A People-Sensitive Supply Chain Transformation
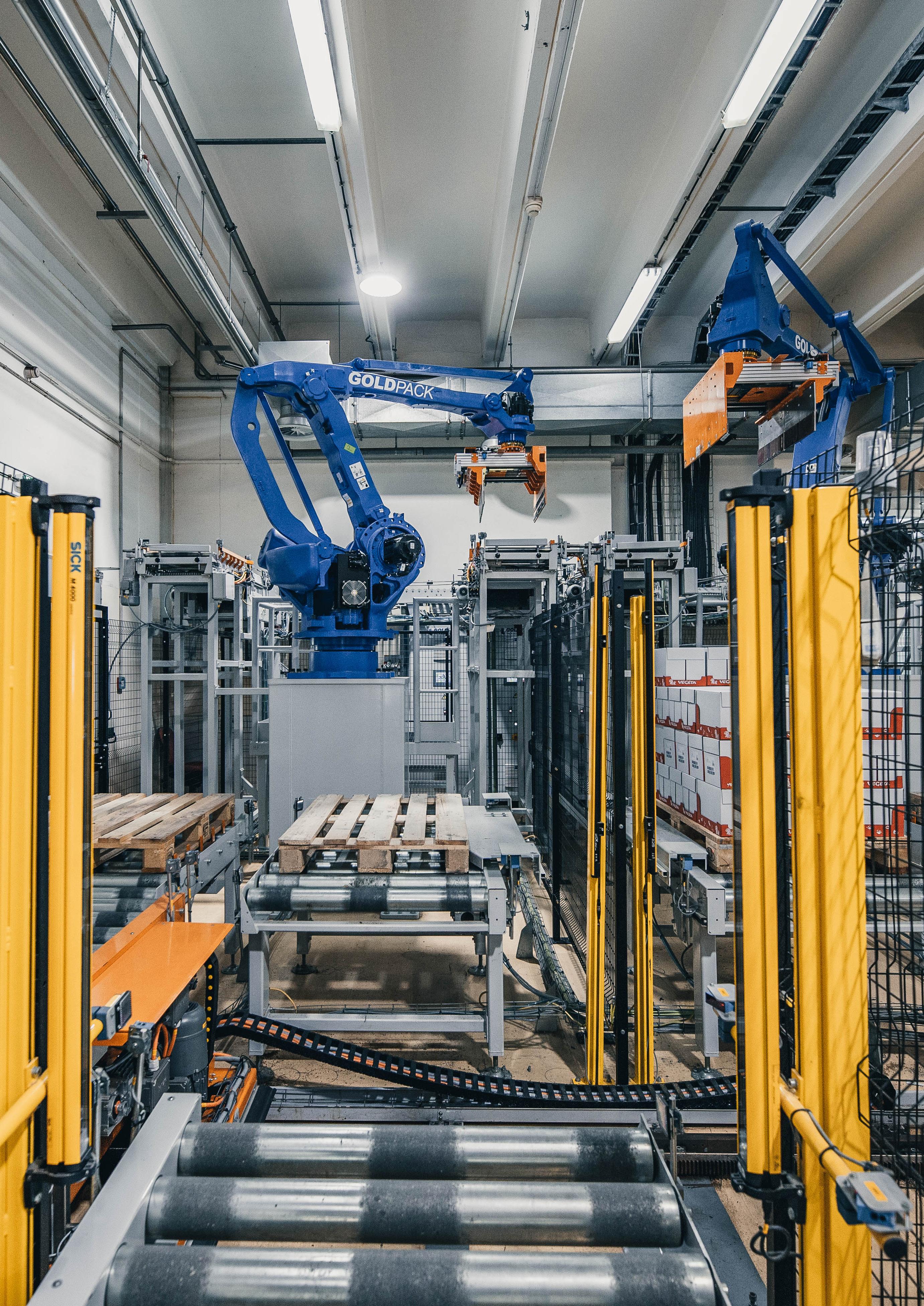
Manuel Brkovic, Supply Chain Director at Podravka, shares his company’s supply chain story in the year that marks its 75-year anniversary.
Podravka is one of the largest food manufacturers in Southeast, Central and Eastern Europe and is proud to be celebrating its 75th anniversary this year.
s well as the food processing side of the business, the group has a pharmaceutical company, which has been in existence for 50 years. There are over 1,800 different products in Podravka’s impressive portfolio, with around 6,500 employees. The company has 17 production sites in four countries, serves over 70 markets and its revenue in 2021 was around 600 million euros.
Manuel Brkovic, Podravka’s Supply Chain Director, tells us more; “If you look at the Podravka supply chain itself, we have 17 manufacturing sites and over 1,000 SAP warehouse/ storage locations all over the world.
When you consider the size of our market, which is the whole world, you can understand the complexity we are facing. Our long history and the fact that our region is still in a transition to a developed democracy and modern productive society means our supply chain transformation has brought about big changes.”
Manuel talks about three main pillars of Podravka’s transformation journey – lean excellence, digitalisation, and modernisation/automation, and all of them surrounded by a green/sustainability agenda. He continues, “Such a large company started facing the global problem of finding the right employees, but also finding enough of them to cover our growth. Additionally, with the development of Croatia, labour costs are going up, which impact our bottom line. About 20 years ago, Croatia offered cheap labour, great knowledge, and people that knew how to make high-quality products, and this was easily bringing jobs from more developed countries. We are now finding that we are losing workers because salaries are going up in other industries, but the food industry is not closely following this trend, and competition is also getting stronger and stronger.”
The aforementioned pillars were chosen to remove non-productive work from employees, enabling them to focus on producing the value. Manuel says, “With lean and digitalisation, data is available on screen and paperwork can be removed. People can lose up to two hours per day setting up the machines, preventing them from producing real value in this
time. The automation of production machines enables them to cut down on the time they spend on mundane tasks and be more productive. If a robot can do something, why shouldn’t it?”
These changes ultimately serve the buyers i.e. the retail stores. Manuel explains, “Our production needs to be planned and runs at one to one
and a half months, so that orders can be delivered 24 to 48 hours after they are placed. We need to be able to forecast to prevent shelves from being empty because the production time is too long to produce an order straight after it is placed. That is why we introduced sales and operations planning and stock control. To be such a big manufacturer, you need stock
availability, which means hundreds of millions of euros in stock. It can put a great strain on the business without proper planning.”
Better planning and stock control also amplify a sustainability element. Manuel elaborates, “If a machine is 10 per cent more
“If a machine is 10 per cent more productive in a specific timeframe, you are using less energy to get the job done”
productive in a specific timeframe, you are using less energy to get the job done. Less paperwork is also better for the environment, and if the machine has to be higher in energy class, it will make the same product with less energy consumed. This is what we call our green strategy for the supply chain transformation.”
What challenges has Manuel faced in implementing his supply chain strategy? He answers, “Lean is a modern method that is still not completely understood in this area of the world. Technology and digitalisation face the same problem because the workers in Podravka are typically 45 to 50 years old. They are not used
“Digitalisation and technology are running through Podravka, age of the company, it is always with a human approach. Industry 5.0 is about, putting the people at the centre”
to touchscreens. But, if we work across the three pillars with better planning in place, we can slowly and continuously approach training our people to be more productive.”
This challenge in changing the mindset is perhaps the biggest obstacle for Manuel and his team. He explains, “With a 75year old company and employees who have been here for over 25 years, the new technology, new methodology and new ideas can be frightening. The operations and technology team is socially-sensitive and fast to explain that the people will be doing much more valuable work.
Instead of noticing only when there is a mistake, they can now see how they can save money and improve the productivity, so they are understanding that they are increasing their value, together with increasing the company value. It is easy to transform through technology, but you need to have the people on board. Our sociallysensitive approach show the
Podravka, but due to the approach. This is exactly what
employees how they can use their time for much better things.”
Manuel says Podravka’s biggest achievement in its 75-year history is the fact that it is still going strong. He continues, “After switching from communism and socialism to the free market, too many companies in our region disappeared from the market. With the growing competition and the big global players cornering the market, it is a huge achievement to be still here.”
to implement SAP, and with the help of our partner Atos, one of the first regional companies to use BW (Business Warehouse) that connects and shows all important financial and business data. We are further developing our technology to switch to the newest SAP software available, and Atos is continuing to support us on the reporting side.
“The founder of Culmena was one of the first people in Croatia to start talking about lean. We brought
Podravka’s strategy for the future involves collaboration with key partners such as SAP (Atos) and Culmena. Manuel highlights, “Our partners are the core of our transformation. Our ERP system connects all the dots in our company. Without it, the supply chain, sales, finance, and all other departments would have their own software and not be able to see the entire impact on business. Podravka was the first company in Croatia
Culmena here to Podravka to help bring that knowledge. The project is all about trying to teach our people how to think lean. Culmena understands the mentality of the Croatian people, so we are able to take a psychological approach to slowly convincing them that these changes are for the better.”
Leveraging the opportunities of Podravka’s transformation will be Manuel’s next job. He says, “We
“Podravka was the first company in Croatia to implement SAP, and with the help of our partner Atos, one of the first regional companies to use BW (Business Warehouse) that connects and shows all important financial and business data”
Logistics and supply chain management are a finely integrated art. Recent disruptions have made it even more important to have accurate, real-time information about every part of your supply and delivery chain — including your warehouses.
Intelligent, automated warehouse management solutions from Atos and supported by SAP provide a unified, integrated way to monitor and control your critical warehouse operations. We integrate consumption predictions for superior stockkeeping, plus track-and-trace on large warehouses and yards, delivering:
• Optimised control of day-to-day operations
• Easy storage and retrieval, even on very large sites
• Real-time updates and visibility
• Full traceability of all operations
Learn
have just finished our production digitalisation project in our pilot factory, so we will now need to add 16 factories in the next two years to make all of Podravka’s manufacturing part digitalised. Every department will be able to read the same information from the same dashboard, which will be automatic. Modernisation is going on all the time. We are building new factories and renewing the machines. With the global energy crisis, being green and sustainable is so important.
We have one of the biggest solar plants in the country. Our five-year plan is to have 90 to 95 per cent of our energy produced in-house
by solar and biomass in our main production zone.”
The vision for continuous improvement means Manuel is always looking at what is coming next. He concludes, “Digitalisation and technology are running through Podravka, but due to the age of the company, it is always
with a human approach. This is exactly what Industry 5.0 is about, putting the people at the centre. We have to slowly show them that technology can improve their work and their lives, which is not so easy. It is something you have to do continuously.”
For further information on Podravka, visit www.podravka.com
“Culmena understands the mentality of the Croatian people, so we are able to take a psychological approach to slowly convincing them that these changes are for the better”