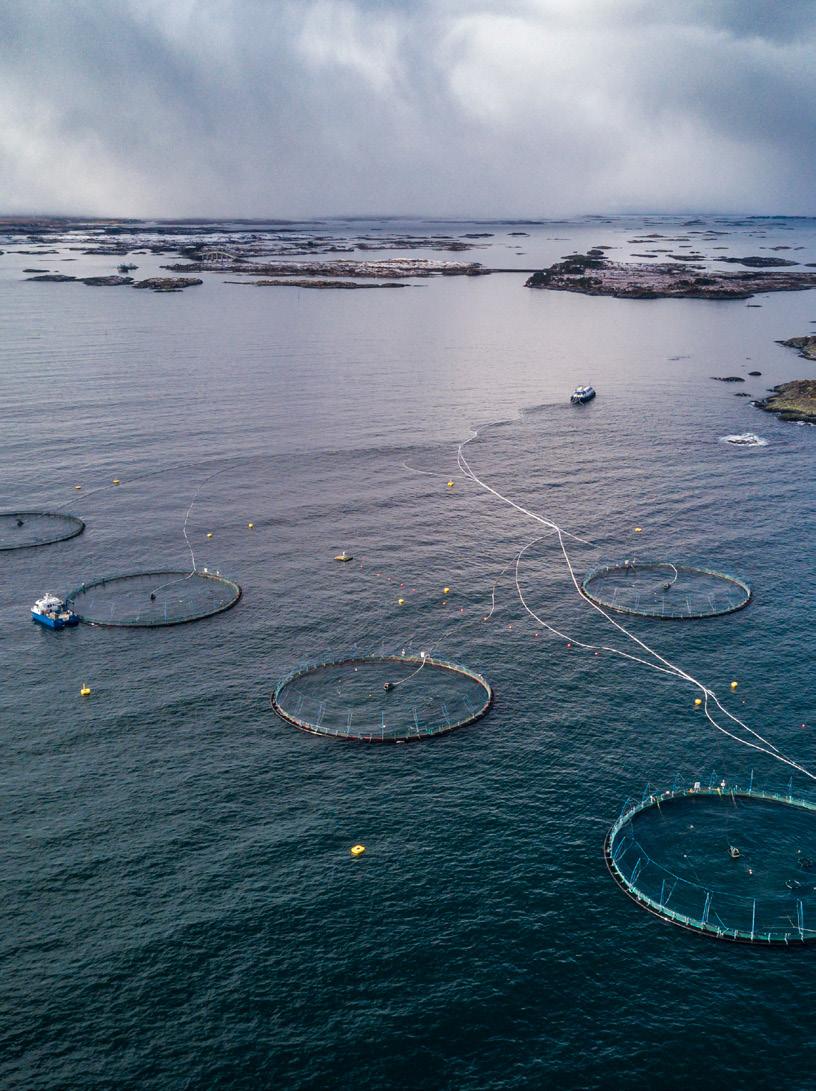
18 minute read
INTERNATIONAL CASE STUDY
AUTOMATING PRODUCTION
at the World’s First Facility Making Omega-3 Oil from Marine Algae
Advertisement
BY DELL WILLIAMS
When two international companies created the world’s first high-volume facility that manufactures omega-3 oil from natural marine algae, the $200M joint venture had to minimize any impact at the plant, which was already producing another product. Even more challenging, this had to be accomplished while adding new automation capabilities and upgrading a variety of systems and equipment.
Today, in “landlocked” Blair, Nebraska, the joint venture – called Veramaris, between German-based Evonik and Royal DSM of the Netherlands – sustainably produces omega-3 fatty acids without using fish oil from wild-caught fish, with unique production capabilities that enable a much larger scale of production than ever seen before in algae cultivation. The breakthrough combines a special strain of algae of unprecedented richness in EPA and DHA omega-3, two fatty acids that are proven essential for good health in people and to produce healthier farmed fish. Veramaris’ mission is to expand the world’s access to sustainable EPA and DHA in support of aquaculture growth, as a means to provide healthy, nutritious seafood with a smaller environmental footprint.
Much of the challenge in creating this facility revolved around how to effectively and efficiently scale up to full production after several years of research and development. The answer, it turns out, involved implementing significant automation in a successful collaboration between the international companies and vendors, which contributed the necessary expertise to different aspects of the project.
“The project involved taking some of the existing plant’s capability and repurposing that to produce the omega-3 oil, which required new equipment and controls. At the same time, the plant’s automation system was upgraded. Basically, every arrow in our [automation] quiver was used, so to speak,” says Dwight Wood, vice president of global sales for Owings Mills, Maryland–based NovaTech LLC Process Division, which specializes in continuous control system architecture.
“This was a very complex, demanding project with a tight schedule and a diverse global team, so it was a monumental task to bring it all together and integrate it into an existing production line, while separating out new equipment,” adds David McBride, automation engineer at the Blair, Nebraska, plant.
According to Wood, NovaTech’s portion of the project included implementation and integration of a Distributed Control System (DCS) update and expansion; new applications programming, a High-Performance Human-Machine Interface graphics; sophisticated S88 batch management software;
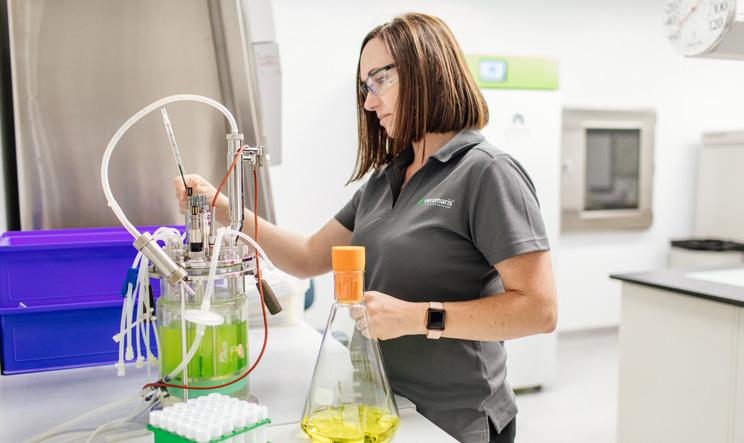
Work in the laboratories at the Veramaris facility in Blair, Nebraska. Credit: Dana Damewood Photography
Veramaris, the joint venture of DSM and Evonik, held a topping-out ceremony on site in Blair, Nebraska.
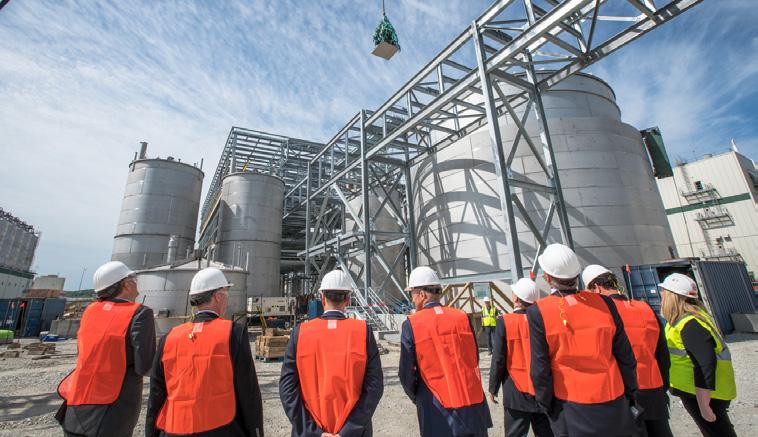
an updated real-time data historian application; and I/O migration from an older version to a new modern I/O platform, along with startup and ongoing onsite support.
“The key was implementing the full set of processes in a very robust, reliable, flexible system. It also needed to be highly automated, so the plant can effectively run on its own with minimal operator interaction,” says Wood.
While many companies may begin with a standardized solution, as a project develops, much customization often needs to be done to tailor applications to specific processes.
“On a different project, we worked with a larger automation vendor and they refused to cater to some of our special needs, and instead required us fit into their mold,” says McBride. “NovaTech, a mid-sized company, was more flexible and quickly able to offer custom solutions.”
Although certain procedures and processes are increasingly standardized and automated, numerous key steps in and around the automation are still dependent on operator input or manual intervention. When the operator is interrupted to handle other tasks or responses vary from operator to operator, off-spec product can result, requiring costly corrective steps or product disposal.
So, to minimize such potential operator variability while enhancing automation along with consistency and reliability, DCS are utilized. A DCS is a hub of a processor’s operations and monitors key variables such as flow, applied temperatures, pressure, level and material conveying/handling. The operator user interface brings all the data collected from production equipment and the controllers process and presents it in a highly “human factored” manner for an operator, generating trends, alarms, etc.
While the plant was already utilizing NovaTech’s D/3 DCS, this was further upgraded to display real-time process information in a complete, high-performance graphical human-machine interface. Custom graphics, built using dynamic objects from an extensive library, make it easy for the operator to control the process, enter information and interact with sequence programs.
“For this particular project, there were extremely stringent specifications to produce the end product, so batches must be performed reliably and correctly every time,” explains Wood, who notes that NovaTech had a team of engineers onsite at the plant. “We worked with the customer to understand the requirements, and then outlined an automation strategy to meet their specific goals from a control perspective.”
According to Wood, dealing with fermentation processes can be challenging to control due to a number of variables. The process involves preparing vessels, incoming media and downstream tanks, as well as managing volume, time and temperature in regards to the cultivation of beneficial microorganisms essential to the process.
“Because of all the demands for successful fermentation, it is vital to fully understand the criteria and parameters before executing an automation strategy. This must be aligned to satisfy the control and production objectives,” says Wood.
When manufacturers produce batches, particularly when utilizing fermentation, they are trying to replicate a perfect “golden batch” each time. Toward this end, the project integrated ISA S88-based layered batch management software called FlexBatch, which is designed to help reduce cycle times and life-cycle automation costs. It was also implemented to
aid control and flexibility when slight recipe adjustments may be required.
The batch management software integrates recipe management and the automation layer so operators can quickly and easily develop, scale up, modify and schedule batch manufacturing recipes as required.
Comparing each batch historically against the perfect standard also can be an important element of maintaining quality control. To enhance this capability, the project integrated an upgrade to the PI System by OSIsoft, a real-time data historian application with a highly efficient database. The application efficiently records data from process control systems like the NovaTech D/3 into a compressed timeseries database. This provides manufacturing sites historical predictive insights in real-time.
“It is important to have both real-time and historical access to product data. Having the ability to quickly retrieve that kind of information allows manufacturers to more consistently manufacture product of the highest quality and integrity. And if there is ever a problem with product in the field, it simplifies tracking and troubleshooting,” says Wood.
In order to implement plant automation, it also was necessary to migrate to a modern I/O system, the 8000 series platform, a remote I/O family native that is highly integrated with the D/3 system. “The combination facilitates greater automation with better diagnostics, troubleshooting and asset management capability. With the configuration used, we can drill down to the controller, to the specific I/O card so the operator does not have to go into the field to get the status of a specific card,” says Wood.
Since there were hardware, software and engineering requirements tied in to the project, NovaTech tested these in its facility before implementing them at the plant. “Even with state-of-the-art manufacturing equipment, controls and production automation in place, how these are applied makes all the difference in the success of the project,” concludes Wood.
With the automation project now complete, the plant is producing omega-3 oil from natural marine algae, with the capability of producing enough EPA and DHA equivalent to that derived from 1.2 million tons of wild-caught fish each year. The plant’s initial annual production is expected to meet about 15 percent of the current total demand for EPA and DHA in the salmon aquaculture industry.
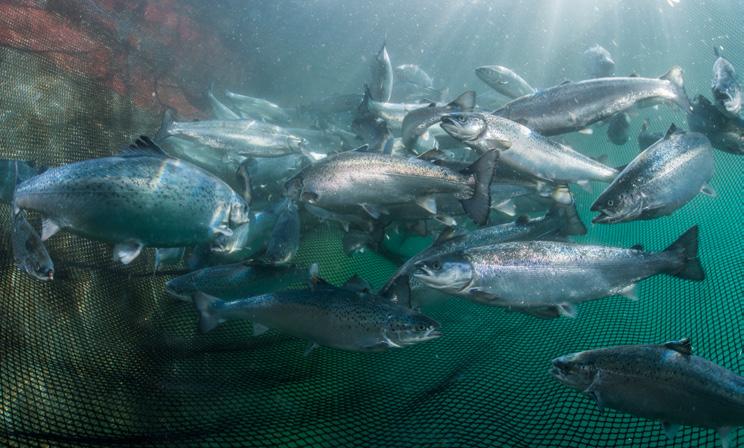
Aquaculture farm on the Norwegian island Smøla close to Kristiansund. For more information, visit: novatechweb.com.
Thrive Bioscience recently introduced the CellAssist, which enables cell culture researchers to image, analyze and document all cells, plates, reagents and workflow details in a centralized database. The CellAssist raises the bar for adherent cell culture by imaging and analyzing all the cells in a plate, not just cells chosen during typical manual inspection. Minutes after inserting a standard multi-well plate, the CellAssist captures, analyzes and displays hundreds of high-resolution images of cells at multiple magnifications, using phase contrast or bright-field. The visualization and analysis software allow researchers to comprehensively review images and metrics of the entire history of a project from one’s office or laboratory. thrivebio.com
COVID RESULTS IN MINUTES
The Hyris bCUBE was recently approved by Health Canada for use as a medical device for COVID-19 human testing. As a portable device, the Hyris bCUBE provides onsite and accurate results in minutes. The Hyris bCUBE is a portable DNA-testing laboratory in a box, offering Point of Care (POC) testing wherever people are – anytime, anywhere. Controlled by any device with an internet connection, including a smartphone, the scientifically validated bCUBE analyzes test samples through a cloud-based platform that delivers accurate results in minutes. The device deploys PCR (Polymerase Chain Reaction) technology that has demonstrated a 95%+ accuracy rate in clinical trials. songbirdlifescience.com
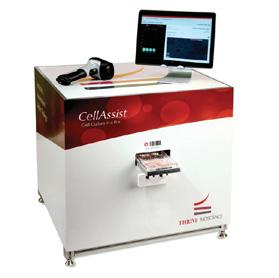
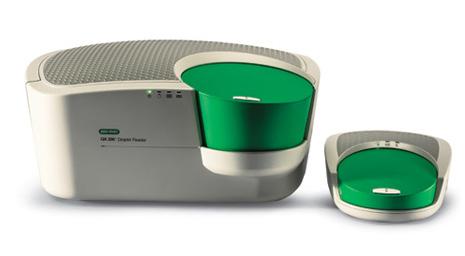
QX200 DROPLET DIGITAL PCR SYSTEM
The QX200 Droplet Digital PCR (ddPCR) System provides absolute quantification of target DNA or RNA molecules for EvaGreen or probe-based digital PCR applications. Offering precise and sensitive digital PCR solution for a wide variety of applications, the system features flexible digital PCR chemistry – optimized for TaqMan hydrolysis probe and EvaGreen assays, flexible assay setups that are scalable for high sensitivity or high throughput, droplet partitioning by the QX200 Droplet Digital technology to reduce bias from amplification efficiency and PCR inhibitors and a host of other benefits. It’s ideal for a full range of applications, from cancer biomarker studies to environmental monitoring. bio-rad.com
TTA TABLE TOP ROBOTIC SYSTEM
A compact design that is extremely flexible, this table top robot is precise and multi-functional. It arrives prefabricated and fully assembled with a built-in controller ready for use. It is idea for clinical environments, with eight types of functions such as pick and place and sorting applications. The dedicated ZR-axis option enables video image processing and analysis for micro-dosing applications in biotechnology. It is equipped with a battery-less absolute encoder, a high-precision AC servo motor and a new PC software SEL Program Generator that enables the positioning data simply by drawing the operation path on the screen. intelligentactuator.com
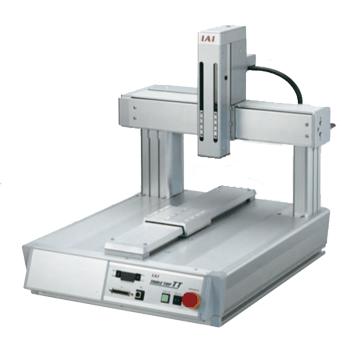
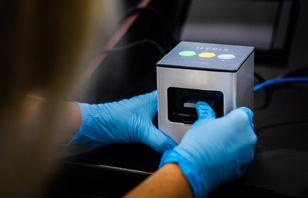
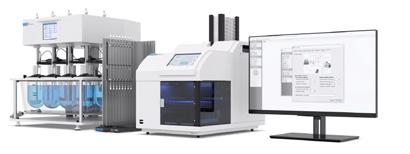
NEW PLASTIC ANALYZER SIMPLIFIES EVALUATION OF PLASTIC DEGRADATION
Shimadzu recently released its Plastic Analyzer, a Fourier transform infrared (FTIR) spectrophotometer that is ideal for analyzing microplastics or contaminants, like those floating in marine environments. The system includes an IRSpirit FTIR spectrophotometer, a thermaldamaged plastics library, a newly released UV-damaged plastics library which is a database for identifying plastics degraded by ultraviolet rays, a new plastic analyzer method package and a QATR-S single-reflection ATR accessory for the IRSpirit series. The system allows accurate identification of contaminants with significantly more accuracy than before. shimadzu.com
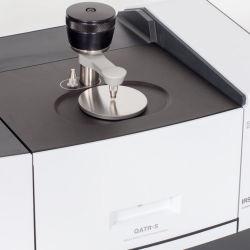
TAQMAN REAL-TIME PCR ASSAYS
Quantitative PCR (qPCR) or real-time PCR is used for sensitive, specific detection and quantification of nucleic acid targets. To help harness the power of qPCR across a range of applications, Thermo Fisher developed powerful new assay design algorithms, supported by intuitive data analysis software. Applied Biosystems TaqMan real-time PCR assays consist of target-specific primers and one or more probes optimized for specific applications, including gene expression, SNP genotyping, miRNA, mutation detection and copy number variation analysis. The company’s predesigned assays can detect virtually any gene product, offering powerful-coverage assays that can detect the highest number of transcript variants possible. thermofisher.com
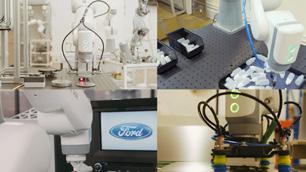
AWARD-WINNING NANODIS SYSTEM
Agilent’s NanoDis System provides formulation scientists with accurate release profiles of APIs using conventional dissolution apparatus in an automated, compliant manner. This functionality enables analysts to uncover the best nanoparticle formulation faster and get new drug formulations to market more quickly. It enables an easy transition from research and development to quality control environments and achieves consistent, reliable dissolution results for nanoparticle-based formulations in an automated process while ensuring cGMP compliance. The Agilent NanoDis System was selected as a finalist for the CPhI Pharma Awards for excellence in Pharma: Analysis, Testing and Quality Control. agilent.com
EVA LAB AUTOMATION SYSTEM
Eva is the affordable solution for the automation of lightweight (<1.25kg) pick and place applications. It is best suited to highly repetitive processes that don’t require skilled staff to perform. The most common use cases for Eva include machine tending, product testing, inspection, sorting and lab automation. Lab automation has a number of different applications that are suited for Eva, including: loading and unloading plates, cuvette and Eppendorf tubes for analysers and centrifuges. Eva can easily integrate with liquid dispensers, plate washers or readers, allowing to run tests both during the day and overnight. automata.tech
LIST OF ADVERTISERS & WEBSITES
BioTalent Page 2..................................................................biotalent.ca/wagesubsidies Metrohm Page 5................................................................metrohm.com/spectroscopy CPDN Page 47 .................................................................................................... cpdn.ca CLSA Page 48...................................................................... clsassoc.com/memappl.tpl
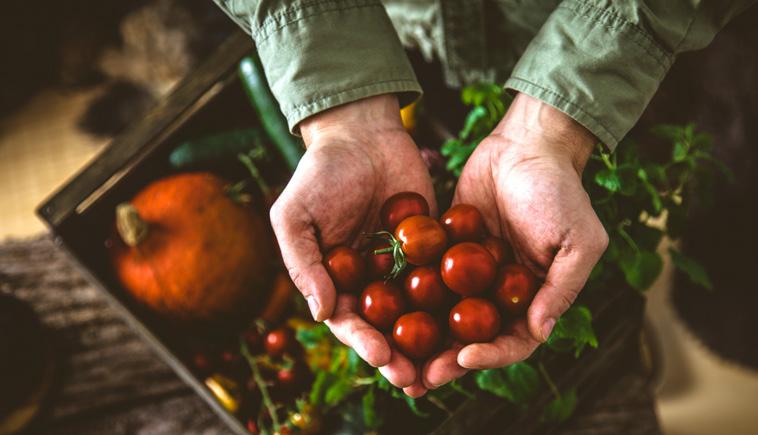
Three Pandemic Trends That Are Here to Stay
WHILE the pandemic has presented some of the biggest challenges food businesses have ever faced, it’s also been exciting to witness so much innovation. We’ve seen hundreds of businesses across Canada and around the world get creative and pivot literally overnight in order to thrive in this fast-paced and unpredictable world. From farmers and grocers, to breweries, bakeries and meal prep companies, everyone is getting on the innovation bandwagon.
When COVID-19 hit, grocers in particular experienced an unprecedented spike in demand. But consumers who normally shopped at retail stores faced empty shelves, long lines and stay-at-home orders. So, many turned online and formed new behaviours – and there’s mounting evidence these new behaviours are here to stay. A recent study of nearly 60,000 U.S. shoppers projects online purchases will account for about 21.5 percent of total U.S. grocery sales by 2025.
This is just one of many exciting new trends in the world of grocery. Here are some more:
Trend #1: Shop local
The local food movement is undergoing a renaissance thanks to COVID-19, with local farms, producers and CSAs seeing a significant uptick in demand.
“We got lucky in that we didn’t have any supply chain interruptions,” says Jesse Bradley, fleet manager at Local Foods, a retail market and wholesale distributor in Chicago. “Whether or not there is a pandemic going on, crops are still going to be growing and farmers are still going to be harvesting. Our ultimate strength is how high-quality our product is and where the produce comes from. When you buy apples from us, it’s really the freshest food you can possibly get outside of going to an orchard.”
Such local producers or distributors – also known as “farmto-table” or “farm-to-door” – present an enticing offering: First, supply chain transparency gives consumers a sense of security, knowing exactly where their food has come from. And second, fewer touch points means a much lower risk of contamination.
As a result of the pandemic, local farms and food hubs have raised their profile as a healthy, sustainable and resilient source of food for communities around the world.
Trend #2: Home delivery is everywhere
As people stay at home for their health and safety, home delivery has become a critical offering. The pandemic has forced grocers to meet this demand in order to keep their businesses afloat. Toronto-based wholesale grocer Bondi Produce – which traditionally supplied restaurants and institutions – is a great example.
“Our business took a big hit,” says warehouse supervisor Claudio Bondi. “We locked ourselves in a boardroom and said ‘How can we stop the bleeding?’ We had always wanted to get into home delivery and expand our product range, and this was our chance to test those waters.”
Within two weeks, they put up a new website complete with an online store, and then retrofitted the back of the wholesale warehouse to house grocery and home delivery items. The team then integrated delivery management software which allowed them to plan and execute on the hundreds of home deliveries orders that came flooding in as people refrained from going into traditional retail grocery stores.
“Right off the bat, it was a huge hit. And because we’ve implemented delivery management and routing technology, our home delivery business has the potential to scale. We plan to continue to offer a home delivery service even after the pandemic is over,” Bondi says.
Trend #3: Zero waste
Local food businesses and their consumers are often passionate about protecting the environment. In fact, the movement towards zero waste is gaining momentum across all industries. But when it comes to running a profitable business, sustainability isn’t easy to achieve.
“If you are not organized and ready for a zero-waste, returnable packaging model, it can actually turn into a liability very quickly. But if you plan ahead, you can actually increase your margins,” says Jeff Pastorius, founder of On The Move Organics, a company that delivers local and organic food to communities across southwestern Ontario.
On The Move makes their deliveries in large Rubbermaid bins, and smaller items are packaged in glass jars within the bins. After deliveries are made, these containers are picked up on a subsequent delivery, sanitized and prepped for another delivery.
“People will often pay a deposit of one dollar on a jar, and this would normally cover the cost of disposable packaging. So, even if the customer doesn’t return the jar, we’ve offset the cost and reduced risk – all while maintaining our zero-waste strategy,” Pastorius explains.
Implementing an efficient zero-waste program takes time and effort – but it’s worth it if it means staying true to the company’s core values. “This is an industry where you need to take your punches and learn how to make this work in the interest of the Earth not imploding,” Pastorius adds.
By taking a hard look at the opportunities in front of them, these companies are making the best of a tough situation. Typically, rethinking their business model was the first step to success, and home delivery has become a saviour for many food suppliers.
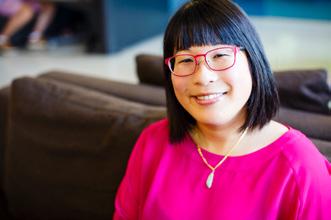
Suzanne Ma is co-founder at Routific, a delivery management and route optimization solution that helps local food businesses scale up home delivery operations.
EDITOR’S NOTE: COPING WITH CHANGE, & MAKING A DIFFERENCE
Along with exposing Canada’s food security and distribution issues, we all know that COVID-19 has impacted the restaurant and bar industry on a dramatic scale. Restaurants Canada estimates that 10,000 restaurants closed in 2020, resulting in approximately 800,000 job losses; if lockdowns continue, it’s estimated approximately 50 percent of restaurants could shut down. From what I’ve seen, I’d guess more.
Several organizations, including Restaurants Canada, are engaging in campaigns to support local businesses; delivery and pickup options have contributed to the survival of many restaurants, and retailers in general, although few can say they aren’t losing money, according to most reports.
To support those who work(ed) in the hospitality industry, Not9to5.org is a new online initiative, providing mental health resources and educational courses “to educate and empower hospitality workers and employers on mental health and substance use literacy and support skills.”
In the realm of food security, one of the people who is making a big difference in Canada is Lori Nikkel, CEO of Second Harvest (interviewed in the Spring 2019 issue of Canadian Food Business). In February, she was appointed as a member of the new Canadian Food Policy Advisory Council, established by Agriculture and Agri-Food Canada. The Canadian Food Policy Advisory Council is a key component of the Food Policy for Canada and brings together 24 experts and stakeholders from a variety of sectors, including the agriculture and food sector, health, academia and non-profit organizations.
As the CEO at Second Harvest, Canada’s largest food recovery charity, Nikkel led the recovery and redistribution of more than 22.3 million pounds of healthy, unsold food to nonprofits across Canada in the last year. She was also named as one of the 2021 Women of Influence for her role in expanding the organization’s reach during times of need; a nationwide effort by Second Harvest provided approximately 62,000 meals per day. Nikkel also was a key player in the Surplus Food Rescue Program, which purchases surplus produce from farmers to be distributed to community groups such as shelters and school breakfast programs.
In times of crisis, when the community supports those in need, we all come out ahead. Thank you to everyone who is making a difference!

New Tracking Tech For Livestock
A new direct-to-satellite smart livestock ear tag, Ceres Tag (developed in Australia) is a gamechanger for farmers with large herds. The solar-powered tag is an accelerometer with RFID technology, the first of its kind designed to meet accreditation guidelines with national livestock traceability programs. Each tag lasts more than 10 years to ensure lifetime coverage. Recently, Ceres Tag announced the addition of eGrazor technology, developed by Australia’s government agency, CSIRO; the sensor uses algorithms to monitor a wide variety of cattle behaviours, including pasture feed intake. cerestag.com
Study Generates Genomic Atlas For Global Wheat
Fifteen varieties of wheat from around the world were catalogued by a team from the University of Saskatchewan, enabling scientists and breeders to much more quickly identify influential genes for improved yield, pest resistance and other important crop traits. The research results, published in Nature, provide the most comprehensive atlas of wheat genome sequences ever reported. The 10+ Genome Project collaboration involved more than 95 scientists from universities and institutes in Canada, Switzerland, Germany, Japan, the U.K., Saudi Arabia, Mexico, Israel, Australia and the U.S. One of the world's most cultivated cereal crops, wheat plays an important role in global food security, providing about 20 percent of human caloric intake globally. It’s estimated wheat production must increase by more than 50 percent by 2050 to meet increasing global demand.
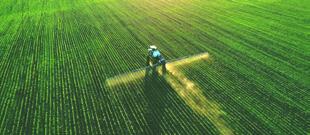