Experiencing
End2End Digital Supply Chains with SAP and their Partners
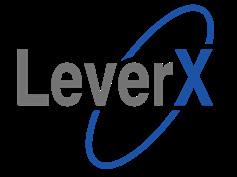
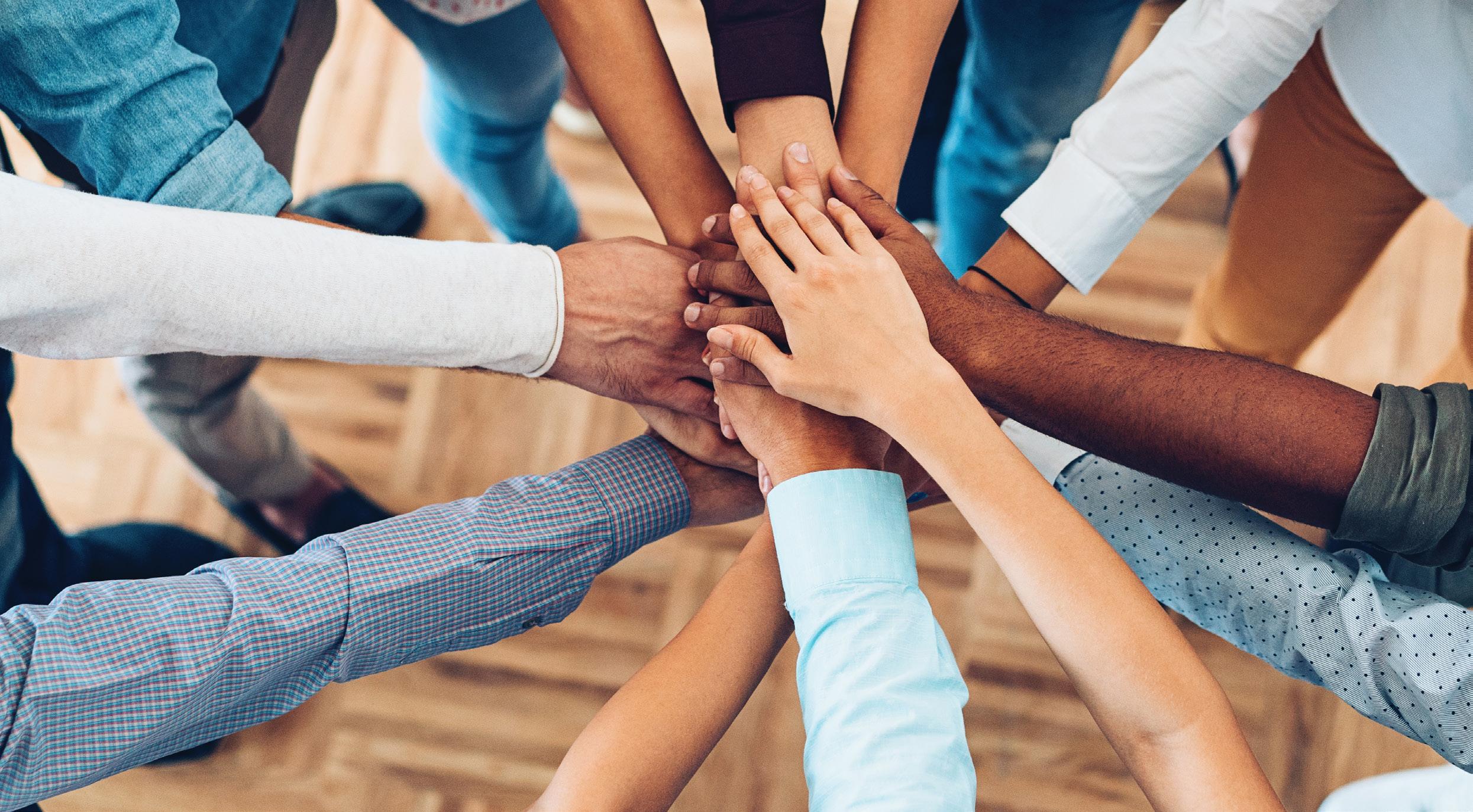
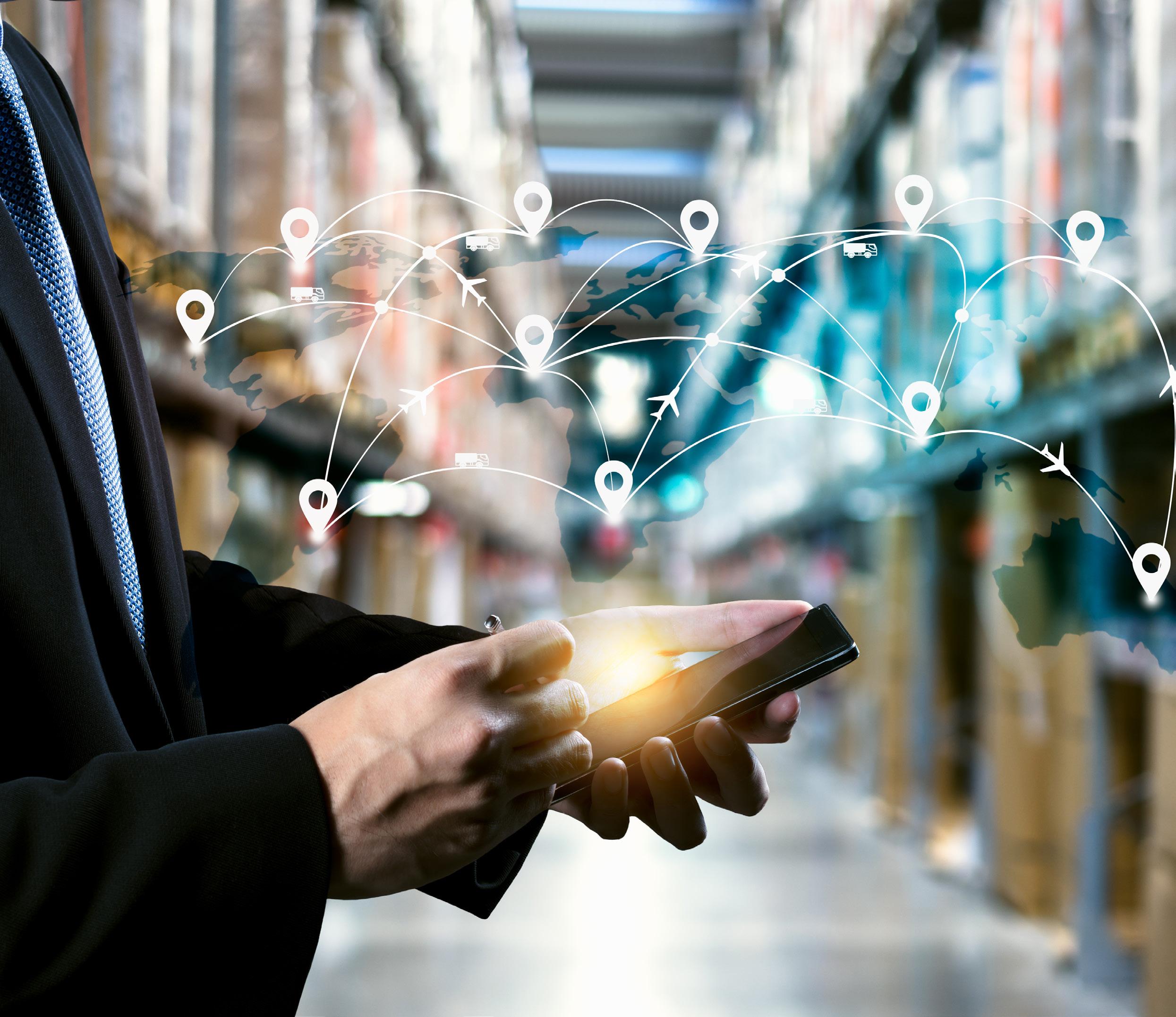
The senior executives who manage the SAP Digital Supply Chain organisation in Middle and Eastern Europe (MEE) provide us with insights into the enabling power of digital solutions, collaboration and technology. As they align these hot topics to SAP’s expertise, capability, and partnership-led approach to solving challenges, they lead us through the key trends and opportunities of 2023.
Dr. Johannes Tulusan deliver their cautiously optimistic view of the year ahead.
AP’s optimism is founded in business projects that were planned and being executed long before the current economic shakeup. Across SAP, teams are looking to improve the solutions they already offer clients, switching from on-premise to cloud-based options, for example, and demonstrating how to increase product traceability and improve environmental, social and governance (ESG) performance.
Dr. Johannes Tulusan remains cautiously up-beat and explains, “You have to see the glass half full. Global circumstances might not improve in the near-term, but they give decisionmakers the chance to rethink how to operate their business. Resilience in supply chains is already very important, and sustainability will definitely become important too. We at SAP are in a good position to support our customers on those fronts.”
Andreas J. Wagner starts his assessment by saying that supply chain visibility and supply chain flexibility are key differentiators in business. “The supply chain function is not a backoffice function any more,” he explains. “It can either be a source of strength or weakness. Think about the loss of sales because of stockouts and the loss of loyal customers.”
He continues, “It has really become a strategic topic for our customers. Championing the design to operate process in the market can be a key differentiator because you will have digital and integrated processes and can really showcase the end-to-end value of the solutions within your key processes.”
This is about not only innovating and breaking down silos within a company, Andreas states. “You also need to standardise your connections with
There is a feeling fizzing out of SAP right now: enthusiasm. SAP’s SVP and General Manager of Digital Supply Chain MEE
the outside world,” he says. “It's a very important process. For example, in the area of design innovation you already need to check early in the process whether the necessary suppliers are
available and whether they can support needed quality and quantity before you even produce master data in an enterprise resource planning system,” he says. “And you also need
Camelot’s Supply Chain
Resilience Center is not only sustaining and improving our business processes every day but also working with us towards our goal of achieving a balance between supply chain maturity and supply chain operations cost.
Claud Noh, Corporate CIO / Vice President at ZinusTo achieve an efficient, agile, risk-resilient, and sustainable supply chain, organizations need an end-to-end process vision, and they require to embrace cloud innovation cycles to enable continuous improvement.
Supply chain issues are in the spotlight right now – disruptions, material shortages and rising costs made it abundantly clear that today’s supply chains have become more complex and hyperconnected than ever. Often, when disruptive events occur, the result is a reactive and uncoordinated response that puts achieving margin, profitability, sustainability, and service level goals at risk.
The new supply chain complexity requires close collaboration between lines of business and stakeholders as well as transparency and flexibility across the supply network, making it mandatory to have enterprise systems to be digitally connected, coordinated, and operated. This constitutes a so-called intelligent enterprise. In the context of supply chain this means digitalization of processes from Design to Operate (D2O).
The overall goal of D2O is to be resilient to adapt to the next threat and to be flexible to embrace the next innovation. It starts with how you design new products in an innovative way, followed by a resilient planning process that drives sustainable manufacturing and logistics to deliver products to your customer and ultimately, maintaining these products.
As a long-standing implementation partner of SAP with more than 25 years of experience, Camelot ITLab supports customers on their journeys to realize the full potential of SAP Digital Supply Chain solutions. "In our experience, the key to every successful transformation is to follow this end-to-end vision for D2O processes and to cover all aspects from strategy to process, implementation, and continuous improvement," says Aseem Gaur, Executive Vice President at Camelot ITLab.
The digital transformation to build resilient supply chains is a continuous process and customers require, both an innovative solution and services approach to support this journey.
INNOVATIVE SERVICES APPROACH
One such innovative solution approach is the development of accelerators and extensions to the SAP solution portfolio on SAP Business Technology Platform (SAP BTP) in order to address industry challenges and augment SAP functionality. Following this solution approach, Camelot is realizing Kellogg’s Smart Factory vision by leveraging SAP Digital Manufacturing Suite and extending existing functionalities with industry specific accelerators: contributing to Kellogg’s sustainability goals while at the same time offering tailored industry-specific extensions for organizations.
Another example for an innovative solution approach is to extend SAP Integrated Business Planning (IBP) with cloud-based concurrent Production Planning & Detailed Scheduling (cPP&DS) capabilities
Realizing the value of SAP Digital Manufacturing Suite powered by Smart Factory
Accelerating the digital transformation by embracing resilience and continuous innovation
With Supply Chain Resilience Center (SCRC) as innovative services approach Camelot is offering a framework where all stakeholders can collaborate to improve and accelerate delivery of business value. It allows customers to sustain their supply chain transformation on an ongoing basis by addressing key challenges around technology, talent and processes. SCRC was leveraged at Zinus not only improving business processes to be more resilient every day but also facilitating supply chain maturity.
The SAP Digital Supply Chain portfolio offers interoperability between business processes and systems as well as frequent feature updates (cloud-based). Therefore, supply chain transformation is not a one-time activity. Instead, resilience and continuous improvement or adoption must be incorporated into the overall strategy. It is crucial to tackle a digital supply chain transformation with an end-to-end vision in mind. Camelot ITLab offers end-to-end supply chain consulting, services and innovations in the context of the SAP Digital Supply Chain portfolio, thus realizing the Design-to-Operate vision for our joint customers.
to think about how you can quickly qualify a second or a third source in case of supply chain shortages of existing suppliers. You can only become successful with the close collaboration between sourcing and design – so between an internal function and the network outside of the company.”
What software solutions, technologies and strategies do SAP executives deem to be critical for enabling supply chain resilience in 2023? The benefit of cloudbased solutions, Andreas and Johannes agree.
Johannes considers Scandinavia and North America to be well advanced in adopting cloud solutions, while Switzerland is picking up adoption quickly; in comparison, Germany and Austria are somewhat behind. He acknowledges that there are businesses and industries that are not yet ready to use a full cloud approach for a critical key process, understandable when there is a highly automated production line, for example. He says the adoption process starts when there’s a need to improve flexibility or find better ways to address issues such as global supply chain shortages and higher energy costs. As decisionmakers assess the right time to make the switch, they are balancing multiple factors against each other. A cloud approach means embracing change in the way software architecture is hosted. Continuing capital investments in data centres versus new cloud
innovation investments can be quite a big stumbling block, Johannes acknowledges. “Businesses do realise innovating is key to staying competitive,” he says.
Another challenge comes when deciding which cloud software vendor to work with. There are so many newer ones to choose from that finding the right solution for a business’s existing
products, processes or production can be difficult without expert guidance.
Johannes says, “Something that seems to be the ‘best’ solution might not actually be easily integrated into, say, an existing application landscape.” This is where SAP’s proven capability, established reputation, experience and network offer
confidence when compared with less well-known “challenger” suppliers.
This is another area where SAP capabilities can add value in terms of cloud services, security and innovation. Together with its strong partner ecosystem, SAP has been helping business leaders respond to a constantly changing world, and recover from supply chain disruptions.
The advantages of SAP’s partner ecosystem are discussed with the leadership of SAP’s MEE regional digital supply chain partner organisation on page 31.
Considering other challenges to face in 2023, Andreas points out the issues of security and the rise in the number of hacking attempts. “If you have your IT server in the ‘basement’ of your factory, it is at higher risk of hacking right now. There’s also a risk that in the long run you won’t have the right resources any more, or enough IT staff to maintain it overall. We are seeing labour shortages,” he warns.
The lack of data centre knowledge is partly the result of a shift to cloud solutions, and while fewer younger workers are entering the labour market, there are more older workers retiring. The imbalance between generations is affecting many industries and services. In January 2023, the German Chambers of Commerce and Industry (DIHK)
reported that more than half the nation’s companies were finding it difficult to fill vacancies due to a lack of skilled workers. In DIHK’s survey of 22,000 companies, 53% reported such shortages.
Next, Andreas and Johannes highlight the trends of nearshoring (bringing manufacturing operations or supply closer to a company’s headquarters or end customers), onshoring (basing operations in a company’s home country), and reshoring (returning operations to a home nation) as key components to maximising risk-resilient supply chains that are backed by technology.
After the challenges of the pandemic years, the vulnerability of the global supply chain has been further exposed by geopolitical unrest. For a very long time, the focus has been on building lean, low-cost operations that were predominantly offshore, but this left companies defenceless against the supply and demand issues that the
“Something that seems to be the ‘best’ solution might not actually be easily integrated into, say, an existing application landscape.” This is where SAP’s proven capability, established reputation, experience and network offer confidence when compared with less well-known “challenger” suppliers”
Dr Johannes Tulusan, Chief Operating Officer for Digital Supply Chain MEE
Economic and political upheavals pose major challenges for companies in all sectors. Buzzwords could be extreme weather conditions, disruptions to important waterways, pandemic-related closures of port facilities or airports, as well as rising energy and commodity prices. However, for a proactive response to short-term and unforeseeable market situations, the classic ERP logistics modules are not appropriate. Such situations call for digitally networked end-to-end solutions that offer maximum transparency and real-time information.
Market researcher Gartner predicted disruptions in the global supply chain as early as 2021. Unfortunately, their forecasts turned out to be more than accurate. To effectively meet these challenges, users need suitable solutions. Although digital tools can’t overcome hurdles, they help to evaluate the risks along the entire value chain realistically, making them transparent and controllable. This optimal balance between responsiveness, delivery, stock, lead times, sustainability (circular economy) and customer satisfaction enables a proactive response to volatile markets.
Integrated company planning connects sales, marketing, finance, procurement, and production to optimise costs, service and stock levels. It focuses on all areas of planning, from long-term and strategic planning to medium-term planning and right through to the execution. Segmented and synchronized end-to-end planning to match supply to customers helps to separate demand signals from market noise and facilitate incremental changes in service, inventory and overall equipment effectiveness (OEE). Digital planning transformation, progressive monetisation, integrated business planning (IBP) and scenario modelling by using leading technologies such as robotic process automation (RPA), simulation and artificial intelligence (AI) help to improve forecasting and planning outcomes and reduce the planning effort required.
With the experience gained from hundreds of implementation projects with well-known companies from discrete and process-orientated manufacturing, CONSILIO’s experts master all aspects of the supply chain repertoire and know which SAP solutions can be used to successfully meet the challenges ahead – keywords here are, for example, the cloud-based SAP IBP and S/4HANA Manufacturing for planning and scheduling (embedded PP/DS).
CONSILIO’s experts, together with their client BLG LOGISTICS – Europe’s leading logistics service provider - use IBP to make the sustainability of goods flows in a global network trans-parent and controllable at a granular level. With this solution, BLG LOGISTICS is boosting its competitiveness in the automotive logistics sector by digitalising the strategic planning processes with SAP IBP. Simultaneously, with CONSILIO’s support, BLG has implemented CO2 balancing in IBP to calculate volume planning, thereby documenting and actively modelling the company’s sustainability.
In addition to rough planning, CONSILIO is also an expert in detailed planning. For the wellknown German engine manufacturer MTU, CONSILIO implemented detailed planning with SAP Embedded PP/DS for the first time globally. The manufacturer is delighted and reports that they are able to comprehensively coordinate the production plan to match market requirements, purchasing restrictions and manufacturing capacities by means of a smoothed and feasible production plan.
SAP also values the skills of the SAP specialists from CONSILIO in Munich. CONSILIO is not only a certified SAP Gold Partner, it also supports the Walldorf company as a strategic development partner with its know-how in further developing and modernising the tank planning process. Tank planning is predestined for fine planning in PP/DS.
CONSILIO provides excellent consulting services when it comes to digitising and automating business processes. The specialists combine functional-technical SAP application expertise with industry and business process know-how. Our experts aim to improve their clients’ compe titiveness through the effective and efficient use of standard software. Well-known national and international companies from different branches place their trust in CONSILIO and build on the company’s 25 years of experience, expertise, and innovative strength.
“Thanks to the consulting expertise provided by CONSILIO staff and the advanced planning and simultion functionalities of PP/DS, we now have coordinated, smoothed and feasible production programs throughout the company.”
The forward thinkers. The process optimizers. The solution developers. More Details?
pandemic created. It is not surprising, therefore, that the benefits of nearshoring, onshoring, and reshoring are hot topics for 2023. By moving supplier sources closer to key markets, supply chain – and business leaders are able to mitigate risk, manage cost, optimise time to market, improve visibility and communication, and increase flexibility in response to disruption. But before eradicating existing production facilities, supply routes, or manufacturing chains, it is essential to bring key data into the picture. It was once a relatively straightforward decision to locate a factory in Asia based on overall costs. Since the pandemic, however, so much is being reconsidered. There
has been strong evidence of this in the United States, where reshoring and nearshoring are already happening as manufacturing companies move operations from Asia to Mexico, Central America, and Canada. Johannes sees European businesses that are also assessing how they can bring important operations closer to their home factories or key markets, but it is not as simple as it might seem. Making such a decision can be a complex and nuanced process.
BearingPoint’s award-winning carbon accounting solution (BearingPoint Emissions Calculator) has merged with SAP Product Footprint Management (PFM) to strengthen the fight against climate change.
In line with the leading climate reporting standards, the cloudbased solution enables companies to quantify Scope 1, 2 and 3 carbon emissions and calculate cradle-tocradle footprints across entire value chains in an easy and automated way.
The merged solution shows how to reduce carbon emissions in a structured, fact-based way. It also gives companies the transparency that will be key to fulfilling the requirements of upcoming regulations.
Let our new Virtual Reality Process Experience take you to a different dimension. Use our technology to create 3D digital twins of your factories, warehouses or other infrastructure. Facilitate collaborative and immersive virtual
Boosting responsiveness through technology and digital processes can smooth spikes in demand and iron out materials shortages, allowing planning across company networks, www.bearingpoint.com
workshops, identify inefficiencies in repetitive workflows while reducing business travel, and train staff in a safer and emission-friendly way.
Scan the QR code to learn about a more sustainable future.
improving accuracy in predicting lead times, and enabling the ability to track goods. This can all be achieved more effectively if there’s transparency between suppliers, the manufacturer and the customer.
Digital integration also enables transparency for decision-makers who are considering their approach to sustainability. This is a topic that comes up again and again.
Andreas says customers and employees are making sustainability a requirement of their buy-in. He
cites an anecdote from a client whose prospective new employee turned down a job offer on the basis that the company’s sustainability strategy was not clear enough.
On another front, customers and consumers are looking for traceability along the supply chain. Tracking all raw materials – from source and value creation through production and delivery – is of prime importance, Andreas explains, not just because of regulatory requirements.
A significant proportion of purchasers
and customers will choose ethical traceability over a doubtfully cheap alternative.
“These regulatory requirements, they really affect the entire supply chain throughout the design to operate cycle, end-to-end, and at the end,” Andreas states. “It's all about generating and managing master data. You really need master data to be generated and managed across the entire value chain, so you are able to decide every step in the business process. How sustainable is this step? What are my choices? What is the financial impact? And then, as a decision-maker, you need to have
the data available there to make the right decision here.” This is where SAP’s design to operate (D2O) approach is well positioned to enable companies to get a view on every aspect across critical business processes and make intelligent decisions backed by data. In addition, SAP CEO Christian Klein has already talked about SAP adding a green ledger to enterprise resource planning (ERP) so that companies can account for their carbon emissions in the way they currently account for their financial situation.
“We can offer you reliable environmental, social and governance (ESG) data for your entire enterprise,” says Andreas. He cites the newest version of the
“It's all about generating and managing master data. You really need master data to be generated and managed across the entire value chain, so you are able to decide every step in the business process”
Andreas J. Wagner, SVP and General Manager of Digital Supply Chain MEE
One of the everyday challenges of companies with logistics are the shipping documents.
Handling incoming and outgoing trucks is very time-consuming. It takes a lot of work (and office space) to print, sign and file the freight documents. Sometimes you have to search for papers relating to older processes and the volume of folders is constantly growing.
The sign-pad app simplifies your daily work routine. Thanks to a user interface designed with SAP Fiori it provides an intuitive way to read and digitally sign documents on a mobile device. The papers are immediately filed with the correct process in the system.
. legally valid signatures via mobile device
. digital documents save paper, time and stress
. immediate filing without media disruption
. streamlined self-service processes
Today we would like to introduce you to our app sign-pad. In an SAP project it is sometimes useful for the implementation partner to introduce additional solutions in order to close technical gaps, cover or supplement functional requirements, or accelerate the implementation. And one of them is our sign-pad.
Please check out the success story of our customer in the beverage industry.
With the enterprise's growth, the interaction between the horizontal and vertical departments is getting more complex. The modern business approach must manage the increasing complexity of the product by introducing innovations into the development and ensuring transparent business processes and communication within the company.
Looking back to last year the LeverX experts, Natallia Arkhipava, Lead PLM/RD Consultant, and Darya Hauruseva, Lead PLM/EPD Consultant, consider five key challenges manufacturers face and tell how SAP Recipe Development, SAP Enterprise Product Development, and LeverX IPS solutions can address them.
Compliance checks should be incorporated into the product development process during early stages and repeatedly examined to mitigate potential future costs related to corrections and rework. Compliance and legal requirements are constantly changing per country, region and/or regulatory jurisdiction, so multi-regional and global companies must continually be ready to adapt their products.
SAP Recipe Development integrated with S/4HANA for Product Compliance.
The pandemic caused a rapid spike in product demand in many industries, forcing companies to quickly increase the production volumes. Insufficient internal collaboration between the departments involved in product development may lead to gaps in information and data flow and time delays.
WE ADVISE
LeverX Integrated Process Solution (IPS) integrated with SAP Recipe Development and SAP EPD.
The ability to simultaneously update data for large numbers of items has been a critical requirement in virtually every project. Mass updates became especially vital for our clients in the pharmaceutical and chemical industries during the first months of the pandemic when discontinued raw materials and supply chain changes were rampant.
WE ADVISE
SAP Recipe Development integrated with LeverX IPS.
Companies look for ways to design and manufacture products that comply with the company's sustainability goals. They need tools that can calculate and provide product data to analyze the environmental impact, for example, packaging decomposition and carbon footprint information.
WE ADVISE
SAP EPD Collaboration integrated with SAP Recipe Development and SAP Product Footprint Management.
Typically, external parties don't have access to a company's SAP system due to infrastructure and security reasons. Companies have to rely on email or third-party solutions for collaboration that may cause additional delays in product development, overloaded IT tools environment and not timely requested and updated product data.
WE ADVISE
SAP EPD Collaboration and Provisional Specification integrated with SAP Recipe Development.
Read here for the full story of how SAP RD, SAP EPD, and LeverX IPS solutions can address those challenges.
Get to know more about the solutions — ask for a free consultation at contact-leverx@leverx.com leverx.com
ALL ABOUT US
in 60 sec
SAP® Sustainability Control Tower solution that lets you record and report audit-ready ESG measures and act on them, since the ability is already embedded into your business process. He continues, “Design, plan, manufacture, deliver to operate: It's all about waste reduction, emissions reduction, green packaging, energy reduction, lower carbon footprint, and fewer accidents. Every step of every process of design to operate has to have a strong link to sustainability. As I’ve already said, supply chains are right at the heart of sustainability topics.”
As businesses innovate, renew and move forward after the challenges of the last few years, SAP’s proven experience and expertise in business software development and delivery offer business leaders a range of opportunities to innovate in their core processes and meet markets’ demands. Up-front enthusiasm gets noticed and existing customers know the ability of SAP’s teams to meet new demands is all about excellence in understanding their customers’ requirements in their respective industry.
When deciding how to respond to these key supply chain trends and challenges, SAP took action. Adding
to SAP’s already comprehensive solution, service offering, and SAP Experience Centers around the world, October 2022 saw the launch of a new showcase area of SAP Industry 4.0 Center in Walldorf called The Factory, just a short walk from the SAP Experience Center. Together, these provide industry professionals with the opportunity to visit state-of-the-art spaces and witness SAP innovation, solutions and technologies in action. They illustrate how SAP works closely with customers and partners to find solutions to their challenges, and demonstrate SAP’s position as a market leader in digital supply chain (DSC) and integrated supply chain solutions and services.
Ralf Lehmann, senior director of SAP global solution management, and Matthias Deindl, head of SAP Industry 4.0 Center EMEA and India, present The Factory at SAP Industry 4.0 Center, in Walldorf. Taking a tour of the new facility offers glimpses of both the future and the cutting-edge present day of supply chain innovation. The Factory can be adapted to suit a wide range of scenarios, depending on a customer’s needs. It can focus on both batch production, as well as discrete manufacturing, addressing a multitude of different industries. It is unique in the sense that it is an end-to-end setup with real software systems and real shop-floor integration. All stages of the product lifecycle are demonstrated in a
While it is possible to tour The Factory virtually, it is the in-person, immersive experience that is proving very popular. Ralf, who is also creative director of SAP’s digital supply chain showcase, and Matthias, say that after years of pandemic restrictions, many customers and prospective clients actively want to come to Walldorf. They are keen to engage with the valuable supply-chain content in The Factory for themselves. Sustainability and the net-zero targets surrounding travel have to be factored into research costs, so SAP’s dedicated video-streaming equipment allows for a hybrid approach.
“People want to travel because there's a social element, and they want to
see our software showcase and talk directly to our management in our headquarters building only 100 metres away from The Factory,” Ralf explains. In contrast, a global customer was able to stream the same experience to teams based across Europe, Asia, and South America simultaneously.
“Sometimes we have put on an overview and inspirational session for the top management, and then we will have three or four follow-up sessions for the whole team virtually,” explains Ralf.
SAP’s own teams value the interaction and are pleased to have in-person customers again, with direct feedback.
“We answer customer-specific questions and show the end-to-end value of supply chain – and SAP's ERP solutions integrated with our industrial hardware partners,” says Matthias.
The scenario is interconnected, and processes are visualised with lights.
“Imagine we are working here with liquid concentrate and have the standard production for the process industry with lots of tubes and tanks in there, all 100 percent realistic but our different ingredients are red, green and blue. We can mix different colours to demonstrate the customer scenarios,” says Ralf.
The key thing about The Factory at
SAP Industry 4.0 Center is this: it comes across as an evolution (although it may be a revolution) that provides a visual and actual representation of all the digital supply chain has to offer clients, customers and partners. That is because the physical factory is a genuine representation of a real-life scenario. So, when a customer first arrives, whether that is physically or virtually, their impression is not of a “too pristine to be believable” film set, but of something that could be their own production line, manufacturing facility or processing plant.
As Matthias explains, “It's really interesting to see how, when they enter our factory, our customers have a smile on their face because everything is not super-shiny or what you might expect from a marketing pitch. It's hands-on, with work centres of the kind you would find in real life.”
Maybe it’s the lab coat hanging up in the corner. Or perhaps it’s the (deliberate) tank overfill that Matthias
Most manufacturers today have some form of IoT or Industry 4.0 initiative in place. They may have sensors on the shop floor, computers across the supply chain, and are regularly generating masses of industrial equipment data – even if aren’t sure how to monetize it.
Driving sustainable value and intelligently connecting your business strategy with your people, processes and technology is essential, with smart manufacturing, sustainability and agility having moved up every manufacturer’s priority list.
Putting smart components or more automation into the process, in the hope of achieving smart manufacturing is simply not enough. Unlike a traditional factory, where people, assets, and systems all operate in isolation from each other (and must be continually coordinated), a Smart Factory integrates machines, people, and Big Data into a single, digitally connected ecosystem, which monitors and triggers its own maintenance.
At Atos, we understand that the convergence of the physical and digital worlds – from the shop floor and operational equipment, to the intelligent enterprise and the wider ecosystem – require both the right experience and the right technology infrastructure.
Our deep sector expertise means we know how to guide our customers to successfully
processes, and technology
transform their manufacturing plant into an adaptable, agile, closed-loop Smart Factory, including self-optimising, selfhealing production processes within a connected business network.
In conjunction with our technology partner, SAP, we use some of the world’s most advanced technologies, such as AI and Machine Learning, to create factories that not only orchestrate the manufacturing processes, but actually learn from their experiences.
The combination of SAP’s technology (like SAP BTP, SAP Digital Manufacturing Cloud, SAP Asset Intelligent Network, Team Center) and our step-based approach means our customers can easily adapt at their own pace to meet all sustainability, environmental, productivity and commercial needs.
The shift from single, soiled systems and organisations to networks of capabilities is a game-changer for manufacturers. Our experience in this area means we are the trusted partner for some of the world’s leading manufacturing companies.
Atos’s consultative Smart Manufacturing service gives you:
• A clear strategy and a flexible roadmap with insight on how and where to start, what to expect, and how to scale.
• Advice on how to accelerate business gains, and drive sustainable value and environmental gains.
Atos is a global leader in digital transformation with 112,000 employees and annual revenue of c. € 11 billion. European number one in cybersecurity, cloud and high-performance computing, the Group provides tailored SAP endto-end solutions for all industries in 71 countries.
Atos is a Global and Platinum SAP Partner.
• Co-development environments demonstrating proof of concepts and prototypes.
• Integrated solution design and implementation.
Download our brochure, speak to one of our experts, or request a tailor-made demonstration addressing your specific challenges.
Find out more at atos.net
sets up to showcase the digital adaptability of the process, or the fact that a pick-and-pack scenario is running in the warehouse in the background. These combine to lend true authenticity to the experience and deliver real understanding.
“We show that we can speak with the automation layer, and that the automation layer can speak with SAP solutions. It’s about vertical integration, the information technology (IT) and operational technology (OT), and the total integration of those two worlds. It’s really demonstrable,” says Matthias.
C-suite executives, factory managers, IT experts or researchers can grasp the processes quickly, Matthias points out. And experts from different departments within the same company can come to the same place at the same time – virtually or in a hybrid format – without the need for multiple explanations as supply chain solutions are shown in action.
A chief operating officer (COO) or head of supply chain who is familiar with their own production facility can formulate questions about the industry-specific supply chain scenarios within The Factory at SAP Industry 4.0 Center. Convincing a chief
financial officer (CFO) to buy in to the head of manufacturing’s enthusiastic appreciation can be harder because they may have less knowledge of the ground floor. Yet sometimes the commissioning process starts at the other end of the business, in the C-suite, before it moves through to the manufacturing team, Ralf says.
“What we try to do is not only address those who are doing the purchasing, but also those who are using the products later on,” says Matthias. That is where a virtual tour alongside the in-person, real-life tour, can be invaluable. For example, two principal decision-makers can stream a live
a
they want to see our software showcase and talk directly to our management in our headquarters building only 100 metres away from The Factory”
element,
feed to watch those who have to set up and operate a new process, or vice versa. It means questions or key issues can be pointed out and discussed through streaming technologies in different parts of the country, or the world, simultaneously.
“So, experts on the manufacturing side might want to know, ‘How did the automation of this robot work here? How did you integrate your smart tool? How does it work – show me!’ Then they can deep dive into the systems based on what they can see happening in the real enterprise IT landscape that we have in The Factory. And because everything is real, nothing is fake, it generates trust with our customers,” says Matthias. “People in top management don’t really need the details, but they can see the tangible use cases. It’s something they can grasp and discuss in a very short time.”
“People want to travel because there's
social
and
Ralf Lehmann, Senior Director of SAP Global Solution Management
Ralf adds that inclusivity across levels promotes communication. For example, a factory worker might point out that glitches could be created if a tool or table is used in a proposed context. Such a small but essential comment might play a crucial role in improving manufacturing or maintenance processes. On the flip side, this immersive experience also provides an opportunity for customers to provide valuable feedback, creating a collaborative community environment.
This sense of collaboration is right at the heart of SAP’s approach. Ralf points out that where competitors
might only run a scenario based on one operation or one out-of-the-box vendor, SAP is working in collaboration with many other business partners – small, medium, large, and global. Collaboration in this sense means building bridges, rather than operating in silos – a key mindset for SAP. The Factory is the perfect showcase for anyone needing to see discrete manufacturing, design to operate (D2O), and design to consume (D2C) capabilities, albeit on a small scale, and to visualise how something similar might fit into their own business. One of SAP’s great strengths is collaboration and cooperation, working with both partners and customers to help ensure
DISCRETE ASSEMBLY
Design, build and operate a discrete unit to produce and mix syrups.
BATCH PRODUCTION
Develop a recipe for a concentrate. Produce, mix and pack the product.
the right solutions are available to suit particular needs.
“We would love our customers to run only SAP but – we have to be honest with ourselves – in reality, that is not the case. We are living in a heterogeneous world where the SAP
software environment and different cloud companies play an active role. So, it's about connecting and being able to execute the business process end to end in the most efficient and secure way,” Ralf says. He has plenty of experience with companies operating on a silo-based
“We are living in a heterogeneous world where the SAP software environment and different cloud companies play an active role. So, it's about connecting and being able to execute the business process end to end in the most efficient and secure way”
Matthias Deindl, Head of SAP Industry 4.0 Center EMEA and India
approach, which makes it difficult to connect solutions or software, and so he welcomes the newer outlook of collaboration.
“Times are changing, and customers are pushing for harmonisation and open industry communications standards,” explains Ralf. In a world of mergers and acquisitions, he adds, with multiple vendors across factories, a heterogeneous approach allows for digital transformation, mass personalisation, and configuration, which in turn adds value and futureproofs a customer’s business.
“We have a lot of service and implementation partners, and SAP is powerful because of the partner ecosystem. They are all important partnerships, from the smallest automation-centric, to the biggest as well,” he says. And if there is something that the last three years have shown, it is that no business is an island, and no supply chain is 100 percent secure.
Around 25 or so industrial partners support The Factory setting either by providing service input, supplying hardware, or jointly interacting over a digital supply chain order. Ralf and Matthias emphasise that partnership is SAP’s superpower.
“They all play a crucial, active role in bringing solutions to our end customers,” says Ralf. “SAP has such
SAPʼs solution and growth strategy is clearly focused on its partners. What role do partners play specifically in the design-to-operate solution portfolio?
Design-to-operate, or the digital supply chain, represents one of the broadest and strongest ecosystems within the SAP world. SAP partners are an essential part of our growth strategy, especially with regard to the digital supply chain. Partners play an important role in our portfolio development of our, and we view partner-generated revenue as a strong KPI that impacts SAP ʼs success as a company. In addition, we have always relied heavily on our partners in various business-related dimensions, be it sales and presales partnerships, value-added reselling, or the development of add-on solutions provided via the SAP Store. If we now look at SAPʼs cloud strategy, the role of partnerships becomes even more crucial: based on their expertise and their add-on and implementation solutions, they will be a mainstay for our cloud-related offerings and processes.
CENIT ʼs position as a certified SAP partner for implementing true end2end design to operate processes, as a developer of new software offered on the SAP price list, but also as a reseller of SAP licenses and cloud solutions, is unique in the design-to-operate solutions market. What are the most important advantages for CENIT ʼs customers?
PETER SCHNECK CEO CENIT AGCENIT is THE one-stop solution when it comes to SAP and digitalization in manufacturing industries. Our core message to our customers is: no matter whether you are running a PLM system or an SAP PLM system and an SAP ERP solution, there is this one experienced partner that can help connect these data pots. Our background is our strong expertise throughout the SAP world. And we are highly familiar with the different PLM systems on the market. Based on our experience and thanks to our proven track record with more than 6,000 customers in this environment, we have a unique selling proposition in this respect.
a broad portfolio when it comes to digital supply chain, and we think many of our customers across the world don’t realise that. Being able to support events here and put on inspirational sessions with hundreds of virtual attendees will showcase that.”
Whether they are showing off the discrete assembly or the process industry scenario, Ralf and Matthias have a spring in their steps as their enthusiasm spills over.
“We are running cloud solutions, such as the digital manufacturing cloud in order to live this in a very tangible way,” says Ralf. “And the funniest thing is, whenever we start a customer session we say, ‘Everything you can touch here is not actually what we’re selling.’ What we do at SAP is the brain inside the orchestration, the software that is empowering these scenarios. But what you can touch is what is familiar and recognisable from home, from your own factories, and this is the really cool part of The Factory at SAP Industry 4.0 Center.”
Ralf and Matthias’s passion for innovation, collaboration, and “building bridges, not silos” is shared by Sasa Glisic, Anna Jagodzinska, and Bernd Meier-Mader, who form the leadership team of SAP’s MEE
digital supply chain (DSC) partner ecosystem. Their joint task is to connect DSC partners and SAP’s organisation and to accompany partners through the process of successfully setting up and delivering supply chain implementation projects to customers. At the same time, they help to generate growth, increase revenue, and boost competitive advantage.
“We are each based in different market units, and together we are responsible for a strong DSC partner ecosystem in Middle and Eastern Europe, which consists of 26 countries,” says Anna, leading the conversation as they set out how they go about achieving their mutual aims.
Building bridges starts with transparency, agree Bernd, Anna and Sasa, who strive to offer clarity and help businesses to benefit from SAP’s DSC partner ecosystem. They highlight practices that favour close, successful,
“SAP partners also benefit from early knowledgesharing, enabling development of new tools such as the recently launched SAP Quality Issue Resolution solution, which enables customers and suppliers to collaborate in a problem-solving process”
Sasa Glisic, SAP MEE digital supply chain (DSC) partner ecosystem
and well-coordinated cooperation. Gaining SAP’s official DSC partner status is a seal of both approval and trust, and to achieve it a continuous flow of information is exchanged between parties.
“We can assist partners in gaining access to various funds that, for example, they can use for business
development activities depending on their objectives,” says Bernd, highlighting just one of the many advantages of the partnership. The team points out that, in addition, SAP offers a range of business models through which DSC partners can sell SAP software solutions, maximising the benefits from a leading solution portfolio in a fast-growing market.
As a pioneer in the aerospace industry, Mynaric also decided to become a first mover in the SAP world and was one of the initial customers to choose SAP S/4HANA Private Cloud Edition (PCE).
Due to the complex requirements and the desire for agility and reliability of the IT system, the decision was made to pursue this path together with NTT DATA Business Solutions and SAP. The initial focus was to find a setup that would allow the complex IT project requirements, international expansion, and production scalability at the same time. SAP S/4HANA was implemented within the framework of SAP Best Practices and could be put live after almost six months. With this step, Mynaric shows that they recognise the added value of future-proof and sustainable IT and also focus on it despite a large investment decision.
With the future-oriented system, intelligent technologies and smart services, the course has been successfully set for future growth, strategic decisions and visionary plans at Wingcopter GmbH.
The startup chose a RISE with SAP solution, an intelligent SAP Cloud ERP landscape, which is significantly raising the game for business processes at the innovative start-up. NTT DATA Business Solutions has qualified itself as a powerful IT partner with a high level of expertise and the flexibility to operate in an extremely dynamic project environment.
With the launch of the new fit-to-standard solution after six months, several goals have been achieved: the gradual development of an ERP+ system to meet the business objectives, and the establishment of an IT environment that complies with documentation requirements and enables efficient management of production. At the same time, the cloud and service-only strategy was successfully implemented with NTT DATA Business Solutions. In a competitive market with short innovation cycles, the investment in a future-proof IT system landscape with a modern ERP system offers the ideal preparation for a digital future.
What are the trends for 2023 in the supply chain?
I am firmly convinced that, in addition to the further digitalisation of intralogistics through the introduction of automated warehouse systems and automated transport systems, extralogistics in particular will also become more digitalised. Logistics is becoming more and more technical through vertical and horizontal integration and more transparent across company boundaries in the interaction of all participants in the supply chain. The focus continues to be on the planning of these chains. The supply chain is increasingly becoming the chain to the network and thus, in the next step, the platform. Economic, regulatory and environmental influences will have an even greater impact on this area. Every end user of the software solutions and thus every company will have to pursue and realize the basis and the subsequent expansion stages here.
What does resilient supply chain stand for?
Resilient means reacting more insensitively to external influences and thus being stable in function and reaction to constant changes or “sudden” events. If the supply chain is resilient, this means that the chains or future networks can respond to external influences such as disrupted processes due to war, pandemics or strikes with stability and functionality.
What do you offer customers to fully cover their supply chain processes?
NTT DATA Business Solutions first of all offers its customers the entire range of SAP solutions in the area of supply chain, production and comprehensive planning. In addition, we close “white spots” that are not covered by SAP itself with SAP-based OwnIP solutions. For and with customers, we develop IoT solutions in partnership, which open up new business models and represent their and our innovative strength.
How can NTT DATA Business Solutions help clients establish sustainable processes?
In order to establish sustainable processes, it is important to include environmental, social and societal indicators in addition to profitability indicators such as time or costs. Two concrete examples from practice: we are currently establishing a logistics platform for a young drone start-up to quickly and safely deliver medicines to remote villages in Africa (see Wincopter case on this page). For another customer, we are currently pursuing the goal of transparently mapping the so-called “productbased carbon footprint” of its products in order to simulate product variants that have better carbon footprints. This covers all information from the entire supply chain from Scope 1 to 3. As it is important to include all parties involved, from suppliers through the company’s own production to sales and operations.
How sustainable can the supply chain be, what is the focus?
This depends on the specific use case and its sustainability goals. There is no one solution for everything. Let me have two examples here: energy-intensive production processes not only attach importance to optimisation due to increased price developments on the energy market, but also aim to drastically reduce CO2-equivalent emissions, especially since the EU-wide climate agreement. Another topic area is, for example, the reuse of raw materials in the sense of a circular economy. Here, goods, services and products that have been decommissioned are returned to the production cycle and thus serve as raw materials for new products in the sense of a cradle-to-cradle supply chain. This goes far beyond the recycling of a PET bottle. Because here, a car can then also be made into a car again.
Which SAP solutions are used?
We currently see enormous potential for the SAP Cloud for Sustainable Enterprises portfolio in conjunction with SAP S/4HANA to meet current environmental and social issues such as the supply chain due diligence act in Germany . Worth highlighting are the solutions SAP Product Footprint Management to track productbased emissions, SAP Responsible Design and Production to support the circular economy and the holistic reporting tool SAP Sustainable Control Tower. Together with our Co-Innovation Partners, we also develop our own innovative and sustainable business solutions.
Once approved as a partner, a business also has the option to use SAP as a sales channel for its own solutions.
“We motivate SAP’s DSC partners to break new ground,” says Sasa, citing the example of businesses being able to package their own intellectual property and services in combination with SAP solutions. “This offers a smart solution and allows us to combine the strength of partners and SAP, which in turn leads to the easier initiation of transformation projects for customers.”
By building up their own knowledge of both customers and partners, Sasa, Anna and Bernd help and enable new partners to demonstrate their organisations’ deep technical expertise. Sasa adds, “Imagine a circumstance where a customer wants to know what is needed to switch from an on-premise solution to the cloud. SAP partners also benefit from early knowledge-sharing, enabling development of new tools such as the recently launched SAP Quality Issue Resolution solution, which enables customers and suppliers to collaborate in a problem-solving process.”
New partners who join SAP’s partner programme gain access
to a portfolio of industry-leading solutions that can boost business. “In addition to that, we provide access to SAP demo systems for partners,” says Sasa. The team’s objective is to pursue an efficient approach to partnerships, which enables continuous development of new customers and business. Typically, Anna, Bernd and Sasa plan go-to-market (GTM) activities that align with SAP’s partner network. This helps ensure that they have an in-depth understanding of how they can support each partner and increase the adoption of modern supply chain and manufacturing solutions. This year, the team has already kicked off GTM activities with a central theme of efficiency.
Sharing how they source information and define actions that drive efficient cooperation, Anna, Bernd and Sasa explain that they screen the partner project pipelines, DSC readiness, and utilisation. This could mean sharing recent organisational changes, updating information on strategy to keep partners aligned on key topics such as sustainability solutions, or highlighting how SAP Business Technology Platform can be used in supply chain.
Anna says the team and the partner keep track of the success of a project as it goes live to enable a smooth rollout. Maintaining dialogue between all parties helps ensure
that customers are satisfied. Happy customers lead to more referrals by recommendation, which in turn lead to the implementation of similar projects for other customers. Collaboration also opens opportunities to sell new licences, and as demand increases, raises revenue for both SAP and the partner.
Another objective is to motivate partners to develop and deliver solutions that are not already available in SAP’s standard portfolio and the SAP Store online marketplace. In turn, this allows more customers to benefit from partners’ innovation. As support, Sasa, Anna and Bernd stay aware of market demand. This allows the team to suggest training for existing partners, enabling them to satisfy any specific customer interest, requirement, or request. Take the area of sustainability, which is increasingly important to customers, as an example. The trio can also demonstrate how partners can leverage The Factory for customer engagements.
“The annual GTM conversations are crucial and help us to understand the partner perspective. In our experience, we find that the greatest success occurs when both the alignment is good and we have facilitated the incorporation of our partners’ knowledge into SAP’s organisation and portfolio,” says Sasa.
What then, is the most important strategic direction that Sasa, Anna, and Bernd will be sharing with the partner network in 2023?
“We are each based in different market units, and together we are responsible for a strong DSC partner ecosystem in Middle and Eastern Europe, which consists of 26 countries”
Anna Jagodzinska, SAP MEE digital supply chain (DSC) partner ecosystem
“We are asking partners to support customers’ big digital transformation projects focusing on the RISE with SAP solution and consider supply chainrelated, and manufacturing-related improvements because these projects are of high interest,” Sasa says.
RISE and Supply Chain Solutions allow customers to improve efficiencies, fund innovation, and transform their mission-critical systems while minimising business risk. The solution can be combined flexibly from:
• Cloud ERP for every business need
• Industry next practices and extensibility
• Analytics and business process transformation
• Outcome-driven services from SAP and our partners.
Big transformations in particular provide a good opportunity to form the foundations for future capabilities and supply chain competitiveness. Such foundations have an impact on the future readiness and success of a company, according to Sasa, Anna and Bernd.
“We rely on partners to use their industry expertise and objective viewpoint to showcase the power of new cloud solutions to customers and help convert them from an onpremise-based architecture,” Sasa explains. “We want partners to help customers with their precious product and industry know-how. They can run innovative and customer-valued sales cycles and successful project delivery approaches that will allow
“We can assist partners in gaining access to various funds that, for example, they can use for business development activities depending on their objectives”
Bernd Meier-Mader, SAP MEE digital supply chain (DSC) partner ecosystemBernd Meier-Mader
Mid-sized manufacturing companies today must operate global supplier networks, omni-channel sales and guarantee quick delivery and comprehensive services to meet customer demands. What you might not know is that even just a few targeted investments can allow great progress, from networked processes to increased transparency along the entire supply chain. This covers the spectrum from procurement, warehousing and transport down to maintenance and customer service.
All for One won the SAP Digital Supply Chain Appreciation Award 2022 at the Diamond Initiative for Partners.
SUSTAINABILITY
RESILIENT SUPPLY CHAINS
SUPPLY CHAIN DIGITIZATION
WAREHOUSE LOGISTICS & MATERIAL FLOW
EFFICIENT WAREHOUSE MANAGEMENT
TRANSPORT MANAGEMENT & SHIPPING
CUSTOMS & FOREIGN TRADE MANAGEMENT
SUPPLY CHAIN PLANNING
PRODUCT DATA MANAGEMENT
ALLFORONESTEEB.COM/DIGITAL-SUPPLY-CHAIN
Every day at All for One Group 2,700 experts give their all to increase the competitiveness of our customers. We gather together the deciding factors from among the facets of competitive advantage to support over 3,000 customers in Germany, Austria, Switzerland and Poland in transforming their companies and strengthening their competitiveness.
a simultaneous boost to indirect sales revenue growth rates while identifying further relevant cloud solutions. In addition, we want partners to actively contribute to meet customer requirements more easily and quickly through the positioning of ‘ready-to-use’ solutions from SAP Store.”
The trio agrees that the powerful circle of customer, partners and SAP’s reputation and knowledge will be crucial for continued success.
“This is particularly true during the current phase, where we have to restore supplyand-delivery capabilities and competitiveness under new and more difficult conditions,” Sasa says.
As a team, Anna, Bernd and Sasa are highly motivated to turbocharge SAP’s success with the help of a great partner network that still has so much potential to fulfil. There are lots of new topics and innovations that SAP’s partners can offer to their installed base and to new customers.
“DSC is a very consultationintensive business, so we will continue to onboard
“We want partners to actively contribute to meet customer requirements more easily and quickly through the positioning of ‘readyto-use’ solutions from SAP Store”
all the processes are interdependent. That is why a digitization project is particularly challenging in this field. Over the years we decided that working with an SAP demo system right from the very start provides an important hands-on experience for the customer and serves as a solid foundation for the discussions that are crucial to specify the project requirements as precisely as possible. This initial phase is designed to convey the necessary terminology, processes and integration options of the system for the customer. On the other hand the SAP experts will learn more about the customer’s logistics processes and requirements. The subsequent discussions in the concept workshops will take place with a better mutual understanding on both sides.
Every company has its individual processes to be considered, there are also some components and features the customers require time and time again. So we came up with a compilation of readymade best practice and customizing components that have repeatedly been used in previous projects ranging from small warehouses to distribution centres with a material flow system. A »Best of«, if you will: The prismat/RAKETE (»Rakete« is German for »rocket«) is a system base that is preconfigured for S/4HANA and that serves to discuss process workflows and details. It is also suitable for testing and knowledge transfer before the realisation phase of the project even starts. The prismat/RAKETE for S/4HANA is designed for a cloud deployment, enables efficient project implementation and ensures a successful result.
To make sure that the customer will end up [happily ever after] with the solution that is needed, we offer three different versions of the prismat/RAKETE: the Discover Edition, the Prototyping Edition and the Implementation Edition, each covering different requirements and scopes, depending on the customer’s needs.
If you are wondering, what a digital transformation with the prismat/RAKETE will look like when put
into practice, please watch the video we made with our customer WISKA Hoppmann GmbH, a supplier of cable glands, installation material, maritime lighting and CCTV, for the maritime industry, shipbuilding, offshore facilities etc.
The prismat GmbH is your partner for the implementation of sustainable SAP solutions for their logistics. As a spin-off from the Fraunhofer Institute for Material Flow, we have been using our expertise since 1991 to help companies successfully optimize processes in warehouse and transport logistics, offering a comprehensive range of services including consulting, implementation, platform and migration strategies, licenses, support and training. We place particular emphasis on standards-based implementation. More than 220 colleagues work every day on our vision to revolutionize the efficiency and sustainability of logistics processes and systems.
knowledgeable partners in our ecosystem,” says Sasa. “We have a new competency framework in the SAP PartnerEdge® program that gives good guidance to develop partners’ own capabilities, raise market visibility, and make it easier for customers to recognise – and trust – partners’ proficiency in any given area.”
The team shares the conviction that SAP will become an even more partner-led company in 2023. As Sasa summarises, “It is a pleasure to watch as collaborations lead to a
win-win-win strategy, where partners, customers and SAP gain not only a share of the expertise, but also the successes.”
SAP executives would like to express gratitude to all the partners who have joined us to contribute to this issue: all for one steeb, Atos, BearingPoint, Camelot ITLab, cenit, CONCIRCLE, CONSILIO, LeverX, NTT DATA, prismat and TeamViewer.
For further information on SAP’s offerings, visit www.sap.com