SUSTAINABILITY REPORT 2022
SUSTAINABILITY REPORT 2022

INTRODUCTION
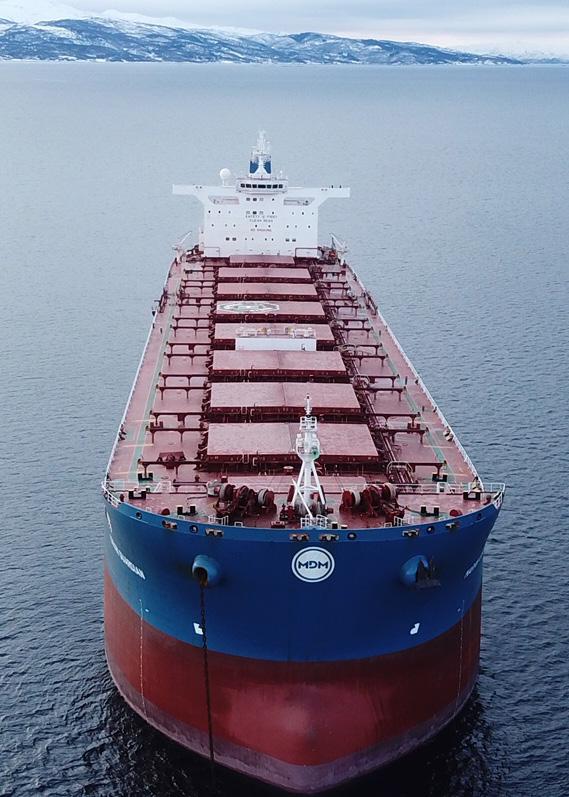
SUSTAINABILITY REPORT 2022
2022 was yet another challenging and unpredictable year, from the energy crisis stemming from the war in Ukraine to the lingering impact of the COVID-19 pandemic. Communities and businesses across the world faced a series of renewed obstacles. Despite the challenges, however, I am pleased to note our Group’s resilience and continued excellent performance. My sincere gratitude goes out to all our employees, onboard and ashore, for their tireless efforts in delivering the exceptional service that our customers have come to expect.
Demonstrating our commitment to transparent reporting, we are pleased to share our Sustainability Report for the third consecutive year, documenting our progress towards achieving our goals and evolving our business practices sustainably and responsibly. The report showcases our recent initiatives and gives our stakeholders insight into how we embed environmental, social and governance factors throughout our business processes and working environment.
Although decarbonisation remains a critical challenge for the maritime industry, we cannot ignore the urgent need for climate action, which has driven our ambition to work towards achieving a net-zero goal. In July 2023 the International Maritime Organization has taken a bold step to accelerate the decarbonisation process by formally adopting the ambition to reach net-zero GHG emissions from international shipping by or around 2050. Our focus is to keep our fleet
well positioned for this ongoing energy transition while working closely with our stakeholders to select the most suitable net-zero strategy for ASGL.
With regard to zero-carbon or low carbon based fuel options, we are currently evaluating all alternative options to determine their suitability and assess the potential supply volumes that will be available over time in conjunction with relevant regulatory developments. We are also getting involved in testing programs, for example, in 2022, we participated in a pilot project during which our 2004-built VLCC, Elizabeth I.A, successfully operated using biofuel.
As we continue to expand and renew our fleet, our most recent investments include state-ofthe-art, environmentally friendly dual-fuel LNG tankers and dry cargo ships. Our new vessels will lead the way in energy efficiency, as they will be equipped with the latest-generation dual-fuel main engines, a shaft generator, advanced anti-fouling technology and energy-saving devices. We are proud that our VLCCs are the most environmentally friendly vessels in their segment in the world today.
We constantly monitor our energy efficiency performance and adopt new innovative solutions to improve our operating and maintenance practices. At the same time, we are working with shipyards to explore alternative ship designs and technologies to meet emerging industry requirements and decarbonisation goals. As a Group, we are tech-
“ Our sustainability culture is deeply rooted in our core values and embraced by all our people.
nology- and fuel-agnostic, and aim to be amongst the early adopters of new technologies once they become commercially viable and safe to use.
The Group also actively participates in local community initiatives to increase sustainability awareness. It was heartening to see many of our colleagues and their families taking part in a recent beach clean-up in Athens which not only revealed a different perspective of our beloved Greek beaches but also prompted participants to reflect on the importance of taking care of our planet.
Alongside our firm commitment to environmental and social responsibility, creating a diverse, inclusive and equitable workplace has long been a cornerstone of the Group’s values. In 2022, we conducted an engagement survey for both office and shipboard employees. The inputs and perspectives gained from the responses will contribute directly to our ongoing efforts towards ensuring a healthy and rewarding work environment for our current employees and a more attractive proposition for new talent.
Since keeping our people safe has and always will be our number one priority, our responsibility to employees is even more critical in challenging situations. In 2022, we took extraordinary measures to support staff affected by the Russia-Ukraine war. We provided financial support to Ukrainian colleagues who were unable to join vessels and ensured the safe repatriation of Greek and Filipino colleagues from two vessels at the Ukrainian
port of Yuzhny. In September, we secured the departure of our vessels Maran Astronomer and Maran Excellence from the Black Sea, after a safe corridor was established in the framework of a UN-mediated grain deal.
Although 2022 presented numerous challenges, our people’s resilience and perseverance allowed us to excel and maintain a leading and reputable position in our industry and community. Sustainability, equality and responsible business are core values that lie at the heart of our Group’s identity and are fully embraced by our people. As an employer to thousands on land and at sea, and a business with a positive presence in communities across the world, ensuring a better future for our planet and our children is not just a duty, but a privilege.
We know that there is a long journey ahead to achieve the world’s social and climate goals, and we remain fully committed to every step aimed at advancing environmental responsibility and fostering social equity not only within our workplace but also across our supply chain, which will play a key role in our sustainability journey ahead.
Maria Angelicoussis Chief Executive Officer Angelicoussis Group
Angelicoussis Group aims to be a positive contributor to society, a supportive employer, and to ensure the ethical use of resources. Creating shared value and fostering conservation of natural resources have always been at the heart of our corporate strategy. Accordingly, we fully recognise our responsibility towards the global community and the environment. As part of our commitment to sustainability, we hold ourselves to high standards of comprehensive and transparent sustainability reporting.
This is our third sustainability report and covers our disclosures on material ESG topics, related impacts and performance in the calendar year ending 31 December 2022. The report provides information on our operations at our headquarters in Athens and our offices in Singapore, Manila, London and our site office in Okpo, as well as on the vessels owned and operated by our three management companies, Maran Tankers Management, Maran Dry Management and Maran Gas Maritime.
Our Group constantly strives for sustainability excellence and each year we launch new initiatives focused on ESG issues. Through this report, we aspire to share our sustainability vision and performance with our key stakeholder groups, including investors, employees, clients, supply chain partners and others.
Global Reporting Initiative (GRI)
The report has been prepared in accordance with GRI Standards 2021, which are widely seen as the global best practice for sustainability reporting.
Sustainability Accounting Standards Board (SASB)
We have also applied sustainability reporting standards developed by SASB to guide our disclosures on sector-specific ESG issues.
United Nations Sustainable Development Goals (UN SDGs)
The report also links our sustainability disclosures to the UN’s SDGs.
The report covers the financial year from 1 Jan 2022 to 31 Dec 2022
This Sustainability Report was published in October 2023 and is available online at www.angelicoussisgroup.com/sustainability
sustainability@angelicoussisgroup.com
With more than 76 years’ experience in the maritime industry, Angelicoussis Group has embraced the evolution of shipping markets and technology over the last few decades to continue innovating and building on our proud history.
1947
Angelicoussis Group is founded by Antonis I. Angelicoussis
2021
Maria Angelicoussis, who joined the Group in 2008, becomes CEO
1989
John A. Angelicoussis who joined the Group in 1973, becomes CEO
Maran Tankers Management Inc. (MTM) is established as Kristen Navigation Inc.
Friendly Maritime Services Inc (FMS) is established in Manila
Delphic Maritime Training Centre, the first in-house training centre run by a major shipping company in Greece, is established
Maran UK Ltd, is established The Group moves into new, state-of-the-art headquarters in Athens
Maran Dry Management Inc. (MDM) is established as Anangel Maritime Services Inc.
Maran Gas Maritime Inc. (MGM) is founded
Maran Asia is incorporated in Singapore
Maran Ship Supplies Pte Ltd (MSS) is established in Singapore
First cargo vessel, MV Astypalea (500 DWT), acquired
Acquisition of first Liberty-type vessel, Enosis
Three more Liberty-type vessels purchased in 1961
42 new buildings ordered and delivered by IHI Japan, consisting of Freedom-, Fortune-, Friendship- and Future-type bulk carriers
First ULCCs, T/T Kirsten and T/T Karoline, acquired, followed in 1993 by three VLCCs, Astro Alpha, Astro Beta and Astro Gamma
First newbuilding VLCC, MV Maria A. Angelicoussis, delivered by Daewoo
Four Dual Fuel VLCCs are ordered at Samsung Heavy Industries
First ocean-going cargo vessel, Adelfotis (3,745 DWT), acquired
First newbuilding (bulk carrier) MV Afovos was ordered. Delivered in 1968
John A. Angelicoussis orders the first four capesize bulk carriers at Hyundai Heavy Industries Co. Ltd., the largest vessels ever ordered by a Greek shipowner at the time
First double hull Aframax tanker, Astro Sirius, ordered. This was also the first newbuilding order placed with DSME in Korea. Delivery in 1996
First LNG carrier, Maran Gas Asclepius, ordered. Delivery in 2005
Angelicoussis Group is a dynamic multinational group comprising several privately owned entities. We provide best-in-class ship management services, including commercial, technical, operational and crew management. We operate a modern fleet consisting of dry bulk vessels, tankers, and LNG carriers. As a well-recognised global brand in the shipping sector, we are a trusted partner for several leading charterers across the world.
Our fleet serves the oil, gas and dry cargo markets in a safe, efficient and environmentally sustainable manner. Our customers include leading cargo owners, charterers and terminals.
The Group’s executive office is located in Athens, Greece, with operational offices in Singapore, Manila and London, and a site office in Okpo. Operations span multiple countries including Greece, Singapore, Philippines, the UK and South Korea.
46
2
44
40
12 ships under management newbuildings ships under management newbuildings ships under management newbuildings
4
53,377,847
59,445,809
66,141,406 MT Cargo transported MT Cargo transported CBM transported
Maran Dry Management Inc. (MDM) was established in 2001 as a unit of Angelicoussis Group to undertake the commercial, technical and operational management of dry bulk vessels
Maran Tankers Management Inc. (MTM) was established in 1992 to manage the Group’s oil tankers
Maran Gas Maritime Inc. (MGM) was set up in 2003 to manage the Group’s LNG transport operations
VESSELS IN OPERATION
130 18
FLEET CAPACITY (DWT)
VESSELS UNDER CONSTRUCTION 8,272,259 11,463,171 3,665,694 6,668,124
FLEET CAPACITY (CBM)
To be a leader in seaborne solutions.
To provide world-class shipping services to our clients across the LNG, tanker and dry bulk markets, in a safe, reliable and sustainable manner, whilst embracing the energy transition through innovative solutions for zero-carbon vessels.
Our core values inspire us to execute all our operations with excellence and have enabled us to build a culture of resilience and continuous improvement.
We have integrity as the foundation for our business conduct
We deliver cargo in a reliable and efficient manner to our clients and partners.
We promote a culture of innovation to create the vessels of the future.
Our values are the cornerstone of our culture, setting us apart and clarifying our identity. Top management plays a crucial role in driving sustainable development, while sustainable practices are integrated into all activities at all levels. Guiding principles include respect for human rights, protection of the environment, health and safety, energy management and climate action, efficient use of resources, diversity, inclusivity and equal opportunities.
We care about our employees by promoting equality, diversity and continuous learning
We take a longterm view when investing in our people, partners and vessels.
Embedding sustainability in our corporate strategy and daily operations has long been a key part of the Group’s modus operandi. Fully aware of our responsibilities towards society and the environment, we strongly support the UN’s Sustainable Development Goals, aligning our corporate strategy and vision to deliver sustainable long-term growth.
We conduct periodical materiality assessments to identify ESG topics of importance to our business. Material topics are determined on the basis of relevance to our operations and activities, taking account of input from both internal and external stakeholders. The materiality assessments are also taken into consideration when assessing the Group’s impact on external stakeholders.
The Group’s sustainability policy is also periodically reviewed to serve as a driver for continual improvement. Reviews are conducted at least once a year by top management. Following the release of the annual sustainability report, a revised sustainable development trajectory is formulated and a strategy is agreed upon by senior management.
The Group’s sustainability policy is developed by senior management, and inspired by the UN Sustainable Development Goals.
• To reduce greenhouse gas emissions, help mitigate the effects of climate change, and ensure a safe, efficient and accessible energy supply
• To encourage the pursuit of sustainable business and the transition to a circular economy; to form partnerships and collaborate with other sustainability stakeholders to promote the creation of social value
• To hire and retain the highest quality, skilled and experienced personnel while valuing diversity and providing equal opportunities
• To foster a culture of sustainability across the entire value chain, including customers, partners, suppliers and other stakeholders
• To manage the risks associated with business activities to prevent harm to people, assets and the environment
Our Group’s Human Rights Policy reflects our commitment to treat people fairly, with dignity and with equal opportunity.
We do not allow workplace discrimination on the basis of race, colour, religion, gender, sex, age, national origin, sexual orientation, marital status, disability or any other personal attributes, nor in the recruitment, selection, development and advancement of employees.
All activities are conducted in a manner that respects human rights as set out in the UN Universal Declaration of Human Rights and the core conventions of the International Labour Organization.
Key elements of our approach to human rights include adherence to health and safety policies, compliance with applicable laws and regulations, regular dialogue and engagement with our stakeholders, and contributing to the general wellbeing of our employees and communities.
• To ensure compliance with current legal requirements and other industry and corporate frameworks
• To systematically assess and review systems to manage and control risks; to establish mechanisms for continuous improvement; and to control processes to ensure objectives are met
• To respond to stakeholders transparently using economic, environmental and social performance indicators published in the Group’s reports
• To set targets to help achieve the relevant UN SDGs
• To promote a positive difference in the community; to give back to society and contribute to long-term sustainable development
During the year under review, a series of discussions were held on sustainability-linked loans.
This was the third year that the Group was asked by its financiers to report on the fuel consumption and emissions of its vessels, in line with the Poseidon Principles on green ship finance. Angelicoussis Group is fully supportive of this initiative.
Supply chains are emerging as a new focus area for sustainability and can play a pivotal role in achieving organisation-wide goals.
Our suppliers encompass a broad category of industry value chain players. These include shipyards, suppliers of stores, provisions, marine fuels, lubricants, spare parts, as well as providers of services relating to port logistics, forwarding, brokerage, agency, surveying and repairs.
The Group awards contracts and places spot orders to meet its supply needs and enable it to provide first-class shipping services across the globe. Our suppliers’ locations are determined by newbuilding contracts, planning for drydocking and maintenance, chartering arrangements and voyage routes, and availability of products. International and local restrictions, pandemic de-
velopments and political disruptions are also factors which contribute towards the selection of our suppliers. Additionally, market conditions and the availability of resources in specific regions may also play a part in the selection process.
Due to its busy newbuilding and drydocking programme, the Group targets bulk orders, not only to maximise economies of scale but to limit emissions related to the supply chain. Our suppliers are periodically re-evaluated, and new suppliers are placed on a one-year probation period, after which they are classified accordingly.
Consistent with our commitment to continuous improvement, our spare parts suppliers are regularly evaluated, with the aim of creating a supplier governance database to ensure alignment with our values.
Angelicoussis Group believes in spreading environmental awareness beyond our organisation and actively working with local communities on sustainability initiatives.
In this spirit, our employees and their families took part in a National Environmental Volunteering Movement initiative to clean up Agios Kosmas beach in the south of Athens on 23 October 2022. In total, 16.45 m3 of rubbish was collected.
The event provided a good opportunity to spread environmental consciousness and educate younger generations on the value of caring for the environ-
ment, while at the same time encouraging an exchange of ideas about adopting more sustainable practices in our daily lives. The Group will continue to organise similar environmental initiatives in the future, and we thank our employees and their families for their contribution to this important cause.
Our Athens headquarters has received LEED® platinum certification. Its bioclimatic design includes operable windows, an atrium, natural shading, skylights, a green roof and a green wall, along with large water features which improve the microclimate.
Green office spaces not only reduce waste and environmental impact but also provide our employees with a healthy and sustainable built environment.
Several measures have been taken to promote energy efficiency and water conservation.
LED lighting, motion and daylight sensors to minimise energy consumption
Highly efficient HVAC system using geothermal energy
High-reflective roofing materials in combination with green roof areas to reduce the urban heat island effect
Parking areas equipped with electric car charging stations and secure bicycle parking
Cisterns for the collection of rainwater and air-conditioning condensate to reduce potable water consumption
Irrigation of planted areas mainly from rainwater stored in tanks, with potable water used only if the collected rainwater does not cover irrigation needs
Secure bicycle racks provided for employees to encourage a more environmentally friendly commute to/from work
Office spaces with design features to improve thermal, optical, and acoustic comfort, with high levels of daylight and outside views
All materials are chosen to have the least possible emissions inside buildings, with air quality monitored continuously
A gym and swimming pool in the office building help employees maintain a healthy lifestyle
Over 7,000 lighting fixtures with an additional 1,000 m of concealed linear lighting installed
Over 900 fire detectors and 3,500 sprinklers for fire safety
Shower and changing facilities are also provided to employees
492 fan coil units and 25 air handling units provide a constant comfortable temperature and air flow
Stakeholder engagement is an important aspect of our materiality assessment and business strategy development. We engage with stakeholders to obtain their input regarding our material ESG topics and sustainability priorities. Their perspectives and constant feedback have enabled us to better shape our sustainability governance and ESG performance strategy.
In 2022, we actively engaged with stakeholders on various topics of importance which are emerging in the industry. We also conducted a stakeholder survey to reassess our material ESG topics, applying the principles of double materiality to conduct the relevant assessment in line with leading international sustainability reporting standards.
The purpose of conducting this materiality assessment is not only to identify ESG issues which pose significant risk or opportunity to our business but also issues through which our Group could have a substantial impact on society and the environment. In determining our material ESG issues, we engaged with different stakeholder groups, including charterers, financiers, employees, regulatory bodies, government authorities and industry associations. The results of our most recent materiality survey are presented below.
The top-ranked material topic in terms of relevance to our business and impact on stakeholders is Regulatory and Legal Compliance, which is reflected through our business conduct, strong company ethics, values and integrity. Our values allow us to deliver operational excellence to customers and maintain healthy risk management. In terms of material topics relating to the social pillar of ESG, Human Rights and Occupational Health and Safety are our top priorities both within our business strategy and daily operations. We are firm believers that our success is founded on our people and we take great pride in retaining top-tier expertise within our Angelicoussis Group family.
The relevance of Environmental Protection and conservation for both our business and the impact on stakeholders is growing steadily. The issue of climate change has generated strong momentum for environmental initiatives within the maritime industry, directly impacting our business strategies and operational decisions. Reaching net-zero targets is an ambitious goal we are striving to achieve.
Shipping is a sector heavily reliant on fossil fuel use, hence the industry must undergo a major transition to achieve decarbonisation. Adopting a decarbonisation strategy is essential for companies in the maritime sector to comply with regulations, manage risks, achieve cost efficiency, and enhance sustainability. Being one of the leading companies in the maritime sector, we are working towards meeting the emissions reduction targets outlined by the International Maritime Organization (IMO), but we are also going above and beyond to ensure the implementation of sustainable and environmentally sound initiatives.
We aspire to contribute as a driving force towards decarbonisation, not only through our direct operations but also by reducing whole supply chain emissions. Accordingly, the Group has established Key Performance Indicators (KPIs) and allocated resources for investment in ESG initiatives.
By utilising research and analytics, our Group is gaining a comprehensive understanding of its carbon footprint and identifying the most effective emission reduction measures. This approach helps us develop a robust and effective roadmap to rapidly reduce our emissions, as soon as a supportive global regulatory mechanism is put in place. We believe that our pro-active approach will provide a competitive advantage in the transition to a sustainable future.
Some key elements of our framework development include current fleet assessment, alignment with current decarbonisation strategies as well as gap analysis for the possible revision of these strategies, technology evaluation and its carbon reduction potential, and finally the alternative fuel mix based on the different approaches to Tank-to-Wake and Wellto-Wake emission factors.
Angelicoussis Group has always been a pioneer in the industry and a proponent of sustainable development. We recognise the urgent need for action to combat climate change and are dedicated to implementing decarbonisation measures and modernising our fleet. We feel it is our responsibility to move from ‘Ambition to Action’ and support industry-wide decarbonisation initiatives.
Our Group has already integrated sustainability metrics into fleet performance evaluations, however our target is to connect these existing processes and performance indicators to a Group-wide strategy that will demonstrate our determination for adopting a net zero trajectory.
The Group invests in software digitalisation which enables real-time accurate estimation of the performance of our vessels. In addition, we are constantly upgrading the energy efficiency performance of our fleet by investing in innovative and state-of-the-art technologies and energy-saving devices, optimising our vessel speed, structural and weight optimisation, improving operational practices, weather routing, hull cleaning and low friction coating applications. An example of the results of our efforts is illustrated in the graph below, showing reduction of excess fuel consumption.
In coordination with leading shipyards, we are also exploring alternative ship designs and technologies which will improve the emissions profile of our fleet. New technologies for on-board carbon capture have also been considered. We are keen to adopt new technologies which are more environmentally friendly and sustainable as soon as these become commercially viable and safe for use.
By having a dedicated team of professionals to lead all energy transition engagements and focus on implementing sustainable practices, we can ensure that all aspects of our operations are thoroughly evaluated, and solutions are tailored to meet our specific needs and those of our customers.
The scope of the Green Ships Department extends to new cargo carrier vessels in support of zero- or lower-carbon energy vectors, the exploration of alternative fuels and energy-efficient technologies, as well as regulatory engagement to contribute to a global framework that effectively promotes and supports the energy transition in our operations. This allows for a deeper and meaningful understanding of the technical, operational, and commercial aspects of the energy transition.
The Group has explored various scenarios to assess the potential impact of different technologies and fuel options, as well as the associated costs and risks. As part of this study, we have defined an emissions intensity reduction trajectory in line with IMO’s GHG strategy and have assessed relevant fuel and technology mixes which would be suitable to achieve the required annual reduction levels. The use of alternative fuels such as LNG, e/bio-LNG, ammonia, e- and bio-methanol have all been considered within our scenario analysis.
Alternative fuel pathways have also been considered in our fleet renewal programme, as the vessels we have on order have shifted from conventionally fuelled ships to those capable of using LNG and LNG’s renewable alternatives such as biomethane and synthetic LNG.
Acknowledging the importance of keeping adequate control of our methane emissions across the entire value chain, we have become a founding member of the recently launched ‘Methane Abatement in Maritime Innovation Initiative’, which is aimed at reducing methane slip from ship engines and accelerating a roll-out of methane measurement and control technologies.
The Group is in constant communication and collaboration across our value chain, including classification societies, shipyards, charterers, policy makers and industry specialists to actively engage and assess the feasibility of different sustainable pathways.
Establishing partnerships with multiple organisations has allowed us to contribute to industry-wide decarbonisation efforts, as well as joint development projects and studies. These collaborations have also furthered our insight and knowledge on upcoming technologies and designs to consider for the future. In this way we have been able to continue to map alternative decarbonisation pathways and further assess our capabilities.
It is expected that the updated 2023 IMO GHG strategy and the introduction of market-based mechanisms, including so-called technical measures will provide the required incentives to industry players to drive the transition towards net zero.
A long-term and stable global regulatory framework can promote large scale investment into alternative fuels production around the world, sectoral integration and development of supportive infrastructure, accelerating the adoption of low- and zero-carbon fuels, towards achieving the sector’s decarbonisation goals.
Hence, we support the efforts of various shipping trade associations to engage with regulators and assist them in introducing effective regulations. This will provide the required vision and enforcement at global level, which is essential for companies to plan their respective business strategies. The selection of the optimal regulatory tool mix will be very important for the success of the sector’s transition. The Group is engaging with stakeholders throughout in order to ensure that due consideration is given to the regulatory options under discussion and that the resulting basket of measures will be as clear and effective as possible. The regulatory tool mix will need to include robust certification and enforcement mechanisms to ensure a level playing field.
At Angelicoussis Group we acknowledge that achieving net-zero emissions is a generational challenge, but we firmly believe it is a critical goal. As a responsible and forward-thinking company, we are dedicated to reducing our carbon footprint and doing our part to help mitigate the impact of our operations on the climate.
We have conducted thorough assessments using advanced modelling and data analytics to evaluate our emissions profile and identify potential emission reduction alternatives. Our teams have implemented a range of measures that have already started contributing to the reduction of our emissions, as we continue to explore innovative solutions to further improve our environmental performance.
We understand that this is a rapidly evolving landscape, and we remain committed to staying up to date with the latest technology and regulatory developments. To accelerate the energy transition, we are always keen to adopt alternative energy solutions, while ensuring adherence to the highest safety and environmental standards.
We are proud of the progress we have made so far and are confident that our investments and efforts will help us to create a more sustainable and resilient shipping industry for generations to come. But we are also mindful of the work ahead required to achieve the sector’s objectives in commercial, regulatory and technical terms.
By Stelios Troulis Director of Energy Transition & Sustainability
Around 15.77 m3 of non-hazardous waste recycled
All suppliers vetted on environmental criteria
Waste Water Improved Annual Efficiency Ratio (AER) for all three fleets
Ballast water exchanged and treated: 75,936,103 MT
Rainwater harvested: 2,363 m3
Decarbonisation is one of our top priorities and the Group is taking steps to reduce its carbon footprint in all aspects of its business. In this framework, we are making investments to improve the energy efficiency of our fleet and reduce greenhouse gas emissions from our vessel operations.
The Group deploys the latest technologies to optimise the fleet’s energy performance. Our fleet management approach involves constant monitoring and evaluation of fleet performance, while fleet renewal initiatives focus on adding modern and more efficient vessels which can run on low-carbon fuel alternatives.
5,839,614
750
2022
2021
All our vessels are included in fully automated data collection and performance analysis platforms. These combine data from multiple sources, including onboard sensors and satellite weather services, to compare real-time vessel performance against parameters established during sea trials and engine testing.
As a leading player in the maritime industry, the Group has a responsibility to lead innovation in support of industry decarbonisation. In the area of vessel efficiency improvement and reduction of emissions footprint, there is strong participation in the development of new software, both in-house as well as in joint development projects (JDP) with other industry organisations. Several recent initiatives are described below.
The monitoring tool utilises live data measured by onboard sensors and reported data to calculate the CII rating of any vessel at any point within the year. In this way, CII ratings can be monitored closely, and corrective or preventive actions can be taken.
As of 1 January 2023, the IMO imposed the mandatory Carbon Intensity Indicator (CII) scheme. Ship operators report the annual emissions data for each vessel, which is then given a rating of A (the highest efficiency) to E every year.
Proper monitoring at frequent intervals is needed to track vessel CII performance throughout the year and make the necessary adjustments to optimise annual ratings. For this purpose, the Group has developed a dedicated CII monitoring and simulation tool which uses both live data from onboard sensors and reported data to calculate the CII rating of any vessel at any point within the year, enabling timely corrective actions if needed.
The tool’s ‘simulation’ function allows operators to forecast how end-of-year CII will be affected
by upcoming voyages. Using parameters such as voyage duration, type of fuel, speed and draught, the tool automatically calculates the expected emissions and transport work of the vessel, and therefore the expected CII rating. The impact of weather conditions is also factored into the calculations by using historical data analysis, thereby enhancing simulation accuracy. Both functions of the tool upgrade the Group’s control of CII performance across its fleet, improving its environmental footprint and ensuring that its vessels are highly rated for efficiency.
The tool also enables us to identify parameters which could reduce the CII rating for specific vessels and make relevant corrections, where applicable, in cooperation with charterers.
Maran Dry Management is participating in a JDP agreement with a classification society and ship designer to investigate and develop a new bulk carrier design that can meet the IMO’s 2050 objective. The vessel design features an innovative solution where hydrogen is reformed from liquefied natural gas (LNG) on demand.
Instead of the traditional two-stroke main engine, the vessel will be powered by two 4-stroke engines capable of running on LNG or hydrogen as well as conventional bunker fuel. Shaft power generators will further improve efficiency, while two
diesel generators will also be installed for use in port and during manoeuvring.
Hydrogen will be generated on board from LNG using the gas reforming process and then blended with LNG for use in the engines, thus reducing GHG emissions. The carbon dioxide generated by the reformation process will be stored on board in dedicated tanks. The design and specifications are expected to be completed in the first half of 2023. In addition to opening a new emissions reduction option for the Group, the project also advances a promising technology that could be deployed across the maritime industry to help decarbonise shipping.
The trim of a vessel underway, whether the bow is raised or lowered, can have a significant impact on speed, fuel consumption and emissions. The third series of Maran Tankers’ L-class vessels, as well as its H- and H2-class Suezmax ships, feature trim optmisation software developed in-house by the Group’s Energy Efficiency team.
The software applies machine learning algorithms to a combination of live data and physical hydrodynamic models to determine optimal combinations of speed and trim for a specific draught. The
tool, which was developed as part of a fleet-wide campaign focusing on trim, is expected to generate annual fuel savings in the region of 2% on vessels to which it is applied.
In addition to the in-house trim optimisation software, Maran Gas has joined forces with a major charterer and installed a real-time trim optimisation tool (developed by the charterer) on a number of LNG carriers.
Realising the importance of anti-fouling paint for hull efficiency and consequently for the fuel consumption and emissions of vessels, the Group continuously analyses the performance of different coatings in order to confidently select the best anti-fouling solution.
This is also coupled with full hull blasting to maintain smooth surfaces as vessels become older.
The Group is taking a number of initiatives aimed at reducing the methane slip on vessels powered by LNG, as follows:
• Installation of a methane emissions reduction system in a generator engine on one of the MEGI vessels in order to measure and verify its effectiveness at capturing unburned methane in the exhaust gases.
• Installation of methane slip reduction software in Wartsila generator engines.
REGULATIONS
The Group closely monitors developments in environmental regulations and actively participates in industry initiatives to challenge and correct ship-specific discrepancies and unfair or off-target requirements.
• Participation in the Methane Abatement in Maritime Innovation Initiative (MAMII) led by Lloyd’s Register with the collaboration of major players in the shipping industry. The scope of the initiative is to identify, measure and abate sources of methane emissions. The project is now entering its second phase, with a focus on measurements, and Maran Gas will be actively participating by installing measuring sensors on its vessels.
The Group participates in a number of feasibility studies related to carbon capture onboard with a view to fully exploring this alternative emissions reduction solution and – where feasible – applying it to newbuilding projects as well as retrofits on existing vessels.
• Waste heat recovery from exhaust gas
• Shaft generators to reduce electrical power production with less efficient auxiliary engines while contributing positively to methane slip reduction for LNG carriers and LNG-fuelled vessels
• Air lubrication systems to reduce hull friction and improve propulsion efficiency
• Variable Frequency Drives (VFDs) to improve auxiliary power efficiency
• Close monitoring of developments in carbon capture on board
• Trialling of innovative technologies such as wind-assisted propulsion for future fuel savings
• Innovative hull and propeller design on newbuilds
• Frequent hull inspections, cleanings and propeller polishing
• Advanced anti-fouling paints to prevent marine growth that increases fuel consumption
• Trim optimisation for improved hydrodynamic performance
• Retrofitting energy-saving devices, including wake equalising ducts and propeller hub caps, to reduce fuel consumption
• Exploring the installation of a reliquefication system on DFDE LNGCs to eliminate boil-off gas consumption in the GCU during slow steaming
• Use of LNG fuel on several vessels
• Exhaust Gas Cleaning Systems on several vessels to lower sulphur oxide (SOx) emissions to IMO requirements and reduce particulate matter emissions
• Operation of vessels in full compliance with the relevant nitrogen oxide (NOx) emissions limits set, meeting IMO Tier II and Tier III requirements
• Exploring the alternative fuel space
• Biofuel trials
• Live monitoring of about 500 parameters for each vessel in the LNG fleet and analysis using in-house tools to verify status and optimum performance of machinery, systems and operations
• Real-time RPM monitoring to minimise speed fluctuations
• Vessel emissions and carbon-intensity performance analysis to ensure compliance and identify optimisation potential
• Monitoring of electrical load and respective generator engines in combination to ensure optimum efficiency
• Applying just-in-time arrival to the extent possible
The first step towards effective waste management is minimising and preventing waste generation. The Group has undertaken several initiatives to reduce the generation of waste on board. Some key initiatives include:
We work with suppliers to reduce the use of plastics as packaging material. This aim is clearly stated in texts on purchasing quotations and order confirmations, while our supplier evaluation forms include requirements to disclose the volume of plastics associated with packaging material and the measures taken to reduce it.
Waste streams are managed in the best possible manner to ensure minimum impact on human health and the environment. We follow a well-defined hierarchy for handling waste from our operations, as outlined below:
• Preventing the production of waste or reducing the amount generated at source
• Reducing the volume of waste through treatment and processing on board
Pre-filtration systems have been installed in main water supply lines across our fleets. This upgrade to the drinking water system, along with the distribution of metal thermoses on all vessels in our dry and gas fleets, minimises demand for bottled water and single-use plastic on board.
To minimise the volume of generated waste and increase storage capacity on board, the vessels of our three fleets are equipped with garbage compactors.
• Material recovery from waste streams for further reuse and recycling
• Disposal of waste in an environmentally sound manner
Part of the waste generated on vessels is discharged to port reception facilities which are regulated by local port authorities and national legislation. Any inadequacies of port reception facilities are reported by the company to the IMO and the vessel’s flag state using the relevant form
3,250m 3
Non-hazardous waste generated 33,700 m3
Sludge produced by fleet
9,173m 3
6,860m 3
Waste generated – Fleet (Excluding sludge)
4,650 m 3 4,711 m 3
6,191 m 3
Note: Sludge not included in the chart. Waste
**The ‘Other’ category includes hazardous waste. Indicative sub-categories include medical waste, aerosol cans, fluorescent tubes, sodium and mercury lights, expired pyrotechnics, mercury-containing products, and chemical waste.
The document control system for the Safety Management System (SMS) used by all three management companies has been transfered to a paperless e-SMS platform, while the transition to using only electronic forms is also in progress. It is estimated that this initiative will decrease the Group’s paper consumption by at least 70%.
A study conducted by the Group calculated that 117,524 paper sheets were saved in 2022 as a result of the transition from paper to e-forms, which also significantly reduced the cost and energy associated with printing. This saving equates to the timber extracted from approximately 11.75 trees.2
2 This conclusion has been reached by making the following assumption: the average pine tree has a height of 13.7 metres and a trunk diameter of 0.203 metres, which is enough to produce 10,000 sheets of paper. Data source: Ribble Packaging Company, https://ribble-pack.co.uk/blog/ much-paper-comes-one-tree
Landfill Other processes** ~ 7,114 m3 ~ 16,084 m3 ~ 11,636 m3 ~ 11.75 ~ 117,524
**Other waste disposal processes include garbage disposed at sea (food waste), sludge evaporated, and water evaporated.
pine trees conserved (each averaging 13.7 metres tall)
sheets of paper saved
Proper waste handling and management is prioritised in all the Group’s office locations. Multiple initiatives have been taken to reduce the amount of waste generated in our office buildings. Key activities include:
• Bins to segregate waste of different categories – including paper, e-waste, used batteries and printer toner cartridges – have been placed on all floors
• Employees are encouraged to not only recycle all used items at work, but also bring any used batteries and unused electronic devices from home to be recycled
• Filtered water is available at all kitchenettes in our offices. Employees are encouraged to use this water instead of purchasing disposable plastic water bottles
• Kitchenettes are equipped with mugs, cutlery, and kitchen utensils to avoid use of single-use plastic items
• Biodegradable straws are made available to staff members
• Coffee capsules used at our offices are recycled.
• Binders and file folders are reused instead of being discarded after use
The Maran Ship Supplies (MSS) office in Singapore takes further measures to ensure optimum reuse and recycling of waste, enhancing our contribution towards building a green supply chain and a circular economy. These measures include:
• Repurposing of cartons for use in future supplies
• Empty drums and discarded intermediate bulk container tanks are re-supplied to sister ships requesting them for waste collection purposes
• Waste products are used to construct shelving and storage bins
• Hazardous waste recycled ~ 0.04 m3 (used batteries)
• Non-hazardous waste recycled ~ 15.77 m3 (electronic devices, paper, coffee grounds, aluminium from coffee capsules, etc.)
• MSS has never purchased wood pallets. Those returned from suppliers are repaired and used until the end of their lifecycle
• Cylinders for breathing apparatus, firefighting equipment and medical oxygen are refilled, recertified and reused across the fleet
Our vessels use seawater as part of their regular safe operations. Any seawater taken up for ballasting is treated using approved systems, in line with the International Convention for the Control and Management of Ships’ Ballast Water and Sediments (BWM Convention). Our vessels do not take up water from or discharge water into any water-stressed or environmentally sensitive areas.
The BWM Convention’s D2 standards ensure that the water loaded onto our vessels is treated on board through a variety of approved technologies, such as by ozone UV lamps, direct electrolysis, filtration and chlorine dioxide treatment, or electro chlorination, prior being discharged at sea. For vessels which are not yet fitted with treatment systems, ballast water is replenished through exchange in line with D1 standards.
Our Group adopts a prudent approach to water consumption. Vessels do not withdraw or discharge any fresh water. Fresh water is produced on board from seawater and waste heat energy. Drinking water fountains are installed on all vessels, with water samples analysed at predefined intervals to ensure the quality of potable water.
In line with the LEED certification of the Athens headquarters, we have installed rainwater storage tanks that collect water for use in the irrigation of planted areas throughout the office premises. Potable water is used for other water needs across the site, and might also be used for irrigation, if the rainwater collected does not cover these needs. Overall, subject to annual rainfall, water consumption is significantly lower than what would normally be expected.
75,936,103 MT
Ballast water exchanged and treated
100% 98%
100%
Total water consumption
8,274 m3
Water recycled / saved
2,363 m3
(Athens and Singapore offices) (rainwater harvested)
Oceans are one of the world’s most important natural resources, contributing significantly to climate self-regulation as well as international trade and human livelihoods. Our business and daily operations are reliant on oceans and hence we are extremely conscious of the impact that our vessels have on marine ecosystems, including noise, water pollution, and the spread of invasive species. Accordingly, we undertake multiple initiatives to prevent marine pollution and preserve ocean biodiversity.
Our vessels use environmentally acceptable lubricants (EAL) for all oil-to-sea interfaces – including stern tube bearings, thruster and rudder bearings, wire ropes and bow thrusters – unless technically unfeasible, in compliance with the US Environmental Protection Agency’s 2013 Vessel General Permit (VGP). In addition, all vessels have installed a new stern tube seal system that uses compressed air to provide extra protection against oil leaks.
To further prevent polluting the waters in which our vessels operate, we use tributyltin-free anti-fouling hull coatings in compliance with the International Convention on the Control of Harmful Anti-fouling Systems on Ships.
International regulations require vessels to meet specific operating standards in designated Emission Control Areas (ECAs) and Particularly Sensitive Sea Areas (PSSAs). All Angelicoussis Group vessels adhere to these requirements and also reduce speeds in waters where whales are known to be present. The Group’s vessels operated in restricted ECAs and PSSAs for a total of 23,820 days in 2022 without a single violation of environmental regulations.
To decrease the underwater noise generated by our vessels, we implement noise-reduction measures at the design stage. These measures include vent fan silencers, sound-insulated generator rooms, minimum propeller cavitation and torsional vibration compensators.
Fully compliant with the requirements of the IMO’s BWM Convention, the Group has installed a ballast water management system on most of its vessels to help reduce the risk of transferring invasive species between ecosystems.
Violations of environmental regulations in ECAs and PSSAs
8,099 Active pool of seafarers
511 Shore-based personnel
Average hours of training per seafarer – 22.5
Average hours of training per shore personnel – 8.9
Total Recordable Incident Rate (TRIR): 0.384
Fatalities: 0
8,460
5,598 5,323 EMPLOYEES
At Angelicoussis Group we fully appreciate that our people are the most valuable component of our successful operation. We have designed an attractive and modern work environment, integrating the principles of inclusion and diversity at all levels.
WHO TRAINING
8,099
7,511
active pool of seafarers seafarers on board
275
511
shore-based personnel
COMPUTER BASED TRAININGS (CBT) CREW
189
women at sea (37 new hires in 2022)
191
women on shore
Singapore, Philippines, United Kingdom, South Korea, Ukraine, Romania, Greece and other countries of the European Union.
Our human resources department invests in ensuring employee satisfaction and attracting new talent to cover the Group’s current and future needs. The Group provides attractive salary packages, performance incentives and opportunities for continuous training and upskilling, managed through continuous monitoring of KPIs and state-of-the-art personnel management systems.
LONDON OPERATIONAL OFFICES
OKPO SITE OFFICE
MANILA OPERATIONAL OFFICES
SINGAPORE OPERATIONAL OFFICES
At Angelicoussis Group, we foster talent and believe in offering equal opportunities to all employees. Diversity and inclusion have always been core principles, firmly embedded in our corporate culture, and appropriate measures are taken to uphold these values across all levels within the Group.
We have strong female representation and leadership at all levels, including the board and senior management. Our active pool of seafarers come from many different cultural backgrounds and work together harmoniously to deliver operational excellence at sea while maintaining a close family atmosphere on board.
Angelicoussis Group is a proud member of the Women’s International Shipping & Trading Association (WISTA) and is currently considering participation in
several initiatives to promote and enhance equality, diversity, and inclusion in the workplace.
We comply with all applicable labour and employment laws and ensure fair and decent working conditions for all our people and contractors. Systems and processes are in place for employees to raise concerns in the workplace. The Group does not employ people under the age of 18.
Newly hired employees are provided on-the-job training and familiarised with the Group’s policies. Procedures and policies relating to human rights are thoroughly respected, while the code of conduct, which includes a dedicated section on human rights, is discussed in detail during the onboarding process.
2022 was the first year that IMO officially celebrated the “International Day for Women in Maritime”. As a Group, we support initiatives and actions allowing the wider participation of women, and we embrace gender diversity on board and ashore. Our employees’ diverse experiences and knowledge contribute to our collective competence and significantly boost Angelicoussis Group’s
overall performance. For IMO’s celebratory day for women in maritime our goal was to re-introduce our women seafarers to each other and their colleagues through our social media/newsletters. For this reason, we launched the first “Women in Maritime” campaign, asking all women seafarers on board our vessels to share their stories.
Distribution
New Hires by region
Turnover by region
An active pool of 8,000+ seafarers representing multiple nationalities, ethnicities, and cultures. We encourage participation of women seafarers and employ over 180.
Angelicoussis Group’s workforce at sea consists of an even mix of young talented professionals and highly skilled seafarers with academic qualifications and seagoing experience, each of whom contributes to the sustainable operation of the Group.
Company-wide distribution of seafarers
3,472
Distribution by age group
New hires by region
3,632 732
995 236
Our success is largely dependent on retaining high-quality, talented individuals with an eagerness to evolve and learn. We strive to provide our personnel with a dynamic, stimulating workplace and offer industry-competitive salaries, reviewed on a regular basis to keep up-to-date with market trends. Beyond this, we provide employees with benefits that exceed the requirements of local legislation.
Our Group offers life insurance coverage to all permanent employees.
We provide financial support to employees who are unable to work due to ill health.
The Group complies with local regulations and encourages employees to take parental leave.
To help new mothers, we give employees in Greece flexibility over childcare leave and working arrangements. New fathers are offered an extra day of parental leave and given the flexibility to take these days (15 in total) up to one month before and up to four months after the child’s birth, beyond the maximum of two days before and one month after as required by law.
93%
Return-to-work rate after parental leave
All permanent office employees in our Group enjoy a comprehensive healthcare programme, including private doctors and an annual hospitalisation allowance. More specifically, HQ in Athens offers:
• An occupational doctor, occupational safety technician and two fleet medical advisors, who oversee health and safety issues at our Athens headquarters
• Voluntary annual medical checkups with differentiated programmes based on employee age
• Additional medical tests and screening at reduced prices
• Fully equipped gym and pool facilities with inhouse trainers
• Catering service providing fresh and healthy food
With regard to our seafarers, Angelicoussis Group has a formal agreement with several recognised and accredited health facilities covering the respective geographical locations, in compliance with flag state and insurance requirements.
All seafarers are required to carry out pre-embarkation medical tests approved by the Group’s Medical Examination Scheme, free of charge, at recognised health facilities. Pre-embarkation medical tests exceed flag administration requirements.
All medical checks for shipboard personnel are completed not more than 20 days before crew embarkation, with results reviewed by the Group’s in-house medical advisor prior to the seafarers’ departure from their home country. The frequency of medical examinations is in accordance with flag administration and P&I requirements. Both contracted health facilities and the in-house medical advisor follow the Group’s GDPR policy, thereby protecting our seafarers’ rights to privacy.
To help employees with the increasing cost of living, a tax-free Ticket Restaurant card was provided as a discretionary benefit to all headquarters staff in 2022. This food voucher can be used at supermarkets, restaurants and coffee shops throughout Greece.
All of our Greek, EU and Ukrainian seafarers are covered by the Greek Collective Bargaining Agreement. All employees working for ship management companies at our offices in Greece are covered by the Industry-wide Collective Bargaining Agreement.
At Angelicoussis Group, we recognise the importance of engaging our employees in the development, implementation and evaluation of our occupational health and safety management system. Their active participation and consultation play a crucial role in overall safety standards and fostering a culture of well-being throughout our organisation.
One of the primary avenues for employee engagement is our biannual company forum. During these forums, employees have the opportunity to express their opinions and provide feedback on our safety management system (SMS). Departmental workshops, briefings, and debriefings also support employee engagement. Ship and shore personnel actively contribute their insights, ideas and suggestions for further improvements and their feedback is used to continuously enhance the effectiveness of our occupational health and safety practices.
Additionally, we have set up a Safety Committee on each vessel, which serves as an open forum, fostering discussions related to safety, quality, health, and pollution prevention. The minutes of these meetings are electronically transmitted to the Health, Safety, Quality, and Environment (HSQE) Department for review and follow-up, thereby ensuring transparency and a shared understanding of the matters discussed.
To better understand morale, satisfaction, motivation and engagement across our fleets, Angelicoussis Group carried out a Personnel Satisfaction Survey for shipboard employees.
The survey was conducted via an anonymous online questionnaire, giving seafarers the opportunity to express their opinion and concerns across a range of topics, including:
The feedback received was presented to senior management to strategise ways forward and evaluate proposals and recommendations made by our people, to better our work environment, and to create opportunities for growth for all our employees.
The Angelicoussis Group Crew Forum was hosted by Friendly Maritime Services (FMS) in the Philippines on 3 October 2022.
Feedback was also sought on the cooperation and support of shore personnel.
The survey results were analysed with the aim of improving policies, with a focus on strengthening the collaboration between ship and office personnel.
At the same time, the Group’s HR Department ran an Engagement Survey for office employees, with questio ns on topics such as those listed below:
Diversity and inclusion Pay and benefits
Learning and development
Workplace conditions
The event provided an opportunity for interaction and an exchange of ideas between the Group’s Athens office team, the team from Friendly Maritime Services Inc., and Filipino seafarers. The main topics of discussion were the Group’s history and current developments, as well as its growth and future career plans for seafarers.
Presentations were given by a number of speakers, followed by a Q&A session. Seafarers with the longest service received plaques and gifts from the Group CEO.
Collaboration and teamwork
Workload and flexibility
Angelicoussis Group has a long-standing culture of mentoring, training, and investing in its workforce. Training programmes are customised to our needs and constantly reviewed to keep our talented personnel up-to-date in their areas of expertise.
22.5
Average training hours per seafarer
7,511
seafarers received training
169,417
total training hours
Angelicoussis Group’s DELPHIC Maritime Training Centre was the first in-house training facility established (2004) in Greece by a major shipping company. The Group’s objective is for DELPHIC to remain a leading in-house training facility that develops and delivers company-specific courses. The centre provides high-quality courses for improving both technical and soft skills among seafarers and shore-based personnel.
The centre has state-of-the-art facilities, including an engine simulator, full bridge simulator, Electronic Chart Display and Information Systems (ECDIS) simulator, and a cargo simulator for tankers.
Our seafarers receive training that meets requirements for Greek-flagged ships and mandatory requirements as laid down in the STCW (95) Convention, ILO Convention (No. 180), and IMO Resolution A.481 (XII).
Training is provided in the framework of our company training matrix, which forms part of the Safety Management System. The training matrix consists of mandatory courses, required before embarkation, and a series of optional courses to support career development.
All training is delivered by in-house trainers or accredited external providers. Training sessions are held at our training centre or at sea through the online Seagull platform. In addition, seafarers are given assignments to familiarise them also with shore-based operations.
Training is crucial for ensuring the highest standards of occupational health and safety onboard. In order to make training accessible to all our seafarers, we offer courses free of charge not only at our in-house facilities, but also via job training onboard and Computer-based Training (CBT) on the following topics:
Conformance with SMS policies, procedures, and requirements
Safe operation and preservation of the environment
Impact of work activities and risk assessment
Roles and responsibilities to conform with SMS policies and procedures
Emergency preparedness and response
Consequences of non-conformance with operating procedures and requirements
Importance of identifying near misses, unsafe acts/ conditions, and defect reporting
To make cadets’ first voyage easier, they are provided with a pre-embarkation manual. The manual outlines the fundamental rules and hazards of working onboard our vessels, (customised to each vessel type within our fleet), as well as the safety measures that must be followed to protect our seafarers, the environment, the ship, and its cargo.
Two captains in the Suez Canal Authority, both senior pilots and simulator instructors, were invited to the Delphic Maritime Training Centre to provide training on the Suez Canal transit to our masters and simulator instructors.
This was the first time that Suez Canal pilots provided this kind of training in Greece. Based on positive feedback and the frequency of Suez Canal transits, the Group will explore how to continue and further leverage this cooperation.
Average annual training hours per shore-based employee Number of employees trained of our shore personnel participated in training programmes
The Group offers a variety of training programmes to shore-based employees to upgrade their skills and support their transition to the Group’s corporate environment. Training programmes fall into the following categories:
An occupational safety technician is responsible for carrying out a series of training programmes at our Athens offices, including fire safety, earthquake protection and building evacuation. In 2022, 35 employees participated in safety training sessions.
Advanced training is provided to Fire & Safety team leaders. Present on each floor of the building, these
The Group strives to continuously improve the training it provides to ensure that employees have the skills they need to deliver best-in-class operations and service. Several methods are used to assess needs and ensure continuous improvement in training.
• Career development plan review: Each employee has a career development plan, and the appraisal reports and competency assessments are used to update training requirements.
• Training matrix: Each management company has a training matrix defining mandatory and optional training depending on an employee’s role.
• Industry updates and compliance requirements:
The Group offers further assistance to employees wishing to upgrade their skills beyond the formal internal training programme. Support includes:
Financial assistance for higher education programmes (tuition, books, exam fees)
Memberships to professional bodies and periodical subscriptions
team leaders are responsible for their designated area and colleagues.
The company considers First Aid knowledge to be crucially important. Six training sessions on medical care were organised for our seafarers throughout the year. Office employees are more than welcome to attend. The training is delivered by our medical advisors.
Quarterly management review meetings ensure that new regulatory or industry requirements, trends and best practices are considered, as well as changes in the technological, legal and general operating environment.
• Onboard assessment and simulation programmes: Masters’ reviews, drill reports and individual competency assessments complement the results of simulation-based programmes to identify training needs for onboard personnel. Evaluation of incidents, near misses and non-conformities are also taken into consideration.
• Other methods: Training is regularly updated based on inputs from a variety of sources, including audits and inspections, requests from managers or employees, company forums, departmental workshops, debriefing sessions, incident reports and feedback from trainees.
Flexible working hours for higher education programmes or training sessions
Vessel visits for office employees
Opportunities for participation in industry conferences and forums
Open Business Skills Seminars on widely applicable topics such as problem solving, decision making and leadership
As part of our Group’s continuous efforts to engage with youth, we welcomed students from the World Maritime University in Malmö, Sweden to our premises in Athens. The 25 students from the Shipping Management and Logistics postgraduate programme represented 17 nationalities.
The students attended presentations on various shipping industry topics related to human resources, HSQE, and crew training. The Group’s HR Manager provided a number of useful tips on how to write a successful CV and participate in job interviews, explaining skills that are vital for success in the maritime sector. The students also attended a presentation from our Group’s HSQE managers focusing on sustainability and safety challenges in the shipping industry. The postgraduates gained useful knowledge and had the opportunity to visit the Delphic MTC, attending a live training session with the use of state-of-the-art equipment and simulators.
Angelicoussis Group hosted one of the largest internship programmes in the maritime industry during Summer 2022, with a total of 40 interns.
Over the two-month programme, interns from universities in Greece and abroad gained handson experience of the latest maritime technologies and the processes of each department within a ship management company.
At the end of the internship, all participants were offered career advice and invited to share their experiences with the HR Department with a view to further improving the programme.
For training purposes, groups of our shore employees often visit our fleet vessels to gain a better understanding and perspective of our seafarers’ life on board. During these visits, they have the opportunity to learn about the main areas and operations of the ship and meet our crew members. In this way, we encourage our shore personnel to gain insight into operations onboard and provide meaningful support to our seafarers.
The Group has established a robust performance management process to accomplish Specific, Measurable, Achievable, Realistic and Time-Bound (SMART) goals, competencies, and personal development targets.
Personal development plans for employees take into account not only their own ambitions but also the Group’s mission, vision and strategic goals. Performance management is a continuous process that is core to achieving the Group’s strategic goals. The annual process has three phases.
Shore-based employees given a regular performance & career development review
Upholding one of our core values, namely, caring for our employees, Angelicoussis Group is firmly committed to promoting worker health and maintaining a motivated workforce.
In 2022, the Group initiated a series of sessions on health matters with the aim of raising awareness by inviting specialised doctors to provide medical advice to our employees. The first session was focused on breast cancer awareness. The initiative will continue in 2023.
Also in 2022, the Group launched a series of campaigns to advance skills and knowledge regarding health and safety aboard our vessels.
‘Let’s Talk - Care for your Mental Health’: Awareness training and employee engagement to work on mental health issues (including access to appropriate care), organised on the occasion of World Mental Health Day.
‘Signs of emotional suffering’ leaflet, emphasising key behavioural changes linked to emotional issues. The Group shared the contact details of the in-house medical advisors, and the confidential line that any employee can call for assistance.
‘Medical Advice’ pamphlet, containing general information about common medical emergencies, including warning signs if experienced on board.
Mental health awareness seminars for all our seafarers, to provide training on identifying weak signals and offering support.
Promoting employee well-being
Angelicoussis Group, having recognised the importance of promoting the well-being of its workforce, launched the first in-house ’Seafarer well-being app’, providing free training instructions and fitness tips to its seafarers and office employees.
During 2022, several safety campaigns were initiated, aimed primarily at tackling occupational health and safety impacts. These included but were not limited to:
Fitness challenges such as indoor triathlon, International Yoga Day activities, and push-up contests, increase social interaction among the Group’s employees through friendly competition, while at the same time promoting an active lifestyle.
The Group’s employees are also encouraged to participate in external events such as the Athens Marathon, the Posidonia Sailing Cup, and amateur basketball leagues.
Lifeboat campaign focusing on raising awareness, using questionnaires to engage with crew members in improving safety practices and processes.
Navigation campaign to promote safe behaviour at sea.
Hand and finger injuries campaign to communicate the latest industry trends on such injuries, raise awareness on the associated hazards, compare trends of previous years to current ones, and analyse the effectiveness of existing barriers and guards.
Entry into enclosed space campaign to enhance crew awareness about the hazards of entering enclosed spaces and ensure implementation of risk management measures.
The Gym Department at our Athens HQ runs a new challenge every two months, each time focusing on a different exercise.
The challenge in February/March was: ‘’How long can you stay in a wall sit position?”, which more than 70 colleagues completed successfully.
The wall sit is an easy exercise that works the muscles of the lower body. Most participants were able to hold the wall sit position for longer periods of time as they increased their muscular endurance. The next successful fitness event, which took place in April, was the push-up challenge. Push-ups build upper body strength while also targeting the lower back and core muscles.
The balance test was October’s gym challenge. All participants had to start barefoot, stand on one leg, and put their sock and shoe back onto the elevated foot, tying the laces as well. Then they had to change legs and repeat, completing the challenge in under one minute. This task requires not only good balance but also good mobility for a full range of motion while putting on the sock and tying the shoe.
The Group held its very first Indoor Triathlon in the Athens HQ gym.
The Indoor Triathlon was designed for all employees, whether beginner, intermediate or advanced athletes. Its purpose was to introduce everyone to the three events of a triathlon (swimming, cycling, running), and it provided a great opportunity to compete in a corporate environment and have fun with colleagues.
The Indoor Triathlon is an exciting introduction to the sport for athletes of all abilities. It offers all the health and fitness benefits of an outdoor triathlon, but in the safety of our premises.
Our Indoor Triathlon is based on distance and involves cycling on a stationary bike (5 km), swimming in the pool (200 m) and running on a treadmill (1 km).
After an extended break, the prestigious Posidonia Cup sailing regatta, one of the longest-standing corporate sporting events on the global calendar, brought the international shipping community back together in 2022.
Angelicoussis Group participated in the race. Although the strong northerly winds, in combination with frequent small changes in wind direction, made for a very challenging race, our sailing team won the regatta and the coveted trophy after a stellar performance.
In the build-up to the Posidonia Cup, the sailing experience project was initiated to introduce as many employees as possible to the sport.
Sailing has much in common with our work environment, in which constant changes and unexpected incidents give us the opportunity to work as a team and to adapt, dealing with any new challenges that arise.
Motivated by this idea, more than 60 employees signed up to learn the secrets of the art of sailing for four weeks, after office hours. The participants learnt new skills as a team, solved problems and worked together in a fun yet challenging environment.
The Angelicoussis Group basketball team was formed three years ago and consists of energetic, passionate employees representing our Group in tournaments with other shipping organisations.
With the invaluable support of Group management, employees from various departments join forces to compete and represent our Group’s values of fair play. It also offers an opportunity to get to know colleagues from other departments, fostering a sense of belonging to a high-performing organisation with a close-knit family feel.
Safety is at the core of our operations. We incorporate the highest safety standards in every aspect of our operations while protecting both our onshore personnel and seafarers from health and safety hazards.
Total Recordable Incident Rate (TRIR)
0.384 0.187 0.091 0.094 Work related Fatalities
The Group takes a systematic approach to the identification of weak signals and hazards to develop a proactive safety culture using the risk assessment process. This proactive culture is further enhanced through behavioural-based programmes, including reporting of near misses and unsafe actions or conditions.
It is our Masters’ responsibility to ensure the reporting of all identified near misses through a dedicated electronic form. Any verbal or written statement or complaint which identifies work-related hazards is carefully assessed and, where appropriate, investigated through the appointment of a team by the Group’s respective Designated Person Ashore (DPA).
The sophisticated design of our Safety Management System (SMS) ensures a safe work environment for our employees. The SMS is reviewed on a regular basis by our qualified professionals, in the framework of concerted efforts towards continuous improvement, considering at the same time the latest developments regarding the revisions of international standards and new regulatory requirements, e.g., the International Safety Management (ISM) Code, ISO 14001 Environmental Management System, ISO 45001 Occupational Health and Safety Management Systems, ISO 9001 Quality Management System, ISO 50001 Energy Management System and ISO 31000:2018 for Risk Management.
All offices comply with local regulations and laws regarding health and safety at work. The Athens office, which accounts for the majority of the Group’s employees, is under contract with one of the leading companies in Greece in the sector of workplace health and safety, which provides occupational doctors and technicians for regular visits, while handling all health and safety management matters.
The system is revised and updated at least twice a year to ensure continuous improvement and compliance with all applicable regulations and legislation, as well as to include all accepted employee proposals. Third-party feedback on the system’s effectiveness is assessed and, where appropriate, changes are made to incorporate industry best practices.
Continual improvement of the SMS is also established through the submission of Master’s Review reports. These contain a brief assessment of shipboard
The company has used specialist resources for the development of a user-friendly e-SMS platform with an advanced search tool. SMS manuals and e-forms are easily accessible by all shore and shipboard personnel at all times. The SMS visual presentation uses warnings and notifications and is continuously improved with the involvement of our in-house IT department and industry experts.
activities, addressing identified deficiencies and suggestions for improvement. All masters are required to submit this report upon completion of six months onboard. The reports include a detailed analysis of SMS implementation and effectiveness, along with suggested improvements to SMS procedures.
Proposals for improvement of the SMS are also gathered through debriefings, ship/shore exercises and tabletop drills.
Through our user-friendly e-SMS platform, a new functionality was created to engage our end users and obtain a different perspective, in order to enhance and develop procedures using our seafarers’ experience. Through this functionality, our seafarers and shore personnel can make direct suggestions on improving procedures with the click of a button through the e-SMS manual.
This allows our employees to propose changes directly to the respective department, which are then reviewed, evaluated, approved and/or rejected on the basis of defined levels of authority. The new platform encourages employee recommendations for SMS process optimisation, recognising that the different perspectives gained from our highly qualified and experienced staff can offer added value in improving our safety management.
Our safety risk management process focuses on identifying, assessing, and treating risks. We use validated tools to identify weaknesses and hazards and implement measures to mitigate risks. Any personnel can initiate a risk assessment and we encourage seafarers’ involvement.
We have a ‘no-blame’ culture that encourages reporting of unsafe conditions. Our HSQE department promotes reporting of near-misses and takes appropriate actions. We use Key Performance Indicators to prompt new risk assessments by vessel personnel.
Risk assessment is a continuous process, so we regularly update the library of approved risk assessments and Job Hazard Analysis (JHA) for both routine and non-routine tasks. The Group’s SMS procedures have been issued and updated on the basis of the risk assessment process.
Risk assessment training is provided to all shore and shipboard personnel. Shore personnel promote hazard identification and the risk assessment process during attendances onboard. Any identified training needs during onboard visits are reported and followed up appropriately.
We have constantly supported the Antonios and Ioannis Angelicoussis Foundation since its establishment in 2013. Sharing common values with our Group, the Foundation is dedicated to providing practical assistance and financial support to the local community and society in general in the following key areas:
The Antonios and Ioannis Angelicoussis Foundation donated a new cardiac ultrasound system to the cardiology department of the Ippokrateio General Hospital of Athens, one of the leading cardiology departments in Greece. The new PHILIPS EPIQ CVX cardiac ultrasound with state-of-the-art software brings significant advancements in functionality with clearer and sharper imaging, which will help many more patients with cardiovascular diseases.
Funding was provided for the complete renovation and modernisation of the Kopanari building at West Attica Hospital “Agia Varvara” - General State Hospital of Nikaia. The Ioannis Angelicoussis Psychiatric Clinic for Adolescents in the building has a capacity of 15 beds and has secured the staffing of a multidisciplinary team of child psychiatrists, psychologists, social workers, speech therapists and occupational therapists.
Educational material and stationery donations were made to the 27th Kindergarten in the West Attica municipality of Ilion, with a total of 37 students for the 2022-2023 school year.
The Foundation supports educational workshops for children with special educational needs. The programme, which includes guided tours of the museum’s permanent collections, is organised by experienced staff who specialise in education and art therapy.
The Foundation installed new playground equipment for a schoolyard in Petrousa, Drama, Northern Greece. The kindergarteners sent heartwarming and inspirational drawings as a token of their appreciation.
During the ongoing military operations in Ukraine, the Foundation donated food and medical supplies for the first “Médecins du Monde” mission to the Ukraine-Romania border to support Ukrainian citizens and refugees.
100% - Governance body members and employees receiving anti-corruption training
Anti-competitive behaviour
Zero - Legal actions for anti-competitive behaviour, anti-trust, and monopoly practices
Our Group proudly received the 2022 award for leading participant in the Automated Mutual-Assistance Vessel Rescue (AMVER) Program, having enrolled a total of 114 ships in the system
Maran Tankers Management Inc. received the 2022 GREEN4SEA Tanker Operator Award
Maran Gas Maritime received the 2022 SAFETY4SEA Tanker Operator Award
The focus of the Group is to take business decisions which are not only targeted towards improved financial performance but also have a positive impact on society and the environment.
Sustainability is integrated into all the Group’s activities and organisational levels, taking into consideration the availability of resources and the perspective of our stakeholders, without compromising the interests of future generations. Corporate goals are set every year, embedding ESG in all the Group’s activities.
Our board consists of two executive and two independent members, representing different age groups, professional backgrounds, cultures and genders.
Under the leadership of our senior management, the Group is constantly working towards improving its operational performance and corporate strategy. In order to ensure business resilience to any current and potential risks, we regularly review and update our Business Continuity Plan (BCP). The Group’s BCP was recently updated based on new findings and lessons learned in 2022. In particular, a BCP drill was completed in 2022, helping us review current operations and the impacts that could occur in the event of a disruption.
Top management advance their knowledge and expertise in sustainable development through their active membership in industry and regulatory boards, their participation in industry forum and panel discussions, seminars and an extensive network of technical societies. Furthermore, active engagement with the Group’s customers across our value chain and participation in joint industry studies to explore various energy transition vectors contribute to the Group’s sustainable development.
Managing directors of the operations, technical management, legal and energy transition departments are appointed by the board based on their skills and experience. Department employees report directly to the relevant director and constantly communicate on regular updates, matters of urgency, as well as commercial and operational needs.
Upholding principles of ethics and integrity is an integral part of our business activities. All employees are required to adhere to the Group’s policy of conducting business in an honest, sincere, lawful and ethical manner.
The Group’s ethics and integrity policy is outlined in the code of conduct, which is obligatory for all employees and applied in all business dealings and relationships. The Group is committed to acting professionally, fairly and with dignity and integrity in all activities.
Acts of bribery and corruption are not tolerated. Effective systems are in place to counter both phenomena.
The Group respects the law of the countries in which it operates and where vessels are registered, international conventions related to the Law of the Sea and all local legislation that has been made known to us through the appointment of agents in other countries.
Each part of the Group has a different susceptibility to corruption and bribery. Accordingly, we have identified threats and developed mitigation policies for key operations and geographical areas. These include procurement departments, project departments, and regions which pose a higher risk of corruption.
In addition, we engage the services of TRACE International, a leading anti-bribery standard-setting organisation, to independently assess all facets of the Group’s business. This includes ownership matters, vetting of shareholders, key management, financial transactions and results, management and operations of all vessels, feedback and reports from news media and other third parties.
All employees receive and confirm receipt of the code of conduct, and are accountable for its proper implementation. Additionally, the Group bears a social responsibility to ensure that these values are also upheld by our suppliers and business partners.
When recruiting personnel both on shore and at sea, we obtain references and police reports and include behavioural-based interview questions which are designed to assess the risk of corruption. After recruitment, our induction and familiarisation processes, code of conduct, training, whistleblowing mechanisms and values hierarchy serve as safeguards against the risk.
Anti-bribery and anti-corruption are also discussed in the framework of office forums and workshops, onboard meetings, dedicated training, and other initiatives. External contractors are also briefed on our anti-corruption policies.
Governance body members and employees have received training on anti-corruption. 100%
All personnel are required to avoid any conflict between their personal interests and the interests of the Group in their dealings or relationships with the Group’s competitors, suppliers, contractors, or customers. For our Group’s procurement functions we have internal controls and follow standard procedures to avoid any such potential risks. Additionally, a separate section on this issue is included in the Group’s code of conduct.
The Group’s companies have put in place confidential reporting lines to enable employees to raise any concerns about fraudulent or dishonest conduct, along with a detailed on-board complaint procedure, using confidential email addresses for the reporting of complaints and concerns in relation to unsafe acts, unsound conditions, and cases of non-compliance. These email accounts are included in the code of conduct and communicated to fleet and shore personnel during the pre-joining and familiarisation stages.
Legal actions for anti-competitive behaviour, anti-trust, and monopoly practices
Moreover, each company’s Designated Person Ashore (DPA) is available 24/7 to receive any complaints or reports related to health, safety, environmental or other concerns. The DPA’s contact details are posted on each vessel for easy access by anyone onboard. For office employees, we have a grievance policy which explains how complaints are raised, investigated and handled.
Our dedicated HR function implements the Group’s open-door policy and ensures all employees feel safe and comfortable reporting concerns. Engagement surveys are periodically run to gain insight on topics including working conditions and environment, mental health, stress at work and manager and employee behaviour. Employees are encouraged to communicate any critical concerns they may have. All information gathered is communicated to top management to find solutions to accommodate employees.
Employees have the opportunity to communicate critical concerns to management during their midyear and annual performance reviews. Critical concerns may be recorded in their evaluation template to be further addressed by top management.
Wanting to maintain a close-knit family atmosphere, our Group’s CEO holds weekly ’Morning Coffee‘ sessions with a group of employees selected on a rotation basis. In this way, the CEO is able to maintain a personal relationship with employees and provide a direct line of communication for any concerns or proposals that employees wish to put forward.
Top management maintains an open-door policy and is alerted to all critical concerns through the HR unit, department managers, or directly by employees.
The Group participates in a number of industry associations and committees with a view to promoting safe and environmentally sustainable shipping.
The 65 th panel meeting of the Society of International Gas Tanker and Terminal Operators (SIGTTO) was hosted in Athens by Maran Gas Maritime. The event was attended by more than 150 participants representing LNG terminals, operators, charterers, and service providers worldwide.
The two-day conference focused on environmental regulations, technology developments, floating marine facilities and safety topics, with a dedicated panel discussion on the industry’s path to decarbonisation.
The first seminar of WISTA Hellas, a member of the Women’s International Shipping & Trading Association, focused on the challenges faced by women at sea. Senior shipping executives noted progress towards gender equality but also room for further improvement. From Angelicoussis Group, insurance manager Vivi Kolliopoulou participated as a panellist, sharing our Group’s experiences and perspectives on the topic.
Angelicoussis Group hosted the third Informal Bulker Operators’ Safety Forum (IBOSF) in 2022. This forum, the first in-person version of the event, allowed bulk carrier operators to share ideas and best practices to prevent safety incidents. Participants discussed causes and proposed solutions regarding the two leading accident indicators: navigation incidents causing collisions in congested waters, and fuel system leakages causing fires.
Group training manager Dimitris Fokas was a guest speaker at an Ocean Technologies Group seminar titled ‘Powering the People that Power World Trade: Enabling our maritime professionals in a time of change’. The discussion revolved around new technologies and recent requirements and developments that will place new demands on the skills of crews. Participants explored how technology can be used to find, build and retain talent, and to support maritime professionals.
The Group participates in the Partners in Safety (PnS) programme initiated by Shell, which currently focuses on human performance, leadership behaviour and mental well-being. As a Focus Group member, in October 2022 Angelicoussis hosted the PnS Mediterranean Panel and participated in the development of content for the Partner Workshop. The themes were ’Context Drives Behaviour’ and ’How You Respond Matters’.
The discussions emphasised leadership behaviours and the fact that, since the workforce has different expectations and is more diverse than ever before, companies need fresh ideas and a new way of leading.
To increase public awareness about shipping issues, the Baltic and International Maritime Council (BIMCO) produced a film about industry decarbonisation titled ‘No Turning Back’. Footage of our Group’s fleet was included in the film, highlighting our alignment with the narrative that the industry is responsible for ensuring the sustainability of shipping. OCEAN
Drone delivery services are emerging as a complementary means of ship-to-shore deliveries, saving cost, time and emissions for essential tasks such as transporting documents and small urgent items needed on arrival.
Angelicoussis Group has taken the initiative to become part of the process and help test the technology in Singapore. To date, we have facilitated bunker sample collection from several of our fleet vessels passing through the port.
Since 2019, Angelicoussis Group has cooperated with experts from both the industry and academia on the development of the Human Element Maritime Enhancement Tool (H.EL.M.E.T.).
The tool offers an analytical approach based on a universal list of elements suitable for human-centred risk assessment in the fleet and ashore. The aim is to identify unsafe acts, conditions and practices that have escaped attention, helping to isolate and eliminate them by placing appropriate controls that contain risk to acceptable limits.
The Group co-hosted the 2022 Annual H.EL.M.E.T. Committee Meeting at our Athens office. The meeting aimed to enhance the H.EL.M.E.T. tool and establish an industry-wide commitment to a safe business culture.
Our Group proudly received the award for leading participant in the AMVER Program in 2022, with a total of 114 ships.
Among ship management companies based in Greece, our Group was also honoured with the Gold Fidelity Award for the highest number of vessels participating (1,010) in the AMVER Program over the past decade.
The AMVER (Automated Mutual-Assistance Vessel Rescue) system monitors ships, identifies possible problems and notifies vessels in the vicinity to approach and provide assistance. The Amver Awards Program was inaugurated in 1971 to recognise those vessels which regularly participate in the system.
GREEN4SEA TANKER OPERATOR AWARD
Maran Tankers Management Inc. received the 2022 GREEN4SEA Tanker Operator Award for taking steps to change the profile of its fleet with the latest order of dual-fuel tankers. Nineteen energy efficient eco-VLCCs have been delivered to the company, with orders for more during 2023.
TANKER OPERATOR AWARD
Maran Gas Maritime received the 2022 SAFETY4SEA Tanker Operator Award for placing the health and well-being of its employees among its top priorities. Caring for our people is one of our core values and we are fully committed to ensuring a safe working environment onboard and ashore.
Based on both internal and external stakeholder input, we have also identified key material topics and ESG priorities for each of the Group’s management companies
Marine Pollution Prevention
Environmental Protection
Energy Efficiency Management
Marine Pollution Prevention
Environmental Protection
Energy Efficiency Management
Environmental Protection
Marine Pollution Prevention
Energy Efficiency Management
Human Rights
Occupational Health & Safety
Equal Opportunities & Labour Conditions
Equal Opportunities & Labour Conditions
Human Rights
Occupational Health & Safety
Occupational Health & Safety
Human Rights
Equal Opportunities & Labour Conditions
Corporate Governance and Ethics
Regulatory and Legal Compliance
Operational Excellence & Assurance
Regulatory and Legal Compliance
Corporate Governance and Ethics
Operational Excellence & Assurance
Regulatory and Legal Compliance
Corporate Governance and Ethics Risk Management
The total waste generated reported hereby includes hazardous and non-hazardous materials.
Retention
All our EU and Ukrainian seafarers are covered by the Greek Collective Bargaining Agreement, while all our shore personnel based in Greece are covered by the National Collective Bargaining Agreement.
NOTES ON CONVERSION FACTORS AND ASSUMPTIONS
GHG emissions are calculated using default conversion factors for fuel consumption and grid emission factors for electricity consumption.
Fuel consumption:
Energy conversion factors – LCV (kJ/kg):
MDO/MGO – 42,700; HFO – 40,200; LFO – 41,200; LNG –48,000, Biofuel - 37200
1 TOE = 41.868 GJ
GHG emission factors for fuel consumption – As per IMO guidelines
Electricity consumption:
Energy conversion factors – 1 kWh to 0.0036 GJ
Emission factors for electricity consumption – Grid factors (kg CO2e/kWh): Greece - 0.33664, Singapore - 0.408, United Kingdom - 0.19338
Potential savings of paper usage:
The average pine tree has a height of 13.7 metres and a trunk diameter of 0.203 metres, which is enough to produce 10,000 sheets of paper.
DATA SOURCES USED:
For conversion factors:
IMO Guidelines, ISO standards for Marine Fuels, Association of Issuing Bodies (AIB) 2022, UK Govt – Defra/BEIS (2022), Energy Market Authority (EMA) of Singapore for electricity consumption.
For estimated paper savings:
1. Ribble Packaging Company, https://ribble-pack.co.uk/ blog/much-paper-comes-one-tree
2. U.S. Environmental Protection Agency, Office of Resource Conservation and Recovery, Documentation for Greenhouse Gas Emission and Energy Factors Used in the Waste Reduction Model (WARM) – Containers, Packaging, and Non-Durable Good Materials Chapters.
3. Resource Conservation and Recovery, Documentation for Greenhouse Gas Emission and Energy Factors Used in the Waste Reduction Model (WARM) – Containers, Packaging, and Non-Durable Good Materials Chapters
Greenhouse Gas Emissions
Gross global Scope 1 emissions
Discussion of long-term and short-term strategy or plan to manage Scope 1 emissions, emissions reduction targets, and an analysis of performance against those targets
(1) Total energy consumed, (2) percentage heavy fuel oil, (3) percentage renewable Gigajoules (GJ), Percentage (%)
Average Energy Efficiency Design Index (EEDI) for new ships Grams
Shipping duration in
Ecological Impacts
Percentage of fleet implementing ballast water (1) exchange and (2) treatment
(1) Number and (2) aggregate volume of spills and releases to the environment
(%)
Number, cubic metres (m³)
Number of calls at ports in countries that have the 20 lowest rankings in Transparency International’s Corruption Perception Index
49 out of 3,865 (1.27% of total port calls in 2022)
Abbreviation Description
AER Annual Efficiency Ratio
AMVER Automated Mutual-Assistance Vessel Rescue
BIMCO Baltic and International Maritime Council
CBM Cubic Metre
CEO Chief Executive Officer
DPA Dedicated Person Ashore
DWT Deadweight Tonnage
EAL Environmentally Acceptable Lubricants
ECAs Emission Control Areas
EEDI Energy Efficiency Design Index
ESG Environmental, Social & Governance
GHG Greenhouse Gas
GJ Gigajoule
GRI Global Reporting Initiative
HFO Heavy Fuel Oil
HQ Headquarters
HVAC Heating, ventilation, and air conditioning
IMO International Maritime Organization
ISO International Organization for Standardization
JHA Job Hazard Analysis
LED Light-emitting diode
LEED Leadership in Energy and Environmental Design
LFO Light Fuel Oil
LNG Liquefied Natural Gas
LTIR Lost Time Incident Rate
MARPOL International Convention for the Prevention of Pollution from Ships
MDM Maran Dry Management
MDO Marine Diesel Oil
MGM Maran Gas Management
MGO Marine Gas Oil
MTM Maran Tankers Management
NOx Nitrogen Oxides
PSSA Particularly Sensitive Sea Area
SASB Sustainability Accounting Standards Board
SMS Safety Management System
SOx Sulphur Oxides
TOE Tonne of Oil Equivalent
UN SDGs United Nations Sustainable Development Goals
VFD Variable Frequency Drive
VGP Vessel General Permit
WISTA Women's International Shipping & Trading Association
SUSTAINABILITY REPORT 2022