IMPROVING AIR QUALITY AND SAFETY FOR PEOPLE AROUND THE WORLD

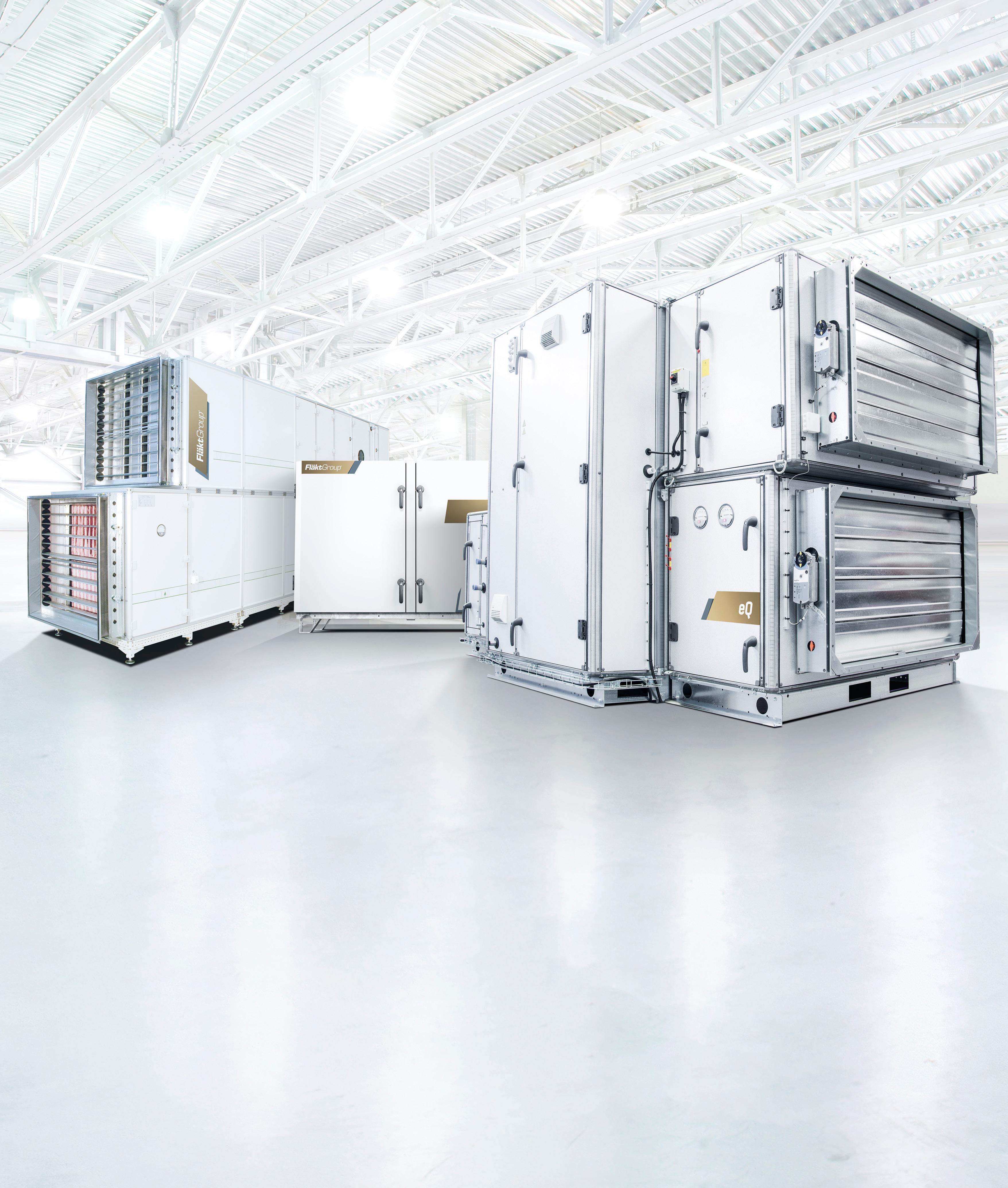
Nadine Hessel, Global Director for Supply Chain & Infrastructure at FläktGroup discusses the company’s innovative technology and supply chain strategies as a leader in the indoor air quality industry.
he name stems from ‘Fläkt’ – the Swedish word for ventilation, an integral part of the company since its original inception in 1909.
FläktGroup was formed in 2016 when Fläkt Woods joined forces with DencoHappel (formerly part of the GEA Group) to become a market leader for energy-efficient Indoor Air Comfort and Critical Air solutions serving a global market.
We sat down with Nadine Hessel, Global Director for Supply Chain & Infrastructure to discuss
the supply chain strategy and innovation at FläktGroup.
Nadine begins by explaining how the company takes a holistic approach to their operations since they cover all stages from design and manufacturing products to delivery, after-sales and servicing provision.
“You can find our products everywhere – in commercial buildings, residential buildings, industrial buildings, and critical applications like data centres,” says Nadine. “We
have 13 production sites, 3,500 employees and we sell in 65 countries around the world. I’m responsible for the supply chain and infrastructure in our business area Services. My main focus is the global availability and storage of spare parts within our service supply chain. This is a bit different from the manufacturing supply chain as the sourcing is not only build and buy, but you can also repair a unit or secure replacement parts.”
Nadine describes how the approach to the service supply
chain today looks different to the provision offered in the past.
“For us, we need to focus on all components of the supply chain,” explains Nadine. “All aspects provide room for improvement. So if we start with planning it has always been important, but it has shifted from planning for just-intime delivery or just-in-case delivery for service, to now even getting components at all. So it's quite different from the way it used to be. We try to have inventory buffers on the one hand, and on the other hand, we seek to find alternatives for missing components. But if there are some components with a lead
time of two years, the customer can't wait that long.
“So instead of replacing them one by one like we used to do, we try to find an alternative part if it's available. Consequently, one of the core components of our strategy is multi-sourcing. So, of course, we have our main suppliers and it's vital to keep our relationships strong with them. But I'm always open to getting in contact with new suppliers. So I have a lot of suppliers that reach out to me on LinkedIn for example. Usually I meet with them and listen to their propositions. Maybe they will have some components I can use. So that has changed.
“The important thing to note with FläktGroup is that we are a group of international companies put together through acquisitions. So growing together is a challenge for us. Therefore it's quite important within the supply chain strategy to take a global view. To find a component for an urgent service visit, for instance, I can check the stock in our factories around the world. I can ask them ‘What is your production stock like?’ and ‘Can I have that part?’ When you have high commodity availability, you can look at individual entities. But in today's situation, I think a global view is critical. So this has brought
us closer together within FläktGroup. We have cross-departmental support and always set a global strategy, even for small parts. I can always just look at all the stocks we have and find parts somewhere.
“What is special about the service supply chain is that the demand is not predictable. But it's a good thing because if it was predictable, it would represent bad news for product failures. There are some components that you can exchange and maintain on a service visit, but most of the demand levels for parts are unpredictable. But nonetheless, for me, it's important to have an overview of what we have sold to do some kind of forecasting when possible. So planning is still super important.”
At FläktGroup the company’s supply chain strategy hinges on embracing innovation and transformation to keep their operations and service
“My main focus is the global availability and storage of spare parts within our service supply chain”
Nadine Hessel, Global Director for Supply Chain & Infrastructure
www.wuerth-phoenix.com
info@wuerth-phoenix.com
Passionate about Dynamics 365, we believe in CRM projects as business accelerators for all companies. Dynamics 365 is a powerful cloud-based platform that offers a wide range of applications to help companies streamline their operations and improve customer relationship management. It already offers a number of specific solutions for sales and customer management. However, we aim to go one step further by introducing Sales+, a value-added feature that caters to the diverse needs of the sales force. Sales+ aims to optimise the daily operations of the sales force by enhancing functions such as offer and order management, article searches, price information, warehouse stock monitoring and automation of approval flows. By leveraging Sales+, users can significantly reduce processing times, minimise manual operation and boost their operational effectiveness.
Constant quality of IT services to support company business.
provision for customers at the leading edge of the air technology industry.
“Especially in a changing business environment, it's important to be flexible and open for innovation,” says Nadine. “I'm not only responsible for the supply chain, but for the infrastructure at FläktGroup as well. We combine those two things, which for me is fantastic because I love IT and bringing them both together. It's
with the benefits and then decide whether it's the right tool at the right time. Not all innovation is good innovation.
“But at the moment, digitalisation is super important for us and we aim to have user-friendly and efficient tools. Here, we have been working with Würth Phoenix for several years to introduce Microsoft Dynamics 365. I started to work with them on a sales project some years ago, and now
a strong combination because if I see there are some processes or systems we need to adjust, I'm then responsible for those changes as well.
“As a company we are always looking for innovation be it in technological terms or digitalisation. But on the other hand, you cannot follow every trend and we won't explore them just because they're hip. Instead, we will compare our experience
in my new role it’s a pleasure to work with them again on behalf of our service technicians. By working with Würth Phoenix, our service technicians can do most of their administrative tasks with a smartphone, say to record their hours or fill out service reports. Of course, many technicians within the group were able to do this before but as we are different companies put together, we used to have different systems. Now we would like to harmonise
“By working with Würth Phoenix, our service technicians can do most of their administrative tasks with a smartphone, say to record their hours or fill out service reports”
that into one global system for everyone.
“Another exciting technological innovation for our service technicians could be smart glasses they wear out in the field. That is one thing we are testing right now. Say the technician requires some support from the back office, their colleagues might need to see the unit as well to help them –especially with such technologically complex products. With smart
glasses, the technician can share exactly what they are seeing with their colleagues – crucially leaving both hands free to continue their work on the ground. In turn, back office staff can then share images, instructions or files with the technician from their end as well and the technician will see them clearly within the device on a small monitor.
“Another important aspect of innovation and transformation for
“We put QR codes on our unit and customers can scan it and find all details regarding their orders like manuals, spare parts lists – everything they need for the order”
FläktGroup is to make life easier for customers as well. So we have started working with QR codes. For example, we put QR codes on our unit and customers can scan it and find all details regarding their orders like manuals, spare parts lists – everything they need for the order. Additionally, we put QR codes on components, so our customers can find a list of contacts and know where to order a new part easily and quickly.
“Besides these QR codes, our customers can also make spare parts requests directly on our website. What’s more, we also have some units that offer remote access and we will be expanding this feature to benefit our customers and enhance the assistance we offer them. As I'm responsible for the whole service supply chain, this includes digital service provision and site visits. Remote access has been a gamechanger because it saves time and
costs for both parties, which is a fantastic innovation for us.”
Underlying the innovation and transformation at the company, Nadine highlights the importance of partnerships for FläktGroup’s supply chain strategy.
“So for us, strong and reliable partnerships are fundamentally important to our operations,” explains Nadine. “We are dependent on primary materials or components and our partners help us meet our requirements and support us in difficult situations. So even if there are lengthy lead times we can talk to our suppliers. If we don't have materials, we cannot produce units or parts. Without partners, there is no growth or success so partnerships are super important to our supply chain strategy and it all starts with the initial supplier. In turn we not only rely on the partnership with our suppliers, but we have to consider the relationships they have with their suppliers as well. Even if our suppliers have a high vertical integration, they rely on others at some point in their supply chain. As a result, it's crucial to share information. So if our supplier knows there are some parts that are at risk, but we know about that in advance, it's less of a problem because we can adapt
accordingly. So if you have partners, you have to share information and be open to each other. Sharing information is important but I also think it's a huge advantage to have partners who know your requirements. For instance with Würth Phoenix, we've been working with them for years. They know our processes, they know our businesses and they know our IT landscape – so they know what we need. Long-term partnerships are essential for our business.”
At FläktGroup innovation, transformation and robust partnerships built on transparent communications are the core components for achieving success with its supply chain strategy. But what are some of the major challenges facing supply chain professionals today that these approaches help offset?
“More and more challenges are coming our way,” says Nadine. “At first it was about optimising processes, saving costs and things like that. Then we had to adapt to sustainability policies and new legal requirements such as the Supply Chain Act in Germany. Now we are facing a shortage of materials which in turn makes it incredibly difficult to decide about warehouses and what needs to be stored because it's always a question of capital
commitment versus the risk of not having material. Supply chain professionals also need to consider new applications or technologies they could deploy – whether these are companywide platforms or dedicated software. But perhaps the most prominent challenge I see is the availability of materials coupled with rising inflation and therefore costs – especially when you need access to materials 24/7 for critical applications such as data centres.”
But despite these challenges facing supply chain professionals, Nadine loves her role and is excited about the future of the supply chain industry and how it might look different in the future.
“In the coming years, I hope that the availability of material will improve or return to normal, so we no longer have to create overstocks. But no one knows how long the shortages will last,” emphasises Nadine. “I think that digitalisation will become even more important and artificial intelligence will play a bigger role in inventory management, warehousing and so on. Lastly, I think the focus on sustainability will keep increasing in the coming years.”
For more information about FläktGroup, visit their website www.flaktgroup.com.
Environmental awareness and striving for sustainability are causes close to Nadine’s heart. She wrote her thesis on carbon footprints and she loves to find ways to become more sustainable. For instance, in her research, she realised how much CO2 is generated by streaming services.
“I try to stream consciously, so I pause the movie whenever I leave the room,” says Nadine. “Not because of the electricity used by the TV, but because the data centre in the background creates so much CO2. Small steps like that have added a lot of value to my life because sustainability is important to
me. Everyone knows when you're driving around with a car, it's creating CO2, but no one thinks about that when streaming Netflix or even if you just watch a video on your smartphone – it’s all generating CO2.”
Nadine is excited to attend the next Digital X event in Cologne which will take place September 20-21, 2023. She loves how unique the experience is at the exposition, where cafes, bars restaurants and even laundromats become exhibition stands.
“It’s a super cool concept and I’m really looking forward to attending,” says Nadine.
Connect with Nadine