
9 minute read
Talking Tech
measuring TECH
Photos & Text by Vahok Hill
This assortment may be the only types of measurement tools you will need in the shop to help maintain your car form a measurement perspective. The trick is to know when you need a different type of measurement tool or one that has a higher resolution.
WITHIN THE RACING WORLD,
measurement is a very important part of the overall racing process. Racers measure everything - lap times, tire pressures, and so on. From a mechanical perspective, measuring is not that difficult of a process. You just need to make sure that you are using the correct tool to measure. Just like you would not want to measure lap times with just the second hand of your watch you will not measure push rod length with a tape measure. You have to pick the correct tool for the job.
Measurement resolution is a topic that needs to be discussed at the onset. You need to understand the resolution of a measurement. In the past I have had people come to me that want me to make a widget for them and we have a conversation and they tell me that the tolerance for a specific dimension is 0.0002 + or - .000001. At that point I smile and tell them they cannot afford that kind of tolerance and I would be guessing that they do not have the ability or the tooling to measure to that fine of a tolerance. For 99.99% of the precision tolerance that the Saturday Night racer needs to measure will be in the thousands range, three decimal points to the right.
As the conversation moves toward precision measurement, the list of tools available to the weekly racer is as broad as are the prices. We can use micrometers to measure the Outside Diameter (O.D.) of shafts and the thickness of shims or sheet metal. While a micrometer can measure both of these two types of parts with great success, we need to understand the level of accuracy required for such a measurement. If we are measuring the So, when you hear about a dimension or O.D. of a tube used in the construction a clearance for main bearing to the crank of a bumper or a frame member we shaft of 0.0025 you have an idea how could utilize a tape measure to measure close those clearances really operate. the cross section of a tube and be quite For the Saturday Night racer, you comfortable with the level of accuracy. may never have a need to measure to However, if you were measuring a bearing a resolution of the fourth decimal place journal, a tape measure is not the tool but it does not hurt to understand how you would use, even a dial caliper is not to accomplish this kind of measurement. appropriate for this type of measurement. In general terms, unless you are building You would want to use a micrometer. engines and the related accessories,
The trick when approaching any gear boxes and or rear ends you will not measurement is to ask the right questions. really need to purchase any ultra precision How critical is this measurement? The measuring tools. answer to that question will drive you to From a day-to-day perspective, a set the type of tool you should be using to of 6-inch dial calipers, a simple dial measure. The only boundary to the tools indicator with some holding brackets and you can purchase is your budget. a magnetic base, a 6-inch drop mic with a
If you are building engines, you need magnetic base will cover 99% of the needs a level of accuracy that will give you of a Saturday night racer. These tools can very exact and precise measurements. be purchased for less than $300 and they If a bearing journal has to be 2.000 in will last forever with a modicum of care. diameter, you will need to use a tool that measures at least to the third decimal place. If your tool only measures to the second decimal place, you will be having some real issues. Generally speaking; most quality micrometers will measure to the 4th decimal place. This is commonly called measuring to tenths. In reference to tenths of thousands of an inch or 0.0001, a human hair The set of snap gauges that have been in use for the past 40 has a range of diameter years. Keep them clean, oiled and well cared for and they will from 0.0015 to 0.0021. last longer than you.
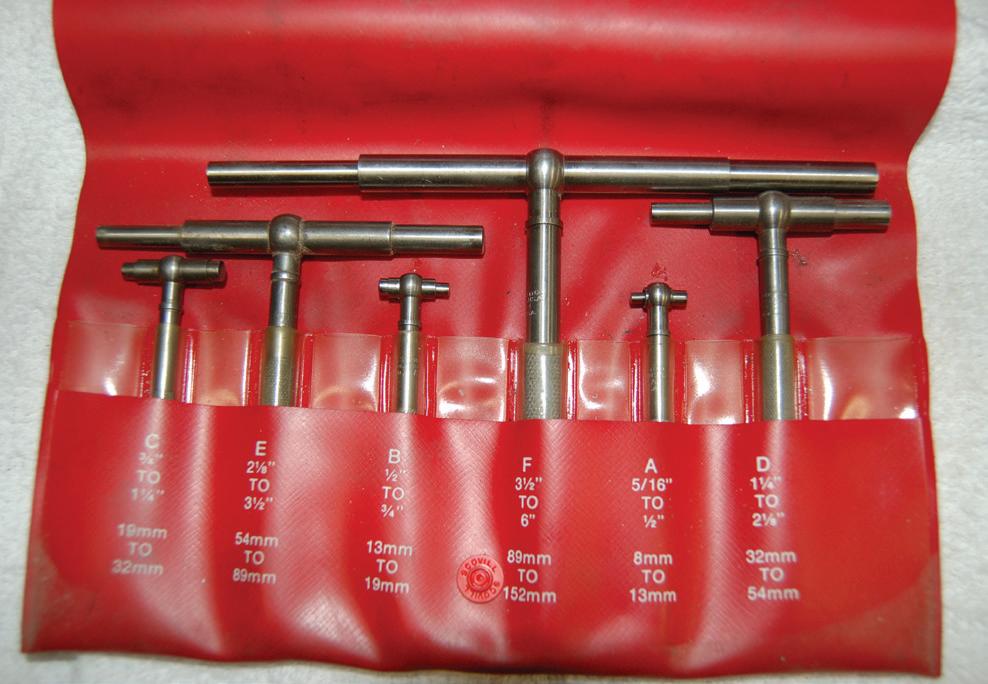
If you start to build your own engines you still may not be required to purchase the complement of tools designed for the engine builder. The reason is that many of the ultra precision functions will be performed, most likely, by an outside engine machine shop and they will handle the majority of the precision measurements.
LIST OF TOOLS FOR A SATURDAY NIGHT RACER
Together we can go down the list of tools that a Saturday night racer should consider the minimum requirements and we can talk about the costs involved.
For measuring outside diameters, (ODs), shims and lengths (within reason, 1 foot and under) and just general measurement you should have at the least a set of sixinch dial calipers. This tool will provide a fast, easy to read measurement and it has resolution to the 3rd decimal place. This is probably one of the most versatile measuring tools you can get and they are very reasonable to purchase. They range in price from $20 to $100 each. In my experience the units costing more do not measure any better or with any greater accuracy. A set of C Micrometers or “C Mics” will handle a broad range of measurement jobs that would call for a higher level of resolution and accuracy. For the racer, a set of three micrometers that range from 0-1, 0-2 and 0-3 to inches is probably more than you will ever need. These can be purchased for about $40 to $55 dollars each and you might even be able to purchase a pre-bundled set for even less per-micrometer. For example, on cost, I was using a set of telescoping gauges, Starrett brand Snap Gauges, the other day and the receipt was still in the box, these were a set of Starrett gauges and I paid $63.78 for the set of six in 1981. They still work great and are in like new condition. Today, 40 years later, a new set is over $300 for the same set. So, this can give you some perspective on cost and the cost of quality.
You need a simple dial indicator for measuring surface parallelism on parts that move like the discs on your brake system or measuring endplay on a gear shaft or crankshaft end play. These are very inexpensive for the level of measurement the Saturday Night racer needs. The dial indicator is reasonably inexpensive but it requires some additional tooling to hold the indicator while the measurement is taking place. The cost for the indicator and the associated tooling will cost in the $60 to $100 range.
Measuring into holes to check depth is the job of a depth micrometer. You can also use the tail of a six-inch caliper to measure hole depths in a pinch but for a truly accurate measurement you will need either a set of depth micrometers or a drop micrometer. A good depth Micrometer can be purchased in a set with up to six rods that are interchangeable and will give you a range of measurement capability from 0 to 1 inch all the way to 0 to 6 inches in depth. The costs will range from $60 to well over $500 dollars.
Measuring inside diameters brings up a whole different set of problems. When dealing with holes, there is a larger group of different parameters that may not concern us like roundness, taper, concentricity and placement in relation to other holes. If all we want to know is the diameter from a general perspective, our set of six-inch calipers can measure an inside diameter but it can only tell you the size of the hole from an edge-toedge perspective. This is fine if all you are measuring is a hole size to see how big of a drill bit is required to drill another hole or to get the size of a hole to tell what size bolt will fit that hole.
From a more precision perspective, if we are concerned about the circularity and the size of the hole, we will use a dial bore to check the size and the circularity or the


When measuring the outside diameter of a hunk of metal, sometimes a caliper will provide a measure that is close enough to make the job faster to complete. If a higher level of precision is required, a micrometer may be the better answer. low buck method would be to use a set of snap gauges and a dial caliper or a set of “C” mics to determine the hole size and circularity but this method has some real drawbacks. It takes a long time and the results are dependent on operator skill, not just the robustness of the process. If we are measuring a cylinder bore for a NASCAR Cup engine, this would not be the method of choice. To measure this type of ID, you really need a dial bore gauge. This tool will tell you how round a bore is as well as the size. I am sure that the use of a profilometer to measure surface would be called in to use to measure the surface finish of each bore. But for the Saturday night racer this would not be a requirement.
The problem with a dial bore is that you need a master dimension to set the tool. Usually this is accomplished with a set of Johannson Blocks or JO Blocks. What Jo Blocks are is a set of ultra precision steel blocks that are ground flat on all sides marked for their individual dimensions and they are assembled together to establish a known dimension. Once this dimension is set you then set your dial bore within the confines of the Jo Blocks to establish the “Zero Point” for your dial bore. Once this is accomplished the dial bore can be placed in the bore and any deviation + or – the zero point gives you the size and the circularity of the hole you are measuring. This works very well for engine blocks and measuring any bore on the engine, cylinder, lifter, main bearing and cam bearing bores. A dial bore is an expensive tool and even more so when you consider the cost of a set of JO Blocks. You can spend upwards of $500 very quickly before you are done. There are alternatives to JO Blocks but they never seem to be as repeatable or as reliable. You can use a “C” micrometer to set a dial bore but it requires a good deal of experience and it is just not the best method.
Using measurement tools is not difficult, it just takes some time to learn the process so you get accurate measurements. Another major consideration is selecting the correct tool for the job; this will make sure you are not trying to use a tool that will give you greater measurement resolution than you really need. It really is just that simple.
The author can be reached at Vahok.Hill@cox.net