
13 minute read
Tow Manager
Tow MaNager Preserving the Environment and Getting Paid For It.
By John Borowski
John Borowski is VP of Tow Industry Programs for AutoReturn. John has over 45 years experience as a tow business owner, wrecker manufacturer specialist, trainer and writer. He was awarded the first “Towman of the Year” by American Towman magazine and two Towman Medals for heroism. He was inducted in the Towing and Recovery Hall of Fame in 2001.
Safety Advertisers
Enzo’s Cleaning
Solutions.......... see p. N, M 53 SafeAll Products...... see p. 17
Dedicated emergency response van dispatched with a trained cleanup expert.
Profit still drives business, but companies in every industry increasingly recognize the benefits of environmental responsibility. It can reduce costs and increase profits. It can positively change the way consumers perceive a company. It can prevent legal problems. Most importantly it may help ensure not only a healthy economy for future generations, but a healthy planet as well. The towing industry is no exception. Recognizing the advantages, towing has recently turned its attention to green initiatives.
For years, as a tower responding to a motor vehicle accident, showing up to a big mess was nothing but a headache. You would have a mixture of fluids, glass and debris spread out over a large area and into a travel lane. In most cases it would take more time for the cleanup than the tow itself. The worst part of it was that you couldn’t charge and get any kind of fee for this. Most guys would simply throw some speedi-dry down and then sweep everything off to the gutter or into the storm drain. If you were to pick it up most times you would need to throw it on the deck of your carrier because you couldn’t carry a large enough barrel to hold all of the waste.
As I jumped back into the trenches ◀

with a towing company that was preparing to move its base of operations (due to the lack of room and the continual growth) we ran into a hurdle with receiving a permit to store cars. It seems the town did not want any vehicles emitting fluids to be parked on the property due to a flood plain at the rear of said property. After thinking about the town’s position, why would I want any vehicle leaking fluids on the property to begin with? I can make all the money I want on towing and storage but down the road I have to be responsible for my contaminated storage lot. Is it worth it?
In working with Bill Johnson several years ago, we decided to comply with the order so that we could continue towing and not have contaminants leaking into what was supposed to be an asset in years to come. Now, any vehicles leaking fluids would have to be placed in our indoor decontamination booth and have its fluids drained before being placed into the general population of storage. A specially designated booth was prepared to contain any drippings. If an accident occurred
after our regular hours the draining of the fluid would occur the next day during normal business hours by a mechanic.
Charges were imposed for the special booth usage, inside storage, labor, and disposal fees for all contaminants and then another tow fee out to the general population. Now, we were able to store the vehicle without jeopardizing the clean condition of the property and of course comply with the town’s order and the State Department of Environmental Protection.
Since this worked very well we decided that we needed to be complete and take care of all possible contaminations caused by these wrecked vehicles. A better process was needed at the accident scenes. Since there is limited space on the tow trucks we decided to form a
any kind of fee for this.

separate company that we could sublet to respond to all accidents involving spills. Some municipal tow contracts say that the tower is responsible to clean up reasonable spills at accidents scenes. After much thought and discussion, we determined what is a reasonable spill for the tower to handle and where the line would be drawn to have a separate service to perform a complete job.
The company adopted a policy to only carry an empty antifreeze jug full of speedi-dry, a broom and shovel for clean ups. Definitely, reasonable! Any spills larger than a quart we call our accident remediation company for clean ups. Once the first tow truck shows up at a scene, the driver determines if they need outside help for cleanup. When necessary an emergency response van is dispatched and responds immediately with a Haz-wopper trained cleanup expert much like an ambulance.
The vehicle carries sorbents and absorbents, an application spreader for them, cases of mats, booms, protective clothing, pig pans, a transfer pump and barrels to transfer fuel or other contaminants. In addition, brooms, shovels, scrapers, tank leak repair kits, straps, fuel tank strap cutters, covered containers to transport contaminants after being lifted were included. The van is fully outfitted with strobe lights and flood lights to not only be seen at the scene but to clearly make the site visible at night. The van stays on scene until the site is restored to a preaccident condition or better.
After clearing the scene the van goes back to the shop empties it waste, gets cleaned and restocks to be back in service for the next call. The emergency response van carries a 2-hour minimum service time which includes the trained responder, for business hour responses Monday through Friday 8am to 5pm. Nights, holidays, and weekends are 4-hour minimum.
A special invoice was created to record all scene conditions, products used, necessary labor and emergency response vehicle service time. The invoice completely records the conditions at hand and if the incident was reportable or if additional labor of remediation is necessary. Also, the proper disposal for the contaminants is recorded and is also charged accordingly.
Now as far as the bill goes, it is a sublet attached to the vehicles tow bill and collected when the vehicle is released. All of these charges are payable by the responsible party’s insurance company under the liability side of the auto policy. Any state that requires property damage coverage which I believe is most if not all, covers this claim. The optional collision coverage does not play any role here.
Adopting these procedures brings your company into the future that we are all trying to preserve for future generations and becomes a profit center.

Slingshot Train Lift

Jim “Buck” Sorrenti, a longtime editor of American Towman, has been our field editor for the past 10 years. He is a freelance writer and photographer with more than 40 years of experience covering motorcycle, hot rod, truck and towing culture. He writes weekly for TowIndustryWeek.com.
A longtime Southern California tow company assists in lifting a derailed train using a specialized sling.
by Jim ‘Buck” Sorrenti
At 11:00 am on Wednesday November 11, 2020 Pepe’s Towing Service received a call from a tow company on scene in Long Beach, California requesting help to reset a rail car. Joshua “Josh” Acosta explained, “We were called by City Tow that needed assistance in lifting a 200,000-pound rail car that derailed and needed to be set back on the tracks.”

Josh responded with Big Flipper, his 2019 Peterbilt 389 with a Century 1075 75-ton rotator. City Tow had two trucks on scene, a 2015 Peterbilt with a Century 9055 50-ton heavy and a 1994 Peterbilt with a Century 1060 60-ton 2-stage rotator.
“Upon arrival, I saw the other tow company had two heavies on scene, one on each end of the rail car.” explained Josh. “I positioned my 75-ton rotator to lift at the very end. Due to the extreme weight I would be lifting, I ran a 4-part line with three 15-ton snatchblocks and I finally got to use my brand new custom 15-foot slings on this rail car. My lines are rated at 25,000-pound, each snatch block is 15-tons and my slings are 52,000-pounds in a basket.”
For the rigging on the rail car, Josh used his two new 15- ◀

15-foot slings rigged in basket configuration.

Due to the extreme
on this rail car.
foot slings in a basket configuration. Each sling has a working load limit of approximately 52,000-pounds. These slings were made by SWOS and custom ordered for Pepe’s by Thad Bailey of Bailey’s Towing accessories. Founded in 1985, SWOS located in Houston, Texas, provides high performance synthetic rigging solutions for various industries such as oil and gas, industrial, commercial marine, mining and more. They became a
Master Distributor, then one of three
Master Fabricators worldwide.
Josh informed, “These slings are much stronger and lighter than chain, and have a special urethane coating that makes them abrasion and cut resistant. Each end of my slings were attached to my BA container links with an oblong.” The axle was chained up to the rail car so that it would not stay on the ground as it was lifted. Once rigged, all three trucks winched in. Josh said, “By starting with my boom head over the rail track instead of over the middle of ◀
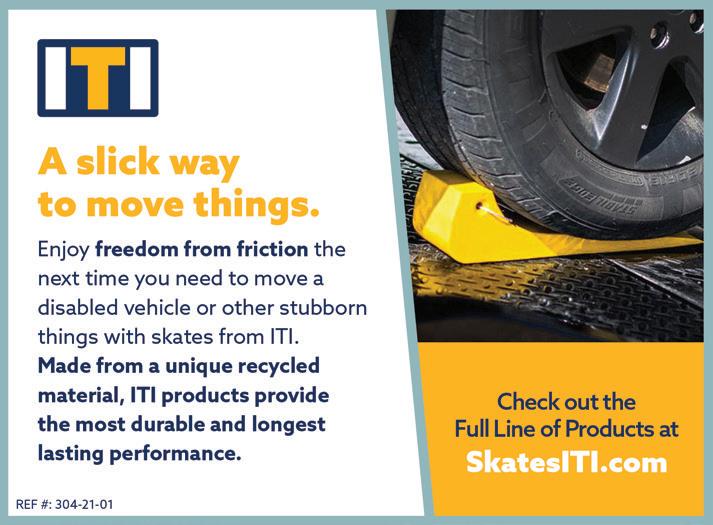

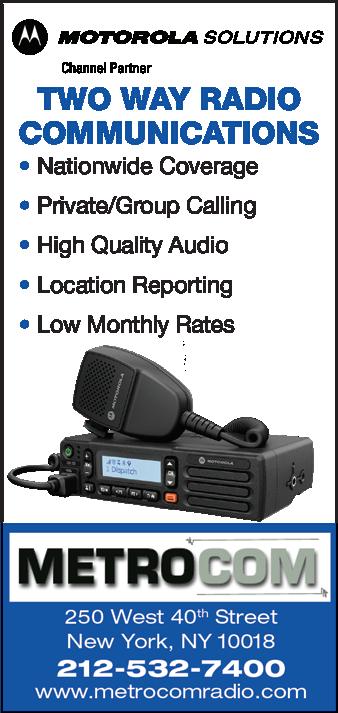

Axle chained to rail car to be lifted along with rail car.
the rail car, I was able to winch it to me while also lifting it high enough to set back onto the track while a forklift helped keep the axle straight.”
Josh set it back on the tracks and was off to the next one. Once set on the tracks, the company pushed the rail car to off load it.

About Pepe’s Towing Service

Pepe’s Towing Service has yards located in Los Angeles, Riverside and San Bernardino Counties. Their specialty and primary focus is medium- and heavy-duty towing and recovery. The company has over 90 employees, a fleet of over 80 trucks, including everything from light to super heavy-duty and specialized equipment.
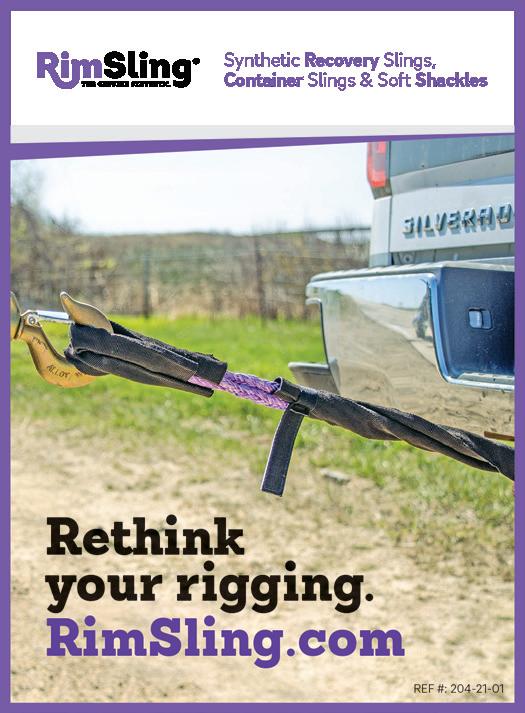


Heavy duty vehicle lift leader Stertil-Koni announced that its U.S. production facility -- Stertil ALM, located in Streator, Illinois – is well on track to produce its 15,000th Mobile Column Lift in 2021.
While Stertil-Koni is widely recognized as offering the broadest range of ALI (Automotive Lift Institute) certified heavy duty vehicle lifts, the company’s Mobile Column Lifts represent its most popular lifting systems in North America – with growth on an impressive trajectory.
These lifts, with capacities ranging from 14,000 lbs. to 40,000 lbs. per column, are indeed mobile --permitting users to safely lift a wide range of heavy duty vehicles quickly and efficiently. “From delivery vans and pumper trucks to school buses and fire engines, from agricultural vehicles and airport tugs to class 8 tractor trailers and utility trucks, Stertil-Koni Mobile Column Lifts can easily raise them all,” explained Stertil-Koni President, Dr. Jean DellAmore.
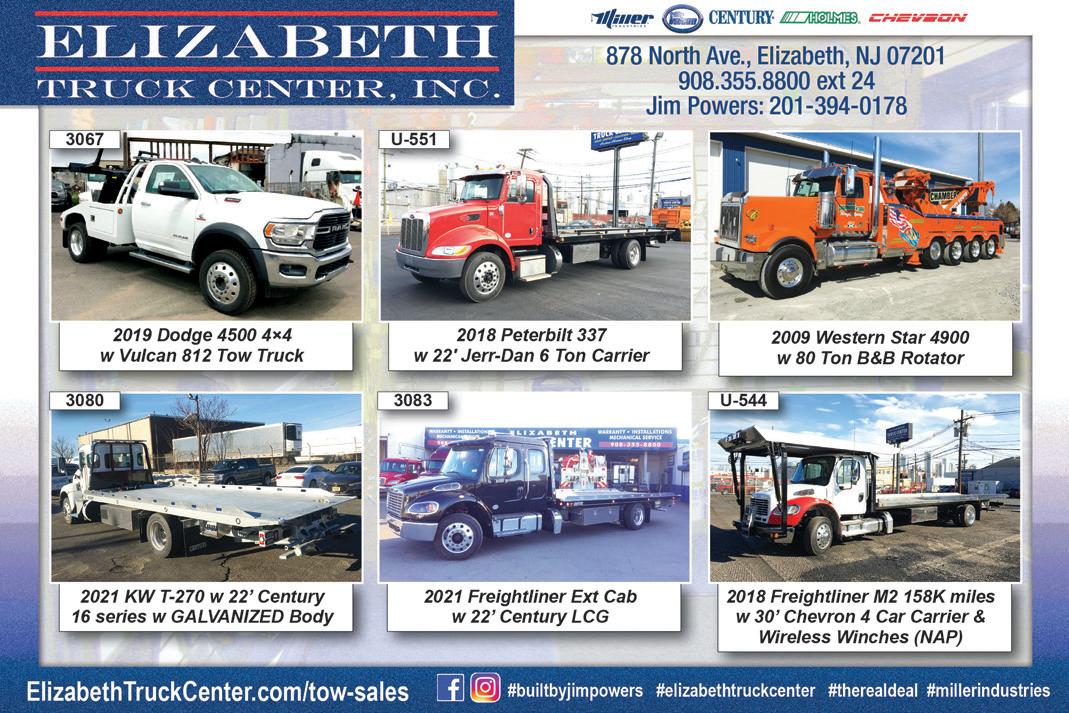
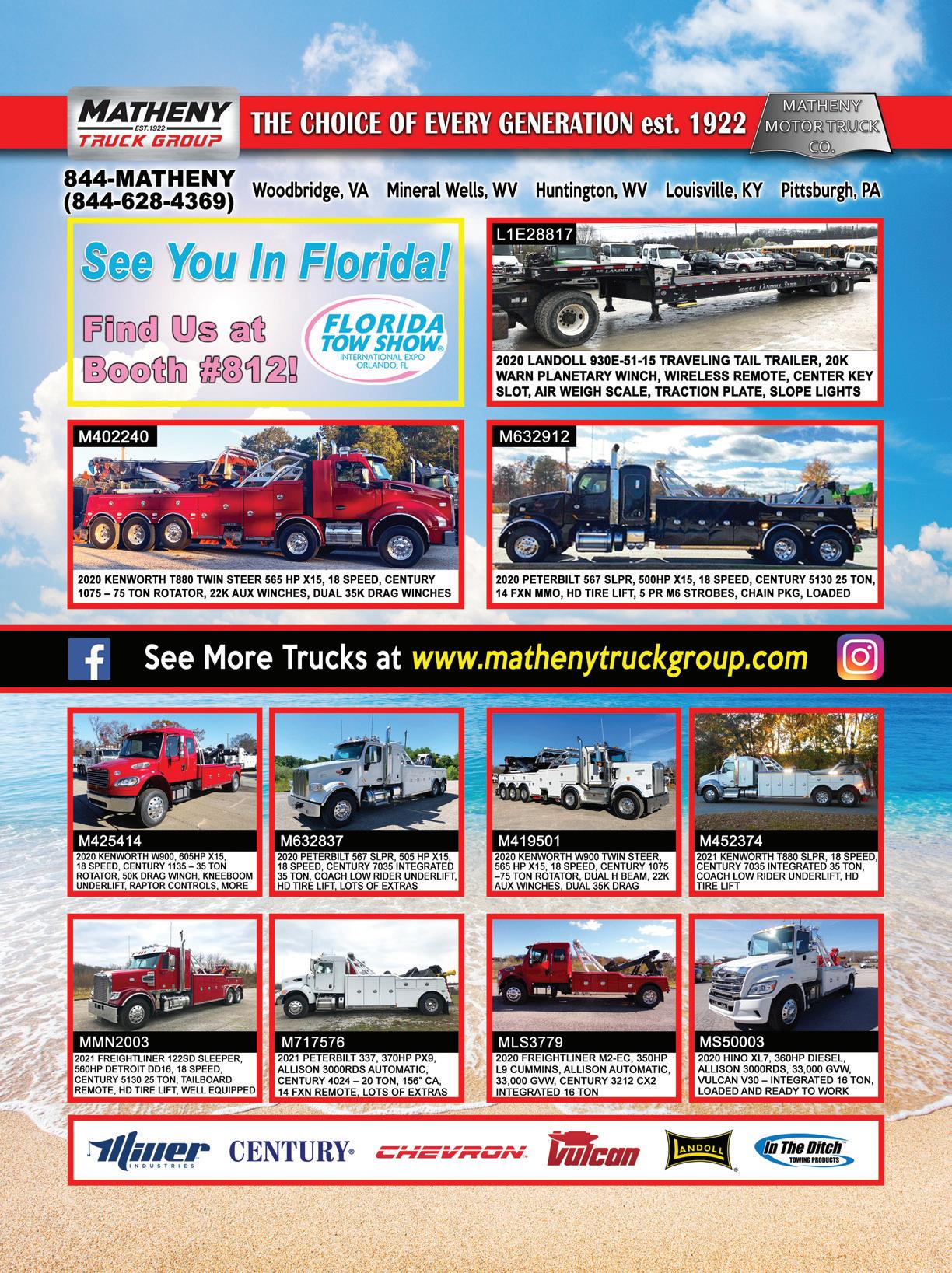
Night Moves UPSTATE

by Jim “Buck” Sorrenti
An Upstate New York tow company works a night shift recovery off a bridge.
In the early morning hours of November 7, 2020, B&W Towing LLC was called to recover a vehicle that went over a bridge. B&W owner Kristen Klemenz went out with the crew. “This incident happened on River Road in the town of Corning, NY at approximately 1:30 am very early Saturday morning.,” said Kristen. “It was a few miles from our shop. We were dispatched by the Steuben County 911.”
Shop manager and rotator operator Blaine Westervelt responded with their Kenworth T800 with a 2019 Century 1150 50ton rotator and operator Leroy Vannatta went out in their 2018 Kenworth with a Jerr-Dan bed. Kristen said, “Leroy, one of our rollback operators, is an amazing guy. He has been with us for over four years. I went out to help and take pictures.”
When they arrived the NY State troopers were on scene. It seems the car left the roadway hit a utility pole and launched across a creek bed in to the riff raff rocks on the other side. There was so much force that it literally shot the car completely under the bridge. The car had severe damage with every air bag blown out.
According to Kristen, the recovery had to negotiate gas and power lines. “We had to use the Century 50-ton rotator to recover the vehicle from under the bridge, between a live gas line that ran along side of the bridge and navigate it between the broken and low hanging utility lines.”

Top: Casualty rigged with an endless loop and two D-rings on the rotator ready for the lift. Bottom: B&W operator climbed down to the casualty to see how to rig for the lift.


Mangled wreck safely secured onto B&W’s Jerr-Dan rollback and ready to be transported back to their yard.
The crew rigged it with an endless loop and two D-rings on the rotator. Blaine boomed the rotator out sideways to get the casualty from under the bridge and then once they had a few hand lines attached, he boomed up and between the gas line and utility lines.
“After the lift, the wrecked vehicle was safely set back on the road, winched and secured onto our Jerr-Dan rollback and transported back to our yard,” stated Kristen. “This was a pretty cool recovery.”
Stayed tuned for more from this dynamic lady and her company.
About B&W Towing LLC
B&W Towing LLC is a local, family owned company based in Painted Post, NY. The company was started in Sept of 2009 with one truck and now has a fleet of over 40 trucks. They are NYS DBE (Disadvantaged Business Enterprise) and WBE (Women-owned Business Enterprise Program) certified and 100% women owned and company owner Kristen Klemenz is very proud of it.
Since 2009, B&W has grown to become one of the largest towing and repair service centers in the Southern Tier of New York. They do repair work on all makes and models for diesel and automotive, offer road side assistance to light- and heavy-duty cars and trucks and also handle NYS inspections on all vehicles. B&W does everything from motorcycle to the tractor-trailer towing and recovery and environmental clean up. They serve one of the largest counties in upstate NY and are expanding in early 2021 to their new location 20 miles away in Bath, NY.
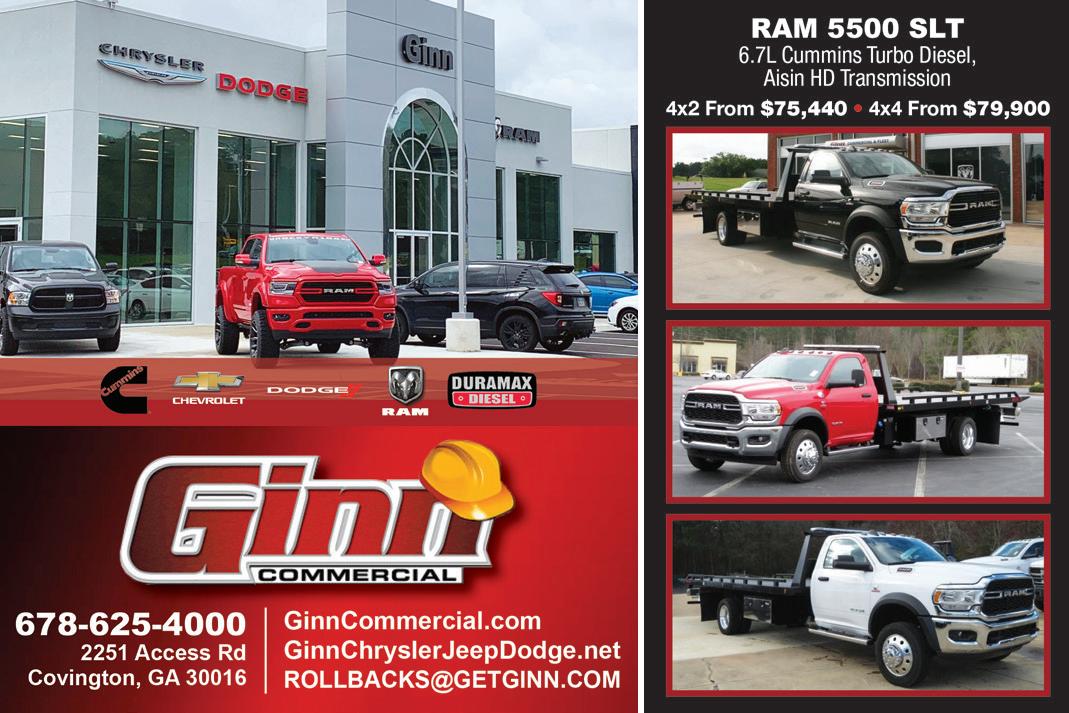
