
11 minute read
An architectural symbol of hospitality Katara Towers, a new luxury hotel complex, is taking shape on Qatar’s coast
AN ARCHITECTURAL SYMBOL OF HOSPITALITY
Timed to be ready for the 2022 FIFA World Cup, Katara Towers, a new luxury hotel complex is taking shape on Qatar’s coast.
Rising from the southernmost point of the 38 km² planned city of Lusail, Qatar, to just over 200 m high, the completed silhouette of Katara Towers will be a distinctive landmark for the nation. The crescent-like design of this future ‘hospitality icon of Qatar’ translates the country’s national identity into an architectural landmark. Symbolically intertwined with Qatar’s heritage, the iconic architectural design integrates the traditional scimitar swords from the national seal into a striking pair of symmetrically arched towers rising 36 storeys from the podium level to a height of 211 m. The vision for Katara Towers is to set new standards that go beyond the borders of the hospitality industry and provide an architectural landmark that is instantly recognised and understood right across the globe.
Katara Towers is a luxury hotel complex being developed in the harbour area of the planned city of Lusail. It will have apartments, offices, leisure facilities and restaurants, in addition to hotel accommodation.
The crossed swords on Qatar’s seal are being architecturally translated into a pair of arched towers, curving 36 storeys above the podium level to a height of 211 m.

The towers, scheduled for completion in May 2021, will boast two luxury hotels, plus apartments, leisure facilities, office space, shops and restaurants.
Rapid cycles with Doka climbing systems
The building is structurally divided into five areas and has a total of eight core walls. The central component of the project is the striking pair of symmetrically arched Towers 2&4. They cover an area of 2,315 m², rise 36 storeys into the sky, and the clear height of the slabs ranges from 4.45 m to 9.15 m. The four core walls 1&2 and 7&8 of the towers are rising upwards with the use of Doka automatic climbing formwork SKE50. For the crane-lifted core walls 3&4 and 5&6, the climbing formwork 150F and a shaft platform are being used to support the large-area formwork Top 50. According to the construction contractors, Hamad Bin Khalid Contracting Company, Doka has developed a reputation in Qatar for being able to provide formwork solutions that aid the delivery of the overall project. In this project, the SKE50 hydraulic climbing system and the delivery of the core walls have contributed to the project progressing faster than anticipated. The more complex storeys 1 to 15 were completed in a 14-day cycle, while storeys 15 to 36 were completed in eight days.
Complex slab surfaces completed quickly and cost-effectively
The biggest challenge arising from the structural design was to install the formwork on the protruding slabs while adhering to the construction schedule. Doka’s table lifting system TLS was used to accelerate the slab cycle, moving the Dokaflex tables in the two high-rise towers two storeys upwards. Due to the inclined façade of the building, the table lifting system had to be modified.

Doka’s SKE50 self-climbing system and the climbing formwork 150F were used to erect the core walls. A versatile approach was needed to manage the different slab configurations in each storey and the use of table lifting systems. To achieve the required flexibility in the table configuration, the 10,000 m2 of Dokaflex tables were delivered in customised sizes. Staxo 40 load-bearing towers were used to reach the 6.10 m high mezzanine level on the ground floor. D3 load-bearing towers supported the 22 m high Tower 3 Hall Area with 4.80 m deep transfer beams.
PROJECT DATA Project
Katara Towers
Location
Lusail City, Qatar
Type of structure
High-rise building, hotel complex
Height
211 m
Number of storeys
36
Client
Katara Hospitality
Construction contractor
Hamad Bin Khalid Contracting Company
Architect
Dar Al-Handasah
Start of construction
09/2018
Scheduled completion
05/2021
Contribution by Doka Products & Systems used
Self-climbing formwork SKE50 Climbing formwork 150F Large-area formwork Top 50, Dokaflex table Load-bearing towers d2, d3 and Staxo 40 Table lifting system TLS Universal support block Safety Net Fan
Services provided
Engineering Formwork Instructor Ready-to-use service Training
All images by Hamad Bin Khalid Contracting Company
LIEBHERR’S FIRST TELESCOPIC WHEEL LOADER
The new Liebherr L 509 Tele telescopic wheel loader is a multifunctional machine which combines the lift height and reach of a regular telescopic loader with the productive material handling capacity of a classic wheel loader - the benefits of two machine types in a single product. Developed on the basis of the Speeder L 509 stereoloader, this new telescopic wheel loader retains the proven stereo steering and can reach a top speed of 38 km/h as standard, thanks to the powerful hydrostatic travel drive. It also complies with the emission stage V/ Tier 4f specifications. The L 509 Tele has an extendable telescopic lift arm which can lift to a height of 4.8 m with a fork attachment. Thanks to the integrated z-bar kinematics, the telescopic lift arm enables the operator to load containers and lorries at great heights or stack loading material. When working with a fork attachment, no manual readjustment is necessary, because the Liebherr engineers have optimised the parallel movement during fork operation.
Increased versatility
The new telescopic lift arm offers advantages in terms of lifting height and reach. The Liebherr stereo steering system, the proven combination of articulated steering and the steered rear axle, ensures manoeuvrability. The combination of these technical solutions makes the new L 509 Tele invaluable in many applications including landscaping, municipal, snow clearing or recycling services. This flexible, versatile machine is user friendly so that even less-experienced machine operators can safely operate it on all types of construction sites. The L 509 Tele has a newly designed hydraulic quick coupler to switch between work tools. It ensures high wear and holding forces and, thanks to its compact design, offers a good view of the attachment being used. The connection dimensions are the same as the L 506 Compact - L 509 Stereo wheel loaders so that operators can use existing working tools for these machines on the L 509 Tele. This ensures year-round efficiency with attachments such as earth-moving and light material buckets, fork attachments, buckets with hydraulic clamp or snowploughs.
Comfortable operator's cab
The L 509 Tele has one of the most sizeable operator's cabs in its machine class. In addition to its generous space, the impressive, well laid out work station offers high visibility. A special feature is the height-adjustable 9-inch touch display which clearly shows all information. Liebherr has also modified some aspects of the standard stereoloader cab. For example it has a sunroof window so that the operator can clearly see the work tools and material being handled even when the telescopic lift arm is extended. The functions of the telescopic lift arm can be easily and intuitively operated using the Liebherr control lever integrated into the operator’s seat as standard. The mini-joystick on the control lever is used for retracting and extending the lift arm as well as controlling hydraulic work tools.
Intelligent overload warning system
Liebherr has equipped the L 509 Tele with an overload warning system as standard. This consists of a load torque limit and a load torque indicator on the display to continuously inform the machine operator about the bearing load situation and the stability of the telescopic wheel loader. In the critical area before the stability limit is reached, the overload warning system ensures that the movements of the working hydraulics are slowed down
to a standstill.
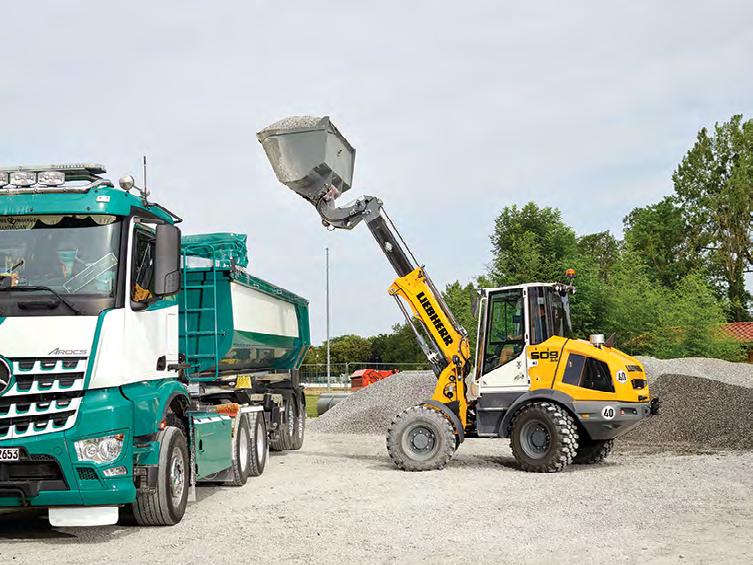
THE W 380 CRI COLD RECYCLER FROM WIRTGEN
With the new generation of cold recyclers, Wirtgen has developed a modern machine for cold in-place recycling. The tracked recyclers also deliver impressive results during full-depth recycling and high-performance milling.
Full-depth recycling in a single pass
The asphalt surface is removed, depending on the level of damage, by a recycling train operating across the entire width of the pavement in a single pass, mixed with binding agents on site, and then paved again immediately. The W 380 CRi can recycle the road surface to a depth of 300 mm, so it is also suitable for fulldepth recycling (FDR).
The W 380 CRi can also restore road surfaces beyond the available working widths of 3,200 mm, 3,500 mm and 3,800 mm. In this case, the recycler picks up the material that was pre-milled on the side by a cold milling machine and adds it to the mixing process. Thanks to a mixing capacity of 800 t/h in combination with rear loading onto a road paver with the appropriate stockpiling and paving screed, even very wide road surfaces can be rehabilitated in a single pass.
Performance as a milling machine
The W 380 CRi can also be used as high-performance milling machine. Thanks to its high engine power of 1,054 PS (EU Stage 5/US Tier 4f) and conveyor capacity, the W 380 CRi can manage removal work to a milling depth of 350 mm. This enables large-scale rehabilitation work to be carried out quickly, such as on motorways, runways at airports, or the removal of complete asphalt packages, as well as the homogenisation and granulation of damaged asphalt layers.
The Wirtgen tracked recycler W 380 CRi is an all-rounder for road rehabilitation, as it can perform cold in-place and full-depth recycling plus high-performance milling.

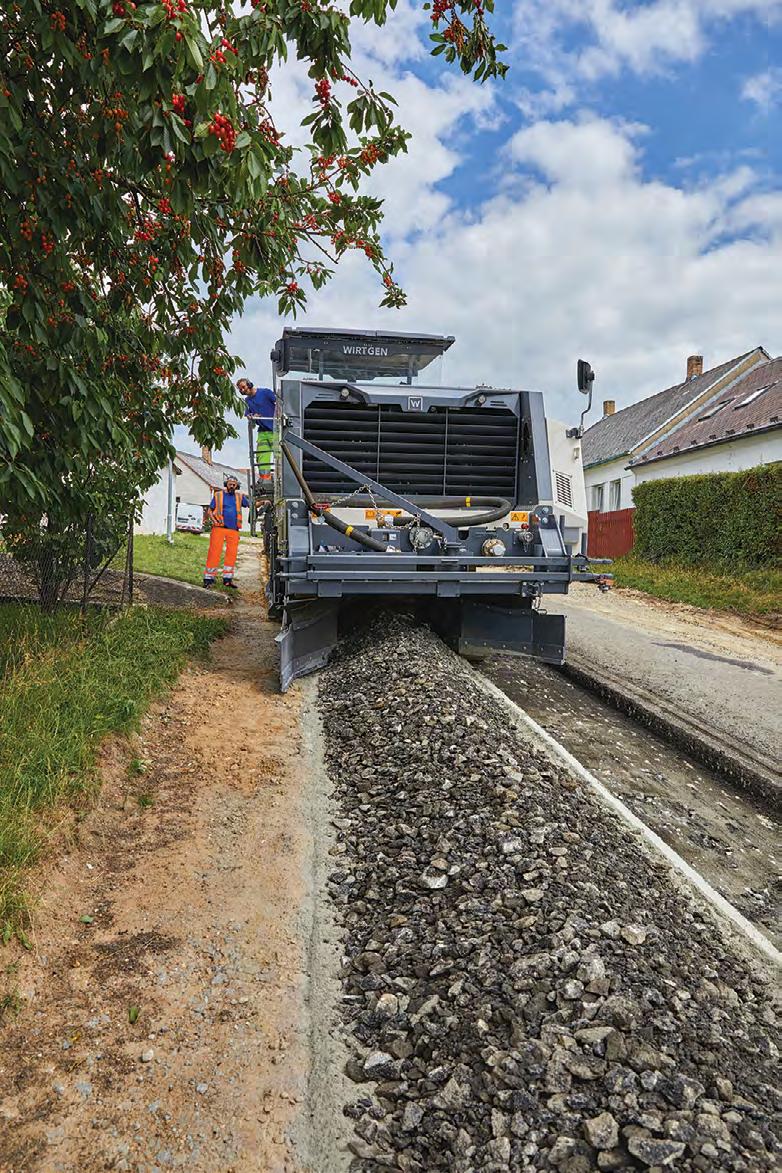
The new Mixokret M 740 Stage V seems to be quite similar to its predecessor on the outside, because the biggest changes were made under the hood which continues to open centrally. Here, a robust 3-cylinder turbo engine from Deutz now operates with an output of 36.4 KW, which is about 10% more powerful than its predecessor. The compressor from Rotocomp delivers an air capacity of up to 4.35 m³/min. Thanks to the sophisticated exhaust gas after-treatment with a diesel particle filter, the machine meets all requirements of the ‘Stage V’ emission standard without the use of urea - also known as AdBlue. This ensures that the machine can be operated in the EU and Switzerland in the future. Furthermore, laying screed in (partially) closed working areas such as underground car parks is also possible, thanks to the ‘TRGS 554’ conformity of the new Mixokret. In order to be able to adapt as flexibly as possible to the conditions on the construction site, the new Mixokret machine performance management allows the selection of five different delivery speeds. For example, fuel savings of up to 15% can be achieved by pumping in ECO Mode, with shorter hose lengths. For longer delivery distances, increasing the delivery speed to POWER mode ensures that the maximum delivery rate is realised. There are also innovations on the drive of the mixing mechanism of the new Mixokret which is now driven hydraulically. This means that the user can also run the mixing shaft in reverse at the push of a button to release a stuck mixture and it simplifies the cleaning of the mixing vessel. In addition, this drive offers safe overload protection for all mixing mechanism components, should a stone block the mixing mechanism, for example. The machine is operated via a clearly arranged control panel, which can still be found in its usual place. The central control element is now a robust keypad with intuitive user guidance, with which the machine can be operated even more easily and safely. The keypad is also resistant to all usual weather conditions, oils and chemicals. The appropriate use of a high-pressure cleaner cannot
ADVERTISERS’ INDEX
CMP Consultants Pte Ltd –––––––––––––––––––Page 09 Facilitators Network Singapore Pte Ltd –––––––Page 13 IES Chartered Engineer ––––––––––––Inside Front Cover IES Membership ––––––––––––––––––Inside Back Cover harm the keypad. The two pressure gauges allow the mixing unit and delivery pressure to be read at any time. Actuation of the emergency stop immediately stops the conveying operation and all moving components. The Auto-Power-Off function promises the prevention of an empty battery the next day. The standard function automatically disconnects all consumers from the battery, even if the main switch is not switched off at the end of work. This ensures smooth continuation of operation the following day and prevents unnecessary downtime due to discharged batteries. From now on, user-specific settings are made centrally via the operating elements of the display unit which is located in the control cabinet under the hood and is well protected. A practical feature here is that settings made by the user, such as the switch-off pressure or the mixing time setting, are automatically saved. In this way, all settings are retained even after the machine is restarted the next day. A further innovation is the batch counter, which can be compared with the odometer in the on-board computer of a car. If it is activated, it counts the batches until it is reset. This number can be used, for example, to roughly estimate the amount of material processed.

The new Mixokret machine is able to adapt flexibly to the conditions on
construction sites. IES Railway Systems Handbook ––––Outside Back Cover Pedro Investigations & ––––––––––––––––––––Security Services Pte Ltd Page 11
Singapore Institute of Technology ––––––––Page 14 & 15 Singapore University of Social Sciences –––––––Page 01

