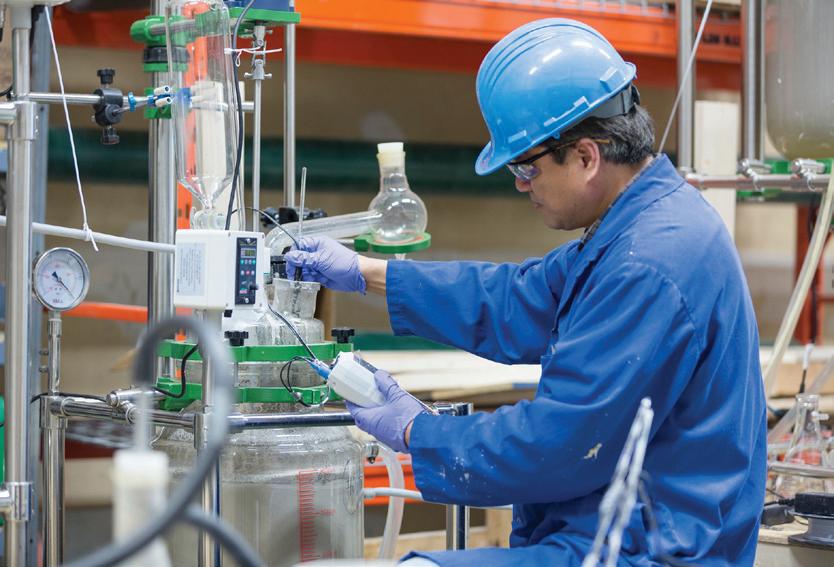
4 minute read
Powering up: Recycling critical metals from lithium batteries
By Brook Thalgott
As electric vehicle technologies advance and the energy transition continues, the demand for critical metals keeps rising. However, the primary resources for battery metals are not able to meet the growing demands for them.
“The supply and demand for major metals, such as lithium, nickel, cobalt, and copper, shows that demand will outpace supply in the next few years,” says Dr. Jack Zhang, director, Rare Earth Element Division and manager, Mineral Processing at SRC. “We may be facing a shortage of critical metals for batteries.”
Critical metals are essential to telecommunications, computing, and clean energy—plus they are a valuable export commodity and vital to Canada’s technology sector and our supply chain.
CritiCal Minerals at worK
Lithium-ion batteries (LIBs) were first invented in 1985 and commercialized
in 1991. Today they power electric vehicles (EVs), renewable energy storage, consumer electronics, power tools, and more. Metals such as lithium, cobalt, nickel, and copper are required to build LIBs and are found around the world.
“However, the current supply chain is vulnerable because the majority of refining takes place in one spot,” says Dr. Zhang. Right now, that one spot is China. “It’s important for us to develop a more balanced supply of refined metals in North America.”
At the end of their working life, LIBs end up as waste. “When a battery reaches the end of its life, it loses function and
Recycling and refining previously used metals are far better than starting a new mine, from both economic and environmental perspectives.
performance,” says Dr. Zhang. “These ‘dead’ batteries are now creating a fastgrowing environmental problem.”
Batteries clog landfills and present significant disposal issues due to their toxic components leaching out over time. At the same time, the demand for critical metal supply is increasing, posing its own environmental concerns for mining jurisdictions around the world. The technologies that require these new batteries (and the metals that power them) are developing faster than industry and governments are finding solutions for the waste.
What if there was another way to source critical metals and address the environmental concerns around spent LIBs?
enter urban Mining
The term urban mining may sound like just another buzzword, but the idea behind it is simple—what if we recycle the usable elements of spent LIBs, thereby reducing their environmental impact and addressing the growing need for more critical metals?
The idea of battery recycling is not a new one. It’s been happening for years, but it’s been focused on the ‘front end’, meaning diverting batteries from the landfill and disassembling the battery into individual components.
SRC’s direct recycling of LIB technology aims to provide an alternate source for critical metals and support the value chain of the EoL battery recycling industry.
Urban mining takes battery recycling one step further, where their metals are extracted from these parts, thereby making them available for battery and other product manufacturing. This mining activity can help meet the growing need of new batteries and technologies. Plus, it generates value from what was previously considered ‘waste’ and removes environmental contaminants from landfills.
This can also reduce the need for new mining operations that have a large environmental footprint. Recycling and refining previously used metals are far better than starting a new mine, from both economic and environmental perspectives.
let’s reCyCle
Drawing on their specialized expertise in lithium recovery processing and technologies, Zhang and his team are developing a direct recycling process of LIB metals that will help industry meet the growing demand for critical minerals and divert batteries from landfills.
EV batteries and batteries from electronics, such as cellphones and computers, are valuable for their components (e.g, aluminum, copper, nickel, and lithium), and recovery processes are designed to maximize the critical minerals from end-of-life batteries.
How it worKs
End-of-life (EoL) batteries will be dismantled in SRC’s lab through an automated process that produces minimal waste residues while carefully preserving the critical metals. These components— such as nickel, cobalt, lithium, aluminum, and copper—are extracted at high purity and recovered for immediate reuse.
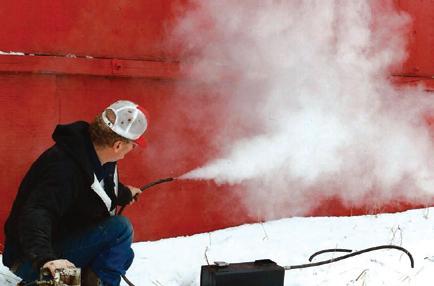
“Battery recycling is complex because of all the types of batteries and their varied composition and chemistry,” says Zhang. “But it’s not impossible. With the appropriate sorting and recycling processes in place, battery recycling can become a viable source for critical metals and minerals that addresses both the market demand and the environmental concerns.”
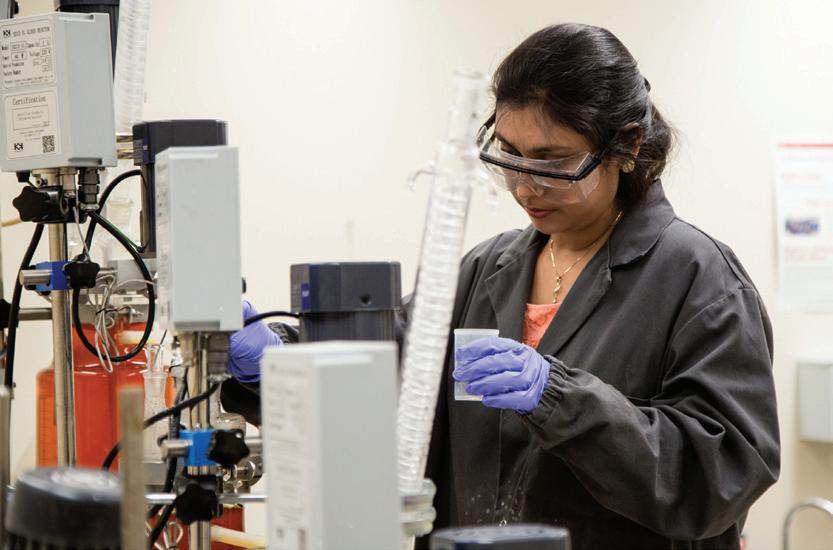
SRC can facilitate the development of the refining process for organizations interested in battery recycling.
srC litHiuM battery reCyCling serviCes
chain of the EoL battery recycling industry. Zhang outlines the following benefits as core factors to SRC’s approach:
• Reduces environmental footprint
• Increases significant secondary resources of LIB metals
• Develops new recycling technologies
• Creates a secure supply of critical metals for high tech and supports industry’s energy transition
Zhang also points to SRC’s state-of-theart labs and facilities and his team of experienced professionals as essential in developing and commercializing the proposed technology for industry.
SRC’s direct recycling of LIB technology aims to provide an alternate source for critical metals and support the value Learn more about battery recycling at src.sk.ca/services/direct-recyclinglithium-battery-metals. 7
