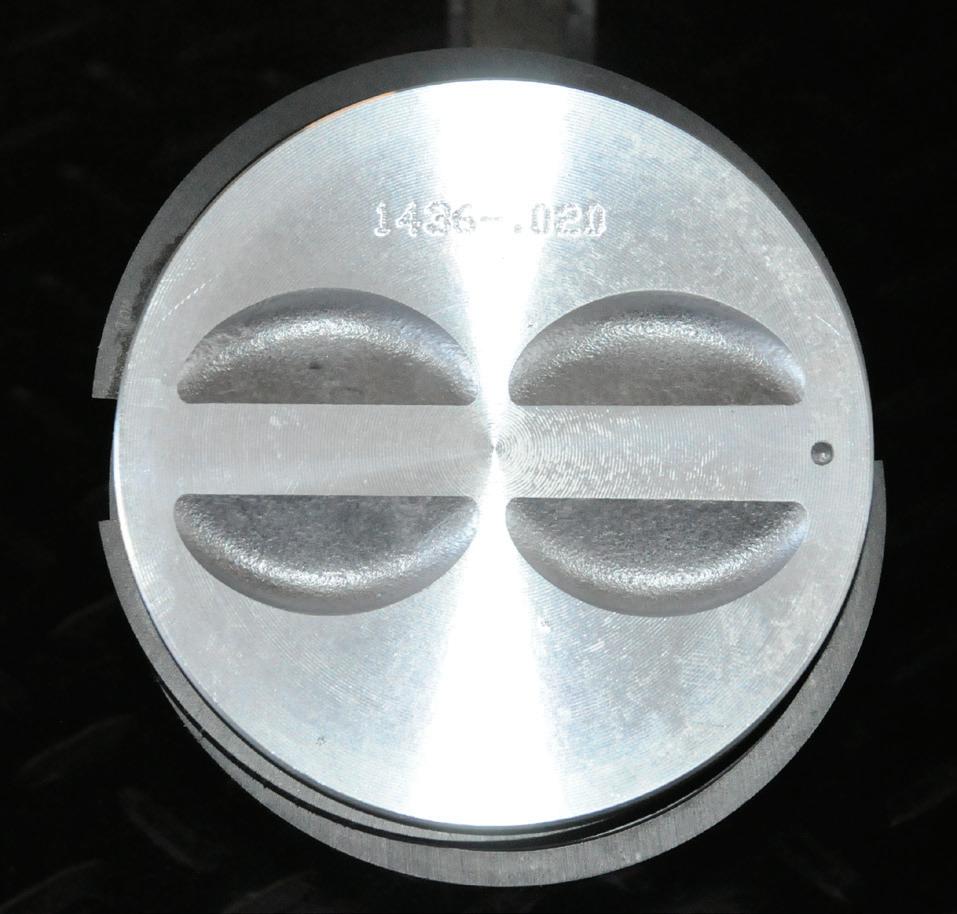
11 minute read
ALL ABOUT PISTONS
IF WE KEEP LOOKING at engine systems and components from a macro level, we tend to lose important details. That is the main reason for looking at a micro level, it can bring out more detail and consequently a greater level of understanding and transfer of knowledge, which is important in the search for durability and development of power. Pistons are an engine component that few really understand.
Engine builders undertake a great deal of effort and expense machining cylinder bores to correct sizes and then even more effort getting the surface finish of the cylinders to a point where “they feel” they get the best performance/durability and advantage over the competition. This feeling is often accompanied by a stack of empirical data. I have seen some builders who prefer a fine cross-hatch pattern and others who prefer a rough cross-hatch pattern on the cylinder surface. Others want a polished surface and they undergo great pains to achieve the surface they want. They strive to get the dimension the same at the top, the middle and the bottom of the cylinder. From the engine builders perspective, it is critical that the cylinder is round and has the surface finish they require. However, pistons placed in those highly machined cylinder bores are far from round. They are a different diameter at the top than at the bottom and they are not even close to round. They are machined with the application in mind. The environment pistons work in is very severe. Temperatures are extreme. They start out at ambient temperature and the temperature rises quickly and the Delta in temperatures is all over the map. Lubrication can be heavy or light and it can vary from cylinder to cylinder.
Advertisement
Prior to exploring more about pistons, let’s get into some specific vocabulary as it relates to the piston:
Crown or Dome The crown of the piston is simply the top of the piston, the part you see when looking into the cylinder from above with the head (s) removed. The crown can be flat, flat with cut outs for valve clearances or they can have a pop up on the crown to develop a greater level of compression and as we all know, “Compression is the cornucopia of horsepower”.
Wrist Pin Bore This is the hole in the piston where the wrist pin is inserted, the wrist pin is how the piston is attached to the connecting rod. Many times, the wrist pin bore is off set from the center of the piston to help with the minimization or equalization of thrust loads. Not all pistons have an offset built/designed in. In some engines, this also reduces the potential for clatter or the mechanical noise that can come from the change in angles during the movement of the piston as it travels through the bore.
Ring Lands These are the horizontal groves cut into the piston where the rings are installed. These groves are critical to piston operation. They need to be very flat on the top and bottom of the groove to facilitate the ring (s) ability to seal. Yes, rings seal on the O.D. (Outside diameter, where the ring meets the cylinder and they also seal on the top and bottom of the ring against the piston.) There is actually more sealing area in the ring groves than the OD of the piston. The flatness of the ring groove is also critical dimension. We could spend a good deal of time discussing the importance of the flatness of the ring grooves and how they impact the ability of the rings to do the job they have to accomplish. (Should be a separate article.)
The crown of the piston is simply the top of the piston. This is where much of the forces that act against the piston are transferred to the piston, not all but most of the forces. The eye-lid looking cuts on the crown are for valve clearance. Depending on the lift and duration of the cam shaft there may be some clearance issues that necessitate that the crown be machined to accommodate valve clearances. Having the valves contact the piston is a bad thing.
Skirt The area of the piston below the ring lands. It is this area that absorbs the majority of the thrust loads and helps to keep the piston moving in a motion that is parallel to the cylinder bore and helps keep the rings square to the bore. For the two or three of you who might possibly care, the skirt does not really continue all around the piston, it is located parallel to the wrist pin bore. This is a critical fit up area of the piston to the cylinder, it is critical with relation to operational success. Too much clearance and the piston rocks in the bore and an excessive amount of thrust is generated against the skirt. If the piston rocks too much in the bore, the rings will not seal as well and power and durability are impacted; if there is not enough clearance, the piston will seize in the bore. Neither one is a good outcome.
Low friction coatings A fairly new addition, these coatings started showing up about 30 years ago, not exactly new from a time perspective but in the timeline for internal combustion engines it is new. These special coatings are usually applied to the skirt of the piston not to the whole surface of the piston. These coatings are usually limited to the thrust sides of the piston, the skirt area. They help the piston avoid scuffs and excessive wear during break in and normal operation. For the most part the piston manufacturers who coat pistons usually do so with coatings that are usually proprietary and we just have to accept that they will do the job they are intended for and take the piston makers word for the performance increase that these coatings offer. Some other makers are more forth coming about the makeup of the coatings. It is a classic case of buyer beware.
Thermal Coatings Again, these started showing up about 30 or so years ago. The intent is to reflect more of the heat from combustion back into the combustion chamber. A great idea from a purely technical perspective but not always something that shows increases in the dyno room. There are coatings that are used in aerospace engine applications, Turbine engine applications specifically, that allow turbine blades to survive in temperatures that are greater than the melting point of the metal they are coating. These are not or have not yet found wide spread applications in the automotive world.
Pistons live in a very hostile environment; it ranges from very hot and not so very hot over some small-time increments. The temperature varies and it does so constantly, under normal operating conditions. If we look at a Four Stroke engine, that is the intent of this discourse, during the inlet stroke the piston is “cooled” by the incoming fuel and air mixture, then as the air/fuel mixture is compressed during the compression stroke the piston is “warmed” up by the increasing temperature of the fuel air mixture during the compression stroke. Then the power stroke occurs and the fuel/air mixture is burned and the temperature skyrockets. Then, as the piston travels downwards in the cylinder, the temperature again starts to drop and then during the exhaust stroke the piston again starts the cooling cycle, this is repeated every two RPM. We need to remember that oil also plays a critical part in removing heat from the piston; either from special jets inside of the engine that spray oil on the piston and from the oil mist inside of the crankcase.
At the conclusion of every stroke, the piston comes to a stop, regardless of RPM, (Revolutions Per Minute). That is a dead stop at BDC (Bottom Dead Center) and TDC (Top Dead Center), so of that sixty second period of time, depending on RPM, just for easy math let’s say the engine is turning 5000 RPM that means in that minute of operating at that engine speed the piston will have stopped completely 10,000 times; each minute. The amount of dwell time, that is how long the piston remains at a stop in the bore at BDC and TDC varies based on a number of factors, Stroke, Rod Angle, (another topic for a different article). So, think about that as you start pushing the engine past it recommended RPM limit; there is a good deal of real world, highly stressful things happening in the world of pistons. We have temperature issues and physical issues just from rotating and pressure issues from combustion.
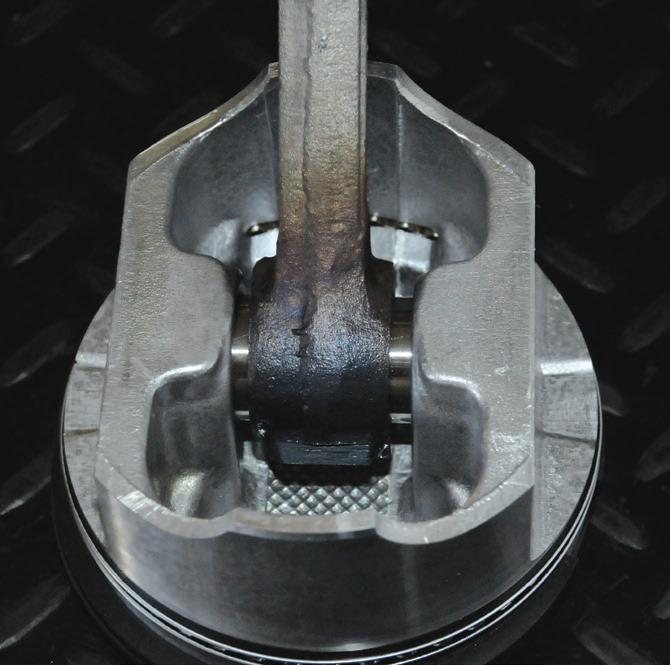
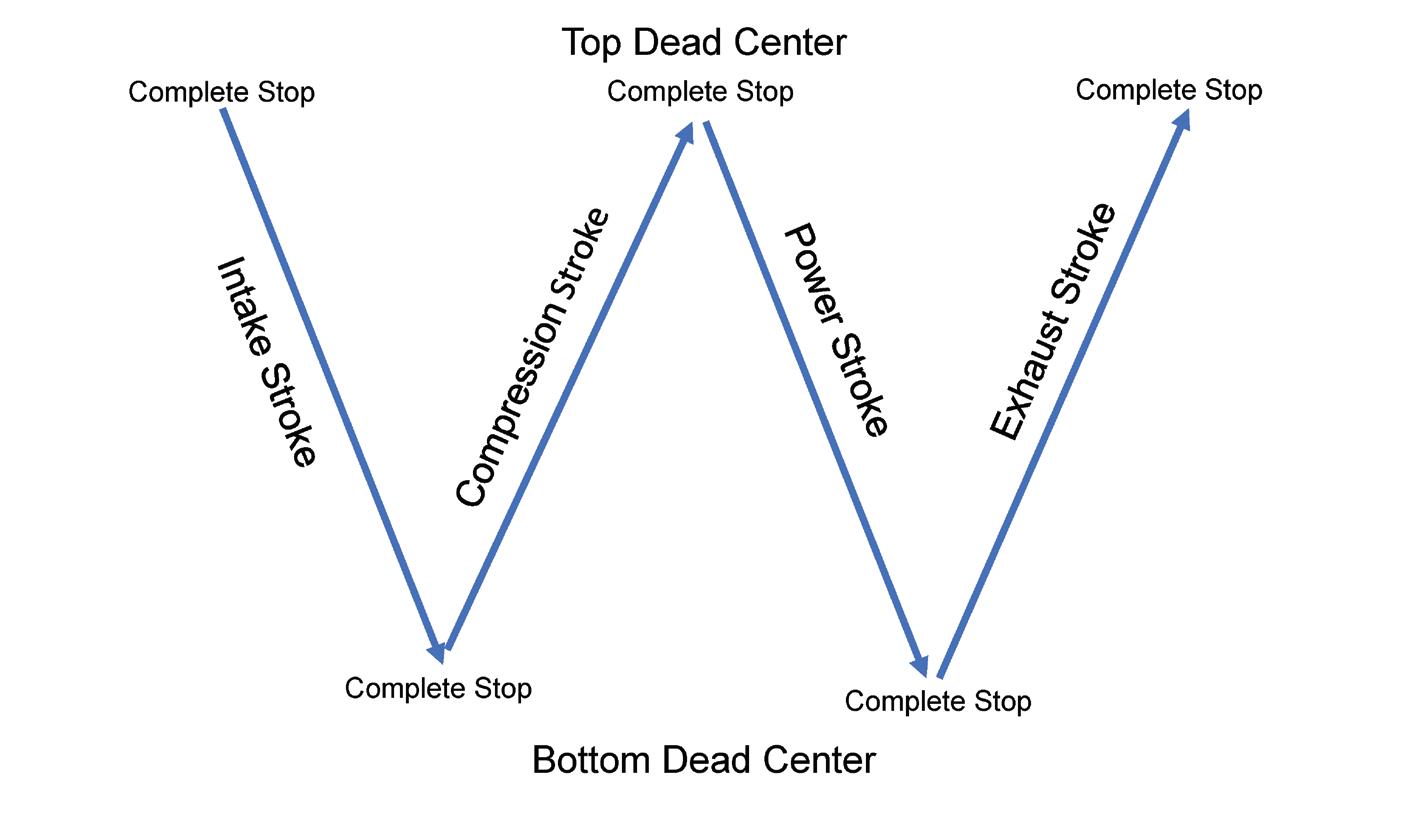
Something else to think about is the acceleration rate for the piston. Once it stops it has to start moving again and the rate of acceleration can be brutal. Not only is the piston accelerating from TDC but on each stroke the piston starts to slow down so it can stop at BDC. Once it slows to a stop at BDC the cycle starts all over again. There is a term, or more accurately an acronym, that describes what piston designers and engine builders use to help figure out just what kind of loads the piston goes through from a mechanical perspective relative to speed, MPS, Mean Piston Speed. This number is an average of the piston speed as it goes through the trip from TDC to BDC. As the piston is always accelerating or decelerating as it travels through its range of motion, Mean Piston Speed is a good way to look at just how fast the piston is traveling. The formula is: Mean Piston Speed in FPM (Feet Per Minute) is equal to: 2 X the stroke X engine speed (RPM) divided by 12 this gives you the value for, Feet Per Minute. (Disclaimer, I have a rule that you should never do math in public as there is always somebody who will say something about the process, no matter how right or wrong you are, but here goes.) So, if we have an engine with a 3.5-inch stroke running at 8500 RPM this is what you get: 2 X 3.5 x 8500 ÷ 12 = 4958.3333 Feet per minute. If you want to see this number in MPH you simply multiply the FPM times 60 then divide by 5280. For this calculation the MPH comes out to
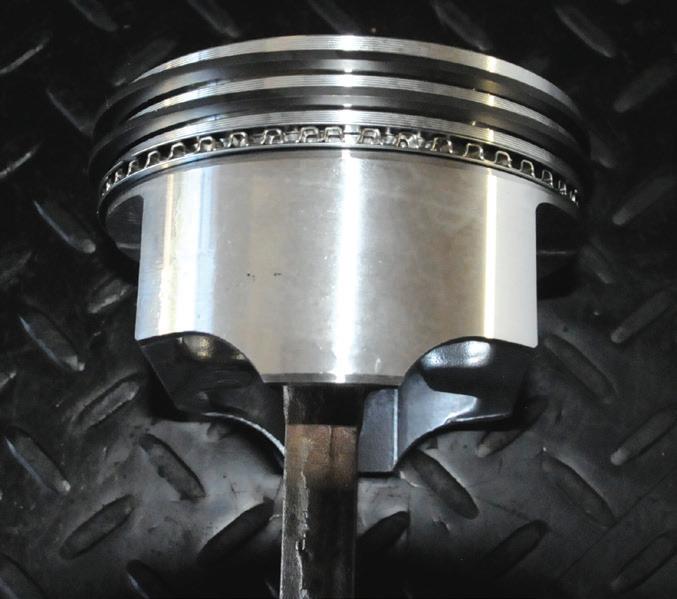
56.344 MPH for our virtual engine with a 3.5-inch stroke.
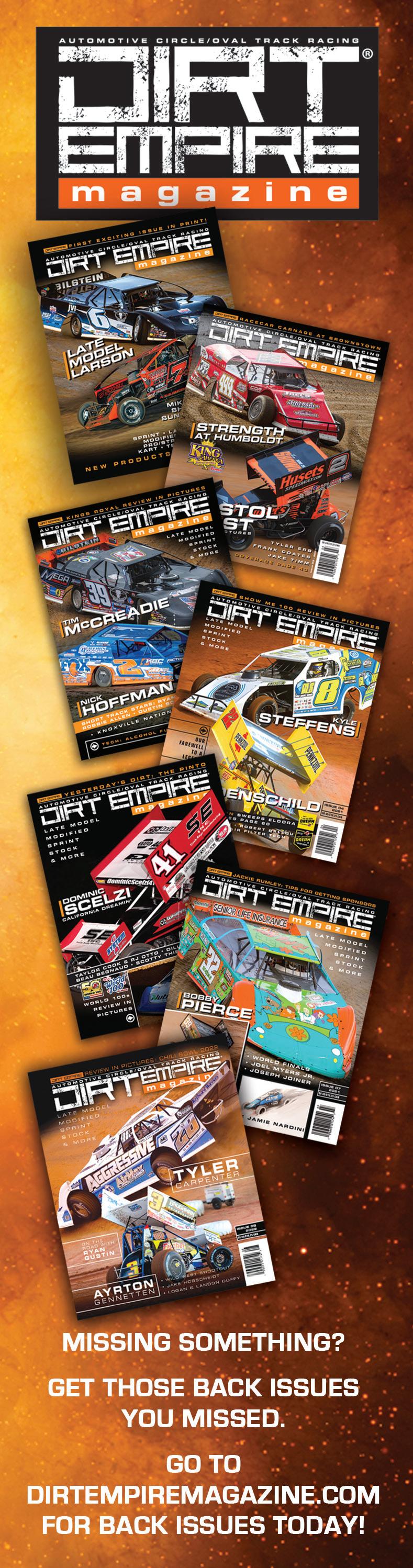
While this speed does not really sound like much, let’s put this number into perspective. Our virtual engine with the 3.5-inch stroke is running at 8500 RPM, that means the piston has an average speed of 56.344 MPH and it comes to a complete stop and accelerates to a Mean Speed of 56.344 MPH 283 times a second. When you put this in perspective, just think of how long it takes your car to accelerate to 56 MPH and then how long it takes to stop from that speed. The piston accomplishes this stop and start in 3.5 inches The forces are quite staggering. There is also a calculation for Maximum Piston Speed, MPS, but I think we have done enough math for today. (If you want to do some more math the formula for MPS can be found by doing a Google search.)
The forces acting on the piston are great, even in your daily driver, unless you are driving an electric car, the piston (s) operate in a very severe environment. If you experience detonation the loads and temperature extremes are even greater. If for any reason you experience detonation due to poor quality fuel for your given application, glowing carbon somewhere on the piston or cylinder head or too much ignition advance or just a case of overheating the coolant and the fuel air charge detonates. At this point the fuel/ air mixture does not burn in a controlled manner, but instead it explodes, just like a bomb. The environment becomes extremely dangerous to the piston (s) and the engine in general, very quickly. The heat during a detonation event skyrockets and the temperature can reach the level that the piston swells to an even greater extent in the bore, the protective layer of oil is burned away and the forces generated by the exploding fuel causes a hammer like physical loading, not a metaphor in this case, the explosion causes forces just like a hammer, a really big hammer, and the hammer is transferring extreme loads to the piston, rod (s) crankshaft and block. These are, or can be, engine ending loads. At the top of the piston the extra heat causes the piston to grow further and the friction rises between the piston and the cylinder walls and the temperatures get extreme enough to start burning the piston, not just melt the piston, but burn. Short story, detonation is not a good thing.
But everything is not doom and gloom. In a less severe operational environment, like the car you drive in daily use or a properly operating race engine, the working environment can be just as harsh but much more controlled and the piston can be expected to last a reasonable amount of time. In a racing environment, the operating conditions are much more extreme, with much higher loads, higher operating temperatures and a more hostile environment, but it can be controlled with proper care and tuning. Running an internal combustion engine is all about making and controlling heat
Let’s look at the piston from a physical perspective. As stated earlier, pistons are not round; in the truest sense of the word. Pistons are oval shaped and they are also for a lack of a better term are cone shaped. Now when you look at a piston they look round and they appear to have straight sides, which would lead you to believe that they are almost square when viewed from the side. If we take a piston and place it on its side and roll it across a table it will roll to either to the left or right, depending on how the piston is orientation to the table. The same way that stagger impacts a race car. Pistons are also a good bit smaller at the top of the crown than at the bottom of the skirt. This will vary by piston manufacture, type of aluminum used, the intended application and if it is a cast or a forged piston. So now we have introduced more variation to the topic. As the piston rolls it will also wobble as it is not round either it will wobble as it rolls, not a great deal, but it will wobble.
Pistons are not Rocket science but it is a close cousin. There is a good deal to know about the selection and operational environment of a modern piston. There is a good bit of development still taking place on piston design, manufacturing and operation. Even with the looming electrification of transportation; pistons will be around for a good bit of time. If you want to see some great designs of pistons look at some of the modern Four Stroke Motocross bikes. You will find pistons that make the pistons used in the engines coming from the car manufactures look like polished stones. And the Pistons used in Formula 1 are works of Modern Art, 100% machined from billet stock they are a wonder to behold and the ones we are able to see are usually several years old and not the most current example of the state of pistons. They keep this technology under wraps. Just like everything else in the world, the complexity level comes down the more you know. It is not magic, it just seems like it. Do not be fooled, pistons are far from a simple part of the engine but once you know a few things the part becomes less daunting and very understandable. It really is just that simple.
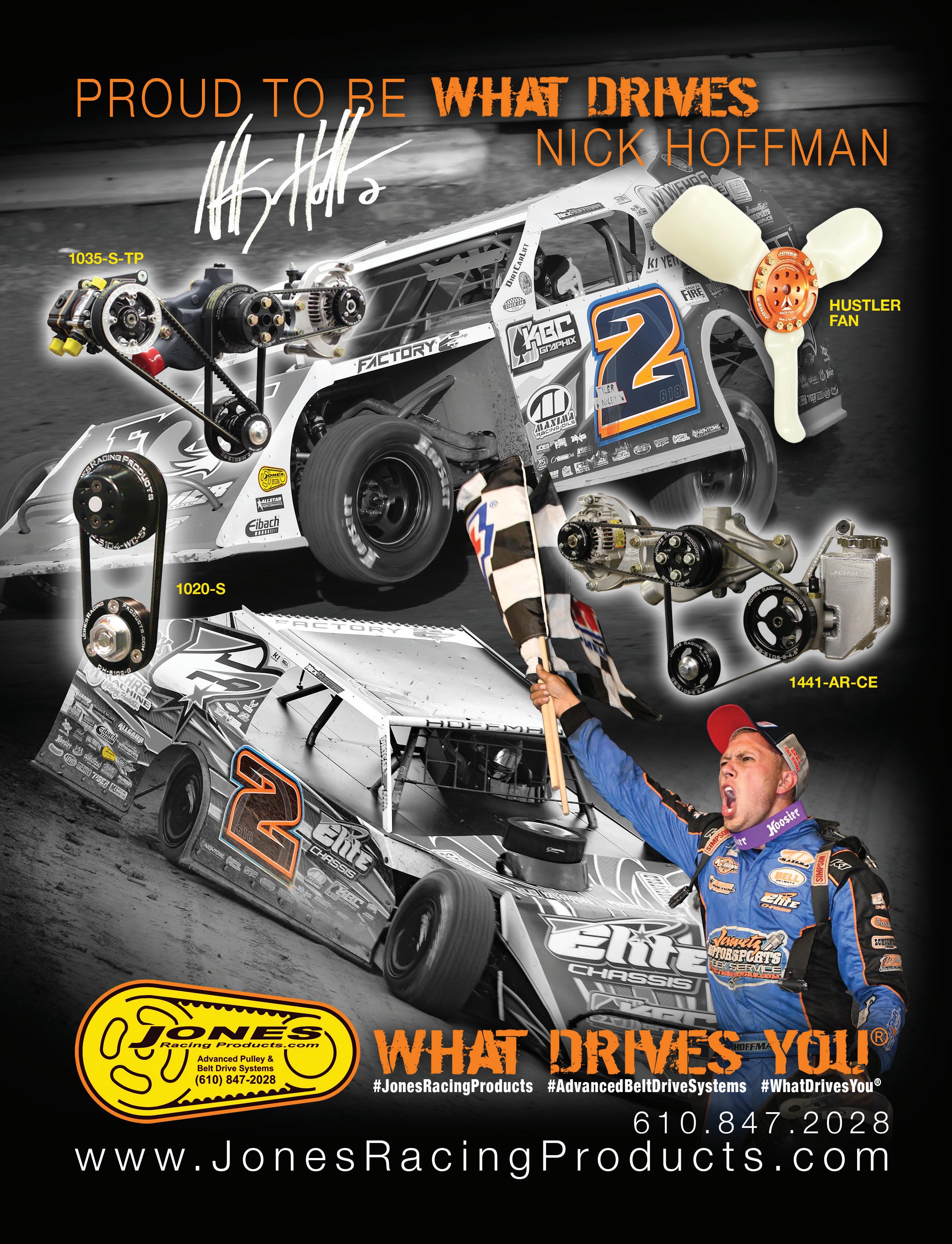