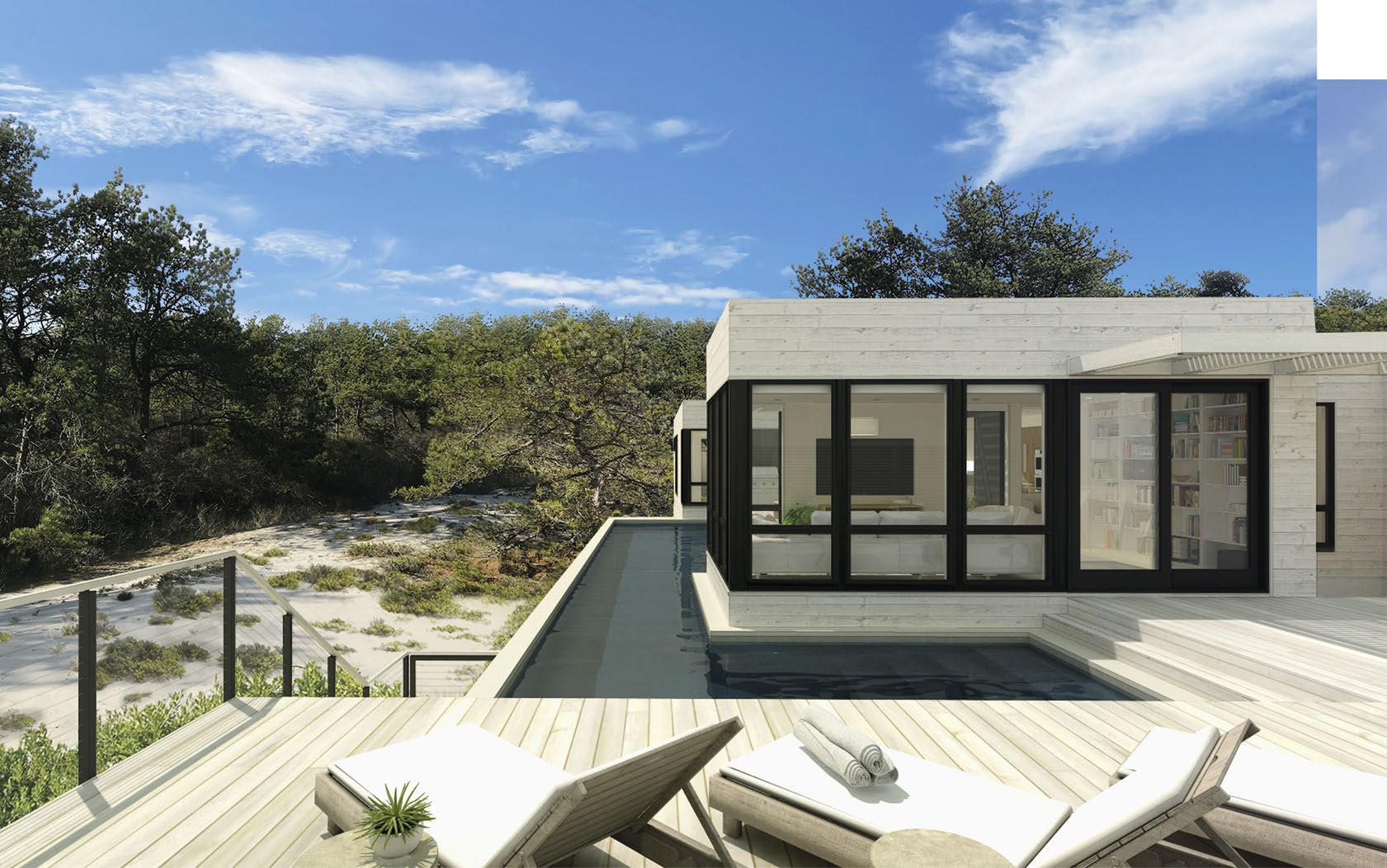
4 minute read
Design
Mod Squad
High-end modular homes and sleek, eco-friendly modular pools are trending. A look at what makes them unique and desirable. by Shaun Tolson
A pool wraps around this modular home’s side to create a sense of swimming among the pines.
INSPIRATIONS
This cedar slat and cement modular beach house was designed to maximize privacy. IT’S BEEN almost two decades since Dwell magazine issued a contest to 16 architects, challenging them to design a modern, prefabricated home for $200,000. In many ways, that design competition permanently positioned upscale, modular homes on the consumer’s radar. Ironically, the concept is one that had been etched into the minds of residential architects for the better part of a century.
“Ever since the dawn of the factory and assembly lines as we know them, there have been architects who have been trying to execute domestic structures utilizing that delivery method,” says Chris Krager, the founding principal at MA Modular.
“It’s nothing new,” adds Joseph Tanney, founding partner at Resolution: 4 Architecture, a Manhattanbased firm that participated in Dwell magazine’s competition back in 2003. “Architects have considered it the holy grail of modernism for quite some time.” But modular homes aren’t just modern in design. There’s a world of possibility in a wide range of architectural styles, from cabins to bungalows to ranch-style homes.
Compared to traditional homes, modular designs are lower in cost. The average modular residence designed by Resolution: 4 Architecture, for example, costs about $500 per square foot to build. When a traditional homebuilder quoted the same project, they estimated the job at just under $900 per square foot. As Tanney explains, the value of modular design and construction is predicated upon how and where the majority of the house is built. “About 80 percent of the home gets built in the factory,” he says. “And it’s a lot cheaper to build something in a controlled environment.” However, Krager points out that the savings clients enjoy up front on a modular home’s design and construction are typically paid back (at least partially) for what it costs to transport those modular pieces to a home site. Additionally, modular parts can only be as big as what can be shipped legally (and safely) on a flatbed truck.
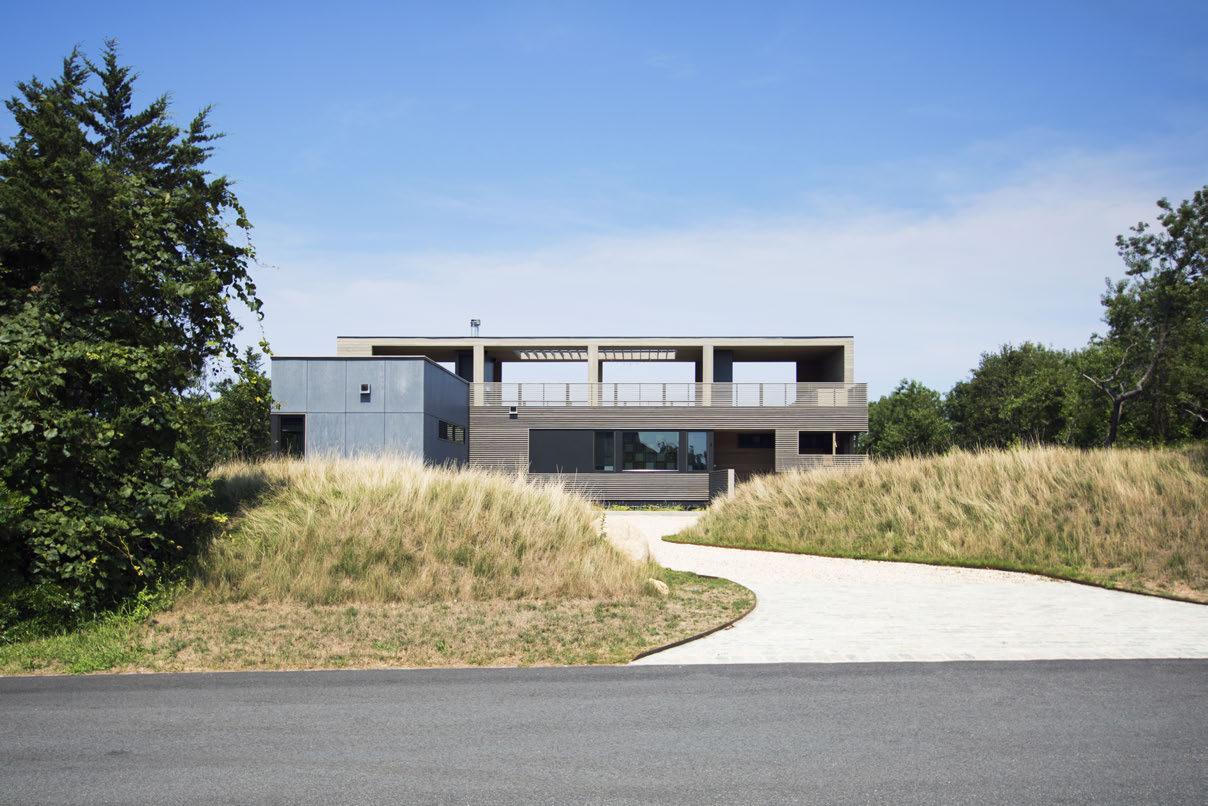
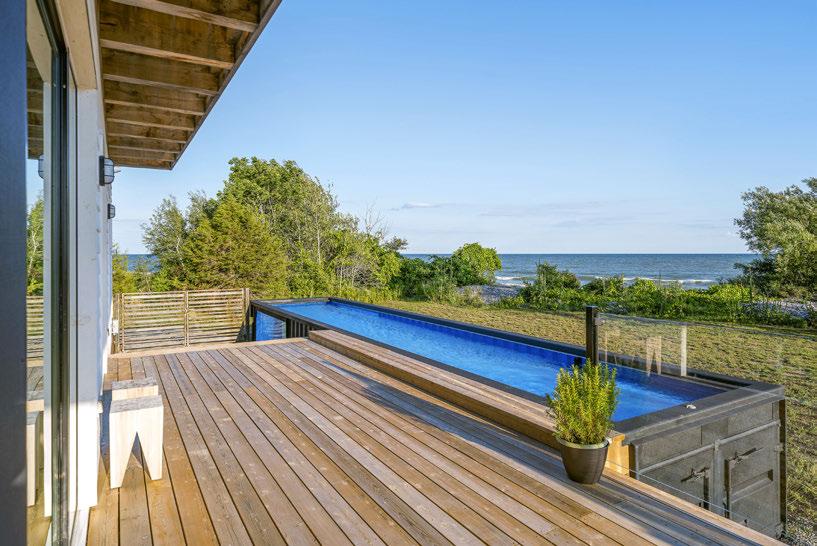
But the speed at which modular homes can be produced is unrivaled. “A two- or three-box modular home that’s 1,500 to 2,000 square feet could be fabricated in a factory in 10 to 12 weeks with an almost complete interior,” says Krager, adding that because the construction is done on jigs and tables in a controlled factory setting, the homes can—at least in theory—be built with greater accuracy and to higher tolerances.
And for those with sustainability on the brain, it’s easier for modular homes to be designed and built with the most advanced, energy-efficient systems in place. “We’ve completed homes that are completely off the grid, and at least half a dozen produce more energy than they consume,” says Tanney. “Most of them are net-zero.”
Such commitment to energy efficiency was recently on display when Van Metre Homes, an architecture firm based in northern Virginia, ventured into the modular category, designing its first residence in a series of modular homes that the firm has branded Powerhaus. The 2,706-square-foot townhouse was designed and built to be net-positive but also upscale in its aesthetic. “The house was loaded with solar panels, Tesla power walls, Mitsubishi mini-splits, a special water heater, induction cooking, and a robust smart-home package that powered and monitored the house,” says Mike Sandkuhler, Van Metre’s VP of building operations. “The finishes are what take it to the next level and make it feel luxurious.”
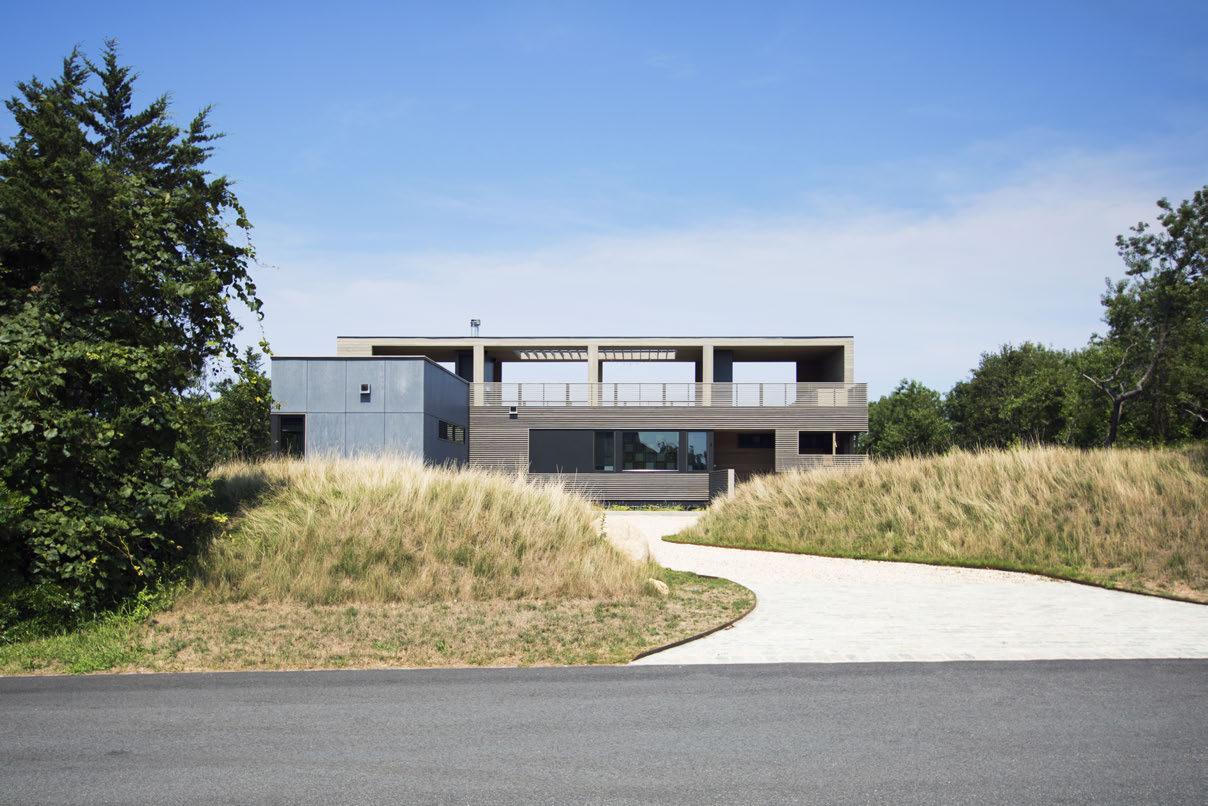
A shipping container finds new life as a lap pool flanked by a wooden deck.
Owners can customize a mod home by connecting various stair modules to different dwelling modules.
POOL CUES
The modular approach to design and construction isn’t limited to houses. Companies like Modpools in British Columbia, Canada, and Lucas Lagoons Design in Sarasota, Florida, specialize in repurposing shipping containers into swimming pools that can be built in ground, above ground, or into existing slopes.
Much like modular homes, these pools are faster to build, particularly when many materials are in short supply. That’s a point for modular design at a time when demand for pools has skyrocketed, thanks to people spending much more time in their homes. Mod pools are also less expensive to design and install than traditional, concrete-poured ones. Other advantages include the fact that their size and shape make them excellent for lap swimming, and they can often be relocated.
Mod pool. Mod home. What’s next in a mod, mod, mod, mod world? Those who focus on modular architecture and construction say that with advancements in manufacturing, the industry has exciting potential to offer even greater capabilities in the future.
