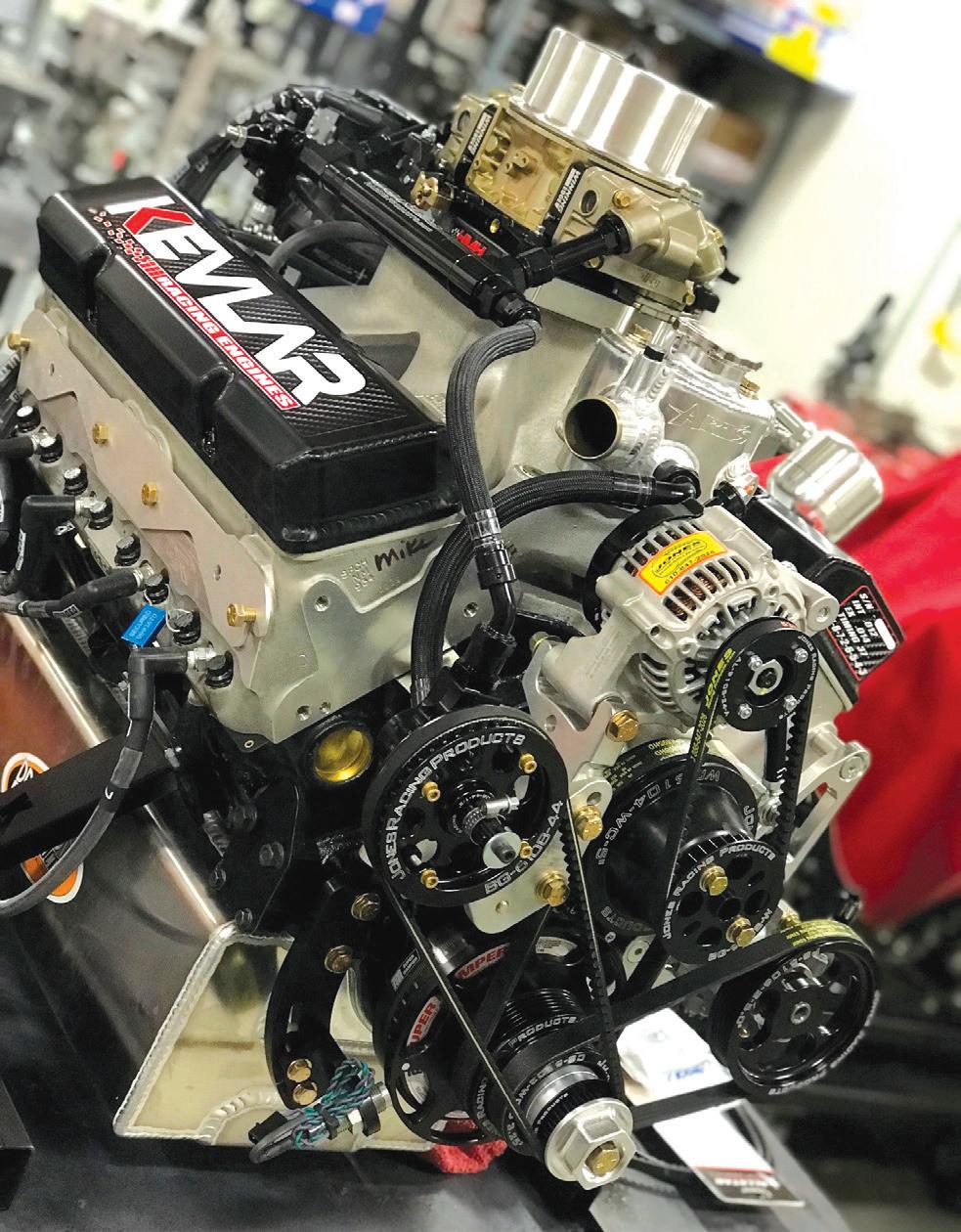
2 minute read
KEVLAR RACING ENGINES BIG BLOCK BUILDER
KEVLAR RACING ENGINES have been building engines primarily used in the Northeast Modified racing scene for nearly a decade and a half. Big-block engines are their specialty, but they also build the DIRTcar spec 358 small block engines as well as 360 and 410 sprint car engines. All in all, Kevlar puts out roughly 40-45 newly built and rebuilt engines annually, by three full time workers at the shop, with 60-75 engines out in the field at any given time throughout the year.
The Kevlar shop is located in Volney, New York, a small town near Fulton, New York. This is right in the heart of big-block racing country with Fulton Speedway, Brewerton Speedway, Oswego Speedway, Weedsport Speedway, Land of Legends Speedway in Canindaigua, NY and Can-Am Speedway in LaFargeville, NY all within less than an hour and a half drive.
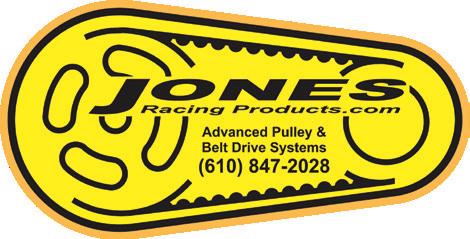
Kevlar Racing engines power the LJL Racing team cars sponsored by Gypsum Express, which is owned by John Wight. Gypsum Express is a leading trucking company with over 650 tractors, 11 terminals in ten states and over 750 employees. John’s love of trucking and racing led him to create the LJL Racing Team which started building LJL Racing Engines which later became Kevlar Racing Engines to separate it a bit from the racing team, as more and more teams wanted a Kevlar power plant under their hoods as well.
The house drivers include Larry Wight and Chris Hile, and in the past has included Billy Decker and Hall of Famer Pat Ward. It provides a great advantage to have excellent drivers as part of the house team. The feedback provided on engine tweaks or new builds allows Kevlar to continue to advance with technology and new innovations.
Rob Hile, brother to driver Chris, started with Kevlar roughly five years ago and handles most of the machining as well as dyno testing, purchasing and anything else that needs doing (including talking about the company
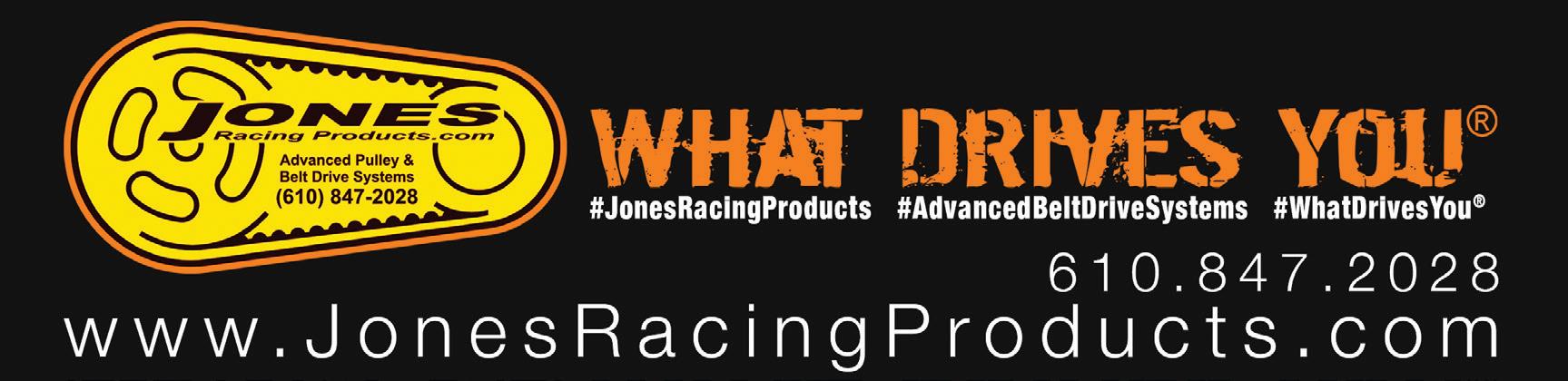
“We recently came out with a new big-block package,” Hile said. “This is a completely new package from what was available previously. We had it last year and Larry took it out and ran it, giving us feedback. We were able to tweak it at the end of last year and get it to where we wanted it to be. What we had before was good, but with this new package we’ve managed to make it even better.”
Kevlar utilizes CNC machining to lighten the big-blocks built in-house. They also focus on using only the best components for their builds.
“Jones Racing Products, Winning Edge Carburation, Mikes Racing Heads, Henrys Exhaust and Headers, Arts Radiator Expansions Tanks, Brown and Miller Racing Solutions hoses, Olson Fabrication Pans and valve covers, Dart Machinery Blocks; we only work with the best,” Hile said. “We exclusively use these vendors on every engine we build.”
More than simply using components from the best vendors, Kevlar builds close relationships with its suppliers so as to provide their customers with the best options available.
“I remember when I first met CJ and Melanie from Jones Racing Products,”
Hile recalled. “We were at the Charlotte World Finals with the Gypsum Racing team and CJ and Melanie came up to us in the pits, this is years ago, and just wanted to make sure we had everything we needed to race. I always thought that was just good customer relations – they didn’t just sell us their products and that was that, they were interested in making sure we had everything we could possibly need to go out there and compete. We try to do the same for our customers.”
There are no real secrets to the success of Kevlar engines – knowledge, hard work, innovation and ingenuity all pour into each build. With drivers like Larry Wight and Chris Hile vying for track championships, it’s clear Kevlar Racing Engines get it done.
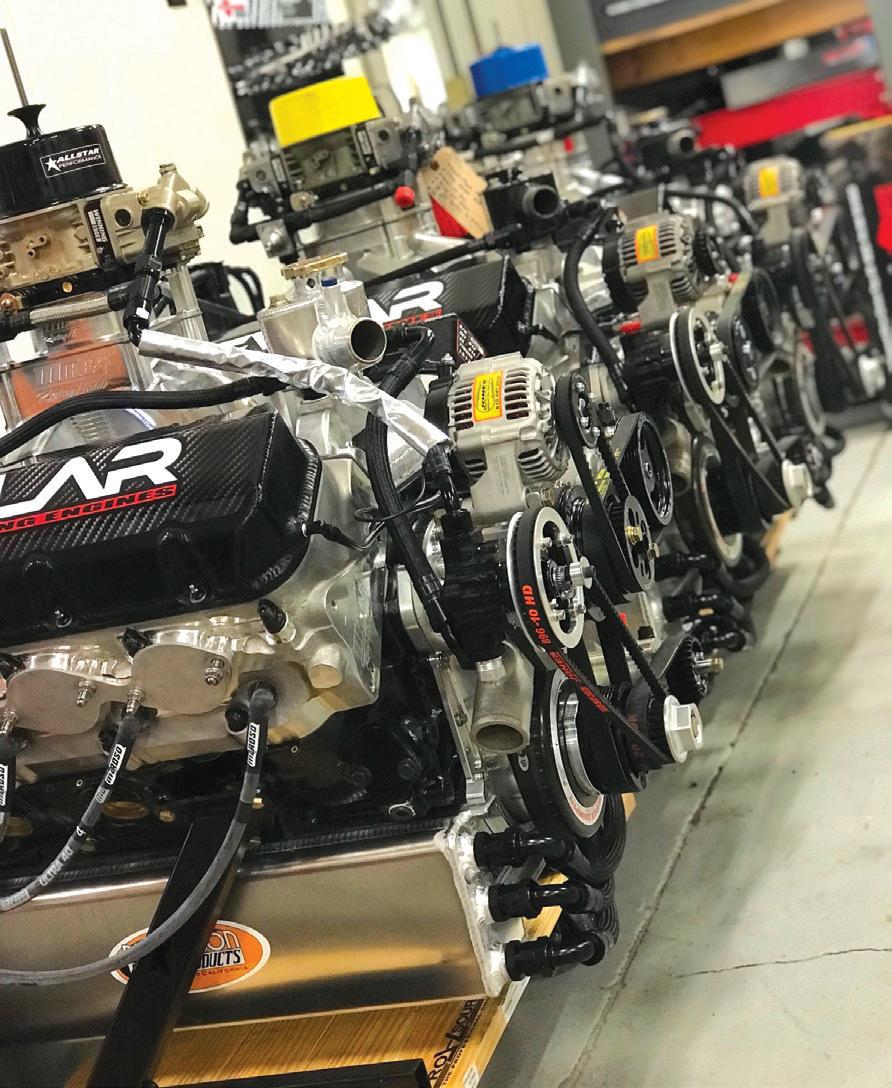
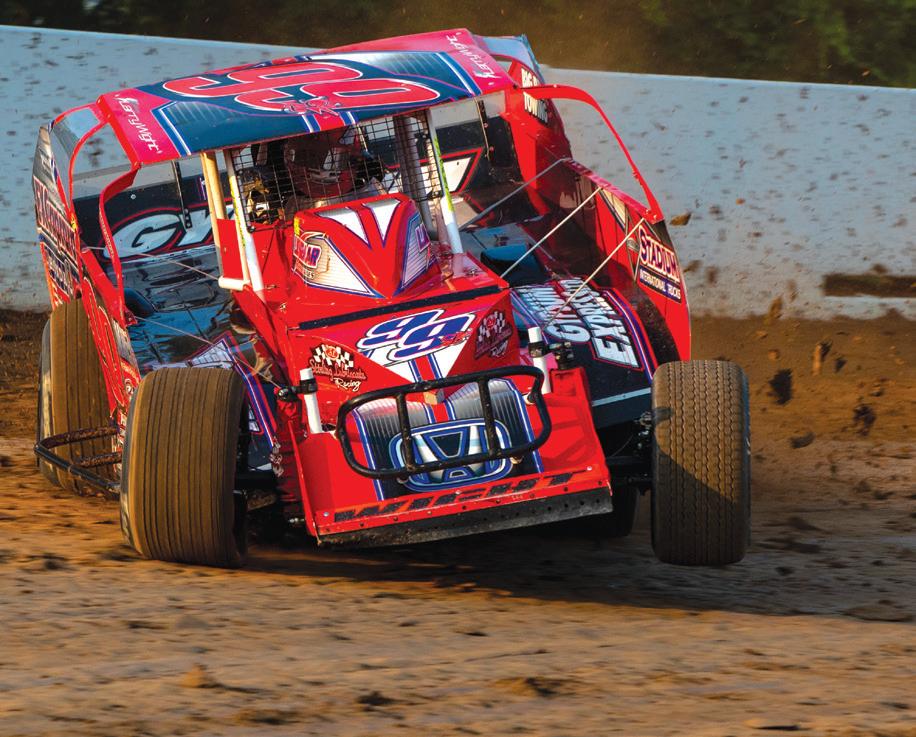
