
3 minute read
Maker Labs – Occupancy changes and inspection requirements
Maker labs
occupancy changes and inspection requirements
Recently we have noted while performing regular loss control inspections of schools, an influx of what we refer to as maker labs and maker spaces. These spaces can be operating with a number of different media including 3D printers, soldering operations, paint, metal, robotics, and general art supplies.
The concerns noted when providing loss control inspections for these location are the same as any other IA shop or similar operation.
Codes and Standards – Change of Occupancy & Inspections
Various codes and standards examples come to mind in areas that we discuss on a regular ongoing basis. The BC Fire Code requires that all owners of buildings shall be responsible for carrying out the provisions of the Fire Code regardless of local fire commissioner, fire inspector, or other authority having jurisdiction inspections. WorkSafeBC and other organizations have provided documented exposure limits for many types of biological and chemical substances including vapors, plastics, and fumes.
NOTE: a change of occupancy occurs when a space or classroom within the school is being operated as something other than what it was originally designed for. An example is when a classroom space is used as a maker lab.
Inspection Requirements – Code Based and Recommended Practices
1. Has a full risk analysis review been provided? 2. Are electrical tools being used? 3. Has standard isolation been provided? 4. Has standard ventilation been provided? 5. Has standard containment been provided? 6. Has safety training been provided?
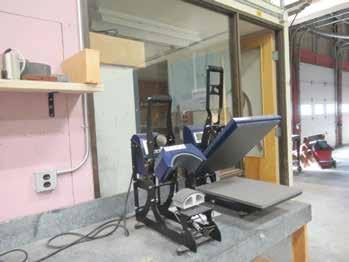

7. Is PPE available? 8. Is supervision provided?
BC Fire Code, Div B, 5.3 & WorkSafeBC Recommended Inspections
A regular (monthly) inspection program — preferably digital — should be developed and put into place which covers the following areas as a minimum: • Housekeeping review. • Electrical equipment & connection review. • Ventilation equipment review. • Isolation review. • Equipment meets requirements,
CSA, ULC, etc. • Hazardous processes and operations specific to maker-labs, 3D printers, heat and dust producing devices, etc.
Summary
1. Conduct a risk analysis or needs assessment. This is the who, what, where, why, and when section. 2. Accumulate information on your maker labs / spaces (safety surveys). The more information you have, the better informed your final decisions will be. 3. Identify all risks/hazards. This provides a starting point from which to develop plans for mitigating potential losses from occurring. Be specific. 4. Monitor progress, and make changes if needed.
Stay informed. Many changes take place on a regular basis in regards to safety equipment, facility safety, dust mitigation, and health issues, as well as the need for continued maintenance and repair procedures for existing facilities.
Talk to risk management professionals - people in your industry such as teachers, staff, and various other organizations. Someone may have already tried an idea that you are thinking about using. Alan Kavanaugh is the director of loss control at Noratek Solutions Inc. He has provided loss control services to school districts/divisions, municipalities, industry, and government operations for over 33 years. He has developed a set of training programs (workshops) and audits (safety related) to help all organizations accumulate and prioritize information and develop short- and long-term compliance plans. Kavanaugh is based out of Prince George, B.C. and provides services throughout Western Canada and the Territories. He can be reached by email at akavanaugh@noratek.com or by phone at (250) 564-2236, or cell (250) 961-8186. n
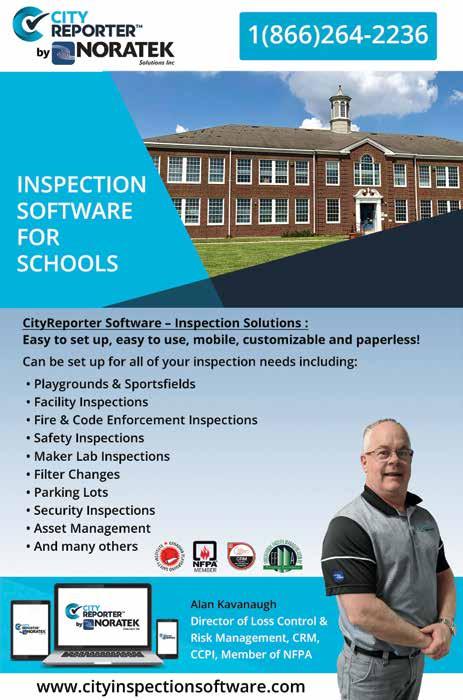