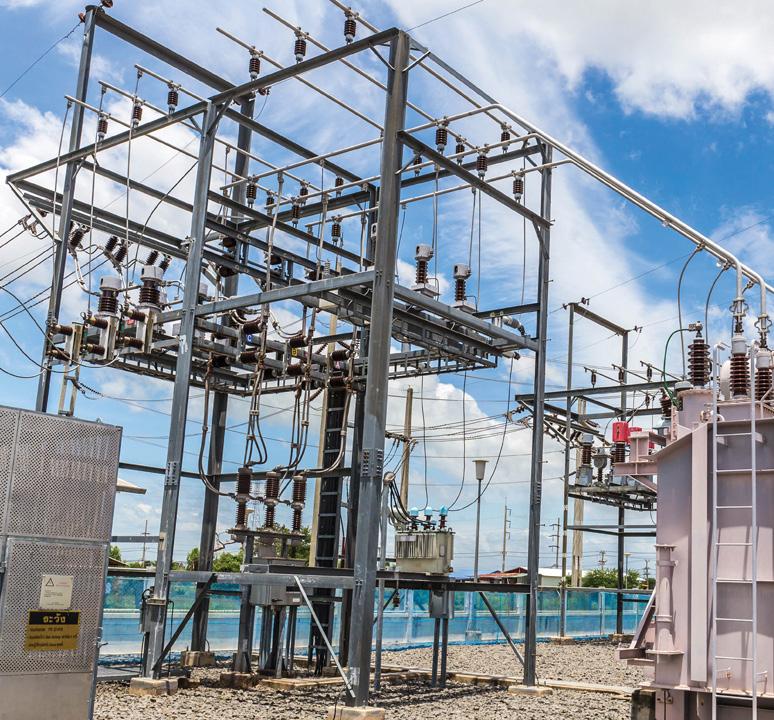
26 minute read
Condition Monitoring and Diagnosis of Power Transformers
Power Power TransformersTransformers

Advertisement
Dr L Ashok Kumar Professor, Department of Electrical & Electronics Engineering PSG College of Technology, Coimbatore askipsg@gmail.com
I. NTRODUCTION Power transformers are important and expensive equipment in electric energy networks. The majority of these devices have been in service for many years under different environmental, electrical, and mechanical conditions. In addition to the costs associated with equipment repair or replacement, the capital loss of an accidental power transformer outage is often counted in million dollars for output loss only. Because of this economic motivation, on- line monitoring and diagnosis (M&D) systems are of benefit to predict fault conditions and maintenance of the high voltage transformers. The selection of the monitoring functions is determined mainly by two goals, the faults must be promptly recognized, so that the operator can avoid critical conditions and the maintenance work is carried out only, if the condition of the plant requires it. The processing of the measured values represents a further aspect. Monitoring is a component of the service concept of the manufacturer. As direct expectation to a diagnostic system, the following terms are important: • extension of the remaining useful life of the transformer
• improvement of loading possibility of the transformer • higher availability and service reliability • condition-based maintenance and repair • prevention of loss and destruction Diagnosis contains interpretation of data to determine the current condition of a transformer. The diagnostic task has an important influence on the overall maintenance cost as well as on reliability and availability. The use of advanced technologies has the potential to greatly reduce the time and increase the accuracy of transformer diagnostics. There are many different techniques for diagnostic purposes, such as: Expert Systems, Case-Based Reasoning (CBR), Model-Based Reasoning (MBR), Artificial Neural Network (ANN), Fuzzy Logic, Knowledge-Based Systems and Genetic Algorithm. All the technologies have their advantages and disadvantages. In most cases they cannot work alone to solve the diagnostic problems and have to complement each other to form an integrated solution. Figure 1 shows the block diagram of M&D system for power transformers.
Power Transformers

Fig. 1. Block diagram of monitoring and diagnosis system for power transformers II. ACTUAL SITUATION A transformer consists of several independently working components. These components are windings and cores as electric and magnetic active parts in which voltage is induced and magnetic flux is guided. Additionally several bushings, insulating oil and tank, tap-changers and coolers are required. A survey of the age structure of transformers from a large German utility clearly shows in Figure 2 that the transformer majority are approaching or exceeding the age of 25-35 years. This situation is more or less similar in many industrialized countries.
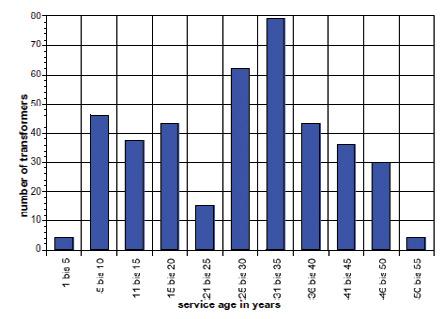
Fig. 2. Age structure of transformers Regarding the information of Fig. 2 the main point in monitoring and diagnosis is the increase of the failure rate with increasing years of service. Fig. 4 shows the typically curve whereby a punctual revision causes a shift of the failure rate of approximately 5 years.
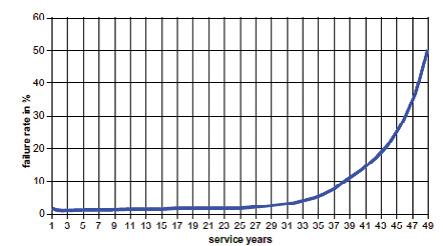
Fig. 3. Example of failure rate as a function of transformer age III. FAILURE CAUSES The premature and unexpected failures in transformers can be caused through the following stresses: • electrical • electromagnetic • dielectric • thermal • chemical stresses Statistics show that the most frequent causes followed by long outage damages are in tap changer, active component and in bushings, according table I. TABLE I. FAILURE CAUSES OF POWER TRANSFORMERS WITH DOWN-TIMES MORE THAN 1 DAY.
Tap changer
coil + core 40 %
35 %
bushings
vessel 14 %
6 %
accessories 5 %
A. Electrical Causes Inside the transformers, insulation systems (made of insulating oil and cellulose), can be locally overstressed, whereby the aging process of the insulating system will be accelerated, leading to acid generation and pollution in the oil, an increase in the water content, gas and mud formation. As a consequence, the breakdown voltage will decrease. The increase in water can lead to an acceleration of the depolymerisation of the cellulose. Paper aging process, depends primarily on temperature and water content 5. The existence of oxygen will also remarkably increase the rate by as much as 2.5 to 10 times normal. Fig. 4 depicts the relation between relative depolymerisation velocity and the water content and temperature.
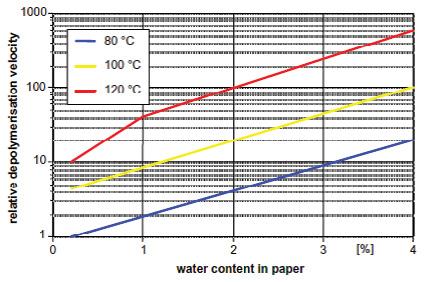
Fig. 4. Relative depolymerisation velocity at different water content and temperature
B. Electromagnetic Causes High forces acting on the coil, which can lead to a deformation, can be caused e.g. by a short-circuit in the network. These deformations can lead to the insulation paper breaking in particular with aged papers. The consequence is first the generation of partial discharge and finally the total breakdown. C. Dielectric Causes The quality of the paper insulation in a transformer depends on the polymerization degree (number of the glucose rings and chains) of the paper. During aging process, the chains are up-smelled consisting of glucose rings and develop water, gases (CO, CO2), groups of carboxyl’s (organic acids). The ageing speed depends thereby on different parameters such as temperature, water content, oxygen content, number and kind of temperature cycles and material properties. D. Thermal Causes As a thermal cause, the losses result from the demagnetization of the core (eddy current losses) and the Ohm's resistance of the coil inevitably. Heating up and cooling processes of the insulation with high temperature gradient, represent additional load of the insulation system which influences the life span of the transformer insulation. E. Chemical Causes Organic acids are developed as aging by-products of the solid and liquid insulation, which attack in particular the paper insulation and accelerates the aging. In addition metals such as copper, iron, aluminum and zinc which exist in each transformer are catalytic, and have an additional accelerating effect on the aging processes of the insulation. IV. TOOLS FOR MONITORING AND DIAGNOSIS Various tools and methods for monitoring and diagnosis of high voltage power transformers are actually available. Basically, they can be divided into: • traditional diagnostic methods that have been used for many years • new methods that range from methods that are starting to be used and • methods that are still at the research stage Some examples of traditional methods are: Dissolved Gas Analysis (DGA), Insulating oil quality, Power factor testing, winding resistance, and thermograph. New methods include online PD testing, recovery voltage measurement, tap changer monitoring, internal temperature measurement, on-line power factor measurement, dielectric spectroscopy, and winding deformation detection. Some of these mentioned methods are implemented using software systems, which gives more definite indications of transformer problems than conventional analysis. The use of software can improve the reliability and provide facilities to analyze the test data. It can also be used to extract information and knowledge that is not available and not visible from the data directly using advanced information technology methods such as Data Mining. The advancement in artificial intelligent (AI) modeling techniques has enabled power engineers and researchers to develop useful artificial intelligent software for diagnosing transformer faults. Artificial neural network or ANN approaches are used for DGA method. Fuzzy logic concept is another AI technique in power system associated with the uncertainty of changing power operational condition, numerous power system configurations, imprecise information input by human operators, disturbances and faults. Expert systems have been proposed to manage knowledge processing. An expert system is a computer program that performs a complex decision making task within a particular narrow problem domain that is normally done by a human expert. It is based on the idea of taking the knowledge from a specialist and expressing it in an appropriate representation to exploit the knowledge in the same way as the human expert does and above all with the same result. The use of expert systems for transformer diagnosis offers the potential of reducing the overhead required by substations for the maintenance of transformers. V. TRANSFORMER CONDITION MONITORING Harmonics within distribution network degrade network performances as well as power quality, including transformer heating. Condition monitoring avoids unwanted risk to transformers. Condition monitoring is part of condition-based maintenance (predictive maintenance). Condition based maintenance analyses the tendency of the equipment as the base of decisions. Condition based maintenance reduces maintenance and workforce and increases the equipment capabilities. Benefits of this method include maintenance cost reduction; operation interruption avoidance; service quality and safety increments; and the transformer lifetime prediction. Some existing condition monitoring methods require some parameters to decide transformer performances. Method in requires gas dissolved analysis, partial discharge analysis, clamping pressure transformer turns and health index. However, in reality, those parameters are difficult to measure as measurement tools are limited and there are too many transformers to measure periodically. Online condition monitoring and analysis in requires insulating oil and transformer turns temperatures. Condition monitoring through CAD simulation is not suitable for PLN as it requires data of moisture content, load vibration, and clamping pressure. Method discussed in needs gas chromatography device. Online measurement which
www.electricalmirror.net
Power Transformers
requires equipment to be integrated with internet is not yet supported, although some technologies are available. This paper proposes a simple method that is suitable for PLN network by using existing monthly transformer load, load profile data and trend analysis of the available data and by applying priority of evaluation based on the potential risk causes. Measurement data is analyzed to extract condition monitoring parameters. As results, additional measurement data is needed to obtain better accuracy. For increase of reliability and achievement of optimum operative management it is necessary to monitor power transformer conditions as it enables to register the various influences for the service term. The automatic estimation of these data allows to find out defects at an early stage of development and to repair on the condition. The reliability of operation of distribution networks can be increased by using automatic monitoring systems for transformers – not only for power transformers but also for distribution transformers. At present, operators do not have either much measured data or advanced information on transformer substations for maintenance and control. This paper describes an advanced monitoring system for distribution and step-up transformers, has low investment and operation costs and is easy to install and use. Experience in Russia has shown that the commercial infrastructure can successfully be used in monitoring of transformer substations. Since 2006 Federal Grid Company introduces high-voltage monitoring system “R-1500” and now this system is just integrated part of full-sized “TDM System” manufactured by "Vibrocenter Company" on energy utility and installed during 2006 year. VI. SYSTEM DESCRIPTION The TDM system is used for continuous monitoring and analysis of power transformers technical condition. It can analyze the parameters of conditions of basic transformer subsystems and form complex conclusion of transformer conditions. TDM system can both estimate technical condition and analyze condition of follow transformer subsystems and elements: • Oil-filled bushings of transformer. Within the control of bushings condition process conduction current, calculation of dissipation factor and capacitive "C1" are measured. • Changing geometry of transformer winding due to on-line computation of parameter "Zk" after every anomalous influence upon transformer winding. • LTC condition under effort on tank temperature, on acoustic partial discharges, on vibration in commutation process, consumed power in drive motor of LTC.
• The temperature conditions control in transformer work and cooling system control in transformer. The operating conditions analysis of oil pumps and cooling system fans. • The registration of overstrains and impulse of current influence on transformer windings, control of the work of transformer protective relay. • Transformer conduction parameters, which are determinate by other diagnostic systems, for example, oil humidity. On particular diagnostic basis we have a possibility of integral analysis of transformer conditions, and a possibility of a forecast of condition’s and defect’s advances. The possibility of trend defects development analysis and remaining life detection is the system’s important advantage. All the fundamental equipment of monitoring system is located next to transformer. It is assembled in a protective box and consists of five fundamental modules as it’s shown on Fig.1: • Module 0. It is a central calculating system module, which has interface with diagnostic subsystems and upper level system SCADA. Secondary devices of temperature transformer conditions control system and oil humidity are located here. • Module 1. The transformer cooling direction system and control of technical condition of oil-pumps and ventilators are ready-mounted in this module. • Module 2. Surge-voltage recorder and pulse current influence on transformer windings. • Module 3. The control transformer inputs system on conduction current (like system R1500 [1, 2]) is ready- mounted in this module. • Module 4. Control of isolation condition by partial discharges level in transformer. • Module 5. The control technical conditions transformer LTC is ready-mounted in this module. • Module 6. Search of partial discharges origin place in transformer tank by acoustic sensors. • Module 7. Vibration control in equipment.

Fig. 5. Main system diagram
VII. TDM Technical and functional possibilities A. The TDM monitoring system basics: • Efficient assessment of technical transformer conditions «on-line», exposure of condition defects. • Forming and delivery of recommendations about transformer operation, necessity and repair work dates. • The management of transformer cooling system and transformer LTC. • Registration of current information about normal and alert transformer condition. • Integration of transformer monitoring system in supervisory control power system (SCADA). • Diagnostic transformer subsystems: • Influence analysis of working regimes on condition of isolation windings, detection of output capability and calculation of transformer lifetime. • Condition of oil-filled bushing diagnostic on the basis of temporary and temperature dependences of conduction current and bushings dissipation factor. • Analysis of windings deformation origin on the basis of on- line computation parameter "Zk" after electrodynamics influences on transformer windings. • Detection of LTC technical condition on the basis of vibration and energy parameters analysis, which are registered in switching process. • Direction and analysis of technical condition of cooling system elements on parameters of starting and working conditions of electric motors. • Use of moisture sensor supplementary information in diagnostics. B. Transformer parameters monitored by TDM system • Cooling transformer system. • Oil temperature in high transformer tank point. • Environment temperature and humidity. • Condition of cooling system elements (switching on– off of pumps and fans). • Cooling system working regime – by user / automatic. • Transformer winding condition. • Maximum rated temperature of transformer winding. • Winding form deformation after electrodynamics influences. • Load and operation parameters. • Current of 3 transformer phases, high voltage side and low voltage side.
• Voltages of three phases, HV side and LV side. They are determinate by bushings conduction current. • Transformer oil-filled bushings condition. • Dissipation factor control of bushings and capacity value "C1". • Nitrogen pressure in bushings, high and lower alarms. • Condition and working regime of transformers LTC. • Temperature of LTC tank, compared to transformer tank temperature. • Vibration control of drive condition and arc presence in contactor. • Partial discharges acoustic control in tank of LTC. • Location of LTC contactor. • Signals from the most responsible protection relay and transformer blocking. • Condition of gas relay. • Pressure in bushings. C. Sensors included with standard TDM monitoring system: • Sensors DB-1 (DB-2) are used for registration of oil-filled bushings conduction currents. • Vibration sensor and acoustic partial discharges sensor for process registration in LTC, which are combined in one flame. • Temperature sensor for stationary assemble in transformer tank surface and LTC. • Humidity and environment of temperature sensors, which are combined in one flame. • Measuring current transformer (they are selected by monitoring object parameters) for current registration in one transformer phase, current electric motor LTC, current electric motor cooling system. • Capacitive sensors for LV transformer side (only for 6-10 kV), which are necessary for control of geometric winding sizes (by using parameter "Zk"). D. Complementary TDM system possibilities Monitoring system TDM is armed at diagnostic functions implementation and intended for transformer technical condition quick-look log. That’s why it could be a part of more difficult system, which registers quality and è quantity of electricity, and has broader functions of registration and secure and alert conditions analyzers in power system unit. Built-in monitoring system diagnostic functions can be extended by complementary subsystems: • Partial discharges registration and analysis in inputs and in transformer.
Power Transformers
• Analysis of gases solicited in oil. You can use HYDRAN device or other devices for implementing these functions. • Connection of similar signals from other systems and control and diagnostic devices, the structure of which is defined at every specific installation system. The real technical system configuration and its functional features are determined upon agreement with the customer. VIII. MONITORING PROCEDURES In contrast to laboratory measurements, on-site measurement is disturbed by extreme and mostly influence- able conditions. In particular, within the range of the high voltage areas, within which the transformers work, precise measurements are more difficult because of the interference of electrical and magnetic fields. On-line procedures make it possible to detect failures at any time and also during the normal operation of the transformer. Furthermore on-line measurements offer the advantage that measuring data can be pursued during a longer period with almost same operating conditions. Thus, slow changes can be detected and a warning message or command to immediate disconnection can take place, if given limit values are crossed . A. Chemical Procedures With the help of chemical procedures, some failures, in the transformer insulation can be determined. One of the standard investigations is the so called “gas in oil analysis (DGA)”, with which a sample of the insulating liquid is taken from the transformer and examined. This sample, after a vacuum extraction undergoes an analysis by gas chromatography to reveal the dissolved gases. The interpretation of different quotients of low-molecular hydrocarbon connections serves thereby to the determination of the failure. As an evaluation criterion, in particular, the triangular method after Duval as well as the MSS procedure after Mueller, Schliesing and Soldner are used. The disadvantage of these procedures is the fact that they allow only one integral evaluation to the insulation. In addition, sampling and the following treatment of the sample can affect the measurement. Further procedures are the furan analysis (HPLC) and the analysis of free gases collected in Buchholz relay. While with the furan analysis, vital information on the quality of the solid insulation is obtained, the analysis of the collected free gases in Buchholz relay provides information about the range of an available failure. The Buchholz relay indicates only gas amounts developed since the last exhaust, however not the history of the gas emergence. So long lasting, but nevertheless low energy failures e.g. PD lead to a continuous gas production, while failures with high energy content like local overheating generate high gas rates within a short period. In order to make a better evaluation of the available failure, it is meaningfully to determine the gas rate. This statement makes the electronic Buchholz relay possible, which is to serve as an extension for the Buchholz relay, without limiting its function. This system determines thereby the history of the gas emergence, which, during simultaneous recording of the operating conditions, permits additional conclusions on an available failure. B. Electrical Procedures While the chemical give a cumulative statement about the period passed since the last analysis, the electrical procedures allow a statement about the current condition of the transformer. The main electrical procedures are the partial discharge (PD) measurement) and off-line the transfer function measurement. Partial discharges are in most cases determined chemically during gas in oil analysis, since they show up typically and strongly increased hydrogen content. A continuous measurement of PD during the operation is not used at present yet, since the narrow-band measurement of the partial discharge signals on site is expenditure and in addition, no localization of failure is possible. A diagnostic system was therefore developed which permits from the wide-band measurement of partial discharge signals a determination of the PD source and a determination of the apparent charge converted at the defective equipment. The diagnostic procedure is based on the evaluation of the signal deformation of PD pulses within the transformer by mathematical algorithms and permits by the determination of PD location as well as the charge quantity a qualified analysis of the failure. For this procedure, it is necessary to note the high frequency partial discharge signals both at the bushing and at the neutral point. In these data both the current pulse caused by the PD and the deformation, experienced by this impulse during its transmission trough the turns of the transformer are contained. If this deformation is known, then it can be reckoned back from the ends of the windings of measured signals on different original places. These computations are accomplished both from the high voltage and the neutral point side. The place where the signals calculated for the different sections of the windings are identical is the true location of the PD source. A further advantage of this procedure is that the calculated signal corresponds to the actual partial discharge signal. It is thus possible to estimate the charge contents of the PD at its origin. Defects can also be recognized by the measurement of the transfer function of the individual transformer coils such as turn short-circuits or deformations. The current measurement is compared with a "finger print", which must be determined first as reference. Deviations between the reference transfer function and the current transfer function indicates then a failure. Whereby, with the bandwidth of the transfer function
measurement, the sensitivity of the method can be increased. Such transfer function measurements can be accomplished on and offline, whereby with offline measurements, the impulse response can be determined by different procedures and with online measurement, a switching impulse can be used. C. Dielectric Procedures The dielectric methods are used as offline procedure and permit a more exact view of the insulating system, if an extended statement about their condition is required. Three procedures are used and well described in the literature: • Recovery Voltage Measurement (RVM) • Polarization and Depolarization Current (PDC) • Frequency Dielectric Response (FDS) D. Further Procedures The overload capacity of a transformer is limited among other things by reaching the permissible maximum temperatures of coil and oil. For the determination of the hot spot temperature different procedures can be used using a thermal model of the transformer and some temperature measurements on accessible points of the transformer. IX. CONCLUSIONS • Monitoring and diagnosis systems for power transformers are available. • The failure sources are well known and also the parameter which strongly influence the ageing of the insulation system. • The procedures for monitoring the various effects are mainly based on chemical, electrical and dielectric measurements and can be recorded. • The crucial point, which needs more statistical data, is the evaluation of the failure risk and the estimation of the residual life time. But this will be improved in future by using more and more monitoring and diagnosis systems on power transformers and by increasing the statistical data basis. X. REFERENCES [1] CIGRE-WG 12-05: „An international survey on failures in large power transformers in service“, Electra No.88 (1983), pp. 21-48. [2] M. Stach,: „Betriebswirtschaftliche Gesichtspunkte im Asset- Management im Zeitalter der Fusion“, Micafil Symposium, 20- 21.März 2002, Stuttgart. [3] M. Wang, A. J. Vandermaar, “Review of condition assessment of power transformers in service”, IEEE Electrical Insulation Magazine, vol. 18, No. 6, pp. 12-25, Nov/Dec 2002. [4] Bengtsson, C., Persson, J-O., Svenson, M.: „Replacement and Refurbishment Strategies for Transformer Populations,“, CIGRE 2001 Colloquium, Dublin SC 12.20. [5] “Guide for the Sampling of Gases and Oil from Oil-Filled Electrical Equipment and for the Analysis of Free and Dissolved Gases,” IEC Publication 60567, 1992. [6] T. Noonan, “Power transformer on-site condition assessment testing,” presented at the International Council on Large Electric Systems (CIGRÉ), Paris, France, 2000. [7] Asghar Akbari, et al.,Transfer Function-Based Partial Discharge Localization in Power Transformers: A Feasibility Study, EEE Electrical Insulation Magazine, 18, 2002. [8] R.S. Brooks , G.S. Urbani, “Using the recovery voltage method to evaluate aging in oil-paper insulation,” in Proc. IEEE Int. Conf. Conduction and Breakdown in Solid Dielectrics., Vasteras, Sweden, pp. 93-97, 1998. [9] Han, Y.; Song, Y.H., “Condition monitoring techniques for electrical equipment-a literature survey”, IEEE Transactions on Power Delivery, Volume: 18, Issue: 1, Pages:4 - 13, Jan 2003. [10] I. Fofana, H. Borsi, E. Gockenbach and M. Farzaneh “Aging of transformer insulating materials under selective conditions”, European Transactions on Electric Power, 2006; 16:1–21 EM
MAIN AuTHOR
Dr. L. Ashok Kumar was a Postdoctoral Research Fellow from San Diego State University, California. He was selected among seven scientists in India for the BHAVAN Fellowship from the Indo-US Science and Technology Forum and also, he received SYST Fellowship from DST, Govt. of India. He has 3 years of industrial experience and 20 years of academic and research experience. He has published 173 technical papers in International and National journals and presented 167 papers in National and International Conferences. He has completed 26 Government of India funded projects worth about 15 Crores and currently 7 projects are in progress worth about 7 Crores.
www.electricalmirror.net

Q. Please tell us about the acquisition of Altanova Group by ESCO Technologies. In 2021, ESCO Technologies acquired the ALTANOVA Group to expand its portfolio and global reach. Hence the three ALTANOVA Group companies, ISA, Techimp & intelliSAW, are now part of Utility Solutions Group together with Doble, Morgan Schaffer, Manta, Vanguard & Phenix. This acquisition makes us one of the largest companies in Testing, Measuring & Monitoring Solutions. We now have seven manufacturing facilities and many local offices spread across different parts of the world. This merger hence brings us closer to our customers, and it will help us serve them better. Q. How would Altanova Group benefit from the recent merger with Doble Engineering Company? It is a win-win situation for both. Doble brand is very strong in the US and Canada, whereas the ALTANOVA brand is very strong in the rest of the world. Doble is a hundred (100) year old company known worldwide for its strong database & wide knowledge, whereas ALTANOVA Group has established itself as the fastest growing & largest selling brand in the rest of the world. We are now better positioned to offer our customers a wide range of products and complete monitoring solutions. We are also more strengthened to offer niche services to the utilities and industries. Hence it is obvious that the new brand ALTANOVA Group (a Doble Company) will take care of the complete business portfolio in the rest of the world. In India, due to this merger, we have now two offices based in Noida & Vadodara. Our team size is also bigger, and hence we are now in a better position to serve our customer’s requirements much faster. Q. What impact do current trends have on testing & monitoring solutions demand in India’s energy sector? The primary role of testing & monitoring products/solutions is to improve the quality and life cycle of the electrical assets. The Indian energy sector is maturing now, and the customer is becoming more & more quality conscious. Asset Managers are now exposed to the best of the technologies. Hence, to ensure the reliability of their systems, they look for more accurate testing equipment which gives them consistent test results. In this way, they can ensure the quality & efficiency of their power systems. Diagnostics are now used to help the O&M managers classify their asset conditions. This classification of their assets leads to condition-based maintenance planning instead of time-based. Q. What are the market’s challenges, particularly cost, technical advancement, and getting raw materials? Due to the prolonged pandemic situation, the supply chain of electronic components has been badly hit. The costs are
www.altanova-group.com
ew I erv T In
skyrocketing, and the availability is getting delayed. This shortage of components/raw materials affects the production schedule leading to delayed delivery. Q. How is Altanova contributing to India’s renewable energy growth? What products do you have for the renewable energy market? We contribute to the renewable sector’s growth by providing quality instruments and onsite services like Partial Discharge testing. Providing services to the Solar sector, in particular, is quite challenging as the testing can only be done during the night. I must thank my colleagues here that they are ready to perform these tests during the night so that the power generation is not affected during the day. Q. What role does R&D play in the advancement of your technology offerings? What have been some of the most significant developments in this regard? A good R&D team is the backbone of any good organisation. We have a very strong R&D team within the group. We shall continue to innovate new products & solutions and improve the existing products based on the customer’s feedback. Since the electricity network is moving towards digitisation, it is also important for the T&M products to effectively adapt to the changed scenario. We also believe that continuous online monitoring of electrical assets is important for future development; we continue to develop such solutions. For us, the voice of the customer is the guiding principle for future product & solution developments. Hence, we shall continue doing the same in future as well. I also believe that the T&M sector will see many changes in the coming years due to the pathbreaking innovations in Artificial Intelligence and IoT. We find that more and more T&M equipment is coming with the IEC-61850 communication protocol. To conclude, the R&D in the T&M sector will lead to increased system availability, lower cost of acquisition, enhanced system and personnel safety, and quick data availability. These developments will strengthen the O&M engineers with faster and efficient communication and additional tools to identify the health of their assets on a real-time basis. Q. How did the Altanova group fare in the year 2021? What are your ambitions and goals for the year 2022? Despite the current pandemic, I am happy to share that 2021 has been a very good year for us, and hence we believe that hopefully, the same shall continue in 2022. The credit goes to our formidable team, who goes all out to proactively support our customers and build a strong and long-lasting relationship with them. By team, I mean both our colleagues and Channel Partners. Our Channel Partner’s consistent performance and proactive business development efforts are the main reasons for our continuous growth. We also firmly believe that a happy customer is the most important reference in any business and hence we serve them accordingly. EM
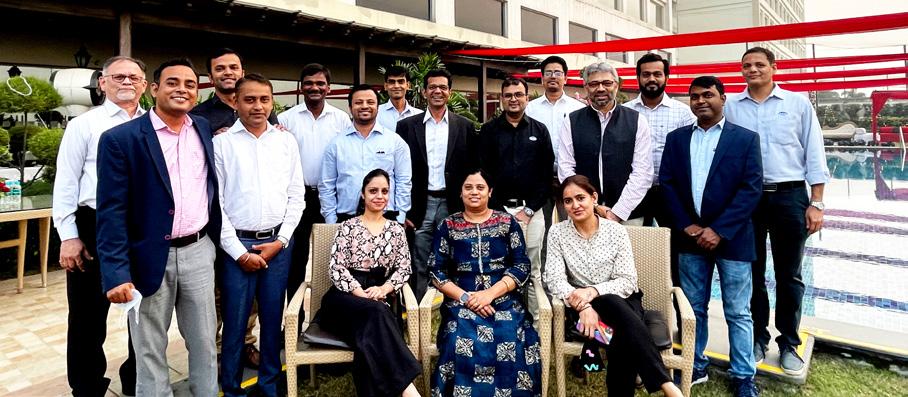
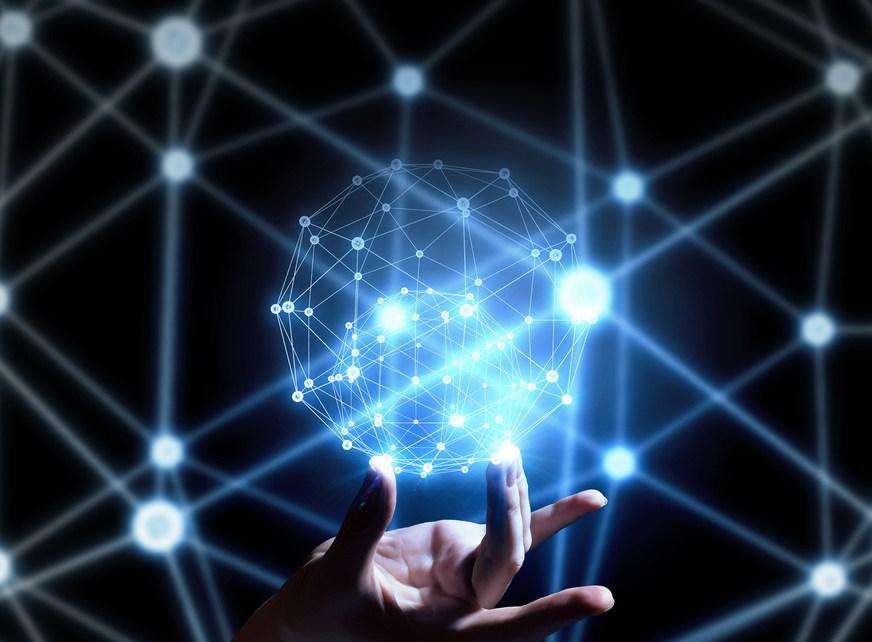
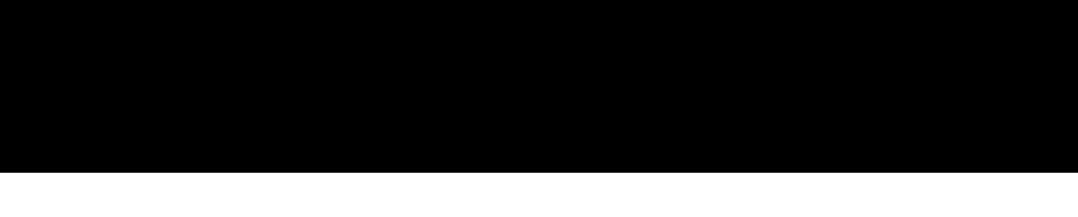