
4 minute read
Moisture: A natural disaster
BY DARRYL WILSON, MAPEI TECHNICAL SERVICES
View of moisture issue with wood flooring.
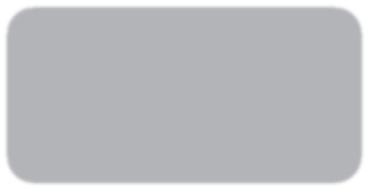

View of moisture underneath carpet moisture.

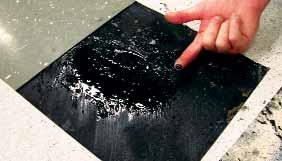
Moisture issue underneath tile.


Vinyl sheet glue re-emulsification through seam. There are many types of beautiful and stylish floors in schools – marble foyers in school entrances, ceramic tile in laboratories, coloured and crafted sheet vinyl in hallways and class rooms, hardwood floors in gymnasiums, carpet in administrative offices, and rubber flooring in areas surrounding aquatic centres. The average cost for installed flooring runs around $4 to $15/square foot for carpeting; $10 to $14/square foot for hardwood; $19 to 60/square foot for marble; $7 to $14/square foot for tile and $3 to $7/square foot for vinyl (according to www.costhelper.com). When work is complete, the flooring represents a significant investment by school facilities’ management. In certain circumstances, the concrete subfloor can compromise this investment, causing costly defects in the floor covering.
If the water-to-cement ratio in the concrete mix is too high, or if the concrete slab does not cure properly, it can become overly porous. As a result, the tiny channels within the concrete may remain permanently connected, increasing the permeability of the concrete slab and the likelihood of moisture movement up through the slab to the flooring. In the absence of a vapour barrier/retarder, natural moisture such as ground water can become a problem. Artificial sources of moisture like irrigation problems, incorrect exterior grading or broken plumbing can also lead to problems with moisture control. The result can be serious failures in the flooring.
In wood floors, moisture could lead to wood crowning or cupping, making that smooth gym floor more like an obstacle course. Carpet could start to buckle and smell due to excess moisture, mould and mildew. Moisture could cause efflorescence of cement-based grout in tile joints, leaving unattractive salt deposits in the grout lines separating the tiles. Stone is known for being sensitive to moisture and could sometimes change colours and/or curl in the presence of too much moisture. When sheet vinyl and other resilients are installed in conditions of excess moisture, adhesives will emulsify, turning gooey and losing their bonding strength. These conditions occur because moisture vapour is governed by the laws of physics.
Water vapour travels from one area to another whenever a vapour pressure difference exists. In a controlled climate (HVAC), the temperature in a room is usually 70 to 80 degrees Fahrenheit, and the relative humidity is 30 to 50 per cent. Under these conditions, the air above the water-laden slab wants to hold more moisture and satisfies itself by pulling moisture from the slab. The warmer the room is, the more water is absorbed. Calcium chloride testing, which is
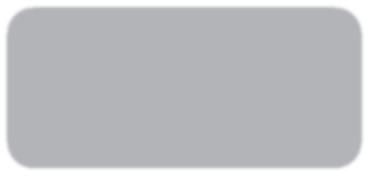

used to measure moisture vapour emission rates, indicates that acceptable MVER should be in the range of three pounds (1.36 kg) of moisture vapour per 1,000 square feet (92.9 m2 ) of space within a 24-hour period. Moisture issues beneath the concrete slab can cause significant increases in the MVER – sometimes as high as 20 pounds per 1,000 square feet, per 24 hours.
Surface preparation can be critically important to the MVER effect on the floor covering, whether it is tile, stone, carpet, wood or resilient. One of the essential components of surface preparation is the specification of the right moisture barrier between the concrete sub-floor and the floor covering. MAPEI supplies two types of moisture remediation, depending on a project’s needs:
Planiseal™ Easy incorporates an acrylic polymer, which can be used on fresh, green concrete that is undergoing standard moisture dissipation. It has been specifically designed to treat interior concrete slabs from 14 days to one year old that exhibit MVER up to eight pounds or 90 per cent relative humidity and reduce transmission rates to three pounds or less. This product can be specified to significantly reduce the time from installation of the concrete sub-floor to installation of the floor covering under ordinary circumstances.
Planiseal™ EMB is a single-coat 100-per-cent-solids epoxy moisture barrier system for concrete slabs that exhibit MVER up
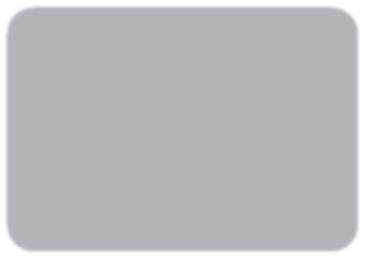
Manufacturers of Fire Alarms, GPS Clocks, Security, Card Access & CCTV Systems
John Smith Account Executive Fire Alarm Division Direct: 604.515.8284 Ext. 128 josmith@simplexgrinnell.com www.simplexgrinnel.com SimplexGrinnell A Division of Tyco International of Canada Ltd. 1485 Lindsey Place Delta, B.C. V3M 6V1 Phone: 604.515.8872 SimplexGrinnell Fax: 604.519.1477 1.800.492.4063 EMB application at Frank Hurt Secondary School in Surrey, B.C.

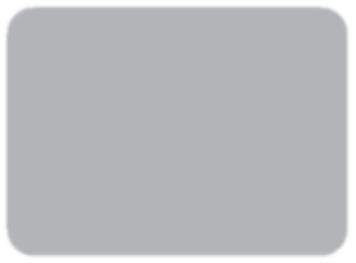
to 20 pounds and reduces transmission rates to less than three pounds. Planiseal™ EMB's high-performance formulation penetrates into the concrete substrate while creating a solid film layer on the surface for the ultimate in moisture transmission reduction. Because of its reduced-odour formula, specifiers can choose this solution when a project involves a concrete subfloor with a serious moisture problem in an occupied building.
Safeguarding installations with the proper moisture barriers will result in sustainable, beautiful flooring that will see students through all their years of schooling.
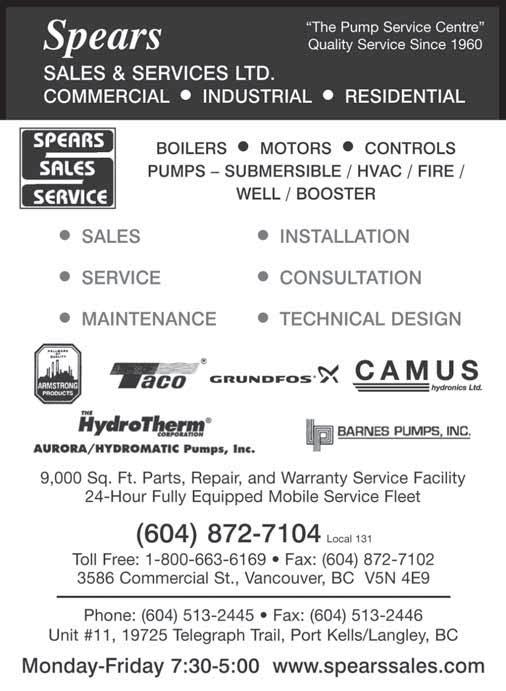