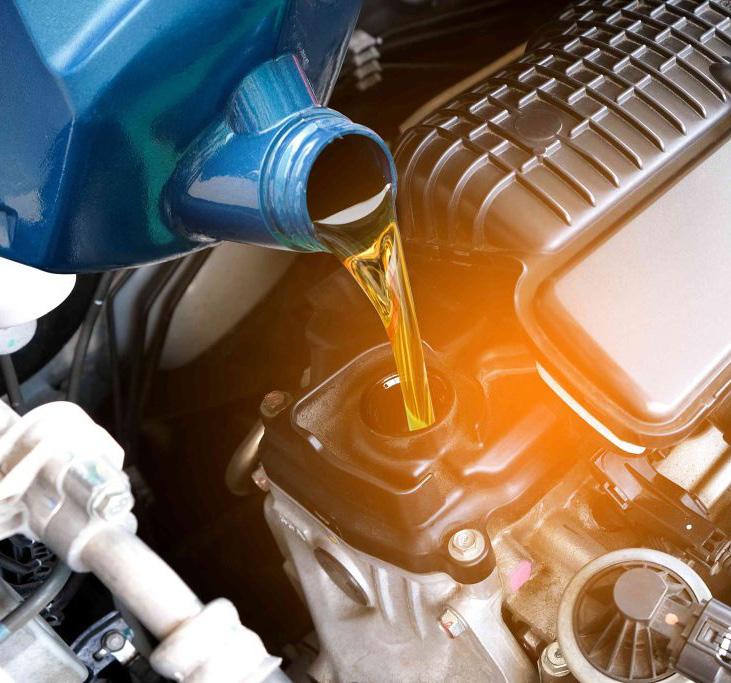
12 minute read
Manual & Automatic Lubrication Which One Is Better?
Lubricants

Advertisement
MANUAL & AUTOMATIC LUBRICATION - WHICH ONE IS BETTER?
Lubricants have a variety of roles in enhancing the functionality, longevity, and many other aspects of machines. To maximise machine uptime and meet your company's deadlines, choosing the right lubricant is crucial. Hydraulic systems are often used by construction workers, and they depend on them to resist variations in temperature, pressure, and speed. In the most severe situations, a hydraulic lubricant is necessary to safeguard the hydraulic system. Operating construction equipment in difficult environmental conditions requires maintenance and reliability. Oil diagnosis is one technique used to enhance the upkeep and dependability of construction equipment. An integrated oil sensor for hydraulic fluid in construction equipment was used in this work to perform condition monitoring. Crane hydraulic oil is contaminated by a variety of substances, including moisture and dust. Contamination can also be caused due to improper lubrication. The lubrication process plays an important role in controlling contamination. So, what exactly is lubrication? Applying lubricants, often known as oily or greasy substances, to moving machine components reduces friction and enables smooth passage of the parts past one another. In order to prevent metal-tometal contact and maintain the machine's efficiency, lubricants create a coating between the metal surfaces of its component parts. Before we can comprehend how temperatures and other operational factors impact lubrication, we must first understand how lubricants work to reduce friction and wear. When a system is first started up or when it is heavily loaded, like in gearsets, the metal surfaces may actually come into contact with one another. In this lubrication scenario, lubricants must have the required viscosity as well as the proper anti-wear or extreme-pressure additive chemistry to eliminate (or
LUBRICANTS
reduce) frictional wear. In boundary conditions, the chemical characteristics of the additive package will be just as important as the physical characteristics of the oil, particularly viscosity, but both will be altered by operational factors like temperature. This lubrication condition develops when a thin layer of oil surrounds a rotating component, such a shaft, preventing the shaft from making direct contact with the bearing. This occurs when a machine begins to rotate and reaches high enough speeds and tensions for an oil wedge to travel between the shaft and bearing surfaces, forcing the shaft away from the bearing surface. Typical applications include a turbine or the crankshaft and journal bearing in an automobile engine. The viscosity of the oil must be such that it maintains the hydrodynamic condition under all operating circumstances, including high speed and high load, low speed and high load, and low speed and low load. Manual lubrication For manual lubrication, a technician with a grease gun or other conventional lubrication instrument is required. Numerous drawbacks of this lubrication technique include prolonged machine downtime, high maintenance expenses, and uneven lubrication (too much, too less, or not frequently enough). Manual lubrication does not meet today's requirements for cost effectiveness and preventive maintenance. The proper amount of oil applied to your equipment at the right time and in the right location, typically while the machine is in use, cannot be ensured by a conventional lubrication system like a grease gun. With manual lubrication techniques, you run the danger of either under-lubricating or over-lubricating your machine, both of which can have detrimental impacts on its components, productivity, and overall expenses. At first glance, using a manual lubrication system for your industrial applications may appear to be a cheap alternative. However, when you weigh all of its drawbacks against the benefits of an automated lubrication system, the latter one will ultimately turn out to be the most cost-effective option. Implementation Takes A Long Time: Manual lubrication requires a lot of labour, which is expensive. It requires extensive preparation work, such as gathering tools and equipment, shutting out gear, and removing coverings and panels from machinery to access the lubrication locations. In order to meet the increasing production needs, today's machines, especially those with high-speed bearings, need to be lubricated more often. This increases the frequency with which the tiresome process of re-lubrication must be performed, raising the expense of equipment maintenance. The major issue with manual lubrication is improper lubrication. Underlubrication can result in a number of issues, such as: • Friction between metal surfaces that is increased, • Friction, which generates more heat, • Premature equipment and bearing failure, which can be brought on by either one, as well as exposure to pollutants and moisture. Just as many issues might arise from excessive lubrication, including: Internal stress on bearings because too much lubrication pushes the rolling parts up against the outside bearing race making the bearing work harder and causing greater heat owing to increased internal friction.
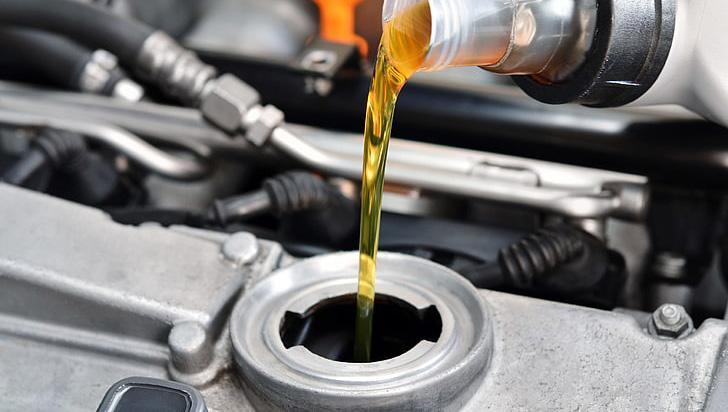
LUBRICANTS
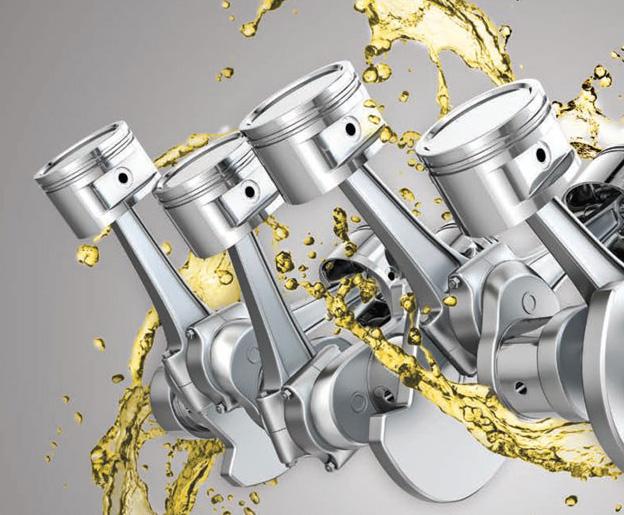
Exposure to Moisture and Contaminants: Industrial bearings can be used in some truly unsanitary conditions. Even adequately sealed grease nipples that are in between re-lubrication activities are vulnerable to contamination from a dirty work environment, dirty hands, or dirty instruments. Contaminants such dirt, sand, metal shavings, wood dust, and gravel may enter the lubrication stream if care is not taken to make sure this nipple is clean before adding lubricant. If this occurs, the bearing itself is in danger in addition to the lubricant's efficiency being impaired. Every time the bearing is manually oiled, there is a danger. Therefore, the lubrication's susceptibility to contamination increases with frequency. Risk of Damaged Seals: A standard grease gun is capable of dispensing grease at pressures of 10,000 psi or more. If the technician is not attentive, this pressure is more than sufficient to burst bearing seals. And if the grease is driven past the seal and into the windings of a motor, for instance, this may be devastating. Automatic lubrications
An automated lubrication system delivers the appropriate amount of oil to your equipment at the proper time and location, typically while the machine is in use. It takes the place of a traditional lubricating system and leads to longer equipment life, less wear, and lower maintenance costs. Automated lubrication advantages
The use of automated lubrication systems has various benefits. Cleanliness, less work, fewer waste, and enhanced environmental health and safety are a few of these. Reduced Wastage and Bearing Failure Risk: Relubrication intervals are determined by the operating circumstances that affect how quickly lubricant degrades, whereas relubrication amounts are determined by the physical space available in the bearing (speed, load, temperature, type of bearing, etc.) Each lubrication point may get the proper dosage of grease at the proper time via a singlepoint automated lubrication system. As a result, there is less grease waste and a lower chance of bearing failure. The lubricant will be subjected to severe deterioration and the bearing will experience lubricant starving conditions if relubrication intervals are extended beyond the specified limitations. The lubricant's characteristics would instead be renewed using shorter relubrication intervals and modified amounts. Cleanliness: Additionally, lubricant contamination will shorten bearing life and raise the possibility of failure. It might be difficult to prevent grease contamination in manual lubrication procedures. Processes must be spotless to prevent grease from becoming contaminated from the outside, and each lubrication point's grease fitting should have a cover. Additionally, every time a point needs to
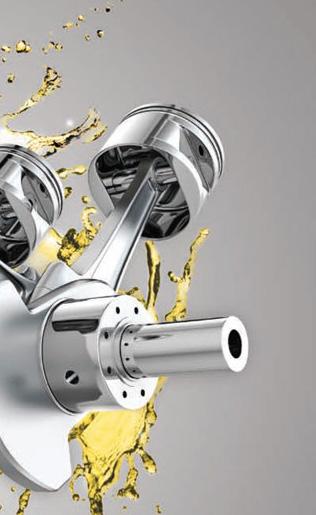
be relubricated, the absolute cleanest procedure must be used. Worker Savings: A machine may easily take over the straightforward process of pulling a lever on a grease gun to apply manual lubrication. The true question is whether you are utilising your competent maintenance technicians to their full potential. These individuals can oversee a lubrication programme by: • constantly enhancing the lubrication routes • implementation of a software for lubricant analysis • implementation of an oil reconditioning and pollution control programme • the implementation of a software to control leaks Remember that while installing automatic lubrication systems can relieve employees of time-consuming fundamental duties so they can contribute more value, it cannot completely replace employees who are able to provide this level of value. Safety and Environmental Health: Relubrication practices done incorrectly can have a big effect on the environment. Reconsider the estimates for the grease waste from the preceding case. Now attempt to calculate the environmental effect of this garbage. Naturally, it depends on the disposal methods you use at your facilities, but in general, less garbage is better for the environment. The possible influence on your staff should therefore be taken into account, as well as areas that are challenging or even dangerous to access. Another situation where automated lubrication systems are beneficial is this one. Disadvantages of Automatic Lubrication System
Cost of Investments: Undoubtedly, installing an automated lubrication system involves some financial outlay. The secret is to select the appropriate solution based on the needs and application's criticality in order to optimise the return on that investment. The typical methods range from simple, low-cost single-point automated lubricators to extremely sophisticated centralised systems with a number of choices for online monitoring. Your criticality analysis will play a large part in determining which choice is ideal for your application. Incorrect Lubricant Choice: The lubricant selection must come first in any lubrication programme as a fundamental need. After all, it is the lubrication that is applied, not the delivery mechanism, that lubricates. To guarantee superior overall performance, the lubricant and the automated lubrication mechanism must complement one another. It goes without saying that not all lubricants are appropriate for use with all automatic lubrication systems, and how a particular lubrication system affects the structure of the lubricant depends on its technology. As a result, while installing an automated lubrication system, factors like oil separation and pumpability must be considered. Additionally, relubrication intervals need to be set up such that the lubricant doesn't remain fixed inside the lubrication ducts, especially when exposed to high temperatures that might hasten premature deterioration. The effectiveness and related advantages of adopting an autonomous lubrication system may be impacted by a failure to comprehend and address these challenges. Inadequate Inspections: Even though the system has an automated lubricating device, it still has to be inspected. An automated system will produce its best outcomes with regular examinations. Additionally, an inspection can assist to discover installation problems (broken fittings, leaking or clogged pipes, lubricators not distributing lubrication at the proper rate, etc.) and indicate when lubricants need to be changed or refilled. Additionally, lubrication routes need to be updated, and manual lubrication jobs need to be switched out for inspection jobs at regular intervals. Although inspection frequency is lower than that needed for manual relubrication, it still has to be scheduled. Appropriate for Any Application: There are many different types of automatic lubrication systems, each with its own advantages and application areas, including single-line parallel, series progressive, dual
www.constructionmirror.com
LUBRICANTS
line, and multi-line. Due to this broad range, an automated lubrication system may often be used to lubricate any application. Reduced Machine Downtime: The key to increasing your total productivity is to prevent a halt in your installations. Automatic lubrication systems do not need to be shut down in order to add extra oil, in contrast to manual lubrication. While the lubrication system takes care of delivering the proper amount of oil for effective lubrication, lock-out and tag-out operations may be avoided and the machines can continue to operate. Your labor- and downtime are dramatically reduced as a result of automated lubrication. The key to increasing your total productivity is to prevent a halt in your installations. Automatic lubrication systems do not need to be shut down in order to add extra oil, in contrast to manual lubrication. While the lubrication system takes care of delivering the proper amount of oil for effective lubrication, lock-out and tag-out operations may be avoided and the machines can continue to operate. Your labor- and downtime are dramatically reduced as a result of automated lubrication. Construction Lubricant Market
According to Quince Market Insights, the global market for construction lubricants under COVID-19 is expected to reach USD 6209.65 million in 2021 and show a CAGR of 3.65% by 2030. The mineral oil and synthetic oil segments of the global construction lubricants market are based on base oil. Since mineral oil is widely accessible and inexpensive, it is anticipated that it will continue to dominate the construction lubricants market throughout the projection period. Despite having certain advantages over mineral oil-based lubricants, synthetic oil-based lubricants have a greater viscosity index, better chemical resistance, and enhanced shear stability and drain intervals. The market is divided into Excavators, Loaders, Crawler, Dozers, Motor Graders, Material Handling Equipment, and Heavy Construction Vehicles based on the kind of equipment. Portable and small machinery, which are becoming more and more popular, have been introduced to the construction industry. The market is dominated by motor graders, and this sector is rapidly expanding. Smaller gears and hydraulic machinery, together with longer replacement intervals, have led to a decrease in lubricant use in the construction sector. Due to underlying reasons like urbanisation and the global economic recovery, the construction sector will experience tremendous expansion in the upcoming years. It is anticipated that the use of construction lubricants would increase as a result of the exceptional rise in the worldwide construction sector. Infrastructure development is receiving more attention in both established and emerging countries, opening up attractive prospects for producers of construction equipment and perhaps expanding the market for construction lubricants. According to estimates, the demand for construction lubricants is supported by the growth of OEMs for construction equipment and machinery throughout the major areas. Strong investments in the sector are anticipated to be fueled by an increased focus on performance optimization of construction equipment. As need for high-quality speciality solutions to support advanced sorts of construction equipment & machinery gathers steam, this will result in a significant demand for construction lubricants. Indian Oil Corporation said in April 2022 that it will spend close to Rs 840 crores to increase its POL (Petroleum, Oil, and Lubricant) storage capabilities, including by building a new facility in the Northeast. By 2030, the business wants to increase its POL capacity from the current 3,160 Thousand Metric Tonnes Per Annum (TMTPA) to 5,530 TMTPA. CM
C ONSTRUCTION MIRROR
FOLLOW US ON: