LAMINATED TIMBER PRODUCT OVERVIEWS
Sarah Hicks
Element5, Marketing & Communications
“Canadian-owned and operated mass timber fabricators have recently joined the mass timber market. With their introduction comes the opportunity to source mass timber products sustainably and locally, to manufacture high performance wood components and buildings.”
Collectively, the construction, maintenance, and demolition of the built environment is a leading source of the world’s carbon dioxide emissions. In the face of climate change, exponential population growth, and urban densification, it is imperative that society develops sustainable building solutions to meet the housing and infrastructure needs of a growing population without accelerating climate change. These goals cannot be achieved by doing things the way they have always been done. New products, systems, and ways of thinking must prevail. The need for a radical shift in the construction industry is, in part, fueling the mass timber revolution today.
The shift to more wood construction is not solely the result of environmental pressures; the uptake in wood use is also tied to the industrialization of the construction process.
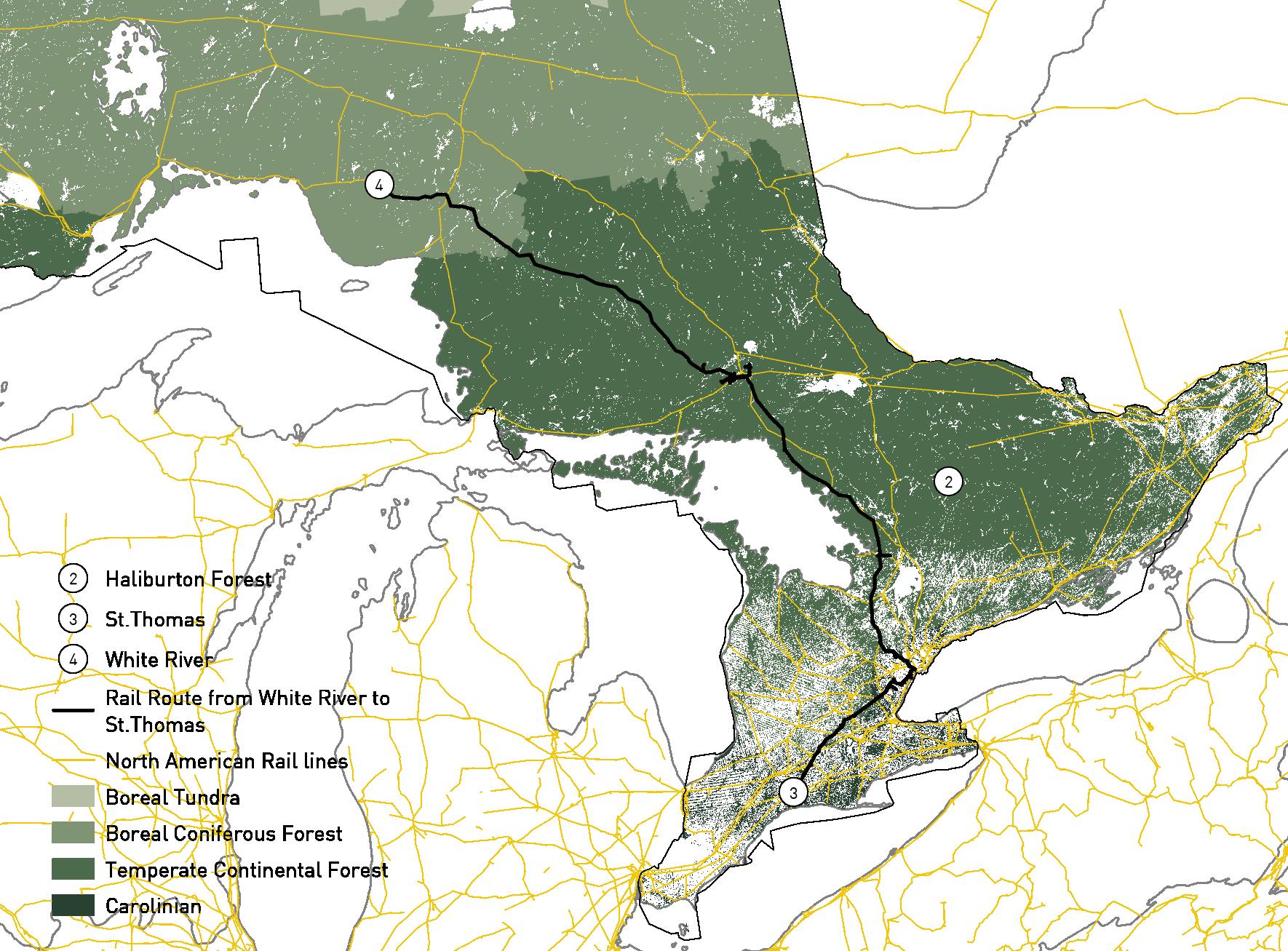
Industrialization in construction is, in essence, the growing shift from site-built developments to off-site manufacturing that is enabled by Building Information Modelling (BIM) and Computer Numerically Controlled (CNC) fabrication. Yes, mass timber is the most sustainable choice as a renewable, carbon sequestering resource, but it is also the material best suited to this new form of construction. A fully integrated suite of professional services and products offer a single point solution for the supply, design, and construction of mass timber buildings.
The significant gains that can now be made through offsite manufacturing, including just-intime delivery, are fuelled by BIM technology. BIM provides real-time visualization capabilities for an integrated schedule, enabling simultaneous monitoring of offsite and field activities,
empowering the project manager to carry out the construction schedule more effectively. The ability to integrate offsite and field construction allows a project team to work in ways that synchronize the progress of these operations. Site preparation, for example, can be done while the building components are being fabricated in the shop.
Asset information, such as specifications, part numbers, suppliers, and loading sequences, can be exchanged during this process. Panels and components are identified through a codification system that corresponds to the digital twin (BIM model). This enables accurate traceability of the panels and supports planning, logistics, and assembly activities, notably in the form of 4D modelling. This process provides an opportunity to make ongoing improvements by recording performance against planning and budget to
integrate lessons learned.
The role of the mass timber supplier is to ensure the constraints relative to the mass timber shell are thoroughly considered at all stages of the design and strategic decision-making process, from early design to assembly. In this way, the fabricator can help guide the project team toward improvements that can be realized at scale through a commitment to detailing out complexity in form and sequence, thus generating savings.
Canadian-owned and operated mass timber fabricators have recently joined the mass timber market. With their introduction comes the opportunity to source mass timber products sustainably and locally, to manufacture high performance wood components and buildings. More than just mass timber fabricators, these
Canadian companies are innovators producing advanced wood systems that will benefit the built environment through the adoption of sustainable mass timber construction.
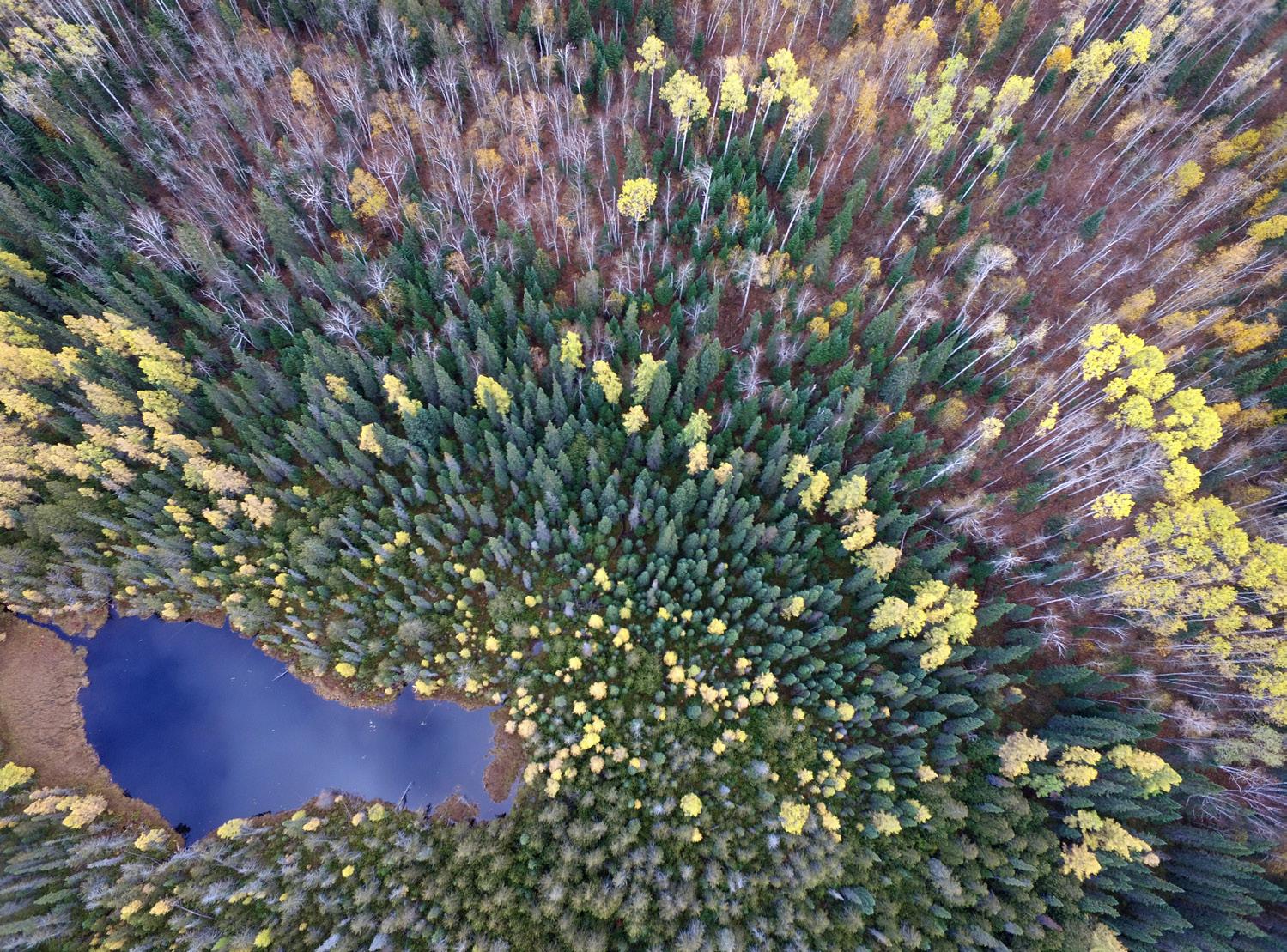
At Element5’s CLT factory in St. Thomas, Ontario, state-of-the-art, high capacity mass timber fabrication can produce approximately 50,000 m3 of CLT and glulam, with the ability to increase that output based on outside demand. CLT panels can reach dimensions of up to 16 m in length by 3.5 m in width and up to a maximum thickness of 380 mm. The number of plies available is based on 380 mm divided by ply thickness, with 3, 5 and 7-ply panels being the most common. Glulam can be pressed to create beams up to 250 mm wide by 16 m long and 1,500 mm deep. Lumber grading and sorting are completed by a lumber supplier. Lumber is then shipped to a factory where the material is received, inspected, labelled, and stored in
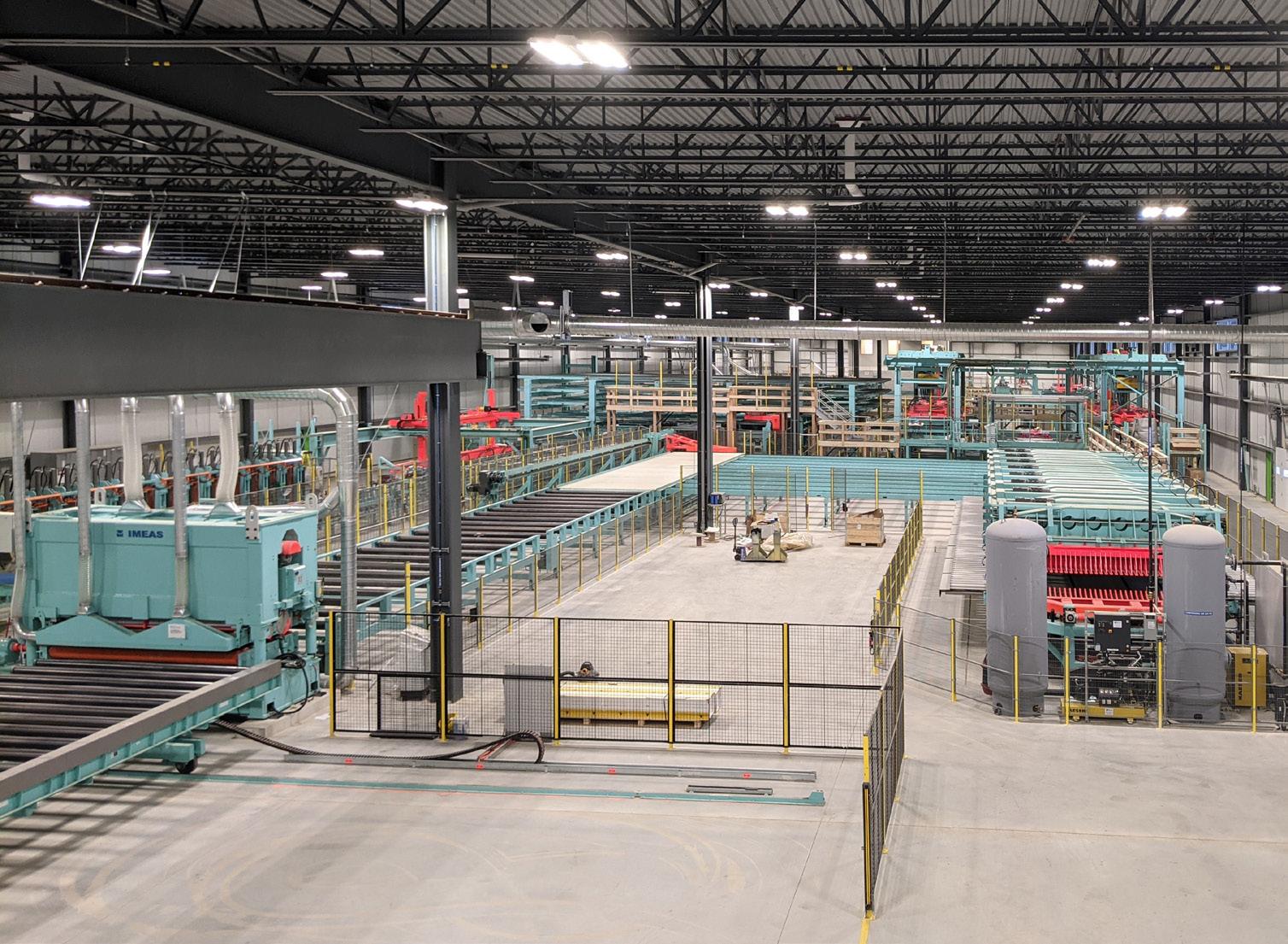
a conditioning building to maintain and set the humidity levels necessary for manufacturing. Lumber is planed on four sides prior to assembly into glulam or CLT. After assembly, the CLT panels are sanded on one surface; glulam members are planed on all four sides. Sanding capabilities are up to a maximum of 44,000 m3 per year.
The entire line is integrated under the X-Lam Manager, a PC-based master computer system developed by Ledinek Engineering that provides production management, production flow control and visualization, statistics, real-time information, and production analysis tools.
CNC milling is completed on a CMS 5-axis machining center. The overall machining envelope is 20 750 mm in length, 6000 mm in width and 1 300 mm in the vertical. Accuracy is 0.534 mm in the length axis, 0.165 mm in the width axis and 0.048 mm in the vertical axis.
Value-added CLT-based components include hollow-core floor and roof cassettes and CLT clip wall panels for maximum efficiency and quick assembly. The degree of prefabrication is determined through a collaborative assessment phase that leads to a design optimized for manufacturing and assembly (DfMA). The model successfully integrates architectural, structural, mechanical, and logistical constraints. Design and manufacturing are intrinsically linked in this modular mass timber construction.
DfMA represents a shift in the delivery model of the standard engineer-to-order procurement method. The process of adding value is front-loaded, with earlier decision-making and purchasing required. Design integration activities are defined at the outset of the project to understand constraints and boundaries. The integration takes place in a collaborative BIM environment where dimensional information can
be co-ordinated.
In the last decade, engineering innovation and the commercial development of mass timber components has improved the construction industry’s ability to respond to the challenges of climate change, urban intensification, skilled labour shortages, demanding project timelines, and economic constraints. These outcomes require a level of efficiency and co-ordination that can only be achieved through computer modelling and offsite manufacturing, an area where the wood sector is already operating and positioned to grow.
The future of construction is high-performance buildings that pay attention to embodied carbon and operational impact while striving to achieve maximum social and economic value. The result is the mass timber revolution we are witnessing today.