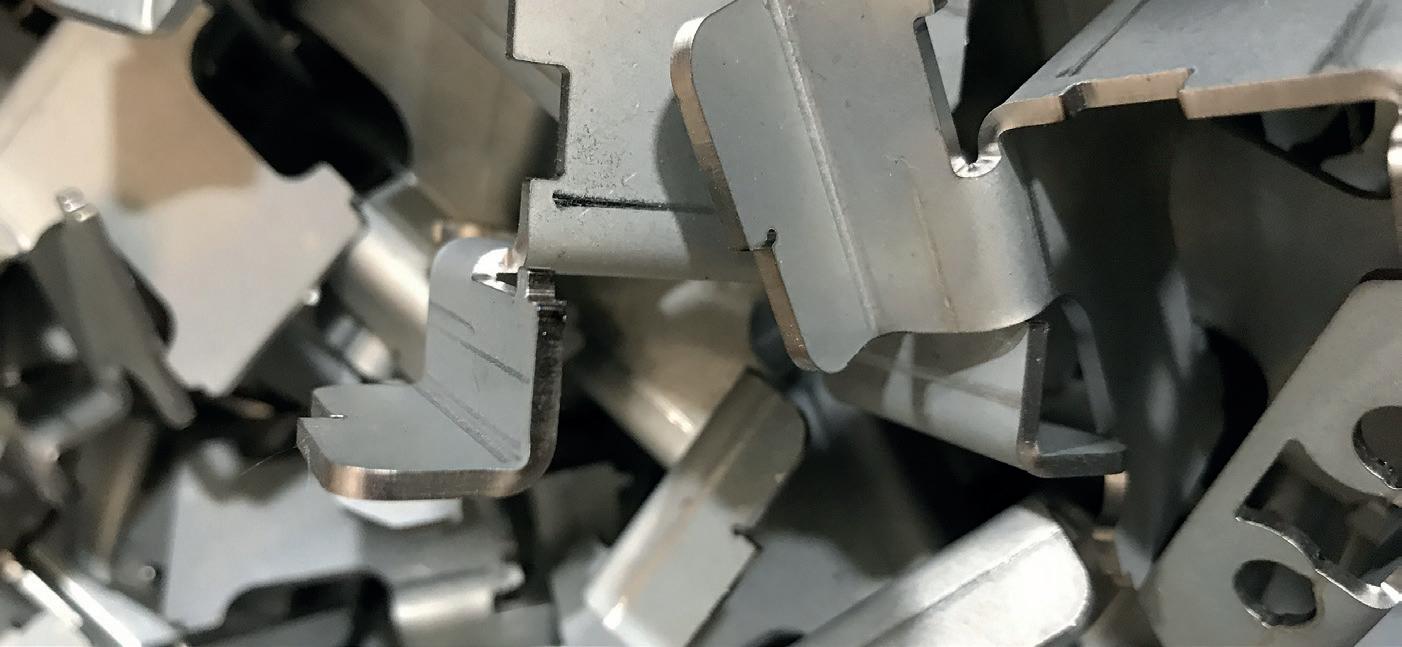
4 minute read
big interview
Sheet metal specialists shows their true mettle
Sheet metal engineering and fabrication specialist Stevens Rowsell (Precision) Ltd provides high tech manufacturing services at its cutting edge 20,000sqft factory in Hastings.
Advertisement
Kelly Sweetman
Owner - Director
Its three owner-directors – Kelly Sweetman, Barry Douch and Michael Gough - and 17 members of staff offer the best in laser cutting, punching, folding, welding, assembly and powder coating.
All they are waiting for now is a little bit of normality to return. “I don’t think we’ll return to pre-Covid levels until next year at the earliest,” said Kelly. “That will be two whole years of living very much hand to mouth.
“We’re taking each day and month as it comes – protecting the business is first and foremost.”
The business was started in the 1967 by one Ian Rowsell, quite literally in a shed in his back garden. At the turn of the Millennium, he sold it to an investment businessman – a Geordie shipbuilder by trade – who subsequently sold it on to the current owners in what was a management buy-out, in 2017.
While Michael looks after the engineering and manufacturing on the shop floor, Barry is responsible for quality control, health & safety and sales development, and Kelly, who has been with the company since 2002, takes care of the admin side of things, including finance, human resources and customer service.
Together the trio have turned Stevens Rowsell into a well-equipped factory capable of taking the most basic of scribbled ideas to the most detailed of product design through to the point of sale.
Kelly said: “If the product has electrics, we can arrange that too. We were determined to be a one-stop shop, so our customers don’t have to go to two or three different places to get their product made.
“We predominantly focus on the batch production of general and fine limit sheet metal components, but we can also work on everything from initial prototype through to contract production.
“The factory and plant layout we have here has been designed according to lean manufacturing ideology, giving us an efficient and effective operation.” That includes equipment which enables Stevens Rowsell to do its own powder coating, something the team had previously spent £160,000 a year outsourcing. She said: “When you sub processes out, you lose full control over time and quality and when you are selling your services based on quality, that’s no good, so we installed the powder coating plant. “We started off with an electro-static spray booth and an oven. Now, we have two spray booths, two ovens, a conveyor belt and an automatic washing machine. “The investment would have paid for itself by now if it wasn’t for Covid.” The installation of a new Trumpf 4kw laser cutting cell – one of the largest sub-contract manufacturing facility of its kind in the UK – represents another major investment. A 1000sq.ft extension was built to accommodate it.
The cell incorporates two eight-metre high material storage towers and a handling system that automatically feeds the flat bed laser, allowing sheet metal to be cut without any loading/unloading interruption or the downtime associated with the operator fetching sheets from the traditional racking store.
“The Trumpf laser cell provides us with a high speed and cost effective form of profiling sheet metal which ensures that the work we produce has a high-quality, oxidefree finish,” said Kelly. “We also operate latest generation software which automatically nests part profiles from different jobs on the same sheet, maximising sheet usage and reducing wastage. “This software coupled with the laser technology we employ helps us offer highly competitive pricing and a genuine value for money option.” While most of their customers tend to opt for the whole package in terms of service, some do just want to make use of individual elements, perhaps the powder coating or machining of components. “Quality benchmarking – a lot of our customers, in sectors ranging from automotive to green energy and everything in between, want that,” she said.
This past year has tested Stevens Rowsell itself to the hilt, of course. On the one hand, they are lucky in that the factory is big enough to allow for generous social distancing, a godsend when staff cannot work from home. But on the other, the work hasn’t been there for them to do in the first place. “Our customers closed their doors and our order books became depleted,” she said. “We had no sales at all two months running.” They used the furlough scheme and made a number of staff redundant to keep the wolf from the door.
Although they are now back up and running, Kelly is very aware of the uncertainty surrounding them in the manufacturing sector. “People question whether this freedom is going to last or if there is going to be another lockdown … It’s affecting everybody. “You feel things are starting to move again and then there’s another announcement, about the Delta variation or some such, and confidence falls off a cliff again.” The effects of Brexit have been lost in the pandemic, she adds. It’s hard to tell which one is responsible for some of the results she’s seeing. Stevens Rowsell is looking to the future and on a recruitment drive, but Kelly has received no responses to the five job adverts she had published the previous week. Recruitment is just one of the areas of business that has suddenly become a whole lot harder.