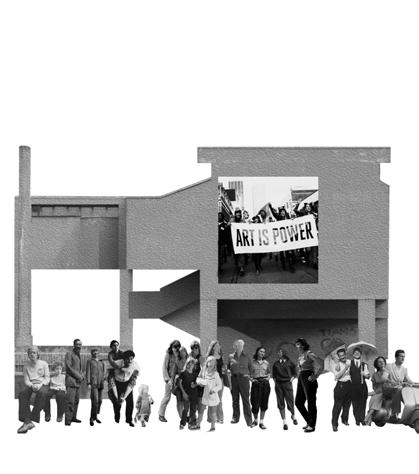
7 minute read
TIMELINE + OCCUPATION
PHASE 1: PLANNING PHASE 2: RENOVATION
May 2023
Advertisement
March 2024
PHASE 3: BUILDING
January 2025
PHASE 4: USE AND CONVERSION FUTURE REUSE???
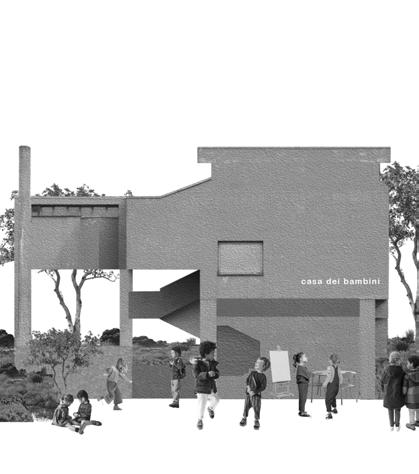

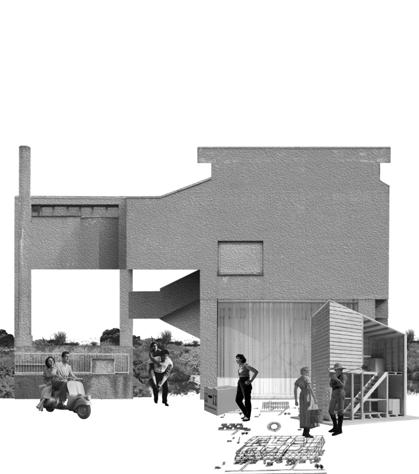
2026 - ??
20??
Living Situation:
Residents are camping within the building, initially without water/ electricity
Site office and communal kitchen is established at the ground floor. The ground floor bathrooms are used in the meantime.
Living Situation:
Once the insulative boxes are built the residents can move into these spaces to continue the works, initially without dividing walls.
The communal kitchen and bathroom continue to operate. The meeting space is constructed in polycarbonate, a garden kitchen is established to feed the residents, rainwater is harvested for irrigation of the garden and in construction work.
Living Situation:
Once the insulative boxes are built the residents can move into these spaces to continue the works, initially without dividing walls.
The communal kitchen and bathroom continue to operate. The meeting space is constructed in polycarbonate, a garden kitchen is established to feed the residents, rainwater is harvested for irrigation of the garden and in construction work.
Living Situation:
Residents continue to live within the units, most residents remain, some residents may move on move on or move into larger units within the school.
New residents move in and communal spaces are utilised by all. Communal activities continue in the maintenance of the garden space and restoration and maintenance works needed for the building.
(NON) Living Situation:
Residents move out of the building and the school is no longer used for private living. Having been restored and conserved over the years by maintenance works and continued occupation the building is in good condition to be repurposed by the municipality.
The ramp remains as a visible landmark to recent intervention and the insulated boxes remain so the spaces are still habitable
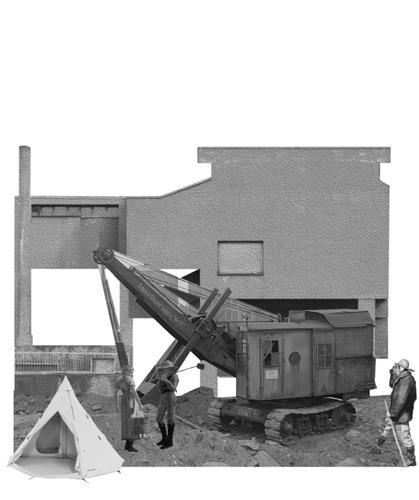
GROUND FLOOR 1:20
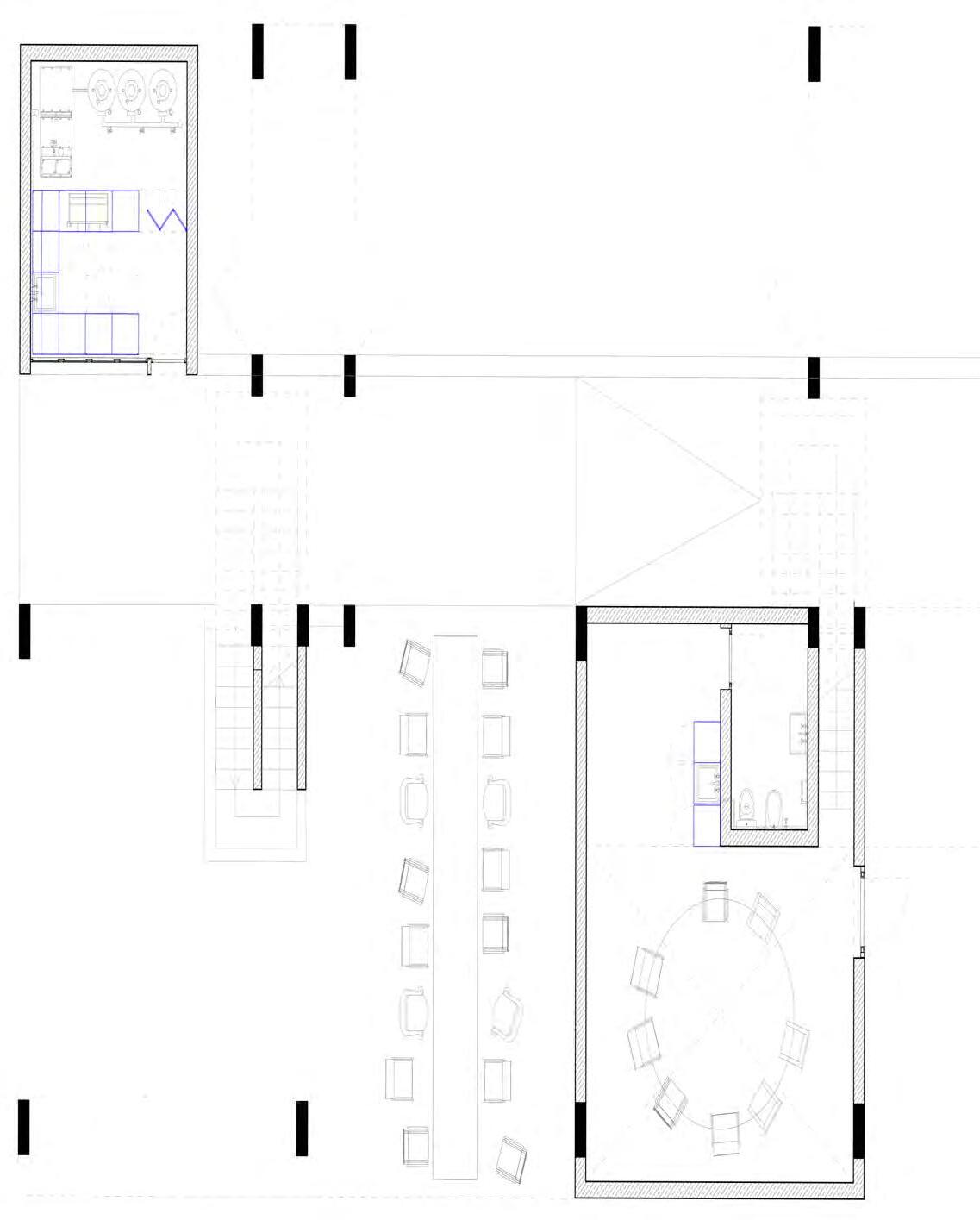
Coffee is served from the former technic room, which continues to serve as the central systems room but has accquired the secondary function as a cafe tabaccheria for the residents and local community. The long table is where the residents and locals meet, take a coffee and discuss the ongoing project, upcoming events and general small talk of everyday life.
The long table informs a communal spirit and is a space for all generations to gather and engage with the project and the community.
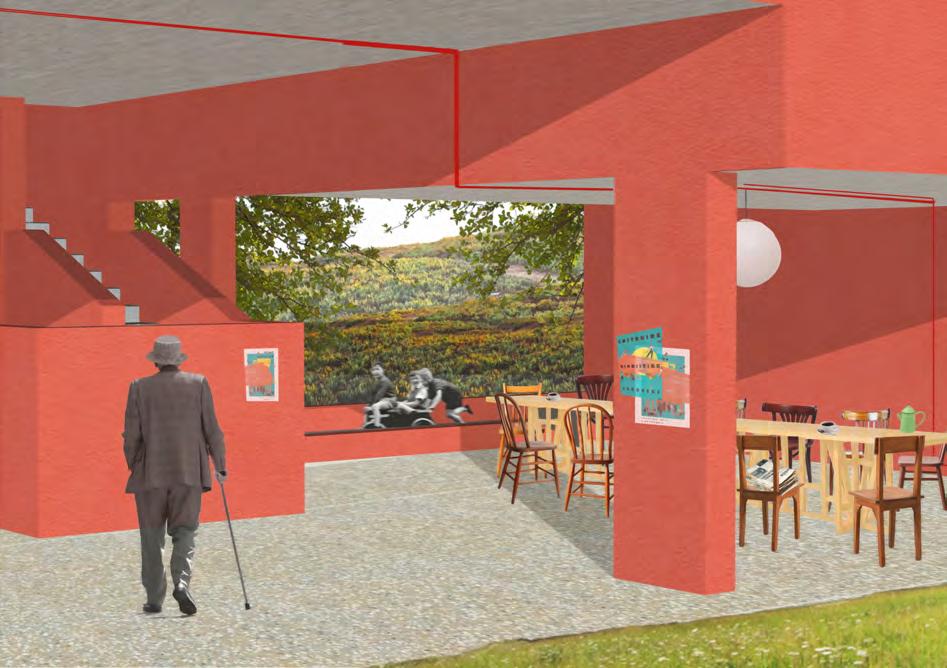
The former corridoor and entryway is maintained and links the first floor residences and mezanine common spaces. The new landmark ramp brings residents into the northern entrance allowing the full length of the corridoor to be utilised and appreciated, giving a sense of arrival specific to the upper floors. The corridoor space was formerly utilised as a entryway like space to hang the childrens coats and bags.
The circulation space takes on a new semi communal programme, using the existing niches to zone activies such as reading, playing chess or studying. Privacy increases as you go up the floors and this first floor zone is intended to be semi-private and is a semi-cold space with no heating.
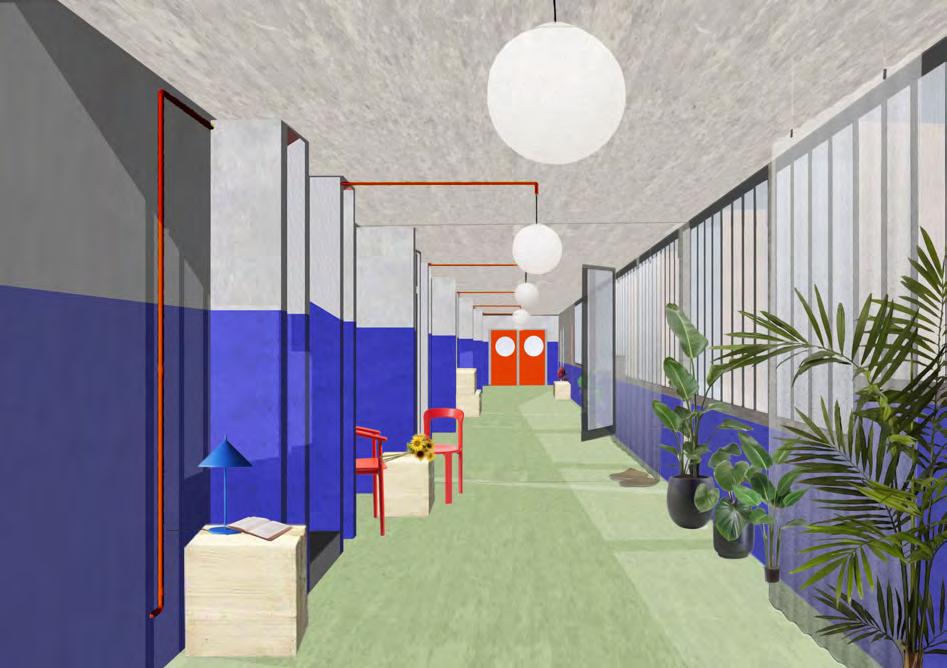
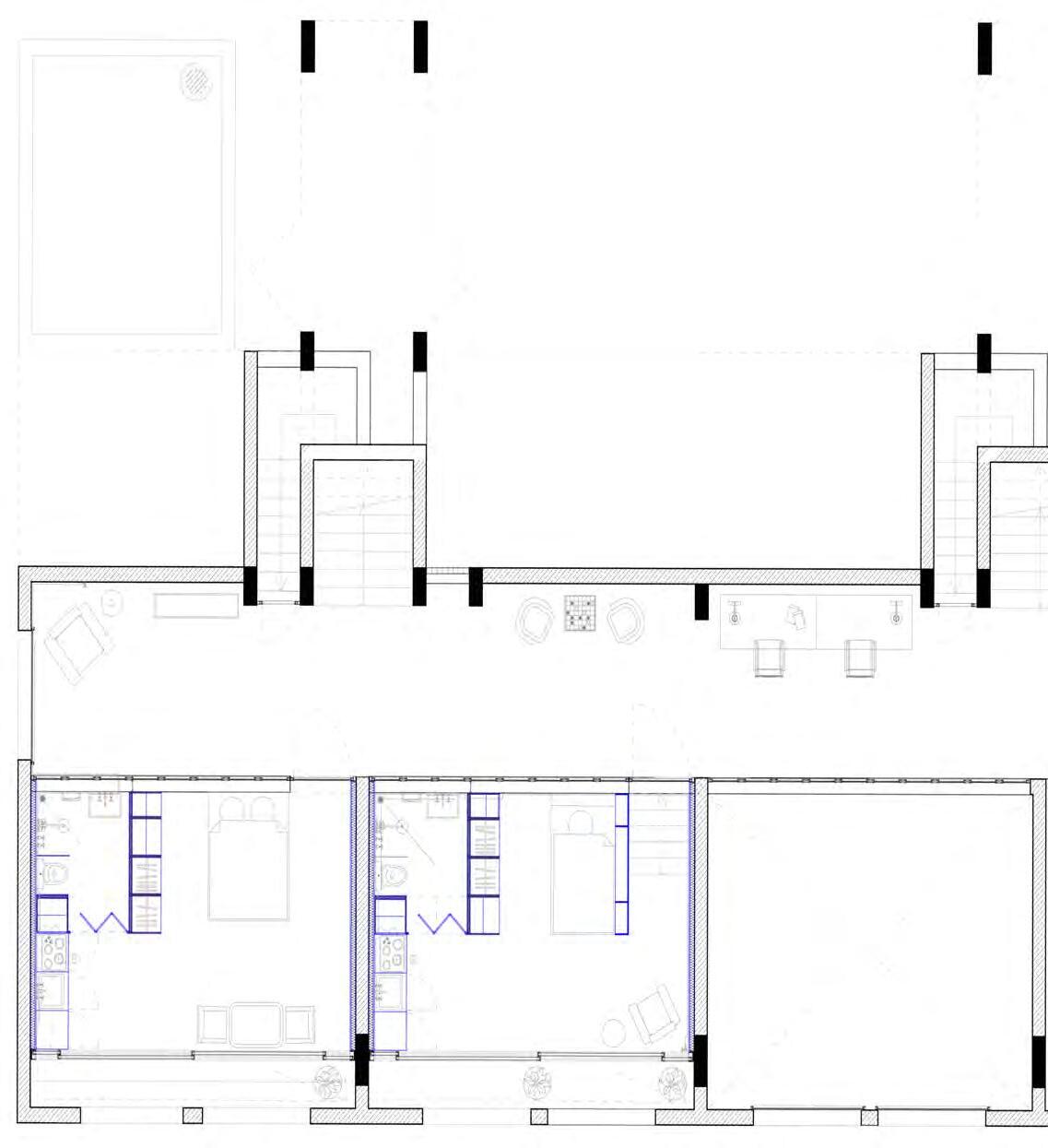
The foyer provides additional occasional living space for the smaller studio units, extending their usable space in the mid-season and allowing them to meet and spend time with their neighbours, especially important for the older and retired residents.
The upper floor is characterised by modular and repeated ‘shells’, provided by the architects at the initial stage of the project. These insulated and heated boxes sit centrally within the former classrooms with varying balcony and terrace spaces. In some units a larger balcony is provided to the north, while in others the lower floor mezanine terrace is left open air creating shady outdoor space to retreat through the hot summers.
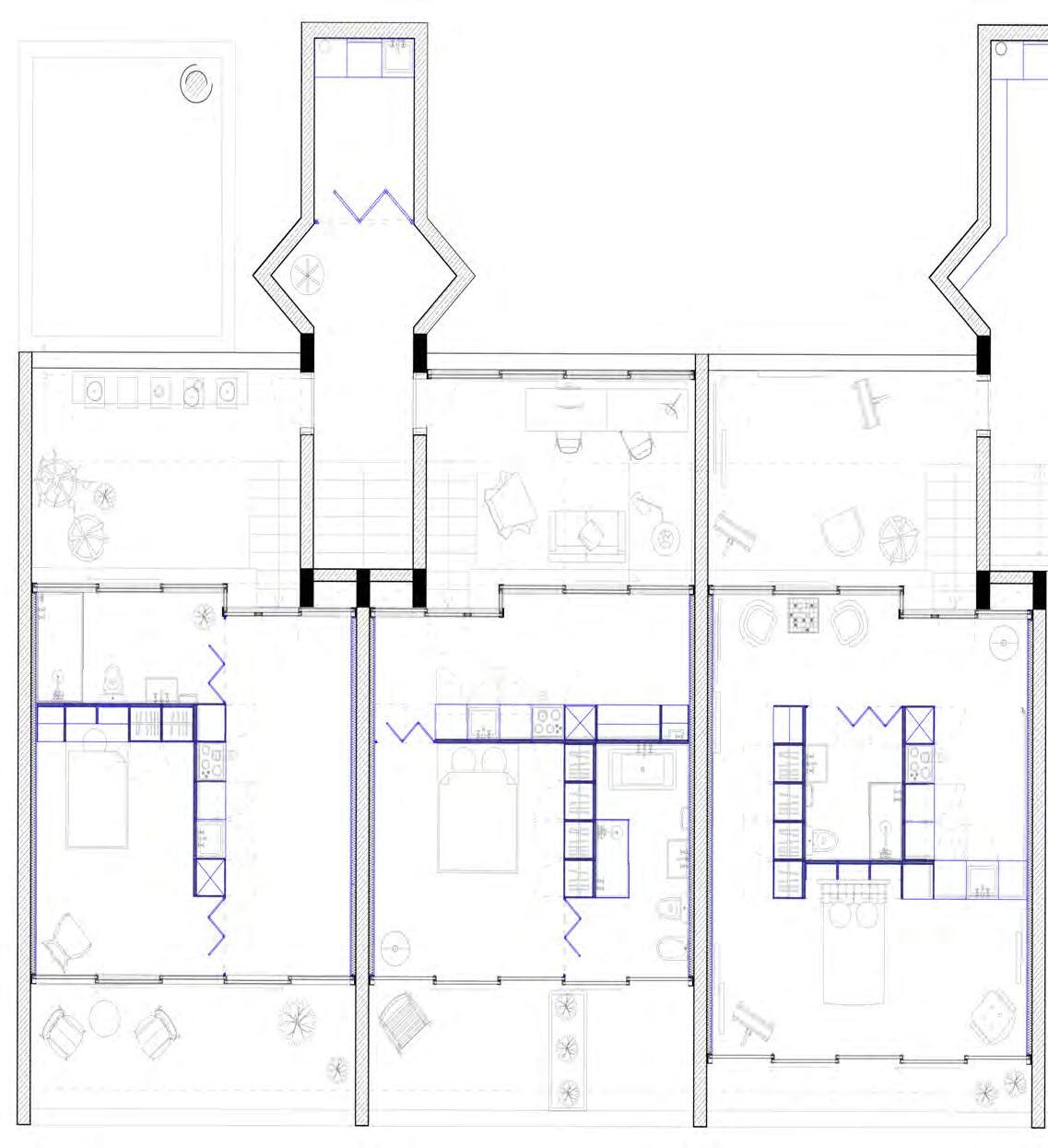
Within the units the residents shape and divide their space using modular box elements which form wall segements housing the storage, kitchen and wardrobes for the homes. These box walls serve as nucleus for the home allowing free plan in the surrounding spaces divided only by sliding doors or light curtains to give privacy where needed, maximising the use of the small units.
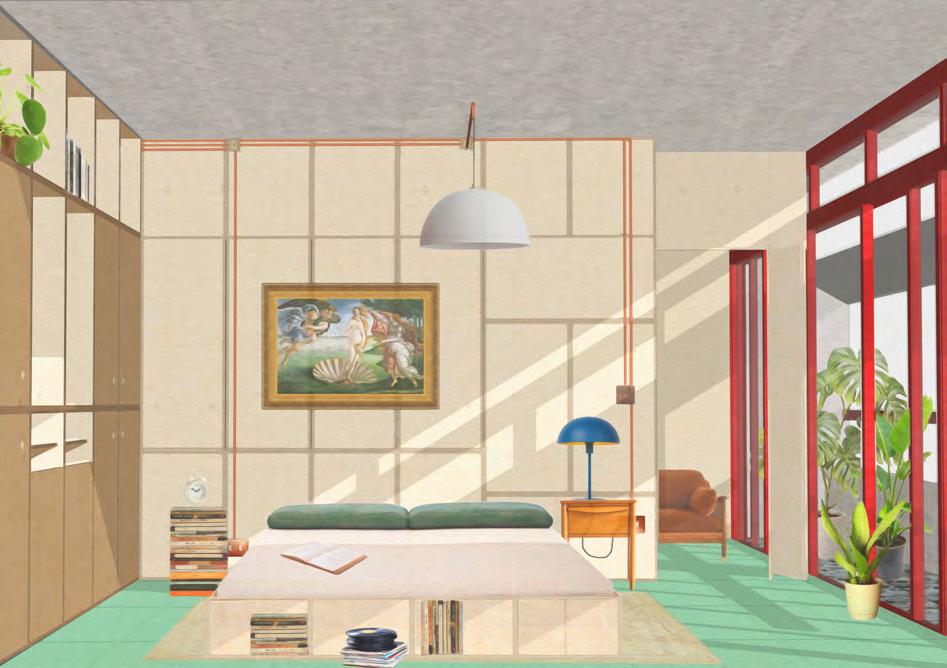
Technical Drawings
The project follows three key stages, firstly demolition and renovation works to the existing building, uncovering and reconnecting the electrical and pipework systems and removing material and old finishes.
The architect’s intervention then follows creating an insulated habitable box within the units using a shell of glazing and plywood within the central zone of the unit, prescribing terrace and balconies on either elevation. Underfloor heating is added to these insulated boxes and electrical points and pipes are connected to the previous wiring and plumbing.
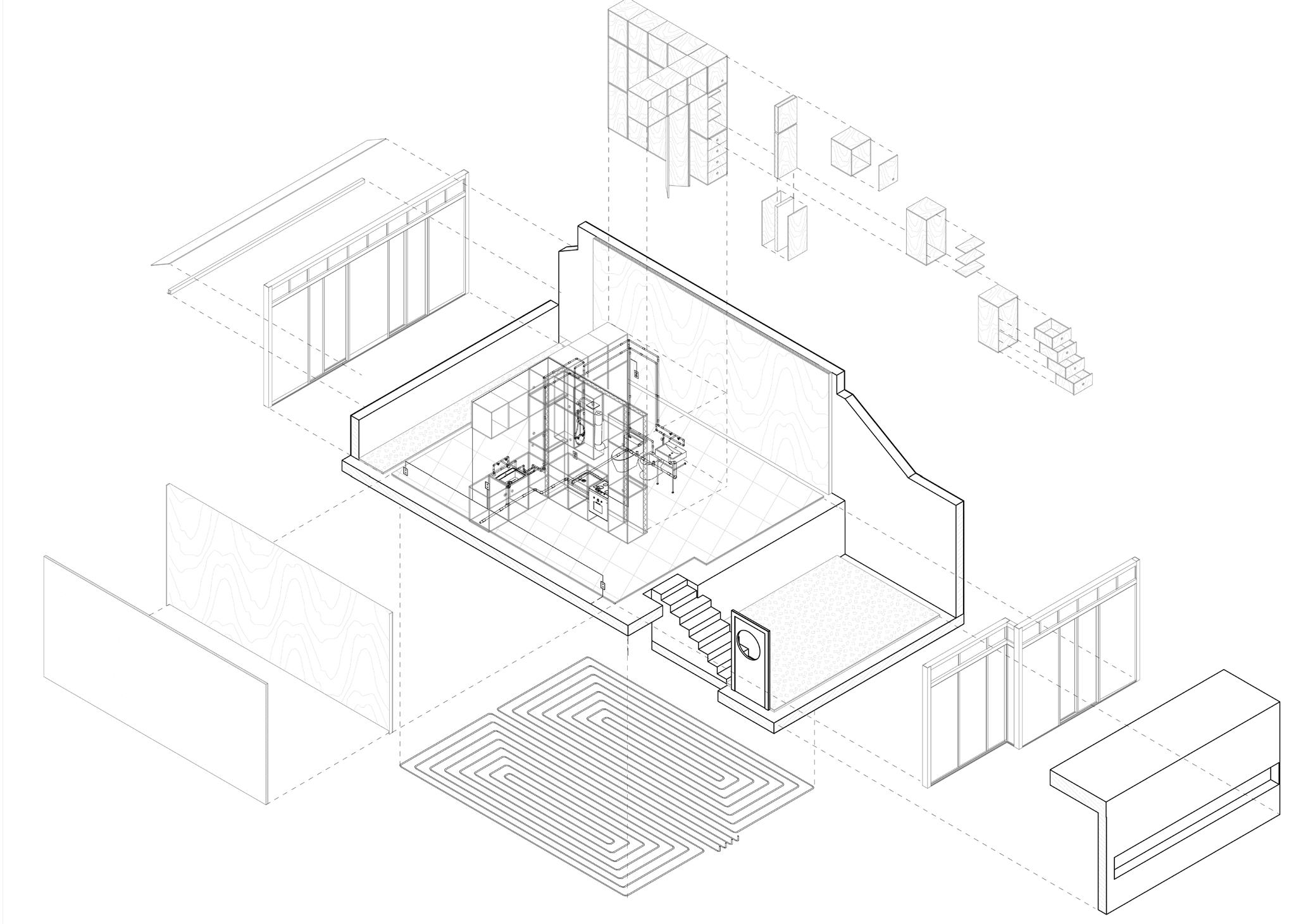
Lastly the residents inhabitance, using the modular box system residents build their interior walls, dividing and arranging spaces freely within the shell. They are then able to connect the plumbing wiring and vent to the existing systems through rudimentary systems of exposed copper pipes. The modular boxes hold all of the main functions of the home and serves as a nucleus of the space.
Existing structure with removal works ie. window frames
Red steel glazed walls
Terrazzo floor finish to outdoor spaces and drainage works
Underfloor heating system
Linoleum indoor floor finish
Connection to existing electrical points
Thermal insulation and Plywood panel finish Steel hand rail added at height of previous window frame
Modular Plywood box system with acoustic insulation
Plywood inserts to provide box function
Exposed pipework connecting to existing plumbing
A
DETAILS 1:10
Glazed wall to ground
200x130mm mild steel extruded joist attached with steel screws
35x125mm mild steel frame with 100mm aluminium sill
2x6mm insulated glazing in mild steel framing on a sliding mechanism
B
15mm floor finish: linoleum sheet with 300x300mm tile indent
20mm underfloor heating pipes with levelling material
1mm reflective membrane
250mm reinforced concrete slab
Glazed wall to ceiling
C
2mm bitumen waterproofing
10mm waterproofing membrane
25mm rigid insulation
100mm insulation
215mm reinforced concrete
135x35mm mild steel track with 35x125mm mild steel frame attached by steel screws
2x6mm insulated glazing in mild steel framing fixed
2x6mm insulated glazing in mild steel framing on a sliding mechanism
Terrace floor
D
15mm Terrazzo Tile flooring using recycled concrete from demolition works and local stone
20mm cement leveling screed with 2% slope for drainage
275mm concrete slab
E
25mm diameter stainless steel rainwater drain pipe
Parasitic window to wall
F
2x6mm insulated glazing in mild steel framing on a sliding mechanism
2x6mm insulated glazing in mild steel framing fixed
130x25mm mild steel rail attached with steel screws
250mm reinforced concrete wall
G
DETAILS 1:10
Translucent window
2x6mm insulated glazing with translucent finish in mild steel framing fixed 35x125mm mild steel frame attached with steel screws
Skylight
H
2x6mm insulated glazing in mild steel framing on a sliding mechanism
I
2x6mm insulated glazing in mild steel framing fixed 100mm mild steel casement
200x130mm mild steel bracket attached with steel screws
J
10mm depth extruded mild steel ‘beam’ to support upper skylight window
Exposed pipework
L 25mm diameter copper pipework with copper connections and brackets 25mm diameter hole drilled through existing wall to pass through pipework in order to reach existing plumbing
Inner Insulation
M
200x130mm mild steel bracket attached with steel screws
35x125mm mild steel frame with 100mm stainless steel sill
2x6mm insulated glazing in mild steel framing on a sliding mechanism
NOT CUT IN SECTION
20mm [560x1160mm] plywood panel
80mm [560x1160mm] rigid insulation
1mm Damp proof membrane
MATERIALITY + GRAPHICS
EXISTING BUILDING SURVEY. Existing Material Palette - Exterior.
Proposed Material Catalogue
Main external walls.
Main external walls.
Pre cast concrete walls with plaster finish A
Painted in a Vermillion Red, potentially inspired by Le Corbusier Couleurs no. 32090 (Rouge Vermillion). RESTORED AND REPAINTED TO ORIGINAL COLOUR.
Material EX.A
Concrete wall cast in form work A
Painted in Vermillion Red colour. Not sand-blasted or finished and mould of form work planks still visible as well as aeration in the concrete.
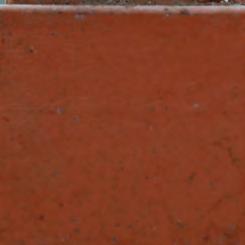
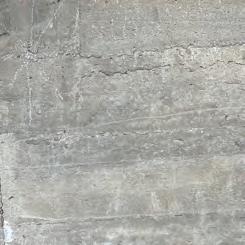
RESTORED AND REPAINTED TO ORIGINAL COLOUR.
Material EX.B
Pre cast concrete wall with plaster finish B
Thicker plaster coverage Painted in Red Vermillion colour. RESTORED AND REPAINTED TO ORIGINAL COLOUR.
Material EX.C
Concrete wall unfinished.
Concrete wall with no plaster finish and painted in Red Vermillion colour.
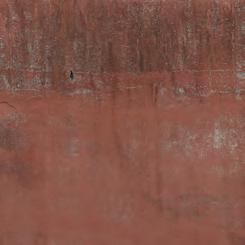
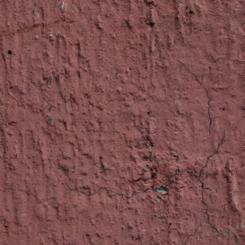
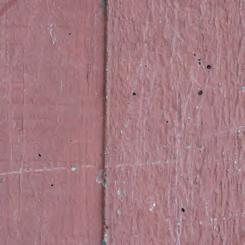
RESTORED AND REPAINTED TO ORIGINAL COLOUR.
Material EX.D
Exterior Elements.
Other wall materials.
Poured concrete foundations.
Poured concrete infill foundation to ground floor at north end. Unfinished and untreated with exposed concrete texture and form work marks visible.
Material EX.E
Cast concrete wall in form work B
Cast concrete walls previously covered in plaster and paint. CHIPS AND DAMAGE RESTORED
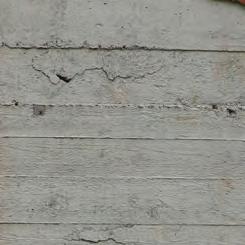
Material EX.F
Blue Permeable Tartan Ramp
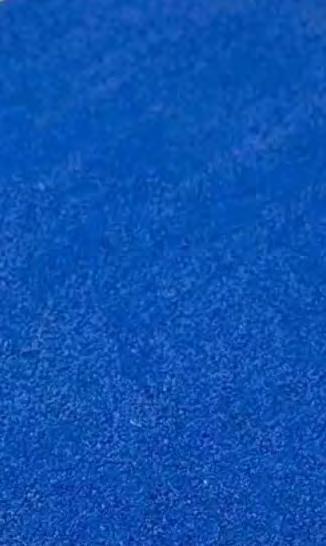
Cut into the landscape and finished with Cobalt blue tartan which is permeable to allow drainage. Where encased in a concrete supporting wall the wall is painted in the same blue colour.
Transparent Skylight and Glazing
Used in replacement windows and skylights, double glazed and encased in a red mild steel frame. In some areas glazing is operable to allow natural ventilation.
Metalwork.
Further materials.
Interiors. Further materials.
White glazed wall tile.
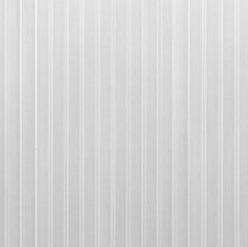
Roughly 100x100mm glazed ceramic tile in white colour. Repurposed from former bathrooms to be used to new kitchen countertops and as bathroom tiling.

Birch Faced Plywood.
Birch faced 2mm plywood with un-tinted treatment
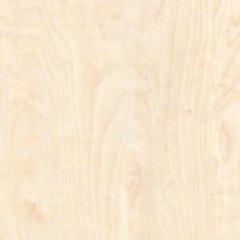
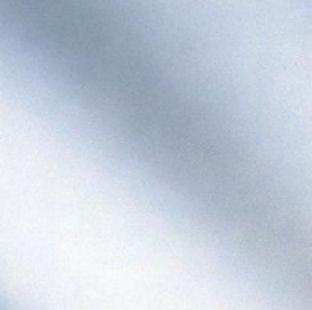
Material K
Pistachio Green Linoleum Floor.
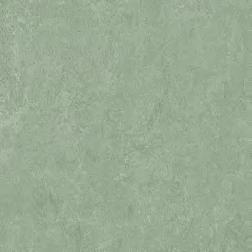
Pistachio Green ‘Forbo Marble’ Linoleum flooring sheets with 300x300mm tile indents to mirror the original linoleum tile flooring of the Scuola.
Terrazzo Tiles 600x600mm.
Terrazzo tiles produced using waste concrete recovered from the building demolition and locally sourced stone. Use to ground floor terraces and walkways.
3
Terrazzo Tile 300x300mm.
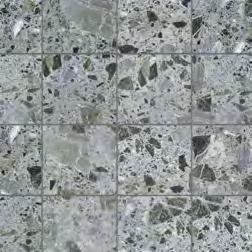
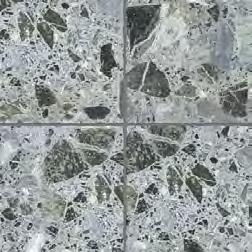
Terrazzo tiles produced using waste concrete recovered from the building demolition and locally sourced stone. Used to terraces and balconies.
Mild steel framing with burnt red power-coated finish to mirror the original red steel railings.
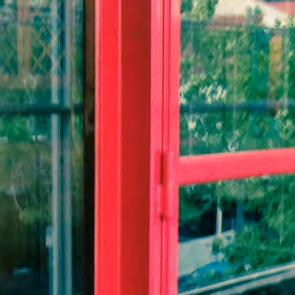
Mild Steel Window Frame. Exposed Copper Pipework.
Exposed copper piping for both water, drainage and electricity pipes and wires. With copper fixtures.
Polycarbonate Window
Translucent Polycarbonate sheeting used to windows to first floor studio rooms to allow light through the space whilst maintaining privacy.
Unit 2.3 belongs to Alessandro + Gio, a couple who are both practising artists and writers. They use the lower open air terrace as an atelier space for painting during the mid season and summer months.
The box units are used as central nucleus housing the bathroom and dividing the space into kitchen, dining, dressing and bedroom. The bedroom faces south with access to balcony garden. The box nucleus allows free plan, and all main furniture is oriented along the box walls allowing the main walls to be free for painting and hanging artwork.
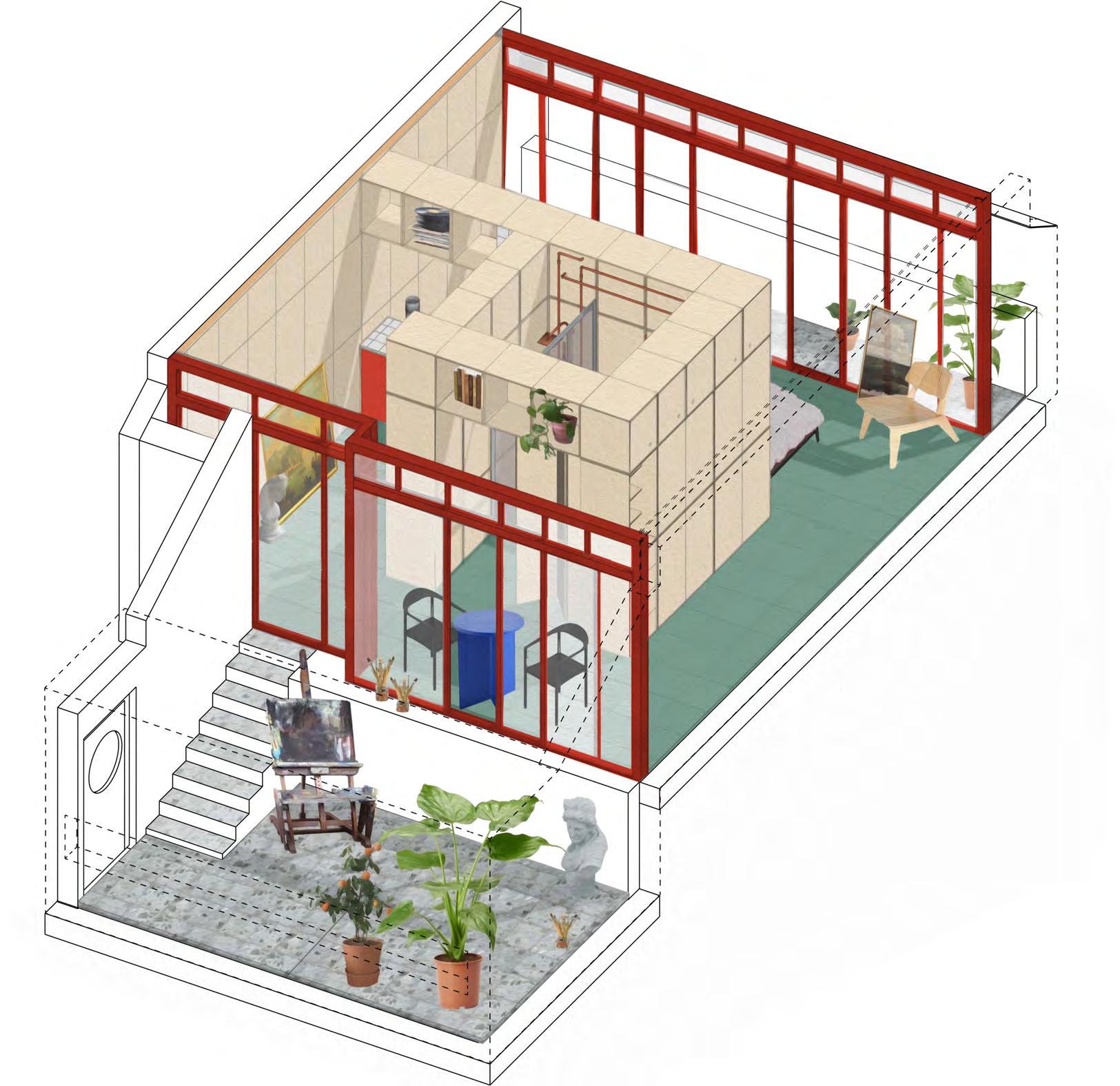
The shell - consisting of the red glazed walls, insulated inner walls and flooring makes up the architect’s intervention and is designed and fixed.
The interior space is free to be changed and adapted as the households change or grow.
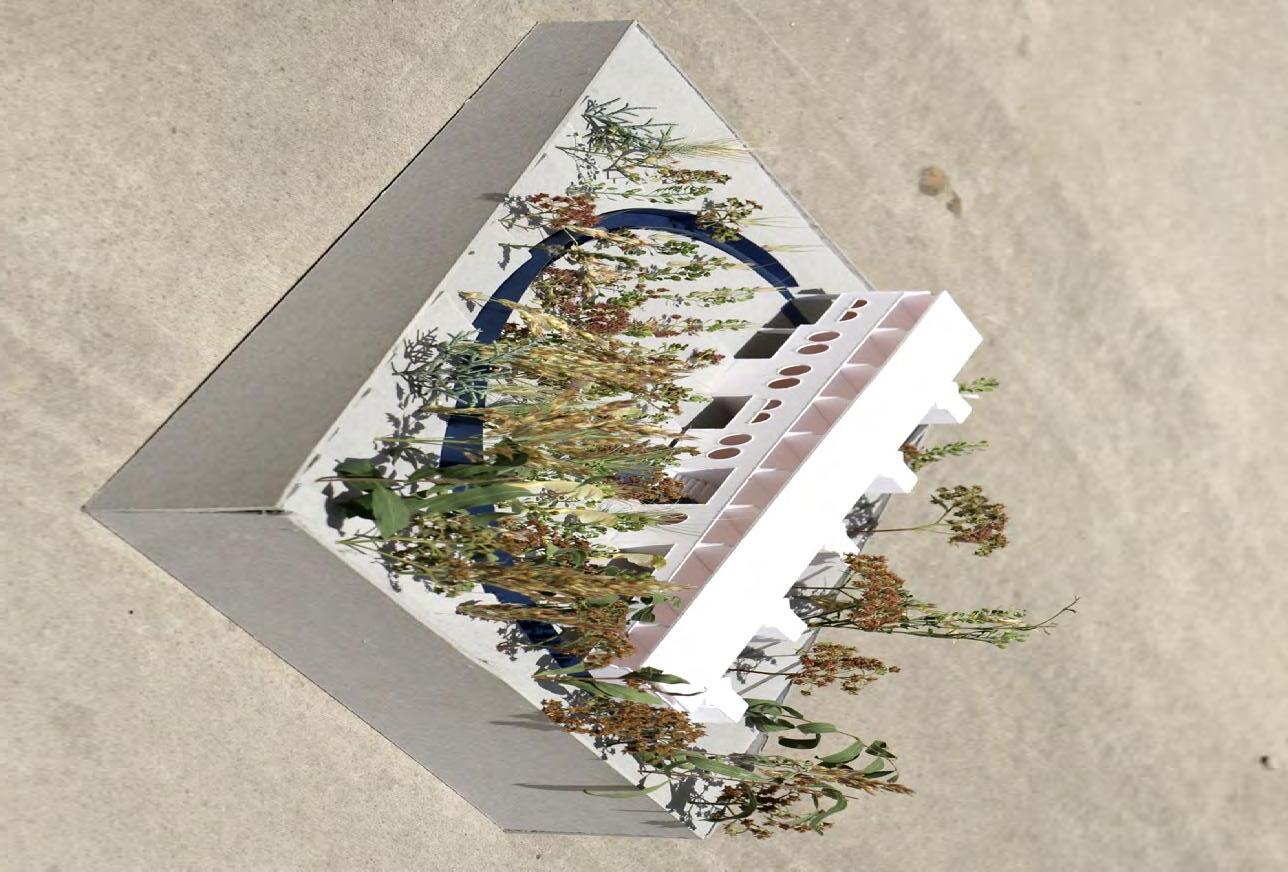
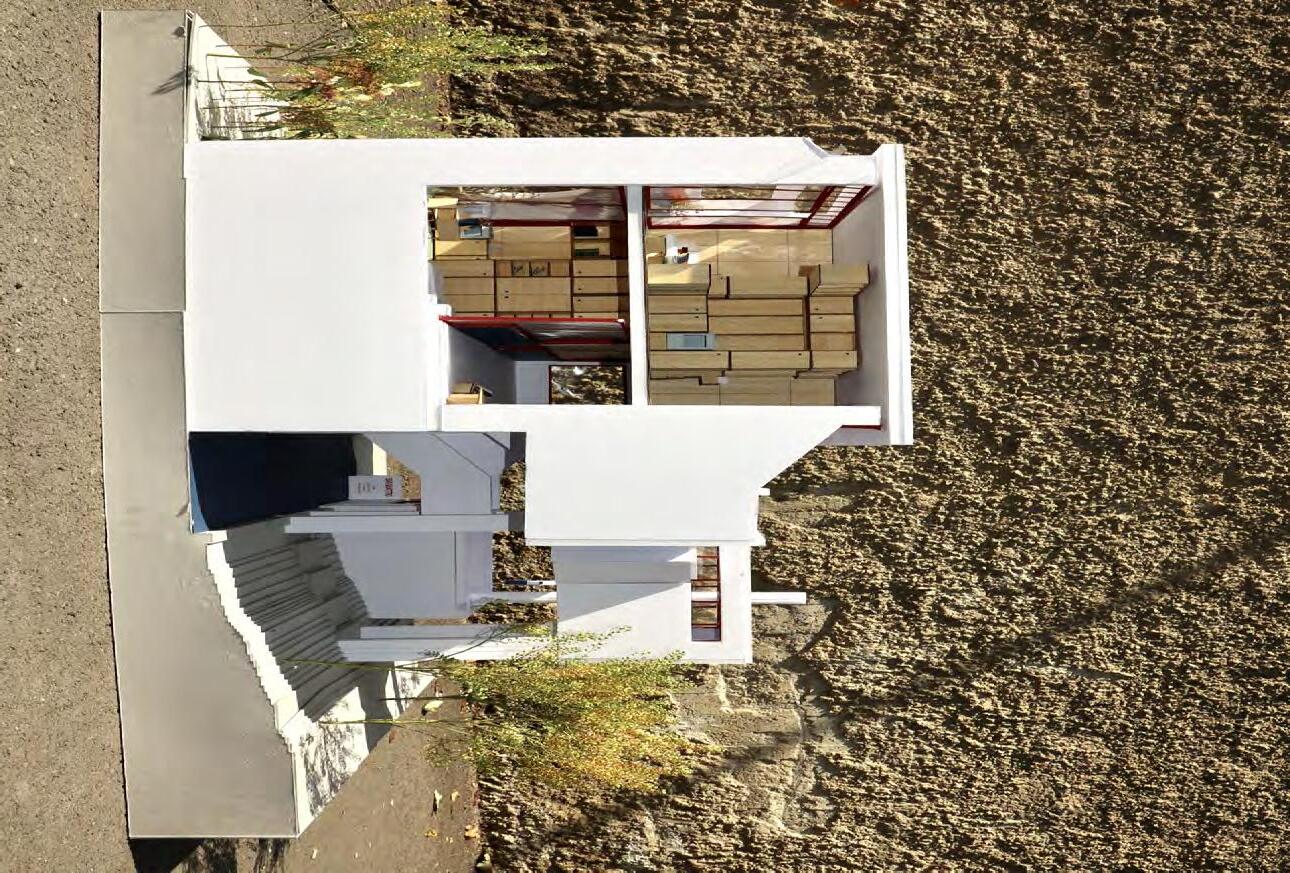
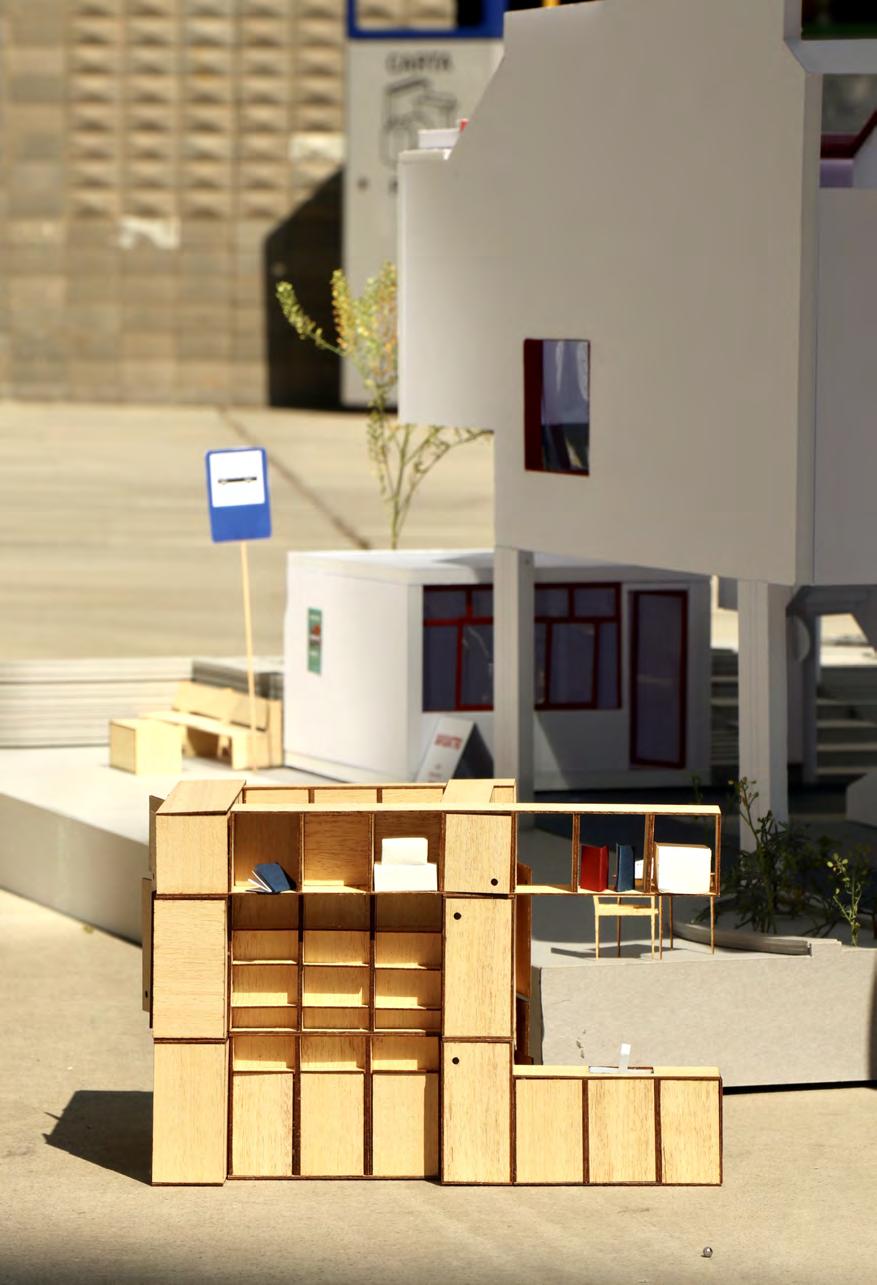
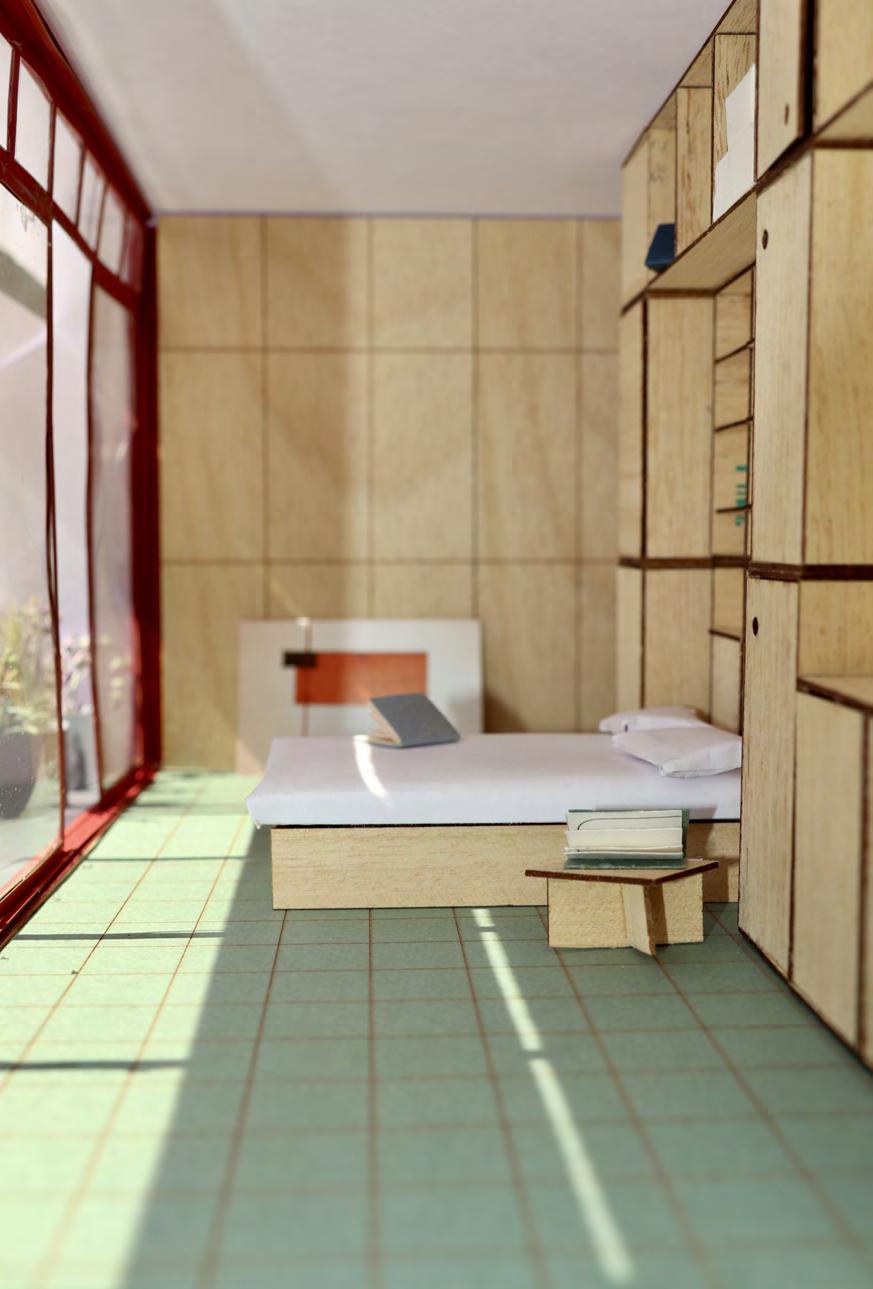
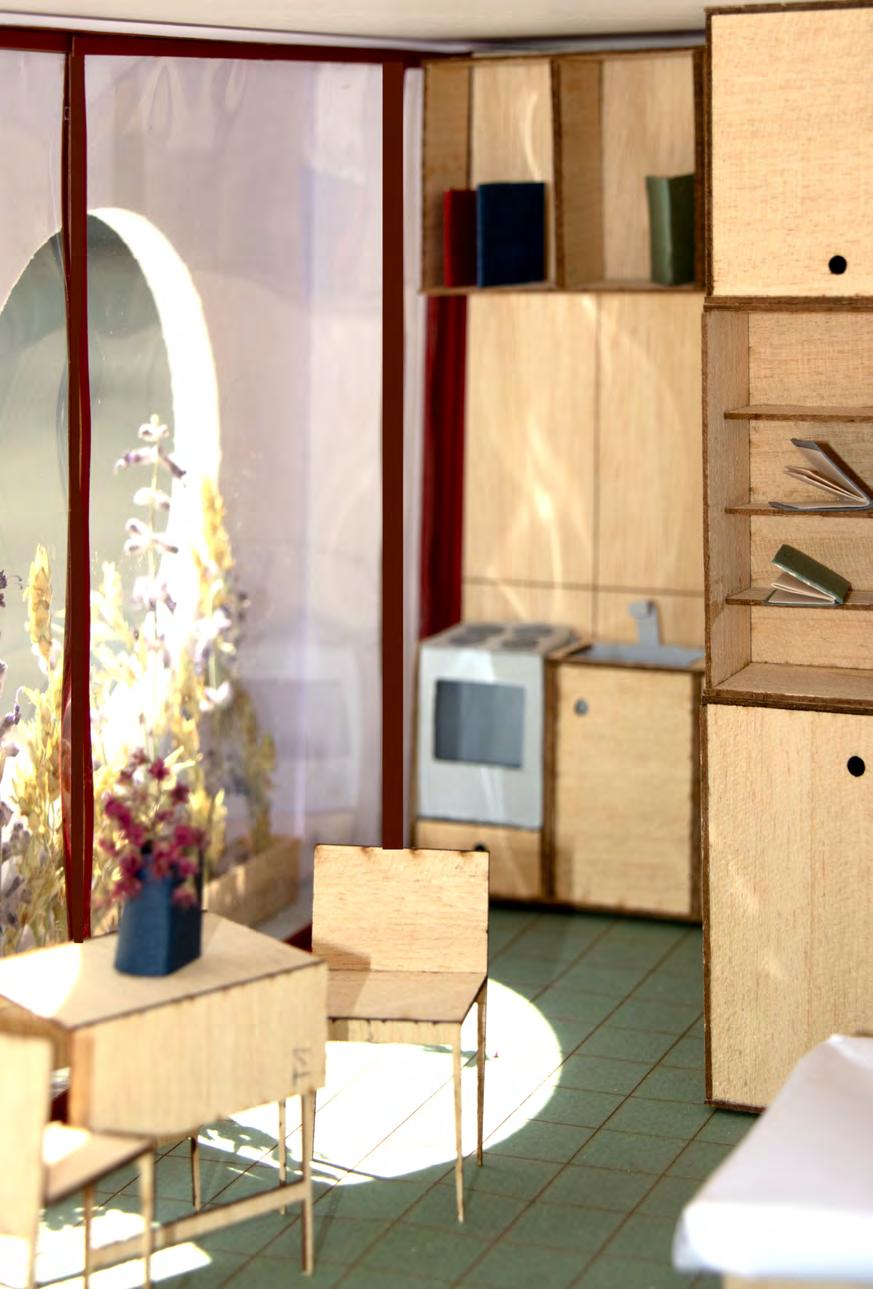
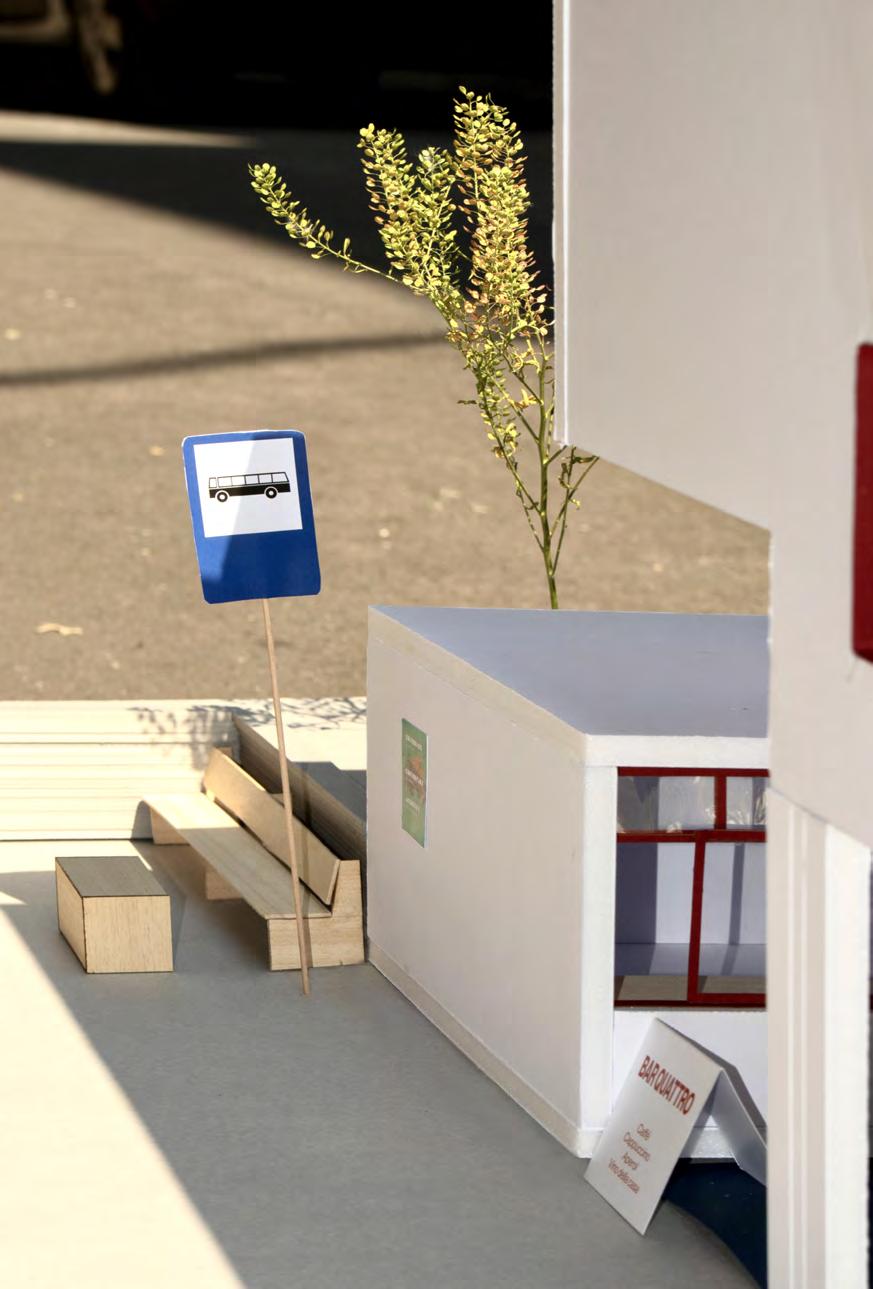
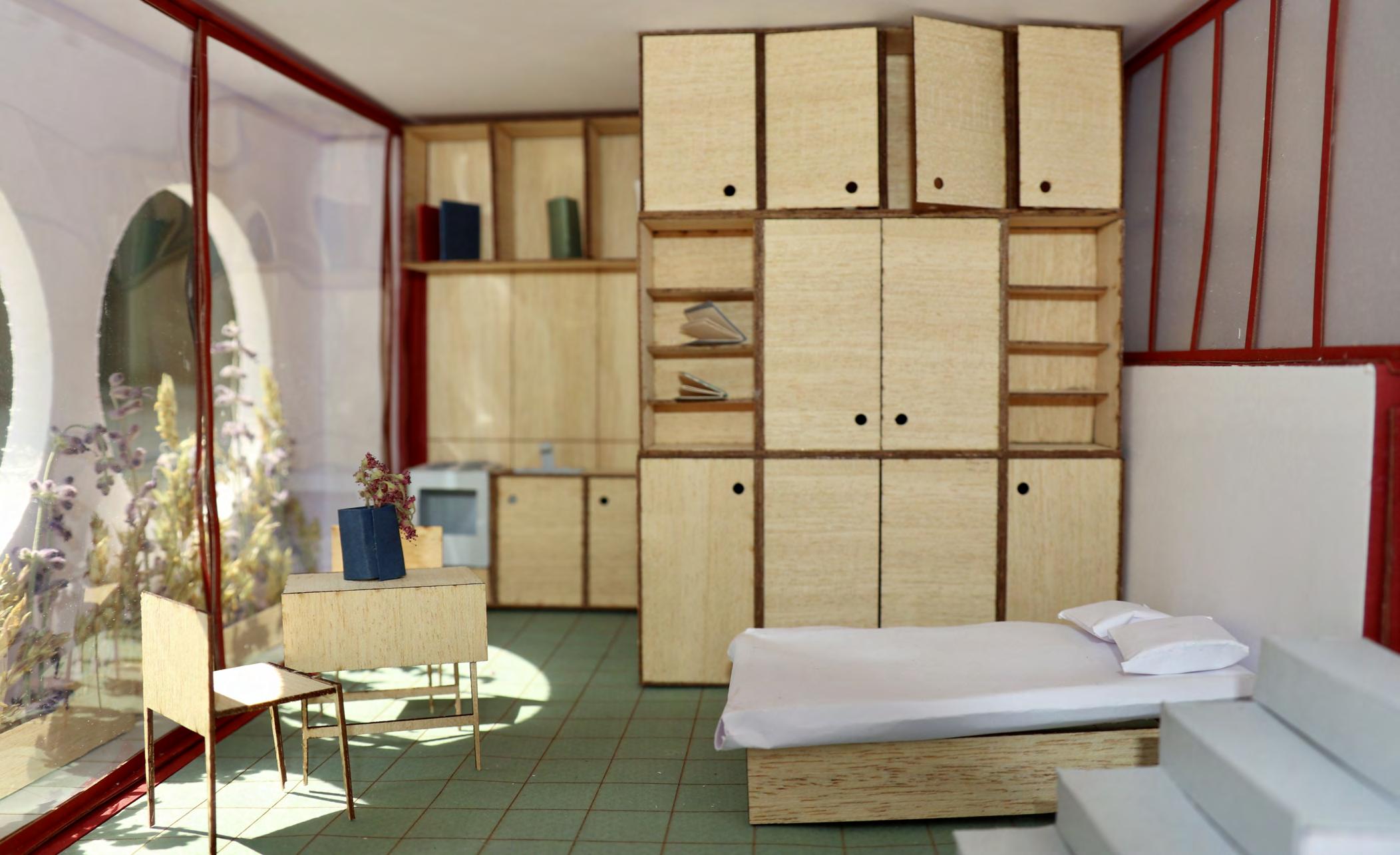
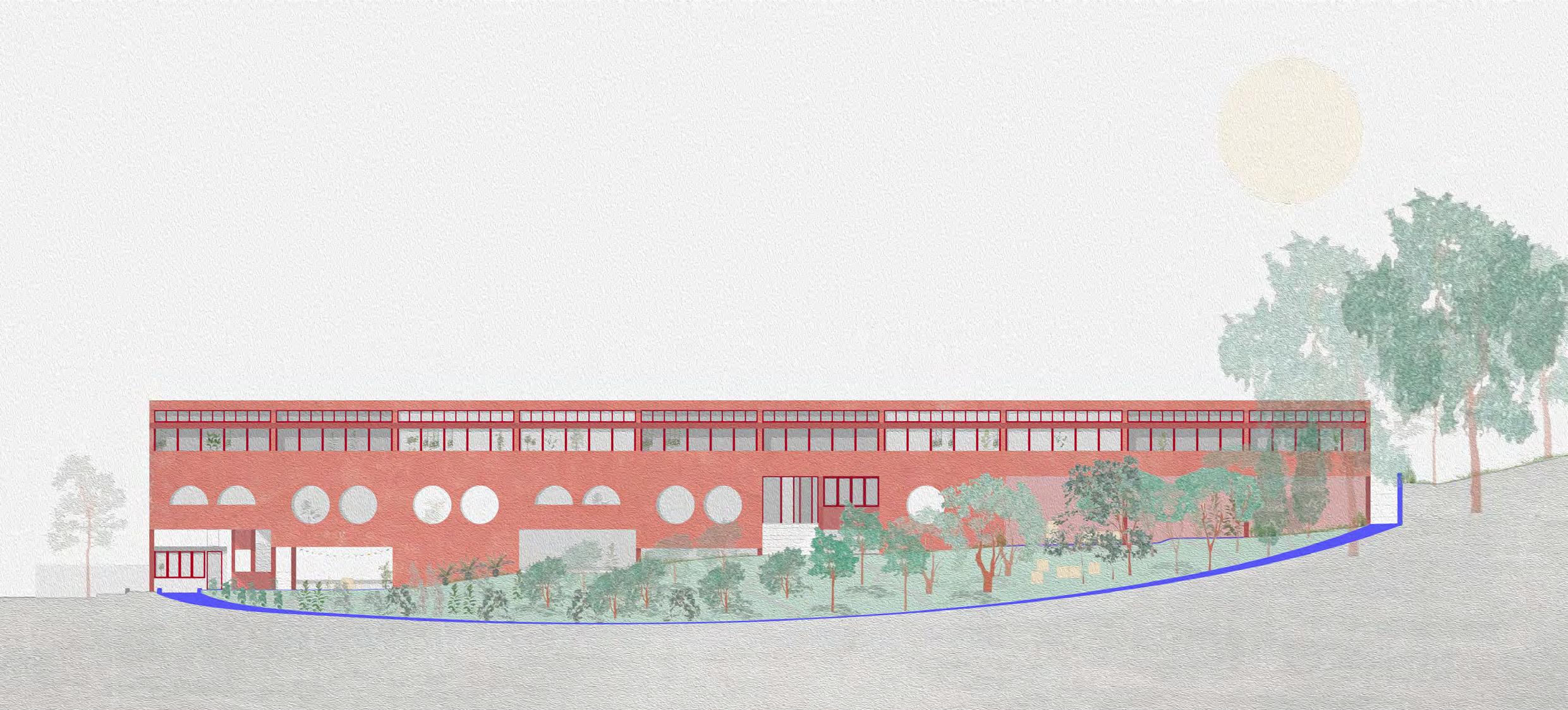