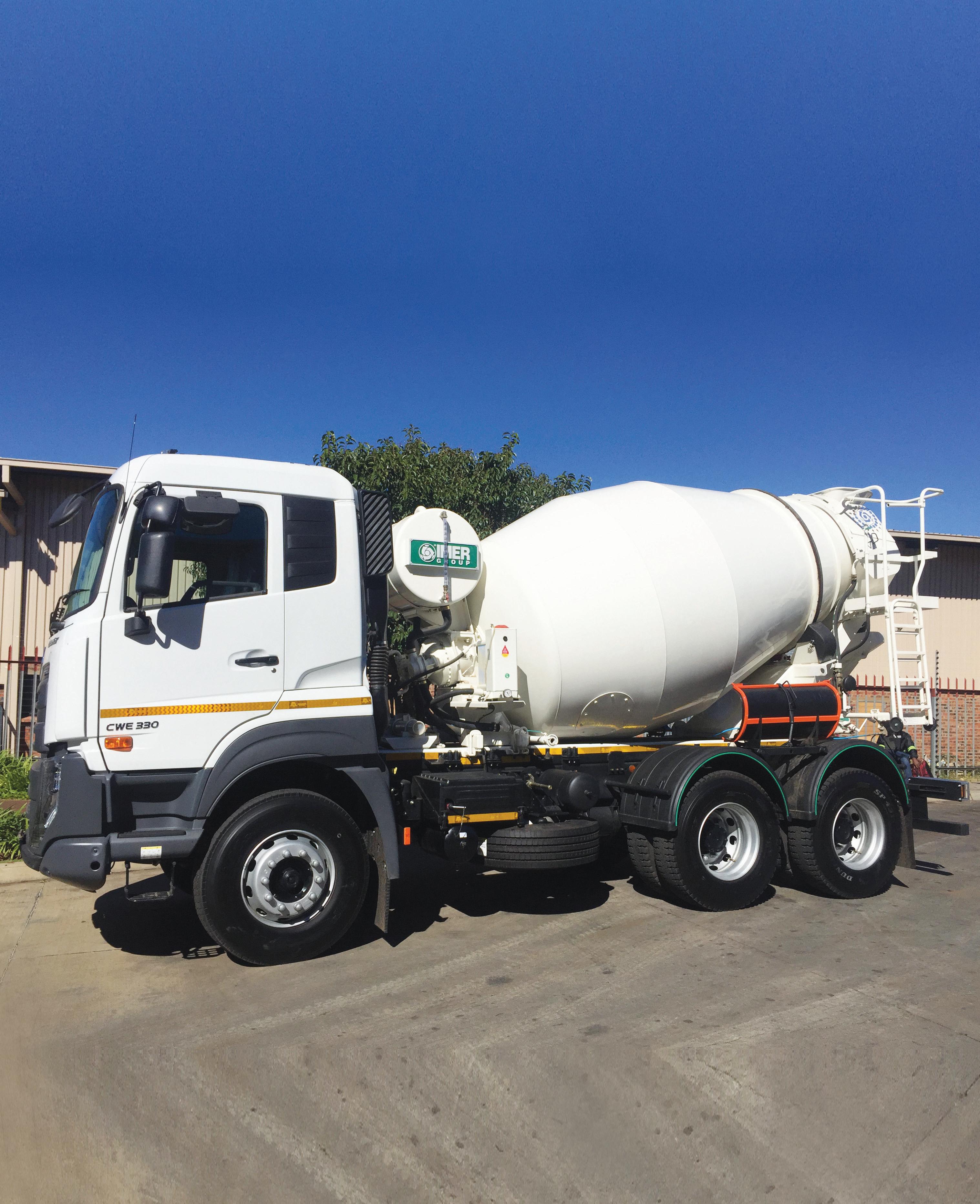
6 minute read
Ready-mix trends: PMSA
When concrete is the same price as five years ago, your truck may be the difference between profit and loss
By Eamonn Ryan
Advertisement
In a market when suppliers are delivering concrete at the same price as five years, they can only achieve that by being smarter – particularly with the costs of their readymix trucks. Quintin Booysen, Sales and Marketing Manager at PMSA (Pan Mixers South Africa) gives PMSA’s views on trends in the ready-mix and equipment sector.
“T raditionally South Africa has a strong culture of dry mixing whereby the mixing is done on the ready-mix truck, which required further time-consuming mixing at the production site. With the improvements in technology in recent years, this system has rather favoured pre-mix whereby everything is mixed at the batching plant. It has the advantage of allowing for a higher-quality mix through everything being batched together and mixed in one go and discharged into the truck.”
This also permits a better utilisation of trucks. “There are other means to speed up the process, for instance through moisture control. When making concrete there’s always some extraneous water in the system, for instance in the aggregates, lowering the strength of the concrete. By rather doing this in the batching plant, it enables the moisture level to be closely monitored for a more precise moisture level and less wastage, while the trucks themselves can also have an on-board Ludwig moisture monitoring system in the drum providing live feedback throughout the journey,” explains Booysen.
“You get transit mixers and you get ready-mix trucks, and in the latter what is critical in the drum itself is the number of blades inside. The more blades there are and their position result in a better quality mix and quicker mixing time. Then when the truck arrives on site, these more modern technologies result in delivery of concrete which is more consistent and predictable.”
South Africa has strict axle loads and weighbridge formulas, limiting the country to loads depending on the truck axles. Booysen explains that generally the South Africa market best suits drums of 6m3 or 8m3. “However, the make-up of the
drum affects this. In cases where the steel in the drum is too thick the weight of the drum increases and this reduces the load that can be carried to say 5.5m3 for a 6m3 drum. There is the option of a 10m3 or even 12m3 in certain circumstances, but these do not suit a typical urban environment. At PMSA we supply the full range,” says Booysen.
WAYS TO REDUCE COSTS
Other ways to reduce costs include having the right truck with the right power-to-weight ratio which uses less diesel; as well as a drum which has good wear resistance. Greater longevity of the drum means more cubic metres of concrete can be delivered from the same drum over its lifecycle. “If one can transfer some of the wear and tear from the drum to the batching plant, that results in greater truck efficiency. This is particularly important to an owner-driver who is paid per load, and consequently wants minimal wear on their truck. If they are transporting a dry mix where all the mixing is done in the truck’s drum, this reduces the life of the drum as it is an intense mixing as opposed to just an agitation.
“Furthermore, the faster the drum turns the more power and diesel it requires. We try restrict this to an output drive of 1,500 rpm but with more mixing blades inside the drum which does the same job at a lower speed.
“A mixing drum can be loaded onto almost any truck, leaving the client to choose the most cost-effective truck for themselves, and we mount the drum onto it for them. The truck does need to have a power offtake (to rotate the drum) to power the hydraulic system. The truck also has to have a horsepower of between 250hp and 280hp for a 6m3 drum. Clutches tend not to last that long on a ready-mix truck because of the demanding treatment, and so an automatic shift may be better. A semi-automatic gearbox is also worth considering. Among the drawbacks of an automatic is that they are more expensive and sometimes not suited to hilly terrain.”
Often a purchaser considers the thickness or lightness of the drum’s skin, without considering what material it is actually made of. “There are many different types of steel to choose from and we use one called 30 MnB5 made from steel with Chromium and Boron guaranteeing a real wear resistance to the wear and tear caused by concrete. You can make the material more wear resistant but it could become brittle and liable to crack. Our material has more malleability, allowing the material to be scratched and retaining the material, rather than scratching off and reducing the thickness faster overtime. This allows us to make a 4mm drum thickness with lighter material (by 350kg) permitting a higher loading to achieve 6m3 or 8m3 – and it lasts longer.”
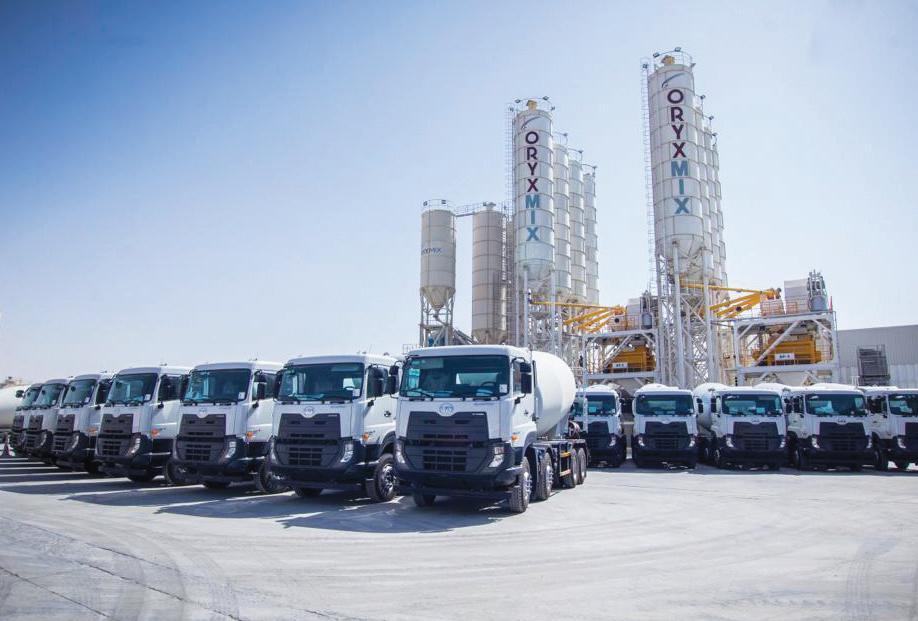
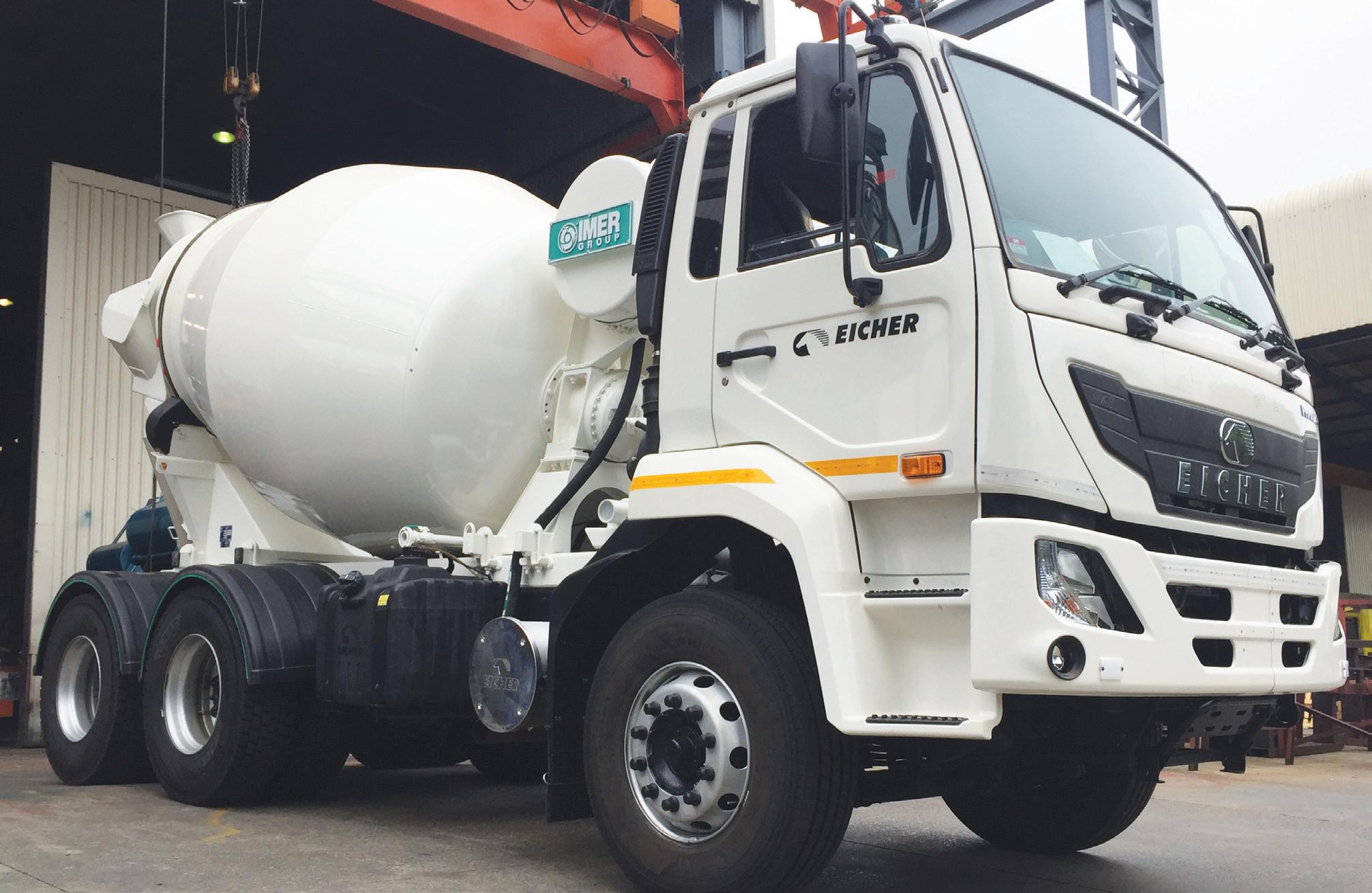
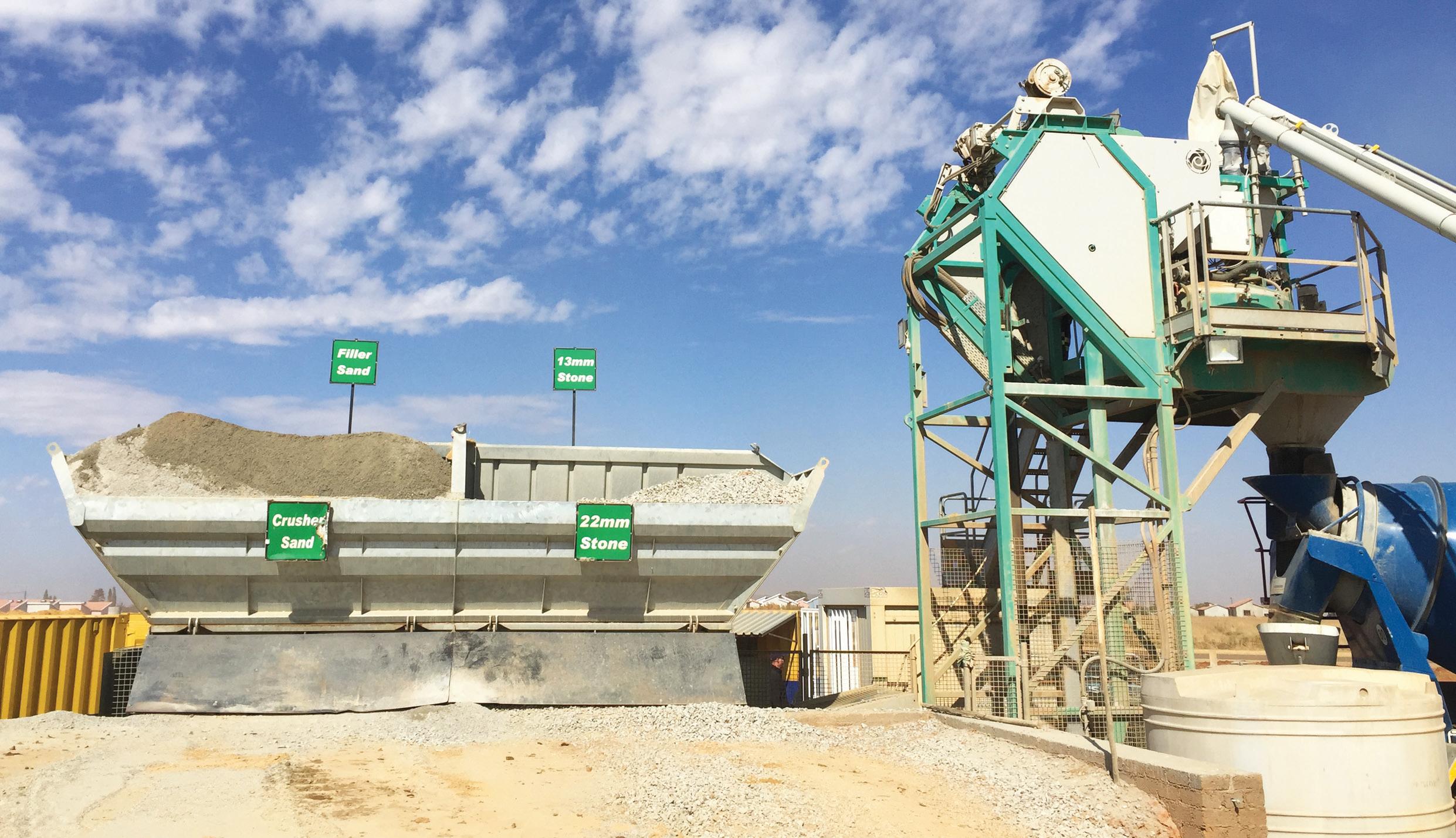
COMPETITION
There is a lot more competition in the ready-mix business today as the barriers to entry have lowered and pushed ready-mix prices down. “It’s purely based on capital, with no special skills any longer required for the mass market.”
There are about six suppliers of drums in South Africa with a lot of competition in the manufacture of the ready-mix equipment. The major ones are: PMSA, Putzmeister, Liebherr, Cifa, TFM, ECEM. Local manufacturers are restricted to the grade of local steel they can get, and the limited size of the local market – with an absolute maximum of 300 units sold a year, and a low of 100 – does not always offer economies of scale.
“South Africa is definitely price sensitive, so one of the major considerations of buyers is affordability. Within a certain 10-15% window of affordability, a buyer will then look at different technologies, longevity of the equipment and support. For 2022 the main consideration will be availability – factories in Europe are experiencing shortages of raw materials and this is compounded by logistics bottlenecks with shipping which will affect supply of both drums and trucks.”
THE FUTURE
For the short-term future, Booysen doesn’t anticipate much changing other than a steady increase in infrastructure projects in the country – bridges, dams and concrete freeways – coming on line over the next year to two. “There is demand for higher quality concrete, which means wet batching is required.
“What has entered the overseas market but not yet always available in South Africa is self-levelling concrete and self-compacting concrete – these will become more the norm in the future. This requires a high-quality drum and mixing equipment, as well as a really good mix design – normally on site there’s no vibration used in casting the self-levelling and self-compacting concrete, so mix design is crucial. I anticipate seeing this trend in South Africa over the next two to five years.
“Over the five-to-ten-year time span I believe there’s a good chance of seeing 3-D printing technologies entering the construction market in a big way – especially the printing of houses and buildings. In this scenario, the ready-mix truck will arrive with the ‘ink’ in the form of printable concrete. Instead of pouring concrete into moulds we’ll be printing it into buildings, and this is already a reality. Some manufacturers are already looking at ways of converting ready-mix to a printable format,” says Booysen. n
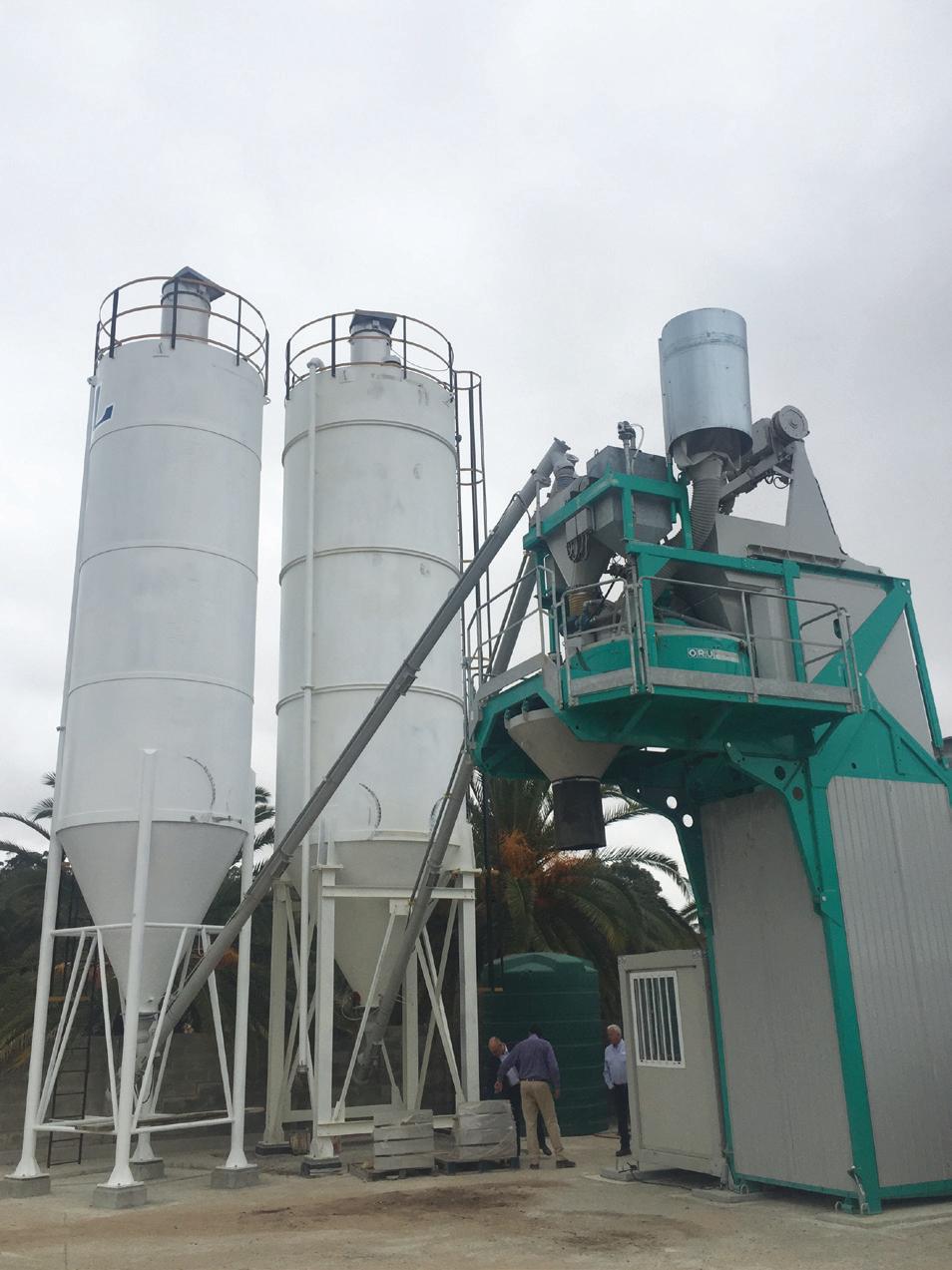