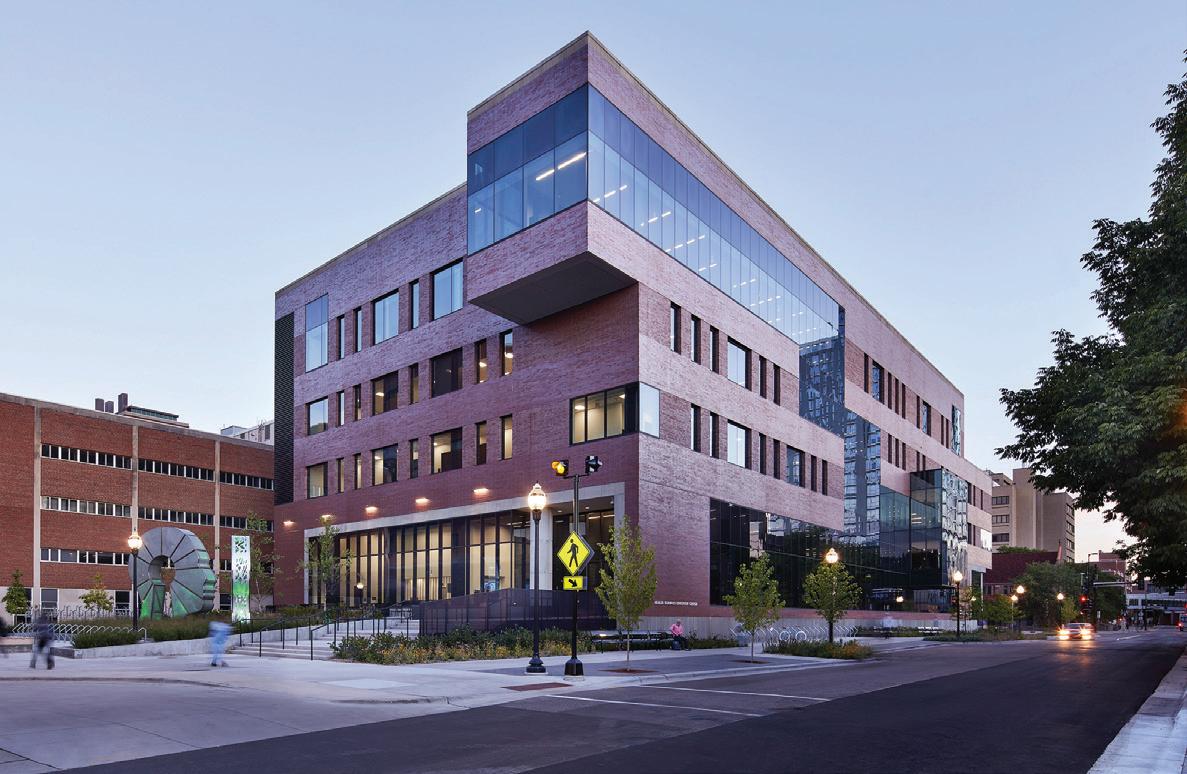
4 minute read
University of Minnesota Health Sciences Education Center
PROJECT SPOTLIGHT
Minneapolis, Minnesota
CHANGING THE FUTURE OF HEALTHCARE
Changing education and evolving healthcare needs means that many university programs and facilities are changing as well to accommodate 21st century team-based learning and advance integrated healthcare across the state. With approximately 150,000 gross square feet of new construction and the renovation of roughly 52,000 gross square feet of existing space in the Phillips-Wangensteen Building at the University of Minnesota, the school’s new Health Sciences Education Center (HSEC) is now the front door to the Academic Health Center (AHC). The building is designed to support the AHC’s interprofessional education model and fosters a team-based, experiential approach to patient-centered care training to better serve 70 percent of Minnesota’s healthcare professionals. It includes a new three-story, above-grade, 149,000 SF building that features formal learning environments that foster unparalleled student-teacher interaction, state-of-the art immersive simulation suites, knowledge creation and knowledge management spaces, as well as social learning spaces outside of the classroom.
CREATIVE LOGISTICS FOR CONSTRUCTING ON AN ACTIVE CAMPUS
HSEC required mass demolition of two existing buildings that occupied a majority of the two-acre site. The project site was flanked on all sides by fully occupied buildings including an active hospital, a 15-story clinical building, a church, and two student housing facilities. This required JE Dunn to assemble an extensive disruption avoidance plan including items such as dust control, vibration monitoring, existing utilities investigation/ identification, emergency vehicle access, and public vehicular and pedestrian traffic control. “During demolition, JE Dunn had
trades people in aerial lifts with fire hoses spraying down demolition debris in addition to misting machines in an effort to control dust migration on site,” said Senior Project Manager Brett Dunlap.
Logistics on the job were further complicated by both above- and below-grade conditions. As an example, the only viable location for the tower crane on the project was located over an active below-grade pedestrian tunnel serving the adjacent hospital, which required some innovation solutions. “Our team came up with a design that incorporated a four foot concrete pad spanning the existing tunnel with a city base for the tower crane. This pad was supported by a combination of drilled soldier piles extending to bedrock on one side and micropiles and grouted tiebacks on the other side. These micropiles needed to be strategically located to avoid existing electrical duct banks serving the active hospital,” said Dunlap. At other locations around the site, additional micropile clusters were also installed to accommodate concrete pump truck outriggers. This allowed us to span the pedestrian tunnel and transfer loads down vertically to avoid overloading our soil retention system and the pedestrian tunnel walls.
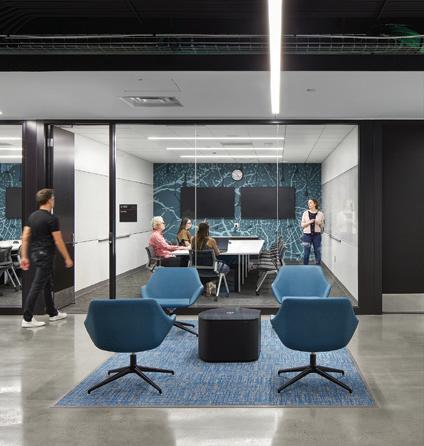
MINIMIZING DISRUPTION THROUGH TECHNOLOGY
Keeping the renovation portion of the project on schedule while working within an existing building that was 75% occupied presented many challenges. This is where the team leveraged BIM technology to complete the work efficiently while minimizing disruption to the owner as well as the students and staff using the building each day. The renovation work within the existing 15-story Phillips-Wangensteen Building, including 53,000 SF of remodeling levels 2, 3, 4 and 5, which tied into the state-of-the-art Health Sciences Education Center. To coordinate new MEP systems within the existing construction to remain, our team provided BIM and select laser scanning for verifications. We also worked closely with University Facility and Energy Management staff to complete base line test and balance readings prior to construction to ensure occupied floors above and below were not negatively impacted by demolition and construction activities. JE Dunn self-perform crews completed all selective demolition and carpentry for the renovation, which included structural saw cutting for the new grand stair connecting all renovated floors.
Working above, below, and adjacent to building occupants, the team coordinated with University classroom management staff to schedule any noisy construction activities around classes and exams, but the deliveries required careful planning as well. The team relied on a simple solution that was easily accessible technology for all partners—a phone app. “Using the Microsoft Bookings app with trade partners allowed the team to coordinate construction deliveries around University events (e.g., move-in day, game days, etc.) and allowed trades to reserve on-site loading dock space, tower crane picks, and hoist time,” said Dunlap. “This technology helped the team anticipate deliveries to better manage traffic congestion and reduce disruptions to University operations.”
A FACILITY FOR THE FUTURE
From creating formal learning environments for student-to-student and studentto-teacher interaction to immersive simulation suites for outpatient, inpatient and general clinical training, the team worked hand in hand with the owner to ensure all needs of the finished facility and renovations met everyone’s needs. “Working on a highly active site on a project with unique teaching and lab space components always presents new challenges,” said Dunlap. “Thanks to collaboration with the client and some creative thinking, we were able to deliver a facility that will help shape the next generation of healthcare innovators.”
Our team implemented air monitoring and installed vibration monitoring equipment in adjacent buildings to ensure there were no disruptions to ongoing operations, clinical care, and research.”
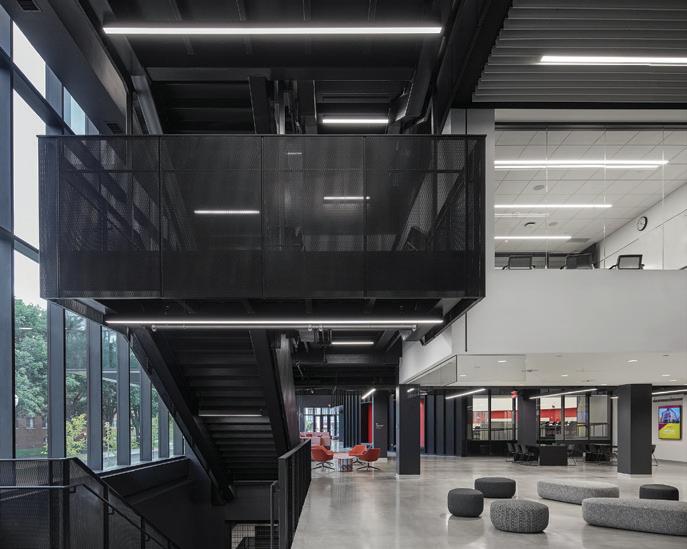