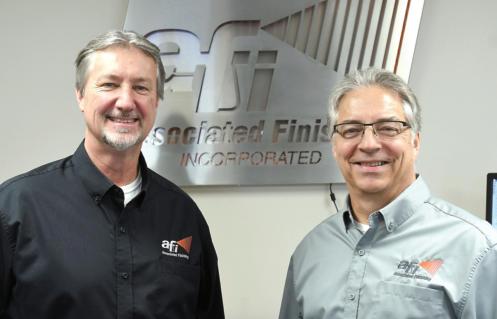
4 minute read
Covering it all
from Mnvalley 2 18
Ted Schreyer, left, and John Kapsner own Associated Finishing in Mankato.
Company finishes everything from tiny NFL screens to ag equipment
Advertisement
By Dan Greenwood | Photos by Pat Christman
John Kapsner and Ted Schreyer knew a long time The partnership between Schreyer and Kapsner ago that they would become the owners of was sewn in 1988. Kapsner was a banker for Associated
Associated Finishing, a Mankato-based powder Finishing when previous owner Chuck Klammer and coating company. In 2009, that Schreyer met with him over lunch. dream would become reality. Powder coating protects Profile Klammer asked him business full time. to join the everything from machinery to “At the end of the conversation I household items as an alternative to paint, without the said I would do that on one condition. Someday I use of solvents. Schreyer says they grind plastic up to would have an opportunity to buy the company,” the consistency of talcum powder and pump it through Kapsner said. “Ted chuckled and he says ‘well that’s a hose. why I’m here. Eventually I want to buy the company.’”
He likens the process to rubbing a balloon and With that, the three shook hands. When they sticking it to a wall. bought the business in 2009 they had 20 years
“There’s an electrical charge put on the powder and working together. Kapsner had the financing that makes the powder stick to the grounded part,” experience while Schreyer knew the production side. explains Schreyer. “So you may have negatively “Our strengths complimented each other and the charged powder, a positive ground on your part and partnership has worked out real well,” Schreyer said. the opposites attract so the powder will stick to it. You bake that approximately 400 degrees and then it melts Expanding their base and makes a real hard coating, much harder than While the company has largely focused on powder typical paints.” coating agricultural machinery, an economic slump in 16 • FEBRUARY 2018 • MN Valley Business

Dale Taylor hangs parts for painting. Right: Bill Neegaard paints parts in a booth.
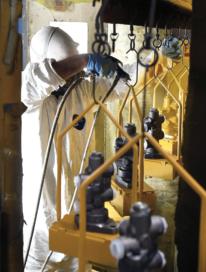
farming in 2008 meant they would need to expand their customer base because companies such as John Deere, Bobcat and Caterpillar had fewer orders to fill. Since then they’ve expanded to accommodate several industries. The company’s longevity combined with a solid sales and marketing team allowed them to find new clients with relative ease.
“Associated finishing has been around since 1954,” Kapsner said. “In the Midwest there’s very few people that don’t know who we are. So then it’s just a matter of targeting the market you need to go to and what our niche is. We started identifying some industries we wanted to go after.”
When they bought the company in 2009, the military already had large orders for them to fill.
“We worked pretty much 24/7 for almost 90 days,” Kapsner said. “Back in Iraq, roadside bombs were going off and wounding our forces. A company developed a kit that attached to those vehicles. They were armor coated. We powder coated all that with chemical agent resistant coatings.”
Their client base would also expand to medical and dental equipment, aerospace and computers. They even powder coat equipment for professional football announcers.
“If you watch football on Sunday, you see the head coaches on the sidelines; they have their little microphones and on the end of their microphones there’s a little screen,” Kapsner said. “One of our customers manufactures that and we powder coat those all for the NFL.”
Even though Associated Finishing have expanded their clientele, they are preparing for an uptake in manufacturing for agriculture. So much so that they opened a facility in Litchfield.
“What we do in Mankato is a lot of small parts, high volume,” Schreyer said. “We have conveyers that are doing thousands of parts at a time. But we didn’t have a good way to do small quantities, large parts.”
He says the majority of what they are doing in Mankato fits in your hand. The new facility in Litchfield accommodates the larger farming equipment, along with semi-trailers and dump truck boxes. To do that requires a 12 foot wide by 40 foot long oven. It takes about 20 minutes to complete the heating process.
Their workforce is now made up of more than 100 people as they continue to grow and expand. One of the first decisions the new owners made back in 2009 was to take a collaborative approach with the employees.
“Prior to us running the company we were kind of a top/ down management style company,” Kapsner said. “When we bought the company we made the announcement that we were changing to a bottom up (company).”
The way they see it, the management works for the people on the floor. They also promote from within and include their employees in decision making. Schreyer says it’s that kind of inclusive work environment that translates to the longevity of employees. Many have worked there for 15 to 20 years and more. It doesn’t hurt that they have firsthand experience with the powder coating process.
“It helped that I worked right on the floor, John did too. We’re not afraid to get our fingernails dirty,” Schreyer said. “Our whole management staff is that way too. There are people like me that worked their way through school. John and I are very open with employees that we want everybody to succeed. If we can do well, we’re all going to do well.” MV