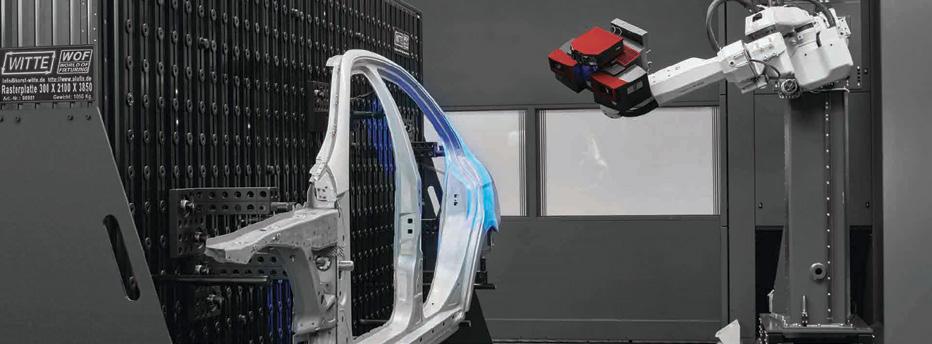
7 minute read
La revolución del IIoT avanza en
La revolución del IIoT avanza en la industria del metal
Gracias al auge de la Internet Industrial de las Cosas (IIoT), los fabricantes de herramientas están desarrollando soluciones inteligentes, dotadas de sensores y tecnología que aporta información durante las operaciones de mecanizado. Asimismo, a través de la filtración y digitalización de datos, han logrado incorporar de manera integral los procesos de producción. Así es la era de la fábrica digital.
Advertisement
Los procesos industriales en cuanto a producción, delatan un mundo digital donde coexisten soluciones orientadas a la gestión segura de los datos generados. Sumado al aporte tecnológico de una fabricación aditiva junto a materiales innovadores, agilizan y optimizan los procesos.
Brevemente y a continuación, se describen algunos ejemplos de las tendencias y conceptos que marcan el mundo tecnológico en cuanto a la producción actual.
Fabricación aditiva, su esencia La fabricación aditiva, que rápidamente se instaló en el entorno industrial, no es una sola tecnología, sino que son muchas. Una soldadora por deposición Láser, genera un baño fundido en la superficie del componente en el cual se introduce polvo metálico con ayuda de un inyector. Proceso utilizado en la aplicación de capas de protección contra el desgaste, reparación de componentes y creación de nuevas estructuras. A su vez y con máquinas Láser, mediante un proceso aditivo, es posible fabricar componentes a partir de lecho de polvo.
También es necesario saber que las capas funcionales y las estructuras de los componentes, también se pueden crear sin la utilización Láser. Mediante un proceso de impresión rotativa, el material semiacabado se deposita en la superficie del componente, fundiéndose por el efecto de la fricción generada e integrándose a él. Este es el caso de la tecnología de impresión en 3D.
Con un paquete de software, y una impresora 3D constituye una solución para la fabricación aditiva con metales. La producción es apta para diversos productores y procesos. Los datos se importan, se coloca el componente y de esta manera es posible crear y optimizar estructuras y geometrías con vistas a una fase de producción.
Tecnología integrada y sensores Un claro ejemplo es el desarrollo realizado por Sandvik Coromant, que muy bien representa su visión de la Industria 4.0. La plataforma CoroPlus, integra sensores en herramientas y portaherramientas utilizados en los procesos de mecanizado.

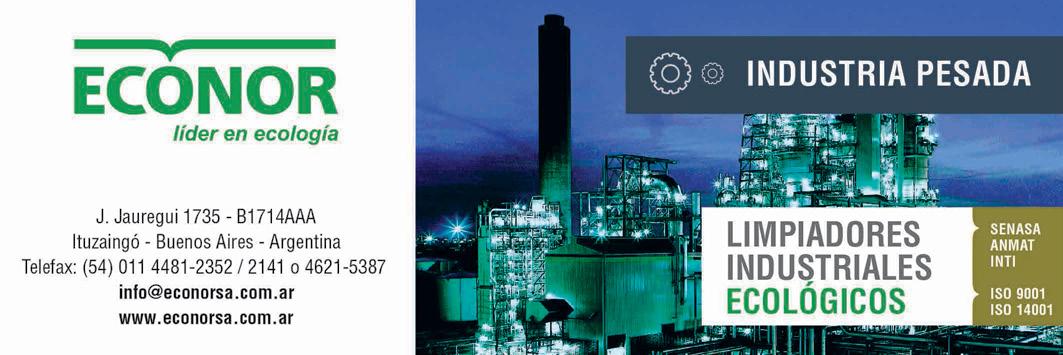
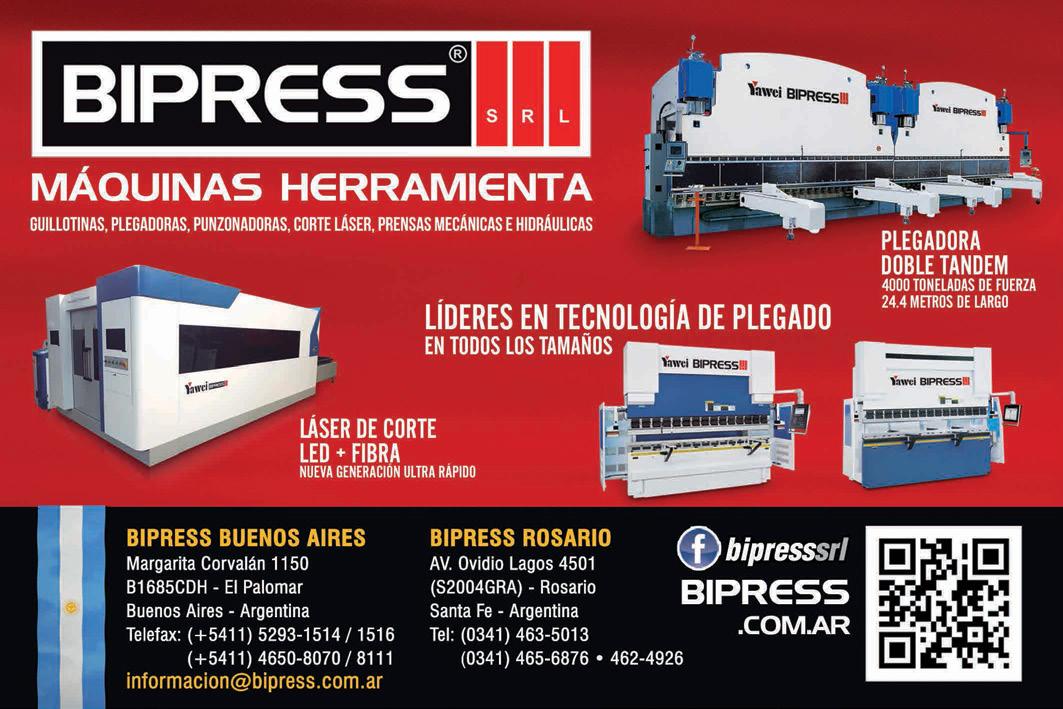
visar el proceso de replegado de la cuchilla. Los datos se transfieren al sistema de control de la máquina mediante un protocolo de comunicación desarrollado específicamente con dicha finalidad, el cual impide que la herramienta entre en contacto con algún punto de la superficie del componente si la cuchilla no se repliega correctamente.
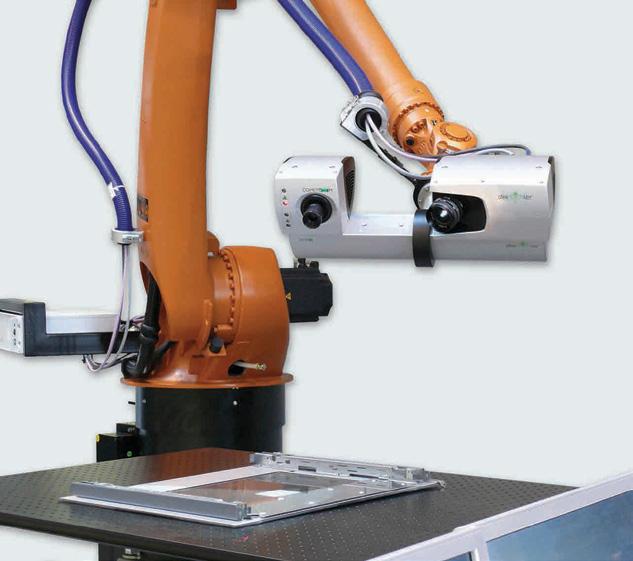
Los portaherramientas inteligentes envían datos sobre los tiempos de ejecución o el nivel de carga y de batería a una aplicación, posibilitando así el mantenimiento predictivo. A su vez, los cabezales de perforación fina pueden ajustarse al milímetro gracias a una aplicación diseñada para la perforación de orificios con diámetros muy precisos.
En tanto BIG Kaiser (Suiza) desarrolló una tecnología similar con el valor agregado de que no es necesario realizar ajustes manuales constantes en el dispositivo de preconfiguración de la herramienta, la que puede desplegarse y replegarse adaptándose a los distintos diámetros mediante una aplicación cargada en una tablet. De esta manera es posible acortar la cadena de procesos y reducir los tiempos no productivos dedicados al ajuste de herramientas.
Avellanadoras inteligentes Estas fresas se emplean cuando el mecanizado se realiza en una superficie que solo es accesible a través de un orificio, como ocurre con las carcasas cerradas. Si se invierte el sentido de rotación, la cuchilla de la herramienta se despliega. Para poder extraer la herramienta del orificio tras el mecanizado, es necesario replegar la cuchilla.
En el marco de un proyecto emprendido conjuntamente con O. Bilz y EWS, Hermann Bilz han desarrollado una herramienta avellanadora que permite super
Orden y almacenamiento Fabricantes de herramientas de precisión como Iscar, Gühring o Sandvik, y empresas especialistas en metrología, como Zoller GmbH, cuentan con soluciones de almacenamiento inteligente de herramientas, componentes y accesorios. Es mucho más que orden.
De esta manera el usuario puede calcular los costos exactos asociados a la herramienta y cada uno de sus componentes, asegurarse de que las herramientas siempre están disponibles al instante y evitar seleccionar la herramienta incorrecta.
Asimismo, los sistemas inteligentes se conectan a la máquina-herramienta y reciben información sobre cualquier desperfecto, activan el proceso de pedido al vendedor y proporcionan al operario una herramienta de características constructivas idénticas. Los flujos de herramientas en el entorno de producción son de este modo mucho más claros y transparentes.
Filtración de datos Las innovaciones en torno a IIoT (Internet Industrial de las Cosas) se plantean ofrecer soluciones para la producción digital conectada, donde los sistemas pueden conectarse a distintos niveles. El paso siguiente es preguntarse si todos los datos deben enviarse a La Nube de manera instantánea.
En este caso está bueno saber de la experiencia de la empresa Bosch Rexroth; su respuesta es no, e inmediatamente hace saber su solución proponiendo su Data Analytics Server. Su propuesta consiste en proporcionar capacidad de computación local adicional instalada en el armario de control de la máquina-herramienta para poder recopilar, almacenar y analizar datos del equipo y los procesos.
Con este paso, los datos pueden filtrarse de antemano para enviar a La Nube comprimidos solo aquellos realmente necesarios y evitar sobrecargar las líneas de datos. Resta determinar qué datos deben enviarse, cosa que puede decidir el propio usuario empleando herramientas analíticas y programas de configuración que requieren un conocimiento previo mínimo.


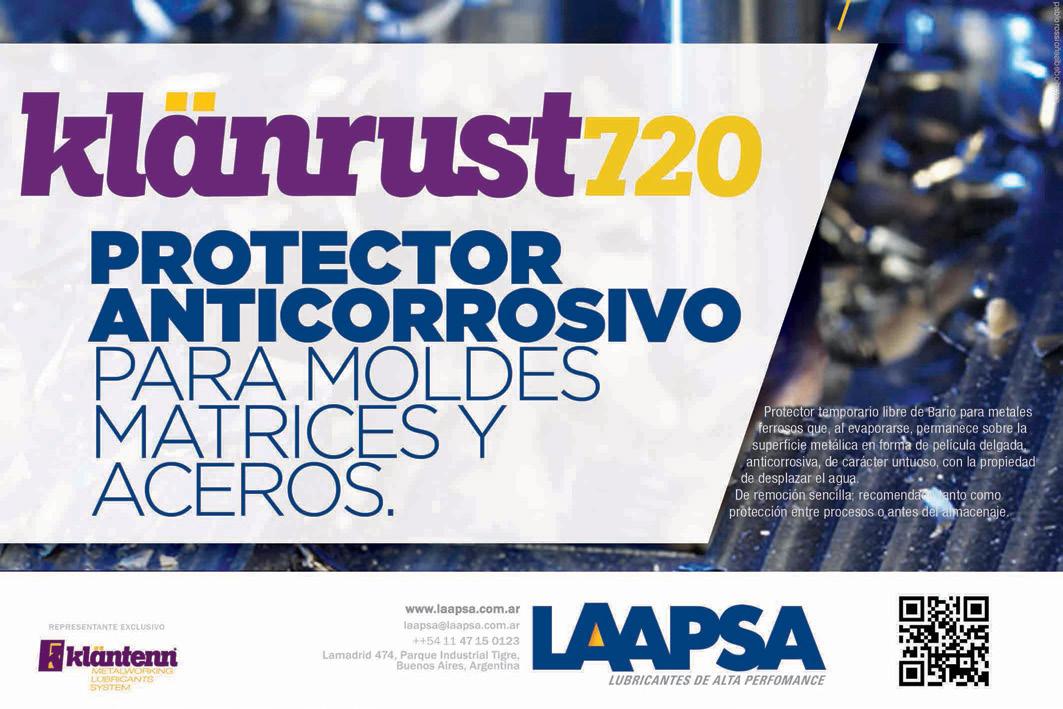
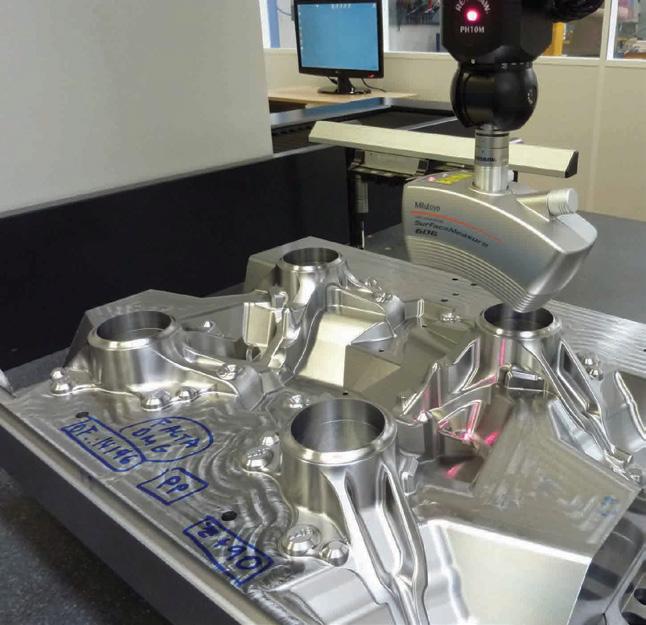
Soluciones, pero sin La Nube Por su parte, el Connected Machining, de Johannes Heidenhain GmbH, permite gestionar el entorno de trabajo digital de forma fluida: procesos transparentes, secuencias de trabajo más breves y uso eficaz de los datos. En la misma línea Heidenhain cuenta con su herramienta Remote Desktop Manager, con la que los usuarios pueden acceder a ordenadores de la red y al software que está instalado en ellos directamente con el sistema de control y con tan solo pulsar un botón.
Para comprobar el estado de las distintas máquinas integradas en la red no es necesario desplazarse; gracias al paquete de software StateMonitor basta con echar un vistazo a la pantalla y los indicadores de estado tipo RAG (rojo, amarillo y verde).
Las soluciones de Heidenhain van dirigidas a empresas pequeñas y medianas con entre diez y quince máquinas, por lo que se han concebido deliberadamente sin funcionalidad en La Nube.
Siemens AG ya había presentado hace tiempo su concepto de Internet de las cosas (IoT), plasmado en el ecosistema MindSphere: una plataforma de digitalización indicada para todos los sectores industriales. Con esta aplicación es posible digitalizar toda la
cadena de valor añadido, como se demostró con un componente de un dron moldeado por inyección.
Gracias a estos ejemplos prácticos y específicos, los fabricantes y operarios de máquina-herramienta pueden descubrir las ventajas de fusionar el entorno real y el virtual. A través de la aplicación Manage MyMachine, y desde una computadora, puede obtenerse información en tiempo real sobre el código de mecanización en ejecución y el estado operativo de máquinas distribuidas por todo el mundo. Tal grado de apertura requiere, como es lógico, soluciones para proteger adecuadamente los datos.
Identify3D es la respuesta a dicha necesidad, ya que ofrece trazabilidad de procesos digitales de fabricación para garantizar la protección de la propiedad intelectual, al tiempo que brinda acceso a datos de diseño y producción para desarrollar componentes con especificaciones técnicas precisas y en cantidad limitada. Además de sus soluciones de conectividad, Siemens cuenta con nuevas herramientas de software, como Analyze MyWorkpiece, una aplicación gráfica intuitiva que permite visualizar y analizar la trayectoria del extremo de la herramienta para editar y mostrar distintas velocidades de desplazamiento y orientaciones.
La producción conectada, en la comunidad global industrial genera trabajo asociativo, con este espíritu la Asociación Alemana de Fabricantes de Máquina-Herramienta (VDW) ha puesto en marcha una iniciativa sectorial en materia de producción conectada. Su objetivo es desarrollar y aplicar una norma para reunir un conjunto muy diverso de sistemas de control de máquinas en una interfaz común.
En la fase inicial del proyecto interviene un equipo central integrado por VDW y empresas de primera línea como DMG MORI, Emag, Grob, Heller, LiebherrVerzahntechnik, United Grinding y Trumpf.
En el marco de esta iniciativa sin precedentes de colaboración entre VDW y empresas del sector de la máquina-herramienta se desarrollarán equipos adaptados al futuro digital. El objetivo es conectar y unificar las operaciones de producción mediante la interacción segura con sistemas de procesamiento electrónico de datos (PED) y nubes.


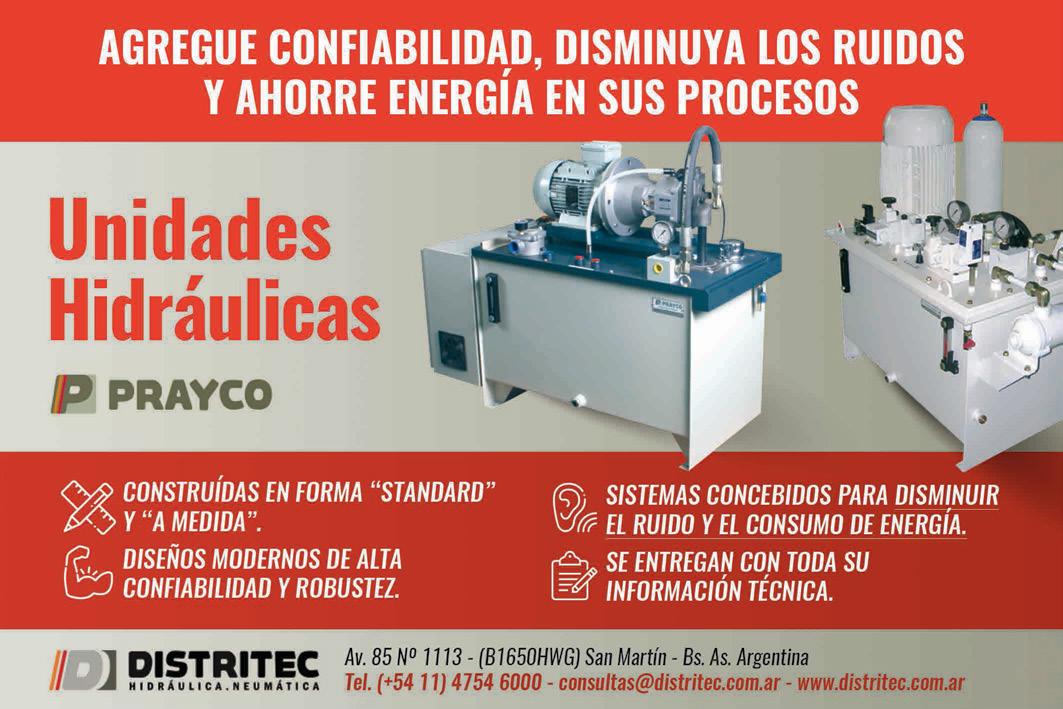