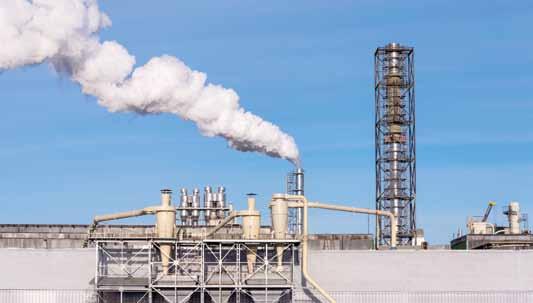
4 minute read
Thinking out of the envelope about your envelope
With the increasing demands of building-code officials and the expanding scope of limitations placed on the building community by government environmental agencies, the work of product developers and formulators continues to become more difficult.
InnovatIon tHrouGH reGulatIon
One specific limitation is related to the allowable level of volatile organic compounds (VOC) in architectural coatings. This product classification includes many of the common roof coatings that are available in the Canadian market today. The following chart describes the current limitations as described by the Canadian Environmental Protection Act. In many cases, the concentration limits are derived from limits developed in the U.S. Current changes are underway in the U.S. to further reduce the allowable VOC in architectural products. If history is an indicator, the new VOC limits will soon become part of the Canadian standards. (Depending on which side of parliament you are on, this could be a good thing or a bad thing.) Regrettably, this can make formulating useful products more difficult.
Description1
Thermoplastic Rubber coating and mastic, incorporating no less than 40% by weight of Metallic pigmented coating, containing at least 48 g of elemental metallic pigment per litre of coating as applied Bituminous roof primer Any other bituminous roof coating Non-‐bituminous roof coating, for application to roofs to prevent penetration of the substrate by water or to reflect heat and ultraviolet radiation
VOC, although not completely accurate, is synonymous with solvent. Solvent is the carrying media for the proper application of each of the described architectural products. The solvents work to reduce the viscosity of the applied product and allow for ease of application; and in some cases, the leveling properties of coatings. As the levels continue to become more restrictive, it becomes more and more difficult to produce an effective product. Simply “taking more solvent out” becomes an unviable option.
Many formulators over the past several years have explored and implemented

thermoplastic rubbers in its total resin solids, for application to roofing or other structural surfaces. the use of “exempt solvents”. Exempt
VOC Concentration Limit (g/L)
550
500
350 300
250 solvents are considered to be lower ozone “depleters” than alternative solvents. There are few exempt solvents that are a proper fit for use with roofing products. The more common choices include TBAC (tert-butyl acetate), DMC
GreenLock application. GreenLock odourless polyether adhesive application by Garland.
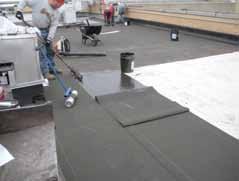

(dimethyl carbonate), and PCBTF (parachlorobenzotrifluoride). Each of these candidates, while somewhat effective at producing an acceptable finished product, has its own shortcomings, be it strong and undesirable odour (PCBTF), low flash point (DMC), or potential cancer risk (DMC). With proper usage, much of this can be overcome, but ultimately formulators could seek more environmentally compliant solutions. For example, ultra-high solids or zero-VOC chemistry is available.
By utilizing reactive polymer chemistries, such as moisture-cure polyurethanes or waterborne coatings, formulators can provide effective solutions that both comply with VOC limits and meet the demands of rooftop performance. Many of these solutions are quite common, such as acrylic-based reflective coatings, while others are less common, such as low-solvent urethane coatings or moisture-cured polyether adhesive. Seek out the alternative solution and work with quality manufacturers to get the best solution available. InnovatIon tHrouGH need
While some of the demand for change comes from regulation and code, others may come from innovation and need.
Recognizing that air quality in enclosed structures is becoming more and more critical, and with the proliferation of MRSA and airborne pathogens, innovators have begun exploring means by which coatings can be used to assist in bio-mitigation. There are many solutions that have been formulated to coat interior walls for bio-resistance; there are also several different products available that can be applied to exterior walls to reduce algae and mould growth. More recently, formulators have turned their focus to the rooftop as a potential pathway for unwanted biological activity to enter buildings. Through proper formulation, one U.S. manufacturer has introduced the first application solution for rooftop control of biological growth.2 The annually applied treatment works to eliminate mould, algae, and microbial growth on the rooftop surface and can be applied to smooth, polymeric, metal, granule or aggregate surfaces.
expect More
As facility managers and owners, staying in tune with codes and regulations is critical to compliance. Understanding the downstream implication of code and regulation changes can be critical to
long-term sustainable performance. And embracing, seeking, and utilizing new and novel technology can be the launch pad for advanced facility performance and safety.
Staying in touch and informed leads to ultimate success.

About the Author: Joe Mellott holds several patents for roof-related innovations and received the 2006 Industry Statesman Award from the Roof Coatings Manufacturers’ Association (RCMA) for his work in advancing roof-coatings industry technology. A graduate of Case Western Reserve University, Mellott holds a B.Sc. in engineering, is a frequent contributor of technical articles to industrial publications, and is also a participant in numerous roofing-related organizations. He has served as the technical chair and president of the Roof Coatings Manufacturers’ Association, on the board of the Cool Roofs Rating Council (CRRC), and has held memberships in the Roof Consultant Institute (RCI), the National Roof Contractors’ Association (NRCA), and the Asphalt Roofing Manufacturers’ Association (ARMA).
reFerences: 1 http://laws-lois.justice.gc.ca/eng/regulations/
SOR-2009-264/20091028/P1TT3xt3.html 2 The Garland Company, Cleveland, OH, U.S.A.;
Clear-Shield Rx™ introduced in 2013. b