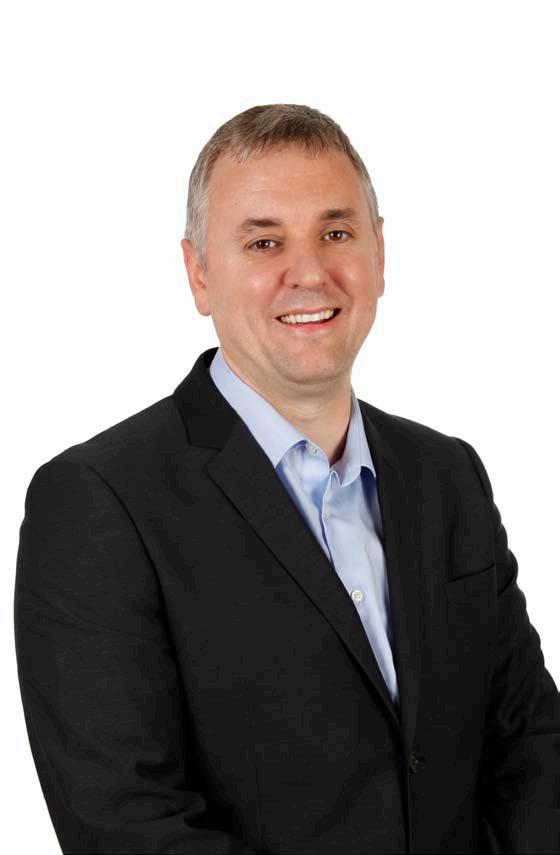
6 minute read
SSR Mining
A SHARPER EYE
SSR Mining has been through a rapid expansion over the past five years, and now it’s undergoing changes again. Whereas its last burst of development was in the physical realm, its new changes are in the digital one, as the company seeks to streamline its operations with the latest IT solutions. We spoke with David Thomas, Director of Information Technology, about why it’s important for mining to digitise.
SSR Mining Inc. is a Vancouver-based mining company producing precious metals – more specifically, gold and silver. For 70 years, the company operated under the name ‘Silver Standard’, but changed its name to SSR Mining Inc. in August 2017 as it evolved from a silver producer to a precious metals producer. In fact, a lot has advanced at the company recently: in 2014, it grew from being a one-mine operation to having three producing mines today, including the Marigold mine in Nevada, U.S.A., the Seabee Gold Operation in Saskatchewan, Canada, and Puna Operations in Jujuy Province, Argentina. SSR Mining also has two feasibility stage projects and a portfolio of exploration properties in North and South America.
The Marigold mine has operated consistently since 1989 and produced 205,161ounces of gold in 2018. The Seabee Gold Operation, in continuous production since 1991, produced a record 95,602 ounces of gold in 2018. SSR Mining’s Puna Operations, which consists of the Pirquitas property and the Chinchillas mine, declared commercial production in December 2018.
Everyone knows that both silver and gold are used heavily in the production of jewellery and Endeavour Magazine | 35
other forms of decoration, but there are other, less immediately obvious industries that also use the precious metals. Electronics is one: gold is used in bonding wire production, and silver is used throughout everyday technology such as mobile phones and laptops, as well as more specialized applications such as satellites and even high-tech weaponry! As is well known, prices for both silver and gold fluctuate, as does investor interest, but the uses of the metals persist. The industry isn’t going anywhere, but due to factors such as world politics, competing stock interests and many more, the price of silver and gold is variable. We spoke to David about how SSR Mining responds to this, and his answer was so sensible, we wondered why we hadn’t thought of it. “While we can’t control the price of gold, we can impact our costs to drive margins, profit and cash generation.” This is a brilliant way for SSR Mining to take control and get as much benefit from its portfolio
as possible, but how is the company going about it?
By David’s own admission, mining is one of the last industries, along with agriculture, to fully embrace the benefits of digitisation, but, like agriculture, it is also one that can greatly benefit from the level of visibility and analysis this change supports. Mining is an industry with many factors at play, across multiple sites, with everything from exploration results to vehicle routes needing easy-to-read monitoring so that efficient, cost-effective actions and decisions can be made. This is exactly what SSR Mining is working towards. As Director of Information Technology, David was able to tell us more:
“For us, the key driver is to be more efficient, and also to improve on our operational processes. One example would be truck productivity; even just taking a different route on a pathway in the mine can have an impact on the cost per ounce, due to gas consumption. Multiply that by a thousand times a day, at multiple mines, and that’s a big impact.” And those are just the small details. Being able to monitor and manage everything from minor details to wider-scale planning allows for loose bolts to be identified and tightened. SSR Mining has been working on developing and implementing the software needed for this for the past two and a half years and is already seeing the impact, and there’s still a long way to go.
“I don’t think there is ever an endpoint. Mining is one of those industries with so many areas to apply Operational Excellence analytics to: from truck productivity all the way to exploration drillhole sampling, process mill productivity, and even safety and sustainability.” With so many areas to consider, this is a continuous process of improvement for SSR Mining.
Regarding this change, David described SSR Mining as fast followers rather than innovators. The desire to try new ideas is there, but to be on the front line of this development would be too costly an endeavour for the company’s size. However, whilst they don’t have the budgets of mining giants, they also don’t have the deeply entrenched legacy IT systems, which gives the
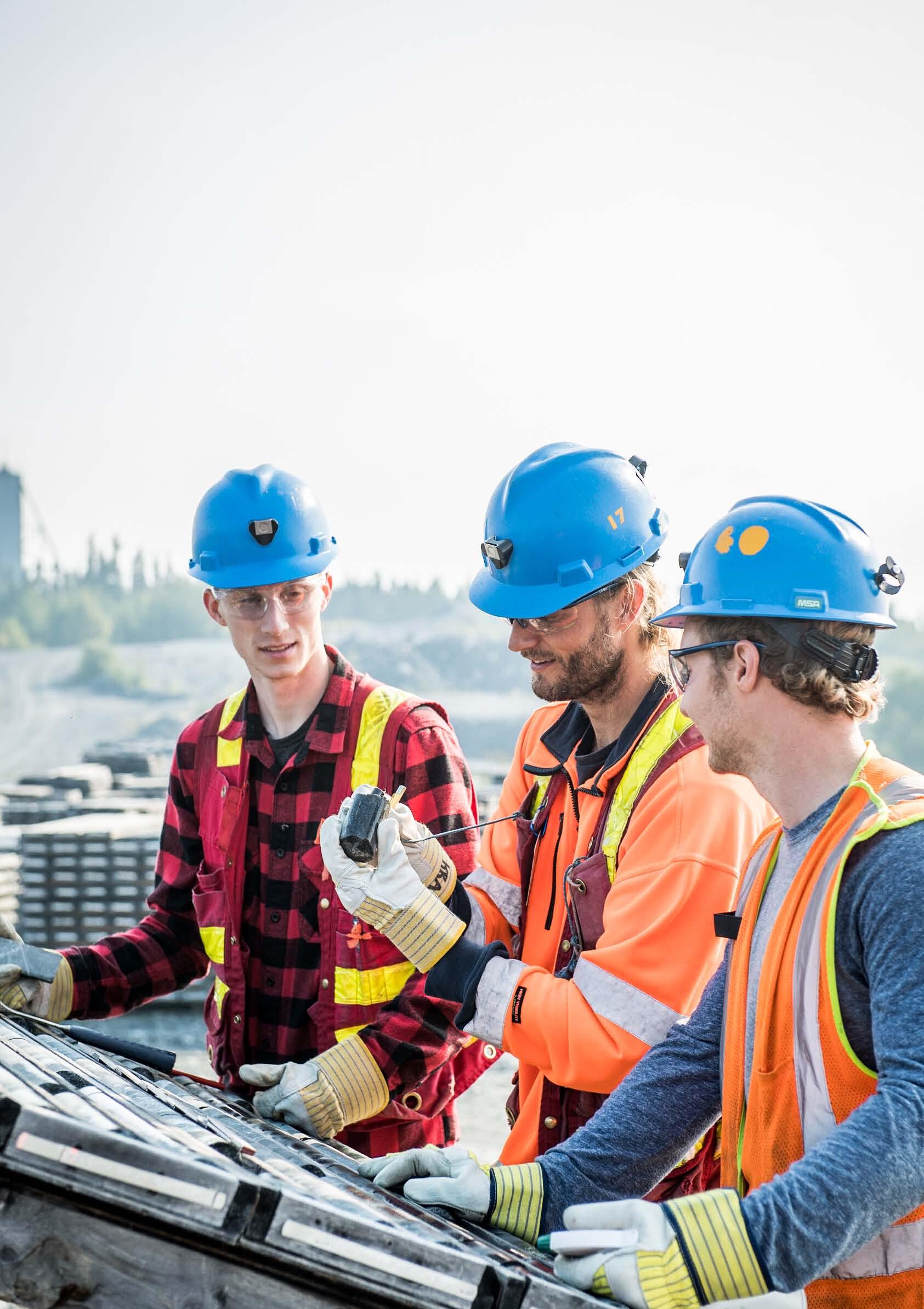
company a strong advantage. “We are able to quickly move into the Cloud any project we undertake, and we try to encourage our vendors to set up in such a way where they can be supported in the Cloud.”
Not reinventing existing research and development allows SSR Mining to leapfrog over steps of the process faced by larger companies. However, this, and being a fast follower, doesn’t mean there there’s no work at all. The company must carefully select which existing routes and approaches to take, and even though they aren’t process pioneers, they are devising the system in-house. “Quite honestly, there’s not really any off-the-shelf product. The software that is available was written by geologists in the 1980s and 90s.” Engaging with software developers, analytics, industry leaders and graduates alike, SSR Mining has been devising its system carefully for these past two and a half years. It is also working closely with vendors such as Komatsu and Hitachi Wenco, whose trucks have inbuilt software that SSR Mining can upload and integrate into its own analytical processes.
One dramatic example of how gamechanging these capabilities could be relates to SSR Mining’s Seabee Gold Operation in Northern Saskatchewan. Access to the mine site is fly-in, fly out by small fixed wing aircraft to an airstrip located on the property. Equipment and large supplies are transported to the site via a 60-kilometer winter ice road, which is typically in use from January through March. Therefore, supply chain management and forward planning, down to the last detail, is essential for cost-saving, and simply making sure that the mine is ready to function for the year to come. “With ice road access between January and March only each year, we need to carefully plan, order and schedule shipments via the ice road in preparation for the year ahead. We need to transport fuel, equipment and all other items necessary to run a mine.”
We Manage, Solve, and Deliver I.T.
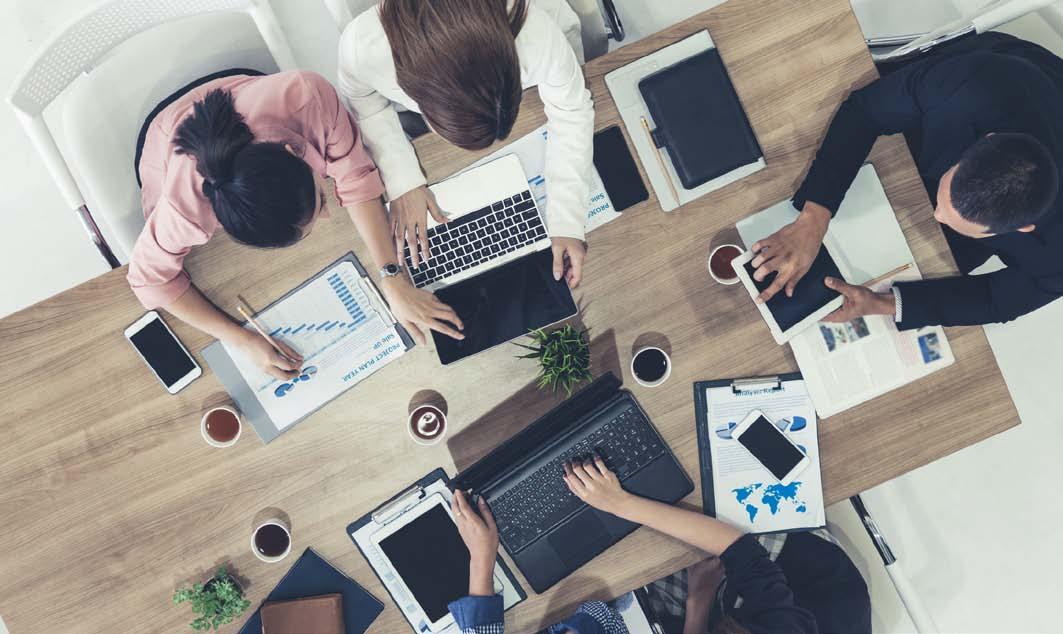
Managed IT Services
A comprehensive range of IT Support for Businesses, Organizations and Educational Sectors. Remote and Onsite IT Services We can provide our services remotely or onsite for customers requiring support within their environment. Proactive IT Services
IT problems can be identified and rectified quickly by our proactive engineers.
By being able to dot all of the ‘I’s and cross the ‘T’s, and monitor its operations in new levels of analytical detail, SSR Mining can plan for this in a tighter and more cost-effective way than ever before. Whilst an extreme case, this same benefit is felt throughout SSR Mining’s operations – with so many factors at play, and at such a scale, every detail helps.

Proud strategic partners with:





Transwest Air and Northern Shield Helicopters are proud to support SSR with fixed wing and rotary services for their projects in Saskatchewan. CLICK HERE TO SEE OUR SERVICES
CHARTER 1-877-989-2677
/transwestair Follow us on
RESERVATIONS 1-800-667-9356
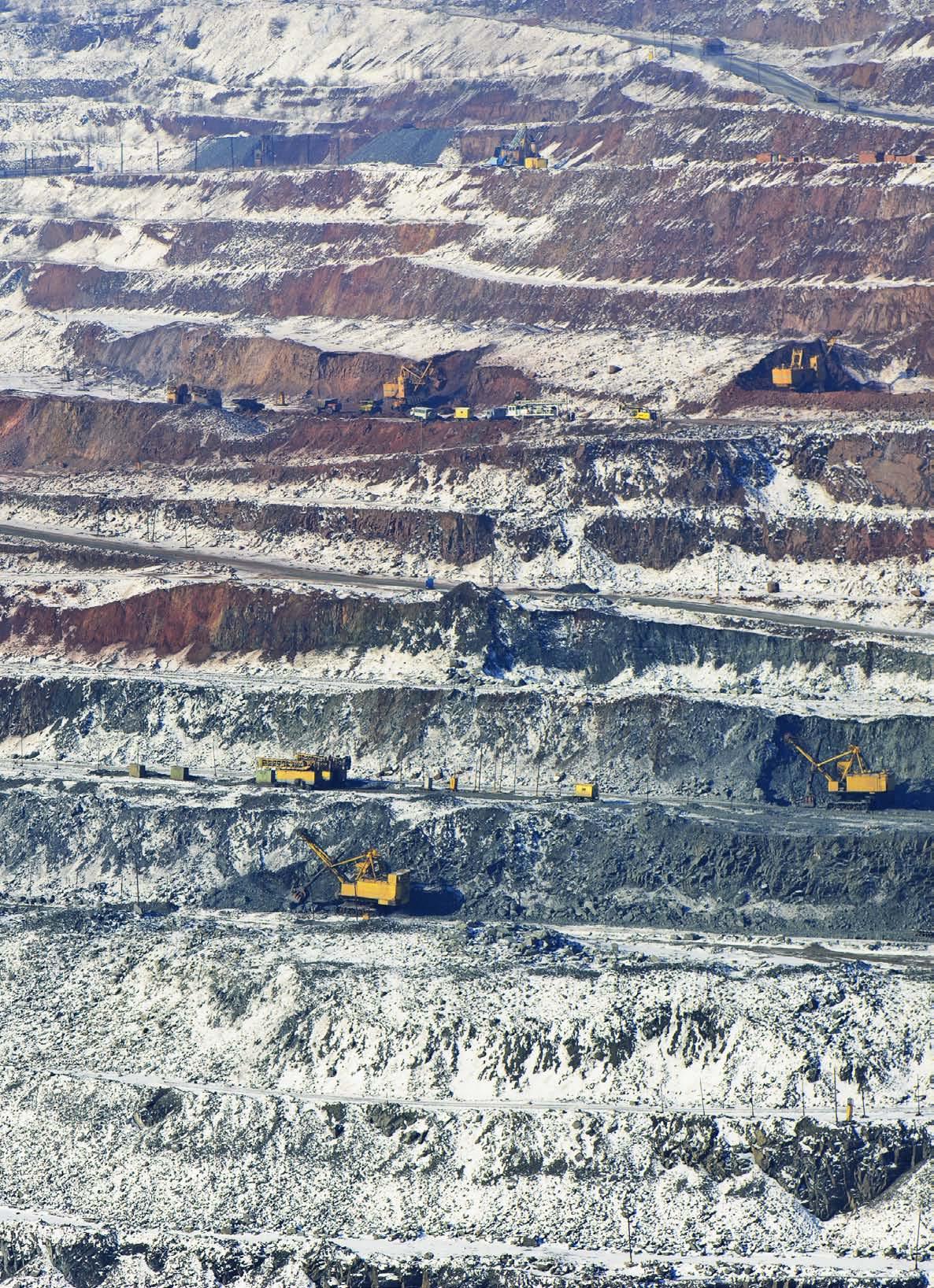