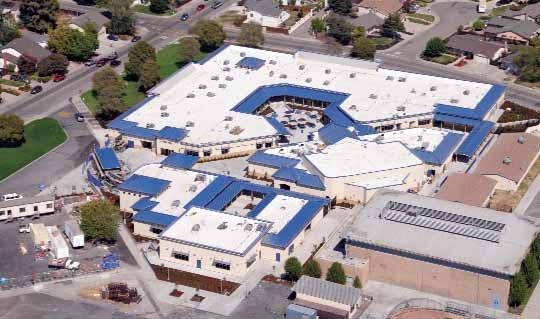
9 minute read
Four steps to successful roofing projects
BY BRIAN LAMBERT
Schools require unique, rugged roofing solutions that are easy to maintain and provide long-term leak-free solutions.
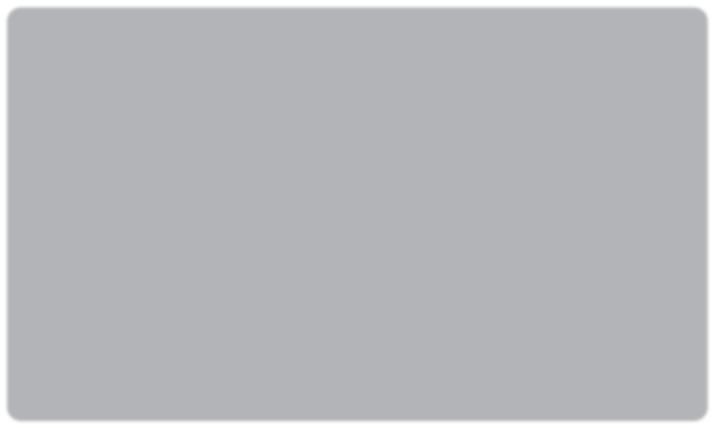
Facility managers, school administrators, and design professionals commonly report roofing problems as one of their most pressing needs and frequently cited headaches.1
Whether you have a handful of facilities or 22 campuses to care for, it often seems as though there are one or more roofs in need of repair or replacement each year. For school facility managers and hospital administrators, longevity, durability, rugged performance, and ease of repair are vital to roof design. To help secure the high level of performance that schools and hospitals, it is helpful to understand four critical components: • Proper analysis, evaluation, and design • Quality products • Proper application and regular inspection • Corrective and preventive maintenance
Proper Analysis, Evaluation, and Design
Understanding what you have and why you are having problems is critical to all projects – especially roofing projects. Due to downsizing and budget cuts, most facility managers no longer have an experienced roofing expert on staff. Therefore it is important to find someone you trust and respect to help manage your roofing program: an architect, your local roofing contractor, or a technically trained manufacturer’s representative.
Qualified roofing professionals can assist you by: • Properly identifying roofing problems • Providing yearly budgets estimates • Prioritizing roof problems by degree of severity • Identifying which roofs can be restored and which ones need to be replaced • Supporting the design team responsible for developing technical specifications and details that are customized to your specific roof-top problems
Roofs will rarely leak in the field of the roof. Therefore, it is important to spend your time and effort focused on flashings. Address these common problem areas first. In assessing the condition of roofs or searching for existing roof leaks, start at
drains, curbs, vents, wall flashings, and edge metal. Flashings and penetrations typically account for nearly 80 per cent of all reported roof leaks.
Another fundamental component of good roof design is positive slope. Providing even ¼:12 slope will help roof systems last longer. Although all low-slope roofs are designed to be waterproof, shedding the water off the roof and into internal drains or gutters will help extend the service life of your roof. There is good reason why many roofing manufacturers nullify their warranties under ponding conditions. Ponding water negatively affects low-slope roofs by: • Adding unneeded weight to the structure, which could cause deck deflection or structural roof collapse (a 10 foot by 10 foot area with just three inches of water adds approximately 1,500 pounds to your roof). • Promoting the growth of microorganisms and vegetation whose roots can penetrate the roof and extend into the insulation. • Accelerating deterioration by adding head pressure to any imperfection in the roof that can become an entry source for moisture. • Eroding the roof surface in colder climates in winter, when ponding water turns to ice, increasing the coefficient of thermal expansion.
Additionally, flashing details and providing slope is where roofing experts and design professionals earn their money when designing new roof systems. Despite the fact that technology has made it tempting to simply pull generic specifications and typical details off a manufacturer’s website, never accept boiler plate specifications and details for your roofing projects. Each roof is different and deserves specific tailored specifications. Hospitals typically have a tremendous amount of roof penetrations and resulting foot traffic, and schools deal with vandalism that is uncommon to other applications. If the design professional does not provide customized specifications and job-specific details, then it is left to the roofing contractor to figure it out on the job. Many contractors are creative and experienced, but many are not. The design of the roof should be done by the design professional, and installed by the contractor.
Quality Products
Commercial roofing products have evolved substantially over the last two decades. As roofing technology advances, it is sometimes difficult for facility managers to keep track of the all the new products being developed.
Traditional BUR — It was not that long ago that the commercial roofing market was dominated by built-up roofs (BUR) with gravel surfaces, and the only question was whether to choose an asphalt or coal tar BUR. Built-up roofs have had a long history of successful performance – primarily because of the redundancy of three, four, or five layers of alternating bitumen and reinforcing fabric. With BUR, alternating layers are literally “built up” on the roof. Although their application requires a skilled labourer, the redundancy in the application does not require perfection. Multiple plies of protection are key to the long-term success of built-up roofs.
Modified Bitumen BUR — As raw materials and technologies continued to improve, the commercial roofing industry began to mix asphalt with polymer modifiers to increase roof system longevity. Rather than radically reinventing the wheel, manufacturers took the proven performance of built-up roofs, added a little science, and developed the modified bitumen roof system. Polymer modifiers such as SBS and APP are commonly used today. Factory fabrication of modified bitumen sheets allows for better quality control, thus ensuring uniform thickness and physical properties. Additionally, modified bitumen systems add a tough reinforcing scrim in place of the traditional felts used in BUR systems. The added strength from the fiberglass, polyester, or fiberglass/polyester scrim significantly increases a roof’s tensile performance. Finally, lighter-weight surfacing options, such as minerals and energy-efficient cool roof surfacings, are now frequently used instead of gravel.
Modified bitumen roof systems have over 30 years of proven performance. Today, manufacturers are raising system
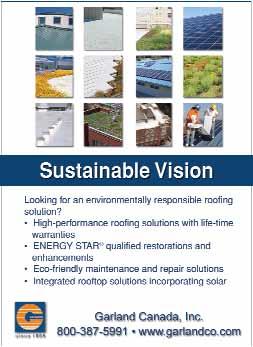

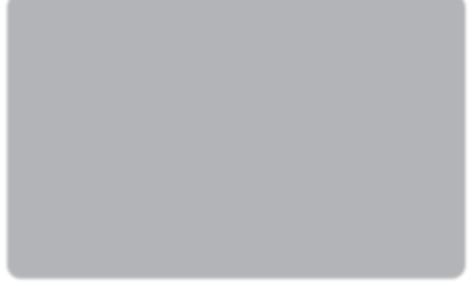
Multi-ply modified bitumen roof system with a lightweight cool roof surfacing option.

Planned preventive maintenance will extend most properly designed roofs well beyond the manufacturers’ warranty.
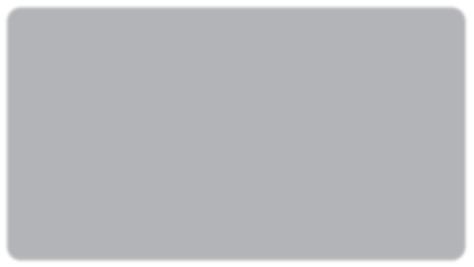
performance to a new level with technologies that maintain or improve tensile strength, UV resistance, and elasticity while incorporating next-generation materials, such as bio-based raw materials or recycled content, providing the building owner with better, longer-lasting roof systems while minimizing environmental impact.
Single Ply — Single-ply roofs have continued to gain market share over the last 30 years – first with EPDM and PVC, and more recently with TPO technologies. Single-ply roofs are typically 45 to 60 mils thick, lightweight, and often light-coloured. Due to their low initial cost and easy installation pro cess, single-ply roofs are commonly specified on big box retail stores and new construction projects. However, as their name states, there is only a single ply of waterproofing protection. When seamed and installed perfectly, they have performed well. But since we live in an imperfect world, the reality has been that installation problems, foot traffic, and rooftop maintenance too frequently have created problems with single-ply roofs.
With the newer TPO membranes, some are questioning its ability to withstand conditions in the high-heat regions of the U.S. and in conditions where reflections from windows, architectural metal, or PV systems create extreme heat exposure on the membrane. According to Mark Graham, the National Roofing Contractors Association’s associate executive director of technical services, “The concerns raised regarding TPO membrane performance need to be addressed.” 2
Ironically, schools and healthcare institutions, which are frequently strapped for funding and may therefore wish to take advantage of the lower initial costs of single-ply membranes, may be reluctant to do so given the extreme levels of performance their applications typically require.
Proper Application and Regular Inspections
After your project has been analyzed by qualified roofing professionals, tailoured specifications created, and quality materials selected, it is now important to select an experienced contractor to install the project. In public bidding scenarios, it may not be possible to select the qualified and proven contractor you have successfully used in the past. However, by working with a design professional, language can be included in your customized specifications to help ensure that only qualified contactors are permitted to bid on your project.
The National Roofing Contractors Association suggests prequalifying contractors for upcoming roofing projects. Although this may take some time, a qualified professional roofing contractor is critical to the success of roofing projects. Here are a few items to investigate: • Determine if the contractor has a permanent place of business • Find out how long has the contractor been in business under their current name and ownership
• Review their proof of insurance, specifically their workers compensation and general liability insurance • Check the contractor’s references of completed projects
Even with the best contractor, someone needs to provide regular inspections. Are the materials being installed properly? Are the specifications and details being followed? Are materials stored properly? Is trash being removed from the site or allowed to blow around the grounds? Experienced facility managers may elect to perform this critical task themselves, or use a construction manager to perform this task. Many large roofing manufacturers also include this service as part of their package.
Corrective and Preventive Maintenance
One of the most frequently forgotten parts of roofing projects is corrective and preventive maintenance. Nothing on the exterior of a building will last forever – roofs included. A yearly preventive maintenance program will extend the service life well beyond the warranty period for most well-designed roof systems. A comprehensive preventive maintenance program should include the following: • Inspect roofs for clogged drains, debris, and fasteners left on the roof • Examine edge details, flashings, and penetrations for obvious problems • Periodically recoat flashings with a reflective coating • Trim overhanging tree branches and vegetation • Check caulking and sealants on coping stones and flashings
A trained roofing professional should walk each roof twice a year to inspect the roof for deficiencies before leaks begin to occur. Typically, this inspection should be done in the spring and fall.
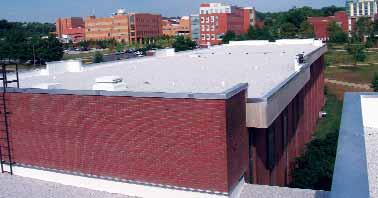

It often seems as though there are one or more roofs in need of repair or replacement each year.
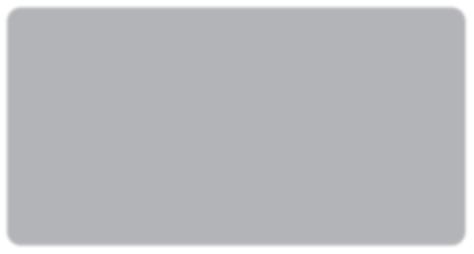

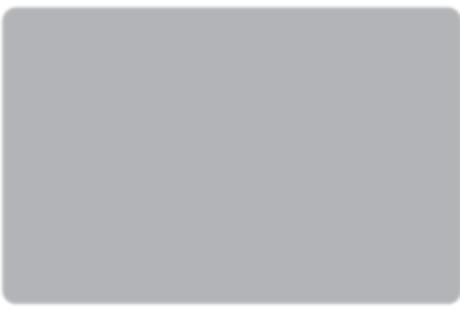
Attention to detail during the design and construction of roofing projects will lead to better projects and fewer problems.
Conclusion
Facility managers of healthcare and educational institutions must multi-task and juggle projects involving a variety of operating systems, from HVAC and plumbing to electrical and roofing. There is no fundamental reason why roofing projects should be the excruciating experiences they too often are. Whether you have the labour or expertise in-house, or use a qualified roofing professional to assist you, following the four steps outlined in this article will ensure that your roofs perform as specified. About the Author: Brian Lambert is director of products and systems for The Garland Company, Inc. Lambert has been active in industry initiatives since 1993, is frequently a guest speaker at architectural and building maintenance seminars, and has written many articles on roof system performance.
FOOTNOTES:
1 “Architect Claims go through the Roof”, Tom Owens, DPIC Companies, as posted by Benchmark, Inc., 2000
2 Professional Roofing – “Issues with TPO Membranes,” August, 2010