
4 minute read
The surge in industrial robot orders
by iThink Media
A RECORD YEAR

A report by the Association for Advancing Automation (A3) has revealed that more robots joined the US workforce last year than ever before, taking on jobs such as plucking bottles and cans from conveyor belts at trash recycling plants, and putting small consumer goods into cardboard boxes at ecommerce warehouses.
nd it looks like still more robots will come aboard in 2022, limiting the sting of labour whilst maximising the talents of current employees. According to McKinsey, annual industrial robot installations are estimated to increase to 600,000 this year after already growing to 450,000 since 2015.
A report by the Association for Advancing Automation (A3) has revealed that more robots joined the US workforce last year than ever before, taking on jobs such as plucking bottles and cans from conveyor belts at trash recycling plants, and putting small consumer goods into cardboard boxes at ecommerce warehouses.
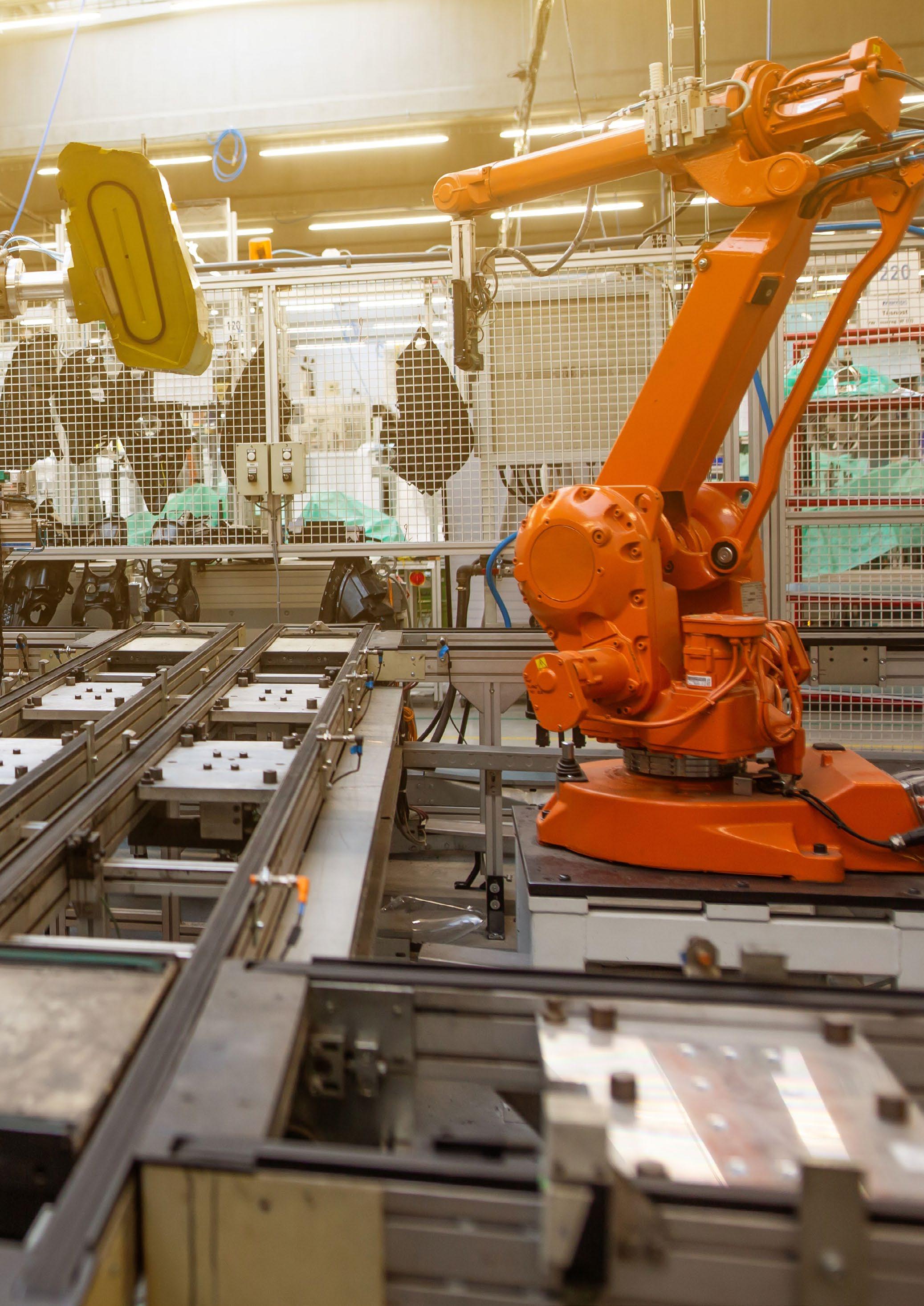
Companies across North America laid out more than $2 billion for almost 40,000 robots in 2021. Robots went to work in a growing number of industries, expanding well beyond their historic surge in the automotive sector.
Jeff Burnstein, President of A3, said, “More industries
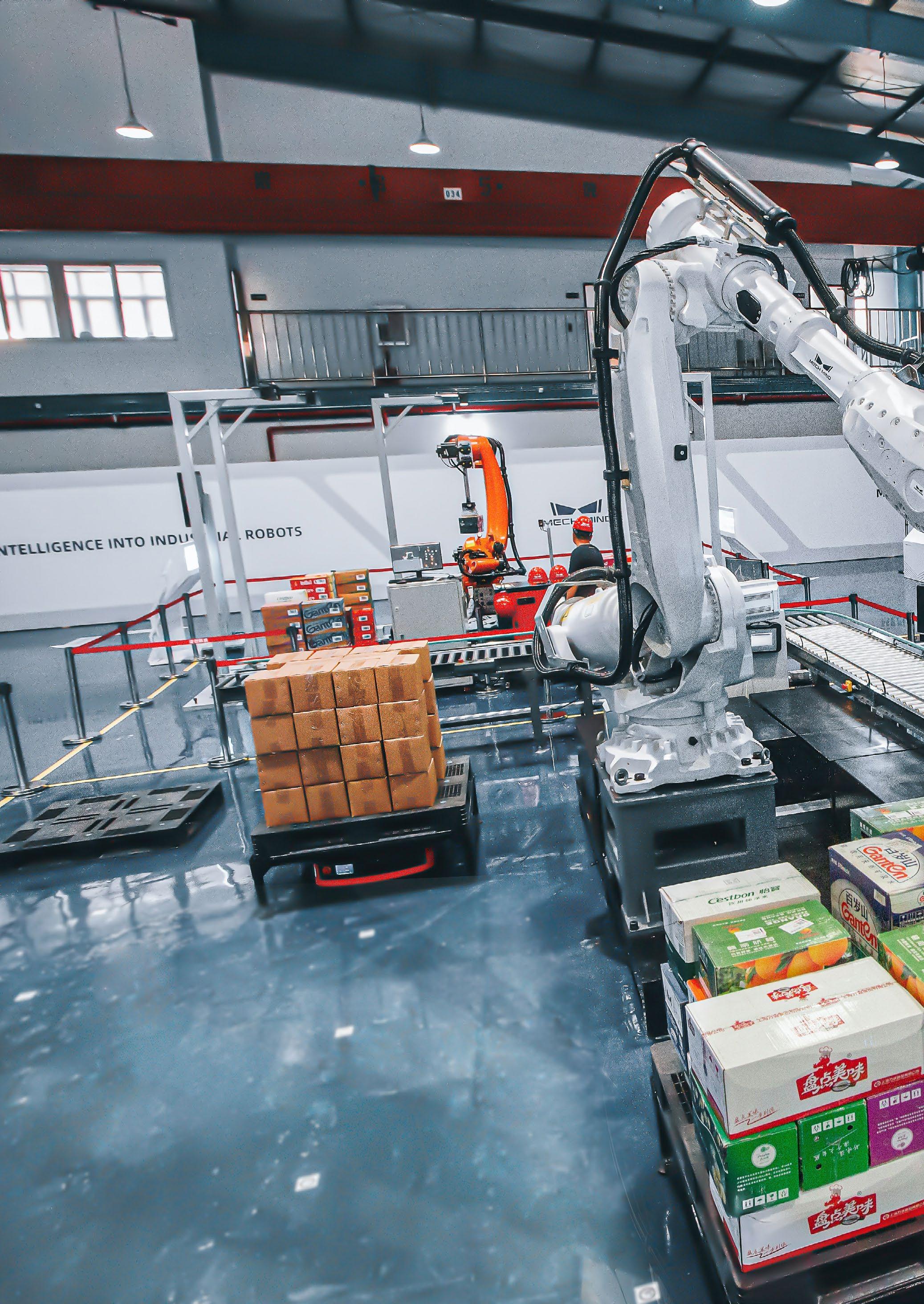
recognised that robotics could help reverse productivity declines and fill repetitive jobs human workers don’t want. It is no longer a choice whether to deploy robots and automation. It’s now an absolute imperative. As we’ve long believed – and users continue to confirm – robots help companies compete, ultimately creating more jobs to handle their growth.”
DCL Logistics in Fremont, California, started installing robots on ecommerce fulfilment lines during the pandemic. Brian Tu, Chief Revenue Officer, said, “With human labour, what they produce depends on if they’re hungry or are they tired or have they had their coffee.”
Many companies are also tapping into automation in answer to the greater operational strain on their warehouses. FedEx, for example, accelerated its robotics investments to better handle the variety of packages streaming through its sorting facilities.
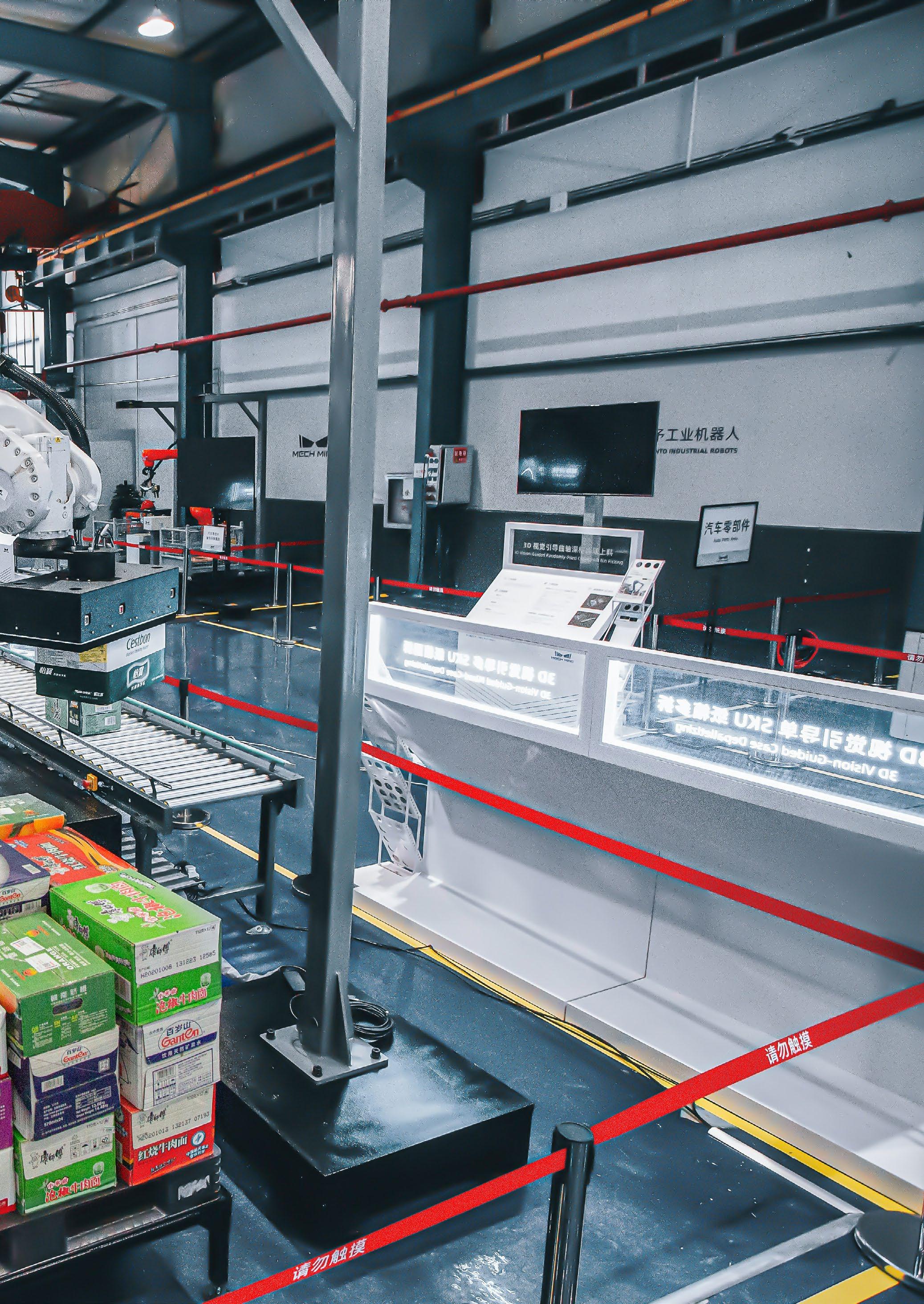
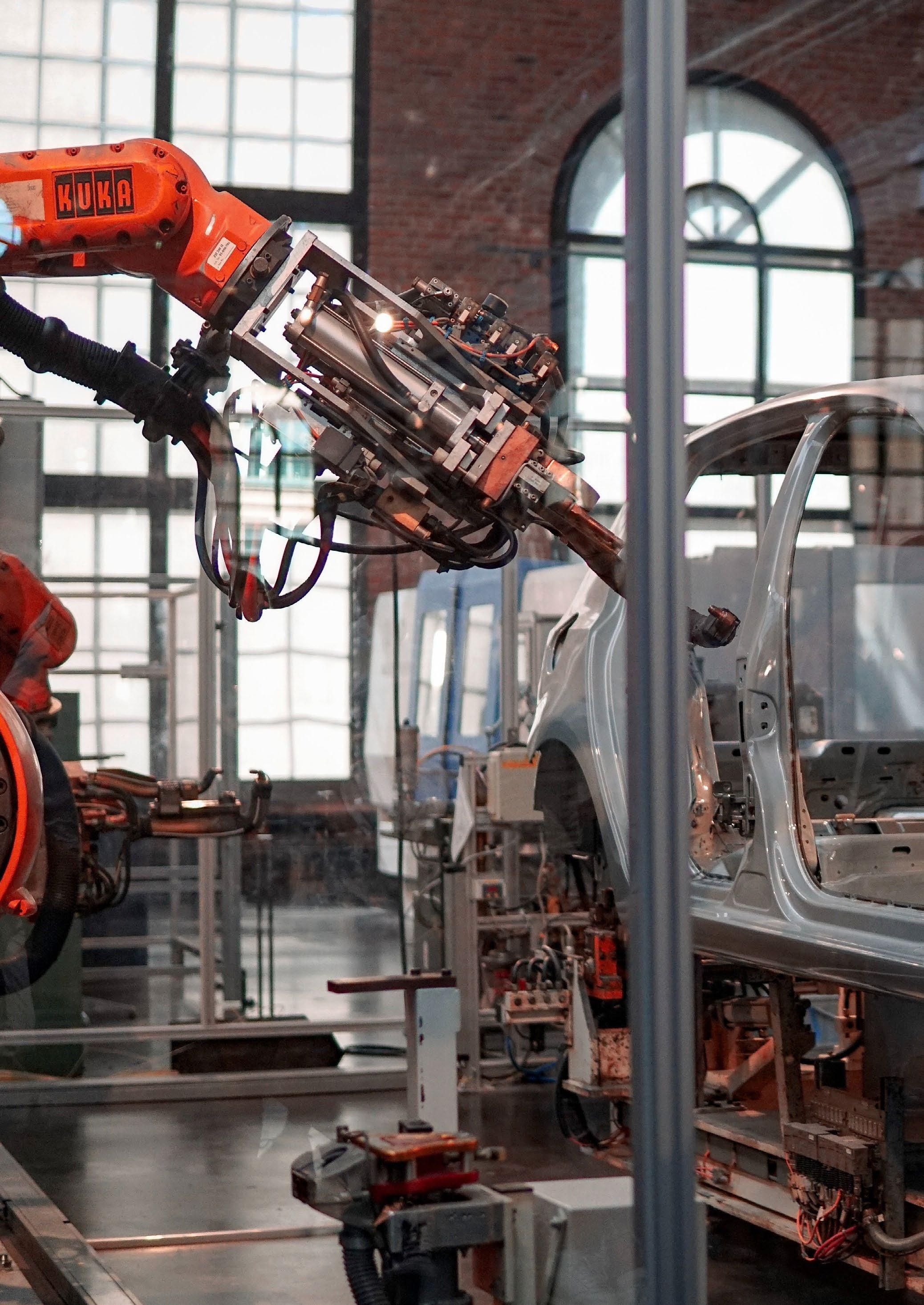
Factories and other industrial users ordered 28 per cent more robots last year than the previous year, according to the report. The previous annual record for robot orders was set in 2017 – when North American companies ordered 34,904 robots valued at $1.9 billion.
Some of the fastest growth in robot orders is in the metals and food and consumer goods industries. Ecommerce is another fast growth sector. At DCL, which has five US fulfilment centres and will soon open a sixth, the lines that have robots can operate with fewer people – and yet produce 200 per cent more. Tu added, “We still have employees working around the robots, but we can reduce labour by roughly half.” There is also a growing trend for a new breed of ‘cobots’, designed to work alongside humans on assembly lines. Universal Robots, a unit of Massachusetts-based Teradyne Inc (TER.O), specialises in cobots. Joe Campbell, a Senior Manager for Applications Development, said, “The number one driver for automation is the labour shortage in manufacturing.”
But, cobots are making inroads into many other industries that long resisted automation. In construction, for instance, Universal Robots has sold robot arms to a firm that uses them to install drywall in large building projects, a notoriously labour-intensive process.

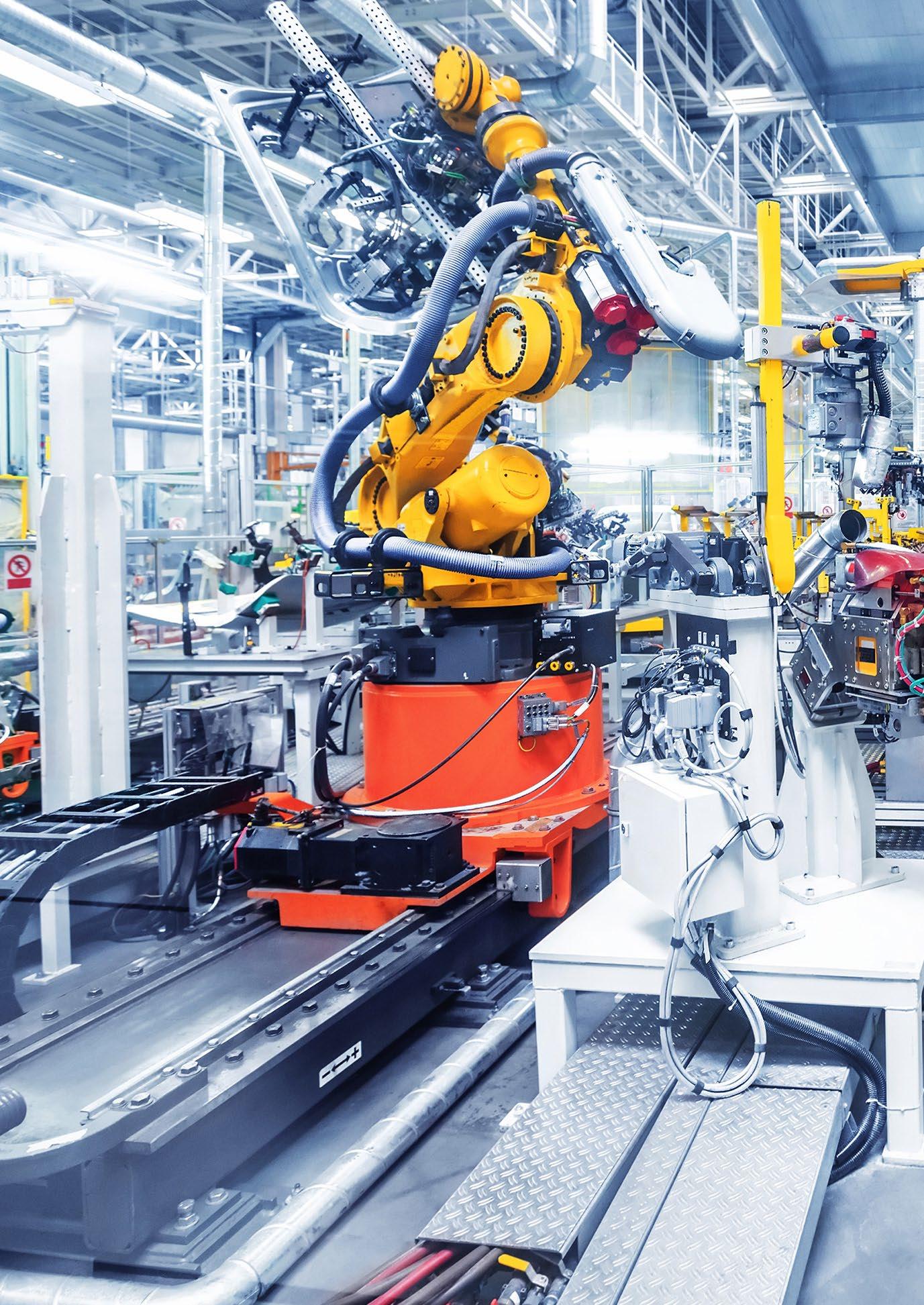
Auto plants are also finding new uses for cobots. Stellantis N.V., the Dutch automotive manufacturer, is now using Universal’s cobots in the final assembly area of its factory in Turin, Italy, to help produce the new Fiat 500 electric vehicle. The arms are attached to a framework that moves over the car, where they locate and fasten nuts. As a wider range of firms dives deeper into new uses of automation, they will need to navigate how much the technologies will impact their current workforce. Change management is more important than the technology itself, according to Ted Dengel, FedEx Ground Managing Director of Operations Technology and Innovation. He said, “It's really about just being
open and communicating very clearly out of the gates, ‘This is what this machine is going to do, and here's how you're going to interface with it’. We do a lot of time training and making sure they’re very comfortable with it before we start it. There's no mystery behind it.”

Meanwhile, a new generation of rentable robots has made the costs feasible for facilities to make a measured entry into automation. Joe Montano, President and CEO of engineered polymer and adhesive products maker, Delphon, added, “By hiring robots to operate machines for pad printing and component cleaning, we were able to redeploy eight operators to other jobs and see a $70,000 return on investment in less than a year.”