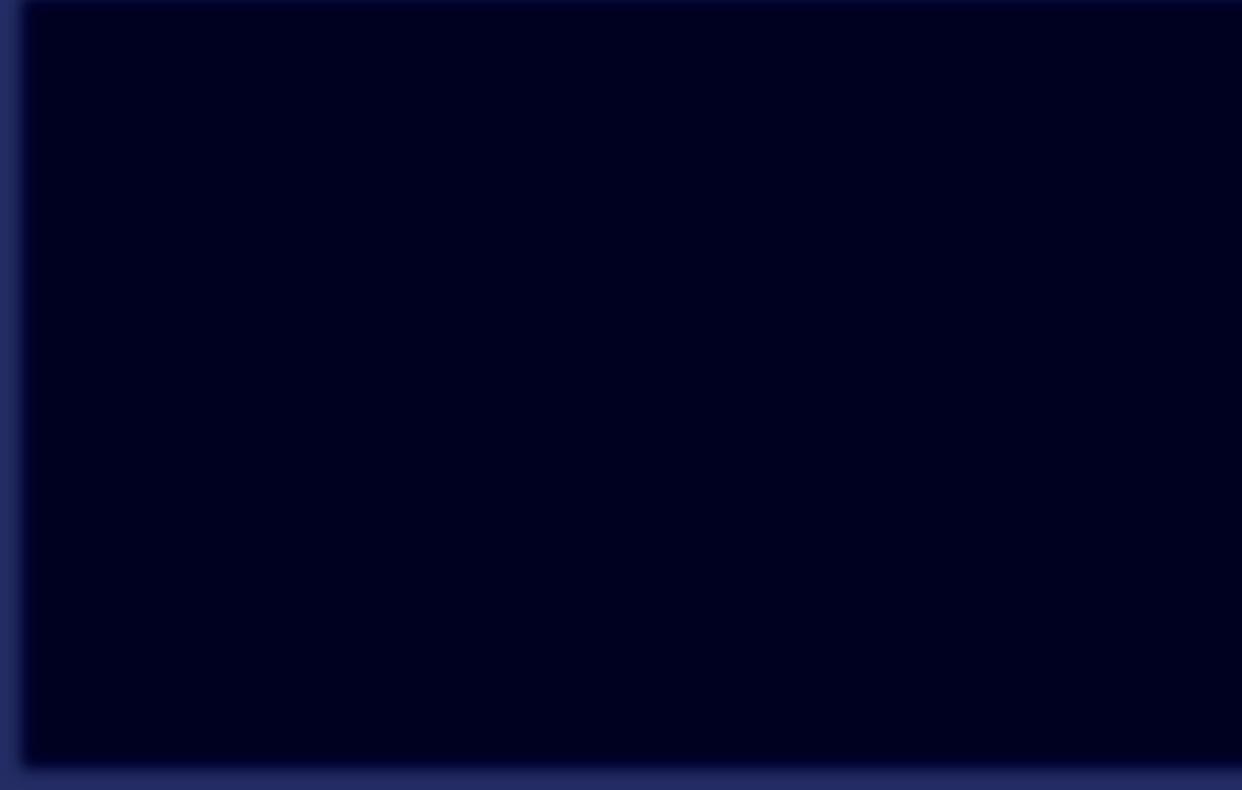
From military tanks to school textbooks, Landstar Government Services delivers. Our proven track record and unparalleled commitment to safety ensures U.S. government agencies worldwide get reliable, responsive transportation solutions for every shipment, every day.
As a leader in protective services and movement of arms, ammunition and explosives, Landstar is ready to roll when U.S. troops are deployed.
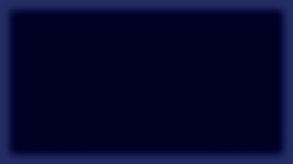
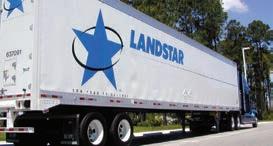
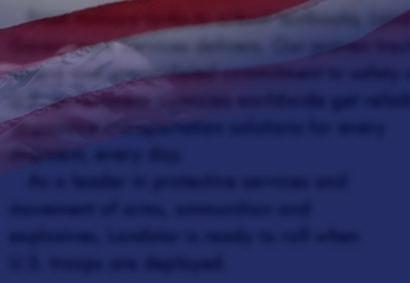
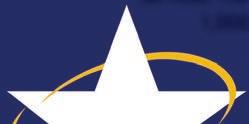

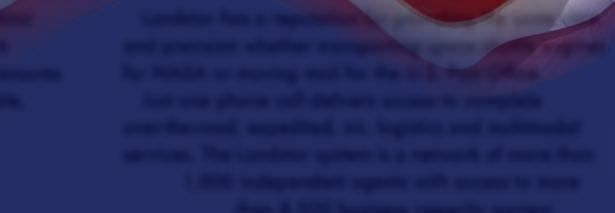
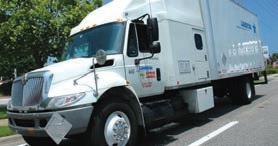
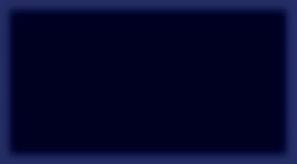


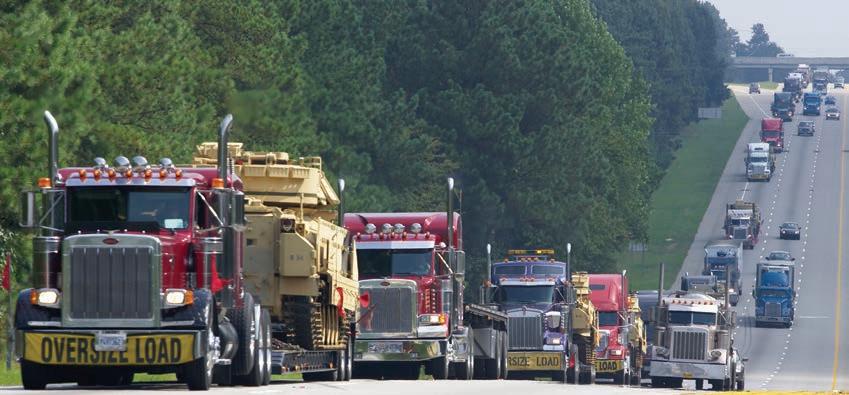
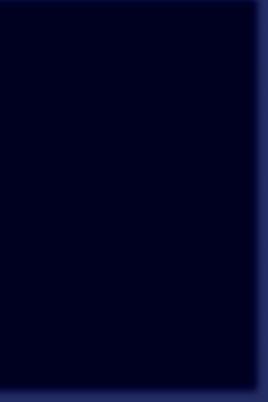
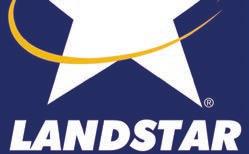
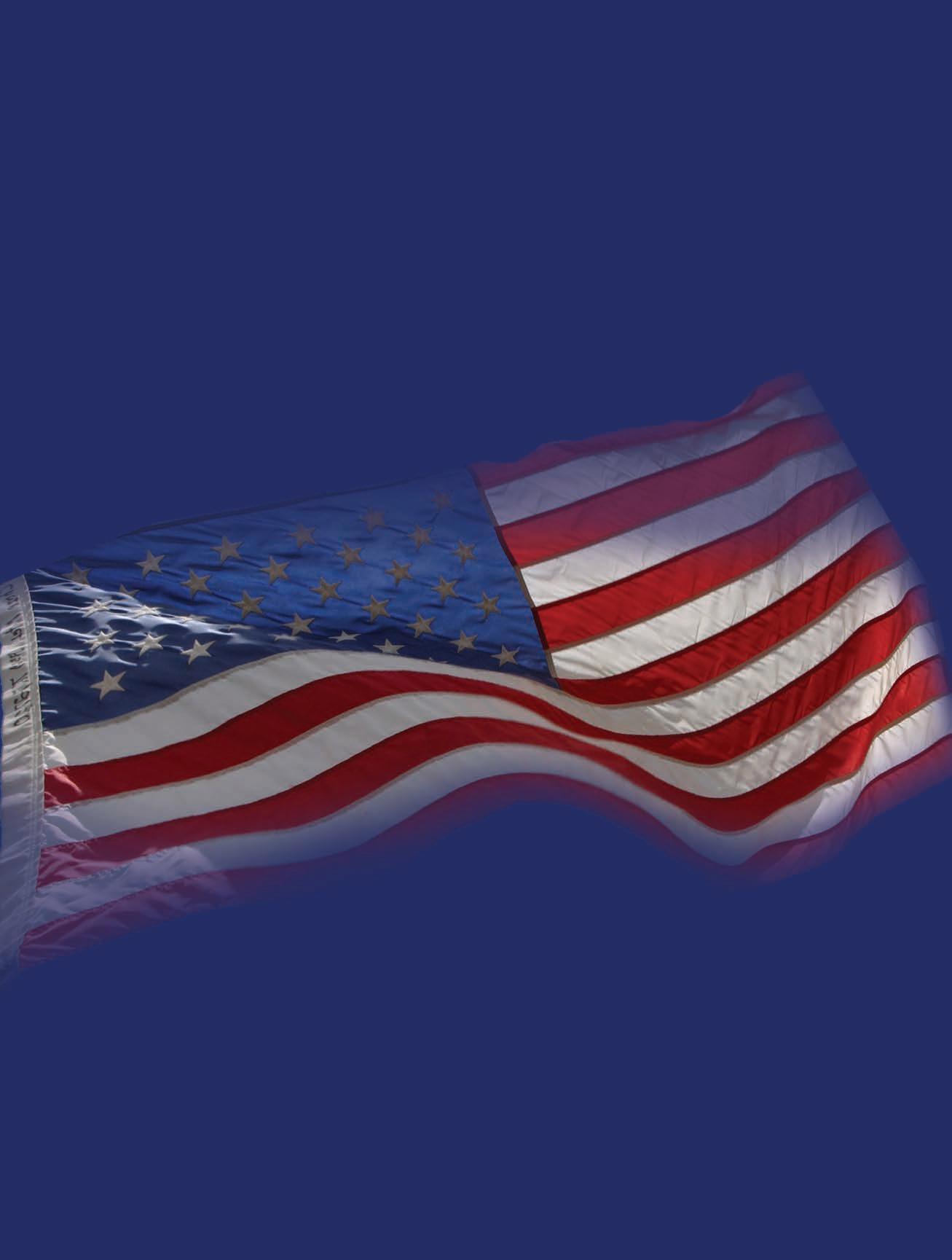
Landstar has a reputation for providing the same care and precision whether transporting space shuttle engines for NASA or moving mail for the U.S. Post Offi ce. Just one phone call delivers access to complete over-the-road, expedited, air, logistics and multimodal services. The Landstar system is a network of more than 1,000 independent agents with access to more than 8,500 business capacity owners
(BCOs) and more than 23,000 approved broker carriers.
SDDC The perfect salute to National Transportation Week—a joint effort that employs all modes to accomplish the Strategic Seaport mission in South Carolina By Capt. Chris LeCron Army 841st Trans BN Public Affairs Charleston, SC
The strategic seaport of Charleston’s continuous military deployments and redeployments since 9/11 are managed and operated by a true “joint” team of soldiers, sailors, marines, mariners, civil servants, contractors, and commercial transportation partners.
The overall command and control of each military seaport mission is managed by the SDDC’s Army 841st Transportation Battalion. However, the 841st Transportation Battalion, also known as SDDC Charleston, is made up of a mix of army officer, non-commissioned officers, army civilians, and contractors.
Military deployments in Charleston over the last two years have supported numerous missions to include Operation Iraqi Freedom, Operation Enduring Freedom, Kosovo Forces, humanitarian deployments, mine resistant vehicle deployments, and unit sustainment.
One mission of SDDC Charleston is to supervise and manage the contracted labor provided by Marine Terminals Corporation East (MTC). MTC is made up of experienced civilian longshoremen that work both commercial cargo and military cargo missions in Charleston.
SDDC Charleston also manages the transport of cargo to and from the seaport. This commercial transport mainly
Soldiers from SDDC Charleston set up a mobile radio frequency tracking kit with the help of Unisys contractors during a high priority mine resistant ambush protected vehicle sealift mission, Feb. 2008. Photo by Master Sgt. Kevin Young.
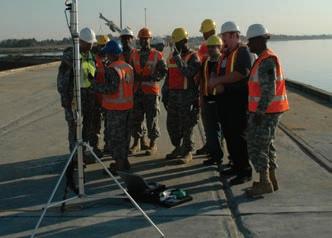
comes in the form of the commercial trucking industry. During certain missions, cargo is transported by rail to and from the seaport. Both Norfolk Southern and CSX operate trains for military missions to Charleston.
Cargo that is transported by commercial truck is controlled and operated by
the cargo documentation and freight sections of the 841st. These sections arrange for receipt and pickup of cargo by commercial truck. The operation must verify which cargo is sent to which location and at what time.
The cargo ships that transport military cargo are either military chartered cargo ships or MSC Navy cargo ships. Both types of ships are operated by merchant mariners. These mariners operate and maintain these cargo ships that transport high priority military cargo.
Although the bulk of the labor is completed by civilian longshoremen, the 841st often utilized a port support activity team of personnel to supervise the labor, direct cargo, provide security and force protection, and movement control. This port support activity team includes DA civilian marine cargo specialists and military personnel.
The military personnel that compose the port support activity are usually army reservists or Marine Corps reservists. The “Savannah Marines,” a port operating unit based in Savannah, GA, has provided continuous port support activity support to Charleston operations since early 2007.
Several information technology specialists work at the 841st as contractors. Their job entails the proper maintenance of all technology programs to include computers, intranet, tracking technology, radios, phones, and video-teleconferencing as needed.
Although SDDC Charleston works mostly with the Coast Guard, merchant mariners, Marines, and deploying unit liaison officers, there is interface with the Navy and Air Force. Several of the cargo piers used by SDDC Charleston are on a Navy installation. Each operation involves coordination with the Navy.
The Charleston AFB conducts cargo airlift in the same manner as SDDC Charleston conducts sealift. If cargo requires a quicker transit overseas, it can be bumped to airlift. If transit time is not an issue, the cargo will usually shift to sealift. The close location of the Charleston airport and seaports allows for this interchange.
The military sealift mission of SDDC Charleston requires a true “joint” effort of multiple DOD partners. Every type of transportation service and industry to include commercial and military is involved in the Charleston mission at one time or another. DTJ
INDUSTRY NEWS*
*Some articles have been condensed due to limitations in space.
AAFES Higinio Ortiz must be living right! For the second time in a year, AAFES Commander Brig. Gen. Keith Thurgood has handed this AAFES driver the keys to a shiny, new custombuilt Freightliner tractor and Hyundai trailer, valued at more than $103,000.
Ortiz was presented the truck in honor of being named AAFES’ 2007 Driver of the Year. In a ceremony at the Waco, TX, Distribution Center on February 15, Ortiz joined an elite group of drivers who represent the very best of the trucking industry. And he’s definitely one of the best! Last year, Ortiz received a new tractor/trailer when he became the first AAFES driver—and one of 80 drivers nationwide to receive the prestige honor—to log more than four million accident-free miles.
According to Rose Marie Brady, Chief of AAFES Fleet Operations, AAFES motor vehicle operators are key components of the AAFES supply chain. Happy drivers are good drivers, and AAFES seems to Higinio Ortiz AAFES’ 2007 Driver of the Year
please as the average length of service for a driver is 18 years, and they drive more than 75,000 miles each year, she said.
To date, 43 AAFES drivers, out of 420, have reached the milestone of having driven one million safe miles; 17 AAFES drivers have doubled that feat and driven two million safe miles. Only four AAFES drivers have obtained the three-million mile safe milestone.
The Driver of the Year Program recognizes the professional expertise of motor vehicle operators. Eligibility Factors include no preventable accidents, no disciplinary actions, evaluations, miles driven, AAFES awards, special recognition awards, letters of appreciation/commendation, and National Safety Council Safe Driver Award.
As AAFES’ official ambassador, Ortiz will make appearances at events throughout the US, traveling in excess of 100,000 miles in 2008.
THE HOWLAND GROUP NDTA announces Shelley A. Warren, Managing Director of the Howland Group Communications, as Chair of the Communications/Publications Committee. Professor William DeWitt was former Chair. Shelley holds a degree in American Studies earned with honors, and has also earned project management certificates in Planning & Strategies Identification, Scheduling & Monitoring, and Post Implementation Review. Over the past 20 years, she has played an integral role in assisting the Howland Group’s clients in developing and executing successful information and communication strategies. From 1988 to 1992, Shelley served as Director of Policy for Bucks County, PA, where she was responsible for coordinating policies and program development among various county agencies, non-profit organizations, and the private sector. Her most notable achievement, for which she was recognized by housing advocates, was organizing the creation of a private/public partnership to develop Bucks County’s first emergency homeless shelter and, subsequently, facilitating the Affordable Trust Fund. Shelley also serves on the Howland Group’s Board of Directors and is a member of the Transportation Research Board, Military Transportation Committee.
Welcome Shelley! NDTA is pleased to have you ONBOARD. DTJ
Are You Ready? US CBP Proposes New Reporting Requirements for Importers and Carriers of Cargo Destined for the US
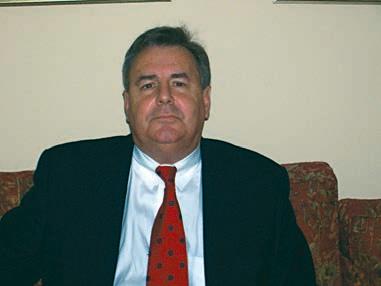
Lee Jackson Lead, Information Systems Engineer The MITRE Corporation
The US Customs and Border Protection (CBP), an operating agency within the Department of Homeland Security (DHS), issued a Notice of Proposed Rulemaking (NPRM) in the Federal Register on January 2, 2008. In the NPRM, CBP proposed the electronic transmission of new cargo reporting requirements for importers and carriers of cargo transported by vessel to the US. Readers impacted by the proposed requirements should know that comments to the NPRM must be submitted on or before March 3, 2008. Comments can be submitted in writing or electronically through the Federal eRulemaking Portal: http://www.regulations.gov.
It is important to understand that these proposed requirements are in addition to the required entry requirements that importers and carriers are required to submit via electronic manifest 24 hours prior to lading containerized and nonexempt break-cargo at foreign ports on vessels destined for the US This requirement, referred to in the trade as the “24-hour rule,” has been in place since October 13, 2006, and is specified in Section 203 of the Security and Accountability for Every Port Act of 2006 (referred to as the SAFE Port Act; P.L. 109-347). The basis and justification for the “24-hour rule” was to enhance and improve CBP’s high-risk targeting efforts occurring through the Automated Targeting System (ATS). The additional information CBP proposes to require is intended to further improve CBP’s ability to identify high-risk shipments and cargo destined for the US
THE PROPOSED REQUIREMENTS The new program and requirements being proposed are referred to by CBP as the “10+2” Program. Although the “10+2” Program and the requirements being proposed are new in terms of mandated requirements, this program has been in existence on a voluntary basis within CBP for several months. I believe, but don’t quote me on this, that the new requirements of the “10+2” Program were discussed both within CBP and with their participating trade stakeholders at the last meeting of the Customs Operations Advisory Committee (COAC). The COAC is the public/private partnership that CBP participates in and uses as a sounding board to float new ideas within the trade community prior to CBP moving forward with the idea or proposal.
Specifically, the proposed new data requirements of the “10+2” Program are as follows:
IMPORTER REQUIREMENTS 1. Manufacturer/supplier name & address; 2. Seller/owner name & address; 3. Buyer/owner name & address; 4. Destination name & address; 5. Container stuffing location; 6. Consolidator (container stuffer) name & address; 7. Importer of record #/Foreign Trade Zone applicant #; 8. Consignee #’s; 9. Country of Origin; and 10. Commodity Harmonized Tariff Schedule #.
CARRIER REQUIREMENTS 1. Vessel Stow Plan for vessels destined to US; and 2. Container status messages, providing container status, movements, eg, empty or full.
DISCUSSION AND FINAL NOTE Importers and Carriers impacted by these new CBP proposed requirements should carefully examine their current operations and evaluate the impact these new requirements may have on your operations. At a minimum, providing such
HOMELAND SECURITY
new information electronically prior to a vessel being laden, if you are already not providing such information, may pose a logistical and information system challenge and could at the outset, prior to your incorporating such a process into your operations, result in potential delays of your cargo being processed. Consideration should also be given to how you will be able to protect the confidentiality of this information, especially due to the number of individuals involved in the process of preparing goods for export.
This NPRM is most likely the first of many new requirements shippers, carriers, and transportation companies will see this year, as the Federal agencies involved in furthering our homeland security seek to enhance the programs and requirements for cargo entering the US. Another similar proposal recently adopted is the Transportation Worker Identification Credential (TWIC) program. The TWIC program is being implemented on our ports and requires additional information for all employees working on our Nation’s ports. Both of these initiatives are only pieces of a larger puzzle. Stay in touch, there is more to come. DTJ
Requirements from Section IV of the Federal Register’s On-line via GPO Access; CBP NPRM, 1/2/08; Bulk Carriers carrying exclusively bulk cargo are exempt from these regulations.
ANSWER
Milton Hershey
SAVE THE DATE NDTA Atlantic Regional Forum June 26-27, 2008 Hershey, Pennsylvania
Lockheed Martin— Aligning Logistics Career Development to their Corporate Business Strategy
Jerry Cothran Senior Manager, Logistics Engineering, Center for Performance Excellence Lockheed Martin Corporation
In Shakespeare’s Julius Caesar, Brutus remarks insightfully to Cassius, “There is a tide in the affairs of men. Which, taken at the flood, leads on to fortune.” They are, of course, discussing battle strategy, but this famous phrase is equally applicable in the business world.
Lockheed Martin Corporation, long a leader in the design, development, and production of sophisticated defense systems, is rapidly recognizing, along with many other Aerospace and Defense (A&D) companies, that the “tide” of defense business is undergoing a paradigm shift, unveiling new and growing opportunities in the area of after market support services. The convergence of many factors, such as the end of the cold war technology race, the changing global threat environment, the decline in procurement of new systems, and the corresponding rising cost of supporting aging systems, has prompted a new era and approach to defense system sustainment—those activities that assure operationally ready systems for today’s national security environment.
PERFORMANCE BASED LOGISTICS (PBL) At the forefront of this paradigm shift is a fundamental restructuring of the product support process to an approach, entitled PBL, in which the DOD is transitioning from accomplishing support through the iterative, transactional acquisition of the basic elements of support (eg, spares and repairs) to a more commercial model in which they enter into agreements with product support providers to deliver performance and support outcomes, such as system availability, and leave the determination of “how” to achieve those outcomes to a Product Support Integrator (PSI).
The success of PBL, based on hundreds of programs over the last 9-plus years, has been exceptional. In implementing PBL, DOD has often turned to the defense industry to assume the PSI role. As a consequence, A&D companies are suddenly discovering opportunities for business relationships that may span periods far longer than their core design and development business—as long as thirty or forty years, based on the current and planned useful life of most DOD systems.
Lockheed Martin is aggressively expanding their presence in this business sector. To better posture themselves for this growing market, they have instituted a comprehensive Logistics work force development effort aimed at equipping their logistics personnel with the requisite skills, knowledge, and abilities to successfully accomplish this business strategy.
LOGISTICS AND SUSTAINMENT INSTITUTE At the core of Lockheed’s professional development plan is the establishment in 2006 of the Logistics and Sustainment Institute, or LSI. The goal of the LSI is to establish a multi-dimensional framework that offers their 13,000 Logistics personnel (and 7000 other career–field personnel who frequently perform logistics-related activities) a career roadmap and structure to facilitate opportunities for career planning, education and training, professional certification, and a collaborative learning network.
When fully implemented, the career roadmap will provide clear guidance regarding the required and recommended education, training, credentials, and experience requirements necessary at progressive levels within the Logistics and Sustainment profession. The benefits will be two-fold; employees will benefit from having an established career development path, and corporate management will gain visibility of the level of experience and training, across the logistics work force. Patrice Jackson, the primary force behind the ongoing development of the LSI, emphasizes the value of the multi-dimensional approach. “In a complex discipline like logistics we need to be innovative with our career development program. We can’t limit our focus to a traditional path from college new hire through vice-president; we need to provide specific course curriculum and qualifications at progressive levels across a broad spectrum of career paths. This approach not only provides our managers insight into the levels of workforce expertise, but also provides our employees a clear understanding of their professional growth opportunities.”
COLLABORATIVE LEARNING NETWORK In addition to training, we’ve added a virtual Collaborative Learning Network (CLN) dimension, which allows our logistics and sustainment professionals the opportunity to collaborate by sharing knowledge to increase their performance and in turn deliver better solutions to our customers.”
CENTER FOR PERFORMANCE EXCELLENCE One of the critical foundation pillars in the framework is formal training. To ensure the ready availability of high quality internal training, Lockheed Martin established the Center for Performance Excellence (CPE), headquartered in Rockville Maryland, as a focal point for internal professional development education. The CPE provides training across several functional disciplines, including Program Management, Engineering, Software, Business Management, Quality Assurance, and, recently added, Logistics.
Doug Rowell, who manages the CPE, stresses the critical role of training in the overall corporate framework and business strategy. “The Center for Performance Excellence provides training and professional services across the corporation. CPE training integrates the program performance curriculum, mentioned above, to ensure that Lockheed Martin professionals understand the full spectrum of capabilities required of our leaders and individual contributors. The CPE is focused on flawless execution because our primary goal is to support programs in the pursuit of perfect program performance.”
KNOWLEDGE ACQUISITION AND CULTURAL ACCLIMATIZATION Logistics training within the overall company strategy is equal parts knowledge acquisition and cultural acclimatization. Lockheed Martin has exceptionally qualified logisticians—lack of logistics skills is not the imperative. However, application of those skills is significantly different in a sustainment environment versus a production environment. Planning a supply chain strategy for a manufacturing process primarily involving the procurement of new components that feed the production line is markedly dissimilar from a sustainment setting where a significant percent of spare part components result from repair and overhaul processes rather than new procurements.
The unique nature of the PBL business relationship, where industry providers take on significant responsibility for managing most aspects of support over the life cycle, brings new risk into the equation, such as obsolescence management and mitigation of aging and wear out events. Consequently there is an enhanced role for leveraging industry technical engineering expertise in planning and executing PBL sustainment strategies. This means that Lockheed Martin’s logistics training has to ensure a blend of traditional logistics with a significant level of technical content. Clearly, the business value proposition in taking on PBL work requires addressing not only the objective system supported (eg, an aircraft) but the enabling support systems as well (supply maintenance, transportation, configuration management) over the life cycle.
PBL COURSEWARE With a primary focus on capturing Performance-Based Logistics business, the CPE (in coordination with the LSI) is implementing a Logistics curriculum fully aligned with corporate business processes. To date three courses have been developed, with a fourth course planned for delivery in the fourth quarter of 2008. Each of the courses, and their relationship to enabling the corporate business strategy, are summarized below.
• Introduction to PBL: This 2-day course provides a solid foundation in the concepts, application options, cost and technical trade space analysis, designing, and implementing of PBL strategies. • Design for Sustainment: This 3-day course emphasizes the application of engineering and related technical methodologies to optimize the design of systems for supportability, not only at initial fielding but throughout the service life. Advances in sensor-based technologies are facilitating the development of “autonomic” systems on board the objective system that enable continual health monitoring and management for improved supportability, a key outcome requirement in PBL support. • Win PBL: This 4-day course puts students through an intense week long “war game” scenario in which teams compete to “capture” (build a winning proposal for) PBL business. PBL contracts, as already mentioned, are much more than routine sales of transactional goods. They are complex, evolving sustainment plans tailored to the operational role and environment of the system to be supported—hence the need to craft a viable proposal that delivers the specified outcomes at best value to the customer while providing business value to the corporation. • Execute PBL: This 4-day course (in development) completes the PBL “cycle” of training by putting students through a discrete set of system scenarios in a war game environment to design, develop, and present a feasible PBL implementation and execution strategy that will meet customer requirements while maintaining flexibility to adapt to evolving system, operational, and financial factors throughout the system life.
In summary, students completing this cycle of courses have gained valuable training ranging from a fundamental understanding of PBL to leveraging corporate technical expertise for supportability to capturing PBL business to successfully executing PBL strategies throughout the life cycle.
The competition for PBL business and, in the broader sense, after market support services, is intense and will remain so for the foreseeable future. But with a comprehensive Logistics career development plan and corresponding training aligned with their corporate business strategy, Lockheed Martin looks well postured to capture a significant share of this business while providing excellent value and service to their customers.
LEARNING OBJECTIVES: • Learn the role of Performance Based Logistics in DOD’s transition from iterative, transactional acquisition to commercial models delivering performance. • Gain understanding of the importance of professional development to insure expertise for delivering PBL. • Understand the role of knowledge acquisition and cultural acclimatization in logistics training.
DEFINITIONS • Performance Based Logistics – buying Performance, not transactional goods and services. PBL delineates outcome performance goals of weapon systems, ensures that responsibilities are assigned, provides incentives for attaining these goals, and facilitates the overall life-cycle management of system reliability, supportability, and total ownership costs. It is an integrated acquisition and logistics process for buying weapon system capability. (Defense Acquisition University) • Cultural acclimatization – “Incorporating corporate culture, made up of attitudes, experiences, beliefs, and values of an organization . . .”the specific collection of values and norms that are shared by people and groups in an organization and that control the way they interact with each other and with stakeholders outside the organization. (Kotter, John. 1992 Corporate Culture and Performance, Free Press) • Sustainment – “the provision of personnel, logistic, and other support required to maintain and prolong operations or combat until successful accomplishment or revision of the mission or of the national objective.” (Joint Publication 1–02, DOD [Department of Defense] Dictionary of Military and Associated Terms. DTJ
Please contact Jerry at jerry.d.cothran@lmco.com or 301-721-5711 www.ssrc.lmco.com
Change! COL Denny Edwards, USA (Ret.) VP of Marketing and Corporate Development NDTA
from Pages PAST
One thing becomes immediately apparent as you look over past DTJs. Change is everywhere. Or, like the often heard statement, “nothing is constant but change itself.” NDTA is no exception, as the extracts from past journals printed below illustrate.
From its very inception, the National Defense Transportation Association has been changing. Founded as the Army Transportation Association in 1944, it was a scant five years before the name and entire mission of the association was changed. The National Defense Transportation Association emerged on April 25, 1949—and with it a new logo and a new masthead for the Defense Transportation Journal. In fact, the journal masthead has changed no less than 14 times since the first issue—about once every four years! DTJ
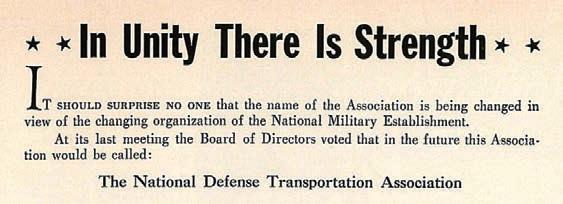
May-June 1949
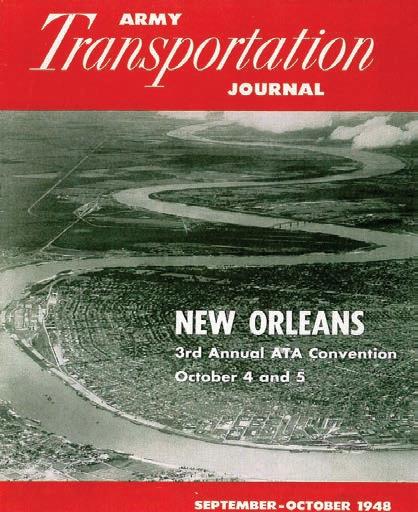
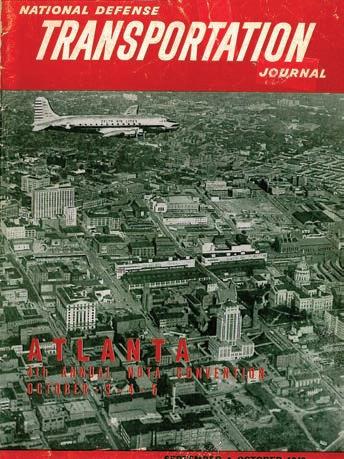
Covers from the New Orleans and Atlanta Forum issues show the change in the association’s name.
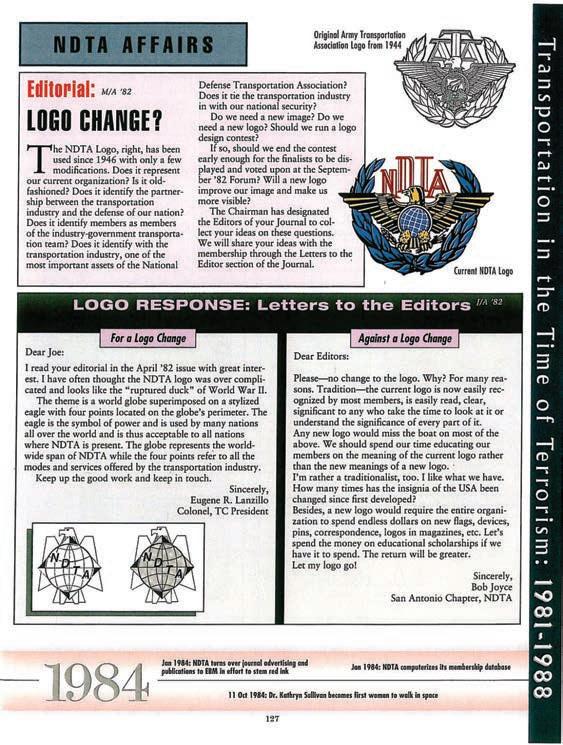
In 1982 a logo change was a hot topic of discussion within the membership.
In 1984 a new logo was proposed. Thankfully, some have said, it was not accepted.
Today the issue is before us again. This time, not the logo itself, but the appropriateness of the association’s name. To many, Defense Transportation seems to be too narrow to fit the current emphasis on distribution and supply chain management. Suggestions are to emphasize the initials NDTA in our name the way big companies like IBM, AT&T and 3M do. The actual name would not be spelled out, but a tag line would be added that would be more descriptive of our association. Examples that have been suggested include: NDTA – The Association of Logistics Professionals; NDTA – Serving Logistics Professionals; or NDTA – A Partnership of Logistics Leaders.
ALL OF THESE FIRMS SUPPORT THE PURPOSES AND OBJECTIVES OF NDTA
SUSTAINING MEMBERS
A.I.R., Inc - USA d/b/a M 2 Transport AAR Mobility Systems ABF Freight System, Inc. Air Transport Assn. of America Air Transport International, LLC AIT Worldwide Logistics, Inc. American Maritime Officers American Public University System American Road Line American Trucking Associations American United Logistics ARINC Army Air Force Exchange Service Arven Freight Forwarding, Inc. Associated Global Systems Astar Air Cargo, Inc. ATA Airlines, Inc. Baggett Transportation Co. Blue Bird Coachworks BNSF Railway Co. Bender Shipbuilding and Repair Co., Inc. Boyle Transportation Cargo Transport Systems Co. Carlson Hotels Worldwide C.H. Robinson Worldwide, Inc. Chalich Trucking, Inc. Chamber of Shipping of America Computer Sciences Corp. Comtech Mobile Datacom Corporation CRST International, Inc. Crowley Maritime Corp. CWT SatoTravel C2 Freight Resources, Inc. Delta Air Lines, Inc. Dimensions International, Inc.,—
wholly-owned subsidiary of Honeywell DynCorp International Dynamics Research Corp. Efficient Hauling Systems LP dba EHS Industries Enterprise Rent-A-Car Europcar Fikes Truck Line GE Aviation General Dynamics/American Overseas Marine GeoDecisions Global Maritime & Trans. School-USMMA Greatwide Dallas Mavis Intermodal Association of North America (IANA) Intermarine, LLC International Commodity Carriers, Inc. International Longshoremen’s Association, AFL-CIO Intl. Organization of Masters, Mates and Pilots ITLT Solutions, Inc. Interstate Distributor Co. KGL Transportation Co. Kansas City Southern Keystone Shipping Company Knight Transportation Liberty Maritime Corporation LMI Lockheed Martin Aeronautics Co. Luxury Air Jets MacGREGOR (USA) Inc. Matson Integrated Logistics Matson Navigation Co., Inc. Mayflower Transit McCollister’s Transportation Systems, Inc. MEBA Menlo Worldwide Mercer Transportation Co. Mi-Jack Products Mobility Resource Associates National – Alamo (Vanguard Car Rental USA, Inc.) National Air Carrier Assn., Inc. National Van Lines NCL America, Inc. North Carolina State Ports Authority Northwest Airlines NYK Logistics Americas Ocean Shipholdings, Inc. Old Dominion Freight Line, Inc. Omega World Travel Omni Air International, Inc. OSG Ship Management, Inc. Overdrive Logistics, Inc. Pacer Transport The Pasha Group Pilot Air Freight Services Port of Beaumont Port of Oakland Powersource Transportation, Inc. Pratt & Whitney PRTM Management Consultants, LLC Priority Air Express Raith Engineering Sabre Travel Network Savi Technology Sealed Air Corp. Sealift, Inc. Seafarers Int’l Union of N.A. AGLIWD Sea Star Line, LLC Southeast Vocational Alliance Southwest Airlines SRA International, Inc. Stanley Associates, Inc. SSA Marine Team Worldwide TQL Totem Ocean Trailer Express, Inc. (TOTE) Transportation Institute Transportation Intermediaries Assn. (TIA) TRI-STATE Expedited Service, Inc. Tri-State Motor Transit, Co., (TSMT) TTX Company Tucker Company United Maritime Group Union Pacific Railroad United Airlines UPS Freight United Van Lines, Inc. UTi Worldwide, Inc. VT Halter Marine, Inc. Wagler Integrated Logistics, LLC Whitney, Bradley & Brown, Inc. XIO Strategies, Inc.
REGIONAL PATRONS
AAAA Forwarding, Inc. AAT Carriers Acme Truck Line, Inc. Advantage Rent-A-Car AHI Corporate Housing American Moving & Storage Assn. Association of American Railroads Asynchrony Solutions, Inc. Avis Budget Group AWARDCO Freight Management Group, Inc. BEC Industries, LLC C5T Corporation The Cartwright Companies Center for the Commercial Deployment of Transportation Technologies (CCDoTT) Ceres Terminals, Inc. Chassis King C.L. Services, Inc. CSI Aviation Services, Inc. Delaware River Maritime Enterprise Council (DERMEC) DHL Japan Dollar Thrifty Automotive Group Federated Software Group FlightWorks Fox Rent A Car General Freight Services, Inc. Great American Lines, Inc. Green Valley Transportation Corp. Hawthorn Suites – Alexandria, VA Hilton Hotels Corporation The Howland Group, Inc. HudsonMann, Inc. Hyatt Hotels and Resorts The Indiana Rail Road Company
IntelliTrans, LLC JAS Forwarding (USA), Inc. Kalitta Charters, LLC Korman Communities AKA a division Labelmaster Software Liberty Global Logistics LLC Logistics Management Resources, Inc. LTD Management Company, LLC Maersk K.K. MCR Federal, LLC (MCR) MTC Technologies MBA | Morten Beyer & Agnew Naniq Systems, LLC NCI Information Systems, Inc. Oakwood Corporate Worldwide Patriot Contract Services, LLC Payless Car Rental Philadelphia Regional Port Authority Port of San Diego PowerTrack, US Bank Project ACTA Quality Support, Inc. Seabridge, Inc. Sea Box, Inc. SkyLink – (USA) SR International Logistics, Inc. Stratos Jet Charters, Inc. Trailer Bridge, Inc. Trailways Transportation System Transcar GmbH Trans Global Logistics Europe GmbH Truva International Transportation & Logistics USMMA Alumni Foundation, Inc. Utley, Inc. The Virginian Suites Veteran Enterprise Technology Services, LLC
Agility Defense & Government Services + PLUS American Shipping & Logistics Group (ASL) + PLUS APL Limited + PLUS Bennett Motor Express + PLUS Choice Hotels International + PLUS CEVA Logistics (formerly EGL Eagle Global Logistics) + PLUS FedEx + PLUS Global Aero Logistics, Inc. + PLUS Horizon Lines, Inc. + PLUS IBM + PLUS InterContinental Hotels Group + PLUS Landstar System, Inc. + PLUS National Air Cargo + PLUS Panther Expedited Services, Inc. + PLUS Ports America Group + PLUS Universal Truckload Services, Inc. + PLUS YRC Worldwide + PLUS
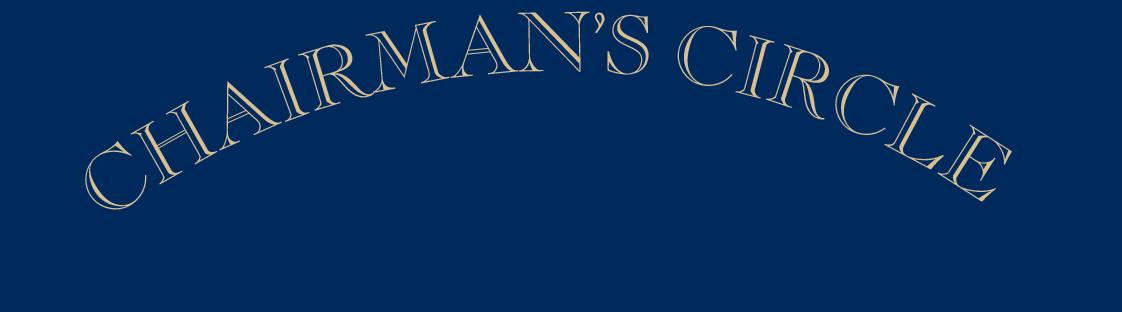
Accenture American Roll-On Roll-Off Carrier, LLC Atlas Air Worldwide Holdings BAX Global Benchmarking Partners The Boeing Company Booz Allen Hamilton Bristol Associates CorTrans Logistics, LLC CSX Transportation DHL Evergreen International Airlines, Inc. Gemini Air Cargo, Inc. Hapag-Lloyd USA, LLC The Hertz Corporation International Shipholding Corp. Kuehne + Nagel, Inc. Lockheed Martin Maersk Line, Limited Norfolk Southern Corporation Northrop Grumman Corporation Odyssey Logistics & Technology Corporation Qualcomm Incorporated R&R Trucking Ryder System, Inc. Science Applications International Corp. (SAIC) UPS UTXL, Inc.
A Worthy Cause Denise A. Bailey Director, Government Sales Yellow Transportation
Ok, I know what you are thinking . . . more money out of my pocket. But wait, read on because I think this is a cause that your company may want to support.
Morill Worcester, Founder of Wreaths Across America (WAA) and President of Worcester Wreath Company in Harrington, Maine, will receive the NDTA Distinguished Service Award at the Atlantic Regional Forum in Hershey, PA, on June 27. In what began as one man’s dream and a heartfelt gesture, Worcester initiated the Arlington National Cemetery project—donating thousands of wreaths each Christmas season to adorn the headstones of our fallen veterans. The idea caught on and has picked up steam since its inception in 1992!
This year, Morrill Worcester and the Worcester Wreath Company will continue to make their annual wreath donation, but transportation assistance is needed. Perhaps 90 to 100 truckloads will be needed to accommodate the nearly 500,000 wreaths expected to be made and donated this year.
In 2007, seven companies made a contribution in kind. NDTA corporate members Boyle Transportation and UPS were among the generous corporations who donated their transportation services. This year, people in Houston have placed a HUGE order, so help will be needed to deliver wreaths made in Maine to the National Cemetery in Houston.
If you’d like to take part, please contact Marcy (T: 207-483-2039) at Wreaths Across America headquarters. Wreaths are delivered and displayed at Veteran’s cemeteries in several cities. Or, you may want to initiate ceremonies at a new site.
If you plan to attend the Regional Forum in Hershey, you’ll have a chance to meet Morrill Worcester. Members of NDTA’s Central Pennsylvania Chapter, co-host of the event along with the Washington, DC, Chapter, will be on hand, too. They participated in WAA ceremonies last year, and their Chapter President, John Fasching, has made the challenge to all NDTA members to join the cause this holiday season.
A worthy cause indeed! DTJ
Dr. Kent N. Gourdin
Deregulation and Competition: Lessons from the Airline Industry by Jagdish N. Sheth, Fred C. Allvine, Can Uslay, Ashutosh Dixit, Fred C. Allvine (SAGE Publications, 2007), ISBN-13: 9780761935964, 348 pp, $49.95. T he US airline industry has been taken as an in-depth case study. This thought-provoking book chronicles the evolution of the airline industry and explains what lies ahead for airlines across the globe. The authors present compelling evidence on how the paradigm shift that is taking place in the airline industry is linked to the big-bang approach to deregulation. There are lessons to be learned from the US as Europe and Asia undergo the (airline) deregulation experience from a public policy as well as a corporate perspective. Deregulation and Competition: Lessons from the Airline Industry also addresses the crucial question of what will happen to the airlines that are in turmoil. In addition to the comprehensive analysis of the airline industry’s evolution, the authors draw from extant theory as well as from their own research to predict and explain which (and what kind of) airlines are likely to succeed and fail in domestic and international markets. The downfall of legacy carriers and rise of discount carriers is analyzed in detail. The nontechnical analysis is intended for a broader audience than airline and management professionals and is especially interesting given the unexpected rise in fuel prices since the book was written. DTJ (From the publisher)
Agility. . . . . . . . . . . . . . . . . . . . . . pg. 26 ARRC . . . . . . . . . . . . . . . . . . . . . . pg. 11 Avis. . . . . . . . . . . . . . . . . . . . . . . . pg. 21 Enterprise. . . . . . . . . . . . . . . . . . . pg. 8
DTJ INDEX OF ADVERTISERS
FedEx. . . . . . . . . . . . . . . . . . . . . . . Cov 4 Intercont. Hotels Group . . . . . . pg. 22 Kane Company. . . . . . . . . . . . . . pg. 28 Landstar. . . . . . . . . . . . . . . . . . . . pg. 31 Maersk SeaLand. . . . . . . . . . . . . pg. 1 Marine Terminals Corp.. . . . . . . pg. 5 Panther . . . . . . . . . . . . . . . . . . . . . pg. 2 SAIC. . . . . . . . . . . . . . . . . . . . . . . . Cov 3
T. F. Boyle Transportation. . . . . . pg. 6 United Van Lines. . . . . . . . . . . . . Cov 2 UT Center for E.E.. . . . . . . . . . . . pg. 32
Integrated Systems, Integrated Transportation Networks, and Integrated Supply Chains.
Supporting the Warfighter. We take it personally.

SAIC is driven to keep Warfighters supplied. Our integrated logistics systems automatically sense and respond to current stock levels, helping transport supplies when they’re needed. Our radio-frequency identification (RFID) system helps enable asset visibility so you know where the supplies are, whether in stock or in transit. Whether single mode, multi-modal, or virtual; oil, parts, or information; SAIC systems help get the warfighters what they need, where they need it, when they need it.
For more information, visit www.saic.com
A
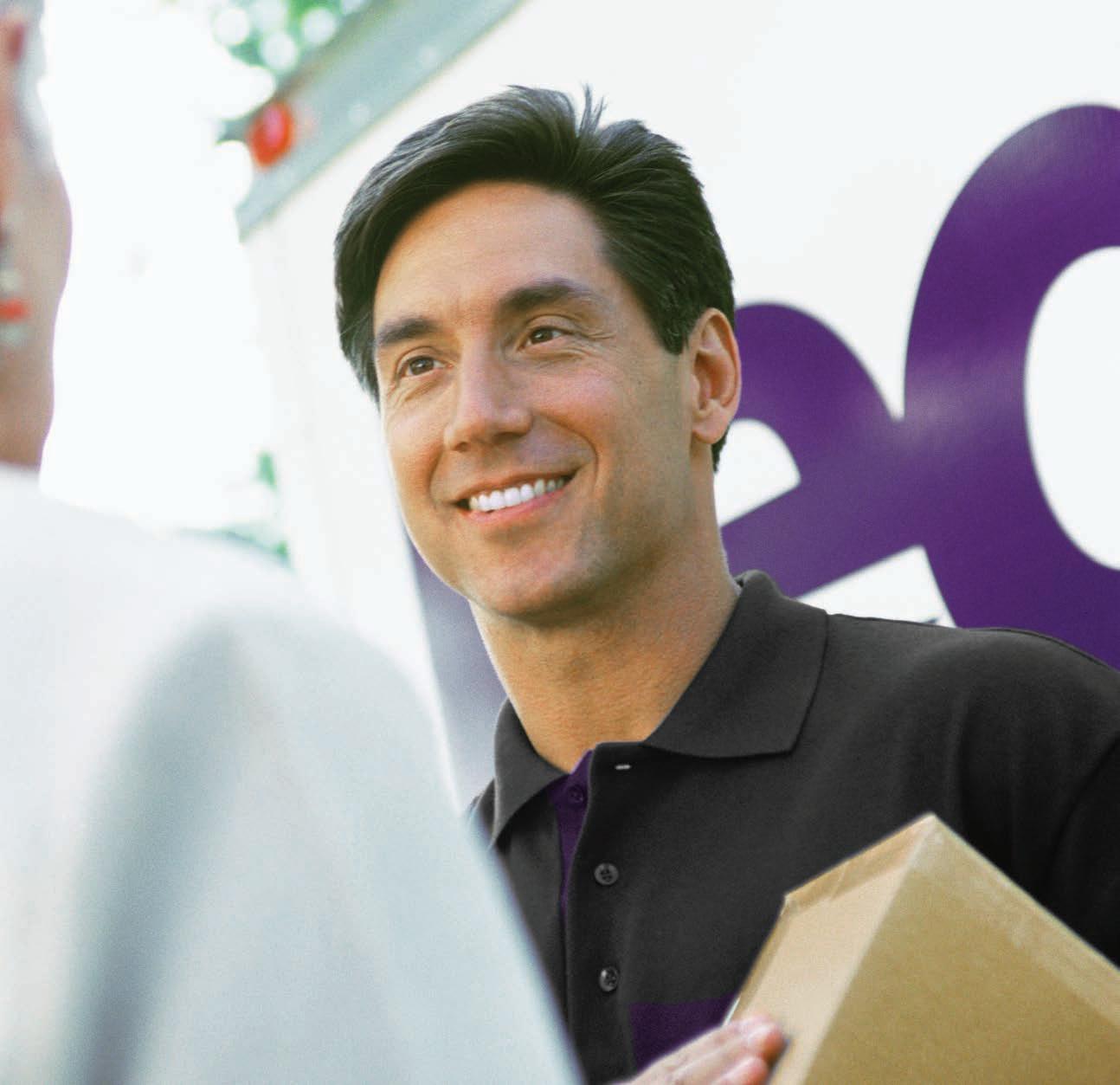
We’re trained for special services.
In the U.S. Armed Services, there’s no room for error. You need access to goods and information from around the world and a shipping company with the reliability and expertise to deliver it. With FedEx you have access to more than 220 countries and territories and the flexibility to handle whatever comes your way.