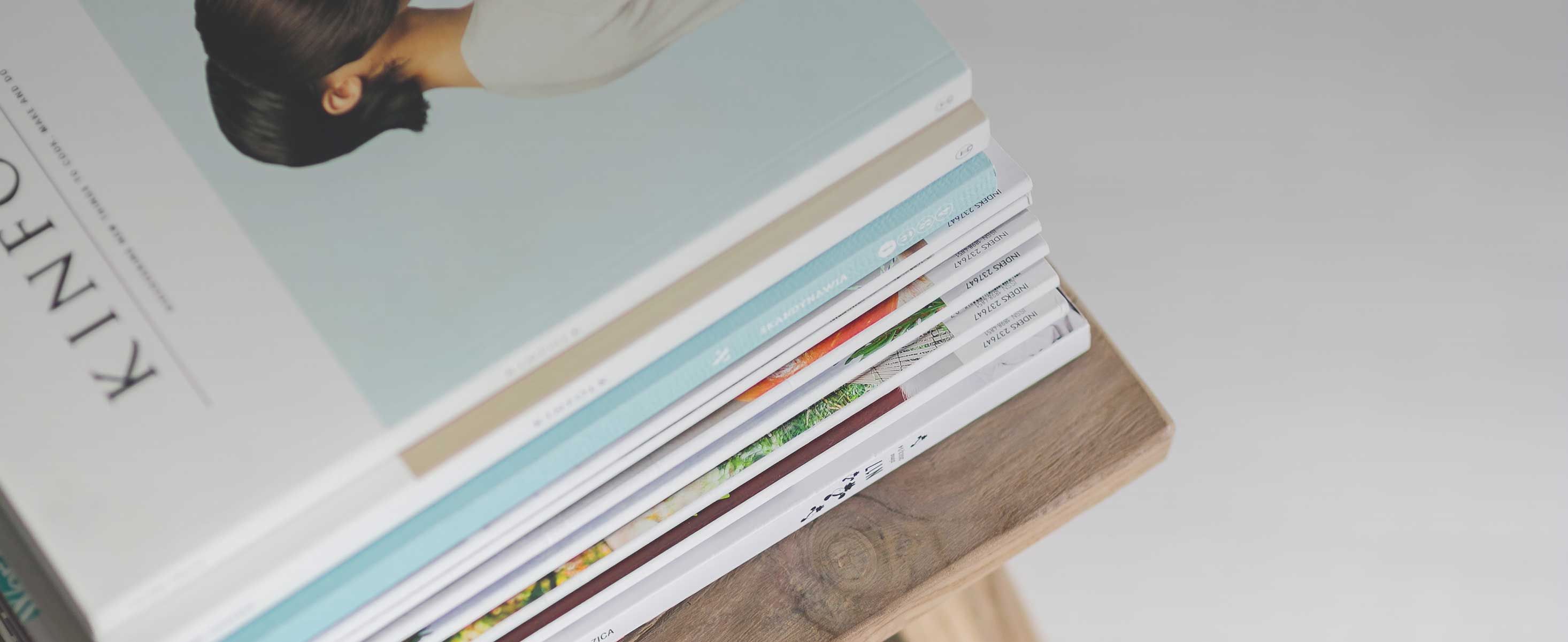
2 minute read
Creating value across our production processes
Driving our culture of agility, innovation and continuous improvement across our production sites.
Our commitment to customers drives our culture of innovation and continuous improvement at all our 73 production sites around the world. Each day, with speed and agility, our production teams transform the original creations of our perfumers and flavourists into products that meet customer demands and consumer preferences as well as increasingly stringent quality standards.
Advertisement
Through our acquisitions in 2019 we added seven new production sites in six different countries. This expanding global footprint ensures we are close to our customers and their markets, and enables us to bring value-added flavour and fragrance products and solutions to market faster.
Continuous improvement
In Flavours in 2019, we completed the second of our three-year cycles of food safety audits, which showed clear and significant improvements in our Operations performance. While we continuously enhance our systems and standards to adapt to increasing regulatory, statutory and customer requirements, we also seek to strengthen even further our culture of food safety. More than 100 food safety experts across all regions, including in our recent acquisitions, are forming a global network to bring food safety within Givaudan to the next level. As part of the integration of our acquisitions, we have built a combined expert team so we can align collaboratively on best practices, reflecting Givaudan’s high quality and food safety standards.
Our Operations infrastructure in Fragrances is based on a global SAP platform, which means all systems, applications, nomenclature and specifications are consistent and global. This allows us to leverage our highly automated facilities in, for example, ingredients, compounding and Active Beauty, to service our customers with best-in-class lead times. Global quality, supply chain, and production methodologies serve as enablers to this footprint. Our aspiration is: "Be great at what you do, always aspire to be better, and ensure that you have our customers’ needs in mind." We constantly invest in training and development for our teams, and provide them with robust tools and methodologies to drive improvement. We gauge our effectiveness by our focus on key performance indicators that include safety, quality, service and cost. We strive assertively to deliver improved performance against these metrics.
Our moves towards global harmonisation in Flavour and Fragrance Operations, particularly with our recent acquisitions, are facilitated by Givaudan Business Solutions (GBS) through its Continuous Improvement (CI) Centre of Excellence, which aims to leverage knowledge and best practice across both business divisions. This CoE will ultimately serve all of Givaudan and its customers in Operations and beyond by continually improving performance, efficiency and product quality.
Driving supply chain excellence
Our supply chain organisation remains on track to complete the implementation of its 2020 operational plan, which aims to bring more agility to meet fast-changing customer needs while continuing to reduce costs. The new operating model has been put in place in all regions, with only some parts of Asia Pacific remaining. Further progress in integrating the supply chains of our recently acquired companies is also expected during 2020.
We plan further investments in digital integration with trading partners in capacity planning processes and tools, and in risk management. With increasing changes in market conditions and opportunities for our customers, our responsiveness continues to be a focus area. Our significant global footprint is an opportunity to be in close proximity to customers, and we see potential to leverage this in the coming years.