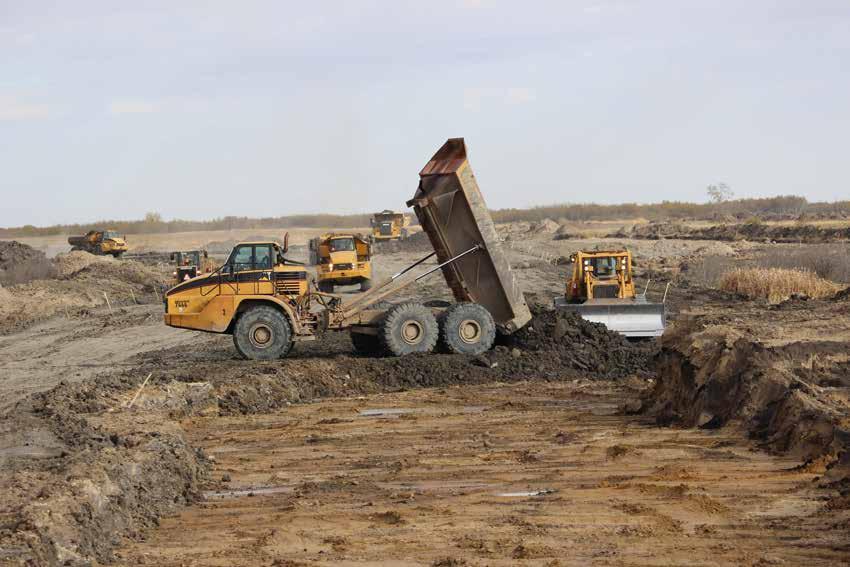
5 minute read
Panteluk Construction Ltd
KELLY PANTELUK CONSTRUCTION LTD.
When passing by a highway project or a large civil project and observing the excavation and placement of some dirt, it appears like it is a relatively easy thing to do – dig here, dump there. However, in her infinite wisdom, Mother Nature did not make all dirt equal and as it turns out there is a vast amount of science and a good dose of experience and knowhow to get the desired characteristics and performance that the design engineer and contractor want from Mother Nature’s product. Unfortunately, for many project owners and design engineers of those projects they are typically relegated to using the soils found within the confines of the project to keep project costs in line. While this could be a bad thing given the highly undesirable nature of some soils for construction purposes, Saskatchewan project owners located in the mid- and southern half of the province have access to some of the best soils in the world for constructing earthworks. This building material is commonly referred to as till and was formed through the movement and deposition of soils by glaciation. In its very basic form, till is a mixture of gravel, sands, silts, and clays in proportions that make it an ideal, stable building material for roads, dams, dykes, and relatively impervious containment cells.
Most potash mines in Saskatchewan are located within the glaciated fields of Saskatchewan and as a result, the mines have access to an abundance of till and other soil materials for constructing the civil structures required to operate potash mines. Most of these civil earthworks can be found at the back of the plant or downstream of the processing operations and are necessary for containing fine and coarse tailings – a byproduct of processing the potash. Owing to the high salinity of the tailings, containing and controlling runoff and seepage from the tailings is one of the more important functions of these earthworks’ structures. of the brine and tailings ponds, a lot of engineering science and construction know-how goes into the building of these structures to achieve the desired operating outcomes. The till materials found on most potash mine sites is the ideal material for achieving these outcomes. However, as related in the opening paragraph, Mother Nature did not necessarily place the till in an ideal state for constructing a brine pond or other structures for that matter, and that is where construction experience and good old knowhow comes into the equation. While design engineers will specify the construction materials they want used in the construction of a brine pond, it is up to the contractor to ensure that these materials are found and incorporated into the earthworks. It takes a well-trained eye to pick out silt seams and pockets within a unit of till to ensure that these are directed to a waste site and not incorporated into a fill area. Similarly, that well-trained eye needs to identify tills that contain too high a percentage of gravel, silt and\or clay
which could cause havoc with fill placement operations or fill that is too wet or dry to get the density (compaction) specified by the engineer. In the former case, the material needs to be dried in the borrow area before being hauled for placement, and in the latter case, additional water has to be incorporated into material in the fill prior to being compacted.
Like a conductor conducting an orchestra, the earthworks supervisor overseeing the fill operations must be highly organized and on top of their A game. It might seem like an easy task, dig the dirt up here and place it over there, but there are many variables at play to make fill placement operations work seamlessly. First the fleet of equipment constructing the brine pond must be sized correctly to match the construction schedule. How much earth fill must be moved daily to ensure the construction schedule and the owners timelines are met, keeping in mind that some time will be lost in the schedule due to weather-related events; 5,000 cubic metres, 10,000 cubic metres/day? Next, the earth-hauling equipment must be matched correctly to the earth-loading equipment based on the daily targeted fill volume and haul distance so as one truck is leaving filled, the next truck is just arriving. After the fill is hauled to the specified fill area and dumped, sufficient dozer power must be in place to spread the fill to the lift thicknesses specified by the engineer and subsequently packed with the correct type and weight of packers. And if the fill is too dry, it must be sprayed with a water truck and the water incorporated into the material by a grader working the material from one side of the fill and back before being compacted. All this bearing in mind that this is an operation in series and if the series is broken, productivity comes to a halt. Good planning, good maintenance, and good people are the hallmarks of ensuring a continuous, productive operation.
So next time you observe a contractor digging dirt here and placing it there, you know there is a little more to it. To be a successful and competent contractor in the earthworks business takes a great amount of knowledge, organization, and care to do it productively and safely. l
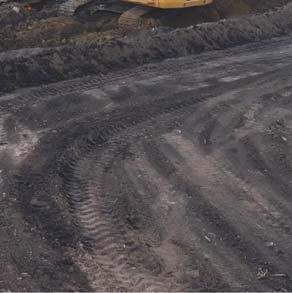



KELLY PANTELUK CONSTRUCTION LTD. KELLY PANTELUK CONSTRUCTION LTD.
Building Today for Tomorrow
Highways | Interchanges | Roads | Mining | Tailings | Rail | Site Grading | Water Control Structures
www.kpcldirtmovers.com


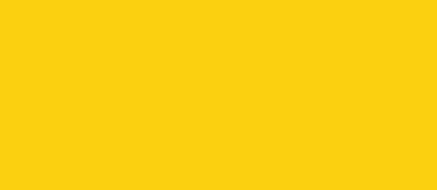

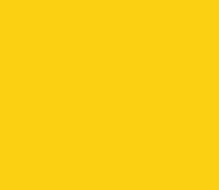