
4 minute read
Entrer dans l’ère de l’industrie minière 4.0
Jeff DeNigris, Division des solutions d’automatisation des processus, Malvern Panalytical
Àl’instar de nombreuses industries, les sociétés d’extraction minière ont recours aux solutions d’analyse et d’automatisation en ligne qui associent des technologies scientifiques éprouvées en laboratoire (telles que la diffraction au laser) aux procédés de production (tels que le fraisage/le broyage et la classification), et ce, afin de mieux comprendre les variables qui affectent le produit final. Au fil du temps, la qualité, la composition et l’aptitude au broyage des matériaux extraits changent souvent, ce qui a un impact sur la taille des particules. À cet égard, il est nécessaire d’avoir un aperçu de ces variables en temps réel pour optimiser les performances de ces procédés.
Dans l’exploitation minière, les broyeurs à rouleaux verticaux (BRV) sont souvent utilisés pour réduire la taille des particules du minerai. Cependant, ils sont coûteux à installer et à exploiter et peuvent produire des centaines de tonnes de produit broyé à l’heure. De plus, ils ne fournissent aucune donnée sur leur performance en termes de matériau produit. Par conséquent, les BRV utilisent des contrôles avancés pour aider à maintenir les niveaux de performance du broyage et les caractéristiques du produit à la sortie, tout en s’adaptant aux changements des matières premières. Des capteurs logiciels sont utilisés avec des schémas de contrôle à variables multiples pour prédire ce qu’un capteur direct pourrait indiquer, et ce, à partir d’estimations issues de données d’analyses de laboratoire hors ligne. Des caractéristiques telles que la minéralogie, la morphologie, la distribution de la taille des particules et la couleur peuvent tous être des facteurs à prendre en compte lors de l’évaluation des performances d’un circuit de broyage et, à cet égard, la possibilité de surveiller chacune de ces caractéristiques en fonction du temps s’est avérée très utile. Tel qu’indiqué dans un article de la société Vulcan Materials1, la capacité d’amélioration du procédé de broyage a été rehaussée de façon spectaculaire lorsqu’on est passé d’un capteur logiciel à un analyseur de la taille des particules
Figure 1 – Données de performance d’un BRV (Vulcan Materials). / Figure 1 - VRM performance data from Vulcan Materials. en ligne. Le rendement, la consommation d’énergie et les écarts-types ont tous été considérablement améliorés (figure 1).
Dans le secteur minier, il existe trois catégories principales de procédés qui peuvent nécessiter des analyses en ligne pour garantir leur optimisation : le broyage à sec, le broyage par voie humide (boue) et les procédés de séparation/filtration. Chacune de ces étapes implique une réduction de la taille des particules et des techniques telles que la diffraction au laser peuvent être mises en œuvre en ligne pour recueillir des données pertinentes en temps réel, et ce, afin d’obtenir un meilleur contrôle et une meilleure modélisation de la prédiction. Qu’elle soit humide ou sèche, la technique est la même : déterminer la solution d’échantillonnage, préparer l’échantillon pour la mesure, mesurer et exporter les données en temps réel sous forme d’information exploitable. Il s’agit ensuite de mettre en place une boucle de rétroaction pour maintenir le procédé à son niveau ou encore l’optimiser (figure 2).
L’imagerie en cours d’opération peut également être utilisée dans l’exploitation minière avec surveillance du minerai concassé (figure 3) ou in situ à partir d’hydrocyclones/d’hydroclasseurs pour observer les résultats du processus de séparation. Il est possible d’identifier divers composants en suspension dans la boue, tels que des cristaux, des particules amorphes, des solides sphériques, des gouttelettes et/ou des bulles (figure 4). Un appareil d’imagerie en cours d’opération, telle une sonde SOPAT (technologie d’analyse intelligente de particules en ligne), utilise des algorithmes de réseaux neuronaux avancés pour transformer ces images en données très utiles telles que les distributions granulométriques fondées sur le volume et le nombre, la circularité, le rapport d’aspect et la concentration.
Figure 2 - Boucle de rétroaction de dimensionnement des particules. / Figure 2 - Particle Sizing Feedback Loop.

Plusieurs types de particules peuvent être analysés à partir de la même image et les boues à forte concentration peuvent être surveillées directement sans dilution ni prélèvement d’échantillons. Ces caractéristiques peuvent fournir un aperçu détaillé du processus en temps quasi réel et donner aux opérateurs la possibilité d’appliquer des techniques d’optimisation du processus, en évitant les temps d’arrêt coûteux, le recyclage, le retraitement et/ ou le reconditionnement et, du fait, en améliorant le rendement avec des données quantitatives.
En résumé, la tendance actuelle vers une véritable industrie minière 4.0 nécessite des données, et beaucoup de données. Avec l’avancement de communications plus rapides, plus fiables et plus sécurisées, les capacités de contrôle du procédé vont nécessiter un plus grand volume de données. Les analyseurs scientifiques, la puissance de calcul avancée et les communications à haut débit rendent désormais fiables les systèmes en temps réel. Ce paradigme doit clairement étendre l’utilisation des analyseurs en ligne pour garantir la disponibilité et la robustesse de l’information exploitable, ce qui permettra une plus grande efficacité des performances afin de renforcer l’expertise de fabrication des entreprises et fournir non seulement des exploitations minières de premier ordre, mais aussi de calibre international.
Figure 3 - Imagerie SOPAT de minerai. / Figure 3 - SOPAT imaging of mining ore.
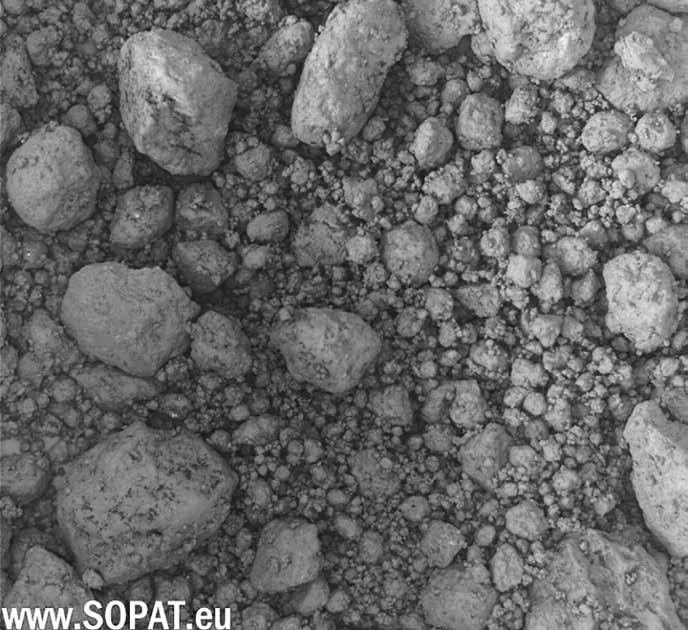
Figure 4 - Imagerie SOPAT de l’écoulement d’un hydrocyclone. / Figure 4 - SOPAT Imaging of Hydrocyclone Flow. 1. DeNigris, Jeff, Murphy, J., Levonian, D., et. al., (juillet 2009) « Reducing Costs », World Cement. Également disponible en ligne : https://www.worldcement.com/magazine/world-cement/july-2009/ u
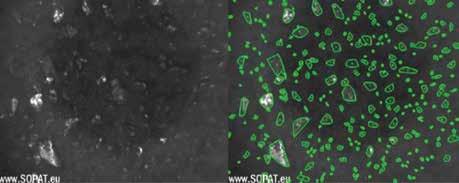