
7 minute read
A profile on Beyoung Outdoors
A profile on Beyoung Outdoors The Art of Making a Surfboard
Established in 2009, Beyoung Outdoors is a Ningbo-based exporter specializing in water sports products, including kayaks, S U P, Surfboard, Bodyboard, Skim board and a wide variety of kayaking gear and surfing gear. An ultimate one stop buying experience for those wanting to source high value quality gear.
FACTORY Their factory facility covers over ten thousand square meters and employs a full-time staff of sixty people working on different jobs. Equipped with state-of-the-art manufacturing and testing equipment and more importantly, the most experienced of staff members.
This hub of activity is supported by a research and development team who consistently improve and develop their technology based on market trends. This makes Beyoung Outdoors completely
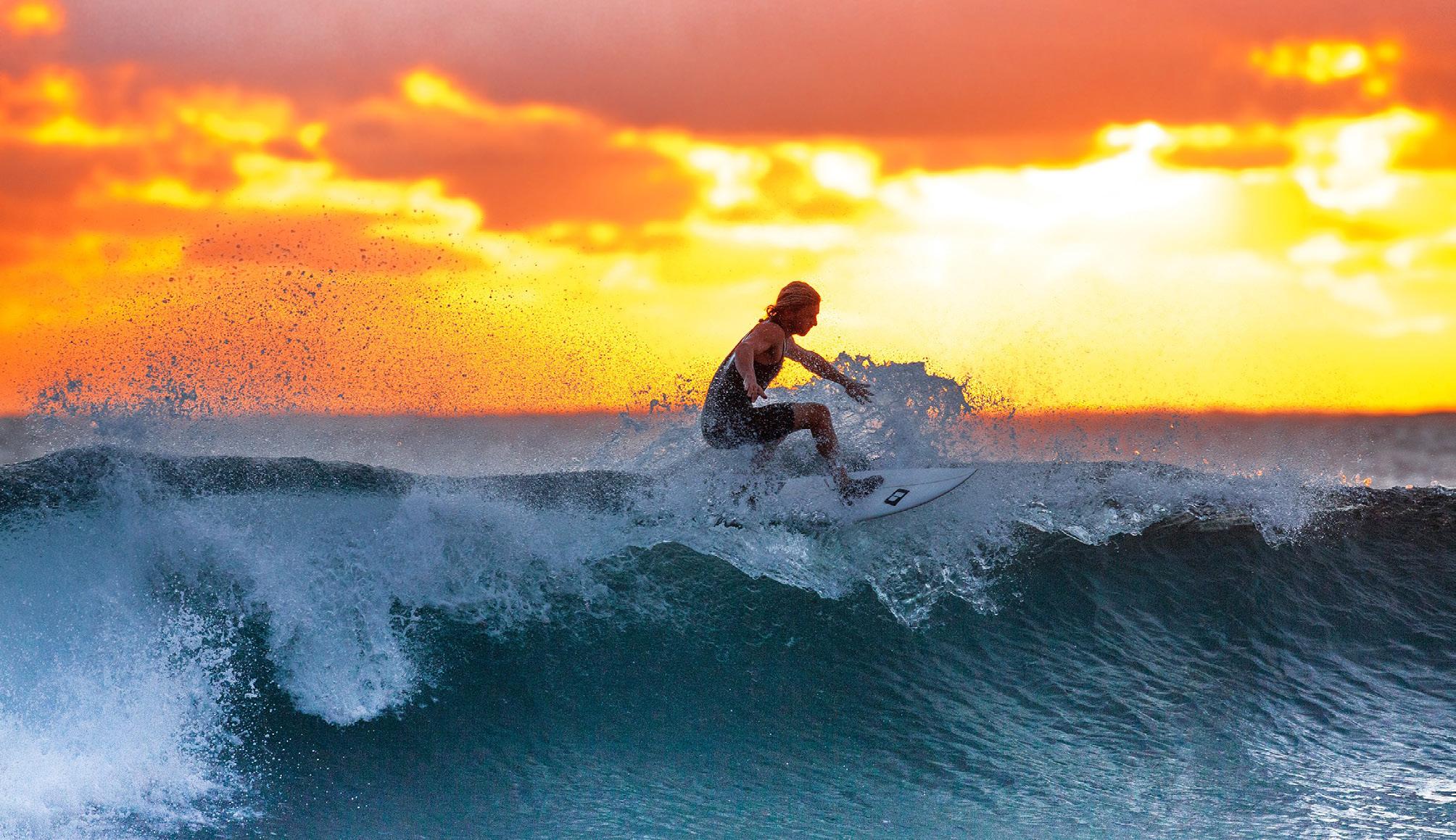
capable of customising different shapes, graphics and 3D modelling designs.
The quality control team have a reputation for being brutally thorough and careful with checking. Making sure that every item made for their customers is the best possible standard.
THE SURFER’S RIDE Surfboards were invented in ancient Hawaii, where they were known as papa he’e nalu in the Hawaiian language and were traditionally massive at nearly five metres in length and extremely heavy. Made from wood from local trees such as koa, they were far removed from the sleek and modern examples of surf boards that we all associate with the sport today.
Manufacturing standards have increased significantly, and other design advancements have

changed the face of surfboards completely over the years. These include the addition of one or more fins (skegs) on the bottom rear of the board to improve directional stability, and numerous improvements in materials and shape.
Modern surfboards are made of polyurethane or polystyrene foam covered with layers of fiberglass cloth, and polyester or epoxy resin. The result is a light and strong surfboard that is buoyant and manoeuvrable. The Polystyrene surfboard was invented by Reginald Sainsbury of Wilcove, Torpoint in the early 1960s whilst working for the Poron Insulation company who were looking to expand into the leisure industry.
Since then the surfboard technology has evolved even further with the inclusion of carbon fibre and Kevlar composites, as well as experimentation in biodegradable and ecologically friendly resins made from organic sources. Every year, nearly half a million surfboards are manufactured, and they are built to last and endure.
POLYURETHANE (PU) BOARDS Having become the norm, many surfboards are constructed using polyurethane foam. They are made stronger with one or more stringers going down the middle of the board.
The foam is moulded into a rough shape of a surfboard which is known as a “blank” at which time it is giving to the shapers. The shapers are responsible for creating the specific shape of the board, a process that is still mostly done by hand. Finally, the board is covered in one or more layers of fiberglass cloth and resin. It is during this stage that the fins or boxes for removable fins are attached and the leash plug installed.
Although foam boards are usually shaped by hand, the use of machines to shape them has become increasingly popular. Vacuum forming and modern sandwich construction techniques borrowed from other industries have also become common.
Many surfers have switched to riding sandwichconstruction epoxy boards, especially beginner surfers who are looking for a more durable, inexpensive, entry-level board.

BALSA BOARDS Originating in the Hawaiians, the balsa wood’s surfboard history starts in the 1940s. Being light and strong, balsa wood was long considered a perfect material for surfboards. However, shapers could not use this fragile wood to make entire surfboards until after WWII, when fiberglass skins were invented which allowed a greater structural strength.
Balsa wood boards are more buoyant and lighter than other boards and therefor easier to handle. However, these boards have some disadvantages such as they are not as sturdy as solid redwood or polyurethane boards. Due to this, balsa boards are not considered suitable to beginners as they can be damaged easily.
HOLLOW WOODEN BOARDS Hollow wooden surfboards are made of wood and epoxy or oil (as a sustainable alternative to epoxy) and are a reversion to using wood after the foam became dominant in the 1950s.
Specifically, hollow wooden surfboards have no foam in their construction. (*interesting note, boards that are made with foam and wood are commonly known as compsands or veneer boards.) Various construction methods are used to hollow the inside of the surfboard and lighten the weight of the completed board.
This lightening is important, because due to the materials used a hollow wood surfboard is deceptively heavy. From 30% to 300% heavier than a standard foam and resin surfboard.
Apart from beauty, the main inspiration behind a hollow wood board is that this is a more environmentally friendly method of construction (compared to epoxy and polyurethane methods) which uses fast-growing plantation wood such as paulownia, cedar, spruce, redwood, and balsa.
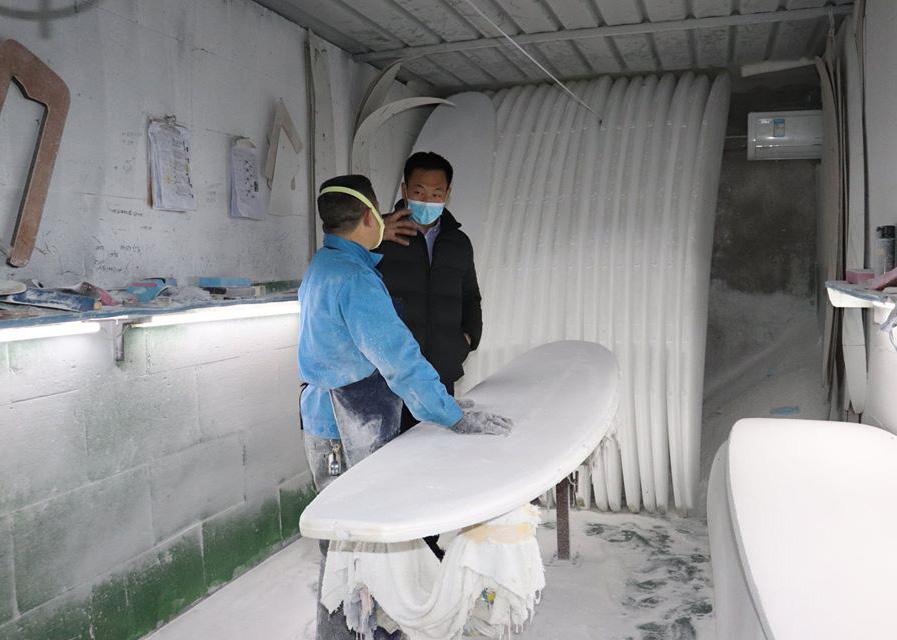
MODERN CONSTRUCTION METHODS The current construction methods descend from the 1930s Tom Blake paddle boarding method, which favours a central stringer with individually shaped transverse ribs covered with a skin and rails. A modern interpretation of Tom Blake’s work is the perimeter stringer method used by some manufacturers, utilizing laminated rails as stringers connected with a series of plywood ribs. This skeleton is then sheathed with 5mm-thick wood strips, creating a fast hollow board with good flex properties.
The parallel profile system was developed from cold moulded (double diagonal) boat building and uses at least four layers of material laminated over a male mould into a curved blank, including enough wood for rails, which are then shaped.
The chambering method follows a system in which planks of paulownia wood are selected and the rocker of the board is cut into each. The planks are then chambered to reduce weight, and then bonded together to form a hollow or “chambered” blank.
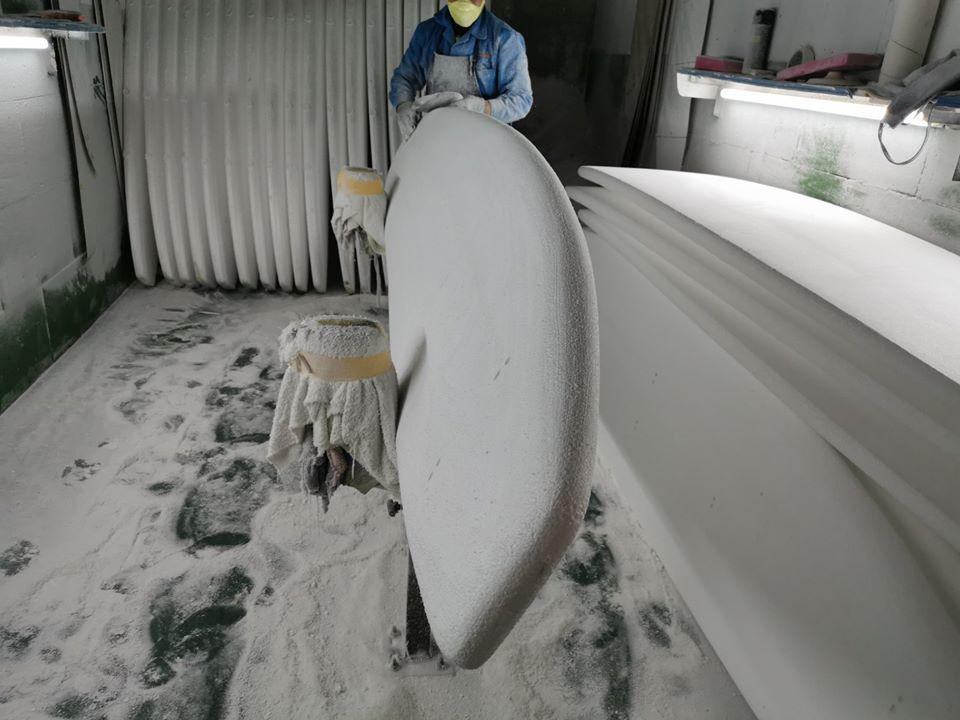
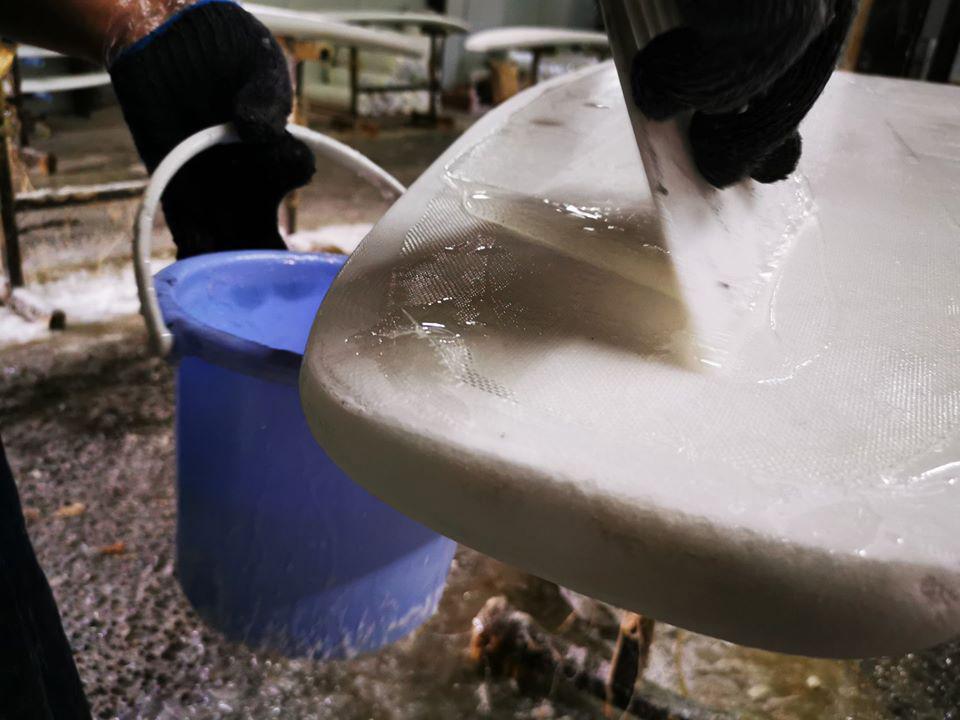
CUSH - SKINNED SURFBOARDS A very recent modern development in surfboard technology is the creation of high performance boards wrapped in a stretchable and soft hydrostatic skin.
The internal structure of these cushioned “Cush” boards is an epoxy surfboard with an EPS (extruded polystyrene) shaped foam core. The “skin” is made of a gloss coated foam and is stretched and vacuumed adhered to the entire board.
The cush offers added protection for the light board as well as dampening the chatter and absorbing the impacts of various moves. Jim Richardson, a 25-year veteran shaper on the North Shore of Oahu, first pioneered this technology in the mid 1990s.
Recently a number of companies including Spacestick, Radiowake and CUSH (brand) have begun to market the advancements to the surfing community. Silencer surfboards is the current manufacturer for the various brands as of 2018.
COMPOSITE SANDWICH CONSTRUCTION Composite Sandwich board construction gained popularity among garage shapers and then major manufacturers during the 90s and early 00s.
Entailing a hand or machine-shaping foam blank from EPS foam and then vacuum-bagging or hand-laminating a denser layer of foam, wood, or carbon onto the bottom and deck of the EPS foam core. These two layers are usually separated with lightweight fiberglass cloth or other composites cloths.
This can also be accompanied with parabolic rails made of balsa or other buoyant woods, carbon, or other high-density materials. This blank construction is then laminated with epoxy resin and fiberglass or other composite cloth as any other surfboard would be, by hand or via vacuum bag.
Obviously, the many different layers is why this construction method is referred to as a sandwich. It is not as heavy as it would sound with the various layers added buoyancy and it is a sturdier too. Firewire Surfboards pioneered this technology for the mass-produced surfboard market beginning in 2006.
BEYOUNG OUTDOORS Surf boards are not the only product that Beyoung Outdoors manufacture and create. Using the polyurethane method. Their range also include paddle boards, skin boards, kayaks and more. Aiming to provide a one stop shop for the creation and purchase of bespoke outdoor water equipment they believe that knowing everything about your industry is the only way to provide the customer with the level of service they deserve.
WEBSITE: www.beyoungoutdoors.com
TELEPHONE: +86 57487657242
EMAIL: info@beyoungoutdoors.com