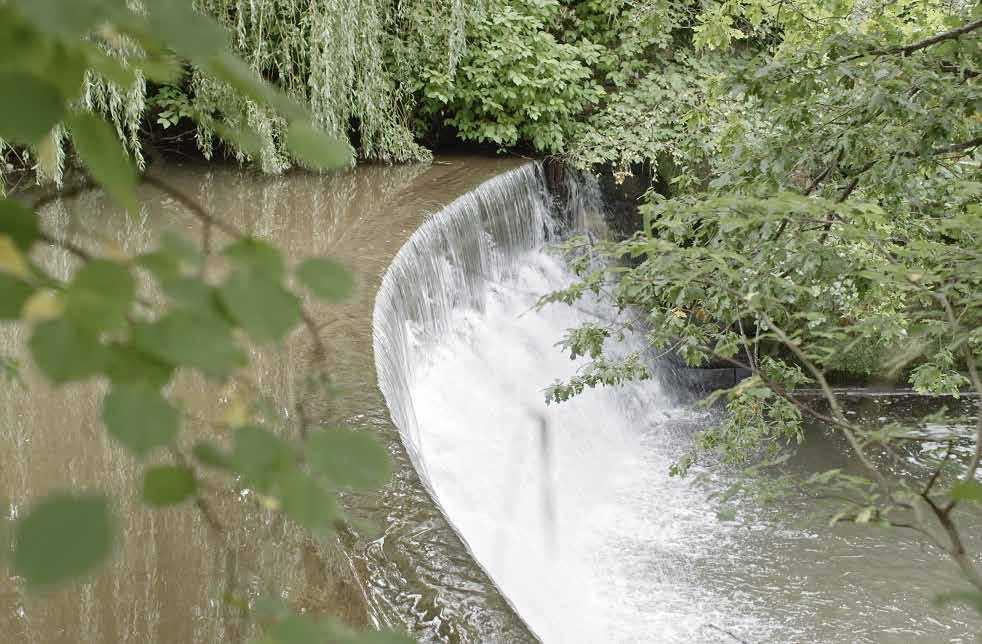
4 minute read
Green Tech 14
Using Virtual Reality, Digital Twin, the Industrial Internet of Things (IIoT), Advanced Robotics, Cloud Technology and Additive Manufacturing, the plant has produced up to 50,000 variations of its products to meet demand, increased productivity by driving down costs, and improved efficiency.
In 1990, 400 workers made 50,000 variable speed drives and controls a year. Today, a similar number of workers produce 1.2 million electrical devices - including 600,000 variable speed drives (VSDs) - within the same physical footprint. The factory is surrounded by industrial units and housing estates, with no room to expand, meaning Congleton has one of the highest productivity rates per m2 of any Siemens’ sites.
Advertisement
Faye Bowser, Head of Siemens’ Energy & Performance Services GB&I, said: “The climate emergency puts the demand on businesses of all sizes and sectors to really accelerate their efforts for decarbonisation. But a challenge is that often decarbonisation isn’t their core business. So, at Energy and Performance Services we make it our business to use our skills, our knowledge and our tools to help our customers transition to net zero in a way that contributes to their business priorities. “Despite us being from the Siemens family, we have approached working with Congleton the same we do with any organisation. It has been fantastic.
“We have ended up with an engineered roadmap to net zero that considers timelines, finance, digital services, all there to safeguard business continuity, and to have a method to continuously identify more opportunities to reduce carbon on site.”
As a global operation, Siemens is committed to ensure all its operations are carbon neutral by 2030 and for all production facilities and buildings to achieve net zero-carbon footprint by 2030.
Progress has been recognised by The Carbon Trust, which partners organisations to achieve sciencebased targets. In June Siemens was awarded its Route to Net Zero Standard tier one certification for ‘Taking Action’.
Olivia Whitlam, Head of Sustainability, Siemens Plc, concluded: “We have 8,600 people spread across offices and 11 manufacturing sites across the UK and we are creating innovation up and down the country with sustainability at the core of our operations and services. Our Congleton factory is paving the way for sustainability whilst setting a great example on how manufacturers can join this amazing journey to net zero.”
The hydro-electric plant at Havannah Weir on the River Dane.
SIEMENS CONGLETON
new.siemens.com/uk
THE BIG SUSTAINABILITY EXPO 2022 SET TO OPEN FOR THE 7TH YEAR
Many of the most influential suppliers and decision-makers in the country will once again head to Hampshire this September for one of the UK’s leading events dedicated to corporate sustainability and the drive to net zero.
Green Business Journal caught up with organisers, The Southern Sustainability Partnership as they prepare to open The Big Sustainability Expo (Southampton) for the 7th year. A leading UK platform designed to highlight the importance of corporate sustainability and the drive towards net-zero carbon. With one of the most comprehensive line-ups of products, services, technologies, innovations and experts making their mark today. A vital, free resource, the Expo offers practical advice and solutions from over 100 different exhibitors and two Keynote speaker theatres. In 2022 the Expo will open alongside two co-events: A clean transport showcase Big Green Wheels 2022 – and the Local Authority Collaboration Forum 2022. Co-directors Anita Potten and Lynda Daniels left us in no doubt as to the importance of an environmental strategy to protect the future of our businesses. Having successfully run a company that supports the public and private sector in their quest to operate more responsibly - this duo has witnessed first-hand the loss of long-term business by organisations that have failed to prioritise this vital topic.
Anita Potten: Protecting your organisation is why we do what we do. Like us we have no doubt you’ve nurtured a culture of outstanding quality and customer service. It’s what we all strive to achieve. But that alone is no longer enough. With far greater scrutiny of the supply chain, we are now urging SMEs to look at what their customers are doing to reduce their own impact on the environment. Having witnessed the ripple effect through the supply chain, as one company is forced to clean up its act, so they refuse to jeopardise efforts by buying from a less responsible supplier themselves.
Lynda Daniels adds: We’ve all read the headlines. Large corporations playing their part in helping the planet. But what came first? Their company or saving the planet? Undoubtedly, their journey began with a need to meet environmental legislation, and it was from those early directives that corporations woke up to its significant benefits. Not least, enormous cost savings matched by increased profits gained from a more positive brand perception. And, of course, they are inevitably helping the planet. So, please, view this as a positive. There are far-reaching benefits and no longer just within the confines of our large corporations.
The duo concurs, it starts with joined-up thinking between departments. Shining a spotlight on areas of operations that may have gone unscrutinised as a business grows. This should incorporate what comes into your businesses versus what goes out as waste. Clearer thinking that will see you keep more of those hard-earned profits. More centralised purchasing is a great move, it ensures you are less wasteful and may also provide stronger buying power. Track your energy data...what you use and where you use it – there are great tools out there today. You may be horrified to learn what you are