
20 minute read
PROCESSING Investment Protection and a Basis for Innovative Applications
Investment Protection and a Basis for Innovative Applications
For 30 years, the BASF Group has been using the I&C-CAE system ProDOK by Rösberg for the planning and operational support of its production plants. User acceptance in day-to-day work is high, but there is also a new demand for the inclusion of innovative applications. For this reason BASF decided to switch to the new system generation ProDOK NG. This involved a Europe-wide migration of the I&C data of about 300 plants with approximately 1.3 million loops at locations as far apart as Antwerp, Basel, Ludwigshafen, Schwarzheide and Tarragona. Without disturbing day-to-day operating processes, within two years the historically-grown, partly heterogeneous data formats were brought up to a unified international standard (eCl@ss Advanced) so as to enable analysis and the use of applications on both a plant-wide and a cross-locational basis.
Advertisement
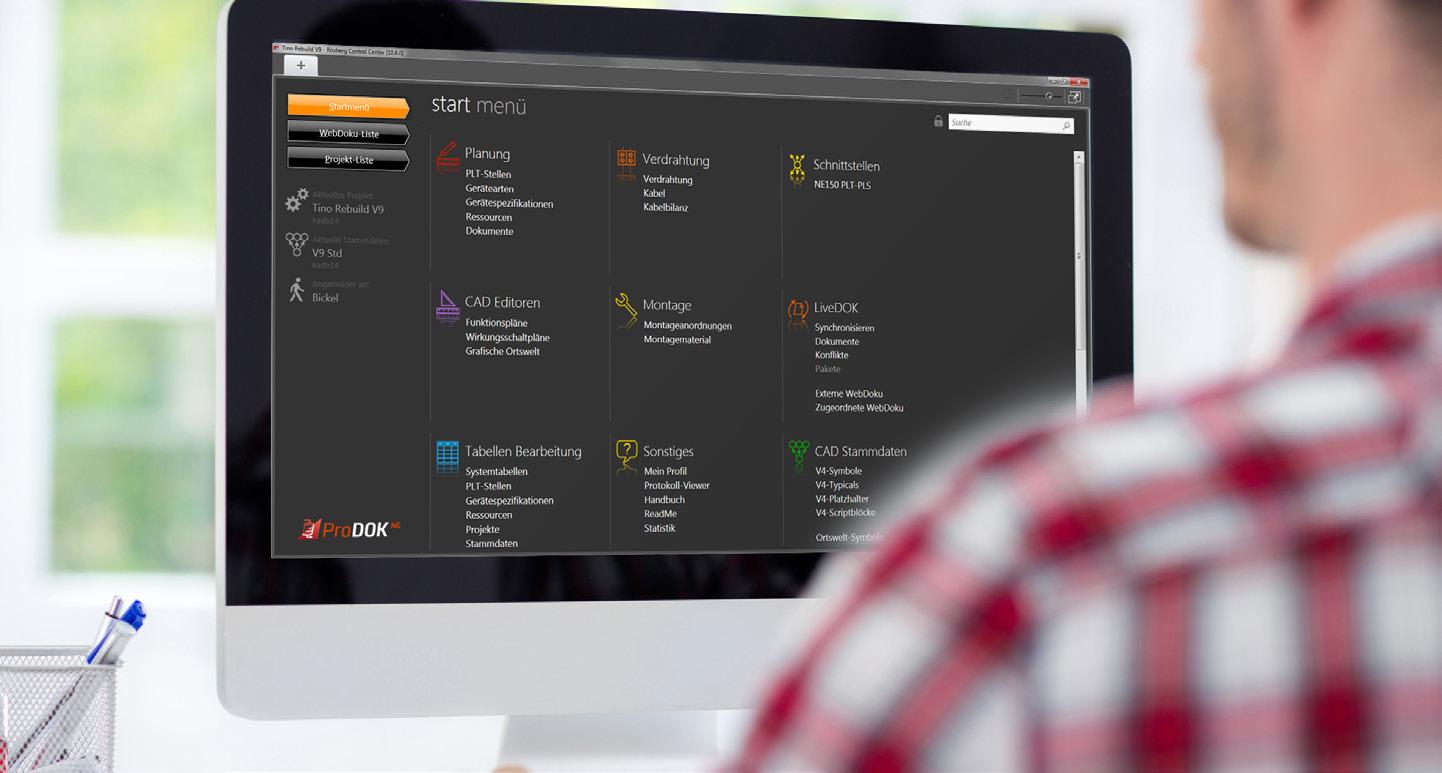
“Spring Clean” for documentation
During the switchover it was also planned to check up on the existing data. Where had unnecessary data and documents accumulated? Where were the data inconsistent? Where were there reports, forms and documents with almost identical content but differently formulated? Where were links that were now inaccurate or irrelevant? In a consulting process the experts from Rösberg gave BASF intensive support in answering these decisive questions. Thus not only did they deliver their I&C-CAE system ProDOK NG – they also supported the migration process throughout, from beginning to end. Here it proved a big advantage that Rösberg’s employees are continually planning and supporting new plants and the modernization of existing plants. They understand the planning At the BASF location of Ludwigshafen alone, around 200 plants were migrated from ProDOK to ProDOK NG (Copyright: BASF). processes represented by the software and are familiar from their own experience with the typical challenges. Before transferring database contents they were first checked for data consistency and integrity by adapted ProDOK standard tools, without changing the engineering technology. Any discrepancies were then removed semi-automatically before migration. Even without migration, this would have been a useful step in itself. locations in Europe. Over the years various different data formats were used there. In some cases, several different documentation standards were even in use at the same location. The migration was taken as an opportunity to consolidate the individual master data records throughout Europe and reduce the number of I&C device specification forms used from around 250 originally to about 60. The unified basis for these device specifications is now IEC standards, is ideally suited to describe process data and is unrivaled at present – at least in Europe. Ralph Rösberg (Fig. 5), Managing Partner of Rösberg Engineering GmbH, explains: “To my knowledge ProDOK NG is the only I&C-CAE system now on the market that comprehensively supports this future-oriented standard for the process industry. Yet in our view significant parts of Industry 4.0 can only be realized if the Standardization and future security eCl@ss Advanced. This standard, which is devices used in plants can also be consistently The migration involved all the big BASF cross-sectoral and compliant with ISO and described in a standardized way. Thus eCl@ss Advanced will be indispensable to enterprises in the medium term if they want to build and operate plants that are future-proof.” The Europe-wide reduction of the master data together with the unified use of eCl@ss Advanced provides more clarity and facilitates location-wide and cross-location comparisons and analyses for I&C planners, plant operators and production workers. Of course, the accesses by many different users in the individual plants at the various locations require basic regulations regarding data and information protection to be observed. For this purpose the BASF Group operates a central administration system for accesses to all its IT systems. Both the I&CCAE system ProDOK NG and the as-built documentation system LiveDOK NG are The I&C-CAE system supports the planning and documentation of large process plants. connected to this central system. Copyright: Rösberg).
Trouble-free I&C data migration in production plants
The migration in Europe was carried out gradually over two years. It was important not to let it interfere with operating processes, so to achieve this a unified migration plan and realistic time schedules were drawn up for all BASF’s production plants in Europe. After exhaustive testing of the whole migration process at selected pilot plants, it was implemented successively. Each weekend the data of about 20 plants at a time were transferred: to do this, at the end of the week the plant operators blocked access to the databases of the old system generation ProDOK 9.5, started the automatic checking of the database contents for consistency and integrity, performed any corrections, and stored the pre-checked data contents in a standard format. These were then made available to The use of ProDOK ensures security of investment. For decades the software has been upwardly compatible and future-safe (Copyright: Rösberg). Rösberg by remote access. Then, each Friday evening, the IT specialists loaded the data The benefits for users in production and forms in ProDOK NG it is largely irrelevant packages onto high-performance servers. There, technical units which big location within Europe employees they were automatically migrated and compared with the predefined standard format for the results, any discrepancies that occurred were analyzed and semi-automatically corrected. Additional support by BASF personnel was not required for this. On each Monday morning the migrated databases were then installed by BASF on new central database servers. The employees in production and technical units at the BASF locations, who had been trained beforehand, were able to start working with the new system straight away. Of course, Rösberg had prepared a fallback plan in case at any point the migration did not run smoothly over the weekend – but they never had to use it. The cost and effort of the migration is demonstrably worthwhile – as evidenced by the many advantages of the unified databases for the whole of Europe that were created during the migration: The new system architecture of ProDOK NG now fulfills the current requirements of BASF’s IT for a centralized server, IT installations as unified as possible and Europe-wide accesses compliant with general information protection regulations. This makes it possible to conduct analyses and integrate new applications both on both a plant-wide and a cross-locational basis. The unified datapool based on standards like eCl@ss Advanced also are assigned to – they will quickly find their way around the I&C plant documentation there. Thus personnel can be deployed more flexibly, and the same flexibility extends to contract partners, further simplifying the outsourcing of individual work steps. This also applies to all work with I&C documentation based on the web application LiveDOK. web, which can be used independently of the operating system on all the usual mobile devices on the market. Asset management also benefits from this. For the first time, information can be called up at the touch of a button about which technical components/devices are installed The external costs of Rösberg for the Europehelps avoid “uncontrolled growth” in future, in which plants throughout the whole of wide migration project were manageable. thus minimizing the necessary maintenance Europe. This is advantageous, for instance, if Expressed in terms of the individual loops in the effort in the long term. there are faults relating to a specific device, as 300 or so production plants, they worked out at approximately half a euro per loop. Thanks to the standardization of reports and well as in failure analyses and the preparation of DCS migrations. As equipment suppliers are required in future to deliver device data in eCl@ss Advanced format, these device specifications can be directly integrated into the I&C-CAE system, making the as-built documentation even better.
The switch to an I&C-CAE system is definitely worthwhile
Companies who have not yet acquired a modern I&C-CAE system can also benefit from all these advantages. In this way they can avoid the problems that crop up in everyday work again and again without an efficient I&C planning and documentation tool. In such cases inconsistent documentation, as typically produced with the use of Office tools for planning, is a standard point of criticism with audits by customers, supervisory authorities eCl@ss Advanced is an ISO- and IEC-compliant, cross-sectoral standard ideally suited and internal revision management. In the to describe the technical data of devices. It is unrivaled at present, at least in Europe worst case, if safety problems occur in the (Above). In future, suppliers plant and it needs to be demonstrated that of equipment to BASF will all relevant regulations have been observed, have to supply the data reliable documentation can be extremely for their devices in eCl@ important for an enterprise. • ss Advanced format. This Rösberg Engineering GmbH will further improve the asbuilt documentation(Right). W: www.roesberg.com, www.LiveDOK.com (Copyright: Rösberg). E: info.ka@roesberg.com T: +49 721 95018-0
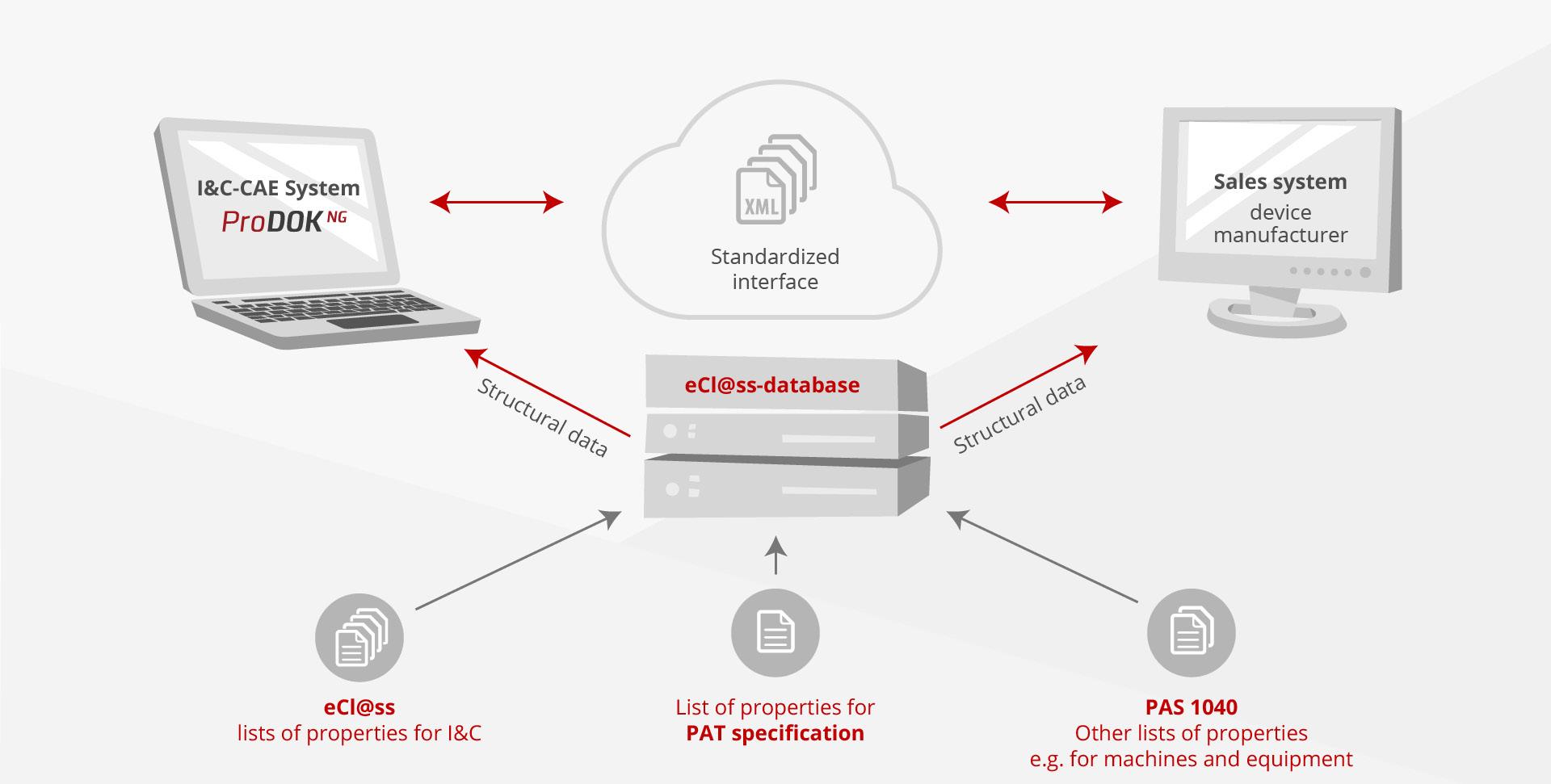
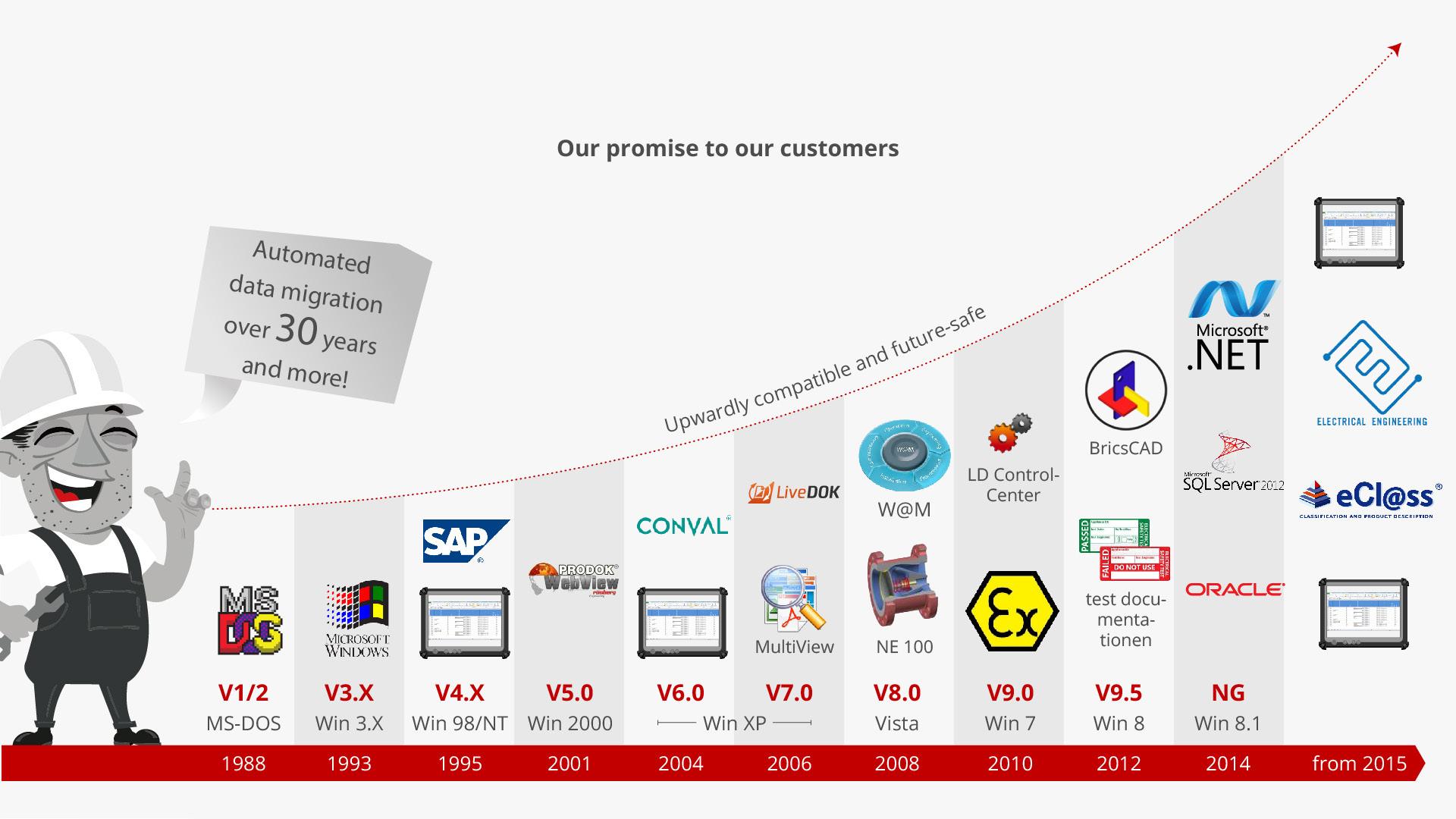
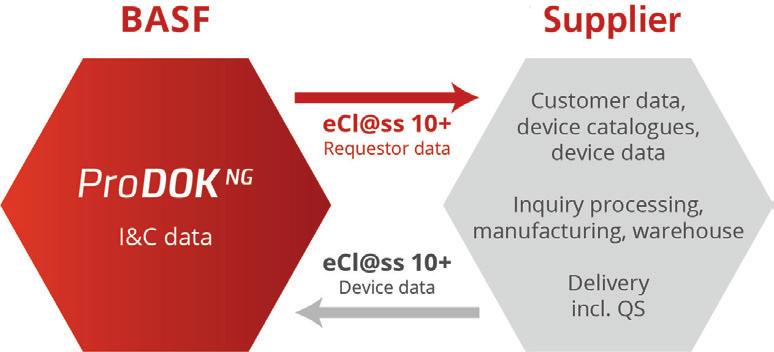
All day, every day, hundreds of thousands of analyzers around the world are measuring the dew point of water and the condensation temperature of hydrocarbons in natural gas. These values are primary indicators of the gas quality. Because gas quality is a large component in the price of the gas, measurement inaccuracies that are as small as ±0.1 °C can result in a loss of millions of Euros for one stakeholder or another. To reduce the risk of financial loss due to inaccuracies in measurements, stakeholders seek the best solutions with the most advanced technology based on the most sound measurement principles that they can find.
Once a solution is in place, it must be relied upon to operate continuously and accurately. The best way to ensure that this happens is to carry out regular preventive maintenance and calibration. This may seem an obvious truth, but theory is often not reflected in the real world. Any kind of maintenance almost always means a disruption in service and, unfortunately, all too often preventive maintenance is put off or delayed. This can occur for a variety of reasons but the end result is the same, maintenance does not take place at optimal intervals. In many, if not most instances, such a delay will not have immediate observable consequences, and this only adds to the likelihood that appropriate regular preventive maintenance may not be carried out in a timely manner. In the absence of regular maintenance, the risk of an unexpected failure increases. Should such a failure occur, it will undoubtedly result in a much greater interruption in service and cause much greater expense than would have been the case if a proper schedule of preventive maintenance had been adhered to. Regular maintenance also ensures that equipment is operating efficiently. Over time if a regular program of inspection and repair is not followed, reductions in efficiency can result in increased operating expenses
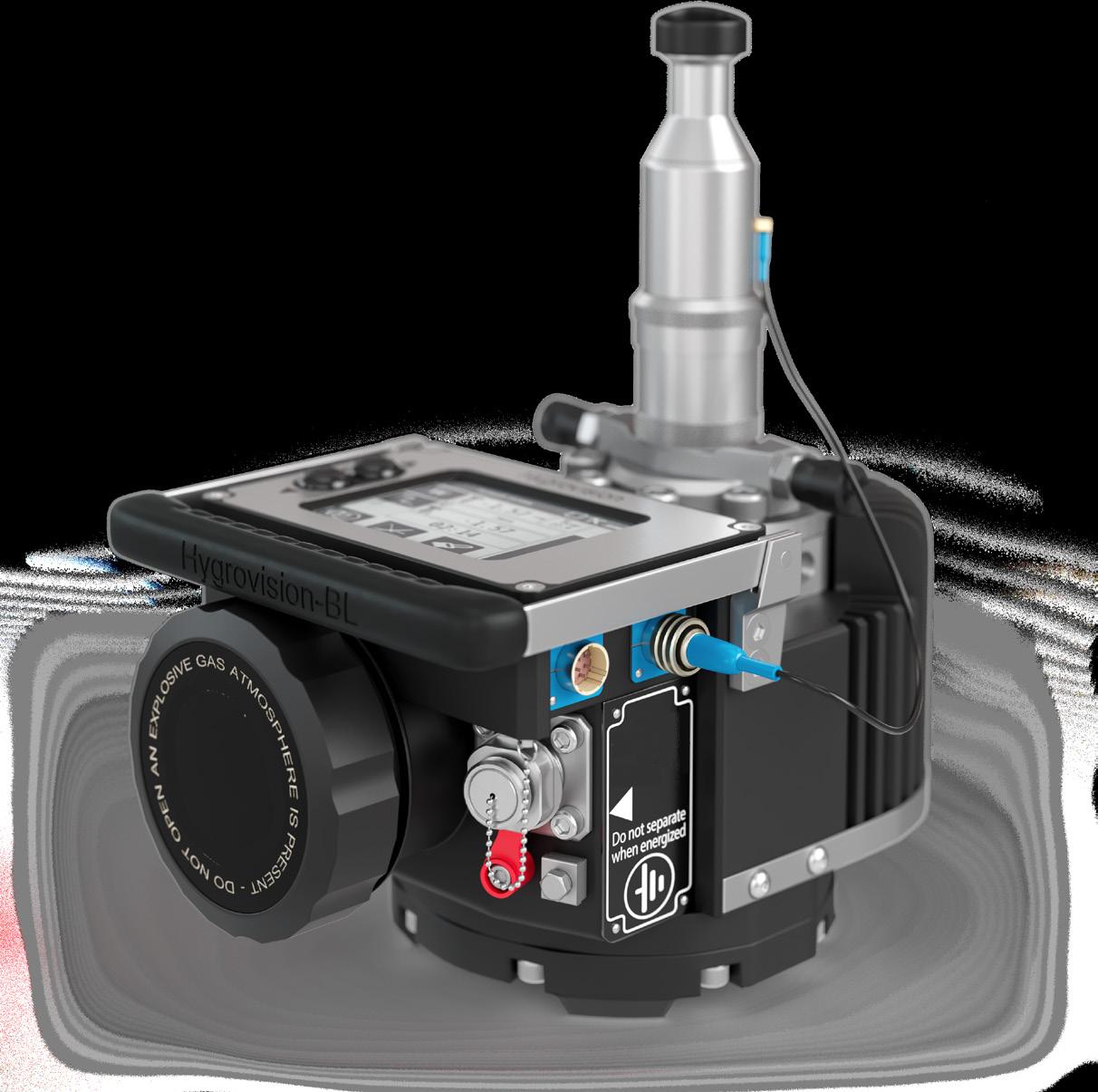
CONG Prima 2M online automatic chilled-mirror dew point analyzer.
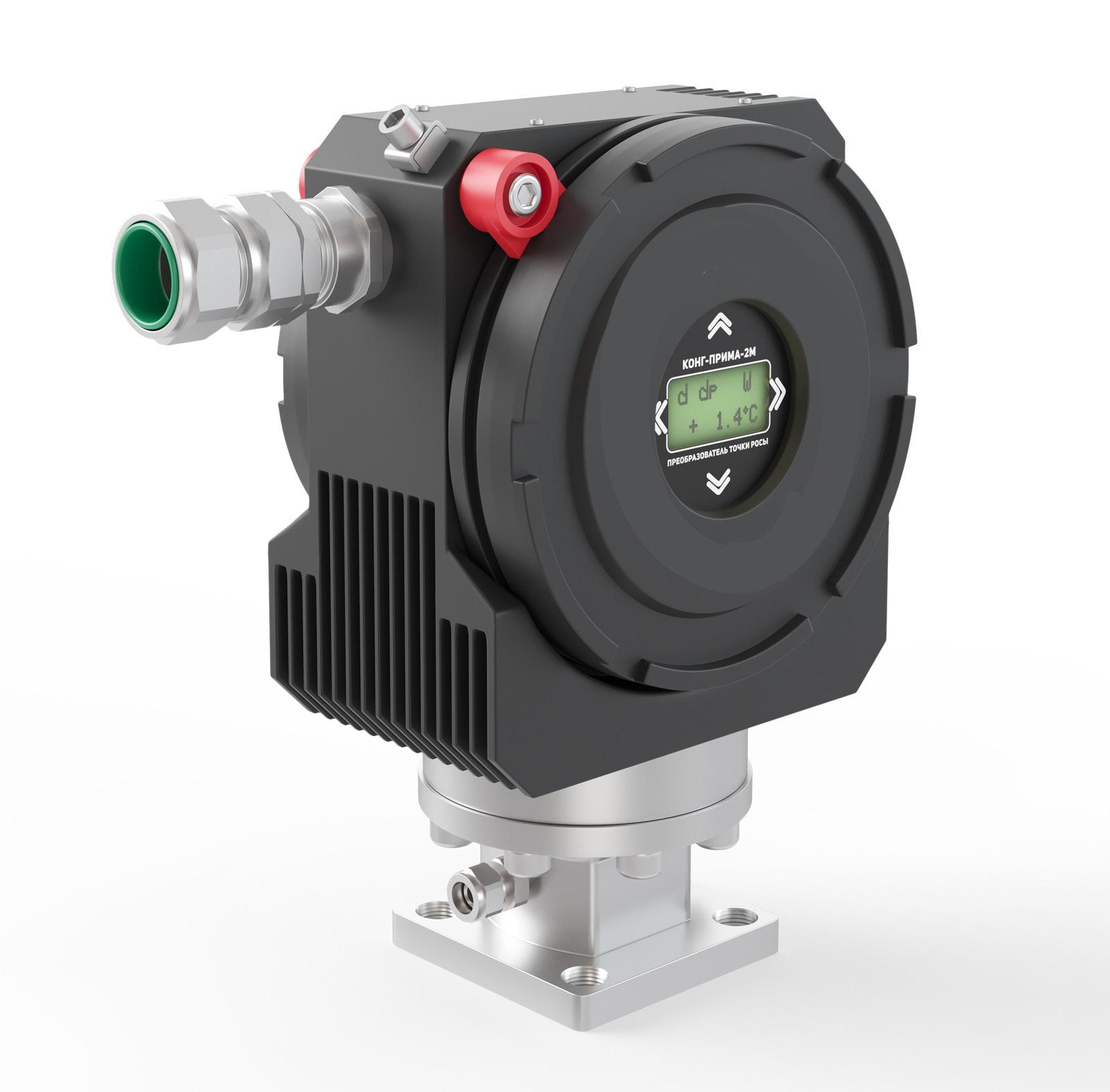
and significant losses due to measurement inaccuracies - as mentioned at the beginning of this article! One way to help owners and operators to avoid unexpected failures and losses due to inefficiency is for equipment suppliers to offer services designed to help ensure that regular maintenance is carried out. The Vympel company, a leading supplier of advanced quality control instruments, offers just such a service, known as VympelCare. Beyond regular preventive maintenance, instrumentation used in quality control measurement must be regularly calibrated and verified, to ensure that the reported measurement results are accurate. Continuous use of these devices necessitates that they be calibrated and verified on a regular basis, and this service is also provided for by VympelCare. As is the case with preventive maintenance, delays in calibration and verification can occur for a number of reasons. As long as the information being reported by the instrument seems to be in line with what is expected, and
Hygrovision mini and mini SL semi-automated manual chilled-mirror dew point analyzer.
the device seems to be operating normally, it is easy to understand why taking a unit off line to have this confirmed may seem like a low priority. In some cases, it may even seem unnecessary and nothing more than an added expense. The issue here, of course, is that these devices are in place to measure actual conditions, not merely to confirm what is expected. If an instrument’s calibration is no longer within tolerance limits, what looks like a confirmation of expected results could really be a misrepresentation of conditions that are outside of acceptable limits. This can result in costly negative consequences. As is the case with preventive maintenance, the best way to ensure the accuracy of the calibration is to adhere to a regular calibration and verification schedule. VympelCare is designed to address both of these aspects of equipment operation: preventive maintenance and calibration / verification – tasks that should be carried out on a regularly scheduled basis even when there does not appear to be an immediate need. In the best case, these two activities would be done at the same time, minimizing the downtime of the instrument involved and ensuring the device, when calibrated, is in optimal condition. This approach ensures the least interruption in service. In fact, this is a pretty to processing and transportation. critical analyzers online and operating good description of VympelCare: a program that provides regular maintenance as well as the best calibration / verification of Vympel instruments. Measurement of the water dew point is a way of directly measuring the moisture content in natural gas as well as establishing the with as little interruption as possible, while ensuring that they provide not only accurate information, but also the “best” information. More specifically, VympelCare is a regularly temperature at which water will condense out Upon arrival at Vympel GmbH in Germany, scheduled service provided by Vympel GmbH of the gaseous phase to form liquid droplets maintenance service is provided by Vympel and OGE, designed to make it easy for the in the gas stream. Moisture content is an technicians, helping to ensure that once they owners and operators of Vympel instruments important indicator of gas quality. Gas that is are returned to their owners, the analyzers to follow through on carrying out regular too wet can result in the formation of clathrate will operate well without interruption. preventive maintenance and calibration. hydrates in the pipeline, which can obstruct VympelCare service includes comprehensive Three times a year, Vympel sets aside a week the gas flow and may lead to catastrophic inspection of the analyzer, cleaning of the to provide VympelCare at its facilities in accidents. An accurate measurement of the measurement chamber, updating the software Düsseldorf, Germany. Customers that intend to water dew point is critical to ensuring the if a new version has been released, making any take advantage of this service simply register in quality of the gas and protecting the pipeline minor adjustments to optimize performance, advance that they wish to reserve one of the slots and other equipment. and preparing the analyzer for calibration. available for an upcoming VympelCare session. The instruments are then sent to Vympel on the appointed date. Active promotion of VympelCare is intended to remind the owners of Vympel instruments of the importance of regular preventive maintenance and calibration, while offering an easy and economical way to carry out these tasks. By optimizing the logistics involved, a device is usually sent back to its owner in a week to ten days, ready to go back into service. Similarly, measurement of the hydrocarbon condensation temperature provides information about the temperature at which hydrocarbons will begin to precipitate out of the gaseous phase, forming hydrocarbon liquids. The presence of these condensates in the gas flow can cause significant damage to equipment such as gas fired turbines. In addition, accurate measurement of the gas flow requires that it remain in a single phase (gaseous). As is the case with liquid water, Then these units are sent to the Open Grid Europe (OGE) lab in Essen, Germany for calibration / verification. Calibration at OGE ensures that the analyzers will provide the best information. To explain what is meant by the term “best information” it is necessary to understand that when it comes to chilled-mirror analyzers, all calibrations are not created equally. The Open Grid Europe (OGE) lab in Essen developed a method for the harmonized calibration The devices covered by VympelCare are hydrocarbon liquids in a natural gas pipeline of automatic hydrocarbon condensation Vympel’s state-of-the art chilled-mirror can cause a number of problems, so knowing temperature analyzers with different levels of hygrometers of the CONG Prima, FAS, the temperature above which the gas must be sensitivity, for the GERG Project 1.64. This and Hygrovision series. These instruments maintained is essential information. method establishes 5mg/m3 of hydrocarbon incorporate cutting-edge technology to measure the water dew point (WDP) and hydrocarbon condensation temperature (HCT) in natural gas. These analyzers can all measure both the water dew point and the hydrocarbon condensation temperature. This type of instrument is an important quality control device that is used for a number of applications at many points along Apart from the operational imperatives, these two measurements are also important for contractual and regulatory reasons. Failure to conform to specified water dew point and hydrocarbon condensation temperature values can result in fines, fees, or other financial penalties. condensate as the threshold for reporting the condensation temperature. In other words, the temperature at which 5mg/m3 of hydrocarbon liquids have condensed onto the chilled mirror’s surface is considered to be the hydrocarbon condensation temperature. Measurements taken by an analyzer calibrated to this standard will be much less the natural gas delivery chain, from production VympelCare is intended to help keep these influenced by changes in gas composition,
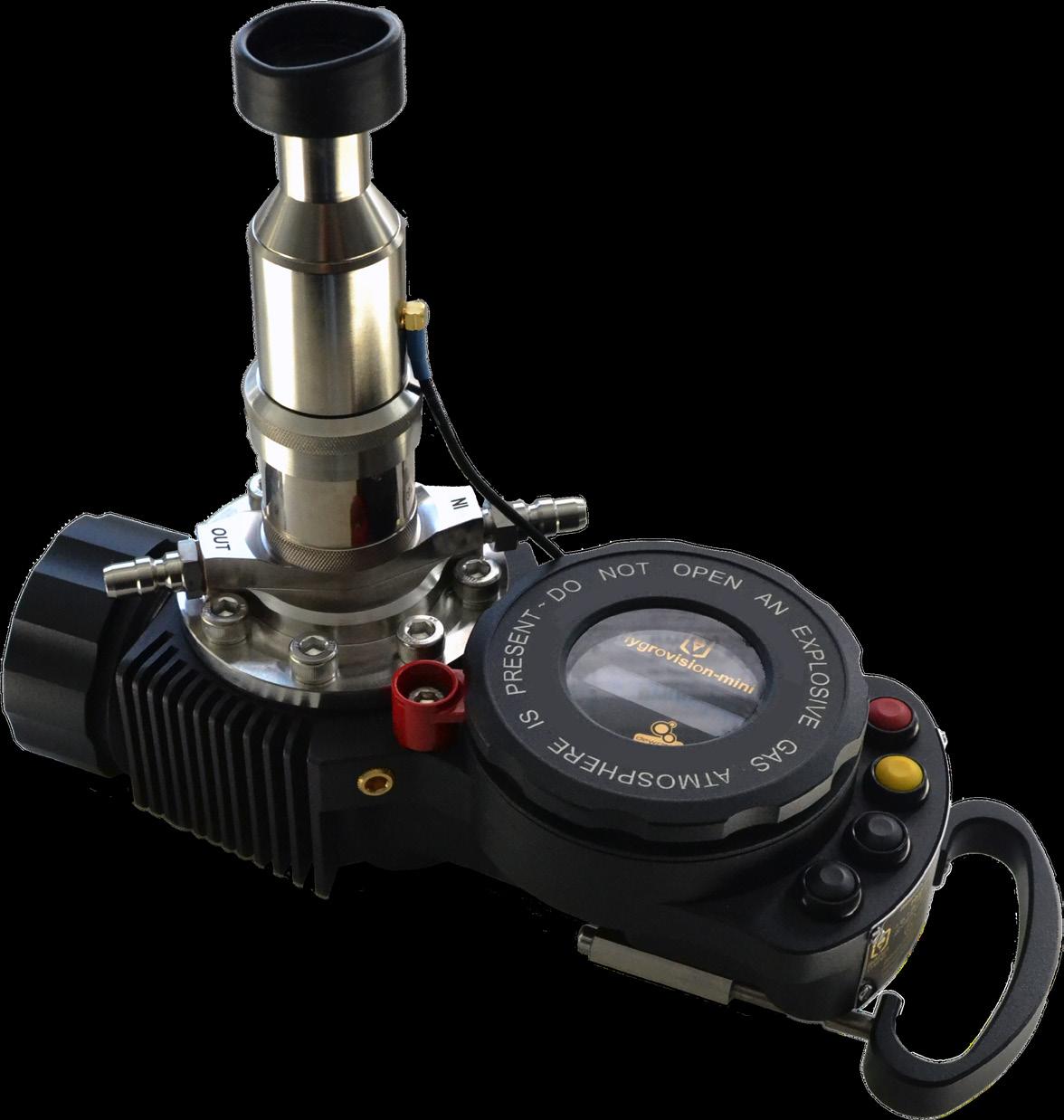
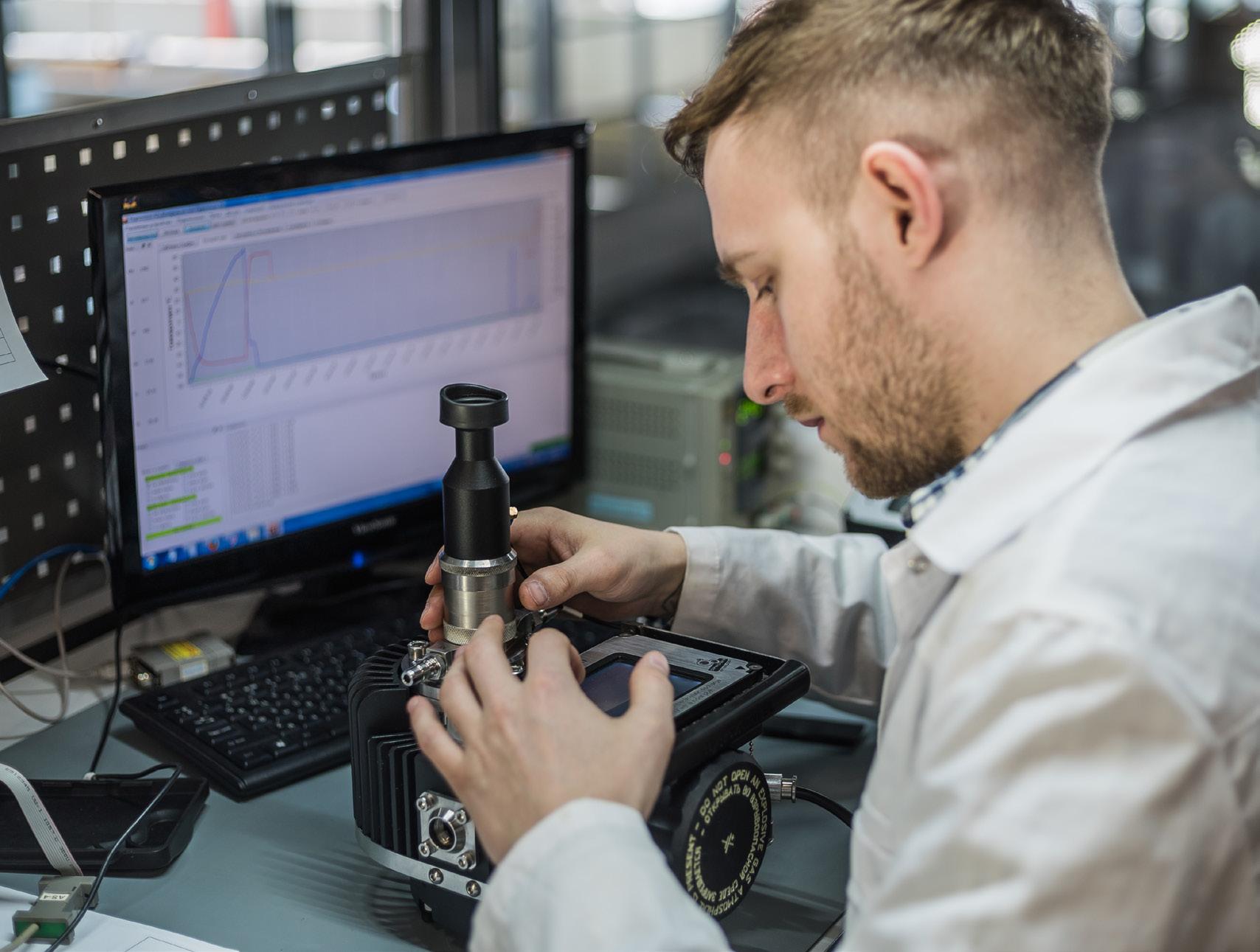
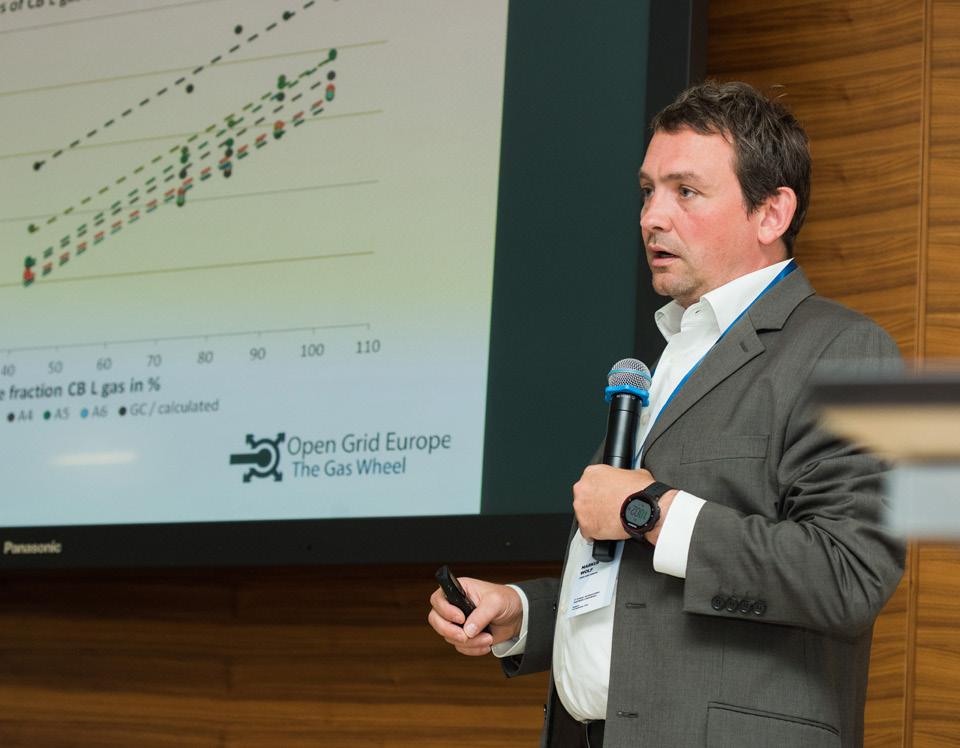
Vympel engineer using computer-based diagnostics as part of VympelCare service for a Hygrovision BL portable dew point analyzer.
for example, and will be more comparable to measurements taken by other instruments. In addition, the calibration gas used by OGE is a representative multicomponent gas essentially similar to pipeline natural gas. As a result, the calibration is made using gas that behaves essentially similar to the way pipeline gas behaves, by slowly building up a layer of condensation. It is this condensation behavior that makes it possible to establish the 5mg/m3 threshold. This is opposed to a single component calibration gas, such as propane, which is often used to calibrate this type of instrument. Propane has a very different condensation behavior that results in so much condensate forming at once that it is not possible to limit the condensation to 5mg/m3. Because of this, it is not possible to discern the beginning of condensation. In other words, calibrating to 5mg/m3 ensures that the analyzer is set to the level of “best” evidence for registering the start of condensation. It is worth noting that ONLY Vympel instruments are sensitive enough to actually resolve 5mg/m3. Competitor devices can only discern a film that corresponds to 40mg/m3 or more, measurement channel is also not as condensation in hydrocarbon gas mixtures. depending on the instrument. This lack of straightforward as one might expect. Water GERG also realized that it was necessary to sensitivity represents a level of uncertainty vapor in a hydrocarbon matrix, such as build a comprehensive and accurate database that will not ensure the required degree of natural gas, does not behave in quite the same relating measured water content to water dew measurement accuracy. For these devices, the way that it does in regular air. point values for a variety of representative GERG calibration requires the incorporation of a correction factor, adding to measurement uncertainty. Vympel instruments are not subject to this uncertainty! The calibration for the water dew point In 1995, the GERG group carried out a project for developing a mathematical correlation between the water content and water dew point in natural gas in order to more accurately define the behavior of water natural gases. It was shown that there was a need to improve the existing correlation values. As a result, a more accurate, compositiondependent correlation was developed on the basis of GERG’s database. This research is the basis for the current ISO standard 18453:2004 “Natural gas — Correlation between water content and water dew point” which also incorporates. And it is this standard that OGE uses when calibrating the water dew point channel for VympelCare units. After calibration VympelCare analyzers are returned to the Vympel facility in Düsseldorf for a final check before being returned to their owners. The whole procedure usually is completed within seven to ten days, and the analyzer that is returned to service can be relied upon to operate well for another 12 months at least. From the beginning VympelCare was developed in response to three basic needs: to provide timely prevent maintenance to Vympel analyzers; to provide those analyzers with the best calibration; and to make it easy and economical for owners to take advantage of these services. The ultimate goal of VympelCare is to ensure that Vympel instruments in the field provide accurate quality control information for the entire service life of the instrument. • If you would like to know more about the solutions discussed in this article please contact:
SPA Vympel
Dr. Markus Wolf, Head of the Gas Quality Department at OGE delivering a presentation +49 211 21077391 about calibration of dew point analyzers according to the GERG* project 1.64. info@npovympel.ru * Groupe Européen de Recherches Gazières (European Gas Research Group).
Granzow A/S has for decades supplied compressed air for drilling rigs and ships where security, economy and stability is a priority.


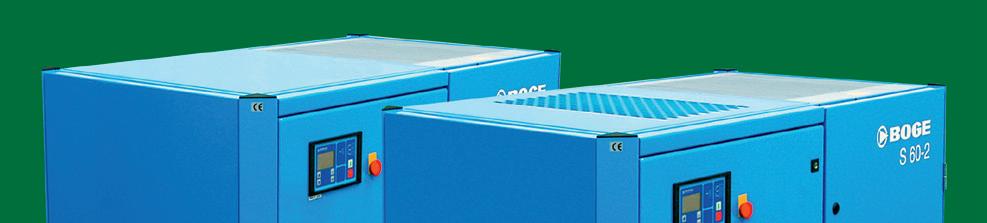
Air-operated diaphragm pumps, wide range of materials permits rating of the pumps to meet individual requirements and matching to the media which must be conveyed.
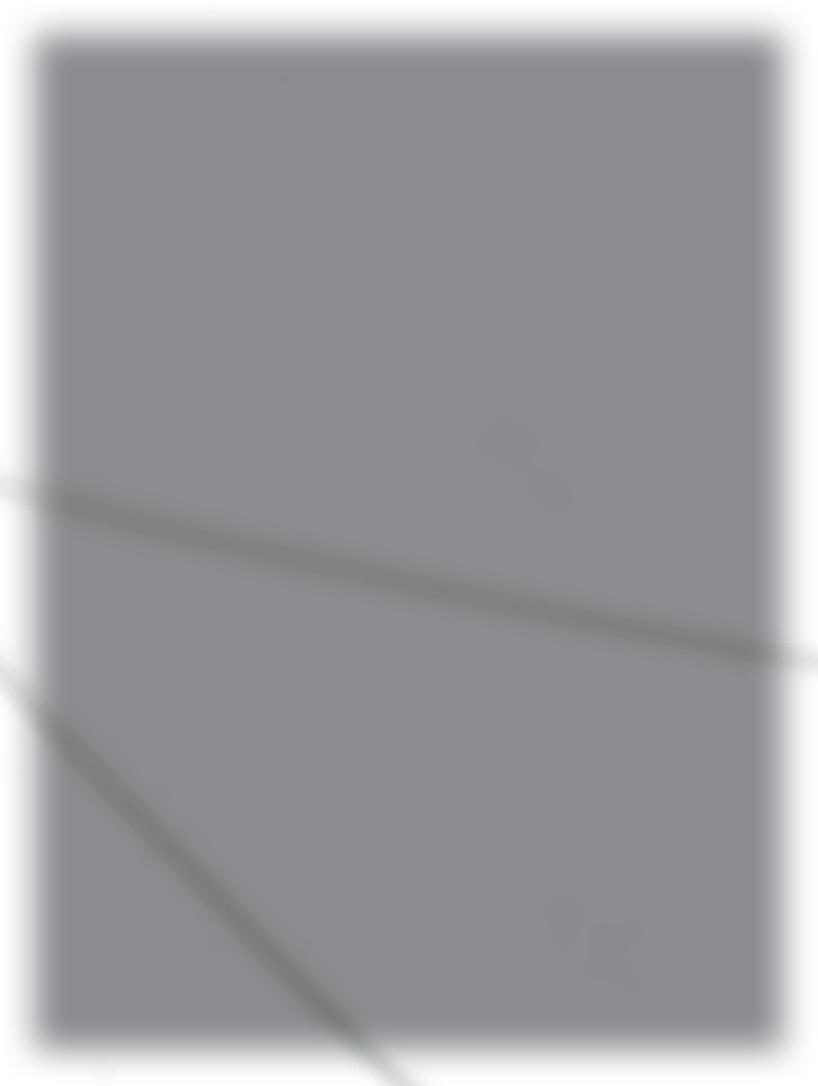
High efficiency, and suitable for many ATEX requirements for use in potentially explosive and hazardous applications.

Bursting Panels for the protection of personnel and equipment by dust explosions. The panels are manufactured individual applications. Pressure from 0.017 bar to 0.35 bar. All materials and certificates.
Who are we? Granzow A/S is a leading supplier for the industry of screw compressors. We also produce a complete range of solutions in automation products, such as bursting discs and panels,valves and pneumatic cylinders. Additional Granzow has an extensive program of pumps and a complete line of vacuum pumps.
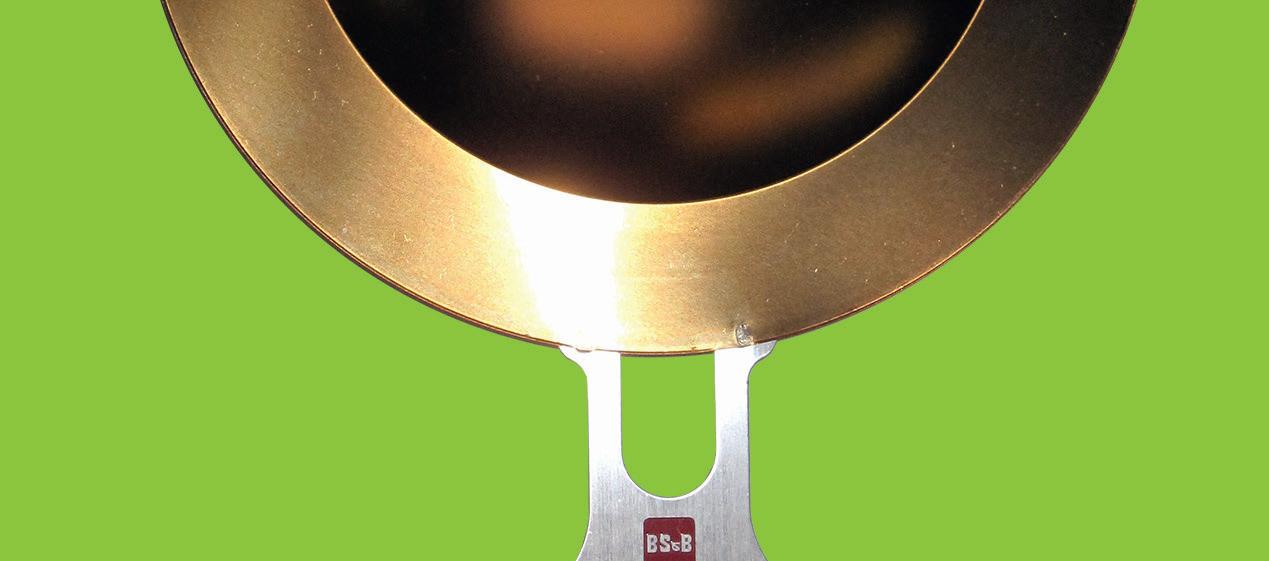
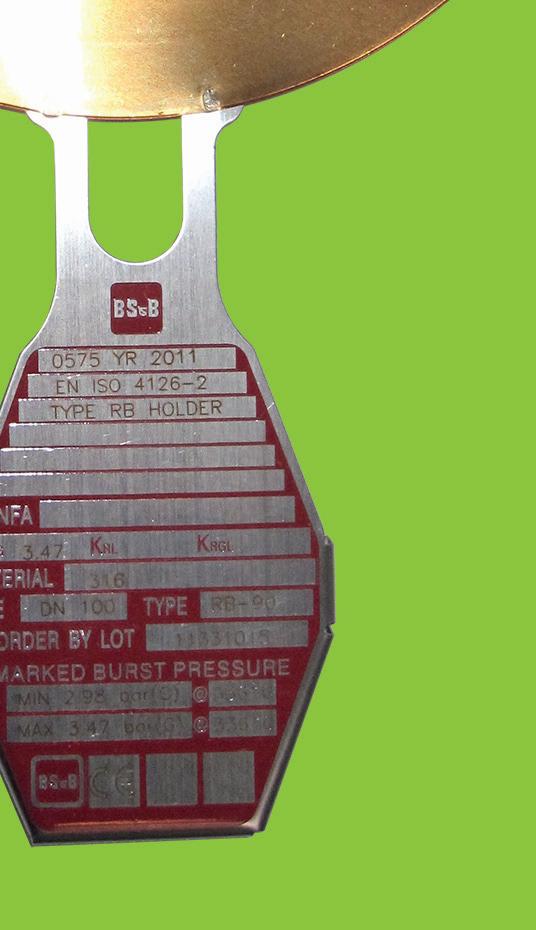
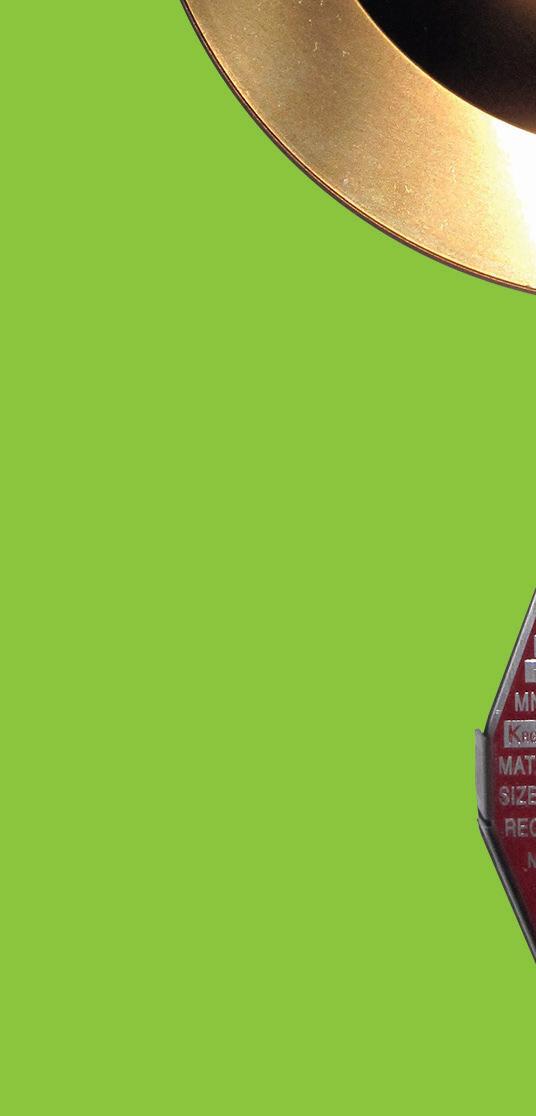
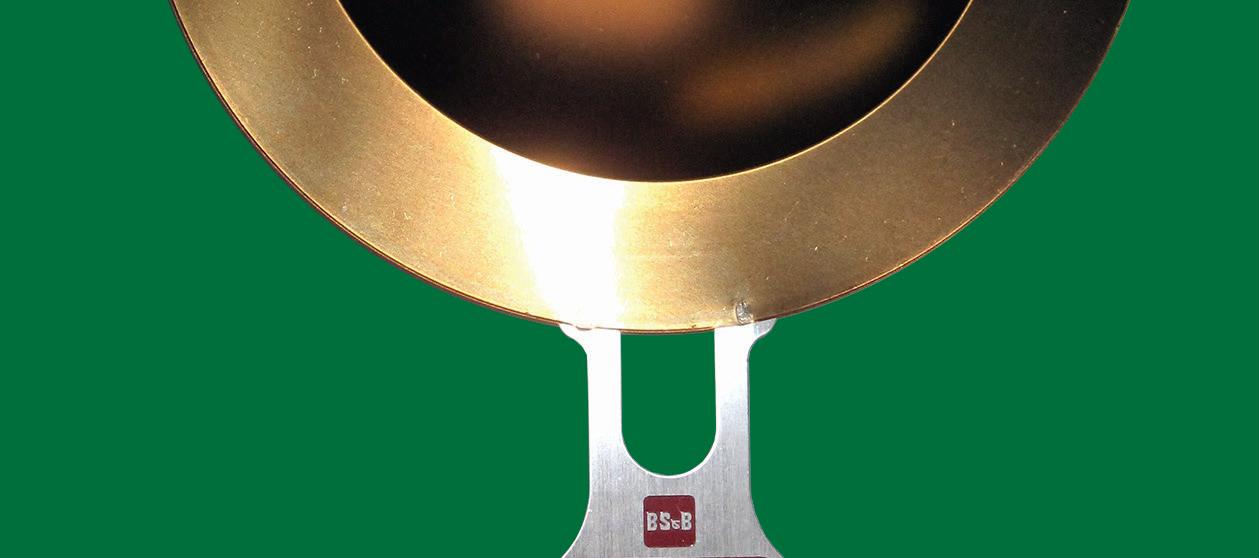
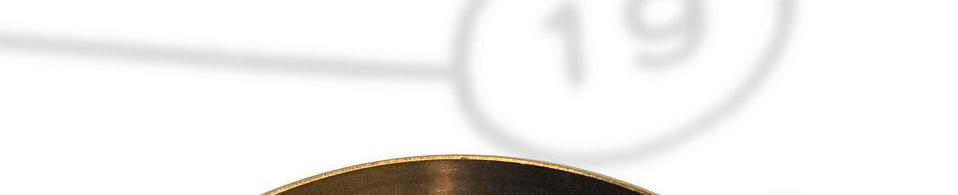

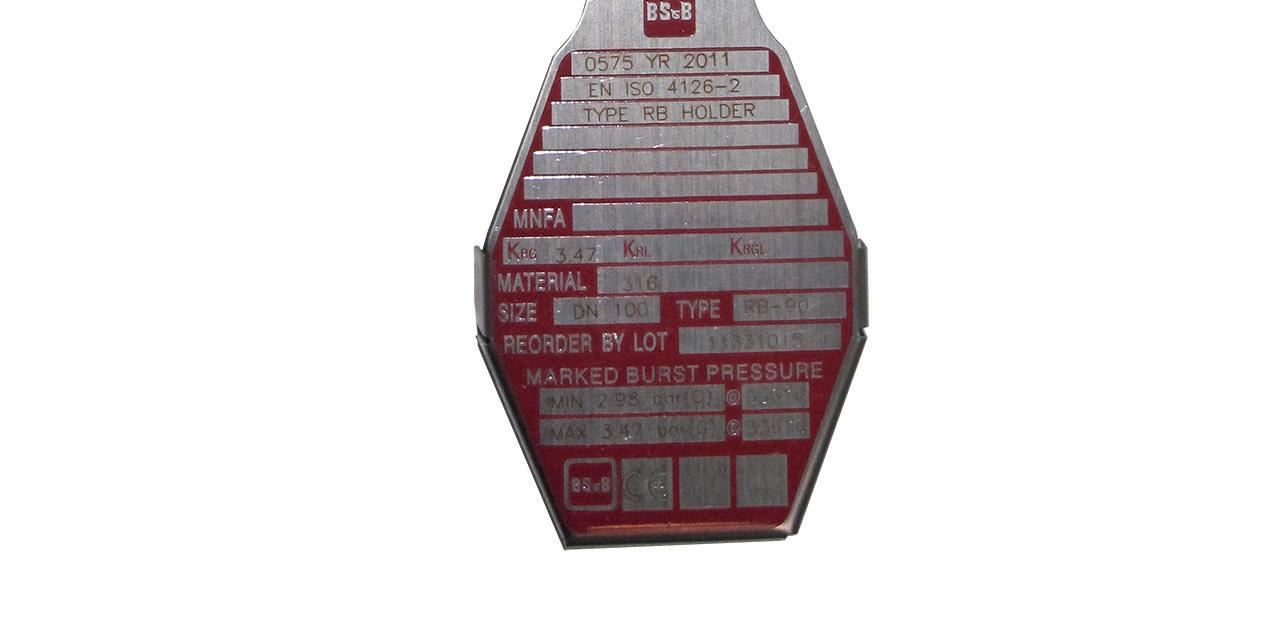
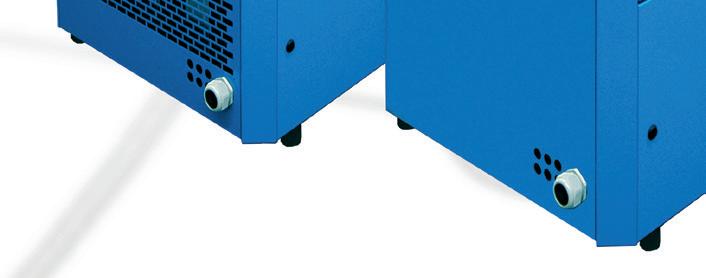
Instrument Air Compressor & Dryer Package for the Offshore Industry in accordance with for the Offshore Industry in accordance with both Atex regulations, Zone II and Zone I both Atex regulations, Zone II and Zone I
Ejby Industrivej 26 · 2600 Glostrup · T: • Helge Nielsens Allé 6C · 8723 Løsning info@granzow.dk • www.granzow.dk • www.trykluft .nu