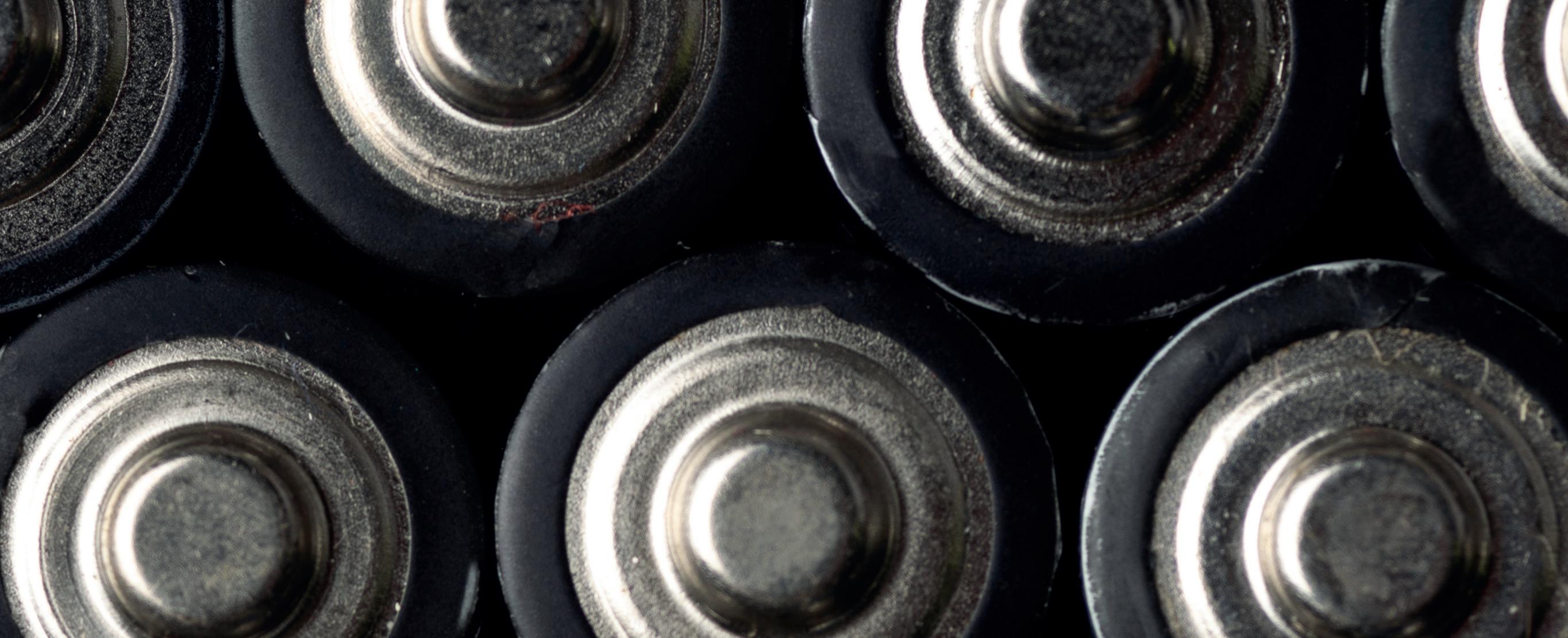
3 minute read
Energy 32
The positive (+)
In new research scientists at MIT have succeeded in adapting the known systems to effectively separate out not only the metal foil parts of a Liion battery but also the LMO cathode material in high purity for recycling into new battery cells1 . Other innovative extraction technologies are also being applied in the battery arena; such as a selective chemical transformation to allow easier separation of valuable elements, either from mined ores or from used Li-ion electrode materials. Isolation processes such as solvent extraction, ion exchange, and precipitation techniques are known to achieve this type of isolation. These commonly use large amounts of solvents, however, many of which may be environmentally damaging. A second research group at MIT has developed a process by which desired elements in an ore or recycling feedstock can be selectively transformed into sulphides allowing separation and then desulphidation to reclaim the valuable material; thus avoiding the use of large amounts of solvents2 . Extraction technology is also being enlisted to address one of the supply-chain hurdles facing Li-ion battery manufacture; sourcing a local supply of lithium.
Advertisement
Worldwide, the main areas of lithium mining (Australia, South America and China) do not, with the exception of China, coincide with the regions of high Li-ion battery production. This leaves many manufacturers forced to import their lithium supply. Application of a variety of extraction techniques to geothermal brines (aqueous solutions having high concentrations of salts resulting from circulation through Extraction technology hot underground rock formations) is touted as is also being enlisted to a possible local lithium address one of the supply- supply to avoid the environmental impact chain hurdles facing Li-ion of transporting lithium battery manufacture; around the world. sourcing a local supply of A variety of extraction techniques have lithium. resulted in large numbers of patents in this area some of which are summarised in a research paper from the Lawrence Berkeley National Laboratory3 . These approaches to extraction of valuable components demonstrate the type of innovative techniques that will be needed to develop local production of elements for battery manufacture and the recycling of valuable materials from spent Li-ion batteries. These clever twists on known technologies will work alongside the performance improvements in the batteries themselves as we strive for a more sustainable battery lifecycle.
SAM BAILEY
Partner and Patent Attorney Mewburn Ellis
mewburn.com
1. “Direct Recycling of Blended Cathode Materials by Froth Flotation” by Tinu-Ololade Folayan, Albert L. Lipson, Jessica L. Durham, Haruka Pinegar, Donghao Liu and Lei Pan, 29 July 2021, Energy Technology. DOI: 10.1002/ ente.202100468
2. “Direct Recycling of Blended Cathode Materials by Froth Flotation” by Tinu-Ololade Folayan, Albert L. Lipson, Jessica L. Durham, Haruka Pinegar, Donghao Liu and Lei Pan, 29 July 2021, Energy Technology. DOI: 10.1002/ ente.202100468
3. Energies 2021, 14(20), 6805; https://doi.org/10.3390/ en14206805 - summary of patents in tables 7, 8 and 11
WHY CLEANER ENERGY DEPENDS ON PEMD
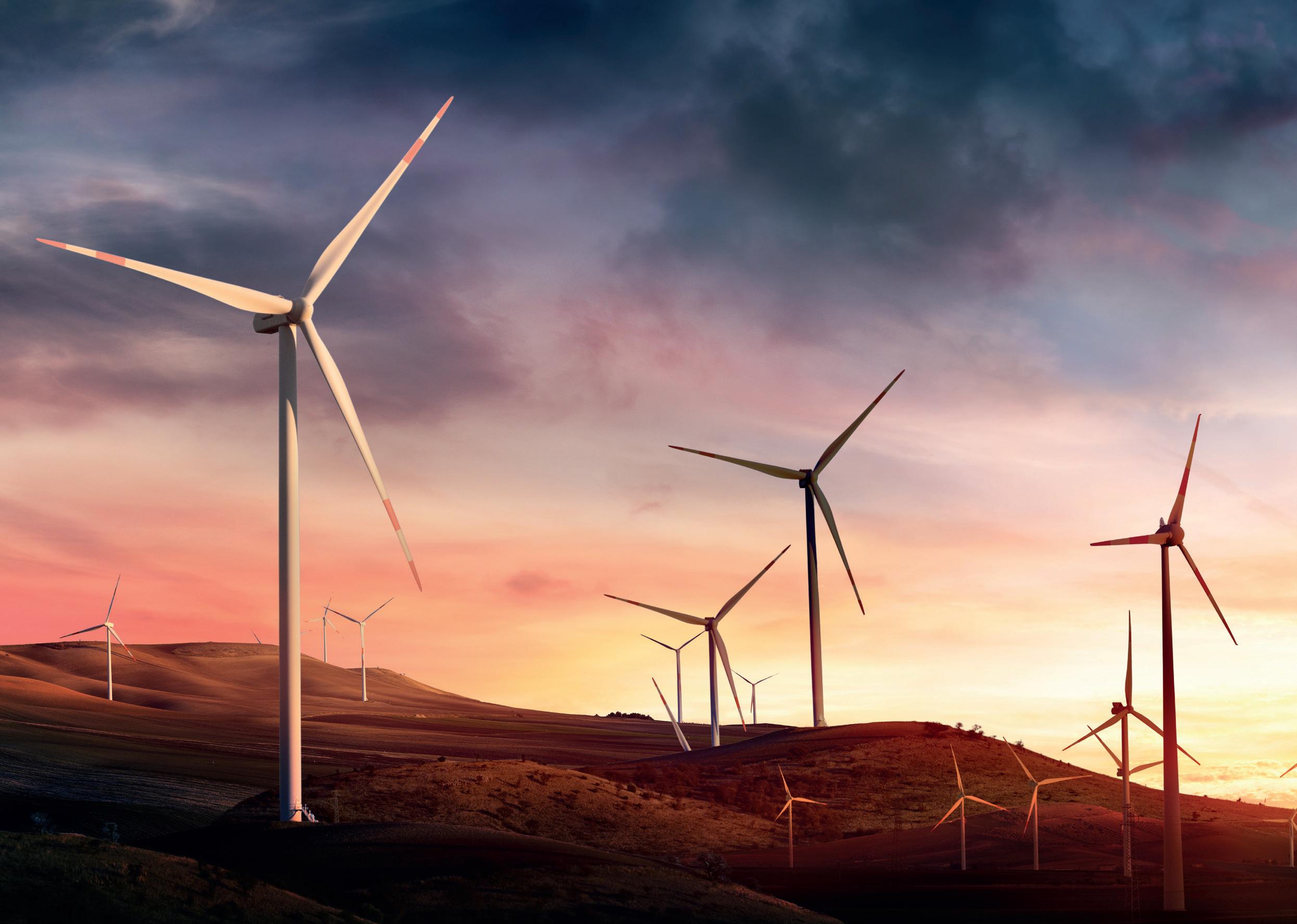
If the UK is to meet its Net Zero targets by 2050, the renewable energy sector will need to innovate, and innovate fast, to ensure supply keeps up with demand as we move away from traditional fossil fuels towards ‘cleaner’ energy.
To meet this demand, and continue to showcase the UK as a leader in environmental engineering, there needs to be an even greater focus on Power Electronics, Machines and Drives (PEMD) technology. PEMD – the most important acronym most people have never heard of – are the enabling technologies that will make electrification possible, at scale, that will make clean energy affordable and accessible for all.
Totalling nearly £80 million, UK Research and
Innovation’s (UKRI) Driving the Electric
Revolution challenge – a governmentfunded programme – is investing into these electrification technologies to support the up-scale of PEMD Manufacturing. The challenge aims to:
leverage the UK’s world-leading research capability in PEMD
help industry create the supply chains necessary to manufacture ‘homegrown’ PEMD products
identify gaps in the supply chains and help industry fill them
ensure cooperation and collaboration so we don’t duplicate effort, waste time and can reuse solutions across all sectors
help fill the skills gap by retraining, upskilling and repurposing engineers from traditional internal combustion businesses into PEMD supply chains.