
17 minute read
Get on board with digital signage
From retailers and restaurants to lobbies and waiting rooms, digital signage is used by businesses and organizations everywhere with increasing frequency. Tyler Reid, head of marketing at iFIDS, gives some insight into how the company has been helping implement effective digital signage in airport settings.
There was a time when digital signage required expensive and proprietary display technologies maintained by expert staff. Mature cloud-hosted solutions for content management, in combination with increasingly capable and affordable hardware have changed the situation. Today, digital signage setup can be as easy as hanging a screen at any location with Internet access and attaching a mini-PC.
Di gital future
As the technology permeates more workplaces, there is an increasing consciousness of the benefits that it brings, such as economizing staff time, conveying information 24/7, customization and impression advantages vis-à-vis static displays, as well as increased engagement and brand awareness. Although conveying up-to-date flight information remains the predominant use for digital signage in airports, other applications are becoming ever more common. Included amongst these are advertising to drive ancillary revenue, promotions that increase brand awareness and airport initiatives, infotainment, visual paging, and back-end screens for dedicated use by operational users. The customization potential inherent in digital displays allows assortments of content to be hosted at a single location as well.
Hands-on experience
The number of displays hosted by iFIDS has been steadily trending upwards in recent years. Though first-time clients account for some of this growth, the addition of new screens by existing customers has been the main driving force behind the higher numbers.
"iFIDS hosts over 500 digital signage displays throughout North America and the Caribbean.”
Dedicated displays for gates, podiums, check-ins, baggage areas, and wayfinding in particular have been rising in popularity.
The increased role of digital signage can allow for multi-functional, context-sensitive screens. One example might be a check-in or gate screen that defaults to standard flight display when not in use, while co-locating a playlist of banner ads and a visual paging footer. Accurate and timely flight information integrated from multiple real-time and scheduled sources is obviously one key to successfully building such a display. Also important are easy-to-use interfaces for manual operations such as late-stage gate reassignment. iFIDS allows management of all displays from any computer or mobile device with flight editors, graphical utilities for gate or asset management, check-in logo selectors, and interfaces for building advertising playlists.
Check out the gate displays
Small changes can yield significant improvements. One example is the deployment of the four gate screens at Prince George International Airport. Prior to their introduction several years ago, passengers for multiple departures congregated in one big area during busy times of day, leading to confusion, additional workload, and potential delay. With the installation of carefully designed screens showing gate assignment and order of flights, passenger guesswork is removed, boarding proceeds more smoothly, and perceived wait time is reduced. According to Lindsay Cotter, manager of marketing and communications at the airport, the signs are "a welcome addition to our boarding lounge. Upon installation, they automatically added a fresh, clean, updated look to the space and have proven to be integral to customer service and passenger direction.”
Si gnage flying high
As the underlying technology becomes more accessible and passenger expectations continue to rise, the demand for digital signage will only increase. Larger, customizable, and more numerous digital displays will continue to improve the travel experience and enrich wait time at airports for the foreseeable future.
Manage ent of change in the airport industry
By Matthew Hopley, M. Eng., P. Eng., Manager – Alberta Branch, LRI Engineering Inc.
When facilities are constructed and commissioned, they begin their lifecycle in a generally code compliant and safe manner. As the facility ages, renovations, change of use, or a multitude of other factors can come into play, which alter the level of safety within a building, facility, or site. Unchecked changes compounded over time can erode the safety factors in the initial design, or can start to move an operation or process outside of its normal operating parameters. As a result, previously safe and appropriately protected facilities can develop high-risk conditions for losses. Losses including process interruptions, spills, environmental contamination, fires, explosions, and losttime injuries can all affect airports and their supporting operations, and the risk of these can increase without sufficient management of change.
Management of change (MoC) is a common term in process industries and within process engineering. It is often used for process management for Occupational Health & Safety compliance, and can be undertaken as part of an organization’s joint health & safety committee. The objective of the MoC process is to formalize changes or proposed changes and assess their impact on the level of safety of the operation. In the case of airport facilities, MoC can include tracking how people complete work, understanding whether or not deviations occur for work processes, evaluating changes to how and where procedures are conducted, and reviewing ongoing maintenance of critical systems. From a fire and life safety perspective, this can include evaluating safe work practices like hot work, considering storage arrangements of goods (both dangerous goods and ordinary products), and reviewing the potential change of use of spaces from one application to another. Changes will affect both land side and air side operations, and both passenger-facing services and back-of-house operations and maintenance.
Frequently, changes including employee turnover or retirement, renovations and drives to densify or improve the service offerings at an airport can catalyze change. Without a defined process or method to track changes, document the conditions, or otherwise transfer knowledge of a site, information regarding the ways in which to maintain safety can be lost from an organization. An important example in the built environment occurs where performance-based design or alternative solutions are used, which depend upon the maintenance of mitigating features, implemented as part of the design. These features can include special considerations regarding detection or suppression, the
use of a space, or something as simple as construction type or finish material. Without adequate MoC, a space designed on a performance basis may no longer meet the conditions for safe, continued use.
Organizations can look to teams, including both internal and external experts, to review MoC processes and documentation, conduct facility inspections and audits, conduct risk analyses, document deficiencies and changes, and develop plans to help maintain an acceptable level of performance and safety. The goal of an MoC program is to develop a consistent, disciplined methodology for identifying proposed changes, evaluating their potential risk to an organization or facility, monitoring progress of the change, and ideally tracking the outcome or effectiveness of the change to achieve continuous improvement. This methodology allows for innovation, while managing the overall risk of a site or operation, reducing it to a tolerable level.
LRI Engineering Inc. (LRI) specializes in emergency planning, fire protection engineering, building and fire codes consulting, and accessibility consulting services, from its offices in Toronto, Ottawa, Calgary, and Montreal. Matthew Hopley, M. Eng., P. Eng., is LRI’s branch manager, Alberta, and is based in Calgary, Alta. Hopley provides building and fire code consulting and fire protection engineering services for private and public sector clients. Hopley can be reached at mhopley@lrifire.com, or ext. 711. For more information about LRI, please visit www.lrifire.com.
Li fe after CO VID-19: Now what?

All immediate and future spending your organization requires should be determined by whether it is a "want" or a "need".
The rule of thumb for a crisis is that it takes 30 days of recovery for every one day of response. Recovery of operations is far more work for your organization than the initial response itself. When making plans for business resumption, airports need to prioritize what is essential and what is a “nice to have”. Consider the health and wellness of your team – whether they have been working during COVID-19 or staying at home, fatigue and a sense of hopelessness can set in. Airports should be doing what they can now to not only take care of their staff, but they should also be developing a strategy to prepare for them to return to the “new normal” of operations.
Given the magnitude and duration of the crisis, the following items will be major considerations that will form your business resumption strategies: • Government grants/loans • Revenue strategies • Cost-cutting initiatives • SMS and regulatory requirements • Staff training • Emergency management – accidents will not take a break for a crisis • Communications – internal and external stakeholders • The team
Airports and airport associations have already begun the process of lobbying levels of government to gain support related to airport operations and employee funding initiatives. Your organization should also be lobbying politicians from all levels of government to ensure that they are supporting and pushing for the muchneeded help in navigating the challenges your airport is facing and will face.
Your organization should assume that the projected budget is at ground zero. It will take time for the airport sector to kick start, and for that reason, projected revenues may no longer be relevant in some cases. Local airport businesses and tenants may not have the immediate ability to pay leases or rent. All immediate and future spending your organization requires should be determined by whether it is a “want” or a “need”. What work can be deferred? What are the consequences of not doing the repair or project?
Cutting the cost of doing business is never an easy task. Organizations gain a certain comfort level in the way they do business, but it is critical to look at every corner of the operation to see where reductions in expenses could be tolerated. With your leadership team, imagine that you have a clear slate and have to take over your airport with minimal resources. Forget about how you conduct business now; what is the minimum staffing level required to meet regulatory obligations? What equipment can perform the tasks? How can you cut utility costs? If you set aside traditional revenue streams, what additional revenue ideas can you come up with based on the airport infrastructure and organizational talent?
Although it is important for Transport Canada to work with airports in allowing some flexibility with hard deadlines
related to regulatory requirements, it should not excuse airports putting the Safety Management System (SMS) program on hold. SMS requirements were put in place to prevent injury and death, as well as to help create a proactive culture to identify potential hazards to aviation safety. Work on a strategy to maintain your SMS to the best of your ability based on business resumption strategies. Staff should still be trained in regulatory subjects, but can your organization adapt new training strategies such as an online platform, where applicable? Accidents and emergencies happen anywhere, anytime, and are a critical component for safety at the airport. Staying on top of your emergency management program and exercises should be considered a priority in your business resumption strategies.
The faster you can instill a sense of life returning to “normal” for staff, the better it will be for morale and work production. Supports such as an employee assistance program should be considered for your staff. It is important to recognize that it could take a while for staff to reintegrate themselves back into the workplace environment.
Everyone needs honest, up-to-date and relevant communication now and until the end of recovery. This includes communication with both internal stakeholders, such as staff, as well as external partners like tenants, airlines, airport users, and the community. When stakeholders do not hear from you, they will turn to others, often receiving misinformation.
Your organization will get through this; it may look different than it was before the COVID-19 crisis, but with the right team and leadership it can also create new opportunities and positive changes moving forward.
Airports and airport associations have already begun the process of lobbying levels of government to gain support related to airport operations and employee funding initiatives during a crisis.

PaviX – PRO VEN WINNER FOR ALL CANAD IAN AIRPORT CONCRETE INFRASTRUCTURE
International Chem-Crete Corporation (ICC) manufactures and sells PaviX, a unique line of crystalline waterproofing products that penetrate into the surface of cured concrete to fill and seal pores and capillary voids, creating a permanent protective zone within the concrete substrate. Once concrete is treated, water is prevented from penetrating through this protective zone and causing associated damage, such as freeze-thaw cracking, reinforcing steel corrosion, chloride ion penetration, and ASR related cracking. Founded in 1969, in Dallas, Texas, ICC has grown into an international leader in VOC free waterproofing chemicals, with exports to over 65 countries. ICC is focused on making environmentally safe water based and solvent free waterproofing products. Chem-Crete PaviX CCC100 is known to be environmentally safe for treating bridges and roadways over open bodies of water, such as Grand Avenue in West Des Moines, Iowa. In 2015 alone over 3 million square feet of concrete has been protected from moisture related issues using PaviX CCC100 in the Midwest alone. Installations including convenience store parking lots, county
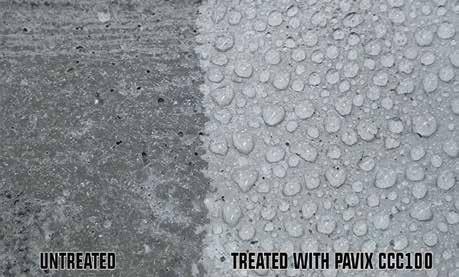
and city bridges, municipal roadways, control joints-interstate highways, airport properties, and concrete block, just to mention a few. As an example Logan Contractors Supply, Inc., of Des Moines, Iowa, has interacted and represented the PaviX product of ICC for approximately 10 years. During this time, the PaviX product has evolved within Logan’s protection product offerings, as one of the premiere barrier technologies. Logan has applied thousands of square feet in the Midwest area, and has been diligent in assisting ICC in their testing and quantification of the crystalline product. PaviX CCC100 is a unique advanced water-based technology designed for the protection of large-scale concrete substrates against moisture intrusion and the damage associated. Damage such as repeated freeze/thaw cycles, advanced de-icing chemical brines, as well as alkali silica reactions are all issues where PaviX CCC100 is superior in protection. PaviX CCC100 assists treated concrete by mitigating moisture intrusion and eliminating or reducing moisture and water associated problems. PaviX CCC100 provides three effective mechanisms for
ICC CANADA
concrete protection in all weather conditions by formation of two types of crystals and water repellency. In the presence of moisture, one type of crystal swells, therefore, blocking the pores completely. The second crystal absorbs the extra moisture on the surface of the first crystal preventing surface moisture from diffusion into the concrete. These hydrophilic and hygroscopic properties provide advance double and durable protection against moisture penetration into the concrete. PaviX CCC100 has undergone a battery of ASTM specified tests by multiple independent testing laboratories familiar

ICC CANADA
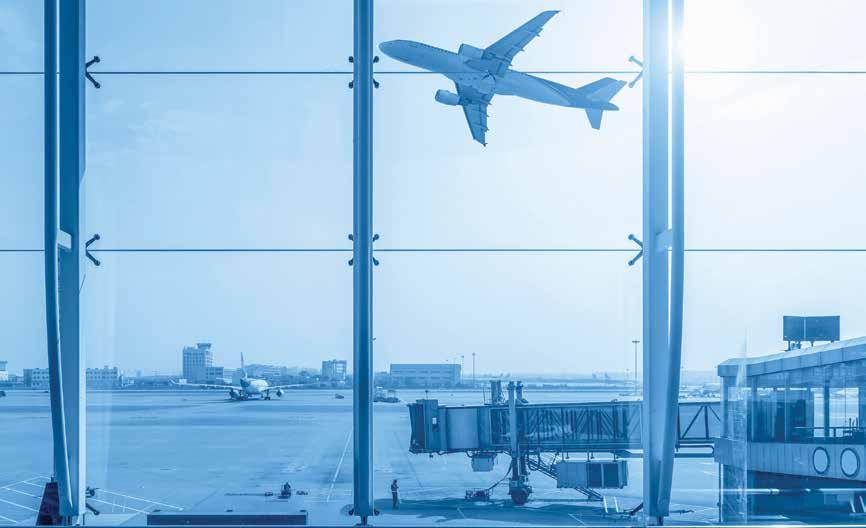
PavixCCC100 is patented dual crystalline waterproofing product that has been proven to penetrate into the surface of green or cured concrete to fill and seal pores and capillary voids, and cracks up to 1/16” creating a permanent protective zone within the concrete substrate.
Once concrete is treated, this proven technology will prevent water from penetrating through the protective zone and causing associated damage, such as freeze-thaw cracking, reinforcing steel corrosion, and chloride ion penetration. One application of the PavixCCC100 crystalline penetrating sealer will waterproof and seal the surface, as the hygroscopic crystals continuously seek out the vapor within the substrate.

FIELDS OF APPLICATION: • Airport Runways • Aircraft Parking • Tunnels • Parking Lots • Sea Ports • Airport Taxiways • Bridges • Concrete Roads • Highways • Buildings • Walkways and more!
4101 106th STREET, DES MOINES, IOWA 50322 250-801-8046 www.canadaicc.com

with current concrete testing methods. The current ASTM tests are as follows: FreezeThaw test C-666, Scaling Test C-672, Product Penetration C-856, Abrasion Resistance C-944, Water Soluble Chloride C-1218, PullOff Strength Test D-4541 and Water Vapor Transmission E96. Additional Facts About PaviX CCC100 Growth Technology.

How long does PaviX last? PaviX product application is permanent. Once placed, the crystals remain active indefinitely. Its unique crystalline growth structure will not deteriorate.
How resistant is PaviX to chemicals? Based on independent testing PaviX is not affected by a wide range of chemicals including mild acids, solvents, chlorides and caustic materials. It is resistant to oils, fuels and prevents dusting.
Is PaviX affected by temperature, humidity, ultraviolet and oxygen levels? Humidity, ultraviolet and the oxygen level (oxidation) have no effect on a PaviX. As humidity increases, the crystals actually swell in the capillaries to block moisture from entering the capillary.
Does PaviX protect reinforcing steel? Yes. By preventing the intrusion of chemicals, salt water, sewage and other harmful materials, PaviX protects concrete and reinforcing steel from deterioration and oxidation. If corrosion has already present,
Is PaviX toxic? No, PaviX contains no volatile organic carriers (VOC) is completely safe to the environment.
Can PaviX be applied against hydrostatic pressure? Yes, because PaviX is not dependent upon adhesion to the concrete surface and instead becomes an integral part of the concrete mass through crystallization, it is capable of resisting hydrostatic pressure from either side (positive or negative) of the concrete.
Is PaviX used to waterproof cracks, joints and other defects in concrete? Yes, PaviX has a specific repair system that utilizes its unique crystalline waterproofing technology to stop water flow through up to 1/16 cracks. In the case of expansion joints or chronic moving cracks, a flexible sealant is recommended.
Is PaviX suitable for use on surfaces other than concrete? PaviX is totally compatible with the chemistry of concrete, whether poured in-place, pre-cast or concrete block. PaviX may also be used on mortar, plaster, stucco, terrazzo, exposed aggregate and any sand aggregate cement combination
Can paint and other finishing materials be applied over a PaviX coating? Yes, paint, cement purge coats, plaster and stucco can be applied or installed over concrete protected with PaviX.
What are some typical PaviX applications? PaviX can be applied to any concrete surface. Applications include bridge decks, airport runways, reservoirs, tunnels, parking structures, sidewalks, sewage and water treatment tanks, secondary containment structures, underground vaults, foundations, roof decks, and below grade construction.
How is PaviX different from other products? The dual PaviX crystalline formation (hygroscopic and hydrophilic) for concrete waterproofing is substantially different from traditional barrier products (membranes, cementitious coatings): 1. PaviX creates a crystalline structure deep within the pores and capillary tracts of the concrete mass to prevent the penetration of water and aggressive chemicals and also form a barrier at the surface of the concrete. 2. PaviX it is resistant to hydrostatic pressure. 3. PaviX will seal hairline cracks up to 1/16 inch. 4. PaviX will not deteriorate after years of intense service. 5. PaviX is permanent and crystals activate whenever moisture is present

What is the recommended application rate for PaviX? Typically, a coverage rate of between 150 and 200 square feet per gallon will provide ample coverage. Consultation with the manufacturer’s technical department or a local PaviX representative for assistance in determining the appropriate dosage rate based on specific requirements and conditions of your project.
INSTALLED PRODUCT PERFOR MANCE
Description test method results toxicity 48-hour acute toxicity test non-toxic to flora and fauna: • V.O.C. Content 0 • Chloride Ion Penetration ASTM C1202/
AASHTO T277 < 2000 coulombs • Abrasion Resistance ASTM C 944 4.2 grams / m2 • Water Vapor Trans. ASTM E 96 2.0 Perms • Adhesion ASTM C 1583 400 PSI • Scaling Resistance ASTM 672 Not to exceed 0.64 • Static Slip Resistance ASTM F 609 No Effect
Skid Resistance • ASTM E 303 No Effect Freeze/Thaw 300
Cycles • ASTM C 666 Mass change not to exceed 0.09 percent Freeze/Thaw 300 Cycles • ASTM C 666 Length Change not to exceed -0.017 percent Freeze/Thaw 300 Cycles • ASTM C666 RDM 97 percent Water
Absorption ASTM D 6489 1.5 percent by wt./ 7 Days.