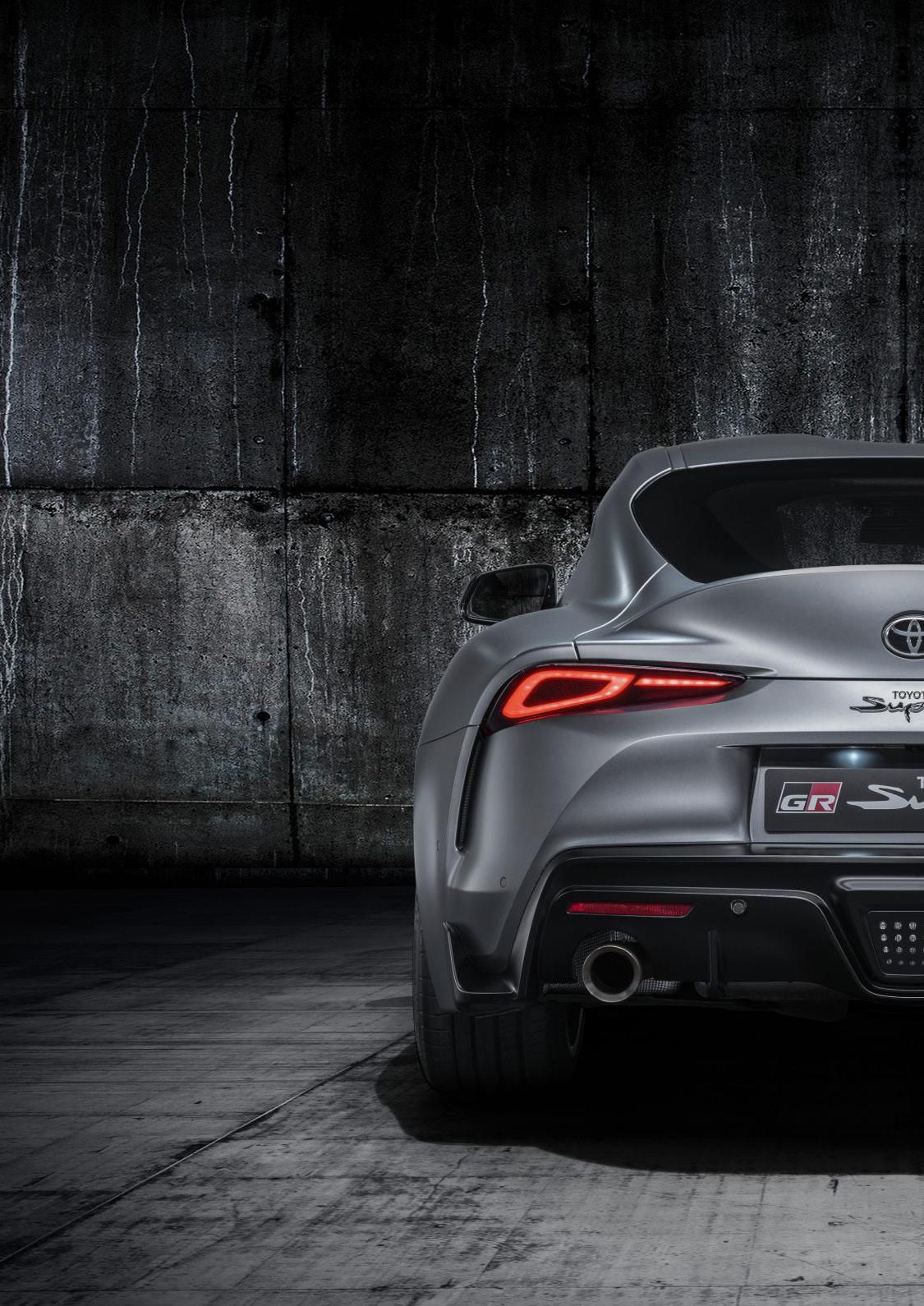
5 minute read
Are lean manufacturing principles outdated?
THE IMPACT OF DISRUPTION
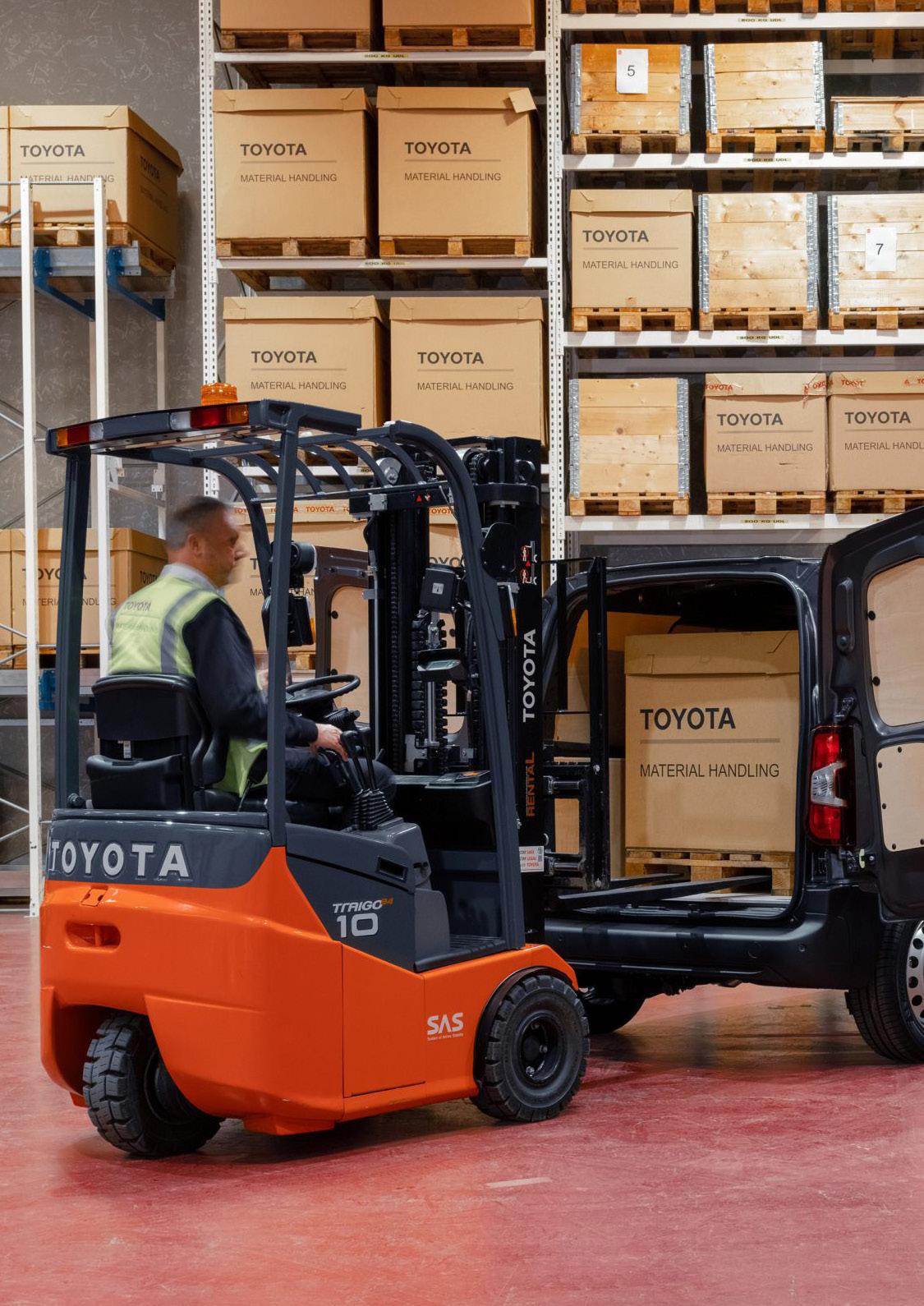
EVERY SUPPLY CHAIN HAS FACED SOME KIND OF DISRUPTION IN RECENT YEARS, BUT WHAT HAS BEEN THE IMPACT ON THOSE SYSTEMS THAT ADOPT LEAN MANUFACTURING PRINCIPLES? TOYOTA’S SUPPLY CHAIN MODEL IS A GOOD EXAMPLE.
oyota’s supply chain model is a good example. Toyota developed its Toyota Production System in the 1940s, which quickly gained global influence, as other companies adopted this methodology. There are two core concepts to this system. One of which is ‘jidoka’, a form of intelligent automation where equipment is programmed to come to a halt when an issue arises to stop faulty products from being produced. The second concept is known as ‘Just-in-Time’. This is where each step within the manufacturing process only produces what’s needed for the next one.
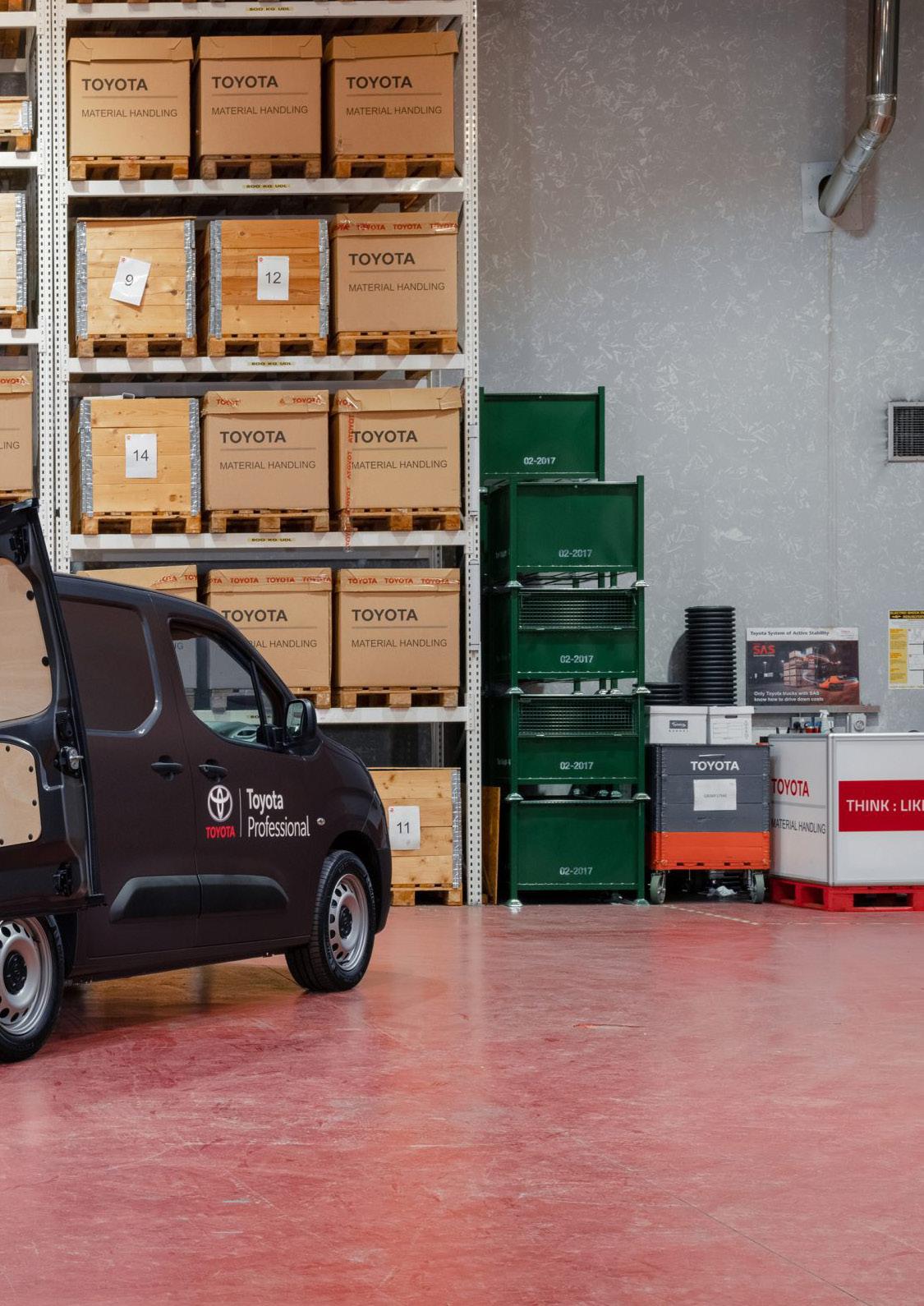
Businesses adopting this model try to structure supply lines so they receive goods just as they need them, cutting down on storage costs and making sure that money is not tied up in inventory. The overall philosophy is to eliminate waste during manufacturing and aim to work in the most efficient way possible, building on continuous improvement over the years.
The downside of this system is its reliance on strong supply chains. The whole system can easily collapse if one link breaks. That is basically what happened for several companies during the pandemic when businesses’ highly complex global supply chains broke. The inefficient, outdated and siloed systems that many organisations had relied on for decades broke down because they were not able to adapt to such a rapidly changing environment.

So, is the Toyota way still the right way for a company that
has grown so much in the past decade? For a company that relies on this production process technique, the big question right now is how do you stay nimble and efficient to keep consumer prices competitive, yet still be able to deal with unforeseen events? Several schools of thought have emerged following recent events:
• The automaker has remained lean while its volume has increased dramatically since the days when the company’s principles and methods were established. Thus, Toyota can no longer maintain sufficient support and quality control, especially as it adds new suppliers around the world. Yet it still governs the design of key components.
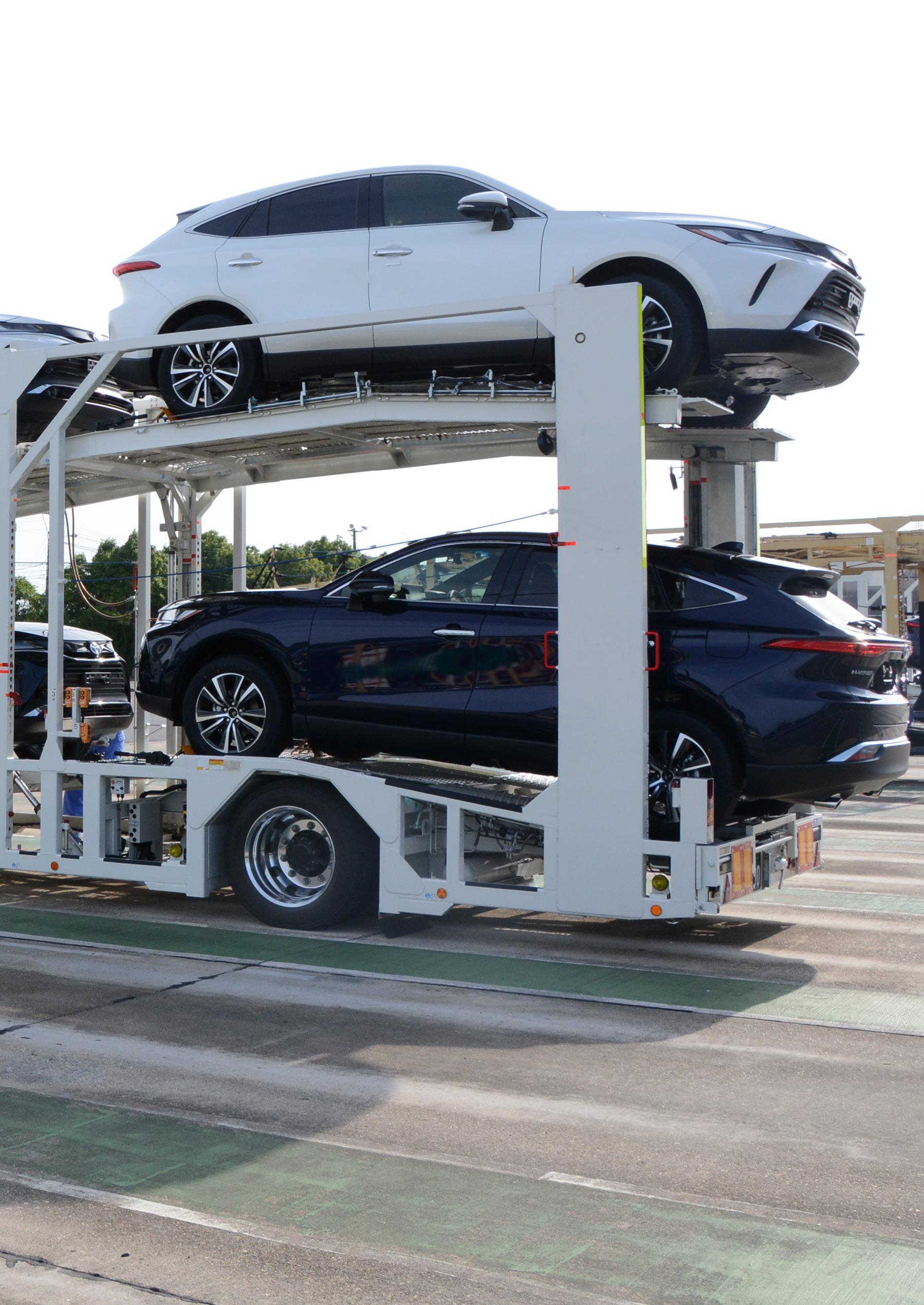
• Toyota’s streamlined supply base is at fault. By relying so heavily on sole suppliers and using parts across multiple
platforms and vehicles, the automaker increases its risks.
• Toyota’s methods have minimised the damage. This enabled a relatively quick fix to its recent sticky pedal problem because of the automaker’s inherent ability to work closely with suppliers on engineering solutions.
The methodology has been revised and improved upon over the years. Toyota implemented a strategy in 2011 following the devastating earthquake and tsunami, which split the procurement of their supplies from three different sources. This meant that should one part of their
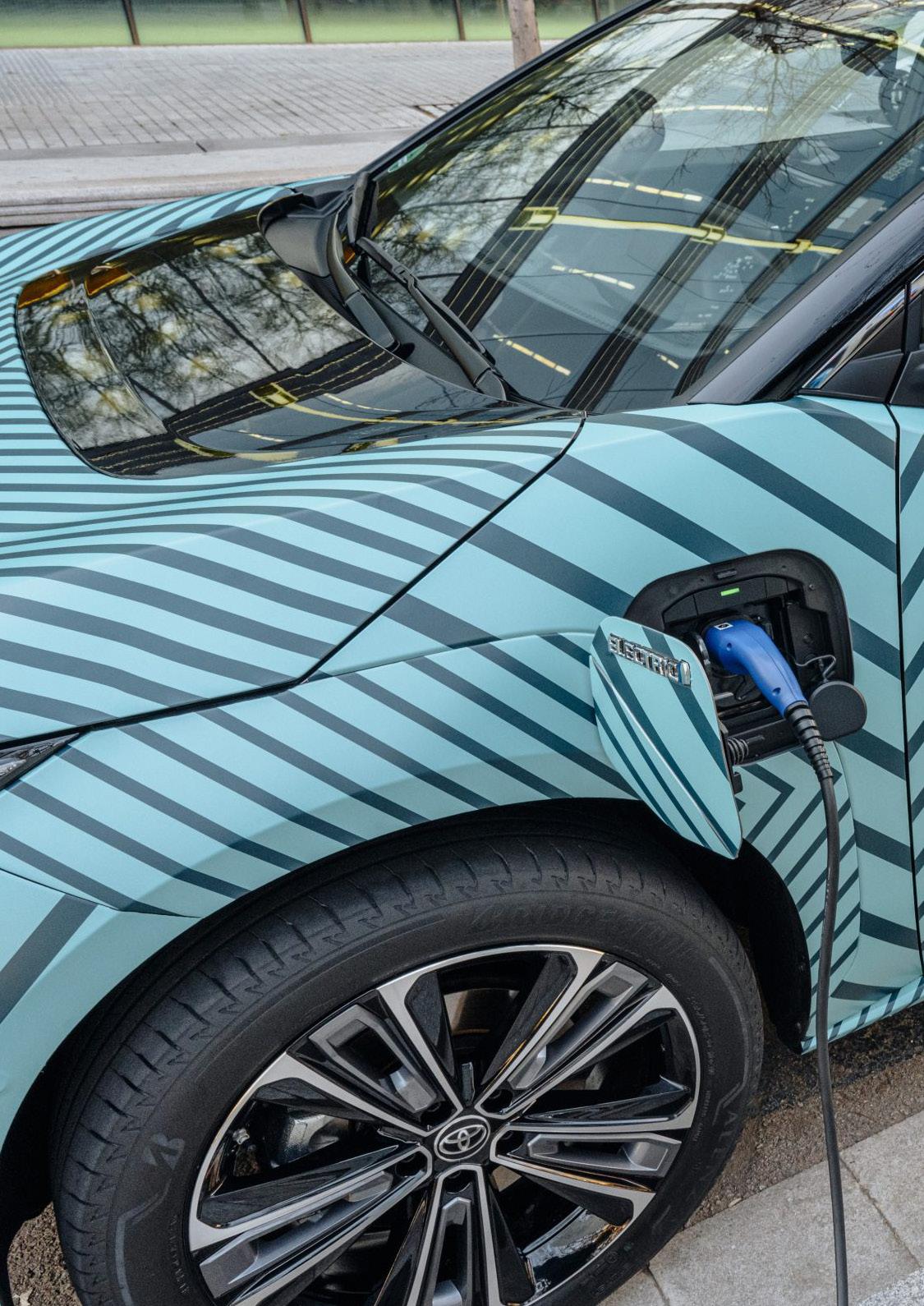
Leila Aridi Afas,
Director of Global Policy
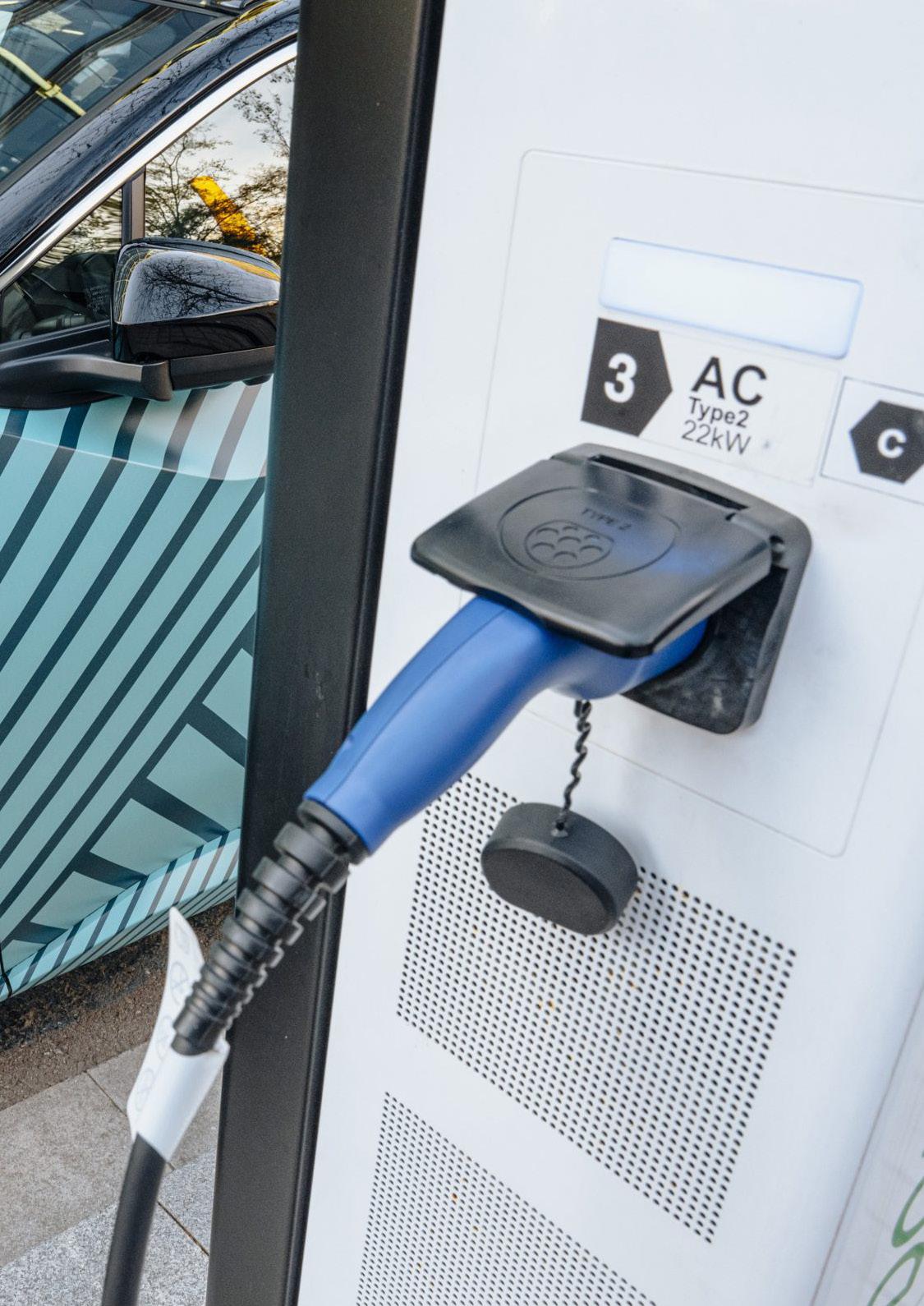
supply chain fall, they would have two back-up options already in place.
When a problem arises, the first step is to gather information, so during Covid, a team in the company worked around the clock to map out the entire supply chain – not just one supply chain for the company, but chains for nearly every single part it takes to make nearly every single one of their automobiles. They identified about 1,400 critical parts (out of roughly 30,000 parts) that had relatively long lead times. If any one of those 1,400 critical parts were not available, the entire production line could be forced to a halt. Leila Aridi Afas, Director of Global Policy at Toyota Motor North America, said, “The team identified their suppliers, their suppliers’ suppliers, and their suppliers’ suppliers’ suppliers.”
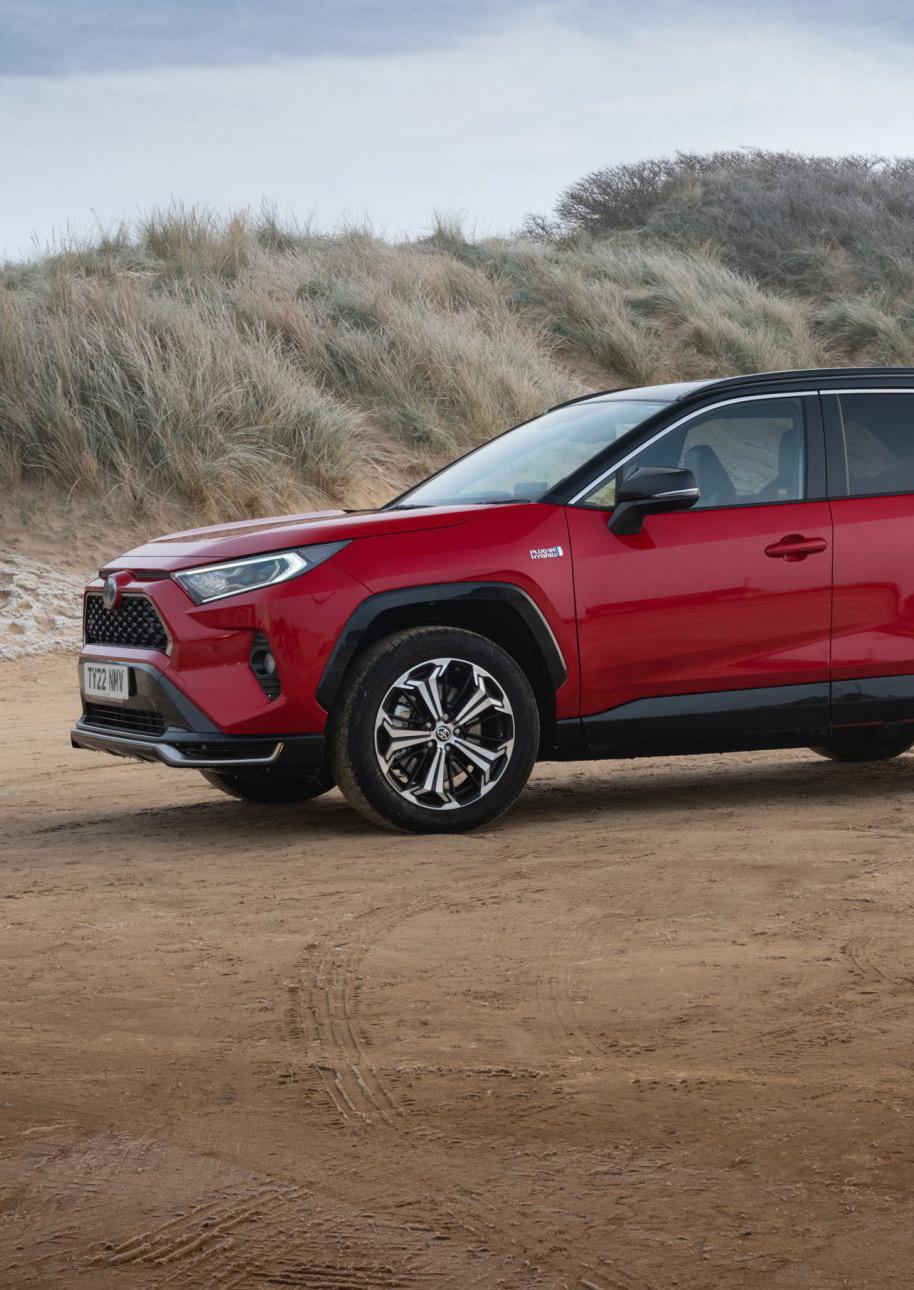
Over time, Toyota worked to increase inventory and manage lead times for these critical parts. Leila described several ways in which Toyota worked to safeguard its supply of critical parts:
• A team within the company worked to diversify its presence in multiple geographic regions while ensuring that it could procure the necessary parts to keep building vehicles if one particular region were unable to produce. • Toyota began standardising parts across different vehicle models. Now, if one supplier shuts down for any reason, another plant is able to increase production of the standardised part to meet demand.
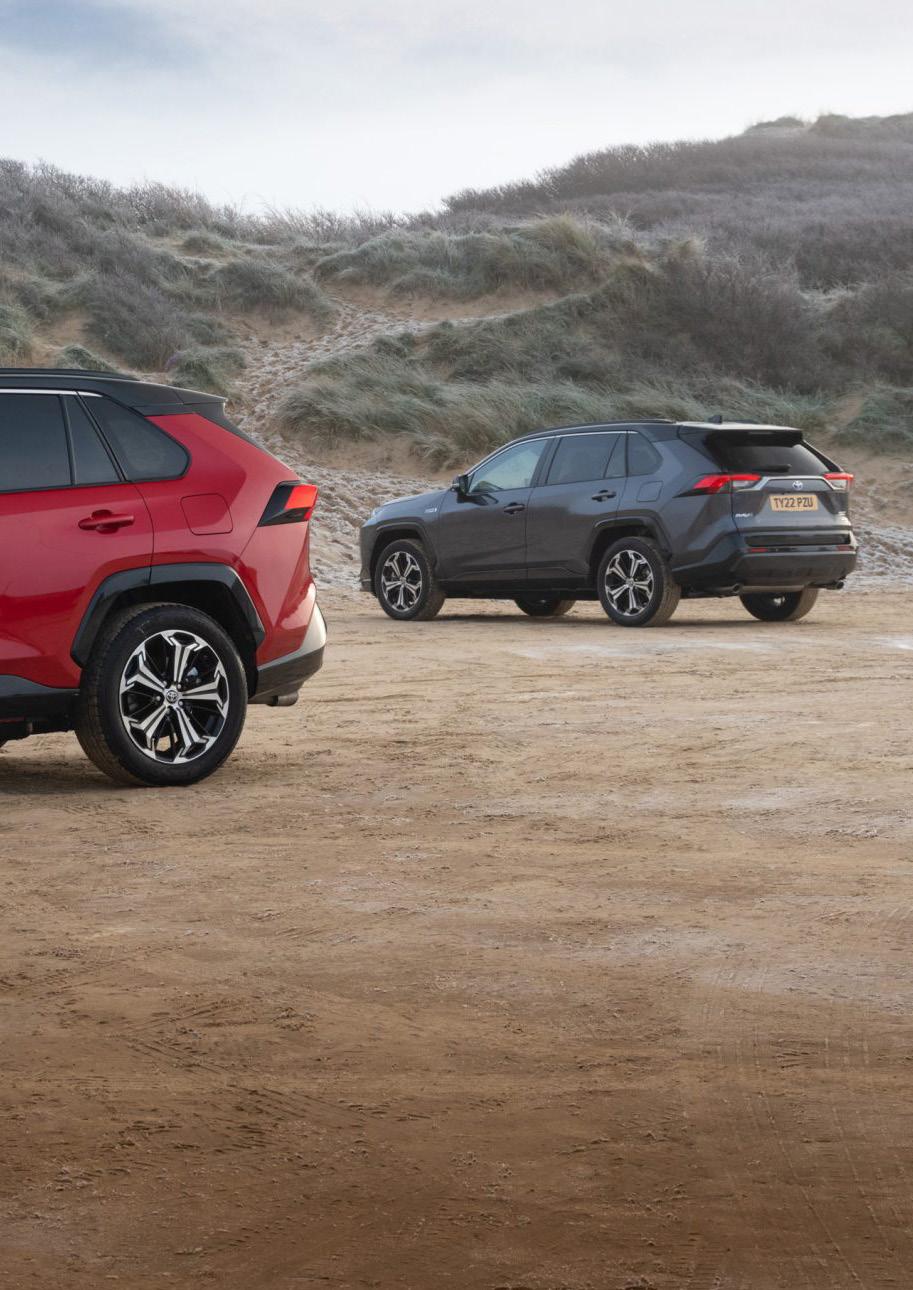
• When standardisation wasn’t an option (as is the case for the 1,400+ critical parts Leila’s team identified), Toyota increased inventory to maintain a supply in case of emergencies.
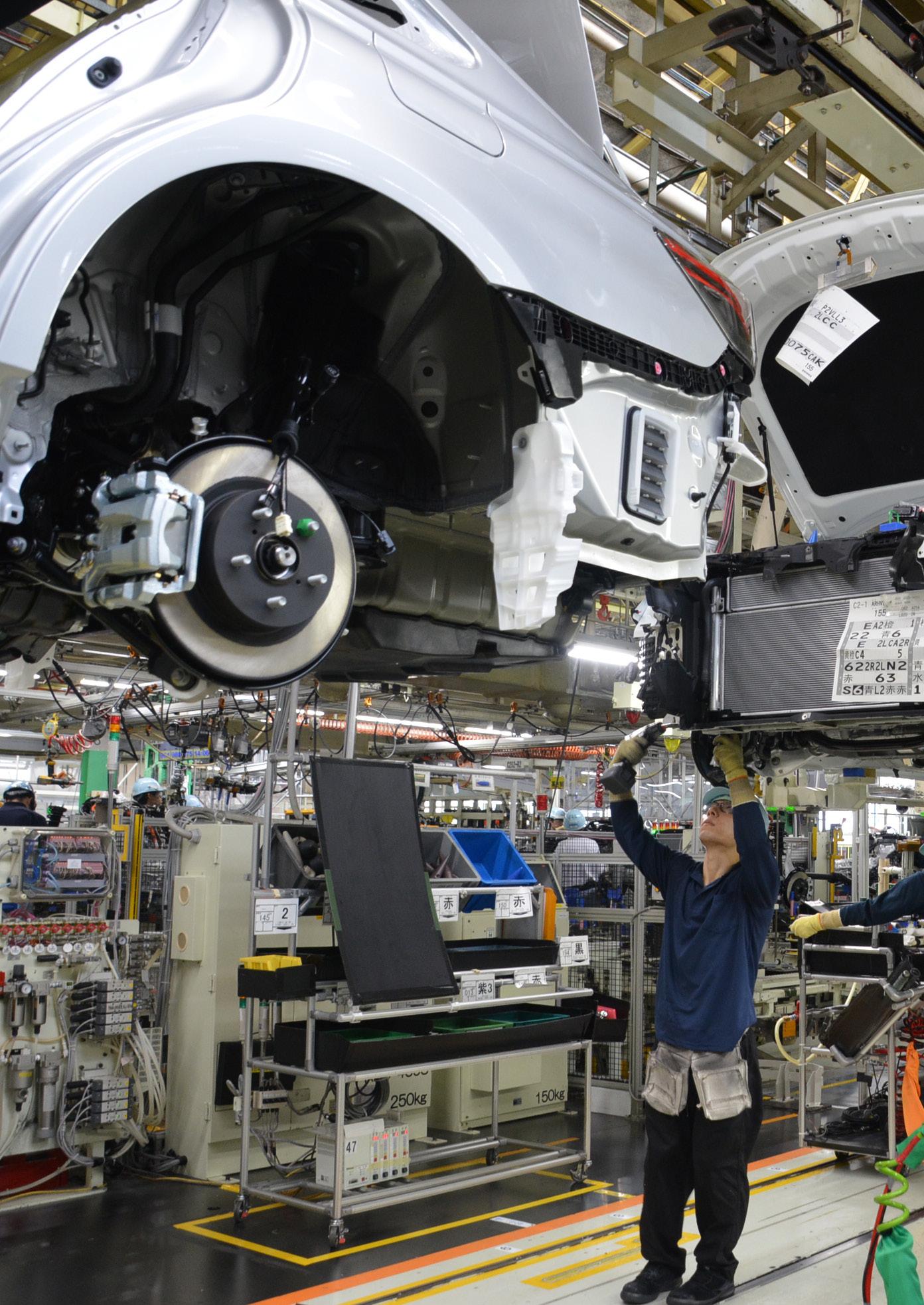
Leila identified several takeaways from Toyota’s experiences in dealing with supply chain problems. She explained, “In my view, the most important part is the trust and respect between Toyota and our suppliers, who are truly partners.”
She also emphasised the importance of staying in close and constant communication with suppliers. She added, “It’s crucial that the information is always up-to-date. You never know when a crisis will strike.”
A supply chain management system that is flexible under unforeseen circumstances is key, with contingency plans in place should the unexpected happen. With the current level of global disruption supply chains are facing, even the best plans might go awry, but being able to analyse and learn from it will be the difference between companies that survive and those that fail. In the short term, it is about evaluating the data, seeing what is possible, and understanding how it can be achieved.
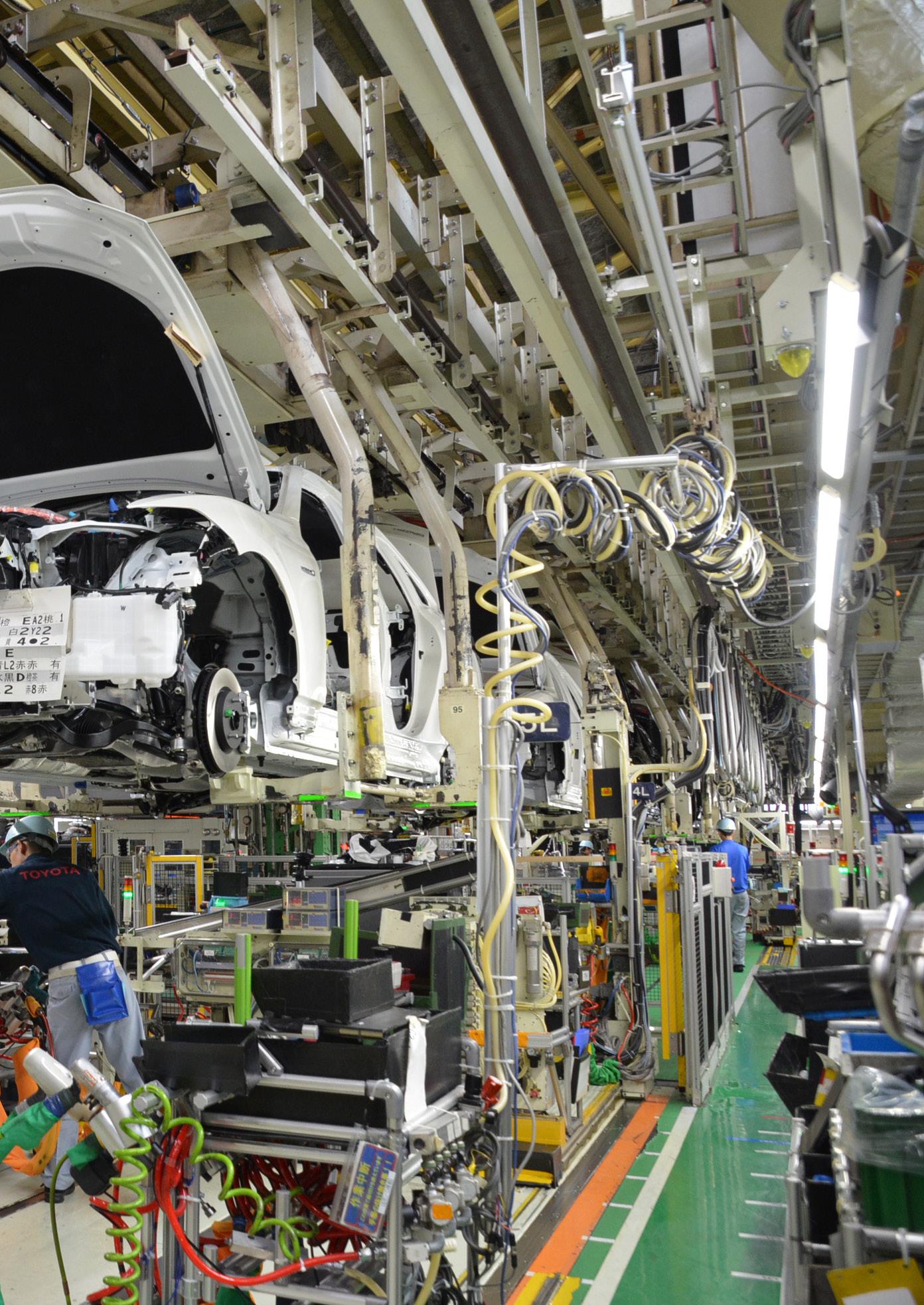
Sources: www.discoursemagazine.com www.just-auto.com