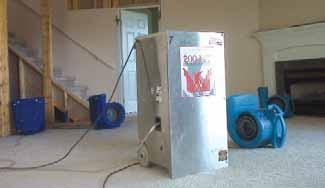
4 minute read
The Science of Drying
BY TROY FEHR
Drying a structure is a science that has been developed over a number of years, but it’s only been perfected in the last ten or so years. The Institute of Inspection Cleaning and Restoration Certification (IICRC) has been promoting this science, and has accordingly developed a graduated training and certifying body that teaches this exact science to businesses and professional restorers around the globe. Approved schools teach advanced drying designations by using prop houses in their compounds and flooding them similar to real loss situations; the flooded prop houses are then dried by the students being trained (this information is further published by the IICRC in the S-500 standards).
The science of drying structures takes years of training, educating, and hands-on work experience to fully comprehend and understand the knowledge to its full potential; however, once the professional restorer absorbs the knowledge, he or she then becomes an asset in any loss, large or small. The restorer will be able to attend a loss and after a short investigation, will be able to determine the appropriate drying solution, including equipment requirements and possible removals.
A thorough understanding of the science of drying is essential to dry the structure within the critical time period of 72 hours. Drying within a 72-hour period will ensure microbial growth is averted, and further ensure people staying within the structure remain healthy by avoiding any exposure to mould. Mould can cause a variety of health issues for all people; however children, the elderly, and individuals with compromised immune systems are at greater risk. Due to the potential health issues, a trained professional restorer should attend all losses.
When we as professional restorers attend a loss, we first take humidity and temperature readings. These readings are used to calculate specific humidity or GPP (grains of moisture per pound of air). The GPP is used as a starting point for our dry down.
Losses are categorized in three ways. Category 1 is clean water; category 2 is grey water; and category 3 is black water. If this is a category 1 loss, more emphasis is put into drying the structure and less on removing hygroscopic materials. Category 2 or 3 losses will require removing some or all hygroscopic materials. Further, category 3 losses should all be tested using a swab tester or hygienic sampler, which measures the amount of present bacteria to ensure sanitization is completed efficiently.
LOSSES ARE FURTHER PLACED INTO 4 CLASSES:
Class 1: Slow rate of evaporation - minimum moisture. Class 2: Fast rate of evaporation - some wet flooring and walls wet less than 24 inches. Class 3: The fastest rate of evaporation - ceiling, walls and insulation wet. Class 4: Specialty dry items - hardwood floors, stone, and plaster.
Regardless of the type of loss, mitigation work such as




extraction, flushing and/or removals must be commenced. The next crucial step is setting up the equipment. The structure is measured to find the exact cubic footage. Using the cubic footage, the category and class of loss, we now have a scientific formula that will calculate for us how many pints of water must be removed per day to ensure the structure is dry within 72 hours. Once this is calculated, dehumidification becomes simple, as each machine has a rating for how many pints of water a day it will remove (cfm if using desiccant dehumidifiers).
Evaporation is also essential. The number of blowers must also be calculated and correctly placed to ensure the balance is kept between evaporation and dehumidification.
Manufacturers of Fire Alarms, GPS Clocks, Security, Card Access & CCTV Systems
John Smith Account Executive Fire Alarm Division Direct: 604.515.8284 Ext. 128 josmith@simplexgrinnell.com www.simplexgrinnel.com SimplexGrinnell A Division of Tyco International of Canada Ltd. 1485 Lindsey Place Delta, B.C. V3M 6V1 Phone: 604.515.8872 SimplexGrinnell Fax: 604.519.1477 1.800.492.4063
Monitoring the daily progress of the structure is another important factor in the successfully drying of the structure. Daily temperature and humidity readings are vital, as these tell us how the structure is drying and confirm that the drying solution is working efficiently. To monitor the drying progress, the restorer uses a variety of sensors, such as penetrating and non-penetrating moisture meters. The meters tell us the moisture content of hygroscopic materials. Flir and Fluke thermal imaging cameras, hygrometers, and remote sensor hygrometers are also used. Remote sensor hygrometers can be left on a loss site by the restorer; viewing the readings live and documented from our office, we can then calculate what is required before the restorer even arrives on site to manipulate the equipment during the daily monitor.
After the critical dry time, the restorer performs a thorough inspection of the structure using their meters and a final specific humidity reading or GPP is taken. This inevitably will be lower than our starting point, and will further provide proof that the structure is dry. Reconstruction can now commence.
If you would like more information about Stutters Disaster Kleenup, or would like to contact us, please go to www.stutters.com.
About the Author: Troy Fehr is a IICRC-certified Master Water Restorer, a Master Fire and Smoke Restorer, and a Master Textile Cleaner. ❏
To view more products or order samples, visit us online at www.interfaceflor.ca. Call us to make your next purchase at 1.800.267.2149, ext. 2128. Carpet Shown: Entropy® - 7204 Metamorphosis; Cubic Colours™ - 6393 Height, 7262 Orange.
© 2008 InterfaceFLOR Canada, Inc. Mission Zero, Cool Carpet and the Mission Zero mark are trademarks of Interface, Inc.
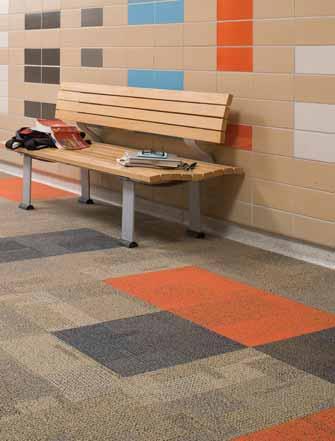