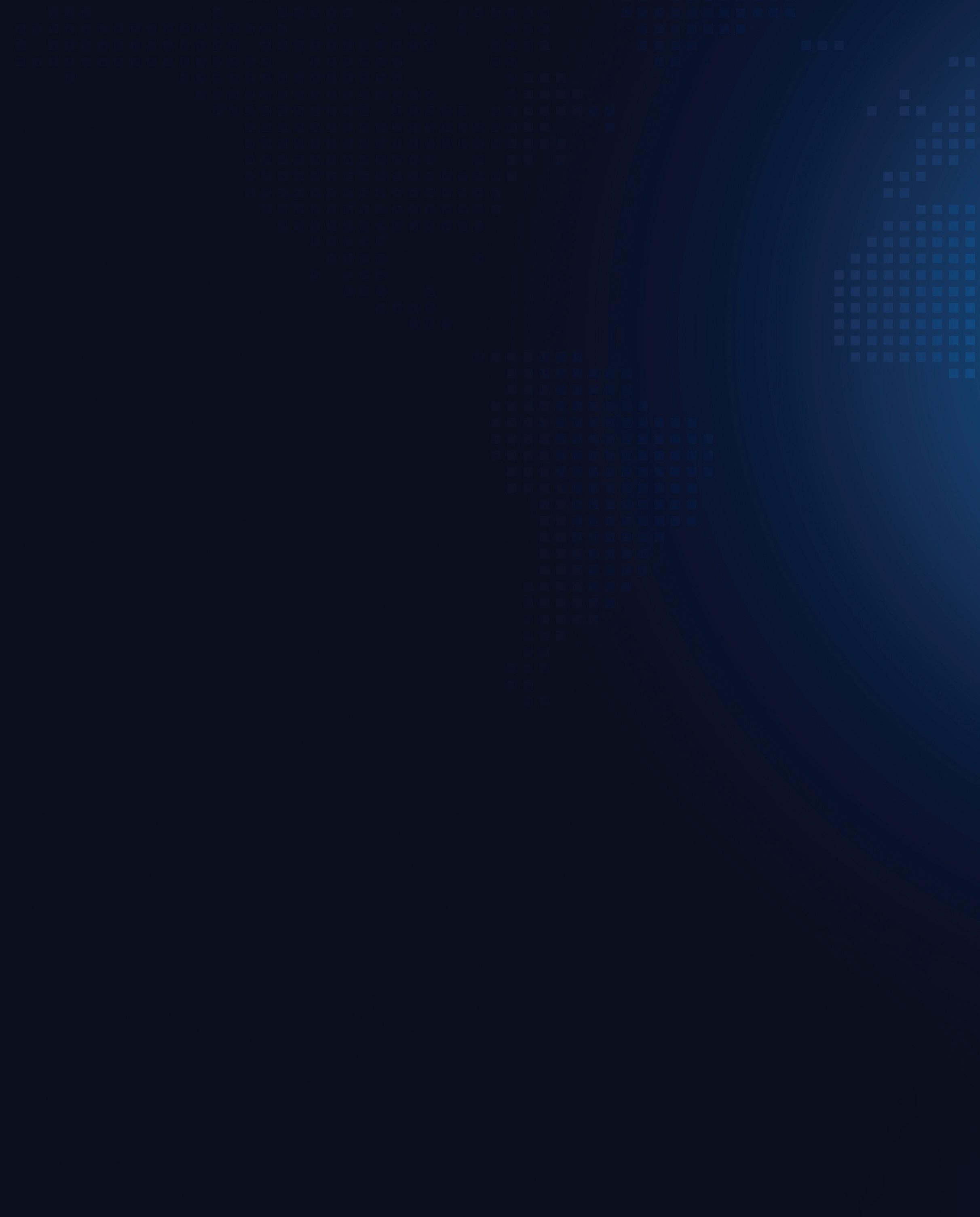
5 minute read
Software automation
Investment in process control can achieve sustainability goals
Investment in process control and smart digital technologies can help brownfield sites achieve production efficiencies and achieve sustainability goals, says Steve Leech, Business Manager, Process Control Systems UK & Ireland, Siemens Digital Industries
Advertisement
In March this year the government launched its industrial decarbonisation strategy, putting the chemical and pharma sectors at the heart of its plan for the green industrial revolution to propel the UK forward towards its 2050 net zero target. The strategy talked about how the next decade will be crucial to lay the bedrock for industrial decarbonisation and begin the journey of switching away from fossil fuel combustion to low carbon alternatives such as hydrogen and electrification, deploying key technologies such as carbon capture, usage and storage, and supporting industrial sites to maximise their energy and resource efficiency to reduce costs for businesses. It prioritised growth in digitalisation and the development of industrial digital technologies, citing digital twin technology and artificial intelligence as opportunities to have a growing contribution to the strategy. While industry 4.0 continues to remain at the forefront of this decarbonisation strategy there is lack of consistent investment into manufacturing, especially into brownfield sites.
In the chemical and pharmaceutical sectors, we have ageing assets that, while they produce the end product, these plants and factories do not look at how efficient they are, or could be.
Could there be more flexibility by investing considerably into technology? The answer is a simple, yes. Whilst a plant or factory may be manufacturing a certain product in a certain way, another producer, who has invested in digital tools and data analytics, is making that same product cheaper, faster and more efficiently. We simply can't just rely on ageing infrastructure to compete against that. For me the market has to start to look at control systems as real assets to their organisation in the same way that they would look at their business systems. For instance, investment in IT infrastructure is much higher and you will very rarely find a high-level system like an SAP running on an infrastructure that is between 10 and 15 years old. But in manufacturing it is quite common to see plants that have decades old operational technology that hasn’t been upgraded. The good news is that game-changing technologies that can simulate a process and improve efficiencies across production lines are available. What is needed is the mindset to really invest into the process and a planned approach to help organisations take advantage of the opportunity that comes just from the data gathered using AI or machine learning. This information can then be converted into actionable information that allows smart decisions that will ultimately impact production in a positive way. With very minimal investment plant operators can get a clear picture of how materials are being used and how energy efficient they are. This new transparency helps businesses establish sustainability goals and set them on the net zero path.
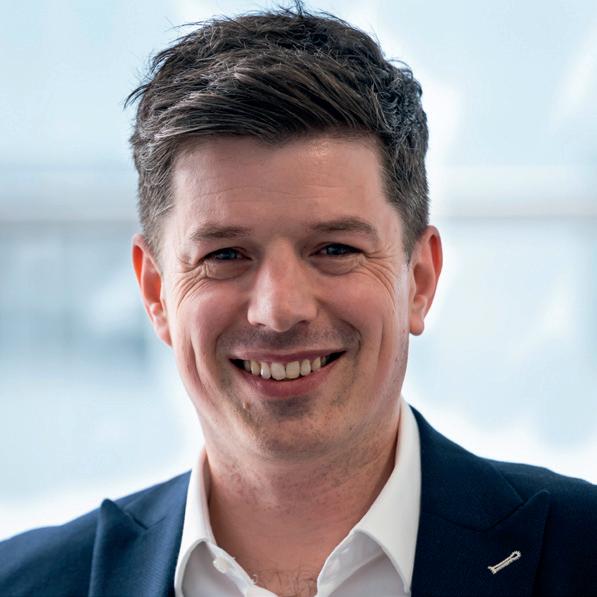
For instance, from a purely production perspective adopting more modern network-based technology like Profibus or Profinet gives way more information about what's going on in the field.
Facilities need to be kept up to date and relevant, and that means adopting and investing in new technologies. This can be illustrated by looking at how GEO® Specialty Chemicals (GEO) increased production of specialty monomers at its plant in Hythe. GEO develops and manufactures high purity chemicals, producing over 300 products for its customers in the coatings, adhesives, medical, water treatment and construction markets.
When the company opened a new production facility at its existing site it looked at enhancing and extending its capabilities, specifically for high purity specialty monomers It installed the SIMATIC S7 control system and WinCC, and a mixture of other technology solutions, to optimise how it makes its monomer products by managing processing equipment such as the reactor, vacuum system, temperature control unit, and charging systems. But within 12 months of commissioning GEO had reached production capacity and needed to scale up. The new production facility inside an existing building runs as a separate unit alongside the original. The key drivers for GEO were to scale up production, increase control, and have the ability to develop and optimise recipes in house rather than bring in third parties at a vast expense. As a top tier COMAH site handling inventories of high hazard chemicals, GEO also needed to ensure the highest level of safety controls, alarms and interlocks. After initially considering upgrading its control unit, it was proposed to deploy a complete solution based on integrated hardware and software, reconfiguring the plant and embedding the blending process into the new design. Commissioned in 2020, the solution included a total automation package utilising the SIMATIC PCS 7 distributed control system, SINAMICS variable speed drives, SIMOCODE motor starters and SIRIUS Low Voltage, SCALANCE network devices, and a complete range of Process Instrumentation, flow (Electromagnetic, Variable Area, Differential and Coriolis), level, pressure, and temperature. SIMATIC PCS 7 fits perfectly to the requirements of being scalable in its deployment, flexible in operation and providing the ability to be able to optimise recipes and develop new recipes in a controlled and standardised manner.
SIMATIC PCS 7’s ability to provide flexible configuration of recipes has been a game changer for GEO. With the new solution, every stage of the process was in-built and done as a baseline, managing the recipe of the chemical mix and other functionalities became easier.
The new solution and control systems empowered engineers and technicians to optimise recipes on their own, rather than having to call in third parties. This resulted in considerable cost saving, freeing up money to invest in improving systems and processes even more. It gave the team full visualisation of the production process, which meant things like tuning valves was a straightforward task. This reduced commissioning time and made them operationally efficient sooner. It resulted in qualification batches becoming much quicker and easier to produce. This is a great example of how control systems and instrumentation give access to the much-needed data that allows us to make an informed decision. The clarity it provides on material usage or how you can substitute something that has been used historically to maximise efficiency and sustainability is proof to the success of digitalisation.
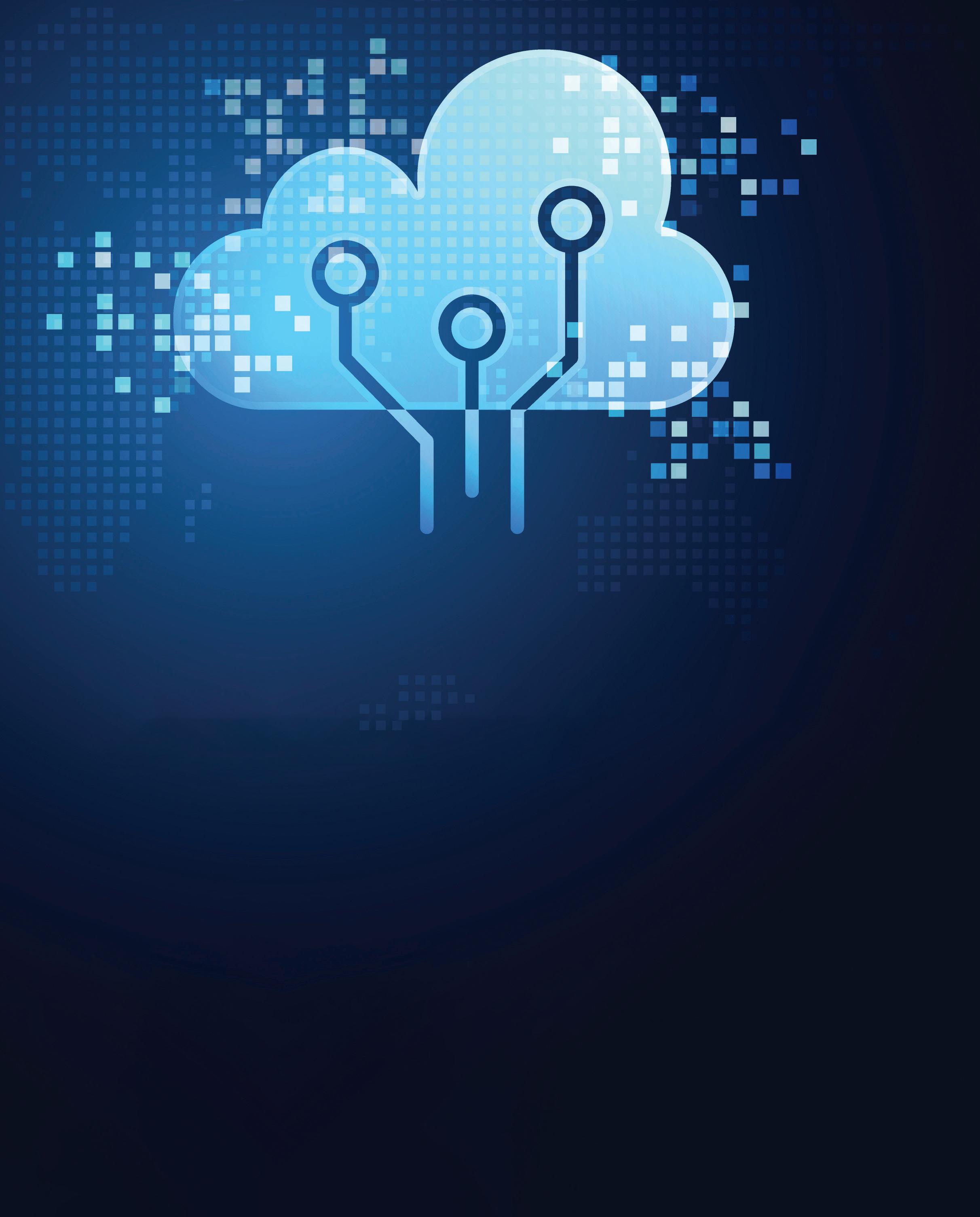