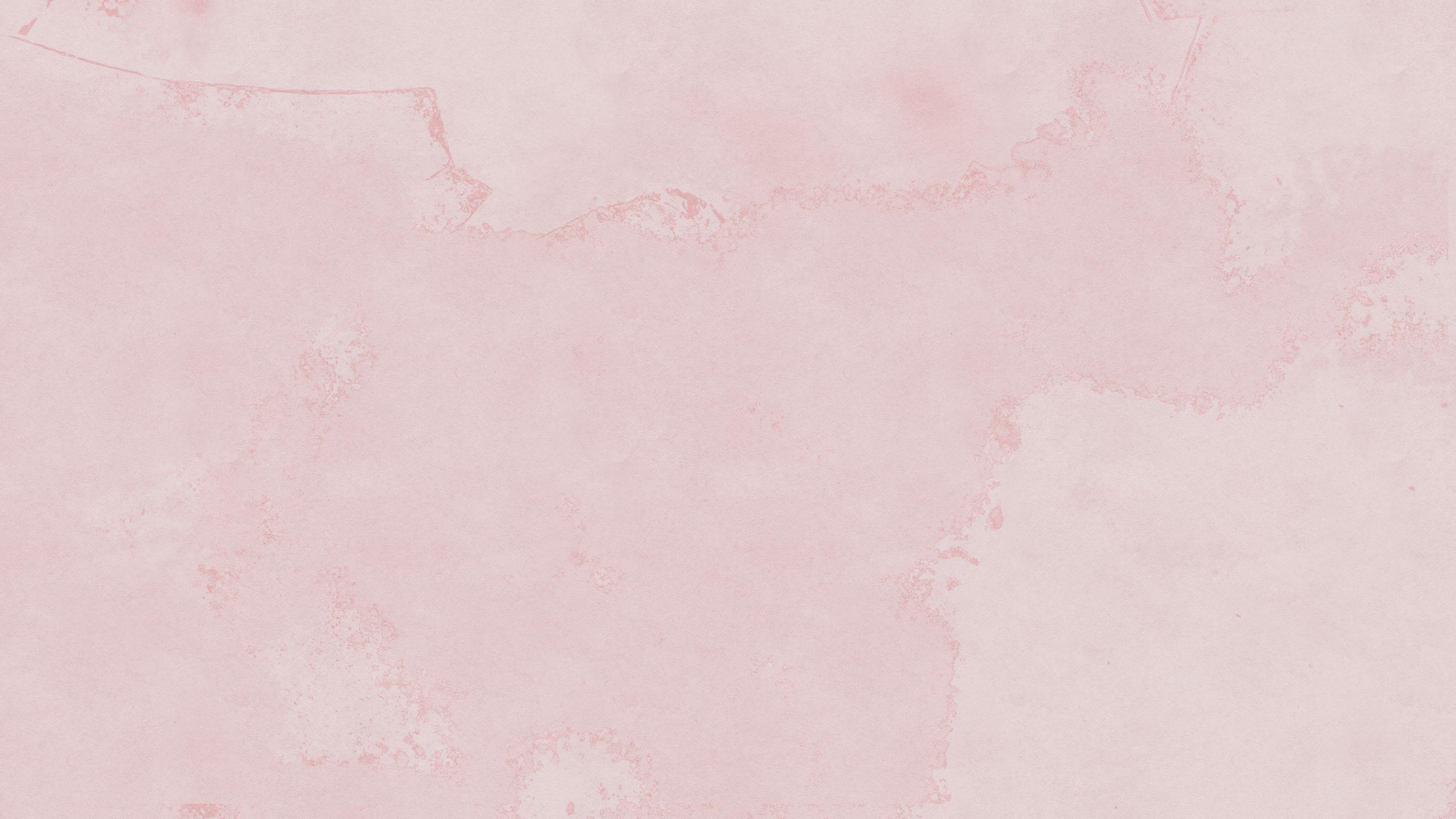
7 minute read
How to design for disassembly & repairability
You might wonder what a non-designer can tell you about design for repeatability and disassembly? I’m not a designer and I’m not a professional repairer, but I’ve been witnessing and helping to build repair events and activities for the last 10 years as part of the work of The Restart Project, and what we’ve seen time and time again is work that helps us make a better sense of the key priorities that should happen in this world. I like to say that we want to focus on a real and universal right to repair.
Right to repair is a phrase that’s been mentioned frequently over the last few years and has become a catchy term with policymakers around the world. I would say it’s quite contested territory, where many people are using it in almost greenwashing ways, so it’s important to be precise with its meaning. We cofounded a right to repair campaign in Europe, focusing on some key aspects extremely relevant for designers - and I don’t just mean people designing products, but also those designing services surrounding the product.
Advertisement
Products should be easy to disassemble without risk of breaking when it needs to be repaired. It’s also about fair access, ensuring that the spare parts and repair information are available and fairly priced.
A key reason people often choose not to repair a product is due to the exorbitant expense to do so. It’s also about making sure that people are properly informed as to what their options are when buying a product. This is not tackled by any of the legislation we’re looking into as campaigners, but we see that the appetite for this is massive - according to the 2020 Eurobarometer report, 8 out of 10 Europeans would prefer manufacturers to be required to make products easier to repair with approximately 85% of people in the UK thinking the same.
Part of our work has been on helping develop real data around the repair movement in America to make sense of the barriers people experience when trying to repair products. This can help acknowledge the massive impact that community repair can have towards change. We collected data and made it openly available, so for designers this could become a great resource on over 62,000 reported attempts to repair products. These attempts are by and large successful, with over 50% recorded as positive fixes at repair events, approximately a quarter that we deem repairable but can’t do at that moment, and about 20% is unrepairable and end of life.
There are a wide range of products that people wish to repair - It’s not just the obvious ones such as smartphones or laptops. While there’s some right to repair regulation coming up in different parts of the world for specific products, it’s a great challenge and opportunity for designers to think ahead of such legislative requirements because designers or manufacturers are in a position to think differently about the way things are done.
Zooming in on an example from our work analysing data from vacuum cleaners brought to repair events and the type of faults they show, we notice an importance for an extremely wide range of spare parts. This data was used in a consultation run by the European Commission considering whether a law requiring only three spare parts available is enough. The same data exists on our website for smartphones, reflecting work we’ve been doing recently in advocating for ambitious legislation on electronic products such as smartphones.
From our data, we notice the age of the products people wish to repair. We see many laptops are five and a half years old, with some much older. We observe that laptops and mobile phones are products with the shortest lives, but which people are extremely keen repair. Building for durability and repairability is essential, people really do care about the products they buy and want to keep them longer.
We asked repairers in our network to indicate the key barriers to repair for products they deemed unfixable. This is really crucial data to help us understand what can be done differently. First of all, spare parts clearly need to be available, but they should also not be too expensive otherwise people will simply not go for it. There is research from France pointing to the fact that people start doubting the benefits of repairing versus replacing at around 25-30% of the price point of a brand new product. There are questions around the value of products once they’re a bit older, but from an environmental perspective repairing continues to be the most important thing that anybody can do for the broadest range of products.
There are other important barriers, such as whether a product is built in a way that makes it near-impossible to open, or whether there’s not enough documentation on how to take the product apart for repair. Also, there is a lack of equipment for a product requiring proprietary devices that may be less common or unavailable.
In a way, we’re not telling a story that’s remarkable. It’s simple ideas such as not using adhesives, or making sure to colour code screws, and to document and provide openly accessible reliable repair information. But somehow there are other forces at play, whether it’s considerations from a business perspective or that manufacturers have difficulty moving from a linear to a circular approach.
It’s important to consider that we don’t just want some products to be repairable, but to make every type of product repairable, and some federal regulations are coming which will help find a way. The French repair score has helped some manufacturers to start some changes to ensure a slightly higher rating - so for example, you might see a company like Samsung potentially making available smartphone repair manuals in France, but not elsewhere.
Some companies are beginning to make available a level of spare parts, and they are making quite a bit of noise about doing so. But often, the way products are designed require replacing multiple parts in a bundled way. We recommend at a legislative level the un-bundling of spare parts, so a product is designed for modular replacement of only the smallest components to reduce cost and environmental impact.
Some manufacturers are actively increasing the barriers around, for example, the use of third party spare parts or the reuse of original parts from a secondhand device. This can be controlled through software which matches the serial number of a part with the serial number of the device. These practices might appear fringe, but there’s a risk manufacturers might reduce our ability to repair even while we are achieving an extra layer of right to repair, so I think it’s essential that designers think about how to make products self sufficient with minimal software involved, or at least to make the software easily patchable.
There are plenty of ways community repair initiatives - like our Restart Parties, the repair cafes around the world, or community fixing factories we’re currently testing - can encourage people to engage and come together in ways that are not competing with for the forprofit repair world, but attempting to give a second lease of life to things that would otherwise not find a suitable marketbased way of finding repair and reuse. There are multiple ways people attempt to extend the life of products designers create, and so all these possible players should be considered when developing a new product design.
Ugo Vallauri
Ugo is a co-founder and steering member of the European Right to Repair Campaign, a coalition pushing for the universal right to repair, meaning legislation at national and European level requiring manufacturers of all electrical and electronic products to design for repairability, while providing access to all independent repairers and the general public to repair manuals, affordable spare parts and long-term software and security updates.