
12 minute read
Prevent Wear & Tear of Your Equipment With Best Lubricants
from CM December 2021
Lubricants

Advertisement
preVent Wear & tear of your equipMent With Best LuBricants
Lubricants are materials that are used to reduce friction and wear between surfaces that are in motion. Although this is the major role of lubricants, they can also be used as a heat transfer agent, a corrosion preventative, a sealing agent, and a means of trapping and expelling impurities in mechanical systems. While oils and greases are traditional liquid and semisolid lubricants, they also come in dry lubricants, gas lubricants (such as air), and other forms. When choosing lubricants for mechanical systems, it's important to examine not just how they'll reduce friction and wear, but also how they'll accomplish any or all of these additional roles. Lubricants aren't all created equal. A high-performance lubricant can have a major impact on operational success in heavy-duty industrial applications like those found on construction sites. Heavy-duty construction equipment, such as that used to create streets, highways, bridges, and buildings, is exposed to harsh environmental conditions. Whether it's a cold, foggy morning or a hot, dry, dusty afternoon, the lubricant's performance will be affected. The following are some of the most common lubricant depletion sites in construction operations: • Heat-sensitive greases can melt and run out of bearings, resulting in bearing failure. Contaminants can enter through grease that does not make a good seal. Somegreases are very sticky and practically immune to water washout, and they can easily carry large loads. Some manufacturers also offers automatic lubrication systems that ensure the proper amount of grease is applied in the right place at the right time. • Engine oil — If you're searching for extended oil life while still preserving your engine from the stresses of the job, LE's superior, long-lasting engine oils and LEAP oil analysis will help you safely lengthen oil drain intervals.
cants I r B u l
• Water can get into the fuel of diesel equipment that is left outside, causing it to lose power. Soot builds up in injectors, making them unclean. Furthermore, due to environmental concerns, lower-performance diesel fuel is now used in on-road and off-road mobile equipment. Some manufacturers have developed diesel fuel improvers to address these issues. They can clean your fuel pumps, injectors, and combustion chambers, restoring fuel economy, lowering pollutants, and lowering your overall cost per mile or hours of operation. Synthetic Oils Synthetic lubricants were developed and used for applications where petroleum-based lubricants were insufficient (e.g., at extreme high and low temperatures, under extreme wear conditions) or where special characteristics, such as long life, improved equipment efficiency, or non-flammability, were required. Synthetic lubricants, on the other hand, aren't just for specific applications; they're also useful when they can save money in areas like machine reliability, oil life, energy consumption, biodegradability, and safety. Among the many successful applications where synthetic fluids outperform conventional lubricants are: high-temperature lubricants for plastic calenders (significantly longer oil-change intervals, fewer machine shutdowns); worm gear drives in harsh service conditions (increased efficiency, lower operating temperatures); air compressors (elimination of combustible petroleum residues); hydraulic fluid in fire-resistant applications (reduced friction losses). The advantages of synthetic lubricant base stocks come not only from their basic molecular structures, but also from the lack of potentially dangerous molecular species that are inevitably present in conventional mineral oils in minute but significant amounts. While many, if not all, of the hazardous chemicals in crude oil are eliminated or improved during refining, depending on the methods used, a significant number of them will invariably remain in lubricating oil stocks, whether solvent- or hydrotreated. As a result, standard oils contain a diverse range of molecular species, many of which are poorly understood. Synthetic goods, on the other hand, are typically created through chemical reactions involving very pure, small molecules in which pressure, temperature, and the ratio of reactants can all be precisely regulated. The synthesis of the reaction up to the desired end product frequently involves several phases, each of which necessitates the separation of the intermediate products. Lubricant specifications Industry lubricant specifications were developed to define the quality level of products that will provide good lubrication when used as recommended and deliver a level of performance on which marketers, OEMs and consumers can rely. Chemical constraints and signatures: Many of today’s engine oil specifications include constraints to limit the use of some chemicals in order to protect parts of the engine and to comply with legal obligations. For example, the ash generated when metals such as calcium, magnesium and sodium are burnt in the engine can plug and damage the vehicle after treatment system, jeopardising the environmental protection they are designed to deliver. In the same vein, phosphorus is known to poison the catalysts used to reduce unburned hydrocarbons. These elements also have strong features including acid neutralisation for calcium and magnesium, antiwear for phosphorus containing components and antioxidant capabilities of the sulphur containing components. Innovation and lubricant formulation: Innovations introduced by vehicle manufacturers often create new performance requirements for motor oils, sometimes vital to the engine.
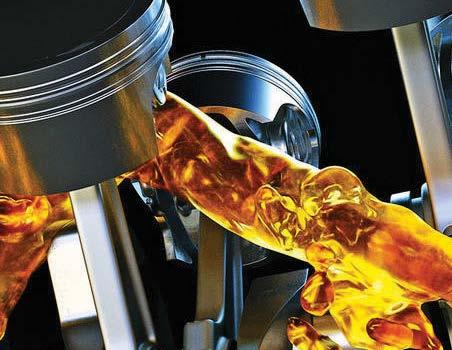
As an example, downsized car engines have been developed to cut fuel consumption and hence reduce CO2 emissions. These engines are often turbocharged, smaller displacement designs for the same or higher amount of power than the engines they replace. With high compression ratios and optimised fuelling, sections of the engine’s speed load /map could lead to a phenomenon called low-speed pre-ignition (LSPI), which can result in dramatic engine damage. New lubricant features were required to help prevent LSPI, and LSPI tests are being incorporated into the latest engine oil specifications. Another recent evolution is the use of low viscosity oils, such as SAE 0W-16 in passenger cars and SAE 5W-30 in heavy-duty vehicles. The aim here is to minimize friction losses in the engine and hence reduce fuel consumption. At the same time we are also seeing the use of new materials and coatings that sometimes have dramatic incompatibilities with certain additive components. These continuous innovations mean that using oils that have been approved by the vehicle manufacturer is increasingly crucial, and is a requirement to benefit from the manufacturers warranties. Things to Know While Choosing a Lubricant Lubricant Selection: There is a great deal of interest regarding the role lubricants play in reducing upfront costs. Lubricants have the potential to improve fuel economy and enhance engine performance and protection. This is achieved through minimizing metal-to-metal contact between moving components, while also reducing pumping and spinning losses. Due to the oil’s lower viscosity, it requires less work to move through the engine, and therefore flows faster. Newer engine types, which run at higher temperatures, can also stress conventional lubricants and accelerate the rate at which the oil oxidizes and derogates. Of particular relevance to those in the construction industry are API CK-4 oils, which are designed to be more robust and resistant to oxidation, as well as have improved resistance to aeration and increased shear stability. Improved aeration control is important for off-road engines where more air than usual could become entrained in the engine oil. A high level of air entrainment is dangerous, particularly at the bearings, where maintaining a suitable oil film is critical for protection.Together, these design improvements provide enhanced performance and greater hardware protection, and may reduce vehicle downtime—a major source of missed opportunity in construction operations. API CK-4 licensed oils are backwards compatible, allowing for their use in the vast majority of older diesel engine vehicles that ran previous oil categories (API CJ-4, CI-4 Plus, CI-4 and more). In addition, users can benefit from the increased robustness of CK-4 oils over the previous CJ-4 oils, enabling increased performance and protection gains. The Role of Oil Analysis Testing: There are numerous benefits to implementing an effective used oil analysis program in a company’s fleet management practice. A good program is part of a sound maintenance regime and is a cost-effective process that can monitor oil condition in heavy industrial equipment. Oil analysis typically involves three steps: taking a representative sample from the equipment, sending the sample to a qualified used oil analysis lab, and interpreting and acting on the results. Oil analysis is most effective when performed at regular intervals, so that a trend can be generated and used to improve performance and efficiency of equipment. Testing can detect impurities and measure their concentration, showing operators how and why machinery is experiencing wear, and helping to identify the source(s) of contamination. By evaluating the condition of lubricant and equipment on a
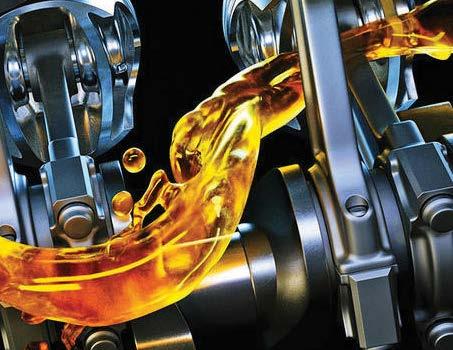
www.constructionmirror.com
routine basis, minor mechanical problems are discovered before they become serious and expensive to fix. To extend drain intervals, and improve efficiency and fuel consumption, it is highly recommended to implement a used oil analysis program. Low/High Temperature Operations: Another thing worth considering is selecting an oil that can handle tough climates and extreme temperatures. Depending on the location, the equipment used in construction operations may be exposed to varying challenges posed by high and low temperatures. In such difficult conditions, the viscosity in the lubricant can become a cause for concern. If the temperature reaches the critical zone, depending on the chemical composition, the lubricant can start to stiffen or become overly viscous. This results in machinery hardware being improperly lubricated and under strenuous conditions, over time, equipment may experience catastrophic failure. To prevent this, construction operations can use a lower viscosity oil, which can stay viscous and maintain flow under a wide range of temperatures. Multi-grade, low viscosity oils perform better over a range of temperatures— it’s not too thick in cold climates or too thin in heat—ensuring proper and adequate flow of oil to protect key critical engine components. In addition, the entire vehicle powertrain and hydraulic system can experience improved operating efficiency by uing the lowest viscosity grades allowed by the Original Equipment Manufacturer's (OEM) ambient temperature requirements. Construction equipment has come a long way - and so have the lubricants that keep it running smoothly. As technology for machinery has advanced, the industry has demanded that lubrication and other fluids keep up with changing transmissions and increased load requirements. Keep these three things in mind when sorting through what your equipment needs. Stress is a (huge) factor: Construction rigs have many different lubrication needs, and whether they are pushing dirt or pulling loads, they all (unsurprisingly) are put under a lot of stress. This is why most construction lubricants are formulated to be pretty tough. The following lubricants, however, should receive special attention: • Hydraulic fluid: Hydraulics need fluids that can withstand lifting and hoisting - along with the wear and tear these activities bring. Hydraulics are often exposed to a variety of outdoor elements, so finding a product that can handle any and all of those conditions is important. • Power transmission fluid: Transmissions can take a beating in off-road construction equipment. Watch out for getting washed out: Construction equipment doesn't get to retreat to a garage or shed at the end of a long day. It tends to sit outside, day in and day out, until the job is completely done. It's important to use a product that can withstand both rain and sunshine - and everything in between. Grease, in particular, is susceptible to washout since it's oftentimes most exposed. Seasons matter: Finally, don't forget about changing seasons. Though construction may pick up in the summer, many projects go year-round until they're complete. Choosing products that are multi-viscosity or have a viscosity that matches the temperature outside is important to ensure your machinery performs at its best. As a general rule of thumb, low- or multi-grade-viscosity products should be used during cool temperatures, and higher- or multigrade-viscosity products should be used during warmer months. What Makes Up the Lubricants We Use? A base oil is the starting point for all lubricants. Mineral, synthetic, and vegetable are the three sorts. We frequently deal with mineral and synthetic materials in industrial settings, so I'd prefer to concentrate on these. Mineral oil is made from crude oil, and its quality is determined by how it is refined. Oil is graded on a scale, and different procedures necessitate varying oil quality. Mineral oil is primarily composed of four types of molecules: paraffin, branching paraffin, naphthene, and aromatic. Paraffinic oil has a long, straight chained structure, whereas branched paraffinic oils have the same structure but with a branch off to the side.
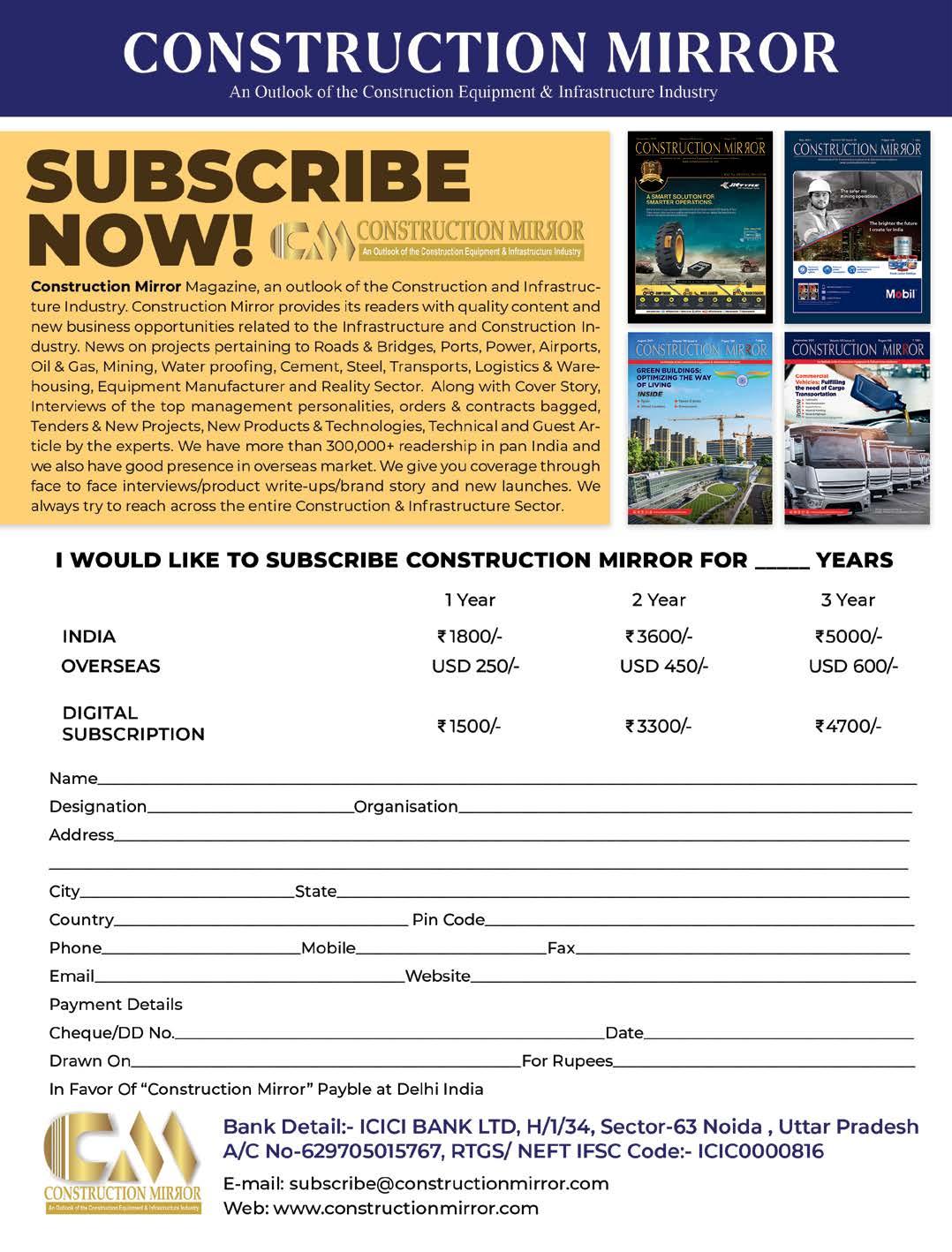
cants I r B u l
Synthetic oils, like branched paraffinic oils, are man-made fluids with comparable straight chained structures. One of the advantages of a synthetic is that the molecular size and weight remain consistent, whereas mineral oils fluctuate dramatically, resulting in fairly predictable features. The lesser the density of the oil, the slower it flows. Molasses, for example, has a high density and a low viscosity, whereas baby oil does not. The viscosity required for a given application is entirely dependent on its speed, operating temperature, bearing type, and component type, such as a gearbox versus a motor. By encapsulating particles and suspending them in the oil, dispersants help to protect components from abrasion by wear products, allowing them to be readily flushed and removed from the system. EP additives react with the surfaces of a component to generate a thin protective coating that prevents metalto-metal contact. In some cases, utilising grease rather than oil has advantages. Grease seals out adulterants, is better for insoluble solid additives like molybdenum disulphide and graphite, and has better stop-start performance because it doesn't void like oil, reducing the risk of a dry start. The broadness of grease, on the other hand, limits bearing speed, lowers component cooling, makes sampling and analysis difficult, and makes determining the right amount of grease to add difficult. This is a critical factor to consider when selecting whether to use oil or grease for a given application. With a simple concept or knowledge of lubrication, you can see why employing the appropriate lubrication in your machinery has so many benefits. Every organisation wants to achieve more efficiency, longer life, improved reliability, and spend less money on maintenance. How the Industrial Lubricants Market is Evolving? The industrial lubricants sector is altering its supply chains and marketing methods, notably in Asia. Greater internet penetration among the region's populace has resulted in a massive increase in online shopping usage, where lubricant marketers have discovered a viable retail platform. Lubricant marketers in Asia have recognised this opportunity and are connecting their supply chains to improve their operations. This helps them to optimise influence at the end-user level while reducing expenses at the supply chain's back end. From a product development standpoint, the sector is likewise changing. Sustainable ways to reduce carbon footprint and greenhouse gas (GHG) emissions are being emphasised more globally. However, at a more granular level, this has resulted in significant advances in green chemistry. The focus on bio-based product development has changed how corporations approach lubricant research and development. CM
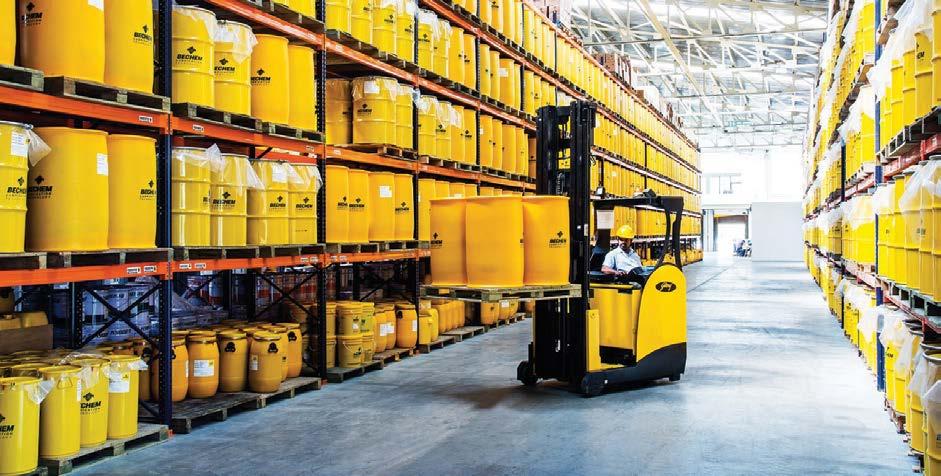
21−23 APRIL, 2022

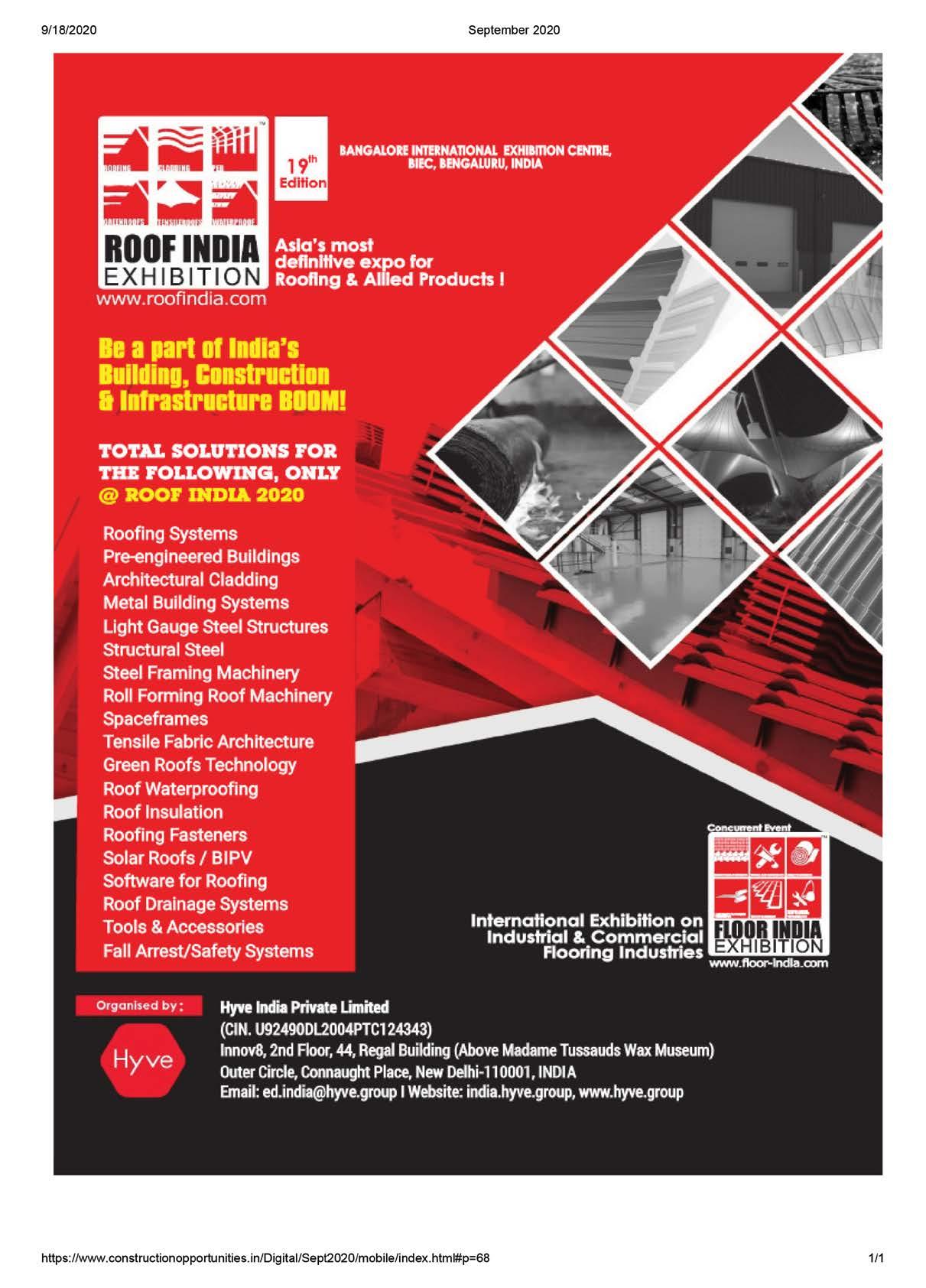