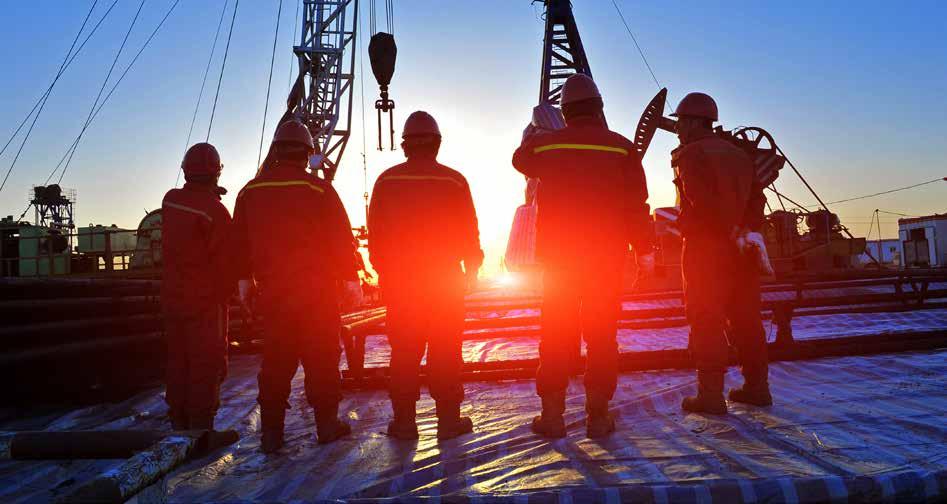
7 minute read
MAKING THE MOST OF OPERATIONAL COST EFFICIENCY STRATEGIES
BY RANA AL KADY While an operational cost efficiency strategy is a notion that has been implemented in various companies in the oil and gas sector. So far, conventional operational cost efficiency strategies have been implemented in Egypt (especially when discussing increased drilling costs), but given the recent impact of the global pandemic (i.e. COVID-19), more detailed and developed strategies are necessary to limit the overall impact.
Advertisement
OPERATIONAL COST EFFICIENCY CONCEPT To begin with, it is important to make note of the fact that operational cost efficiency does not only mean that costs of operations are controlled in the most effective way, but it also means that this must be done while delivering products or services at optimal quality. There are four main components that constitute the concept of operational cost efficiency; these components include: resource utilization, production, distribution, and inventory management. Mahmoud Shawkat, Managing Director at Red Sea International Petroleum Services, has said that “Operational cost efficiency is not something new to the oil & gas industry as it’s a ‘dayto-day’ field practice that all operators are applying in different ways. Egypt is following multiple of good solutions by looking thoroughly at elements that can make investment sense such as gas to power, sharing resources between operators ‘Pipe line and processing stations’, and so on.” For example, resource utilization refers to making the most out of your employees and/or your equipment based on whether a service or final product are being delivered. This means that employees and equipment are used at optimal capacity to attain the maximum profit. In terms of production, manufacturing equipment are maintained and operated to have the best possible efficiencies to enhance output. Additionally, distribution refers to the ways in which products, either tangible or software-based, are delivered through the quickest and most reliable means. Finally, and most importantly, inventory management refers to the ways in which products are either sold or stored. More specifically, in some companies, just enough products are manufactured to meet instant demand of the product, because storing finished goods costs money. However, ideally, there must be middle ground between producing just enough to sell (i.e. under producing)and overproducing to end up with a large number of unsold goods. These are the components that make up the overall concept of operational cost efficiency.
THE IMPORTANCE OF OPERATIONAL COST EFFICIENCY Consequently, it is important to note that this concept is forced unto companies only when situations become critical. However, this concept should be implemented and developed constantly to prevent or reduce as much losses as possible – both technically and financially. This means that operational cost efficiency measures should be taken regardless of the company’s financial well-being or the existence of an international emergency (i.e. a pandemic). Unfortunately, most operational cost efficiency measures are only taken into account when going through difficult times as opposed to implementing such strategies as a form of preventative measures. There are many advantages to implementing operational cost efficiency measures. For example, increased profits, enhanced customer satisfaction and improved overall quality of work are all examples of the importance of such measures.
OPERATIONAL COST EFFICIENCY STRATEGIES There are several operational cost efficiency strategies that have been deemed most effective. Most strategies are often viewed as economical as companies can benefit from their usage, especially considering the effect of recent drops in oil prices. One example of an effective operational cost efficiency strategy is the understanding of the fine line between increasing production and profitable outputs. This means that it is essential for companies to recognize whether it is worth increasing production if there is a possibility that the final output would not be as profitable as producing less. This strategy ensures that the company implements economically feasible solutions based on end-use products. Another example of a valuable operational cost efficiency strategies involves figuring outthe best ways to enhance baseline production. This means figuring out ways in which more resources could be acquired at low-costs or, simply, deciding to aim for the ‘low-hanging fruit’. In the oil and gas sector, this means managing the oilfield to ensure that all the resources from already-existing wells or establishments are dried out before moving along to a new potential site. Nevertheless, a strategy that always seems to work regardless of the company’s output is the application of contracting models that involve the relationship between the operators and suppliers. While suppliers gain from longterm partnerships as well as the low cost associated with being able to tender regularly for a similar scope of work, operators benefit from working on similar operations as it provides them with a sense of consistency in their work (i.e. the errors that occur are the same and become easily fixable and familiar with time). This type of contract could range anywhere between 5-8 years. These types of contracts are encouraged as it provides both companies with consistency and experience as they both work together on projects with the same exact scope over long periods of time. Shawkat has also mentioned that, “One other element that still needs to be optimized in such away that operators save time and the environment. Produced water that is a result of separation is one element that disables production sometimes if not properly handled”. Shawkat also noted that “production waste water is either re-injected to wells to improve reservoir pressure if planned properly using sweep efficiency models or transported to plants for further treatment and rolled to industrial waste lines or sewage after approval from authorities. This waste water can be disastrous to environment if dumped in the desert which results in polluting the underground fresh water that can be used in future plantation.”
CASE STUDY In fact, one of the most successful partnerships was that between WorleyParsons and Shell, which had created a trend in the industry for others to follow. The contract was signed for a period of 5-years with an option available for renewal. The main reason for implementing this operational cost efficiency strategy was to be able to work on the same project-type and, over time, increase efficiency in the same work being produced. This is otherwise referred to as the ‘cookie-cutter’ model; this is in reference to optimizing the operational efficiency with similar work being done each time. This strategy is cost-effective and time-efficient as the same approach methodology is applied time and time again. In doing so, there are no surprises or errors that have not been dealt with before.
FUTURE IMPROVEMENT In conclusion, even though the oil and gas sector typically carries out conventional operational cost efficiency mechanisms, new advances in application strategies could enhance expenditures and performance in the long-run. While some believe that the real efficiency measures lie in the investment in innovative technologies and experienced talent, the truth is that the combination of such measures with effective operational cost efficiency mechanisms could be the key to uncapping potential opportunities and enhancing work flow within an organization. A key opportunity to enhance operational cost efficiency is that“firm rules to waste production water should be in place and penalties to those who miss with it should be applied to save environment and better have operational excellence”, Shawkat added. It is important to understand that the implementation of operational cost efficiency strategies should be considered to be a preventative measure rather than a forced measure. Also, if implemented consistently, any emergency situations or downfalls that may occur would be limited, if not, entirely controlled through the implementation of such efficient measures.
SUPPORTED BY SUPPORTED BY
á ` ` ` ` « f ó © Ÿ G I h ô ` ` ` ã d G h ∫ h ô ` ` à Ñ d G I Q G R h
M i n i s t r y o f P e t r o l e u m & M i n e r a l R e s o u r c e s
9-11 FEBRUARY 2021 | EGYPT INTERNATIONAL EXHIBITION CENTER
SHARE YOUR KNOWLEDGE AND EXPERTISE AT THE REGION’S LARGEST TECHNICAL OIL AND GAS CONFERENCE SUBMISSIONS DEADLINE: THURSDAY 25 JUNE 2020

17
Technical Categories
Upstream: Exploration of Conventional Resources (CONV) Upstream: Exploration of
Unconventional Resources (UNCONV)
Geoscience: Upstream Technology Developments (GEOT) Oil and Gas Field Development (FD) Drilling (DR)
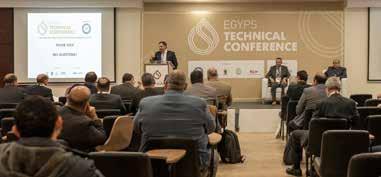
WHY SHOULD YOU SUBMIT ABSTRACTS?
Share your experiences of successfully managed projects
Present your technical knowledge and skills
Showcase best practices and operational excellence
Introduce your research findings that will revolutionise the industry
SUPPORTED BY
Completions (COMPL) Gas/LNG Processing, Transportation, Operations and Technology (GAS) Offshore and Marine
Technology and Operations (MAR)
Oil and Gas Economics, Concession Agreements and Project Finance (FIN) Project Management and
Execution (PM) Operational Excellence (OpEx)
Health, Safety and Environment (HSE) Downstream: Refining Technology, Operations and Marketing (REF) Downstream: Petrochemicals Technology and Operations (PET)
Biofuels, Alternative Fuels and Renewable
Energy (BIO) Digitalisation of Oil and Gas (DIGI) People and Talent Development (PPL)
SUBMIT TECHNICAL ABSTRACTS WWW.EGYPS.COM/CFP
OFFICIAL MEDIA PARTNERS ORGANISED BY