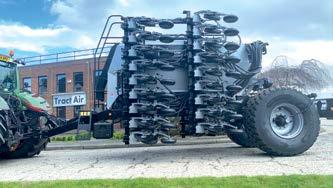
6 minute read
Importance or Tyre Pressures
IMPORTANCE OF TYRE PRESSURES
There can’t be too many farmers now who aren’t aware of the importance of tyre pressures and the advantages that can be gained from selecting the correct ones for the job at hand. Reducing soil compaction is the obvious benefit but testing proves that work rate, tyre life and fuel economy are all negatively impacted by using too high a pressure in the field. On the other hand safety, fuel consumption, tyre wear and comfort are all affected on the road if pressure is too low. Being realistic, changing tyre pressures in the traditional way is time consuming and is very difficult in the field. As a result, most operators will pick a pressure in the middle to try and find a balance, resulting in a pressure that is never correct for either field work or road haulage. For optimum performance, tyre pressures should be chosen based on axle load, speed and ground conditions, so would vary for different operations and at different times of year. Modern high flexation tyres are capable of running very low pressures to maximise footprint and traction so there are big gains to be had if this new technology can be used.
Advertisement
We can now offer a practical solution to this issue, allowing the operator to select the correct pressures at the push of a button, whilst on the move. Our tyre inflation system has been developed specifically for fitment to agricultural vehicles and machinery. It can be installed on any make and model of tractor, trailer, tanker, drill, harvester etc, in fact anything with wheels! The system is supplied to many major manufacturers and is available as a retro-fit solution distributed and supported from our factory in East Yorkshire.
Air is supplied by the on board air brake compressor, or by an additional hydraulic driven compressor if additional inflation performance is needed. The system is controlled via the ISObus interface (or a separate control unit if ISObus is not available) and can be controlled using the joystick. The latest V10 software allows lots of new functionality and the ability to save multiple configurations of machine, implement, weights etc with the corresponding pressures as advised by your tyre manufacturer.
The system then controls air flow to the wheels using a set of valves mounted on the machine and transfers this to the wheels via rotating unions. These are mounted either in the centre of the wheels or, in the case of bar axle equipped tractors, around the axle itself, tucking pipework away on the inside of the wheel. If a trailer or tanker is getting a system installed there are options to pass the air through the axle itself, to keep things neater still.
Mounted in the wheel rim is an additional valve, fitted into a new large diameter hole to improve flow compared to the original tyre valve. The new valve closes automatically when the system isn’t changing pressures, ensuring that leaks don’t deflate the tyres. If necessary, the pipework over the mudguards can be detached with a quick release fitting and stored away up on the mudguard. This can be helpful in particularly tight spaces or in very muddy conditions but in normal use the lines would stay attached. If tyre repairs or changes are needed this happens as normal. Our CTIS system is compatible with dual wheels, either controlling both tyres on each side, or just the inner ones – allowing the outside wheels to be left at a low pressure at all times.
The time to change pressures depends on the compressor fitted and the tyres sizes being inflated, however typical tractor times would be 10-12 minutes to inflate from field to road, and a couple of minutes to go the other way. Inflation times can be reduced by fitting larger or additional compressors however the ability to continue driving means that no waiting is necessary while pressures are changed.
There has never been a better time to invest in CTIS, with systems being covered under the current Farming Investment Fund grant scheme. Grant number FETF109 will cover £2413 of funding towards a CTIS system – accounting for roughly 40% of the total cost. Applications to this scheme are through the Gov.uk website and must be in before January 7th 2022 to qualify.
To contact us with any questions or enquiries on 01482 576222 or via
info@tractair.co.uk
You can also find more information and a link to the grant application page at our website – www.tractair.co.uk
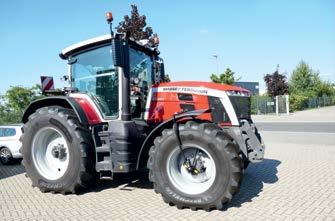
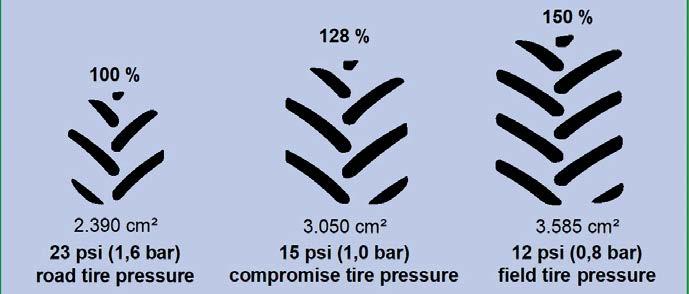
DRILL MANUFACTURERS
IN FOCUS...
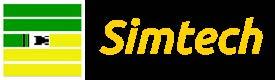
2021 has been a very positive year here at Simtech. A bulging order book, coupled with a move towards producing everything we sell in the UK from our Suffolk base, has not been without many challenges. Added to this is a complete re-design of the entire pneumatic range, as well as some smaller changes to other models.
The main change to our pneumatic models is that we are now building our own hoppers, rather than buying in readymade assemblies, but we are still fitting the tried and tested Sulky metering and distribution system, that we have been using since launching our pneumatic range in 2012. However the configuration is now very different from previous models, with the distribution head now mounted at the rear of the hopper and much lower down for ease of access. Calibration is now done by a front facing stainless steel chute, which directs the seed into a large bucket that is supplied with each drill. The same chute is also used to empty the hopper at the end of each job.
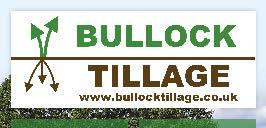
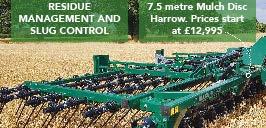

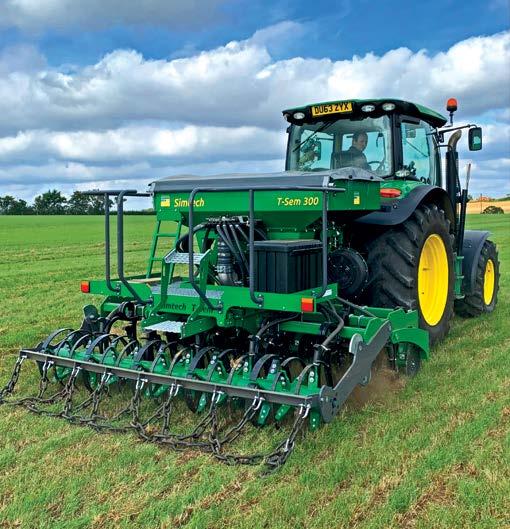
Hopper capacities remain at 1000 litres for the 3m model, but increase to 1300 litres for the 4m version and upwards to 1700 litres for the folding 4.8 & 6m machines. In addition we have placed the hoppers on all the drills as far forward as possible to minimise the weight on the back of the tractor. 3 & 4m models have a large platform area and lower level hopper for easier access and the new design height adjustable level sensor can be reached from the outside.
The big change to the folding models is a new design to allow the entire weight of the hopper/centre frame assembly to bear down onto the two drilling frames along their centrelines. This means that the whole weight of the drill is pushing down evenly across its entire width, but the 2 drilling frames can pivot along their individual centrelines to allow them to follow the ground contours. Added to this is a new simple system for adjusting depth, consisting of a spiral cam and a spring loaded plunger, which allows for 18 individual settings in its 0 to 10cm drilling depth range. With the exception of the 4m model, we have rolled out this new design across the whole T-Sem range.
Come and see us at Lamma 22 on stand 18.360, where we will be please to speak with you about our exciting new range and enable you to tap into our extensive experience on reducing tillage and converting to a more sustainable farming model.